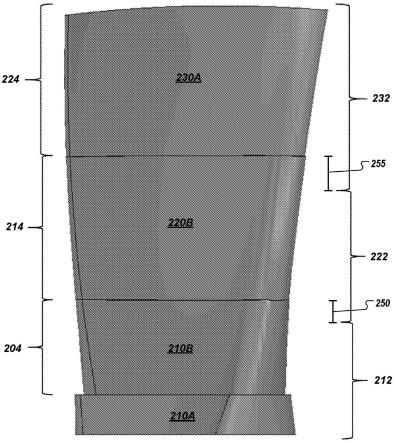
混合增材和减材制造
1.相关申请的交叉引用
2.本技术要求2019年9月18日提交的名称为“hybrid additive and subtractive manufacturing with stainless steel and nickel alloy(不锈钢和镍合金的混合增材和减材制造)”的美国专利申请号62/902,320的优先权权益。
3.关于赞助研究或开发的声明
4.产生本技术的项目已经在第723538号拨款协议下收到欧盟horizon 2020研究和创新计划的资助。
背景技术:
5.本说明书涉及使用增材和减材制造系统和技术对物理结构的计算机辅助设计和制造。
6.已经开发出计算机辅助设计软件和计算机辅助制造软件,并且使用所述计算机辅助设计软件和计算机辅助制造软件来生成零件的三维(3d)表示并例如使用计算机数控(cnc)制造技术来制造那些零件的物理结构。此外,增材制造,还称为实体自由成形制造或3d打印,是指在一系列二维层或横截面中由原始材料(一般是粉末、液体、悬浮液或熔融固体)构建3d零件的任何制造过程。增材制造的示例是熔融长丝制造(fff)。3d挤压打印机通常使用fff来以层的形式放下从线圈展开的材料(诸如塑料长丝或金属丝线),以生产3d打印零件。
7.另外,减材制造是指通过切除物料(一般是大于3d零件的“坯件”或“工件”)的部分而由所述物料产生3d零件的任何制造过程。此类制造过程通常涉及在一系列操作中使用多个cnc机器切削工具,所述一系列操作始于粗加工操作、任选的半精加工操作和精加工操作。在粗加工操作期间,使用cnc机械加工系统的切削工具快速地(相对于半精加工操作和精加工操作)切除工件的大部分,以便接近所制造的零件的最终形状。另外,已经开发出组合了增材和减材制造的混合制造系统,诸如将激光金属沉积与高精度5轴自适应铣削进行组合的cnc机器。
技术实现要素:
8.本说明书描述了与使用混合增材和减材制造系统和技术对物理结构的计算机辅助设计和制造相关的技术。
9.一般来说,在本说明书中描述的主题的一个或多个方面可在一种或多种方法中体现,所述方法包括:获得要通过包括增材制造工具和减材制造工具的混合增材和减材制造系统使用包括一系列两个或更多个阶段的制造过程由材料制造的零件的三维几何形状的数据,所述两个或更多个阶段中的每一者包括用增材制造工具添加材料以及用减材制造工具移除材料;根据所述数据和所述材料的物理性质来模拟所述制造过程的至少一部分,所述至少一部分包括在所述两个或更多个阶段中的第一阶段中使用增材制造工具来添加第一材料,以及在所述两个或更多个阶段中的第二阶段中使用减材制造工具来移除第二材
料,其中第一阶段在第二阶段之前,其中第二材料包括第一材料的一部分,其中移除第二材料包括在第一阶段和第二阶段中添加的材料之间进行混合,并且其中所述模拟包括模拟在第一阶段和第二阶段中添加和移除材料的热效应;根据材料的物理性质基于所述模拟的结果来调整第二材料中包括的第一材料的所述部分的量,以防止零件在制造过程的部分期间偏离三维几何形状,所述偏离会导致没有足够的材料可用于混合;以及提供经调整的量以用于通过混合增材和减材制造系统制造零件。
10.所述制造过程的部分可包括在所述两个或更多个阶段中的第二阶段中使用增材制造工具来添加第三材料,以及在所述两个或更多个阶段中的第一阶段中使用减材制造工具移除第四材料,其中第一材料包括第四材料,第二材料包括第三材料的一部分,模拟包括模拟至少在移除第二材料期间经历的振动,并且所述方法包括响应于振动过高而修改两个或更多个层以及因此修改所述两个或更多个阶段。模拟振动可包括基于预测的切削力和动态响应而模拟切削期间的不稳定性。
11.调整第二材料中包括的第一材料的部分的量可包括相对于零件的三维几何形状增加要在所述两个或更多个阶段中的第一阶段中使用增材制造工具添加的第一材料的过度构建量。
12.所述制造过程的部分可包括在所述两个或更多个阶段中的第二阶段中使用增材制造工具来添加第三材料,以及在所述两个或更多个阶段中的第一阶段中使用减材制造工具来移除第四材料,其中第一材料包括第四材料,第二材料包括第三材料的一部分,并且调整第二材料中包括的第一材料的部分的量包括减小第四材料的量并增加第二材料中包括的第一材料的部分。
13.所述零件可以是涡轮转子,所述涡轮转子包括被设计成在高温环境中操作的毂和叶片,并且模拟可包括模拟在所述两个或更多个阶段中在被包括作为毂的一体部分的叶根的顶部上使用增材制造工具构建的叶片的机械加工。
14.所述方法可包括用混合增材和减材制造系统制造零件。所述混合增材和减材制造系统可包括一个或多个计算机处理设备,所述一个或多个计算机处理设备包括至少一个非暂时性计算机可读介质,所述至少一个非暂时性计算机可读介质对计算机辅助设计程序进行编码,所述计算机辅助设计程序可操作以执行获得、模拟、调整、提供和制造。
15.所描述的方法可使用对指令进行编码的非暂时性计算机可读介质,所述指令可操作以致使数据处理设备执行所述方法的操作。另外,系统实施方式可包括数据处理设备(包括至少一个硬件处理器)和对实施所述方法的计算机辅助设计程序的指令进行编码的非暂时性计算机可读介质。最后,所述系统实施方式可包括混合增材和减材制造系统,并且计算机辅助设计程序的指令可被配置为致使数据处理设备用混合增材和减材制造系统来制造零件。
16.可实施在本说明书中描述的主题的特定实施方案以实现以下优点中的一或多者。在相应的增材加减材制造阶段中以一系列层构建结构允许使用较短和/或更常规的工具,这降低了复杂结构的制造成本。可以使用来自增材和减材制造的组合的数值模拟的反馈来更改制造计划,以便改进制造过程和/或改进所制造的结构的质量。
17.可修改制造阶段的数目和/或在阶段内和在阶段之间的增材减材制造之间的重叠,以防止增材沉积期间的不期望的不稳定性和变形,确保机械加工期间的统一材料移除
和/或提供减材机械加工期间的相对于振动和机械加工动力学的稳定性。可使用在此文献中描述的系统和技术来避免在减材制造期间的过高振动(这可能会损坏工件和/或工具),例如通过切削力和数值模拟所使用的动态预测模型来告知所述过高振动,因此避免了零件不准确性、工具损坏/破裂,以及潜在地不得不完全报废工件。
18.可基于所构建的零件、可用工具的长度和强度以及制造过程的数值模拟(例如,切削工具的长度和强度和因此在减材制造期间的预期振动量)和最小化由增材制造与减材制造之间的转变而导致的制造中断的期望来修改混合制造阶段的数目(和/或由混合制造阶段覆盖的距离)以及调整在每个阶段中要完成的相应的增材制造和减材制造的量。使用在此文献中描述的混合阶段式制造系统和技术可导致用于构建零件的材料的减少、制造零件所需的机器时间的减少。可在单设置混合生产过程中实现这些和其他优势。
19.另外,阶段式混合方法有助于使用更常规的工具(更硬且现成的)而不是专用的工具(长、细且昂贵)。这意味着原本在设计和采购专用工具上花费的资源可花费在制造自身上,从而提高了生产率。此外,使用在此文献中描述的模拟支持式数字工作流可减少对专业知识的需要和复杂制造项目中的猜测工作。
20.在附图和以下描述中陈述了在本说明书中所描述的主题的一个或多个实施方案的细节。本发明的其他特征、方面及优点将从描述、附图和权利要求书变得显而易见。
附图说明
21.图1示出了可用于使用混合增材和减材制造来设计和制造物理结构的系统的示例。
22.图2a和图2b示出了使用混合增材和减材制造而制造的叶片的构建序列的示例。
23.图2c示出了在混合增材和减材制造期间的增材制造过程中的过度构建的示例。
24.图3a示出了基于结构的混合增材和减材制造的数值模拟而更改制造计划的过程的示例。
25.图3b至图3e示出了可在图3a的混合增材和减材制造计划过程中实施的详细示例。
26.图4是可用于实施所描述的系统和技术的数据处理系统的示意图。
27.各个附图中的相同参考数字和标示指示相同元件。
具体实施方式
28.图1示出了可用于使用混合增材和减材制造来设计和制造物理结构的系统100的示例。计算机110包括处理器112和存储器114,并且计算机110可连接到网络140,所述网络可以是专用网络、公共网络、虚拟专用网络等。处理器112可以是一个或多个硬件处理器,每个硬件处理器可包括多个处理器核心。存储器114可包括易失性存储器和非易失性存储器两者,诸如随机存取存储器(ram)和闪存ram。计算机110可包括各种类型的计算机存储介质和装置,它们可包括存储器114以存储在处理器112上运行的程序的指令。
29.此类程序包括一个或多个三维(3d)建模、模拟(有限元分析或其他)和/或制造控制程序,诸如计算机辅助设计(cad)程序116,所述计算机辅助设计程序模拟增材和减材制造的组合并且调整制造计划(在结构/物体的3d建模期间和/或在从3d模型生成工具路径规格期间)以改进结构/物体的混合增材和减材制造。如本文使用,“cad”是指用于设计物理结
构的制造计划的任何合适的程序,而不管所述程序是否能够与制造设备介接和/或控制制造设备来构建物理结构,并且不管所述程序是否可用于设计满足设计要求的物理结构。因此,cad程序116可包括计算机辅助工程设计(cae)程序、计算机辅助制造(cam)程序、建筑、工程与建设(aec)程序等。
30.cad程序116可在本地运行在计算机110上,远程地运行在一个或多个远程计算机系统150(例如,可由计算机110经由网络140访问的一个或多个第三方提供商的一个或多个服务器系统)的计算机上,或者在本地和远程地运行两者。因此,cad程序116可以是在两个或更多个单独的计算机处理器上协作地操作的两个或更多个程序,其中在本地在计算机110处操作的一个或多个程序116可通过使一个或多个计算机150上的一个或多个程序116执行卸载处理操作来“向云”卸载处理操作(例如,数值模拟操作)。
31.cad程序116在计算机110的显示装置120上呈现用户界面(ui)122,可使用计算机110的一个或多个输入装置118(例如,键盘和鼠标)来操作所述用户界面。应注意,虽然在图1中示出为单独装置,但显示装置120和/或输入装置118还可彼此集成和/或与计算机110集成,诸如集成在平板计算机中或虚拟现实(vr)或增强现实(ar)系统中。例如,输入/输出装置118、120可包括vr输入手套118a和vr耳机120a。
32.用户190可与cad程序116交互以创建和/或加载要使用混合增材和减材制造系统制造的零件的3d模型132(例如,在文献130中和/或来自所述文献),所述混合增材和减材制造系统可包括一个或多个计算机数控(cnc)制造机器170。这可使用已知的图形用户界面工具来进行,并且可在计算机中使用各种已知的3d建模格式,诸如使用实体模型(例如,体素)或表面模型(例如,b-rep(边界表示)和表面网格),来限定3d模型132。另外,在一些实施方式中,用户190可在需要时与程序116交互以修改零件的3d模型132。
33.在所示的示例中,模型132是特定涡轮叶轮的3d模型,但许多不同类型的模型可与在此文献中描述的系统和技术一起使用。一般来说,所描述的系统和技术更适用于制造包括高结构并且所述高结构之间具有少量空间的部件,诸如用于航空航天或发电应用的叶盘或涡轮叶轮的叶片(或转子上的轮叶),其中比较叶片的高度,它们常常挨在一起。在此文献中描述的混合制造涉及在相应的制造阶段中以一系列层构建此类结构,其中每个阶段包括沉积材料和移除材料两者,这意味着当制造挨在一起的叶片时可使用较短的工具,因为仅需要跨越当前层的高度而不是整个叶片的高度。然而,尽管对制造其间具有有限量的空间的高结构有这种特定适用性,所描述的系统和技术还可更一般地应用于要使用cad程序和混合增材和减材制造来设计和制造的各种类型的结构。
34.在一些实施方式中,混合增材和减材制造系统是单个cnc机器170,所述单个cnc机器包括减材制造(sm)工具172和增材制造(am)工具176,所述工具可以是可移除的和/或具有可移除的工具头部。将了解,存在可在cnc机器170中可用的许多不同类型的切削工具172,包括具有各种球头、锥形、尖端半径和筒形的铣刀工具。这些不同的切削工具172可包括产生工具172的不同切削表面几何形状的具有不同直径和尖端半径的整体工具(例如,整体硬质合金圆工具)和/或产生工具172的不同切削表面形状的具有不同直径和金属(例如,硬质合金)镶嵌件的镶嵌工具。可按照工具系列布置这些不同的工具172,其中工具系列具有一个或多个共享的工具特性(例如,整体硬质合金圆工具的系列172a具有产生不同切削表面几何形状的不同直径和尖端半径,并且镶嵌工具的系列172b具有产生不同切削表面几
何形状的不同直径和金属镶嵌件)。另外,cnc机器170可包括其他部件和系统,诸如可旋转平台/附接件(例如,针对五轴铣削过程)以及清洁与冷却系统(例如,喷洒水清洁与冷却系统)。
35.此外,各种不同类型的am工具176在cnc机器170中可以是可用的。例如,cnc机器170可包括采用颗粒增材制造技术(诸如选择性激光烧结(sls)或直接金属激光烧结(dmls))的一个或多个am工具176。作为另一示例,cnc机器170可包括采用挤压技术(例如,熔融长丝制造(fff))的一个或多个am工具176。其他am系统和技术也是可用的,诸如将定向能量沉积(ded)用作金属增材过程,其中电源可以是电弧、激光或电子束。另外,am工具176可被设计成使用粉末或线材进料。
36.在一些实施方式中,混合增材和减材制造系统是由可彼此相同或不同的两个或更多个cnc机器组成。在一些情况下,sm工具172和am工具176保持在单独的cnc机器中,而不是在单个机器中组合。因此,机器170可以是不包括am工具176的具有切削工具172的cnc sm机器。但不管cnc机器170是否包括am工具176,cnc机器170的sm工具172可提供多轴和多工具铣削能力。
37.单独的cnc am机器174可包括am工具176。例如,am机器174可包括激光器174a(例如,co2激光器)和扫描仪174b(例如,电流计或旋转多边镜),以使用粉末递送和活塞机构(未示出)在粉末床174c中构建半成品结构。替代地,激光器174a可附接到2.5轴、3轴或更多轴运动控制装置,以使用粉末或线材进料在指定位置处执行激光熔覆。将了解,将单独的cnc机器用于sm工具和am工具的实施方式可需要额外的步骤或装置以将工件从一个机器转移到另一机器,诸如在单独的cnc机器170、174之间移动工件的零件搬运机器人。替代地,此类实施方式可使用单独的cnc机器170、174共享访问的共同工件平台。
38.因此,不管混合增材和减材制造系统是单个am sm机器170还是单独的am与sm机器174、170,都可采用单设置混合生产过程,即,工件可一次固定到工作托盘(或工件被夹持到的其他物体,或另外保持固定在原位),并且然后可对工件执行制造阶段序列(其中有sm操作加am操作中的每一者),以从工件形成期望的零件,而不必在制造阶段序列期间松开工件。例如,单个am sm机器170可包括在由德国梅德的hamuel maschinenbau gmbh&co.kg(或另一公司)提供的混合机器中的由瑞士b
ü
ron的erowa ag(或另一公司)提供的夹具托盘系统和夹持系统,所述混合机器包括过程中测量装置。关于混合增材和减材制造系统的更多细节,参见在此以引用的方式并入的美国专利号us20160221122a1、us20170129180a1和us20portion 200086424a1。尽管要使用的制造系统有这些潜在的变化,在此文献中描述的由cad程序116实施的系统和技术仍适用于要用于混合am sm制造的机器的数目(和其能力)上的这些变化。
39.如上文所述,cad程序116模拟增材和减材制造的组合,并且调整制造计划以改进对结构/物体的混合增材和减材制造。具体地,可执行用于在增材和减材制造过程期间构建结构的一种或多种材料的一个或多个物理性质的数值模拟,以提供用于调整增材和减材制造操作的混合和匹配的反馈。应注意,所作出的调整可包括修改结构/物体的3d模型和/或修改从结构/物体的3d模型生成的工具路径规格(针对am、sm或以上两者)。
40.在所示的示例中,3d模型132是叶盘180的3d模型,所述叶盘是要使用混合增材和减材制造系统构建的物理物体。叶盘180包括多个叶片,比较叶片的高度,所述多个叶片挨
在一起。例如,叶片可以是120毫米长,并且在叶片的顶部处彼此相隔9毫米左右的距离,并且在叶片与叶盘180的毂连接的地方相隔约2毫米的距离。因此,从增材制造的工件铣削叶盘180可能需要专用的切削工具,所述专用的切削工具要足够长且足够薄以触及叶盘180的设计中的所有缝隙。
41.但较长和较薄的切削工具一般会产生更多的振动,这可能使机械加工过程不稳定,可能产生需要使用更精加工的操作来清理的擦痕,并且可能导致更多的工具破损。此问题的一个解决方案是由不那么振动的更强、更特殊的材料构建切削工具,但这增加了成本。应注意,机器工具越长和越薄,其引入的振动往往越多,这导致更多的工具破损和对所制造的零件造成损坏的可能性更高,或在更谨慎地使用机器工具以避免工具破损和损坏零件时导致较慢的制造。
42.另一解决方案是在相应的制造阶段中以一系列层构建叶盘180的叶片,其中每个阶段包括使用am工具176沉积材料和使用sm工具172移除材料两者。这允许将更短和/或更常规的工具用于制造,这降低了成本。另外,使用在此文献中描述的系统和技术可在构建零件时防止am过程和/或sm过程期间的不稳定性和不期望的变形。
43.图2a示出了使用混合增材和减材制造在一系列三个层中制造的叶片的构建序列的示例。毂部分200表示将在其上制造叶片的结构的一部分。毂部分200可以是先前例如通过铸造或模锻(热或冷)和/或通过对起始材料块执行的传统的sm粗加工操作制造的零件,或者毂部分200可使用在混合增材和减材制造系统中包括的一个或多个am工具和一个或多个sm工具来制造。在任何情况下,叶片的第一层210是通过使用混合增材和减材制造系统中的一个或多个am工具的沉积过程204来构建(例如,使用具有1kw纤维激光源的激光头和测量系统176,其使用来自粉末供应系统的熔化金属粉末来构建第一层210)。
44.然后,使用混合增材和减材制造系统中的一个或多个sm工具来执行机械加工过程212(例如,使用与自适应铣削同时进行的高精度和动态5轴机械加工)。应注意,机械加工过程212覆盖毂部分200的一部分和所制造的叶片的第一层210的一部分,从而产生部分机械加工的毂部分200a(或在进行先前机械加工的情况下是完全机械加工的毂部分200a)和叶片的部分机械加工的第一层210a。因此,机械加工过程212以最低程度将第一层210混合到毂部分200中。
45.然而,在一些实施方式中,机械加工过程212覆盖更多(或全部)的毂部分200。即使如此,机械加工过程212应仅覆盖第一层210的部分,从而留下第一层210的在其上要构建下一层的某个未精加工部分。机械加工过程212可包括半精加工操作和精加工操作两者。在一些实施方式中,机械加工过程212包括对叶片的第一层210的整体和毂部分200的至少一部分进行半精加工,接着对毂部分200的所述至少一部分和第一层210的仅一部分进行精加工,因此留下第一层210的在其上要构建下一层的某一未精加工部分。在一些实施方式中,机械加工过程212包括对叶片的第一层210的第一部分和毂部分200的至少一部分进行半精加工,接着对毂部分200的所述至少一部分和第一层210的仅第二部分进行精加工,其中第二部分小于第一部分,因此留下在第一层210的第一部分上方的在其上要构建下一层的未精加工(粗加工的)部分,并且还留下在第二部分上方的第一层210的未精加工部分以促进后续的机械加工操作,包括在叶片的不同层之间进行混合。
46.通过使用混合增材和减材制造系统中的一个或多个am工具的沉积过程214在部分
机械加工的第一层210a的顶部上构建叶片的第二层220。然后使用混合增材和减材制造系统中的一个或多个sm工具来执行机械加工过程222。机械加工过程222以最低程度将第二层220混合到部分机械加工的第一层210a中,并且因此机械加工过程222可完成叶片的第一层的制造,从而产生经完全机械加工的第一层210b。
47.但机械加工过程222仅覆盖所制造的叶片的第二层220的一部分,从而产生叶片的部分机械加工的第二层220a,并且留下第二层220的在其上要构建下一层的某一未精加工部分。与机械加工过程212一样,机械加工过程222可包括半精加工操作和精加工操作两者。在一些实施方式中,机械加工过程222包括对第二层220的整体和部分机械加工的第一层210a的一部分进行半精加工,接着对部分机械加工的第一层210a的所述部分和第二层220的仅一部分进行精加工,因此留下第二层220的在其上要构建下一层的某个未精加工部分。在一些实施方式中,机械加工过程222包括对第二层220的第一部分和部分机械加工的第一层210a的一部分进行半精加工,接着对部分机械加工的第一层210a的所述部分和第二层220的仅第二部分进行精加工,其中第二部分小于第一部分,因此留下在第二层220的第一部分上方的在其上要构建下一层的未精加工(粗加工)部分,并且还留下在第二部分上方的第二层220的未精加工部分以促进后续的机械加工操作,包括在第二层220与部分机械加工的第一层210a之间进行混合。
48.通过使用混合增材和减材制造系统中的一个或多个am工具的沉积过程224在部分机械加工的第二层220a的顶部上构建叶片的第三层230。然后使用混合增材和减材制造系统中的一个或多个sm工具来执行机械加工过程232。机械加工过程232以最低程度将第三层230混合到部分机械加工的第二层220a中,并且因此机械加工过程232可完成叶片的第二层的制造,从而产生经完全机械加工的第二层。
49.在一些情况下,机械加工过程232仅覆盖所制造的叶片的第三层230的一部分,如图2a中所示,从而产生叶片的部分机械加工的第三层,例如,以留下第三层230的在其上要构建下一层的某个未精加工部分。但如果第三层230是叶片的最终层,则机械加工过程232可覆盖叶片的第三层230的整体,如图2b中所示。并且与机械加工过程222一样,机械加工过程232可包括半精加工操作和精加工操作两者。
50.图2b示出了图2a的构建序列示例的完全制造的叶片。使用跨越两个不同的制造阶段的三个单独的制造过程在毂部分210a的顶部上构建完全机械加工的第一层210b。在第一制造阶段中,通过沉积过程204(增材地)构建叶片的第一层,并且然后通过机械加工过程212(减材地)构建叶片的第一层的一部分。应注意,当使用混合阶段式制造过程时,am工具和sm工具仅需要适应叶片的第一层的高度而不是叶片的整个高度。
51.然后,在第二制造阶段中,由于通过机械加工过程222(减材地)构建叶片的第一层,所以机械加工过程222完成经完全机械加工的第一层210b。换句话说,使用在两个不同的制造阶段(第一制造阶段制造第一层,并且第二制造阶段制造第二层)中执行的三个单独的过程204、212、222来完成叶片的第一层。类似地,使用跨越两个不同的制造阶段但与第一层具有重叠的三个单独的制造过程在完全机械加工的第一层210b的顶部上构建完全机械加工的第二层220b。因此,使用在两个不同的制造阶段(第一制造阶段制造第二层,并且第二制造阶段制造第三层)中执行的三个单独的过程214、222、232来完成叶片的第二层。
52.然而,叶片的最终层仅需要单个制造阶段中的两个单独的过程,即,在第三层制造
阶段中执行沉积过程224和机械加工过程232来完成叶片的第三层230a。还可在相应的制造阶段中包括其他过程。而且,请注意,相应的第一制造阶段、第二制造阶段和第三制造阶段可包括构建附接到同一毂的多个其他叶片的第一层、第二层和第三层。另外,制造阶段的数目不需要是三,并且在一些实施方式中,cad程序116确定多少层是期望的,如在下文结合图3a更详细地描述。但不管层的总数和因此制造阶段的数目如何,都将存在关于构建零件的单独的制造阶段之间的一个或多个重叠250、255。
53.重叠250、255是由于机械加工过程212、222、232与通过沉积过程204、214、224构建的叶片的单独的层的偏移而产生,如图2b中所示。因此,重叠250是沉积过程204的结束点与机械加工过程212的结束(或机械加工过程222的起点)之间的差异。同样地,重叠255是沉积过程214的结束点与机械加工过程222的结束(或机械加工过程232的起点)之间的差异。但重叠250、255的大小可依据要制造的特定零件而改变,以便改进零件的混合制造。
54.例如,对机械加工过程222、232的数值模拟可包括模拟am操作相对于sm操作的热效应,这将需要足够的材料以便分别在部分机械加工的第一层210a与沉积的第二层220之间以及在部分机械加工的第二层220a与沉积的第三层230之间进行混合。由于使用了分层制造过程,所以两个层之间的界面处(以及潜在地在总体零件层级处)的一些热效应可致使零件在制造期间移动或变形。为了解决此问题,应在部分机械加工的第一层210a中留下足够量的沉积的第一层210(在机械加工过程212期间)以吸收热,并且防止在添加214第二层220期间的任何(或过多)的移动或变形,从而避免在恰当位置没有足够的材料来成功地完成机械加工过程222,包括在第一层与第二层之间进行混合。同样地,应在部分机械加工的第二层220a中留下足够量的沉积的第二层220(在机械加工过程222期间)以吸收热,并且防止在添加224第三层230期间的任何(或过多)的移动或变形,从而避免在恰当位置没有足够的材料来成功地完成机械加工过程232,包括在第二层与第三层之间进行混合。
55.因此,对沉积过程214、224和/或机械加工过程222、232的数值模拟可揭露需要调整重叠250、255中的一者或两者(在零件的不同区域中将尺寸潜在地增加或减小不同的量)以促进在机械加工过程222、232期间执行的混合。另外,对过程214、222、224、232的数值模拟可揭露需要调整过度构建量(在零件的不同区域中将尺寸潜在地增加或减小不同的量),如在下文结合图2c和图3a更详细地描述。将了解,数值模拟的结果将取决于用于制造零件的材料的物理性质。当在不同的材料(包括不同的金属合金,诸如不锈钢和镍合金)上面添加新的熔化材料时并且当通过给定类型的切削工具对沉积材料进行机械加工时,所述不同的材料将具有不同的强度和稳定性。因此,将需要在所述阶段中的一个阶段中在零件上留下或多或少的材料以确保稳定性,并且避免在混合阶段式制造过程期间的偏离。
56.可进行额外的数值模拟,并且可基于来自所述模拟的反馈来对混合制造过程作出额外的修改。尽管如此,在制造阶段中的前面一个制造阶段期间通过am在一个层中沉积的材料的一部分的量是基于数值模拟的结果来调整,所述部分然后在制造阶段中的后续一个制造阶段期间通过主要对另一(更高)层执行的sm来移除。所调整的“量”可包括在后续的制造阶段与前面的制造阶段之间的重叠的大小(例如,重叠250、255中的一者或两者的大小)、至少在后续的制造阶段与前面的制造阶段之间的重叠区域中沉积的材料的范围(超出零件的3d几何形状的包络,即,过度构建量)(例如,所沉积204、214的材料的量至少在重叠250、255中的一者或两者的区域中超出叶片的外表面),或重叠的大小和所沉积的材料的范围两
者。还要注意的是,在给定层中沉积的材料的范围(过度构建量)对于为在上面沉积更高层提供足够的支持是重要的。
57.图2c示出了在混合增材和减材制造期间的增材制造过程中的过度构建的示例。将了解,制造的增材部分将需要沉积足够的材料来填充最终零件将占据的整个3d空间,加上超出此3d空间的某一额外量以提供被混合制造的sm过程机械加工掉的材料。混合制造的优点在于,将仅需要沉积少量的额外材料(相对于形成零件所需的材料),因此节约了制造过程中的材料。
58.可通过产生用于am构建的零件几何形状的扩大版本来限定所需的少量额外材料。这可通过以下操作完成:产生零件几何形状的3d模型的扩大版本(例如,零件的b-rep的向外偏移),以形成要由am过程构建的结构的3d模型(例如,在sm处理之前的零件的am版本的b-rep),和/或根据零件几何形状的3d模型修改针对am过程创建的工具路径规格。在任何情况下,零件几何形状的3d模型的扩大版本可能没有大至足以支持更高的层和在正确位置提供用于sm过程的足够的材料(例如,在由更高层的am构建引起的任何变形移动之后)。应注意,当在更低物体的顶部上沉积材料时,不管am过程是否允许少量悬垂,情况都可为这样。
59.图2c示出了其中第一层250包括精加工(或半精加工)部分252、转变区254和为下一层准备的过度构建部分256的示例。应注意,为在本公开中清晰起见,在图2c中放大了零件的这些不同区域的大小,但即使如此,每个层的过度构建部分将常常向外渐缩,如图所示。在任何情况下,第一层250的过度构建部分256需要大至足以支持在下一阶段的下一am构建中对材料260的am沉积。并且材料260的am沉积需要足够大,使得下一阶段中的sm过程可切除材料以形成第二层265。
60.另外,形成第一层250的材料的am沉积需要足够大,使得在由在第一层250的顶部上对材料260的am沉积导致的任何移动或变形之后,在第一层250中的正确位置仍然存在足够的材料来允许sm过程切削出零件的正确的最终几何形状。因此,可通过以下操作来制定制造计划:执行在此文献中描述的数值模拟来限定多个层250、265、270、275、280、285中的每一者的精加工(或半精加工)部分、转变区(对应于重叠)和过度构建部分。应注意,在图2c中,通过实线表示层的精加工(或半精加工)部分,通过虚线表示层的转变区,并且通过点线表示过度构建部分。并且所述制造计划可通过以下方式来限定要在混合制造过程期间构建的零件的这些不同部分:针对零件的不同层产生一个或多个3d模型和/或一个或多个工具路径规格(例如,用于am过程和sm过程),其具有合适的过度构建和/或重叠(请注意,重叠可以是转变区与留下的过度构建量的组合)。
61.再次返回图1,cad程序116可执行在此文献中描述的操作来制定零件的3d模型132的制造计划。这可包括通过生成供混合增材和减材制造系统用来制造零件的工具路径来准备用于制造零件的物理结构的3d模型132。例如,可以使用3d模型132来生成工具路径规格文档160,所述工具路径规格文档可被发送到单个am sm机器170并且用于控制一个或多个am工具176和一个或多个sm工具172的操作,如此文献中所描述。
62.这可在用户190的请求之后或鉴于用户对另一动作的请求进行,所述请求诸如将3d模型132发送到可直接连接到计算机110或经由网络140连接到所述计算机的混合增材和减材制造系统,如图所示。这可涉及在本地计算机110或云服务上执行的用于将3d模型132导出到制造所依据的电子文档的后过程。应注意,电子文档(其出于简明起见将简称为文
档)可以是文件,但不一定对应于文件。可将文档存储在保存其他文档的文件的一部分中,存储在专用于所讨论的文档的单个文件中,或存储在多个协同文件中。
63.此外,在一些实施方式中,将计算机110集成到cnc机器170中,并且因此通过将使用文档160来制造零件180的同一计算机来创建文档160。因此,在一些实施方式中,混合增材和减材制造系统包括计算机110,并且可执行在此文档中描述的技术以优化零件的制造策略,并且在一个系统中一起完成对零件的最终检验(使用合适的测量装置,包括过程中测量装置),并且可能在单个机器170中一起完成对零件的最终检验。工具路径规格文档160(例如,适当格式的数控(nc)程序)包括致使cnc机器170使用am工具176和sm工具172来执行混合制造过程以制造物理物体180(对应于3d模型132)的一个或多个工具路径规格。
64.图3a示出了基于结构的混合增材和减材制造的数值模拟而更改制造计划的过程的示例。例如由cad程序116获得300要制造的零件的三维几何形状的数据。所述零件要通过包括增材制造工具和减材制造工具的混合增材和减材制造系统由材料制造,如此文献中所描述。此外,所述数据可包括:零件(或其部分)的3d模型(例如,b-rep);am工具和/或sm工具的一个或多个工具路径规格,所述工具路径规格已经例如基于关于切削条件/参数的输入从零件的3d模型生成;或3d模型和工具路径规格数据两者。
65.所述零件可以是机翼、叶盘、涡轮转子/叶轮或这些的一部分(例如,要构建在毂上的一个或多个叶片或轮叶)。所述材料可以是不锈钢、镍、钛、铝或其一种或多种合金。增材制造工具可以是激光沉积工具或电弧工具,所述工具可与粉末或线材进料一起使用。减材制造工具可以是2.5轴、3轴或5轴或更多轴切削工具。将了解,其他零件(或其部分)、材料和工具也可与在此文献中描述的系统和技术一起使用,其中使用增材制造与减材制造的组合从原材料(大体上粉末、液体、悬浮液或熔化固体)构建3d零件。
66.在任何情况下,通过混合增材和减材制造系统使用由一系列两个或更多个阶段组成的制造过程来制造零件,其中所述两个或更多个阶段中的每个阶段包括用增材制造(am)工具添加材料以及用减材制造(sm)工具移除材料中的一些以构建零件的下一层。在一些实施方式中,层的数目(和因此制造零件的阶段的数目)被设置305为默认初始数目,诸如二或三层/阶段的默认值。在一些实施方式中,层的数目是由用户或另一过程预先限定。例如,层的初始数目可由数据指定,例如,所获得300的数据可包括已经将零件制造划分为(零件的)预先限定的数目的层和因此(零件的制造的)阶段的am工具和sm工具的工具路径规格。
67.在一些实施方式中,可修改层的数目以便在制造过程的生产率与质量之间进行平衡。应注意,较少的层是优选的,因为较多的层意味着不同工具之间的更多转变。使用am工具与使用sm工具之间的更多转变意味着制造过程的更多中断,这一般会降低制造过程的生产率。然而,依据要制造的零件和可用的sm工具,太少的层可导致sm工具进行机械加工期间的不期望的振动,这可能降低所制造的零件的质量。
68.一般来说,要使用的层的数目将取决于材料的强度、零件的3d几何形状(例如,零件的不同部分相对于彼此的形状和大小,诸如叶片的长宽比和叶片之间的间隔),以及制造的切削条件/参数。所述切削条件/参数可包括关于一种或多种不同切削工具的信息和/或可用作混合制造过程中的sm工具的一种或多种不同切削工具的切削数据。切削条件/参数的信息可包括要使用的sm工具的细节(工具大小、形状以及凹槽的数目(如果有))、切削深度、进给速率、主轴转速、切入速率、步越和步降,加上工件材料(例如,镍、钛、铝或其一种或
多种合金)以及工具材料(例如,硬质合金)规格。在一些实施方式中,所述切削条件/参数中的一些或全部是从另一来源(例如,混合制造系统的提供商)获得。
69.开始于最低层,即,开始于第一阶段,例如由cad程序116根据数据和材料的物理性质来模拟310零件的当前层的增材制造。这可涉及使用有限元分析(或其他数值模拟技术)来模拟在当前阶段中添加材料的热效应。数值模拟310可涉及模拟当前层与am工具在其上构建的物体(例如,来自前一阶段的先前层)之间的界面处的热效应、总体零件层级下的热效应,或以上两者(例如,模拟总体零件层级下的热效应和在制造的第一和第二阶段中添加的沉积材料之间的界面处的热效应)。
70.图3b示出了可执行以流线化am工作流并且制定制造计划以用第一次正确制造从零件的3d模型取得成功3d打印的零件的数值模拟的视觉表示。图3b的示例示出了不活动元件311a、演变界面311b和活动元件311c的模拟以及还有移位312的模拟。返回到图3a,模拟310的热效应可包括由使用am工具导致的正在制造的零件的移动或变形。一般来说,可使用影响零件将如何移动或变形(在沉积材料以形成零件的当前层期间)的任何合适的信息(例如,测试数据)来生成在am工具的数值模拟310中用于构建工件的热与力模型,然后使用sm工具切削所述工件。
71.例如由cad程序116根据数据和材料的物理性质来模拟315零件的当前层的减材制造。这可涉及使用有限元(fe)分析(或其他数值模拟技术)来模拟在当前阶段中移除材料的振动和/或热效应,其中移除材料包括在当前层与在当前层下方的物体(例如,来自前一阶段的先前层)之间进行混合。数值模拟315可涉及模拟当前层与在当前层下方的物体之间的界面处的热效应,模拟总体零件层级下的热效应,或以上两者。应注意,可从来自前一阶段的先前层(或在当前层下方的其他物体)的顶部界面(以及从侧面)移除材料。
72.数值模拟315可涉及模拟由sm工具在从当前层和在当前层下方的物体移除材料期间经历的振动,所述移除包括在当前层与在当前层下方的物体之间进行混合。所模拟315的振动可与切削条件/参数一致,并且可包括在通过sm工具从工件切削材料时评估sm工具和工件所经历的偏斜。一般来说,可使用影响工具和/或工件将在切削期间如何移动的任何合适的信息(例如,测试数据)来生成sm工具对工件施加的力的力模型以在模拟315中使用。应注意,sm工具越短且越强,在减材制造期间工具中将存在的振动越少(较短的工具天然较硬)。
73.例如由cad程序116进行检查320,以查看是否仍然需要模拟制造的更多层。如果是,则过程移动325到下一(更高)层,以模拟310、315am工具和sm工具构建该下一层。在所示出的示例中,在对制造计划作出任何改变之前模拟制造的所有阶段。但将了解,这不是必需的。在一些实施方式中,在评估模拟的结果以确定是否需要改变制造计划之前仅模拟两个或更多个阶段中的一个阶段或两个阶段。
74.在一些实施方式中,例如由cad程序116针对来自数值模拟315的数值模拟结果中的过高振动进行检查330。机械加工振动(还称为颤振)对应于工件与切削工具之间的相对移动,所述相对移动在机械加工的表面上产生波。可通过分析从切削力和切削动态模型生成的数据来确定被视为过高的振动量。可使用切削力的模型和动力学来预测工具和工件在切削时的切削力和动态响应(包括振动、颤振等)。可分析结果以发现在切削期间多少振动产生不稳定性。
75.在预测了切削力和动力学之后,可使用所述力来限定后续的fe模拟的载荷情况以验证所预测的结果。fe模拟可:(1)基于工件的材料,指示工件自身上的所得的应力是否足以折断或损坏工件;(2)基于夹具(还称为工件夹具)的材料,指示夹具上的所得的应力是否足以损坏夹具或产生夹具中的不稳定性;以及(3)基于切削工具的材料,指示切削工具上的所得的应力是否足以折断或损坏切削工具自身。来自fe模拟的这三个指示中的任一者将构成需要校正动作来解决的过高振动,使得在实际减材制造过程期间的振动量不应损坏工件、夹具和/或工具。
76.如果振动过高,则可例如由cad程序116修改335两个或更多个层和因此两个或更多个制造阶段。这可涉及改变所述层中的两者或更多者的高度和/或增加所述层的数目以减小所有层的高度。如上文所述,较少的层是优选的,因为更多的层意味着am工具与sm工具之间转变更多。因此,进行修改335以对生产率和由于不具有合适的工具(足够长和强)来完成给定层中的机械加工而引起的问题进行平衡。其他和/或额外的修改335也是可能的,包括调整340多余材料的量(如在下文更详细地描述),通过调整工具的操作(例如,主轴转速、齿数和相对位置等)来改变振动频率和/或改变工具(修改角度、尺寸、表面处理等)。
77.修改335可基于可用的切削工具和需要使用那些切削工具进行机械加工的3d几何形状的设计,以选择层的数目和/或层中的每一者的高度。模拟315零件的制造以查看实际上有多少振动,并且基于数值模拟结果来修改335层,包括改变要使用的层(和因此制造阶段)的数目和/或改变那些层中的一者或多者的高度。因此,鉴于零件的尺寸、可用的工具和在制造期间经历的模拟振动,所述过程可计算出如何以及在何处将零件分成多层。
78.另外,所述过程可例如通过cad程序116调整340在第一阶段中添加的第一材料的包括在第二阶段中移除的第二材料中的部分的量。图3c示出了用于制造零件的两个层的材料的相应部分的添加和移除的视觉表示。模拟310可包括在所述两个或更多个阶段中的第一阶段中使用am工具来添加第一材料310a,并且模拟315可包括在所述两个或更多个阶段中的第二阶段中使用sm工具来移除第二材料315b,其中第一阶段在第二阶段前面,并且第二材料315b包括第一材料310a的部分315b1,从而在全精加工(或半精加工)第一层的顶部上产生部分精加工(或半精加工)第二层316b。另外,模拟310可包括在所述两个或更多个阶段中的第二阶段中使用am工具来添加第三材料310b,并且模拟315可包括在所述两个或更多个阶段中的第一阶段中使用sm工具来移除第四材料315a,从而产生部分精加工(或半精加工)第一层316a,其中第一材料310a包括第四材料315a,并且第二材料315b包括第三材料310b的一部分315b2。
79.调整340涉及根据材料的物理性质基于模拟310、315的结果来调整第一材料310a的包括在第二材料315b中的部分315b1的量,以防止零件偏离三维几何形状,所述偏离会导致没有足够的材料可用于sm操作,包括在层之间进行混合。因此,可优化要留下的额外材料的量以减少材料使用和/或制造时间。影响留下一个层的多少非机械加工部分以用于混合到下一更高层的机械加工部分中的因素可包括材料的强度、零件的3d几何形状(例如,零件的不同部分相对于彼此的形状和大小,诸如叶片的长宽比和叶片之间的间隔),以及sm操作的切削条件/参数。
80.因此,所述过程确保将在所制造的零件上留有足够的材料来在减材制造期间将第一层与第二层混合。混合制造过程的热效应可致使零件移动或变形,这可不利地影响完全
制造的零件的质量。通过在第一制造阶段中的减材制造期间在工件上留下足够的材料,所述工件将能够在第二制造阶段中的增材制造期间吸收热而不会变形太多而使在第二制造阶段中的减材制造期间没有足够的材料可用于将两层混合在一起。应注意,调整340可包括增加或减小am过度构建量和/或am与sm的重叠。
81.在sm重叠调整的情况下,调整340可包括减小第四材料315a的量并且增加在第二材料315b中包括的第一材料310a的部分315b1。例如,当数值模拟确定材料不够强和稳定以防止影响所制造的零件的质量的变形时,需要留下更多的材料以吸收来自am的热并且仍然在正确位置具有足够材料以用于sm期间的混合。因此,混合距离通过以下操作而得以增加(例如,增加图2b中的重叠255):减小第四材料315a的量(例如,降低图2b中的机械加工过程222的上限)并且增加在第二材料315b中包括的第一材料310a的部分315b1(例如,降低图2b中的机械加工过程232的下限)。
82.另外,调整340可包括增加第四材料315a的量并且减小在第二材料315b中包括的第一材料310a的部分315b1。例如,在数值模拟确定材料足够强和稳定使得工件的材料将不存在变形的情况下,需要留下较少的材料用于混合。因此,混合距离通过以下操作而得以减小(例如,减小图2b中的重叠255):增加第四材料315a的量(例如,升高图2b中的机械加工过程222的上限)并且减小在第二材料315b中包括的第一材料310a的部分315b1(例如,升高图2b中的机械加工过程232的下限)。因此,调整340可涉及改变在第一阶段和第二阶段中使用的sm机械加工的刀具路径规格。
83.在am过度构建量调整的情况下,除了改变sm量315a、315b以在一个层中留下足够量的非机械加工的材料以确保am在其上构建下一更高层并且对零件进行sm机械加工以产生高质量制造结果的那个层中存在足够的材料并且之外,调整340可包括增加或减小要在所述两个或更多个阶段中的第一阶段中使用增材制造工具添加的第一材料310a的过度构建量(相对于零件的三维几何形状)。此过度构建量的横向范围将取决于am过程和所使用的材料。
84.改变340am过度构建量可通过以下操作来完成:改变am构建的刀具路径规格,或改变am构建的模型的3d几何形状。例如,所述过程可包括自动cad几何形状修改步骤,所述自动cad几何形状修改步骤使用用于相应层中的am构建的零件几何形状的扩大版本来产生作为阶段式沉积模型的数据,并且可基于数值模拟结果来调整340相应层中的am构建(相对于零件的cad模型)所需的扩大量。换句话说,数值模拟指示第一制造阶段的预变形的am沉积形状所需的扩大量,使得在由第二制造阶段中的am导致的变形之后,将仍然存在足够的材料(超出零件的cad模型的外表面)来完成第二制造阶段中的sm。应注意,诸如当所添加的第一材料310a的顶部的至少部分需要被sm机械加工掉(在第一阶段的sm过程中)以产生要在其上添加第三材料310b(在第二阶段的am过程中)的合适表面时,所述扩大可从零件的几何形状垂直向上(除了横向向外之外)。
85.在一些实施方式中,响应于数值模拟310、315而调整340转变区的大小和过度构建量的范围。在一些实施方式中,对热效应的模拟是基于不同层的不同特性。例如,虽然此详细描述集中在使用单种材料的制造,但将了解,可在混合系统中例如使用单个am工具176或一个以上am工具176来使用一种以上材料,并且零件设计和/或制造计划可要求将不同材料用于零件的不同部分中。因此,对热效应的模拟可考虑到在一个层中相对于在其上构建一
个层的物体中使用不同材料(具有不同物理特性),例如较低层(或叶根)可以是比放置在上面的较高层更加热稳定的金属。
86.一般来说,可以使用来自增材和减材制造的组合的数值模拟的反馈来调整制造计划,以便改进制造过程和/或改进所制造结构的质量。可修改制造阶段的数目和/或在阶段内和在阶段之间的增材减材制造之间的重叠,以防止增材沉积期间的不稳定性和变形,确保机械加工期间的均匀材料移除,和/或提供sm机械加工期间的针对振动和机械加工动力学的稳定性。因此,通过模拟变形来改进制造计划的过程,并且对所添加和移除的材料的比例进行更改,以确保使用混合制造过程一致且准确地制造零件。
87.可例如由cad程序116提供345所调整的量和/或所修改的层/阶段以用于通过混合增材和减材制造系统制造零件。在一些实施方式中,所述过程包括通过混合增材和减材制造系统使用所调整的量和/或所修改的层/阶段来制造345零件。例如,所述过程可由cad程序116执行,所述cad程序可编码在至少一个非暂时性计算机可读介质中并且可在包括在混合增材和减材制造系统中的一个或多个计算机处理设备上运行。因此,提供345可涉及将所调整的量和/或所修改的层/阶段传递到处置制造的程序的另一部分。替代地或另外,提供345可涉及将所调整的量和/或所修改的层/阶段保存或存储到计算机可读介质以供稍后检索用于制造中。
88.另外,在一些实施方式中,模拟310、315包括模拟对构建在被包括作为毂的一体部分的叶根的顶部上的叶片或轮叶的机械加工。例如,图3d示出了具有被设计成在高温环境(例如,1000华氏度到5000华氏度)中操作的毂部分360和叶片370的涡轮转子的一部分的3d模型350,并且图3e示出了概念验证制造结构,所述概念验证制造结构示出了在表示涡轮转子的毂的块390上的部分制造的叶片380。在高温环境中,例如在飞机或其他交通工具的发动机的热端中,在叶片与涡轮转子中的毂会合处存在大量应力。因此涡轮转子的此关键部分可比其他部分更频繁地发生故障这种故障可能比在叶片370中的一个更远处的故障更可能损坏发动机。
89.为了解决此问题,零件的设计和/或制造计划可包括叶根作为毂的一体部分。例如,叶根362由相同材料形成为毂部分360的部分,并且使用混合am sm制造的分层和模拟告知方法在上面构建叶片372。与毂成一体的叶根的这种使用增加了涡轮转子的关键部分的强度,这依据在使用期间零件内的热区布置可能是尤其重要的。在am构建到圆柱形工件上的初始层之间的连接处的弱点的任何问题得以消除,或者从涡轮转子的更关键部分转移,于是,这对于受控零件而言不是问题了。在一些实施方式中,叶片370构建在(过度构建的预成型件的)预先机械加工的表面上以从叶片/毂界面移除应力集中。
90.叶片370中的每一者可由与毂部分360相同的材料或不同的材料制成。正在对多材料沉积进行研究,但在此文献中描述的系统和技术将适用于在沉积多种材料方面的新的开发,因为当基于零件的性能和操作要求与设计零件相结合地开发制造计划时,所描述的模拟技术将适用于辅助选择材料和其部分。例如,除了叶片是由与毂不同的材料制成之外,毂的各个部分和/或叶片的各个部分可由不同的材料制成。应注意,一种材料与另一种材料的不同之处可在于它们是同一组材料的合金,但每种材料的使用量不同。
91.在一些实施方式中,对热效应的数值模拟包括鉴于要用于根毂和叶片的材料,评估热区(例如,基于发动机内的零件的位置)来帮助确定叶根的最佳高度。对热效应的数值
模拟还可包括帮助确定在什么地方使用哪些材料,诸如在零件的最热部分中使用更耐温材料,同时还考虑到零件的性能和操作要求。
92.在一些实施方式中,通过首先铸造或锻造(热或冷)设计的相似物,并且然后潜在地执行传统的sm机械加工操作来制造具有叶根的毂。在一些情况下,在锻造或铸造之后,混合制造过程可在没有制备用于首次沉积的表面的初始的sm机械加工操作的情况下开始。例如,精密锻造或铸造可产生准备好用于首次沉积的表面。在一些情况下,通过以下操作来为首次沉积制备初始工件的一个或多个表面:使用传统的sm机械加工操作执行端面铣削,并且然后前进到混合制造过程。
93.在一些实施方式中,具有叶根的毂被制造成在叶根中的每一者的顶部上包括预先限定的界面(平坦或接近平坦),这有助于对叶根上的叶片进行am构建。例如,可向每个叶根表面(将在其上执行初始沉积)添加微小的曲率,其中所述曲率与起始毂适形并且与毂的旋转中心同心(以与叶片相交/相切以形成根的更小直径)。使起始形状与毂形状适形可减小沉积误差,但还可使沉积过程的cnc运动更复杂。
94.在一些实施方式中,使叶根与叶片之间的界面保持为平坦平面(在cnc沉积的x、y维度上)可为优选的,因为这简化了沉积过程。但在一些情况下,叶根的平坦表面可以是成角度的平面。一般来说,使用叶根(与毂成一体)以及在叶根与叶片之间的界面的设计涉及简单机器运动或复杂机器运动之间的权衡,这导致更复杂的沉积和可能更多的沉积低效(例如,当使用激光加粉末ded过程时损失粉末)。在得到使用叶根的益处时可考虑这些权衡,包括(1)通过在接近毂处使用传统sm的已知和稳定的过程并且将在沉积期间使用的高热能移离毂来降低叶盘部件上的此关键区中的故障风险,和/或(2)通过在初始沉积阶段期间降低机器运动的复杂性来简化沉积过程。
95.在图3e中示出的概念验证结构中,块(表示涡轮转子的毂)被粗加工以形成具有叶根的初始工件,包括经粗加工的叶根391。然后,仅执行am过程和sm过程的适当子集(在am sm混合制造的三个阶段中)以构建叶片380。第一叶片部分381示出了叶根391上的am构建1的结果。第二叶片部分382示出了am构建1和sm半精加工1(制造阶段1完成)的结果。第三叶片部分383示出了am构建2的结果。第四叶片部分384示出了am构建1 sm半精加工1以及am构建2 sm半精加工2(制造阶段2完成)加上am构建3的结果。最后,第五叶片部分385示出了在叶根上的三个层中构建叶片380的所有三个制造阶段的结果。
96.然而,所述设计和制造计划的这些细节并非必需的。在一些实施方式中,不使用叶根。例如,可通过铸造或锻造(热或冷)来制造圆柱形毂(或盘)的接近相似物,并且初始的am构建可在此初始工件上。这与传统的sm相比可仍然减少总机器成本和时间,但在叶片与毂(或盘)之间的界面处可存在零件完整性问题,这可能会引入一个或多个应力集中区。而且,将仍然存在使毂(或盘)达到其最终形状所需的显著量的sm机械加工。
97.但是这种方法可能仍然适用于某些类型的零件,这取决于它们在叶片与轮毂(或圆盘)之间的界面处的结构强度要求。而且,应力集中问题可通过适当的过程控制来减少或移除,例如在初始沉积操作之前将毂加热以防止热冲击,所述热冲击可能会引起接头中的裂缝或弱点并且导致操作期间未来的零件完整性问题。因此,通过适当的过程控制和对动力源和过程的理解,可仍然通过此方法实现良好的结构完整性。
98.在一些实施方式中,不使用平坦(或接近平坦)的界面。例如,初始的am构建可在毂
的最终(或接近最终)的形状上而不是在叶根上,所述形状可容易由圆形进料通过车削机械加工而得。这可减少一些类型的零件的总的制造时间量,但在以上另一方法的情况下,在叶片与毂(或盘)之间的界面处可能存在零件完整性问题。因此,这种方法可用于某些部件,这取决于它们在叶片与轮毂(或盘)之间的界面处的结构强度要求、轮毂(或盘)的表面有多复杂、将在其上进行am构建。应注意,以上两种方法可能存在工具可接近性问题,这也应考虑到,这取决于叶片的长度、扭曲度和在一起的接近度。
99.例如,为了确定用于叶片372的合适的混合分层制造计划,可基于叶片372和其侧面叶片371、373的形状来解决可接近性问题。可生成侧面叶片371、373的护罩(例如,叶片371、373的b-rep的向外偏移),并且使用所述护罩进行碰撞校验以限定制造叶片372的工作体积,即,侧面叶片371、373的两个护罩之间的3d空间。所述过程然后可在该工作体积内生成叶片372的工具路径,这取决于关于sm操作的类型(粗加工、半精加工或精加工)和可用于该sm操作的sm工具的输入(例如,用户输入),所述输入将部分地取决于叶片372的大小和/或形状。可在混合制造过程的数值模拟期间考虑此工具路径信息以识别任何工具可接近性问题。
100.图4是包括数据处理设备400的数据处理系统的示意图,所述数据处理设备可被编程为客户端或服务器。数据处理设备400通过网络480与一个或多个计算机490连接。虽然在图4中仅一个计算机被示出为数据处理设备400,但可使用多个计算机。数据处理设备400包括可分布在应用层与操作系统之间的各种软件模块。这些可包括可执行和/或可解译软件程序或库,包括制造模拟的工具和服务、实施在此文献中描述的系统和技术的3d建模和制造控制程序404。所使用的软件模块的数量可以因实施方式而异。此外,软件模块可以分布在由一个或多个计算机网络或其他合适的通信网络连接的一个或多个数据处理设备上。
101.数据处理设备400还包括硬件或固件装置,所述硬件或固件装置包括一个或多个处理器412、一个或多个额外装置414、计算机可读介质416、通信接口418以及一个或多个用户接口装置420。每个处理器412能够处理用于在数据处理设备400内执行的指令。在一些实施方式中,处理器412是单线程或多线程处理器。每个处理器412能够处理存储在计算机可读介质416上或存储装置上的指令,所述存储装置诸如额外装置414中的一者。数据处理设备400使用通信接口418来例如通过网络480与一个或多个计算机490通信。用户接口装置420的示例包括显示器、相机、扬声器、麦克风、触觉反馈装置、键盘、鼠标以及vr和/或ar设备。数据处理设备400可例如在计算机可读介质416或一个或多个额外装置414上存储实施与本文描述的程序相关联的操作的指令,所述一个或多个额外装置例如为硬盘装置、光盘装置、磁带装置和固态存储器装置中的一者或多者。
102.本说明书中描述的主题和功能操作的实施方案可实施在数字电子电路中,或实施在计算机软件、固件或硬件中(包括本说明书中公开的结构和它们的结构等同物),或实施在它们中的一者或多者的组合中。可使用计算机程序指令的一个或多个模块来实施在本说明书中描述的主题的实施方案,所述计算机程序指令的一个或多个模块被编码在非暂时性计算机可读介质上以供数据处理设备执行或者用于控制数据处理设备的操作。所述计算机可读介质可为制造产品,诸如计算机系统中的硬盘驱动器,或通过零售渠道销售的光盘,或嵌入式系统。可单独地获取计算机可读介质,或者所述计算机可读介质稍后可诸如通过经由有线或无线网络输送计算机程序指令的一个或多个模块而被编码有计算机程序指令的
所述一个或多个模块。所述计算机可读介质可以是机器可读存储装置、机器可读存储衬底、存储器装置,或其中的一者或多者的组合。
103.术语“数据处理设备”涵盖用于处理数据的所有设备、装置和机器,包括例如可编程处理器、计算机或多个处理器或计算机。除了硬件之外,所述设备还可包括创建所讨论的计算机程序的执行环境的代码,例如,构成处理器固件、协议堆栈、数据库管理系统、操作系统、运行时环境或其中的一者或多者的组合的代码。另外,所述设备可采用各种不同的计算模型基础设施,诸如网络服务、分布式计算和网格计算基础设施。
104.可通过任何合适形式的编程语言来编写计算机程序(还被称为程序、软件、软件应用程序、脚本或代码),所述编程语言包括经过编译或解译的语言、声明性或程序性语言,并且可通过任何合适的形式来部署所述计算机程序,包括部署成独立的程序或适合于在计算环境中使用的模块、部件、子例程或其他单元。计算机程序不一定对应于文件系统中的文件。程序可存储在保存其他程序或数据(例如,存储在标记语言文档中的一个或多个脚本)的文件的一部分中、存储在专用于所讨论的程序的单个文件中,或者存储在多个协同文件(例如,存储一个或多个模块、子程序或代码的部分的文件)中。可将计算机程序部署成在一个计算机上执行,或者在位于一个场所处或跨多个场所分布并且通过通信网络互连的多个计算机上执行。
105.本说明书中描述的过程和逻辑流可由一个或多个可编程处理器执行,所述一个或多个可编程处理器执行一个或多个计算机程序以通过对输入数据进行操作并且产生输出来执行功能。所述过程和逻辑流还可由专用逻辑电路执行,并且还可将设备实施为专用逻辑电路,所述专用逻辑电路例如为fpga(现场可编程门阵列)或asic(专用集成电路)。
106.适合于执行计算机程序的处理器包括例如通用和专用微处理器,以及任何种类的数字计算机的任何一个或多个处理器。一般来说,处理器将从只读存储器或随机存取存储器或以上两者接收指令和数据。计算机的基本元件是用于执行指令的处理器和用于存储指令和数据的一个或多个存储器装置。一般来说,计算机还将包括用于存储数据的一个或多个大容量存储装置,例如,磁盘、磁光盘或光盘,或者操作性地耦合到所述一个或多个大容量存储装置以从其接收数据或向其传递数据或以上两者。然而,计算机不需要具有此类装置。另外,计算机可嵌入另一装置中,所述另一装置例如是移动电话、个人数字助理(pda)、移动音频或视频播放器、游戏控制台、全球定位系统(gps)接收器或便携式存储装置(例如,通用串行总线(usb)快闪驱动器),仅举数例。适合于存储计算机程序指令和数据的装置包括所有形式的非易失性存储器、介质和存储器装置,包括例如:示例性半导体存储器装置,例如,eprom(可擦除可编程只读存储器)、eeprom(电可擦除可编程只读存储器)和快闪存储器装置;磁盘,例如,内部硬盘或可移除盘;磁光盘;以及cd-rom和dvd-rom盘。可通过专用逻辑电路来补充处理器和存储器,或者处理器和存储器可并入专用逻辑电路中。
107.为了提供与用户的交互,本说明书中描述的主题的实施方案可在计算机上实施,所述计算机具有:显示装置,例如,lcd(液晶显示器)显示装置、oled(有机发光二极管)显示装置或用于向用户显示信息的另一监视器;以及键盘和指向装置,例如,鼠标或跟踪球,用户可借此向计算机提供输入。还可使用其他种类的装置来提供与用户的交互;例如,向用户提供的反馈可为任何合适形式的感官反馈,例如,视觉反馈、听觉反馈或触觉反馈;以及可接收来自用户的呈任何合适的形式的输入,包括声学、语音或触觉输入。
108.所述计算系统可包括客户端和服务器。客户端和服务器一般彼此远离并且通常通过通信网络进行交互。客户端和服务器的关系凭借在相应的计算机上运行并且彼此具有客户端-服务器关系的计算机程序而产生。本说明书中描述的主题的实施方案可在计算系统中实施,所述计算系统包括:后端部件,例如,作为数据服务器;或中间件部件,例如,应用服务器;或前端部件,例如,具有图形用户接口或网络浏览器的客户端计算机,用户可借此与本说明书中描述的主题的实施方式交互;或一个或多个此类后端部件、中间件部件或前端部件的任何组合。系统的部件可通过任何合适形式或介质的数字数据通信(例如,通信网络)互连。通信网络的示例包括局域网(“lan”)和广域网(“wan”)、网际网络(例如,互联网)和对等网络(例如,特设的对等网络)。
109.虽然本说明书包含许多实施细节,但是这些细节不应理解为限制被要求保护或可要求保护的内容的范围,而是对所公开的主题的特定实施方案特有的特征的描述。本说明书中在单独的实施方案的背景下描述的某些特征也可在单个实施方案中组合实施。相反地,在单个实施方案的上下文中描述的各种特征也可单独地在多个实施方案中实施或以任何合适的子组合实施。此外,尽管特征在上文可被描述为以某些组合起作用并且甚至最初因此而受权利要求保护,但是来自受权利要求保护的组合的一个或多个特征在一些情况下可与所述组合分离,并且受权利要求保护的组合可涉及子组合或子组合的变动。
110.类似地,尽管操作在附图中是按特定顺序描绘,但是此不应被理解为要求此类操作以所示的特定顺序或以有序的顺序执行,或所有所示操作被执行,以实现期望结果。在某些情形中,多任务处理和并行处理可为有利的。此外,上述实施方案中的各种系统部件的分离不应理解为在所有实施方案中都需要此分离,并且应理解,所描述的程序部件和系统可大体上一起集成在单个软件产品中或封装到多个软件产品中。
111.因此,已经描述了本发明的特定实施方案。其他实施方案处于所附权利要求书的范围内。
再多了解一些
本文用于企业家、创业者技术爱好者查询,结果仅供参考。