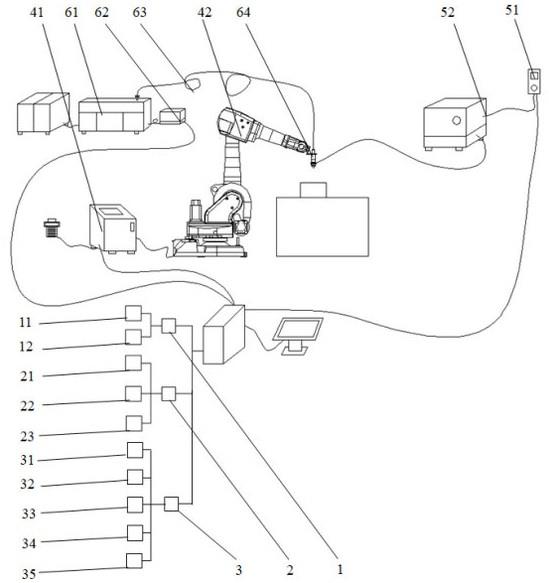
1.本发明涉及机械、材料、物理、计算机、控制等交叉融合的先进制造技术领域,特别涉及一种专门利用激光手段,用于工程仿生的自动化、智能化、精准化和多功能化的制造装备。
背景技术:
2.仿生是模仿生物原理来建造技术系统,或者使人造技术系统具有或类似于生物特征的科学。仿生功能表面是模仿生物体表典型特征元素而设计并制备出的具有类似生物优异功能的人工表面。大量研究表明,设计与制造合理的仿生功能表面可实现减粘、降阻、耐磨、抗疲劳等多种功能特性。近年来,随着仿生技术在工程领域的不断成功应用,使得用于仿生功能表面制造的工艺方法和装备的研究成为国内外热点。
3.现有用于仿生功能表面的制造方法有机械加工、热处理、化学刻蚀、激光加工技术等。其中,激光技术凭借其加工质量好、绿色环保等优点使其具有其它加工手段无法替代的优势。此外,激光加工的急冷急热作用可以改善仿生单元体的组织结构,从而可以达到改善材料表面机械和力学性能的目的。通过对激光加工参数的调节,可以进行激光淬火、激光表面熔凝、激光表面合金化、激光表面熔敷、激光冲击硬化、气相沉积等,且激光加工技术适合与机器人技术相结合,不仅可以提高整个加工装备的智能化、自动化水平,而且可以显著提高系统的柔性和生产效率。
4.激光技术的诸多优势使得激光加工设备可以直接用于仿生功能表面的制造。但加工质量和效率低下却成为制约仿生功能表面研究和一些仿生成果转化的瓶颈。目前,国内外可用于仿生制造的激光加工装备主要存在以下不足:1.适合的加工参数获取困难,严重制约着加工效率的提高。仿生表面特定形态、结构参数等仿生实现要经过多次前期试验,需在试件上先行优化出适合的激光加工工艺参数后方可在待加工工件上应用,使得加工前的工作量大,延长了加工周期,制约了加工效率的提高。因此,国内外尚缺乏一套专门用于激光仿生制造工艺参数选择的数据库系统,能够自动获取实现待加工部件表面仿生特征的激光加工参数和工艺数据的准确信息。
5.2.在仿生信息输入方面,待处理区域仿生单元体的组织、形貌、尺度、力学特征等参数不能直接输入,而是经试验优化激光加工工艺参数后,由工作人员依照经验对设备进行不断调整并输入优化好的激光加工工艺参数方可进行正式加工作业,国内外尚缺乏一种与仿生工艺参数数据库系统直接进行交互并对仿生信息进行直接输入的人机交互界面系统。
6.3.自动化程度低。目前应用于仿生功能表面制造的激光加工装备,加工路径的生成多为工作人员根据预先设想的仿生参数信息进行简单的在线编程,加工方案的生成大部分依赖于工作人员的经验,且仿生表面制备的工艺参数不能自动获取,这些均成为制约整个制备过程的自动化程度以及加工精度提高的瓶颈。
7.4.加工范围小。精准、灵活的小型激光制备装置仅适合小型试件及零部件的仿生
加工,而大型、高功率激光器又达不到仿生加工对表面质量和精度的要求,因此,大型零部件表面的仿生制造受到限制。
8.目前在机械工程领域所应用的自动化程度比较高的激光加工机器人,如应用于汽车车身加工车间的激光切割和激光焊接机器人,其自动化程度高,可以完全在无人干预的状态下进行作业,但其整个系统的设计只针对单一化和专门化生产定制,难以应用到对工艺、表面及加工参数要求很高的仿生表面制造当中。发明人课题组经多年研究,积累了大量的数据及其经验,但缺乏专门的装备技术实施。
技术实现要素:
9.针对现有技术的不足,本发明提出一种适用于各种试件及零部件表面仿生制造的基于数字孪生的智能制造系统,用以实现金属、非金属表面仿生形态、结构、材料等仿生特征的激光制造。
10.基于数字孪生的智能制造系统,由人机交互系统、编程控制系统、孪生虚拟系统以及加工执行系统构成;人机交互系统包括3d模型编辑器模块和仿生加工单元构造器模块;加工方案生成器接收来自3d模型编辑器模块的待加工零部件参数以及仿生加工单元构造器模块的仿生信息参数;仿生信息参数包括仿生单元加工方式的选择、工件基体材料参数的设定、单元体特征参数以及加工位置和区域的构建和标定等;编程控制系统包括高性能计算机、激光器控制器、机器人运动控制器和辅助装置控制器,激光器控制器、机器人运动控制器和辅助装置控制器通过串口直接与高性能计算机相连;高性能计算机上集成有仿生工艺参数数据库、加工方案生成器和集成同步控制器,仿生工艺参数数据库与加工方案生成器提供人机交互系统接口;仿生工艺参数数据库将激光加工工艺参数和环境介质参数输出至加工方案生成器;加工方案生成器将加入了仿生加工单元信息的3d工件模型和仿生工艺参数数据库输出的仿生加工参数信息作为输入,采用智能化的算法分别为激光器、六自由度关节机器人和辅助装置生成相应的控制命令序列;控制命令序列包括时间控制序列和设备命令控制序列,该控制命令序列不仅包含了各自的控制信息,还包含了相互之间的同步信息;集成同步控制器的输入是加工方案生成器生成的时间控制序列和设备命令控制序列,同时接收六自由度关节机器人、激光器和辅助装置三个设备的命令执行反馈信息;集成同步控制器的输出是分别向激光器控制器、机器人运动控制器和辅助装置控制器发送的控制命令;孪生虚拟系统包括制造终端实体场景孪生模型、工艺数据实时采集模块、仿生信息参数离线采集模块、工艺过程离线仿真模块和工艺数据管控器;工艺数据管控器接收来自制造终端实体场景孪生模型、工艺数据实时采集模块、仿生信息参数离线采集模块以及工艺过程离线仿真模块的工艺数据信息;工艺过程离线仿真模块接收来自工艺数据实时采集模块和仿生信息离线采集模块信息,工艺数据管控器的
工艺参数调控结果传输至加工方案生成器生成控制命令序列;仿生工艺参数数据库接收仿生信息参数离线采集模块的工艺信息并对仿生工艺参数数据库的工艺数据进行实时更新;加工执行系统包括激光器、光纤耦合传输单元、激光加工工作头、六自由度关节机器人和辅助装置;激光器通过光纤耦合传输单元与激光加工工作头连接,六自由度关节机器人首端设置的激光加工工作头实现激光加工工作头的多维运动与激光加工。
11.更进一步而言,所述控制命令序列的生成方式为:加工方案生成器首先让用户确定六自由度关节机器人、工件固定装置以及工件的中心坐标,以完成加工方案的整体布局定位,而后加工方案生成器能够对3d工件模型中的仿生加工位置和区域进行遍历,先从3d工件模型中提取出待加工的单元体特征参数,而后使用该仿生加工单元的加工信息从仿生工艺参数数据库中查找到经过优化的工艺参数数据;接着将与路径相关的激光加工参数与待加工仿生单元自身的曲线相结合计算出六自由度关节机器人的行走路径、速度及姿态信息;最后将六自由度关节机器人、激光器和辅助装置的相关控制信息分别分类提取,并使用规则映射的方式,将其分别转换为机器人运动控制器、激光器控制器和辅助装置控制器能够识别的代码序列,同时生成六自由度关节机器人、激光器和辅助装置的协同工作时间序列,代码序列与时间序列之间建立对应的映射关系,以便集成同步控制器对其进行统一控制,使它们能够协调工作。
12.更进一步而言,集成同步控制器分别向激光器控制器、机器人运动控制器和辅助装置控制器发送控制命令的具体方式为:首先根据时间控制序列,分别找到激光器控制器、机器人运动控制器和辅助装置控制器相对应的控制命令并进行发送,同时接收六自由度关节机器人、激光器和辅助装置的反馈信息,将六自由度关节机器人、激光器和辅助装置三者的反馈信息与执行预期进行比较,如果符合预期则说明六自由度关节机器人、激光器和辅助装置三个设备同步运转良好,继续后续控制命令的发送;如果与预期不符,则根据六自由度关节机器人、激光器和辅助装置三个设备的反馈情况,调用预设的同步处理机制进行处理,使其再次达到同步状态再开始后续命令的执行。
13.更进一步而言,所述的工艺数据管控器向加工方案生成器传输工艺参数调控结果的具体方式为:加工方案生成器首先依据用户设定的仿生信息参数在制造终端实体场景孪生模型和仿生工艺参数数据库进行遍历,接收初始加工工艺参数,仿生加工过程中工艺数据实时采集模块通过传感器及视觉采集设备实现加工终端场景感知数据、原位熔池温度、飞溅等工艺数据采集,工艺数据管控器接收来自工艺数据实时采集模块和工艺过程离线仿真模块的相关工艺信息进行综合分析,判断仿生信息参数的准确度并对工艺参数作出实时调整,并与制造终端实体场景孪生模型进行实时的数据交互;仿生信息参数离线采集模块通过对仿生加工要素进行离线采集及录入,并通过工艺数据管控器对仿生工艺参数数据库中的工艺信息进行更新;工艺过程离线仿真模块接收来自工艺数据实时采集模块和仿生信息离线采集模块信息进行仿生制造过程的离线仿真,制造终端实体场景孪生模型通过与工艺过程离线仿真模块的数据交互进行学习,并对模型进行调整。
14.更进一步而言,所述的仿生单元加工方式包括相变、熔凝、雕刻、熔覆、合金化,所述的工件基体材料参数包括材料牌号、吸收系数和导热率,所述的单元体特征参数包括单
元体的形态、间距、深度、宽度、平均显微硬度。
15.本发明的有益效果:1.整个加工过程中人的参与因素较少,自动化、智能化程度更高,客户在加工之前只需向人机界面系统提供待加工试件或零部件cad模型、设计好的仿生单元体特征参数以及材料参数,系统即可自动生成激光加工工艺参数以及机器人和辅助装置的控制程序,减少了加工人员大量的工艺参数选取以及机器人示教的工作。
16.2.降低了仿生功能表面加工成本,提高了生产效率和加工质量。仿生工艺参数数据库使得加工工艺参数的确定摆脱了前期工艺参数的优化工作,也避免了由于人为选择工艺参数的误差而导致的加工质量问题,且制造系统完全由编程软件自动编程,较示教编程手段精度更高。
17.3.提供了一套向导化的人机界面系统,不仅可以直接输入所设计的仿生功能表面的参数信息,而且简化了整个操作过程。
18.4.系统采用了六自由度关节式机器人携带激光加工工作头,增大了整个制造系统的柔性,六自由度关节式机器人可以携带激光加工工作头对零部件进行加工,实现了大型工件的复杂形状表面的仿生制造。
附图说明
19.图1为本发明基于数字孪生的智能制造系统整体结构组成示意图。
20.图2为本发明基于数字孪生的智能制造系统的工作原理示意图。
具体实施方式
21.参阅附图所示,基于数字孪生的智能制造系统,人机交互系统1、编程控制系统2、孪生虚拟系统3以及加工执行系统构成的多部分协调的软件与硬件系统;人机交互系统1包括3d模型编辑器模块11和仿生加工单元构造器模块12;人机交互系统用于待加工零部件特征参数以及仿生单元信息的输入与传输;3d模型编辑器模块11将待加工零部件参数(3d工件模型)输出至加工方案生成器22,仿生加工单元构造器模块12将仿生信息参数输出至加工方案生成器22;人机交互系统是客户需求信息输入的窗口,能够对待加工零部件和仿生单元进行参数化定制,人机交互系统主要指界面系统软件,其特征在于针对仿生耦合表面设计与制备而专门编制,加工前期的准备工作只需客户按照仿生单元信息构建向导的要求输入仿生单元设计的信息即可,界面系统软件主要包括3d模型编辑器模块11和仿生加工单元构造器模块12,3d模型编辑器模块11能够对待加工的零部件进行cad建模、加载、显示、操作、更改、存储和数据导出等;仿生加工单元构造器模块12采用构建向导的方式指导用户一步步完成仿生信息参数的设定,仿生信息参数包括仿生单元加工方式(相变、熔凝、雕刻、熔覆、合金化)的选择、工件基体材料参数(材料牌号、吸收系数、导热率等)的设定、单元体特征参数(单元体的形态、间距、深度、宽度、平均显微硬度)以及加工位置和区域的构建和标定等,若仿生加工单元信息参数中的加工方式选定为熔覆或合金化后,还需弹出添加粉末材料参数对话框对熔覆或合金粉末参数(牌号、组成、吸收系数、导热系数等)进行设定;
编程控制系统2包括高性能计算机、激光器控制器62、机器人运动控制器41和辅助装置控制器51,激光器控制器62、机器人运动控制器41和辅助装置控制器51通过串口直接与高性能计算机相连,编程控制系统2用于待加工零部件特征参数和仿生单元信息与六自由度关节机器人42运动轨迹和加工参数的转换,并由高性能计算机上的集成同步控制器23实现整个系统的集成控制;高性能计算机上集成有仿生工艺参数数据库21、加工方案生成器22和集成同步控制器23,仿生工艺参数数据库21与加工方案生成器22提供人机交互系统接口;仿生工艺参数数据库21将激光加工工艺参数(波长、模式、功率密度、频率、脉宽、离焦量、光斑直径、扫描速度等)和环境介质参数(气流角度、速度、粉末流量、水膜厚度等)输出至加工方案生成器22,仿生工艺参数数据库21依托大量理论和实验数据、参数构建;加工方案生成器22将加入了仿生加工单元信息的3d工件模型和仿生工艺参数数据库21输出的仿生加工参数信息作为输入,采用智能化的算法分别为激光器61、六自由度关节机器人42和辅助装置52生成相应的控制命令序列;该控制命令序列不仅包含了各自的控制信息,还包含了相互之间的同步信息;其工作原理为,加工方案生成器22首先让用户确定六自由度关节机器人42、工件固定装置以及工件的中心坐标以完成加工方案的整体布局定位,而后加工方案生成器22能够对3d工件模型中的仿生加工位置和区域进行遍历,先从3d工件模型中提取出待加工的单元体特征参数(单元体的形态、间距、深度、宽度、平均显微硬度),而后使用该仿生加工单元的加工信息从仿生工艺参数数据库21中查找到经过优化的工艺参数数据;接着将与路径相关的激光加工参数(离焦量、扫描速度)与待加工仿生单元自身的曲线相结合计算出六自由度关节机器人42的行走路径、速度及姿态等信息;这些信息也可以通过将机器人运动控制器41接入加工方案生成器22中,对六自由度关节机器人42进行示教获得;最后将六自由度关节机器人42、激光器61和辅助装置52的相关控制信息分别分类提取,并使用规则映射的方式,将其分别转换为机器人运动控制器41、激光器控制器62和辅助装置控制器51能够识别的代码序列,同时生成六自由度关节机器人42、激光器61和辅助装置52的协同工作时间序列,代码序列与时间序列之间建立对应的映射关系,以便集成同步控制器23对其进行统一控制,使它们能够协调工作;加工执行系统的协调控制主要由集成同步控制器23完成,集成同步控制器23将对六自由度关节机器人42、激光器61和辅助装置52的控制集成到一起进行统一的调度管理,以实现六自由度关节机器人42、激光器61和辅助装置52之间的同步协调运作,集成同步控制器23的输入是加工方案生成器22生成的时间控制序列和设备命令控制序列,同时接收六自由度关节机器人42、激光器61和辅助装置52三个设备的命令执行反馈信息;集成同步控制器23它的输出是分别向激光器控制器62、机器人运动控制器41和辅助装置控制器51发送控制命令,它的工作过程为:首先根据时间控制序列,分别找到激光器控制器62、机器人运动控制器41和辅助装置控制器51相对应的控制命令并进行发送,同时接收六自由度关节机器人42、激光器61和辅助装置52的反馈信息,将三者的反馈信息与执行预期进行比较,如果符合预期则说明六自由度关节机器人42、激光器61和辅助装置52三个设备同步运转良好,继续后续控制命令的发送;如果与预期不符,则根据六自由度关节机器人42、激光器61和辅助装置52三个设备的反馈情况,调用预设的同步处理机制进行处理(比如某个设备停止等
待),使其再次达到同步状态再开始后续命令的执行;孪生虚拟系统3包括制造终端实体场景孪生模型31、工艺数据实时采集模块32、仿生信息参数离线采集模块33、工艺过程离线仿真模块34和工艺数据管控器35;制造终端实体场景孪生模型31包含物理实体场景模型以及大量经模型化、公式化处理的工艺模型;孪生虚拟系统3用于仿生加工过程中加工质量与仿生信息的实时监测与离线仿真,实现工艺参数的实时调整反馈;工艺数据管控器35接收来自制造终端实体场景孪生模型31、工艺数据实时采集模块32、仿生信息参数离线采集模块33以及工艺过程离线仿真模块34的工艺数据信息;工艺过程离线仿真模块34接收来自工艺数据实时采集模块32和仿生信息离线采集模块33信息,工艺数据管控器35的工艺参数调控结果传输至加工方案生成器22生成控制命令序列;仿生工艺参数数据库21接收来自孪生虚拟系统3的仿生信息参数离线采集模块33的工艺信息并对数据库的工艺数据进行实时更新;所述的工艺数据管控器35向加工方案生成器22传输工艺参数调控结果的具体方式为:加工方案生成器22首先依据用户设定的仿生信息参数在制造终端实体场景孪生模型31和仿生工艺参数数据库21进行遍历,接收初始加工工艺参数,仿生加工过程中工艺数据实时采集模块32通过传感器及视觉采集设备实现加工终端场景感知数据、原位熔池温度、飞溅等工艺数据采集,工艺数据管控器35接收来自工艺数据实时采集模块32和工艺过程离线仿真模块34的相关工艺信息进行综合分析,判断仿生信息参数的准确度并对工艺参数作出实时调整,并与制造终端实体场景孪生模型31进行实时的数据交互;仿生信息参数离线采集模块33通过对仿生加工要素进行离线采集及录入,并通过工艺数据管控器35对仿生工艺参数数据库21中的工艺信息进行更新;工艺过程离线仿真模块34接收来自工艺数据实时采集模块32和仿生信息离线采集模块33信息进行仿生制造过程的离线仿真,制造终端实体场景孪生模型31通过与工艺过程离线仿真模块34的数据交互进行学习,并对模型进行调整;加工执行系统包括激光器61、光纤耦合传输单元63、激光加工工作头64、六自由度关节机器人42和辅助装置52;激光器61通过光纤耦合传输单元63与激光加工工作头64连接,六自由度关节机器人42首端设置的激光加工工作头64实现激光加工工作头64的多维运动与激光加工。
22.更进一步而言,加工执行系统可自由装配光纤、半导体、灯泵浦等多种激光光源以及激光加工终端,激光束通过光纤耦合传输单元63传输至激光加工工作头64,能够对金属或非金属部件进行相变、熔凝、雕刻、熔覆、合金化和烧结加工,利用激光与材料的交互作用获得理想的耦合仿生单元,激光额定功率≥500w。
23.更进一步而言,所述的六自由度关节机器人42上设有检测反馈装置,六自由度关节机器人42可携带激光加工工作头64,按照规划好的路径完成加工作业;检测反馈装置包括位置检测、碰撞检测等,可以使机器人精准定位,防止发生碰撞等。
24.更进一步而言,辅助装置52包含夹具(卡具)、传感检测装置等,也包括环境、介质和添加材料等的提供装置,以及为实现不同试件和部件加工而自由选择和装载的必备设施。
25.辅助装置控制器51可以包括同步送粉控制器、环境气体控制器、加工介质控制器等等,按照加工工艺的要求分别为仿生功能表面的制备过程提供材料、环境、介质等。
26.更进一步而言,所述的3d模型编辑器模块11为cad模型编辑器模块。
27.本发明的工作原理及使用过程:用户进入人机交互界面系统3d模型编辑器模块11,建立或导入待加工试件或零部件cad模型,在3d模型编辑器模块11客户还可以对建立或导入待加工试件或零部件进行修改、导出等操作;接着进入仿生加工单元构造器模块12,通过采用仿生加工单元构造器模块12提供的构建向导一步步完成仿生加工单元的构建,首先选择加工方式的类型,如相变、熔凝、雕刻、熔覆、合金化等,而后系统根据用户的选择弹出不同的选择页面,提示用户输入所选加工类型下所需工件基体材料参数信息(材料牌号、组成、吸收系数、导热系数等),若加工方式为相变、熔凝或雕刻,用户只需提供工件基体材料参数信息(材料牌号、组成、吸收系数、导热系数等);若加工方式为熔覆或合金化,用户除了需要提供用户只需提供工件基体材料参数信息(材料牌号、组成、吸收系数、导热系数等),还需要提供添加粉末材料的牌号、组成、吸收系数、导热系数、粉末种类、粒度等参数信息;输入信息确认之后,系统自动返回3d模型编辑模块11,以建立或被加载的待加工试件或零部件的3d模型为蓝本,在其基础上通过3d建模操作,将需要进行加工的仿生加工单元在3d模型上进行标定,以便后期的加工曲线的生成,系统能够根据上述所选择的加工方式类型、工件基体材料参数和/或粉末材料参数,提供适合于选择结果的3d模型建模工具,以便用户在3d模型上标定需要进行仿生加工的位置和区域,包含点、线、面等标定工具;仿生加工单元信息输入完毕并确认后,系统自动进入编程控制系统中的加工方案生成器模块22,加工方案生成器模块22将加入了仿生加工单元信息的3d工件模型和仿生工艺参数信息作为输入,采用智能化的方法分别为激光器61、六自由度关节机器人42和辅助装置52生成相应的控制命令序列;具体而言,加工方案生成器22首先让用户确定六自由度关节机器人42、工件固定装置以及工件的中心坐标以完成加工方案的整体布局定位,而后加工方案生成器22能够对3d工件模型中的仿生加工位置和区域进行遍历,先从3d工件模型中提取出待加工的单元体特征参数(单元体的形态、间距、深度、宽度、平均显微硬度),而后使用该仿生加工单元的加工信息从仿生工艺参数数据库21中查找到经过优化的工艺参数数据(激光波长、模式、功率密度、离焦量、扫描速度、脉宽、频率、保护气体流量、角度等);同时加工方案生成器22从3d工件模型中提取出待加工的仿生加工单元的曲线,接着将与路径相关的激光加工参数(比如离焦量、扫描速度)与待加工的仿生加工单元自身的曲线相结合计算出六自由度关节机器人42的行走路径、行走速度及姿态等信息;这些信息也可以通过将机器人运动控制器41接入加工方案生成器22中,对六自由度关节机器人42进行示教编程获得。最后将六自由度关节机器人42、激光器61和辅助装置52的相关控制信息分别分类提取,使用规则映射的方式,将其分别转换为激光器控制器62、机器人运动控制器41和辅助装置控制器51能够识别的代码序列,同时生成六自由度关节机器人42、激光器61和辅助装置52的协同工作时间序列,代码序列与时间序列之间建立对应的映射关系,以便集成同步控制器23对其进行统一控制,使它们能够协调工作。
再多了解一些
本文用于企业家、创业者技术爱好者查询,结果仅供参考。