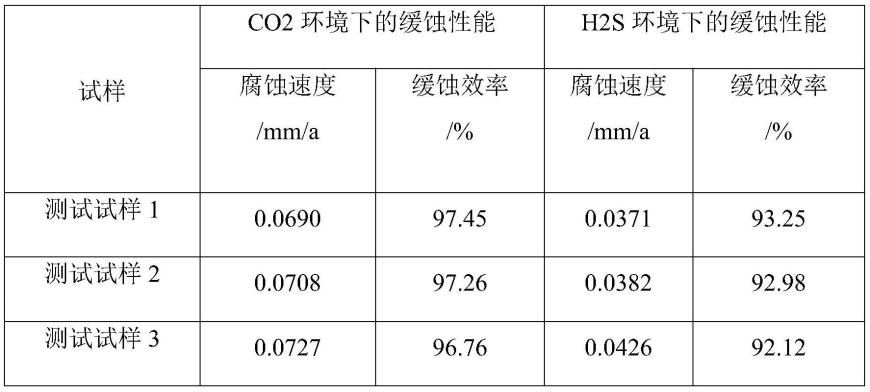
1.本技术涉及油田采油水处理的领域,更具体地说,它涉及一种环境友好型油田缓蚀剂及其制备方法。
背景技术:
2.石油是一种由气态、液态和固体烃类混合而成的物料,油田是石油生产的特定区域,我国主要通过油田注水的方式进行油田的开采,但这种方式会参数大量的含油废水,故在油田注水过程中还需要通过油田污水回注的方式来结束污水的排放。
3.在油田污水回注的过程中,由于油田污水的水质复杂、矿化度高、氯离子含量高、溶解有氧气、溶解有如二氧化碳和硫化氢这类的酸性气体,进而易腐蚀油田开采所用的金属设备及管道。
4.目前,常用间的防腐蚀措施包括使用耐腐蚀设备、涂覆防腐涂层和向油田污水中加入化学添加剂这三类,但前两者操作复杂,经济成本,故在实际生产过程中一般会通过添加如有机胺类、有机磷类缓蚀剂来进行防腐。
5.但有机胺类缓蚀剂和有机磷类缓蚀剂虽然可以达到一定的防腐蚀效果,但其对缓解酸性气体腐蚀金属设备及管道的效果较差。
技术实现要素:
6.为了提高对金属设备及管道缓腐蚀效果,本技术提供一种环境友好型油田缓蚀剂及其制备方法。
7.第一方面,本技术提供一种环境友好型油田缓蚀剂,采用如下的技术方案:一种环境友好型油田缓蚀剂,由包括以下原料制备而成:妥尔油酸、二乙烯三胺、邻二甲苯和丙烯酸;所述妥尔油酸的酸值为190~198mgkoh/g;所述妥尔油酸和所述二乙烯三胺的摩尔比为1:1.05~1.20;所述丙烯酸的用量为妥尔油酸和二乙烯三胺总质量的30~60%。
8.通过采用上述技术方案,本技术中采用了价格低廉的妥尔油酸和邻二甲苯,以及相对环保的丙烯酸作为季胺盐化反应原料,进而在降低本技术生产成本、减少生产过程对环境的污染的同时,制备得到一种具有优良缓蚀效果的产品。在本技术中,若二乙烯三胺与妥尔油酸间的摩尔比过小,则会使妥尔油酸反应不充分,进而降低产品单位质量的缓蚀效果;若二乙烯三胺与妥尔油酸间的摩尔比过大,则会加重本技术的生产成本,如回收时的能耗等;酰胺化闭环反应是放热反应,且在反应过程中二乙烯三胺会挥发,故本技术实际上二乙烯三胺与妥尔油酸大于1:1,且本技术还对二乙烯三胺与妥尔油酸间的摩尔比进行了限定,从而在降低生产成本的同时,综合改善本技术的缓蚀效果。此外,若丙烯酸的用量过少,则本技术季胺盐化反应不充分,制得产品的缓蚀效果较差;但丙烯酸本身很活泼,若丙烯酸用量过多,则丙烯酸的自聚越严重,且采用丙烯酸进行季胺盐化反应的过程实质上是放热反应,且丙烯酸沸点较低,在反应过程中会存在,故本技术中采用了过量的丙烯酸并限定了
丙烯酸的用量,从而在加快反应进程的同时,从而制备得到具有优良缓蚀效果的产品。
9.优选的,所述邻二甲苯的用量为妥尔油酸和二乙烯三胺总质量的15~30%。
10.通过采用上述技术方案,本技术中限定了邻二甲苯有两个作用,其一,邻二甲苯可以与酰胺化闭环反应中所产生的水形成共沸物,进而促使水的移除,且酰胺化闭环反应是放热反应,水的减少可以促使反应向正向移动,进而提高了本技术的产率。其二,由于邻二甲苯的沸点低于二乙烯三胺,故在反应过程中邻二甲苯比二乙烯三胺先变为气态,从而可以减少单位时间内二乙烯三胺蒸发的量,进而提高了二乙烯三胺的利用率,进而促使单位时间内更多的二乙烯三胺可与妥尔油酸反应。此外,邻二甲苯用量过多时,则反应温度很难达到150℃以上,不利于二乙烯三胺的反应;当邻二甲苯的用量过少时,则无法充分实现前面提及的邻二甲苯的两个作用,故本技术中通过限定邻二甲苯的用量,进而改善本技术的生产效率和产品质量。
11.第二方面,本技术提供一种环境友好型油田缓蚀剂的制备方法,采用如下的技术方案:一种环境友好型油田缓蚀剂的制备方法,包括以下步骤:s1,妥尔油酸咪唑啉中间体的制备,将妥尔油酸、二乙烯三胺混合搅拌均匀后,加入邻二甲苯,于常压条件、150~200℃的条件反应进行酰胺化闭环反应,同步将反应过程中形成的共沸物移除,直至反应无水产生后,制得妥尔油酸咪唑啉中间体;s2,负压蒸馏脱去妥尔油酸咪唑啉中间体中多余的邻二甲苯和未反应二乙烯三胺;s3,将s2处理后的物料季铵盐化反应制备得到产品。
12.通过采用上述技术方案,由于妥尔油酸咪唑啉中间体的制备是放热过程,故本技术中将反应所形成的共沸物移除,可以促使反应向妥尔油酸咪唑啉中间体生成方向进行,进而综合改善了本技术的产率。
13.优选的,所述步骤s1妥尔油酸咪唑啉中间体的制备具体包括以下步骤:s11,妥尔油酸和二乙烯三胺混合搅拌均匀后,加入相应质量的邻二甲苯,于常压条件下以20~30℃/h升温至150~160℃后,自然升温至195~200℃,在自然升温的过程中同步将反应过程中形成的共沸物移除;s12,维持常压、195~200℃的条件下反应且同时将反应过程中形成的共沸物移除,直至反应无水产生后,制得妥尔油酸咪唑啉中间体。
14.通过采用上述技术方案,由于经过s1反应后的物料的泡点较高,故本技术采用了负压蒸馏去除了多余的邻二甲苯和二乙烯三胺,进而减少了后续热源达不到温度要求而无法进行蒸馏的可能性。限定反应升温速率,从而控制反应过程中热应力对反应装置的影响。本技术中通过限定升温后的温度为150℃,进而促使邻二甲苯与反应生成的水形成而二元共沸物,当温度过低则不利于酰胺化反应,且步骤s1整个过程均为放热法语,故升温后温度过高则会加大后续温度控制的难度,进而易导致副反应的发生。
15.优选的,所述步骤s11和步骤s12中移除的共沸物精馏处理,精馏处理后所得的有机相返回至步骤s11中重复使用。
16.通过采用上述技术方案,本技术中通过精馏操作,从而提高了原料的利用率,进而在降低生产成本的同时提高了本技术生产的产率和质量。
17.优选的,所述步骤s2具体为:将s1中反应后的物料于压力为-0.098~0.095mpag、反应温度为150~180℃的条件下负压蒸馏处理,直至反应无物料蒸出。
18.通过采用上述技术方案,本技术通过限定减压蒸馏时在交底的负压下进行,一方面有利于邻二甲苯和过量的二乙烯三胺的回收;另一方面,限定压力可以增大物质间的相对挥发度,有效地去低沸点物质,进而提升了反应产物的纯度。
19.优选的,在所述步骤s2负压蒸馏过程中控制回流比为0.25~1.0,且将所述s2中负压蒸馏所去除的二乙烯三胺和邻二甲苯循环回流至步骤s1中重复使用。
20.通过采用上述技术方案,本技术中通过限定反应的回流比,一方面减少了反应所生产的产物随着二乙烯三胺蒸出所造成的产品损失;另一方面,回流比的限定,促使本技术精馏处理后塔顶物料组成接近水和邻二甲苯且控制塔顶二乙烯三胺含量小于等于0.05%(wt),从而提高二乙烯三胺和邻二甲苯回收率。
21.优选的,所述步骤s3中,预先将s2处理后的物料将s2处理后的物料降温至80~85℃。
22.通过采用上述技术方案,由于季铵盐化反应是强放热反应,故为了减少步骤s3中因温度过高而发生副反应的可能性,在步骤s3中预先将s2处理后的物料降温处理,且配合本技术中采用的常温下呈液态的妥尔油酸,故降温并不会使得物料过于粘稠;此外,s2处理后的物料降低后的温度过低,则所需的时间过长,且温度过低则会促使副反应且会降低反应速率;由于丙烯酸投入后反应剧烈且会放出大量的热,所以s2处理后的物料降低后的温度过高,则会使得迫使丙烯酸的投料速度降低,进而影响反应进程,故本技术中限定了s2处理后的物料降低后的温度为80~85℃,进而提高了本技术的产品质量的和生产效率。本技术在步骤s3中在投入丙烯酸时维持温度始终小于130℃,其主要原因是加入丙烯酸后反应剧烈且会放出大量的热,且温度过高会使得丙烯酸发生自聚,故本技术中通过限定丙烯酸加入过程的温度,进而提高了丙烯酸的利用率,进而大大改善了本技术的产品质量。最后,为了便于产品的后续包装,本技术中最后降温至45℃。
23.优选的,所述步骤s3具体为:将s2处理后的物料降温至80~85℃后,于常压下投入相应质量的丙烯酸且维持温度始终小于130℃,投完丙烯酸后反应2~3小时后,维持温度为120℃恒温反应1h,降温至45℃制备得到产品;且在步骤s3反应过程中所产生的共沸物回流至步骤s11中重复使用。
24.通过采用上述技术方案,本技术在加入完丙烯酸后维持在120℃恒温反应1h,从而使少量未完全反应的丙烯酸反应完全或微过量的丙烯酸完成自聚反应,进而减少丙烯酸对于本技术产品质量的影响。
25.第三方面,本技术提供一种环境友好型油田缓蚀剂的应用,采用如下的技术方案:一种环境友好型油田缓蚀剂的应用,将环境友好型油田缓蚀剂和甲醇按质量比为1:0.8-1.2的比例混合搅拌使用。
26.通过采用上述技术方案,由于本技术的产品不溶于水,故使用后必须与甲醇复配才可以使用,且甲醇本技术的价格比较低廉,故将缓蚀剂和甲醇按一定的比例混合搅拌使用,可以在降低使用成本的同时达到良好的缓蚀效果。
27.综上所述,本技术具有以下有益效果:1、本技术中采用了价格低廉的妥尔油酸、邻二甲苯以及相对环保的丙烯酸作为季
胺盐化反应原料;且限定了二乙烯三胺与妥尔油酸的摩尔比,从而在降低生产成本的同时,综合改善本技术的缓蚀效果。本技术中采用了过量的丙烯酸并限定了丙烯酸的用量,从而在加快反应进程的同时,从而制备得到具有优良缓蚀效果的产品。
28.2、本技术的方法,采用了负压蒸馏去除了多余的邻二甲苯和二乙烯三胺,进而减少了后续热源达不到温度要求而无法进行蒸馏的可能性。为了减少步骤s3中因温度过高而发生副反应的可能性,在步骤s3中预先将s2处理后的物料降温处理,且配合本技术中采用的常温下呈液态的妥尔油酸,故降温并不会使得物料过于粘稠;此外,本技术中限定s2处理后物料降低后的温度为80~85℃,进而提高了本技术的产品质量的和生产效率。本技术在步骤s3中在投入丙烯酸时维持温度始终小于130℃,减少温度过高丙烯酸发生自聚的可能性,且本技术中通过限定丙烯酸加入过程的温度,进而提高了丙烯酸的利用率,进而大大改善了本技术的产品质量。
具体实施方式
29.以下结合实施例对本技术作进一步详细说明。实施例
30.实施例1一种环境友好型油田缓蚀剂由包括以下原料制备而成:妥尔油酸(酸值为198mgkoh/g)、二乙烯三胺、邻二甲苯和丙烯酸;妥尔油酸和二乙烯三胺的摩尔比为1:1.15;丙烯酸的用量为妥尔油酸和二乙烯三胺总质量的47%;邻二甲苯的用量为妥尔油酸和二乙烯三胺总质量的20%;一种环境友好型油田缓蚀剂的制备方法,包括以下步骤:s1,妥尔油酸咪唑啉中间体的制备具体包括以下步骤:s11,妥尔油酸和二乙烯三胺按相应比例于第一反应釜中混合搅拌均匀后,向反应釜中加入全部的邻二甲苯,于常压条件下以25℃/h升温至150℃后,自然升温至197.5
±
2.5℃,在自然升温的过程中同步将反应过程中形成的共沸物通过精馏塔进行精馏处理,在精馏处理过程中塔顶使用水相回流,且脱水时塔顶二乙烯三胺的含量控制在≦0.05%(wt),有机相回流至反应釜中重复使用;s12,将步骤s11中制得的产物流动至第二反应釜中,维持常压、197.5
±
2.5℃的条件下反应,且同时将反应过程中形成的共沸物移除,直至反应无水产生后,制得妥尔油酸咪唑啉中间体,将本步骤中所形成的共沸物通过精馏塔进行精馏处理,在精馏处理过程中塔顶使用水相回流,且脱水时塔顶二乙烯三胺的含量控制在≦0.05%(wt),有机相回流至步骤s11的第一反应釜中重复使用;s2,将s12处理后的物料通入至第三反应釜中,于压力为-0.098~0.095mpagmpag、反应温度为170℃、回流比控制为0.5的条件下负压蒸馏处理,直至反应无物料蒸出,且将负压蒸馏所去除的物料回流至步骤s11的第一反应釜中重复使用;s3,将s2处理后的物料降温至80℃后,于常压下投入相应质量的丙烯酸且维持温度始终小于130℃,投完丙烯酸后反应3小时后,维持温度为120℃恒温反应1h,降温至45℃制备得到产品,在步骤s3反应过程中所产生的共沸物直接回流至步骤s11的第一反应釜中重复使用。
31.实施例2本实施例与实施例1的不同之处在于,本实施例中妥尔油酸和二乙烯三胺的摩尔比为1:1.2。
32.实施例3本实施例与实施例1的不同之处在于,本实施例中妥尔油酸和二乙烯三胺的摩尔比为1:1.1.05。
33.实施例4本实施例与实施例1的不同之处在于,本实施例中丙烯酸的用量为妥尔油酸和二乙烯三胺总质量的60%。
34.实施例5本实施例与实施例1的不同之处在于,本实施例中邻二甲苯的用量为妥尔油酸和二乙烯三胺总质量的30%。
35.实施例6本实施例与实施例1的不同之处在于,本实施例中步骤s11具体为:妥尔油酸和二乙烯三胺按相应比例于第一反应釜中混合搅拌均匀后,向反应釜中加入全部的邻二甲苯,于常压条件下以25℃/h升温至197.5
±
2.5℃,在升温的过程中同步将反应过程中形成的共沸物通过精馏塔进行精馏处理,在精馏处理过程中塔顶使用水相回流,且脱水时塔顶二乙烯三胺的含量控制在≦0.05%(wt),有机相回流至反应釜中重复使用。
36.实施例7本实施例与实施例1的不同之处在于,本实施例的步骤s2具体为:将s12处理后的物料通入至第三反应釜中,于压力为-0.098~0.095mpag、反应温度为200℃、回流比控制为0.5的条件下负压蒸馏处理,直至反应无物料蒸出,且将负压蒸馏所去除的物料回流至步骤s11的第一反应釜中重复使用。
37.实施例8本实施例与实施例1的不同之处在于,本实施例的步骤s3具体为:将s2处理后的物料降温至80℃后,于常压下投入相应质量的丙烯酸且维持温度始终小于130℃,投完丙烯酸后反应4小时后,降温至45℃制备得到产品,在步骤s3反应过程中所产生的共沸物直接回流至步骤s11的第一反应釜中重复使用。
38.实施例9本对比例与实施例1的不同之处在于,本对比例的步骤s3具体为:将s2处理后的物料降温至100℃后,于常压下投入相应质量的丙烯酸且维持温度始终小于130℃,投完丙烯酸后反应3小时后,维持温度为120℃恒温反应1h,降温至45℃制备得到产品,在步骤s3反应过程中所产生的共沸物直接回流至步骤s11的第一反应釜中重复使用。
39.实施例10本对比例与实施例1的不同之处在于,本对比例的步骤s3具体为:将s2处理后的物料降温至80℃后,于常压下投入相应质量的丙烯酸,投完丙烯酸后反应3小时后,维持温度为120℃恒温反应1h,降温至45℃制备得到产品,在步骤s3反应过程中所产生的共沸物直接回流至步骤s11的第一反应釜中重复使用。
40.对比例
对比例1本对比例与实施例1的不同之处在于,本对比例中妥尔油酸和二乙烯三胺的摩尔比为1:1。
41.对比例2本对比例与实施例1的不同之处在于,本对比例中丙烯酸的用量为妥尔油酸和二乙烯三胺总质量的18.69%。
42.对比例3本对比例与实施例1的不同之处在于,本对比例中丙烯酸的用量为妥尔油酸和二乙烯三胺总质量的25%。
43.对比例4本对比例与实施例1的不同之处在于,本对比例中丙烯酸的用量为妥尔油酸和二乙烯三胺总质量的70%。
44.对比例5本对比例与实施例1的不同之处在于,本对比例中未使用邻二甲苯。
45.对比例6本对比例与实施例1的不同之处在于,本对比例中用等摩尔的环烷酸代替实施例1中的妥尔油酸。
46.对比例7对比例与实施例1的不同之处在于,本对比例的步骤s1妥尔油酸咪唑啉中间体的制备具体包括以下步骤:s11,妥尔油酸和二乙烯三胺按相应比例于第一反应釜中混合搅拌均匀后,向反应釜中加入全部的邻二甲苯,于常压条件下以25℃/h升温至150℃后,自然升温至197.5
±
2.5℃;s12,将步骤s11中制得的产物流动至第二反应釜中,维持常压、197.5
±
2.5℃的条件下反应,且同时将反应过程中形成的共沸物移除,直至反应无水产生后,制得妥尔油酸咪唑啉中间体。
47.对比例8对比例与实施例1的不同之处在于,本对比例的步骤s2具体为:将s12处理后的物料通入至第三反应釜中,于常压、反应温度为170℃、回流比控制为0.5的条件下负压蒸馏处理,直至反应无物料蒸出,且将负压蒸馏所去除的物料回流至步骤s11的第一反应釜中重复使用。
48.性能检测试验检测方法/试验方法1.在co2环境下的缓蚀性能:按照《sy/t7025-2014酸性油气田用缓蚀剂性能实验室评价方法》的标准进行失重实验测试,测试试样1-10和对比试样1-8的腐蚀效速率和缓蚀效率。测试试样1-10是由实施例1-10制得的缓蚀剂产品与甲醇按质量比为1:1混合搅拌制得;对比试样1-8是由对比例1-8制得的缓蚀剂产品与甲醇按质量比为1:1混合搅拌制得。且实验条件具体包括:试样加注浓度为30/ppm、二氧化碳压力0.5mpa、温度60℃、转速300r/min,腐蚀介质为5%氯化钠溶液、材质为20#碳钢且规格为50
×
25
×
3mm的挂片、实验周期为
72h。
49.2.在h2s环境下的缓蚀性能:按照《sy/t7025-2014酸性油气田用缓蚀剂性能实验室评价方法》的标准进行失重实验测试,测试试样1-10和对比试样1-8的腐蚀效速率和缓蚀效率。测试试样1-10是由实施例1-10制得的缓蚀剂产品与甲醇按质量比为1:1混合搅拌制得;对比试样1-8是由对比例1-8制得的缓蚀剂产品与甲醇按质量比为1:1混合搅拌制得。且实验条件具体包括:试样加注浓度为30/ppm、持续通h2s、温度60℃、转速300r/min,腐蚀介质为5%氯化钠溶液、材质为20#碳钢且规格为50
×
25
×
3mm的挂片、实验周期为72h。
50.表1实施例1-10和对比例1-8的检测结果表
结合实施例1~3、对比例1和对比例6并结合表1可以看出,采用妥尔油酸制得产品性能优于环烷酸制得产品的性能,妥尔油酸和二乙烯三胺摩尔比会影响产品的缓蚀效果,且在妥尔油酸和二乙烯三胺摩尔比为1:1.15的时候,产品的缓蚀效果最优。
51.结合实施例1、实施例4~5和对比例2~5并结合表1可以看出,丙烯酸用量为妥尔油酸和二乙烯三胺总质量的30~60%时,产品的缓蚀效果较优,且丙烯酸用量为妥尔油酸和二乙烯三胺总质量的47%时,产品性能最优;邻二甲苯用量为妥尔油酸和二乙烯三胺总质量的15~30%时,产品的缓蚀效果较优。
52.结合实施例6~10和对比例7~8并结合表1可以看出,工艺参数的变化同样会对产品缓蚀效果产生影响,且在步骤s1中将反应过程中形成的共沸物回收精馏,步骤s2减压蒸馏处理,一方面提高了产品单位质量的纯度,改善了产品的缓蚀效果,另一方面提高了单位质量产品的产率,提高了生产效率。
53.本具体实施例仅仅是对本技术的解释,其并不是对本技术的限制,本领域技术人
员在阅读完本说明书后可以根据需要对本实施例做出没有创造性贡献的修改,但只要在本技术的权利要求范围内都受到专利法的保护。
再多了解一些
本文用于企业家、创业者技术爱好者查询,结果仅供参考。