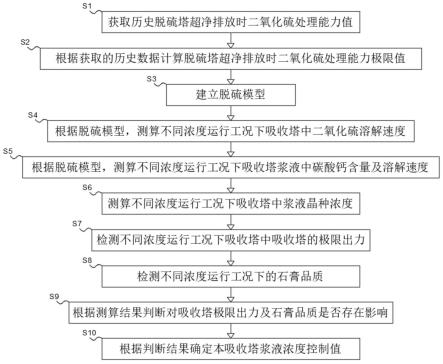
1.本发明涉及脱硫技术领域,尤其涉及一种脱硫吸收塔浆液浓度精确控制方法。
背景技术:
2.脱硫,泛指燃烧前脱去燃料中的硫分以及烟道气排放前的去硫过程。是防治大气污染的重要技术措施之一。目前脱硫方法一般有燃烧前、燃烧中和燃烧后脱硫等三种。随着工业的发展和人们生活水平的提高,对能源的渴求也不断增加,燃煤烟气中的so2已经成为大气污染的主要原因。减少so2污染已成为当今大气环境治理的当务之急。不少烟气脱硫工艺已经在工业中广泛应用,其对各类锅炉和焚烧炉尾气的治理也具有重要的现实意义。其中燃烧后脱硫,又称烟气脱硫(fluegasdesulfurization,简称fgd),在fgd技术中,按脱硫剂的种类划分,可分为以下五种方法:以caco3(石灰石)为基础的钙法,以mgo为基础的镁法,以na2so3为基础的钠法,以nh3为基础的氨法,以有机碱为基础的有机碱法。世界上普遍使用的商业化技术是钙法,所占比例在90%以上。按吸收剂及脱硫产物在脱硫过程中的干湿状态又可将脱硫技术分为湿法、干法和半干(半湿)法。湿法fgd技术是用含有吸收剂的溶液或浆液在湿状态下脱硫和处理脱硫产物,该法具有脱硫反应速度快、设备简单、脱硫效率高等优点,但普遍存在腐蚀严重、运行维护费用高及易造成二次污染等问题。
3.目前,现有的吸收塔在工作时,无法精确控制吸收塔浓度,导致控制的浓度偏高,使得整个脱硫系统出现故障,导致脱硫系统内设备的磨损增加,用电量增加,影响石膏的品质,为此我们提出一种脱硫吸收塔浆液浓度精确控制方法来解决上述问题。
技术实现要素:
4.本发明的目的是为了解决现有技术中存在无法精确控制吸收塔浓度,导致控制的浓度偏高,使得整个脱硫系统出现故障,导致脱硫系统内设备的磨损增加,用电量增加,影响石膏的品质的问题,而提出的一种脱硫吸收塔浆液浓度精确控制方法。
5.为了实现上述目的,本发明采用了如下技术方案:
6.一种脱硫吸收塔浆液浓度精确控制方法,包括如下步骤:
7.获取历史脱硫塔超净排放时二氧化硫处理能力值;
8.根据获取的历史数据计算脱硫塔超净排放时二氧化硫处理能力极限值;
9.建立脱硫模型;
10.根据脱硫模型,测算不同浓度运行工况下吸收塔中二氧化硫溶解速度;
11.根据脱硫模型,测算不同浓度运行工况下吸收塔浆液中碳酸钙含量及溶解速度;
12.测算不同浓度运行工况下吸收塔中浆液晶种浓度;
13.检测不同浓度运行工况下吸收塔中吸收塔的极限出力;
14.检测不同浓度运行工况下的石膏品质;
15.根据测算结果判断对吸收塔极限出力及石膏品质是否存在影响;
16.根据判断结果确定本吸收塔浆液浓度控制值。
17.优选地,建立脱硫模型,包括二氧化硫溶解模型和碳酸钙含量及溶解速度模型。
18.优选地,所述二氧化硫溶解模型的建立步骤如下:
19.确定浆液中二氧化硫的扩散传质过程;
20.确定总四价硫在浆液中变化;
21.确定总六价硫在浆液中变化;
22.确定总钙在浆液中变化;
23.确定总碳浓度分布在浆液中变化;
24.计算浆液中电荷平衡;
25.确定浆液中的化学反应平衡常数。
26.优选地,测算不同浓度运行工况下吸收塔中浆液晶种浓度;
27.当吸收塔浆液浓度大于到11.04%时,吸收塔晶种浓度不影响脱硫极限出力能力;吸收塔浓度小于10.1%时,吸收塔极限出力能力下降。
28.优选地,根据测算结果判断对吸收塔极限出力及石膏品质是否存在影响;
29.判断caso4·
2h2o含量是否小于93%,超过时存在影响。
30.优选地,根据判断结果确定本吸收塔浆液浓度控制值;
31.不存在影响时,吸收塔浓度控制在12%-15%之间;
32.存在影响时,调整吸收塔浓度在12%-15%之间。
33.一种脱硫吸收塔浆液浓度精确控制装置,包括:
34.历史数据获取模块:用于获取历史脱硫塔超净排放时二氧化硫处理能力值;
35.极限值计算模块:用于根据获取的历史数据计算脱硫塔超净排放时二氧化硫处理能力极限值;
36.模型建立模块:用于建立脱硫模型;
37.二氧化硫溶解速度测算模块:用于根据脱硫模型,测算不同浓度运行工况下吸收塔中二氧化硫溶解速度;
38.含量及溶解速度测算模块:用于根据脱硫模型,测算不同浓度运行工况下吸收塔浆液中碳酸钙含量及溶解速度;
39.晶种浓度测算模块:用于测算不同浓度运行工况下吸收塔中浆液晶种浓度;
40.极限出力检测模块:用于检测不同浓度运行工况下吸收塔中吸收塔的极限出力;
41.石膏品质检测模块:用于检测不同浓度运行工况下的石膏品质;
42.判断模块:用于根据测算结果判断对吸收塔极限出力及石膏品质是否存在影响;
43.浓度确定模块:用于根据判断结果确定本吸收塔浆液浓度控制值。
44.优选地,所述模型建立模块包括:
45.传质过程确定单元:用于确定浆液中二氧化硫的扩散传质过程;
46.总四价硫确定单元:用于确定总四价硫在浆液中变化;
47.总六价硫确定单元:用于确定总六价硫在浆液中变化;
48.总钙确定单元:用于确定总钙在浆液中变化;
49.总碳浓度分布确定单元:用于确定总碳浓度分布在浆液中变化;
50.电荷平衡计算单元:用于计算浆液中电荷平衡;
51.平衡常数确定单元:用于确定浆液中的化学反应平衡常数。
52.相比现有技术,本发明的有益效果为:
53.本发明通过整体方法的实施,能够精确控制吸收塔浓度,使得控制的浓度达到使用标准,对整个脱硫系统进行了良好的保护,防止脱硫系统内设备的磨损增加,节约了用电量,同时保证了石膏的品质,防止石膏过饱和度越高,造成石膏在各处沉降,从而造成恶性循环,延长了整个脱硫系统的使用寿命,节约了资源,方便人员使用,值得推广。
附图说明
54.图1为本发明提出的一种脱硫吸收塔浆液浓度精确控制方法的整体流程示意图;
55.图2为本发明提出的一种脱硫吸收塔浆液浓度精确控制方法的二氧化硫溶解模型的建立步骤流程示意图;
56.图3为本发明提出的一种脱硫吸收塔浆液浓度精确控制方法的ph值不在变化时石灰石最小含量曲线示意图;
57.图4为本发明提出的一种脱硫吸收塔浆液浓度精确控制方法的不同石灰石含量下能够达到最大ph值曲线示意图;
58.图5为本发明提出的一种脱硫吸收塔浆液浓度精确控制方法的不同浆液浓度对吸收塔出力影响的曲线示意图;
59.图6为本发明提出的一种脱硫吸收塔浆液浓度精确控制方法的不同浆液浓度对石膏纯度的影响曲线示意图。
具体实施方式
60.下面将结合本发明实施例中的附图,对本发明实施例中的技术方案进行清楚、完整地描述,显然,所描述的实施例仅仅是本发明一部分实施例,而不是全部的实施例。
61.参照图1-6,一种脱硫吸收塔浆液浓度精确控制方法,包括如下步骤:
62.s1:获取历史脱硫塔超净排放时二氧化硫处理能力值;
63.脱硫塔超净排放时so2处理能力极限值(实际运行计算))如下:
[0064][0065]
s2:根据获取的历史数据计算脱硫塔超净排放时二氧化硫处理能力极限值,计算公式为:脱除的二氧化硫的量=耗煤量
×
含硫量
×
2倍燃烧率
×
脱硫率;
[0066]
s3:建立脱硫模型,包括二氧化硫溶解模型和碳酸钙含量及溶解速度模型;
[0067]
二氧化硫溶解模型的建立步骤如下:
[0068]
s301:确定浆液中二氧化硫的扩散传质过程,二氧化硫在浆液表面被吸收,传质通量的方程式为:
[0069]
其中,
[0070]
kg根据frossling方程及气相扩散系数公式确定:
[0071][0072][0073]
由上式可得
[0074]
s302:确定总四价硫在浆液中变化,公式如下:
[0075][0076]
s303:确定总六价硫在浆液中变化,忽略浆液在下落过程中的自然氧化和caso的结晶和溶解过程,因此s(vi)的总量不变,只考虑和由于浆液中ph值的变化引起的相互转化及其对浆滴ph值的影响;
[0077]
s304:确定总钙在浆液中变化,公式如下:
[0078][0079]
s305:确定总碳浓度分布在浆液中变化,公式如下:
[0080][0081]
s306:计算浆液中电荷平衡;
[0082][0083]
s307:确定浆液中的化学反应平衡常数;
[0084][0085][0086]
碳酸钙含量及溶解速度模型,计算式为:
[0087]
[0088][0089]
式中,为传质通量;为烟气中二氧化硫的分压;为浆液中二氧化硫浓度;kg为气膜吸收系数;为二氧化硫的溶解度系数;为化学反应增强因子;ud为浆液下落速度;ug为烟气下落速度;ρd为浆液密度;ρg为烟气密度;d为直径;l为下落高度;t为下落时间;μg为烟气粘度;cd为拽力系数;red为浆液雷诺准数;kg为气相总吸收系数;q烟气流量;为烟气中二氧化硫的物质的量;sh为施伍德准数;a为单位体积浆液亚硫酸钙的表面积;c.浆液各组分的浓度;为二氧化硫在烟气中的扩散系数;sc施密特准数;m
air
为空气的分子量;为二氧化硫的分子量;为二氧化硫的分子体积;v
air
为空气的分子体积;d
l
为二氧化硫在浆液中的扩散系数;t
p
为表面暴露时间;为碳酸钙的溶解速率;为碳酸钙的结晶速率常数;为亚硫酸钙的溶解速率;为亚硫酸钙的过饱和度;为碳酸钙的过饱和度;为硫酸钙的过饱和度;k
cp
为碳酸钙的溶度积;k
sp1
为亚硫酸钙的溶度积;k
sp2
为硫酸钙的溶度积;
[0090]
s4:根据脱硫模型,测算不同浓度运行工况下吸收塔中二氧化硫溶解速度;
[0091]
s5:根据脱硫模型,测算不同浓度运行工况下吸收塔浆液中碳酸钙含量及溶解速度;
[0092]
s6:测算不同浓度运行工况下吸收塔中浆液晶种浓度;
[0093]
当吸收塔浆液浓度大于到11.04%时,吸收塔晶种浓度不影响脱硫极限出力能力;吸收塔浓度小于10.1%时,吸收塔极限出力能力下降;
[0094]
s7:检测不同浓度运行工况下吸收塔中吸收塔的极限出力;
[0095]
s8:检测不同浓度运行工况下的石膏品质;
[0096]
s9:根据测算结果判断对吸收塔极限出力及石膏品质是否存在影响;
[0097]
实际运行中无法实时监测石膏颗粒度,主要考虑石膏品质对石膏销售的影响,同时考虑浆液浓度对吸收塔处理能力的影响,一般石膏生产企业所需石膏品质要求如下:
[0098][0099][0100]
判断caso4·
2h2o含量是否小于93%,超过时存在影响;
[0101]
s10:根据判断结果确定本吸收塔浆液浓度控制值;
[0102]
不存在影响时,吸收塔浓度控制在12%-15%之间;
[0103]
存在影响时,调整吸收塔浓度在12%-15%之间。
[0104]
一种脱硫吸收塔浆液浓度精确控制装置,包括:
[0105]
历史数据获取模块:用于获取历史脱硫塔超净排放时二氧化硫处理能力值;
[0106]
极限值计算模块:用于根据获取的历史数据计算脱硫塔超净排放时二氧化硫处理能力极限值,计算公式为:脱除的二氧化硫的量=耗煤量
×
含硫量
×
2倍燃烧率
×
脱硫率;
[0107]
模型建立模块:用于建立脱硫模型;
[0108]
二氧化硫溶解速度测算模块:用于根据脱硫模型,测算不同浓度运行工况下吸收塔中二氧化硫溶解速度;
[0109]
含量及溶解速度测算模块:用于根据脱硫模型,测算不同浓度运行工况下吸收塔浆液中碳酸钙含量及溶解速度;
[0110]
晶种浓度测算模块:用于测算不同浓度运行工况下吸收塔中浆液晶种浓度;
[0111]
极限出力检测模块:用于检测不同浓度运行工况下吸收塔中吸收塔的极限出力;
[0112]
石膏品质检测模块:用于检测不同浓度运行工况下的石膏品质;
[0113]
判断模块:用于根据测算结果判断对吸收塔极限出力及石膏品质是否存在影响;
[0114]
浓度确定模块:用于根据判断结果确定本吸收塔浆液浓度控制值。
[0115]
其中,模型建立模块包括:
[0116]
传质过程确定单元:用于确定浆液中二氧化硫的扩散传质过程,二氧化硫在浆液表面被吸收,传质通量的方程式为:
[0117]
其中,
[0118]
kg根据frossling方程及气相扩散系数公式确定:
[0119][0120][0121]
由上式可得
[0122]
总四价硫确定单元:用于确定总四价硫在浆液中变化,公式如下:
[0123][0124]
总六价硫确定单元:用于确定总六价硫在浆液中变化,忽略浆液在下落过程中的自然氧化和caso的结晶和溶解过程,因此s(vi)的总量不变,只考虑和由于浆液中ph值的变化引起的相互转化及其对浆滴ph值的影响;
[0125]
总钙确定单元:用于确定总钙在浆液中变化,公式如下:
[0126][0127]
总碳浓度分布确定单元:用于确定总碳浓度分布在浆液中变化,公式如下:
[0128][0129]
电荷平衡计算单元:用于计算浆液中电荷平衡;
[0130][0131][0132][0133]
碳酸钙含量及溶解速度模型,计算式为:
[0134][0135][0136]
式中,为传质通量;为烟气中二氧化硫的分压;为浆液中二氧化硫浓度;kg为气膜吸收系数;为二氧化硫的溶解度系数;为化学反应增强因子;ud为浆液下落速度;ug为烟气下落速度;ρd为浆液密度;ρg为烟气密度;d为直径;l为下落高度;t为下落时间;μg为烟气粘度;cd为拽力系数;red为浆液雷诺准数;kg为气相总吸收系数;q烟气流量;为烟气中二氧化硫的物质的量;sh为施伍德准数;a为单位体积浆液亚硫酸钙的表面积;c.浆液各组分的浓度;为二氧化硫在烟气中的扩散系数;sc施密特准数;m
air
为空气的分子量;为二氧化硫的分子量;为二氧化硫的分子体积;v
air
为空气的分子体积;d
l
为二氧化硫在浆液中的扩散系数;t
p
为表面暴露时间;为碳酸钙的溶解速率;为碳酸钙的结晶速率常数;为亚硫酸钙的溶解速率;为亚硫酸钙的过饱和度;为碳酸钙的过饱和度;为硫酸钙的过饱和度;k
cp
为碳酸钙的溶度积;k
sp1
为亚硫酸钙的溶度积;k
sp2
为硫酸钙的溶度积;
[0137]
平衡常数确定单元:用于确定浆液中的化学反应平衡常数。
[0138]
一种智能计算机设备,包括存储器和处理器,所述存储器中存储有计算机可读指令,所述处理器执行所述计算机可读指令时实现如所述的脱硫吸收塔浆液浓度精确控制方法的步骤。
[0139]
一种计算机可读存储介质,所述计算机可读存储介质上存储有计算机可读指令,所述计算机可读指令被处理器执行时实现如所述的脱硫吸收塔浆液浓度精确控制方法的步骤。
[0140]
以上所述,仅为本发明较佳的具体实施方式,但本发明的保护范围并不局限于此,
任何熟悉本技术领域的技术人员在本发明揭露的技术范围内,根据本发明的技术方案及其发明构思加以等同替换或改变,都应涵盖在本发明的保护范围之内。
再多了解一些
本文用于企业家、创业者技术爱好者查询,结果仅供参考。