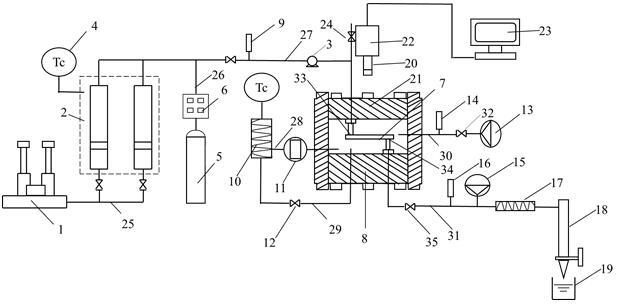
1.本发明涉及微流控实验技术领域,尤其涉及评价含水饱和度及矿化度混相压力影响的装置及方法。
背景技术:
2.近年来,在油气开采过程中注二氧化碳开发是提高低渗油藏采收率的有效方式之一,注二氧化碳驱按实质分为两种形式:一种是混相驱,另一种是非混相驱,两者之间的差别在于能否达到混相的最低压力(即,最小混相压力,mmp)。当mmp大于地层压力时,即可实现非混相驱油;当mmp小于地层压力时,即可实现混相驱油。而且经过大量的理论研究和实践证明,混相驱比非混相驱的更能提高原油采收率。二氧化碳与地层原油是否混相,是决定油藏能否高效开发的关键。而混相驱中的关键参数是最小混相压力,所以如何更高效、更准确、应用范围更广的测量mmp显得尤为重要。
3.现有技术中通常分析组分、温度、co2的不纯度等方面对最小混相压力进行研究,如,宋文鹏.co2驱最小混相压力的影响因素分析.[j].当代化工,2016,45(4):680-681,723中,通过计算,分析温度,原油组成成分,及co2中杂质含量对co2混相驱最小压力的影响;专利文献cn106884635a公开了一种低、特低渗透油藏co2驱最小混相压力的测定方法,进一步分析岩心渗透率、储层非均质性等因素对(特)低渗透油藏co2混相驱替的影响。然而,实际油藏中是含水的,现有技术中均未考虑油藏的含水饱和度及水的矿化度对最小混相压力的影响。
技术实现要素:
[0004]
发明概述:针对现有技术的上述缺点,本发明提供一种评价含水饱和度及矿化度对co
2-原油混相压力的影响规律的实验装置及方法,使微流控实验不仅仅可以考虑含水饱和度及矿化度对最小混相压力的影响,而且具有实时可视化、耗时短、微纳尺度等优点,使其所测的最小混相压力可靠性更强。
[0005]
具体
技术实现要素:
本发明提供一种评价含水饱和度及矿化度对混相压力影响规律的装置,包括:驱替系统、封闭接触系统、温压调节系统、数据及图像采集系统、油水分离及计量系统。
[0006]
所述封闭接触系统包括高压密闭夹持器8、微观可视化芯片7,该系统是混相发生的场所,注入的二氧化碳在微观可视化芯片7中与原油多次接触从而达到混相。
[0007]
进一步的,所述微观可视化芯片7置于高压密闭夹持器8的空腔内,所述微观可视化芯片7上设有输入口33和输出口34;所述高压密闭夹持器8上设置可视化窗口21;所述微观可视化芯片7内设有第一连通区域40、第二连通区域41,所述第一连通区域40通过第一阀门36与输入口33连接,所述第一连通区域40通过第二阀门37与输出口34连接;所述第二连通区域41通过第三阀门38与输入口33连接,所述第二连通区域41通过第四阀门39与输出口
34连接。所述第一连通区域40用于模拟油藏;所述第一连通区域40包含基质圆柱体42,用于模拟岩石颗粒;所述第二连通区域41用于连通驱替系统与油水分离及计量系统,为管线内矿化水的驱除提供通道。
[0008]
所述驱替系统包括高压注入泵1、活塞容器2、气体增压系统6、二氧化碳气源5、真空泵3、放空阀24,为了避免水的矿化离子对驱替泵腔体的腐蚀,由高压注入泵1连接活塞容器2作为液体的驱动系统,而二氧化碳气源5的初始压力无法达到混相压力,需经过气体增压系统6(即气体压缩机)后注入。为了避免气泡的存在对实验结果的影响,需使用真空泵3对微观可视化芯片7进行抽真空。
[0009]
进一步的,所述活塞容器2的进口端通过泵送管道25连接高压注入泵1,所述活塞容器2的出口端通过流体输入主管道27连接输入口33,所述流体输入主管道27上设有真空泵3和放空阀24,所述放空阀24位于真空泵3的下游;所述二氧化碳气源5、气体增压系统6依次通过流体输入分管道26并入流体输入主管道27。
[0010]
优选的,所述活塞容器为可加热耐腐蚀活塞容器。
[0011]
所述油水分离及计量系统包括分离阀35、回压泵15、冷凝管17、油水分离装置18、液体收集及计量装置19。该系统的功能为计算微观可视化芯片7的含水饱和度,从而为之后研究不同含水饱和度对co
2-原油混相压力的影响提供依据。
[0012]
进一步的,所述输出口34通过油水分离管道31依次连接分离阀35、回压泵15、冷凝管17、油水分离装置18;所述液体收集及计量装置19用于收集及计量由所述油水分离装置18流出的液体。
[0013]
所述温压调节系统包括加热容器10、循环泵11、控温阀12、围压泵13、围压阀32、温度传感器4、第一压力传感器9、第二压力传感器14、第三压力传感器16,该系统的功能是模拟真实地层条件下的温度和压力,可实时监测设备的温压变化。
[0014]
进一步的,所述加热容器10通过流体加热输出管道28依次连接循环泵11、高压密闭夹持器8,所述高压密闭夹持器8通过流体加热输入管道29依次连接控温阀12、加热容器10,形成循环回路;所述围压泵13通过围压监测管道30依次连接围压阀32、高压密闭夹持器8;所述温度传感器4用于检测活塞容器2内的温度;所述第一压力传感器9设置在流体输入主管道27上,所述第二压力传感器14设置在围压监测管道30上,所述第三压力传感器16设置在油水分离管道31上。
[0015]
所述数据及图像采集系统包括显微镜20、摄像监测系统22、控制系统23;所述数据及图像采集系统的数据采集不仅减小了数据收集的难度,同时与细管法相比还可记录多个测点,对整个实验过程中的数据进行归纳分析提高了测量的准确性。并且通过图像采集系统可观察到二氧化碳与原油的混相过程,所生成的视频图件可为后期研究提供资料。
[0016]
进一步的,所述显微镜20设置于可视化窗口21的正上方,所述显微镜20用于获取微观可视化芯片7中二氧化碳与原油接触界面的图像;所述摄像监测系统22与控制系统23连接,所述摄像监测系统22用于将显微镜20获取的图像传输给控制系统23,所述温度传感器4、第一压力传感器9、第二压力传感器14、第三压力传感器16都与控制系统23连接。
[0017]
本发明还提供一种采用上述装置评价含水饱和度及矿化度对混相压力影响的方法,所述实验方法的步骤包括:步骤一、安装微观可视化芯片7后,调节密闭夹持器8内的温度、压力;
步骤二、调节微观可视化芯片7内的压力及矿化水、原油的温度;步骤三、关闭围压阀32、分离阀35、放空阀24、第三阀门38、第四阀门39,打开第一阀门36、第二阀门37,通过真空泵3对微观可视化芯片7进行抽真空;打开放空阀24,进行油相驱替,直至通过可视化窗口21观察不到气泡,使微观可视化芯片7完全饱和,打开围压阀32;步骤四、关闭围压阀32,确保高压密闭夹持器8内部始终维持在地层温度和地层压力,切换矿化水进行驱替,待放空阀24处有连续的矿化水流出时关闭放空阀24,打开围压阀32;步骤五、通过水、油两相的驱替速度、驱替时间与油水分离装置18出口端的产水量、产油量对微观可视化芯片7内的含水饱和度进行计算和检验;步骤六、进行二氧化碳与原油的混相实验,记录微观可视化芯片7中二氧化碳与原油达到混相的过程;步骤七、记录最小混相压力。
[0018]
所述步骤一的具体操作过程为:将微观可视化芯片7安装在高压密闭夹持器8中,加入围压液并使用加热容器10加热至地层温度,由围压泵13和围压阀32监测控制围压,使围压始终高于微观可视化芯片7内部压力2mpa;调节显微镜20位置使微观可视化芯片7在控制系统23屏幕正中央,同时调整放大倍数使摄像监测系统22可清楚的捕捉到微观可视化芯片7内的微纳米尺度通道。
[0019]
所述步骤二的具体操作为:调整回压泵15使微观可视化芯片7达到地层压力,同时将矿化水及原油分别放入活塞容器2进行预加热至地层温度。
[0020]
优选的,所述步骤三中原油的注入速度、步骤四中矿化水的注入速度均不高于0.02ml/min。
[0021]
所述步骤五中,微观可视化芯片7中的含水饱和度计算的具体步骤包括:记录步骤三的油相驱替速度ν
油
、油相驱替时间s
油
;步骤四的水相驱替速度ν
水
、水相驱替时间s
水
;关闭第一阀门36、第二阀门37,打开第三阀门38、第四阀门39、分离阀35,记录油水分离装置18出口端产水量v
产水
以及产油量v
产油
。
[0022]
需要注意的是,当测量原油为稠油(即原油的相对密度大于0.92(20℃)、地下粘度大于50厘泊)时或者原油粘度未知时,在记录v
产水
、v
产油
前,需要对流体输入主管道27中的残油进行二氧化碳驱替,直至油水分离装置18出口端没有液体产出。因为当原油为稠油时,油相会附着在流体输入主管道27管线壁面,影响含水饱和度的计算。
[0023]
计算微观可视化芯片7中含水饱和度s
w1
:式中:s
w1
——微观可视化芯片中含水饱和度,%;v
水
——水相驱替速度,ml/min;s
水
——水相驱替时间,min;v
总
——微观可视化芯片中总的孔隙体积,cm3;v
管
——管线体积,cm3;
计算微观可视化芯片7中的含水饱和度s
w2
:s
w2
——微观可视化芯片中含水饱和度,%;v
水
——水相驱替速度,ml/min;s
水
——水相驱替时间,min;v
产水
——油水分离装置出口端产水量,cm3;v
总
——微观可视化芯片中总的孔隙体积,cm3;计算微观可视化芯片7中的含油饱和度:式中:so——微观可视化芯片中含油饱和度,%;v
油
——油相驱替速度,ml/min;s
油
——油相驱替时间,min;v
产油
——油水分离装置出口端产油量,cm3;v
总
——微观芯片中总的孔隙体积,cm3;上述微观可视化芯片7中的总的孔隙体积为:其中:v
油藏
——第一联通区域的体积,mm3;v
岩石颗粒
——总的基质圆柱体体积,mm3。
[0024]
上述管线体积v
管
为:其中,s
管
——管线内截面面积,cm2;l
管
——管线长度,cm。
[0025]
所述管线长度l
管
指流体输入主管道27的长度。
[0026]
进一步的,所述步骤五中,含水饱和度的检验过程包括:当原油不属于稠油时:若s
w1
so=100%(误差小于0.05%)则说明微观可视化芯片中的含水量结果准确。若检验结果正确,则可以继续进行试验,若不正确则对微观可视化芯片进行清洁烘干之后重复以上步骤,重新进行计算。
[0027]
当原油处于稠油或未知时:如果s
w1
与s
w2
的误差小于0.05%则证明稠油的影响已经可以忽略,此时的含水饱和度计算为准确值。若检验结果正确,则可以继续进行试验,若不正确说明流体输入主管道27的管线内壁附有油相影响了含水饱和度的计算,其准确值应为s
w2
。
[0028]
之所以设置两种计算方法是为了节省计算时间,当已知原油不是稠油时不需要计算s
w2
。如果已知原油粘度是稠油或者原油粘度未知时,则需要探讨油相在管线上的附着对
含水饱和度的影响。对于如何控制微观可视化芯片的含水饱和度,只需要控制水相的驱替时间即可,因为已知总的孔隙体积和管线体积,只需控制注水量即可控制含水饱和度。
[0029]
所述步骤六的具体操作过程为,关闭第三阀门38、第四阀门39;打开第一阀门36、第二阀门37;打开气体增压系统6,同时确保高压密闭夹持器8内部始终维持在地层温度和地层压力。使用摄像监测系统22记录微观可视化芯片7中二氧化碳与原油多次接触从而达到混相的过程。
[0030]
所述步骤七的操作过程包括:当观察到二氧化碳与原油的接触界面消失时停止实验,记录第一压力传感器9的数值,即为最小混相压力。
[0031]
在实验完成后使用石油醚冲刷清洗微观可视化芯片7及管线。打开实时记录的数据及视频文件进行混相实验分析。
[0032]
有益效果:1、本装置采用可视化窗口、微观可视化芯片、显微镜,实现混相过程的实时监控,可直接根据二氧化碳与原油接触界面判断混相阶段,记录最小混相压力,不必再借助采收率的变化来反推最小混相压力。
[0033]
2、本装置采用的微观可视化芯片内设有第二连通区域用于连通驱替系统与油水分离及计量系统,为管线内矿化水的驱除提供通道。第二连通区域的设置可计算管线内残余的原油,减小含水饱和度的误差。
附图说明
[0034]
图1为评价含水饱和度及矿化度对混相压力影响的实验装置;图2为均质多孔介质的微观可视化芯片;图3为制作初始含水饱和度的微观可视化芯片;图4为二氧化碳与原油发生混相时相界面消失的微观可视化芯片;图5为不同含水饱和度对最小混相压力的影响规律;图6为不同矿化度对最小混相压力的影响规律。
[0035]
其中,1为高压注入泵、2为活塞容器、3为真空泵、4为温度传感器、5为二氧化碳气源、6为气体增压系统、7为微观可视化芯片、8为高压密闭夹持器、9为第一压力传感器、10为加热容器、11为循环泵、12为控温阀、13为围压泵、14为第二压力传感器、15为回压泵、16为第三压力传感器、17为冷凝管、18为油水分离装置、19为液体收集及计量装置、20为显微镜、21为可视化窗口、22为摄像监测系统、23为控制系统、24为放空阀、25为泵送管道、26为流体输入分管道、27为流体输入主管道、28为流体加热输出管道、29为流体加热输入管道、30为围压监测管道、31为油水分离管道、32为围压阀、33为输入口、34为输出口、35为分离阀、36为第一阀门、37为第二阀门、38为第三阀门、39为第四阀门,40为第一连通区域,41为第二连通区域,42为基质圆柱体。
具体实施方式
[0036]
实施例一:不同含水饱和度测得的最小混相压力一种评价含水饱和度及矿化度对最小混相压力影响规律的实验装置,如图1、图2所示,包括驱替系统、封闭接触系统、温压调节系统、数据及图像采集系统、油水分离及计量
系统;所述封闭接触系统包括高压密闭夹持器8、微观可视化芯片7,所述微观可视化芯片7置于高压密闭夹持器8的空腔内,所述微观可视化芯片7上设有输入口33和输出口34;所述高压密闭夹持器8上设置可视化窗口21;所述微观可视化芯片7内设有第一连通区域40、第二连通区域41,所述第一连通区域40通过第一阀门36与输入口33连接,所述第一连通区域40通过第二阀门37与输出口34连接;所述第二连通区域41通过第三阀门38与输入口33连接,所述第二连通区域41通过第四阀门39与输出口34连接;所述第一连通区域40设有基质圆柱体42;所述驱替系统包括高压注入泵1、活塞容器2、气体增压系统6、二氧化碳气源5、真空泵3、放空阀24,所述活塞容器2的进口端通过泵送管道25连接高压注入泵1,所述活塞容器2的出口端通过流体输入主管道27连接输入口33,所述流体输入主管道27上设有真空泵3和放空阀24,所述放空阀24位于真空泵3的下游;所述二氧化碳气源5、气体增压系统6依次通过流体输入分管道26并入流体输入主管道27;所述油水分离及计量系统包括分离阀35、回压泵15、冷凝管17、油水分离装置18、液体收集及计量装置19;所述输出口34通过油水分离管道31依次连接分离阀35、回压泵15、冷凝管17、油水分离装置18;所述液体收集及计量装置19用于收集及计量由所述油水分离装置18流出的液体;所述温压调节系统包括加热容器10、循环泵11、控温阀12、围压泵13、围压阀32、温度传感器4、第一压力传感器9、第二压力传感器14、第三压力传感器16,所述加热容器10通过流体加热输出管道28依次连接循环泵11、高压密闭夹持器8,所述高压密闭夹持器8通过流体加热输入管道29依次连接控温阀12、加热容器10,形成循环回路;所述围压泵13通过围压监测管道30依次连接围压阀32、高压密闭夹持器8;所述温度传感器4用于检测活塞容器2内的温度;所述第一压力传感器9设置在流体输入主管道27上,所述第二压力传感器14设置在围压监测管道30上,所述第三压力传感器16设置在油水分离管道31上;所述数据及图像采集系统包括显微镜20、摄像监测系统22、控制系统23;所述显微镜20设置于可视化窗口21的正上方,所述显微镜20用于获取微观可视化芯片7中二氧化碳与原油接触界面的图像;所述摄像监测系统22与控制系统23连接,所述摄像监测系统22用于将显微镜20获取的图像传输给控制系统23,所述温度传感器4、第一压力传感器9、第二压力传感器14、第三压力传感器16都与控制系统23连接。
[0037]
本实施例采用如下步骤对微观可视化芯片7内不同含水饱和度时co
2-原油的混相压力进行测试:步骤一、将微观可视化芯片7安装在高压密闭夹持器8中,使用围压泵13加入围压液至高压密闭夹持器8的空腔充满并使用加热容器10加热至地层温度(150摄氏度),由围压泵13和第二压力传感器14监测控制围压。当压力过小时,围压泵13进行进泵操作,当压力过大时围压泵13进行退泵操作,使围压始终高于微观可视化芯片7内部压力2mpa;调节显微镜20位置使微观可视化芯片7在控制系统23屏幕正中央,同时调整放大倍数使摄像监测系统22可清楚的捕捉到微纳米尺度通道。
[0038]
步骤二、调整回压泵15使其达到地层压力(33mpa),同时将已配好的矿化度为10000mg/l的水和地层原油放入活塞容器2进行预加热至地层温度。
[0039]
步骤三、关闭围压阀32、分离阀35、放空阀24、第三阀门38、第四阀门39,打开第一阀门36、第二阀门37,通过真空泵3对微观可视化芯片7进行抽真空,打开放空阀24,使用高压注入泵1以0.02ml/min的流速进行油相驱替,直至微观可视化芯片7完全饱和,在可视化窗口21中观察不到气泡的存在,打开围压阀32,记录油相驱替速度ν
油
、驱替时间s
油
。
[0040]
步骤四、首先关闭围压阀32,确保高压密闭夹持器8内部始终维持在地层温度(150℃)和地层压力(33mpa)。切换为矿化水进行驱替,高压注入泵1以0.02ml/min的流速进行水相驱替。待放空阀24处有连续的矿化水流出时关闭放空阀24、打开围压阀32。记录水相驱替速度ν
水
、驱替时间s
水
。
[0041]
关闭第一阀门33、第二阀门34;打开第三阀门35、第四阀门36、分离阀35,进行二氧化碳驱替直至油水分离装置18处没有液体产出。在油水分离装置18中根据油水密度差异,油水两相会分层,其中水相在下层,油相在上层。等至完全分层后,将水相从油水分离装置18下部放出,分别统计油水两相的体积产油量v
产油
及产水量v
产水
。
[0042]
步骤五、计算微观可视化芯片7中含水饱和度s
w1
:式中:s
w1
——微观可视化芯片中含水饱和度,%;v
水
——水相驱替速度,ml/min;s
水
——水相驱替时间,min;v
总
——微观可视化芯片中总的孔隙体积,cm3;v
管
——管线体积,cm3。
[0043]
计算微观可视化芯片7中的含水饱和度s
w2
:s
w2
——微观可视化芯片中含水饱和度,%;v
水
——水相驱替速度,ml/min;s
水
——水相驱替时间,min;v
产水
——油水分离装置出口端产水量,cm3;v
总
——微观可视化芯片中总的孔隙体积,cm3;计算微观可视化芯片7中的含油饱和度:式中:so——微观可视化芯片中含油饱和度,%;v
油
——油相驱替速度,ml/min;s
油
——油相驱替时间,min;v
产油
——油水分离装置出口端产油量,cm3;v
总
——微观可视化芯片中总的孔隙体积,cm3;
微观可视化芯片中总的孔隙体积v
总
为:其中:v
油藏
——第一联通区域的体积,mm3;v
岩石颗粒
——总的基质圆柱体体积,mm3。
[0044]
第一联通区域40长40mm,宽40mm,高2mm,油藏体积v
油藏
为3200mm3;共有80*80个基质圆柱体42,底面半径为0.2mm高为2mm,岩石颗粒体积v
岩石颗粒
为1608.5mm3;因而v
总
等于1591.5mm3。
[0045]
上述管线体积v
管
为:其中,s
管
——管线内截面面积,0.0314cm2;l
管
——管线长度,200cm。
[0046]v管
——管线体积,6.28cm3;对测量微观可视化芯片7中的含水量的进行验证:当原油不属于稠油时:若s
w1
so=100%(误差小于0.05%)则说明微观可视化芯片7中的含水量准确。若检验结果正确,则可以继续进行试验,若不正确则对微观可视化芯片7进行清洁烘干之后重复以上步骤,重新进行计算。
[0047]
当原油处于稠油时:如果s
w1
与s
w2
的误差小于0.05%则证明稠油的影响已经可以忽略,此时的含水饱和度计算为准确值。若检验结果正确,则可以继续进行试验,若不正确说明流体输入主管线27内壁附有油相影响了含水饱和度的计算,其准确值应为s
w2
。
[0048]
若验证结果显示微观可视化芯片7中的含水量测量正确则可以继续进行实验,若不正确则对微观可视化芯片7进行清洁烘干之后重复以上步骤,重新进行计算。
[0049]
步骤六、进行二氧化碳与原油的混相实验。关闭第三阀门38、第四阀门39;打开第一阀门36、第二阀门37;打开气体增压系统6及二氧化碳气源5,同时确保高压密闭夹持器8内部始终维持在地层温度和地层压力。使用摄像系统22记录微观可视化芯片7中二氧化碳与原油多次接触从而达到混相的过程。如图3示,该图为具有初始含水饱和度的微观可视化芯片,其中白色为岩石颗粒,较浅的颜色为水相,较深的颜色为油相。油相被水相分割,较为分散的分布在微观可视化芯片中。如图4所示,该图为二氧化碳与原油发生混相时相界面消失的微观可视化芯片,从图中可以观察到油气界面消失,这说明二氧化碳与原油发生混相,此时的压力值即为最小混相压力值。
[0050]
步骤七、当观察到二氧化碳与原油的接触界面消失时停止实验,记录第一压力传感器9的压力为最小混相压力。
[0051]
实验结束后使用石油醚冲刷清洗微观可视化芯片7及管线。打开实时记录的数据及视频文件进行混相实验分析。
[0052]
实验结果如图5所示,随着含水饱和度的增加,二氧化碳与原油的最小混相压力增加,这是因为随着水相的增多,将油相割裂,阻碍了二氧化碳与原油的接触,从而使得最小混相压力增大。
[0053]
实施例二:不同矿化度测得的最小混相压力本实施例采用如下实验例1所述的步骤对微观可视化芯片7内不同矿化度时co
2-原油的混相压力进行测试,其中本实施例的含水饱和度为20%。
[0054]
测试结果为如图6所示,随着矿化度的增加最小混相压力减小,这是由于随着矿化度的增加,使得体系中的离子数增加,从而加速破坏了二氧化碳与油相界面的稳定性。使得二氧化碳更容易与原油混相。使得混相压力降低。
再多了解一些
本文用于企业家、创业者技术爱好者查询,结果仅供参考。