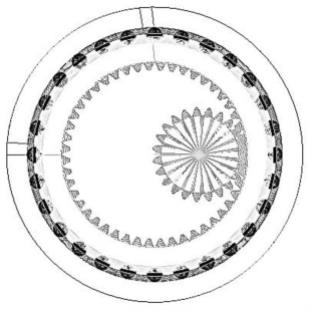
1.本发明属于回转支承技术领域,具体是一种回转支承动态性能的多变量多目标优化方法。
背景技术:
2.1.回转支承是一种新型机械器件,其主要由驱动齿轮、带齿圈的轴承外圈、滚动体、保持架等零件组成,能够同时承受轴向载荷、径向载荷和倾覆力矩的作用,具有结构紧凑,传动平稳,安装简便、易于维护、使用寿命长等突出优势而在工业机器人、风力发电机组、军用装备、医疗器械等众多领域获得广泛应用。
3.2.现有回转支承的分析技术主要集中在滚动体与滚道的静力学特性的设计分析,未考虑滚动体与轴承内外圈、保持架兜孔的静动态接触作用、驱动齿轮与齿圈的啮合作用等关键影响因素,对研发回转支承产品的综合性能缺乏准确的了解和掌握,从而需要反复设计、试制、调试和改进,导致产品研发周期长,耗费大量人力物力财力,且无法预估在实际应用中回转支承的动态性能。
4.3.现有回转支承的设计技术,还是采用传统的经验设计方法,按照静力学准则进行设计,未将回转支承的沟道曲率半径、保持架兜孔孔径、初始接触角、轮齿变位系数等关键设计参数与其动态性能进行多因素多目标的关联优化设计,导致开发的回转支承产品在实际工况下经常出现断齿、磨损、振动噪声大、动态精度差和疲劳寿命低等性能较差的问题,甚至由此发生严重故障,影响企业经济效益和生产安全。
技术实现要素:
5.本发明克服上述现有技术方法的缺陷,提出了一种回转支承动态性能的多变量多目标优化方法,该方法考虑回转支承各元件间的复杂接触力学作用关系,考虑了关键设计参数下单因素及多因素对回转支承动态特性的变化趋势,并采用实验设计(doe)进行全因子试验分析,获得最优参数组合,优化后的参数组合提高了回转支承的各项动态性能。相比经验设计方法和实验方法,开发周期短、成本低、操作便捷,可适用于不同工程应用需求,不同类型的回转支承产品的设计研发。对于了解和掌握实际工况条件下回转支承产品的各项性能指标和改进回转支承动态特性具有重要的指导意义。
6.本发明采用的技术方案为:一种回转支承动态性能的多变量多目标优化方法,该方法实现步骤如下:
7.步骤1:在adams软件中建立全参数化回转支承动力学模型。
8.步骤2:结合实际工况对回转支承各零部件进行相应约束及接触设置,并通过冲击函数法(impact)计算动态接触力。
9.步骤3:计算沟道曲率半径、保持架兜孔孔径、初始接触角、轮齿变位系数等单因素下滚动体与滚道间的接触力、齿轮啮合力、内齿圈质心径向和轴向振动位移动态性能的变化趋势。
10.步骤4:采用实验设计(doe)方法对回转支承沟道曲率半径、保持架兜孔孔径、初始接触角、轮齿变位系数等关键设计参数进行全因子实验设计,基于线性加权法,利用不同统一量纲法和权系数法构造设计新的目标函数,对回转支承动态性能进行多变量多目标优化,获得优化后的组合设计参数结果。
11.具体地,根据步骤1的具体操作步骤为:
12.利用adams自带齿轮模块对主动齿轮、内齿圈进行齿数、模数、节圆、齿顶高、变位系数等结构参数进行参数化定义与三维建模,结合回转支承的结构参数依次对内外圈四条虚拟滚道的直径的沟道曲率半径、滚动体直径和个数、保持架的内外直径、兜孔直径和个数等结构参数进行定义与三维建模,根据回转支承的结构参数和材料参数,对全部滚动体与内外套圈四条滚道的接触参数进行参数化定义,最后对齿轮、内外齿圈、保持架、滚动体进行装配,完成回转支承全参数化动力学建模。
13.具体地,根据步骤2的具体操作步骤为:
14.2.1)用连杆近似代替电机、同步带传动机构及减速器;对回转支承中各零部件添加相应约束,将外圈与大地、四条虚拟滚道以固定副的方式连接,将连杆与大地以固定副的方式连接,将连杆与保持架、小齿轮以转动副的方式连接,将内齿圈与齿圈、虚拟滚道以固定副的方式连接;再对回转支承进行相应的接触设置,具体接触为全部滚动体与虚拟滚道、保持架接触,一对内啮合齿轮接触。
15.2.2)采用冲击函数法(impact)计算接触力:运用公式:fn=kδe cv,式中的fn为法向接触力;k为刚度系数;δ为接触点法向穿透力;e为刚性力指数;c为阻尼系数;v为接触点法向相对速度。
16.具体地,根据步骤3的具体操作步骤为:
17.3.1)选取沟道曲率半径、保持架兜孔孔径、初始接触角、轮齿变位系数为关键设计参数,分别记为dv_1、dv_2、dv_3、dv_4,并分别均匀取四个离散量。
18.3.2)利用adams计算齿轮间啮合力(f1(x))、滚动体与滚道接触力(f2(x))、内齿圈质心轴向振动位移(f3(x))、内齿圈质心径向位移(f4(x)),后获得单因素关键设计参数影响下回转支承动力学的变化趋势。
19.具体地,根据步骤4的具体操作步骤为:
20.4.1)建立多目标优化数学模型,其公式:式中: t(x)=[f1(x),f2(x)
…
,fi(x)]
t
称为向量目标函数;fi(x)为子目标函数;s为设计变量离散集;并创建目标函数:式中:fi′
(x)为各子目标函数fi(x)经过统一量纲处理后的无量纲子目标函数;wi为各无量纲子目标函数fi′
(x)的权系数。
[0021]
4.2)进行统一量纲处理:均值化处理法:式中为子目标函数fi(x)的平均值;极小值化处理法:式中:min为子目标函数fi(x)值域中的最小值。
[0022]
4.3)通过排序法、熵值法及变异系数法选取权系数wi;排序法:根据i个无量纲子
目标函数的极小点,引入离差和均差,通过离差和均差来确定各无量纲子目标的权重;熵值法:通过提取各子目标函数的信息熵,实现对子目标函数的赋权;变异系数法:利用离散程度去判断子目标函数的贡献程度,计算各子目标函数的绝对和相对变异程度,后求取各子目标函数的变异系数并归一处理,得到变异系数权重。
[0023]
4.4)运用adans/view中的实验设计(doe)功能,对模型进行全因子试验设计,在dv_1~dv_4各均匀取四个值,获得系列不同组合参数下的回转支承动态性能,基于结果,采用线性加权法求解多目标并进行优化,公式:式中:fi(x),(i=1,2,
…
n)为每个子目标函数;wi为权系数。最终获得回转支承动态性能的最优参数组合。
[0024]
本发明的有益效果是:
[0025]
(1)本发明是回转支承动态性能的多变量多目标优化方法综合考虑了关键设计参数的单因素及多因素下对回转支承动力学特性的变化趋势,能够实现回转支承产品的性能最优,在实际应用中,具有重要的实际意义。
[0026]
(2)该方法采用试验设计(doe)进行全因子实验分析,相比于经验设计和实验方法,开发周期周期短、成本低、操作便捷,可适用于不同工程需求,对于了解和掌握回转支承的产品的各项性能指标和改进回转支承动态特性具有重要的指导意义,并对于研发高性能回转支承产品具有重要的实用价值。
附图说明
[0027]
图1是回转支承参数化动力学模型图。
[0028]
图2是虚拟滚道内部结构图。
[0029]
图3是滚动体编号图。
[0030]
图4是不同沟道曲率半径下回转支承动态特性曲线图。
[0031]
图5是不同兜孔孔径下回转支承动态特性曲线图。
[0032]
图6是不同初始接触角下回转支承动态特性曲线图。
[0033]
图7是不同齿变位系数下回转支承动态曲线图。
[0034]
图8是多目标优化前后回转支承动态特性曲线图。
具体实施方式
[0035]
下面将结合附图以及具体实施例来详细说明本发明:
[0036]
实施例1:一种回转支承动态性能的多变量多目标优化方法,该方法实现步骤如下:
[0037]
步骤1:在adams软件中建立全参数化回转支承动力学模型。利用adams 自带齿轮模块对主动齿轮、内齿圈进行齿数、模数、节圆、齿顶高、变位系数等结构参数进行参数化定义与三维建模,结合回转支承的结构参数依次对内外圈四条虚拟滚道的直径的沟道曲率半径、滚动体直径和个数、保持架的内外直径、兜孔直径和个数等结构参数进行定义与三维建模,根据回转支承的结构参数和材料参数,对全部滚动体与内外套圈四条滚道的接触参数进行参数化定义,最后对齿轮、内外齿圈、保持架、滚动体进行装配,完成回转支承全参数化动力学建模(图 1)。
[0038]
步骤2:结合实际工况对回转支承各零部件进行相应约束及接触设置,并通过冲击函数法(impact)计算动态接触力。
[0039]
2.1)用连杆近似代替电机、同步带传动机构及减速器;并分别建立了四条虚拟滚道分别为n1、n2、w1、w2(图2);后对回转支承中各零部件添加相应约束,将外圈与大地、虚拟滚道w1、w2以固定副的方式连接,将连杆与大地以固定副的方式连接,将连杆与保持架、小齿轮以转动副的方式连接,将内齿圈与齿圈、虚拟滚道n1、n2以固定副的方式连接;再对回转支承进行相应的接触设置,1~28 号滚动体(图3)分别与四条虚拟滚道及保持架接触,一对内啮合齿轮接触。
[0040]
2.2)采用冲击函数法(impact)计算接触力:运用公式:fn=kδe cv,式中的fn为法向接触力;k为刚度系数;δ为接触点法向穿透力;e为刚性力指数;c为阻尼系数;v为接触点法向相对速度。
[0041]
步骤3:计算沟道曲率半径、保持架兜孔孔径、初始接触角、轮齿变位系数等单因素下滚动体与滚道间的接触力、齿轮啮合力、内齿圈质心径向和轴向振动位移动态性能的变化趋势。
[0042]
3.1)选取沟道曲率半径(dv_1)、保持架兜孔孔径(dv_2)、初始接触角(dv_3)、轮齿变位系数(dv_4)为关键设计参数,并分别均匀取四个离散量;dv_1取 12.875mm、13.000mm、13.125mm、13.250mm,dv_2取25.2mm、25.4mm、25.6mm、 25.8mm,dv_3取40
°
、45
°
、50
°
、55
°
,dv_4取0、0.2、0.4、0.6。
[0043]
3.2)利用adams计算齿轮间啮合力(f1(x))、滚动体与滚道接触力(f2(x))、内齿圈质心轴向振动位移(f3(x))、内齿圈质心径向位移(f4(x))。将回转支承外圈固定,内齿圈施加轴向载荷6000n,倾覆力矩1
×
106n
·
mm,添加驱动转速 step(time,0,0d,0.1,310d),初始接触角为45
°
,保持架兜孔孔径为25.2mm,齿变位系数为0,沟道曲率半径分别取12.875mm、13.000mm、13.125mm、13.250mm,得到不同沟道曲率半径下回转支承动态特性曲线(图4);将初始接触角为45
°
,内外圈沟道曲率半径为13.0mm,齿变位系数为0,保持架兜孔孔径分别取25.2mm、 25.4mm、25.6mm、25.8mm,得到不同兜孔孔径下回转支承动态特性曲线(图5);将内外圈沟道曲率半径为13.0mm,保持架兜孔孔径为25.2mm,齿变位系数为0,初试接触角分别取40
°
、45
°
、50
°
、55
°
,得到同初始接触角下回转支承动态特性曲线(图6);将内外圈沟道曲率半径为13.0mm,初始接触角为45
°
,保持架兜孔孔径为25.2mm,齿变位系数分别取0、0.2、0.4、0.6,得到不同轮齿变位系数下回转支承动态特性曲线(图7)。
[0044]
步骤4:采用实验设计(doe)方法对回转支承沟道曲率半径、保持架兜孔孔径、初始接触角、轮齿变位系数等关键设计参数进行全因子实验设计,基于线性加权法,利用不同统一量纲法和权系数法构造设计新的目标函数,对回转支承动态性能进行多变量多目标优化,获得优化后的组合设计参数结果。
[0045]
4.1)建立多目标优化数学模型,其公式:式中: t(x)=[f1(x),f2(x)
…
,fi(x)]
t
称为向量目标函数;fi(x)为子目标函数;s为设计变量离散集;并创建目标函数:式中:fi′
(x)为各子目标函数fi(x)经过统一量纲处理后的无量纲子目标函数;wi为各无量纲子目标函数fi′
(x)的权系数。
[0046]
4.2)进行统一量纲处理:均值化处理法:式中为子目标函数fi(x)的平均值;极小值化处理法:式中:min为子目标函数fi(x)值域中的最小值。
[0047]
4.3)通过排序法、熵值法及变异系数法选取权系数wi;排序法:根据i个无量纲子目标函数的极小点,引入离差和均差,通过离差和均差来确定各无量纲子目标的权重;具体步骤为,首先设单目标优化模型:minfi′
(x),(i=1,2,3,4),求得最优解集为:得到离差:式中含义为无量纲子目标函数fi′
(x)在f
′
l
(x)的最优解x
l
处的函数值,均差:后求取权系数wi:并构造新的目标函数 f(x)=w1f4′
(x) w2f3′
(x) w3f2′
(x) w4f1′
(x);熵值法:通过提取各子目标函数的信息熵,实现对子目标函数的赋权;具体步骤为,首先假设每个子目标函数的取值分别为: fi(xj),(i=1,2,3,4;j=1,2,3
…
256),得到第i个子目标函数下第j个方案所占比重为:第i个子目标函数的熵值为:式中的k为常数,第i个子目标函数的差异性系数为:gi=1-ei,后对gi进行归一化处理,求取权系数:并构造新的目标函数:f(x)=w1f4′
(x) w2f3′
(x) w3f2′
(x) w4f1′
(x);变异系数法:利用离散程度去判断子目标函数的贡献程度,计算各子目标函数的绝对和相对变异程度,后求取各子目标函数的变异系数并归一处理,得到变异系数权重,具体步骤为:首先假设每个子目标函数的取值分别为 fi(xj),(i=1,2,3,4;j=1,2,3
…
256),得到第i个子目标函数fi(x)的均值为:第i个子目标函数的标准差为:第i个子目标变异系数为:后对各子目标的变异系数进行归一化处理,求取权系数:并造新的目标函数:f(x)=w1f4′
(x) w2f3′
(x) w3f2′
(x) w4f1′
(x)。
[0048]
4.4)运用adans/view中的实验设计(doe)功能,对模型进行全因子试验设计,在dv_1~dv_4各均匀取四个值,获得系列不同组合参数下的回转支承动态性能,基于结果,采用线性加权法求解多目标并进行优化,公式:式中:fi(x),(i=1,2,
…
n)为每个子目标函数,n为正整数,根据实际情况选取,wi为权系数。最终获得回转支承动态性能的最优参数组合。
[0049]
4.4)通过对子目标进行统一量纲处理,运用不同权系数求解方法,求得多组权系数,,并构建了多组新目标函数,对不同权系数和无量纲子目标函数所构建的新目标函数进行相应的计算,得到回转支承最优设计变量组合,如表1所示:
[0050][0051]
表1不同目标优化函数下求得的最优涉及组合
[0052]
4.4)运用adans/view中的实验设计(doe)功能,对模型进行全因子试验设计,在dv_1~dv_4各均匀取四个值,获得系列不同组合参数下的回转支承动态性能,基于结果,采用线性加权法求解多目标并进行优化,公式:式中:fi(x),(i=1,2,
…
n)为每个子目标函数;wi为权系数。获得回转支承的最优参数组合为沟道曲率半径、保持架兜孔孔径、初始接触角和齿变位系数分别为12.875mm、25.2mm、55
°
、0.6。将回转支承参数化动力学模型设计变量的取值设置为优化后的值,并与初始值进行对比,发现优化后的回转支承各项性能参数相比优化前都有了不同程度的改善(图8)。
[0053]
针对经验设计方法存在的缺陷问题,本发明提出基于参数化动力学模型的回转支承动态性能的多变量多目标优化方法,利用动力学仿真软件建立回转支承的全参数化动力学模型,利用试验设计(doe)方法和多变量多目标优化设计方法,生成回转支承的优化设计结果,预估关键设计参数组合作用下回转支承的动态性能,为研发高性能的回转支承产品提供新的设计方法。
[0054]
本发明提出回转支承产品的参数化动力学模型方法和多变量多目标优化设计方法,节省了大量的产品开发时间和人力,成本低廉,精度高,对于研发高性能回转支承产品具有重要的实用价值。
[0055]
上面结合图对本发明的具体实施方式作了详细说明,但是本发明并不限于上述实施方式,在本领域普通技术人员所具备的知识范围内,还可以在不脱离本发明宗旨的前提下做出各种变化。
再多了解一些
本文用于企业家、创业者技术爱好者查询,结果仅供参考。