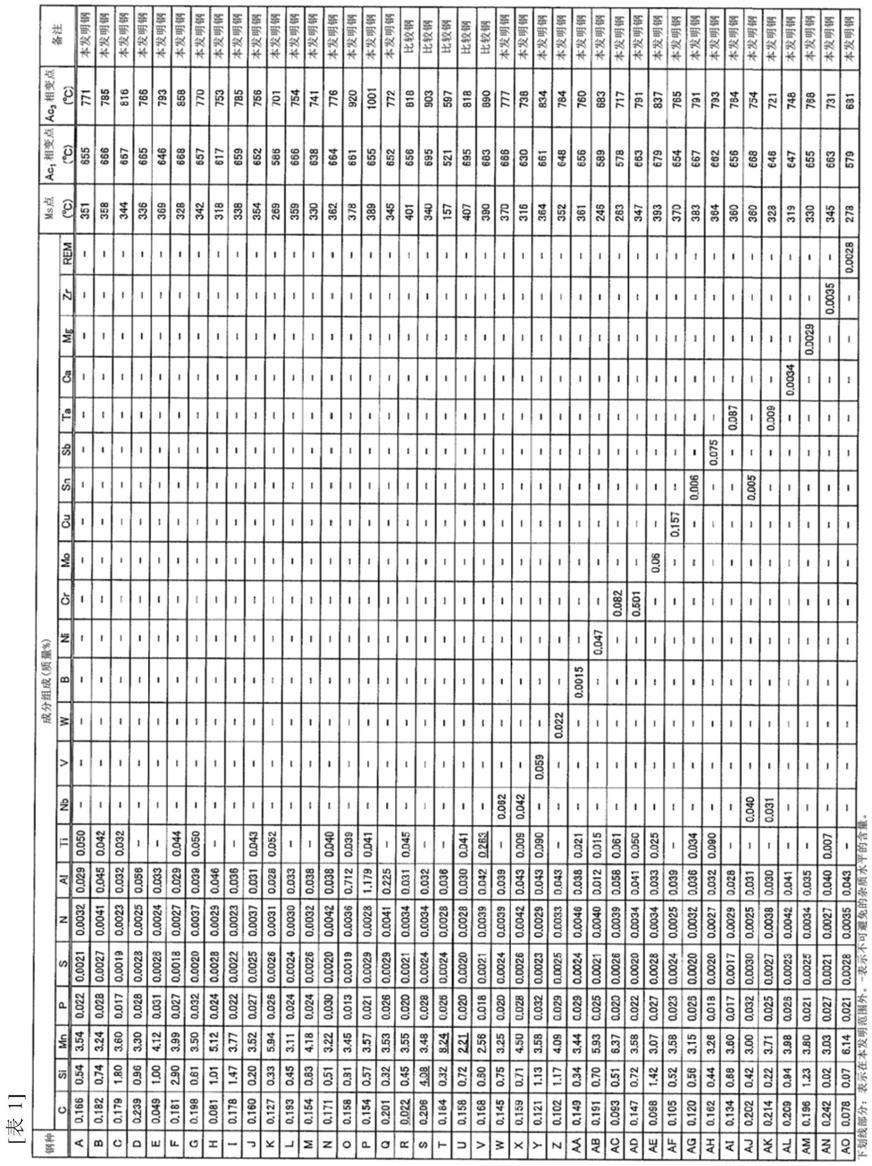
1.本发明涉及适合作为在汽车、电气等产业领域中使用的构件的、成形性优良的高强度钢板及制造方法。特别是本发明要得到具有980mpa以上的ts(拉伸强度)、不仅延展性优良而且扩孔性和弯曲性也优良的高强度钢板。
背景技术:
2.近年来,从保护地球环境的观点出发,提高汽车的燃料效率成为重要的课题。因此,想要通过车身材料的高强度化来实现薄壁化,从而使车身自身轻量化的动向变得活跃,但是,钢板的高强度化导致成形性的降低,因此期望开发出兼具高强度和高成形性的材料。
3.作为高强度且延展性优良的钢板,提出了利用残余奥氏体的加工诱发相变的高强度钢板。这样的钢板呈现出具有残余奥氏体的组织,在钢板的成形时因残余奥氏体而容易成形,另一方面,在成形后残余奥氏体发生马氏体化,因此具备高强度。
4.例如,专利文献1中提出了一种拉伸强度为1000mpa以上且总伸长率(el)为30%以上的利用了残余奥氏体的加工诱发相变的具有非常高的延展性的高强度钢板。这样的钢板通过将以c、si、mn作为基本成分的钢板奥氏体化后在贝氏体相变温度范围内进行淬火并等温保持、即进行所谓的等温淬火处理来制造。由于该等温淬火处理引起的c向奥氏体的富集而生成残余奥氏体,为了得到大量的残余奥氏体,需要添加超过0.3%的大量的c。但是,钢中的c浓度升高时,点焊性降低,特别是在超过0.3%的c浓度的情况下,点焊性降低显著,作为汽车用钢板难以实用化。另外,在上述专利文献中,以提高高强度薄钢板的延展性作为主要目的,因此没有考虑扩孔性、弯曲性。
5.在专利文献2中,使用高mn钢,实施在铁素体和奥氏体的双相区的热处理,由此得到高的强度-延展性平衡。但是,在专利文献2中,对于mn向未相变奥氏体中的富集所带来的延展性的提高没有进行研究,存在改善加工性的余地。
6.另外,在专利文献3中,使用中mn钢,实施在铁素体和奥氏体的双相区的热处理,由此使mn向未相变奥氏体中富集,从而形成稳定的残余奥氏体,使总伸长率提高。但是,没有考虑兼顾伸长率、扩孔性、弯曲性。此外,对于由残余奥氏体、马氏体构成的第二相中的mn以及c的分配控制所带来的扩孔性、弯曲性的提高也没有进行研究。在专利文献3的制造方法中,热处理时间短,mn的扩散速度慢,因此推测,对于除了伸长率以外还兼顾扩孔性、弯曲性而言,mn的富集不充分。
7.此外,在专利文献4中,使用中mn钢,在铁素体和奥氏体的双相区对热轧板实施长时间热处理,由此形成促进了mn向未相变奥氏体中的富集的长径比大的残余奥氏体,使均匀伸长率和扩孔性提高。但是,上述文献研究仅基于mn富集的高强度钢板的延展性和扩孔性的提高,对于由残余奥氏体、马氏体构成的第二相中的c和mn的分配控制所带来的扩孔性的提高、弯曲性及伸长率的兼顾没有进行研究。
8.现有技术文献
9.专利文献
10.专利文献1:日本特开昭61-157625号公报
11.专利文献2:日本特开平1-259120号公报
12.专利文献3:日本特开2003-138345号公报
13.专利文献4:日本专利第6123966号公报
技术实现要素:
14.发明所要解决的问题
15.本发明是鉴于上述各种现状而完成的,其目的在于提供具有980mpa以上的ts(拉伸强度)且具有优良的成形性的高强度钢板及其制造方法。在此所述的成形性表示延展性和扩孔性以及弯曲性。
16.用于解决问题的方法
17.本发明人为了解决上述问题,为了制造具有优良的成形性的高强度钢板,从钢板的成分组成和制造方法的观点出发反复进行了深入研究,发现了以下内容。
18.即发现:重要的是,对含有2.50质量%以上且8.00质量%以下的mn、根据需要适当地调整了ti等其他合金元素的成分组成的钢坯进行加热,在使精轧出口侧温度为750℃以上且1000℃以下的条件下热轧后,在300℃以上且750℃以下卷取。接着,根据需要在ac1相变点以下的温度范围内保持超过1800s,进行冷轧。然后,在ac3相变点-50℃以上的温度范围内保持20s以上且1800s以下后,冷却至马氏体相变开始温度以下的冷却停止温度。接着,再加热至120℃以上且450℃以下的范围内的再加热温度后,在上述再加热温度下保持2s以上且600s以下后,冷却至室温,由此,在接下来的退火工序中,生成成为长径比大的微细的残余奥氏体的核的c富集的膜状奥氏体。上述冷却后,在ac1相变点以上且ac1相变点 150℃以下的温度范围内保持20s以上且600s以下后,冷却至100℃以下,进而,在超过100℃且400℃以下的温度范围内保持10s以上后,进行冷却。可知由此能够制造如下具有优良的成形性的高强度钢板:得到以面积率计铁素体为30%以上且80%以下、回火马氏体为3.0%以上且35%以下、残余奥氏体为8%以上的钢组织。此外可知,在该钢组织中,长径比为2.0以上且短轴为1μm以下的残余奥氏体的面积率除以全部残余奥氏体的面积率而得到的值为0.3以上,并且,残余奥氏体中的平均mn量(质量%)除以铁素体中的平均mn量(质量%)而得到的值为1.5以上,并且残余奥氏体中的平均mn量(质量%)除以铁素体中的平均mn量(质量%)而得到的值乘以残余奥氏体的平均长径比而得到的值为3.0以上,并且,残余奥氏体中的平均c量(质量%)除以铁素体中的平均c量(质量%)而得到的值为3.0以上,并且,残余奥氏体中的平均c量(质量%)除以残余奥氏体中的平均mn量(质量%)而得到的值为0.05以上,并且,钢中扩散性氢量为0.3质量ppm以下。
19.本发明是基于以上见解而完成的,其主旨如下所述。
20.[1]一种高强度钢板,其具有:
[0021]
如下成分组成:以质量%计,含有c:0.030%以上且0.250%以下、si:0.01%以上且3.00%以下、mn:2.50%以上且8.00%以下、p:0.001%以上且0.100%以下、s:0.0001%以上且0.0200%以下、n:0.0005%以上且0.0100%以下、al:0.001%以上且2.000%以下,余量由fe和不可避免的杂质构成;以及
[0022]
如下钢组织:以面积率计铁素体为30%以上且80%以下、回火马氏体为3.0%以上
且35%以下、残余奥氏体为8%以上,长径比为2.0以上且短轴为1μm以下的残余奥氏体的面积率除以全部残余奥氏体的面积率而得到的值为0.3以上,残余奥氏体中的平均mn量(质量%)除以铁素体中的平均mn量(质量%)而得到的值为1.5以上,并且残余奥氏体中的平均mn量(质量%)除以铁素体中的平均mn量(质量%)而得到的值乘以残余奥氏体的平均长径比而得到的值为3.0以上,残余奥氏体中的平均c量(质量%)除以铁素体中的平均c量(质量%)而得到的值为3.0以上,残余奥氏体中的平均c量(质量%)除以残余奥氏体中的平均mn量(质量%)而得到的值为0.05以上,
[0023]
并且,钢中扩散性氢量为0.3质量ppm以下。
[0024]
[2]如[1]所述的高强度钢板,其中,上述成分组成以质量%计还含有选自ti:0.200%、nb:0.200%以下、v:0.500%以下、w:0.500%以下、b:0.0050%以下、ni:1.000%以下、cr:1.000%以下、mo:1.000%以下、cu:1.000%以下、sn:0.200%以下、sb:0.200%以下、ta:0.100%以下、ca:0.0050%以下、mg:0.0050%以下、zr:0.0050%以下、rem:0.0050%以下中的至少一种元素。
[0025]
[3]如[1]或[2]所述的高强度钢板,其中,在表面还具有镀锌层。
[0026]
[4]如[3]所述的高强度钢板,其中,上述镀锌层为合金化镀锌层。
[0027]
[5]一种高强度钢板的制造方法,其中,对具有[1]或[2]所述的成分组成的钢坯进行加热,在精轧出口侧温度为750℃以上且1000℃以下的条件下进行热轧,在300℃以上且750℃以下进行卷取,实施冷轧,然后,在ac3相变点-50℃以上的温度范围内保持20s以上且1800s以下后,冷却至马氏体相变开始温度以下的冷却停止温度,再加热至120℃以上且450℃以下的范围内的再加热温度后,在上述再加热温度下保持2s以上且600s以下,然后冷却至室温,然后,在ac1相变点以上且ac1相变点 150℃以下的温度范围内保持20s以上且600s以下后,冷却至100℃以下,进而,在超过100℃且400℃以下的温度范围内保持10s以上,然后进行冷却。
[0028]
[6]如[5]所述的高强度钢板的制造方法,其中,在上述卷取后、冷轧前,在ac1相变点以下的温度范围保持超过1800s。
[0029]
[7]如[5]或[6]所述的高强度钢板的制造方法,其中,在上述ac1相变点以上且ac1相变点 150℃以下的温度范围内保持20s以上且600s以下后进行冷却,实施镀锌处理,然后,冷却至上述100℃以下。
[0030]
[8]如[7]所述的高强度钢板的制造方法,其特征在于,在上述镀锌处理之后接着在450℃以上且600℃以下实施合金化处理。
[0031]
发明效果
[0032]
根据本发明,可以得到具有980mpa以上的ts(拉伸强度)、成形性、特别是不仅延展性而且扩孔性和弯曲性也优良的高强度钢板。通过将由本发明的制造方法得到的高强度钢板应用于例如汽车结构构件,能够实现车身轻量化所带来的燃料效率改善,产业上的利用价值极大。
具体实施方式
[0033]
以下,对本发明具体地进行说明。需要说明的是,表示成分元素的含量的“%”只要没有特别说明则是指“质量%”。
[0034]
(1)对在本发明中将钢的成分组成限定为上述范围的理由进行说明。
[0035]
c:0.030%以上且0.250%以下
[0036]
c是用于确保回火马氏体、使强度升高的必要元素。另外,c是对提高残余奥氏体的稳定性、提高钢的延展性有效的元素。c量小于0.030%时,难以确保期望的回火马氏体的面积率,得不到期望的强度。另外,难以确保充分的残余奥氏体的面积率,得不到良好的延展性。另一方面,使c超过0.250%而过量添加时,硬质的回火马氏体的面积率变得过大,扩孔试验时,回火马氏体的晶界处的微孔增加,此外,龟裂的传播进行,扩孔性降低。另外,焊接部和热影响区的硬化变得显著,焊接部的机械特性降低,因此,点焊性、电弧焊接性等也劣化。从这样的观点出发,将c量设定为0.030%以上且0.250%以下。优选为0.080%以上且0.200%以下。
[0037]
si:0.01%以上且3.00%以下
[0038]
si使铁素体的加工硬化能力提高,因此对确保良好的延展性是有效的。si量小于0.01%时,其添加效果差,因此,将下限设定为0.01%。但是,超过3.00%的si的过量添加不仅引起因钢的脆化所致的延展性的降低和弯曲性的降低,而且还引起因红锈等的产生所致的表面性状的劣化。此外,导致镀层品质的降低。因此,si设定为0.01%以上且3.00%以下。优选为0.20%以上且2.00%以下。更优选为0.20%以上且小于0.70%。
[0039]
mn:2.50%以上且8.00%以下
[0040]
mn在本发明中是极其重要的添加元素。mn是使残余奥氏体稳定化的元素,而且是对确保良好的延展性有效的、并且通过固溶强化使钢的强度升高的元素。另外,mn对于确保mn富集的稳定的残余奥氏体、确保期望的残余奥氏体中的平均mn量(质量%)除以铁素体中的平均mn量(质量%)而得到的值、得到良好的延展性是有效的。这样的作用通过使钢的mn量为2.50%以上而表现出。但是,mn量超过8.00%的过量添加有时形成因mn偏析所致的不均匀组织、导致扩孔性的降低。另外,得不到期望的残余奥氏体中的平均c量(质量%)除以残余奥氏体中的平均mn量(质量%)而得到的值,难以兼顾良好的延展性和弯曲性。此外,使化学转化处理性和镀层品质劣化。从这样的观点出发,将mn量设定为2.50%以上且8.00%以下。优选为3.10%以上且6.00%以下。更优选为3.20%以上且4.20%以下。
[0041]
p:0.001%以上且0.100%以下
[0042]
p是具有固溶强化的作用、可以根据期望的强度而添加的元素。另外,p是促进铁素体相变因此对复合组织化也有效的元素。为了得到这样的效果,需要使p量为0.001%以上。另一方面,p量超过0.100%时,导致焊接性的劣化,并且在对镀锌层进行合金化处理的情况下,使合金化速度降低,损害镀锌层的品质。因此,p量设定为0.001%以上且0.100%以下、优选设定为0.005%以上且0.050%以下。
[0043]
s:0.0001%以上且0.0200%以下
[0044]
s向晶界偏析而在热加工时使钢脆化,并且以硫化物的形式存在而使局部变形能力降低。因此,s量需要设定为0.0200%以下、优选设定为0.0100%以下、更优选设定为0.0050%以下。但是,从生产技术上的制约出发,s量需要设定为0.0001%以上。因此,s量设定为0.0001%以上且0.0200%以下、优选设定为0.0001%以上且0.0100%以下、更优选设定为0.0001%以上且0.0050%以下。
[0045]
n:0.0005%以上且0.0100%以下
[0046]
n是使钢的耐时效性劣化的元素。特别是n量超过0.0100%时,耐时效性的劣化变得显著。n量越少越优选,但从生产技术上的制约出发,n量需要设定为0.0005%以上。因此,n量设定为0.0005%以上且0.0100%、优选设定为0.0010%以上且0.0070%以下。
[0047]
al:0.001%以上且2.000%以下
[0048]
al是使铁素体与奥氏体的双相区扩大、对降低机械特性的退火温度依赖性、即材质稳定性有效的元素。al的含量小于0.001%时,其添加效果差,因此将下限设定为0.001%。另外,al还是作为脱氧剂发挥作用、对钢的洁净度有效的元素,优选在脱氧工序中添加。但是,超过2.000%的大量添加导致连续铸造时的钢片产生裂纹的风险提高,使制造性降低。从这样的观点出发,将al量设定为0.001%以上且2.000%以下。优选为0.200%以上且1.200%以下。
[0049]
另外,除了上述成分以外,还可以以质量%计含有选自ti:0.200%以下、nb:0.200%以下、v:0.500%以下、w:0.500%以下、b:0.0050%以下、ni:1.000%以下、cr:1.000%以下、mo:1.000%以下、cu:1.000%以下、sn:0.200%以下、sb:0.200%以下、ta:0.100%以下、ca:0.0050%以下、mg:0.0050%以下、zr:0.0050%以下、rem(稀土金属(rare earth metal)的缩写):0.0050%以下中的至少一种元素。
[0050]
ti:0.200%以下
[0051]
ti对钢的析出强化是有效的,使铁素体的强度提高由此能够降低与硬质第二相(回火马氏体或残余奥氏体)的硬度差,能够确保更良好的扩孔性。在添加ti的情况下,优选为0.005%以上。进一步优选为0.010%以上。但是,超过0.200%时,有时硬质的回火马氏体的面积率变得过大,在扩孔试验时回火马氏体的晶界处的微孔增加,此外,龟裂的传播进行,扩孔性降低。因此,在添加ti的情况下,将其添加量设定为0.200%以下。优选设定为0.100%以下。
[0052]
nb:0.200%以下、v:0.500%以下、w:0.500%以下
[0053]
nb、v、w对钢的析出强化是有效的。另外,与添加ti的效果同样,使铁素体的强度提高,由此能够降低与硬质第二相(回火马氏体或残余奥氏体)的硬度差,能够确保更良好的扩孔性。在添加nb、v、w的情况下,优选分别为0.005%以上。更优选分别为0.010%以上。但是,nb超过0.200%、v、w超过0.500%时,有时硬质的回火马氏体的面积率变得过大,在扩孔试验时回火马氏体的晶界处的微孔增加,此外,龟裂的传播进行,扩孔性降低。因此,在添加nb的情况下,其添加量设定为0.200%以下,优选设定为0.100%以下。在添加v、w的情况下,其添加量设定为0.500%以下、优选设定为0.300%以下。
[0054]
b:0.0050%以下
[0055]
b具有抑制铁素体从奥氏体晶界的生成和生长的作用,使铁素体的强度提高,由此能够降低与硬质第二相(回火马氏体或残余奥氏体)的硬度差,能够确保更良好的扩孔性。在添加b的情况下,优选为0.0003%以上。但是,超过0.0050%时,有时成形性降低。因此,在添加b的情况下,其添加量设定为0.0050%以下。优选设定为0.0030%以下。
[0056]
ni:1.000%以下
[0057]
ni是使残余奥氏体稳定的元素,对确保更良好的延展性是有效的,此外,ni是通过固溶强化使钢的强度升高的元素。在添加ni的情况下,优选为0.005%以上。另一方面,添加超过1.000%时,有时硬质的回火马氏体的面积率变得过大,在扩孔试验时回火马氏体的晶
界处的微孔增加,此外,龟裂的传播进行,扩孔性降低。因此,在添加ni的情况下,其添加量设定为1.000%以下。
[0058]
cr:1.000%以下、mo:1.000%以下
[0059]
cr、mo具有使强度与延展性的平衡提高的作用,因此可以根据需要添加。在添加cr、mo的情况下,优选cr:0.005%以上、mo:0.005%以上。但是,分别地超过cr:1.000%、mo:1.000%而过量添加时,有时硬质的回火马氏体的面积率变得过大,在扩孔试验时回火马氏体的晶界处的微孔增加,此外,龟裂的传播进行,扩孔性降低。因此,在添加这些元素的情况下,将其量分别设定为cr:1.000%以下、mo:1.000%以下。
[0060]
cu:1.000%以下
[0061]
cu是对钢的强化有效的元素,可以根据需要添加。在添加cu的情况下,优选为0.005%以上。另一方面,添加超过1.000%时,有时硬质的回火马氏体的面积率变得过大,在扩孔试验时回火马氏体的晶界处的微孔增加,此外,龟裂的传播进行,扩孔性降低。因此,在添加cu的情况下,将其量设定为1.000%以下。
[0062]
sn:0.200%以下、sb:0.200%以下
[0063]
从抑制因钢板表面的氮化、氧化而产生的钢板表层的约几十μm的区域的脱碳的观点出发,sn和sb根据需要添加。sn和sb对于抑制这样的氮化、氧化、防止在钢板表面回火马氏体的面积率减少、确保强度、材质稳定性是有效的。在添加sn、sb的情况下,优选分别为0.002%以上。另一方面,对于它们中的任一种元素,超过0.200%而过量添加时,有时导致韧性的降低。因此,在添加sn和sb的情况下,其含量分别设定为0.200%以下。
[0064]
ta:0.100%以下
[0065]
与ti、nb同样,ta生成合金碳化物、合金碳氮化物而有助于高强度化。除此以外,认为还具有如下效果:通过一部分固溶在nb碳化物、nb碳氮化物中而生成(nb、ta)(c、n)这样的复合析出物,显著地抑制析出物的粗大化,使由析出强化带来的对强度的贡献稳定。因此,优选含有ta。在此,在添加ta的情况下,优选为0.001%以上。另一方面,即使过量地添加ta,有时析出物稳定化效果也饱和,而且合金成本也增加。因此,在添加ta的情况下,其含量设定为0.100%以下。
[0066]
ca:0.0050%以下、mg:0.0050%以下、zr:0.0050%以下、rem:0.0050%以下
[0067]
ca、mg、zr和rem是用于使硫化物的形状球状化、改善硫化物对扩孔性的不良影响的有效元素。在添加这些元素的情况下,优选分别为0.0005%以上。但是,分别超过0.0050%的过量添加有时引起夹杂物等的增加、引起表面和内部缺陷等。因此,在添加ca、mg、zr和rem的情况下,其添加量分别设定为0.0050%以下。
[0068]
上述成分以外的余量为fe和不可避免的杂质。
[0069]
(2)接着,对钢组织进行说明。
[0070]
铁素体的面积率:30%以上且80%以下
[0071]
为了确保充分的延展性,需要使铁素体的面积率为30%以上。另外,为了确保980mpa以上的拉伸强度,需要使软质的铁素体的面积率为80%以下。需要说明的是,在此所述的铁素体是指多边形铁素体、粒状铁素体或针状铁素体,是比较软质且富有延展性的铁素体。优选为40%以上且75%以下。
[0072]
回火马氏体的面积率:3.0%以上且35%以下
[0073]
为了确保高的局部伸长率、良好的扩孔性和弯曲性以及高屈服比,回火马氏体需要为3.0%以上。为了实现高的局部伸长率和良好的扩孔性、弯曲性,回火马氏体的面积率需要设定为3.0%以上。另一方面,含有过量的回火马氏体时,延展性和弯曲性降低,因此需要使回火马氏体的面积率为35%以下。优选为5.0%以上且20%以下。
[0074]
需要说明的是,铁素体和回火马氏体的面积率可以如下求出:对与钢板的轧制方向平行的板厚截面(l截面)进行研磨后,用3体积%硝酸乙醇溶液进行腐蚀,对于板厚1/4位置(相当于在深度方向上距钢板表面为板厚的1/4的位置),利用sem(扫描电子显微镜)以2000倍的倍率观察10个视野,使用所得到的组织图像,利用media cybernetics公司的image-pro算出10个视野的各组织(铁素体、回火马氏体)的面积率,将这些值平均,从而求出铁素体、回火马氏体的面积率。另外,在上述组织图像中,铁素体呈现为灰色的组织(基体组织),回火马氏体呈现为在白色的(淬火)马氏体的内部具有灰色的内部结构的组织。
[0075]
残余奥氏体的面积率:8%以上
[0076]
为了确保充分的延展性,需要使残余奥氏体的面积率为8%以上。优选为12%以上且25%以下。
[0077]
需要说明的是,残余奥氏体的面积率如下求出:将钢板研磨至距板厚1/4位置0.1mm的面后,通过化学研磨进一步研磨0.1mm,对由此得到的面利用x射线衍射装置使用cokα射线测定fcc铁的{200}、{220}、{311}面和bcc铁的{200}、{211}、{220}面的衍射峰的各个积分强度比,将所得到的9个积分强度比平均,从而求出残余奥氏体的面积率。
[0078]
长径比为2.0以上且短轴为1μm以下的残余奥氏体的面积率除以全部残余奥氏体的面积率而得到的值为0.3以上
[0079]
长径比为2.0以上且短轴为1μm以下的残余奥氏体的面积率除以全部残余奥氏体的面积率而得到的值为0.3以上在本发明中是重要的技术特征。长径比为2.0以上且短轴为1μm以下的残余奥氏体抑制扩孔工序前的冲裁时的空隙产生,因此有助于提高扩孔性。为了确保良好的扩孔性,需要在确保足以得到高延展性的残余奥氏体的面积率的基础上使长径比为2.0以上且短轴为1μm以下的残余奥氏体的面积率较多。优选为0.5以上。长径比的上限值优选为15.0以下。短轴的下限值优选为作为ebsd的检测极限的0.05μm以上。
[0080]
马氏体和残余奥氏体通过ebsd(电子背散射衍射,electron backscattered diffraction)的phase map(相位图)识别。需要说明的是,残余奥氏体的长径比如下算出:使用photoshop elements 13,描绘出与残余奥氏体晶粒外切的椭圆,用其长轴长度除以短轴长度,由此算出残余奥氏体的长径比。
[0081]
残余奥氏体中的平均mn量(质量%)除以铁素体中的平均mn量(质量%)而得到的值:1.5以上
[0082]
残余奥氏体中的平均mn量(质量%)除以铁素体中的平均mn量(质量%)而得到的值为1.5以上在本发明中是极其重要的技术特征。为了确保良好的延展性,需要mn富集的稳定的残余奥氏体的面积率高。优选为2.0以上。残余奥氏体中的平均mn量越高则延展性越提高,因此,上限值没有特别限定,但即使超过10.0,延展性的提高效果饱和,因此优选为10.0以下。
[0083]
残余奥氏体中的平均mn量(质量%)除以铁素体中的平均mn量(质量%)而得到的值乘以残余奥氏体的平均长径比而得到的值为3.0以上
[0084]
残余奥氏体中的平均mn量(质量%)除以铁素体中的平均mn量(质量%)而得到的值乘以残余奥氏体的平均长径比而得到的值为3.0以上是极其重要的技术特征。为了确保良好的延展性,需要长径比大、且mn富集的稳定的残余奥氏体的面积率高。优选为4.0以上。另外,优选的上限值为20.0以下。
[0085]
残余奥氏体中的c量(质量%)除以铁素体中的平均c量(质量%)而得到的值:3.0以上
[0086]
残余奥氏体中的c量(质量%)除以铁素体中的平均c量(质量%)而得到的值为3.0以上在本发明中是极其重要的技术特征。残余奥氏体中的c量增加时,在弯曲变形中残余奥氏体残留至高应变区域,因此弯曲性提高。因此,为了确保良好的延展性和弯曲性,需要c富集的稳定的残余奥氏体的面积率高。优选为5.0以上。另外,优选的上限值为10.0以下。
[0087]
上述残余奥氏体中的平均c量(质量%)除以上述残余奥氏体中的平均mn量(质量%)而得到的值为0.05以上
[0088]
残余奥氏体中的c量(质量%)除以残余奥氏体中的mn量(质量%)而得到的值为0.05以上在本发明中是极其重要的技术特征。为了确保良好的弯曲性,需要在mn富集的稳定的残余奥氏体中c量也富集的残余奥氏体的面积率高。通过不仅使mn而且使c也富集在残余奥氏体中,稳定的残余奥氏体存在至高应变区域,因此能够兼顾良好的延展性和弯曲性。优选为0.06以上。优选的上限值为0.10以下。
[0089]
残余奥氏体和铁素体中的c和mn量使用三维原子探针(3dap:3dimensional atom probe)从板厚1/4位置切割出试样来进行测定。首先裁取包含残余奥氏体和铁素体的部位,利用聚焦离子束加工成针状试样。通过3dap对针状试样施加电压,对此时放出的c和mn离子进行分析,用对每个残余奥氏体和铁素体测定的c和mn原子数除以其他总原子数,由此能够以原子%的方式确定mn量。对测定视野内的随机30个残余奥氏体晶粒和30个铁素体晶粒进行上述操作,求出c、mn量的定量分析结果的平均值。残余奥氏体和铁素体中的c和mn量(质量%)通过将上述得到的c、mn量(原子%)换算成质量%而得到。
[0090]
钢中扩散性氢量为0.3质量ppm以下
[0091]
钢中扩散性氢量为0.3质量ppm以下在本发明中是重要的技术特征。为了确保高的局部伸长率和良好的扩孔性,需要将钢中扩散性氢量设定为0.3质量ppm以下。钢中扩散性氢量优选为0.2质量ppm以下的范围内。从退火板裁取长度为30mm、宽度为5mm的试验片,磨削除去镀层后,测定钢中的扩散性氢量和扩散性氢的放出峰。放出峰利用热解析法(thermal desorption spectrometry:tds)进行测定,升温速度设定为200℃/小时。需要说明的是,将在300℃以下检测到的氢设为扩散性氢。
[0092]
在本发明的钢组织中,除了铁素体、回火马氏体和残余奥氏体以外,即使以面积率计在10%以下的范围内包含淬火马氏体、贝氏体、珠光体、渗碳体等碳化物,也不会损害本发明效果。
[0093]
需要说明的是,在钢板的表面可以具有镀锌层。镀锌层可以是进行合金化处理而得到的合金化镀锌层。
[0094]
(3)接着,对制造条件进行说明。
[0095]
钢坯的加热温度
[0096]
虽然没有特别限定,但钢坯的加热温度优选设定为1100℃以上且1300℃以下。在
钢坯的加热阶段存在的析出物在最终得到的钢板内作为粗大的析出物存在,无助于强度,因此可以使铸造时析出的ti、nb系析出物再溶解。此外,从除去钢坯表层的气泡、偏析等、进一步减少钢板表面的龟裂、凹凸而实现更平滑的钢板表面的观点出发,钢坯的加热温度也优选设定为1100℃以上。另一方面,从减少与氧化量的增加相伴的氧化皮损耗的观点出发,钢坯的加热温度优选设定为1300℃以下。更优选设定为1150℃以上且1250℃以下。
[0097]
为了防止宏观偏析,钢坯优选通过连铸法来制造,但也可以通过铸锭法、薄坯体铸造法等来制造。另外,制造钢坯后,除了暂时冷却至室温然后进行再次加热的现有方法以外,也可以毫无问题地应用不冷却至室温地以温片的状态装入加热炉中或者略微进行保温后立即进行轧制的直送轧制/直接轧制等节能工艺。另外,钢坯在通常的条件下通过粗轧制成薄板坯,但是,在着眼于加热温度的情况下,从防止热轧时的故障的观点出发,优选在精轧前使用棒加热器等对薄板坯进行加热。
[0098]
热轧的精轧出口侧温度:750℃以上且1000℃以下
[0099]
加热后的钢坯通过粗轧和精轧进行热轧,制成热轧钢板。此时,精轧出口侧温度超过1000℃时,氧化物(氧化皮)的生成量急剧增大,钢基与氧化物的界面粗糙,存在酸洗、冷轧后的表面品质劣化的倾向。另外,如果在酸洗后局部地存在热轧氧化皮的残留等,则对延展性、扩孔性带来不良影响。此外,有时结晶粒径变得过度粗大、加工时产生压制品表面粗糙。另一方面,精轧出口侧温度低于750℃时,轧制载荷增大,轧制负荷增大,奥氏体在未再结晶状态下的压下率提高,异常的织构发达。由此,最终制品的面内各向异性变得显著,材质的均匀性(材质稳定性)受损,不仅如此,残余奥氏体的长径比减小,延展性和扩孔性降低。因此,需要将热轧的精轧出口侧温度设定为750℃以上且1000℃以下。优选设定为800℃以上且950℃以下。
[0100]
热轧后的卷取温度:300℃以上且750℃以下
[0101]
热轧后的卷取温度超过750℃时,热轧板组织的铁素体的结晶粒径变大,最终退火板的残余奥氏体的长径比减小,难以确保期望的长径比为2.0以上且短轴为1μm以下的残余奥氏体的面积率除以全部残余奥氏体的面积率而得到的值,扩孔性降低。另一方面,热轧后的卷取温度低于300℃时,热轧板强度升高,冷轧中的轧制负荷增大,或者产生板形状的不良,因此生产率降低。因此,需要将热轧后的卷取温度设定为300℃以上且750℃以下。优选设定为400℃以上且650℃以下。
[0102]
需要说明的是,也可以在热轧时将粗轧板彼此接合而连续地进行精轧。另外,也可以对粗轧板暂时进行卷取。另外,为了降低热轧时的轧制载荷,可以使精轧的一部分或全部为润滑轧制。从钢板形状的均匀化、材质的均匀化的观点出发,也优选进行润滑轧制。需要说明的是,在进行润滑轧制的情况下,润滑轧制时的摩擦系数优选设定为0.10以上且0.25以下。
[0103]
对这样制造的热轧钢板任选地进行酸洗。酸洗能够除去钢板表面的氧化物,进一步改善化学转化处理性、镀层品质,因此优选实施。另外,可以进行一次酸洗,也可以分多次进行酸洗。
[0104]
在ac1相变点以下的温度范围内保持超过1800s
[0105]
在ac1相变点以下的温度范围内保持超过1800s使用于接着实施冷轧的钢板软质化,因此优选。在超过ac1相变点的温度范围内保持的情况下,有时mn富集在奥氏体中,冷却
后,生成硬质的马氏体和残余奥氏体,不能进行钢板的软质化。有时在之后的退火工序中,从晶界形成残余奥氏体,长径比小的残余奥氏体增加,难以确保期望的长径比为2.0以上且短轴为1μm以下的残余奥氏体的面积率除以全部残余奥氏体的面积率而得到的值,扩孔性降低。另外,即使在ac1相变点以下的温度范围内而保持1800s以下的情况下,有时不能除去热轧后的应变,不能进行钢板的软质化。
[0106]
需要说明的是,热处理方法为连续退火、间歇退火中的任一种退火方法均可。另外,上述热处理后,冷却至室温,但其冷却方法和冷却速度没有特别规定,间歇退火中的炉冷、空冷和连续退火中的气体喷射冷却、喷雾冷却、水冷等中的任一种冷却均可。另外,实施酸洗处理的情况下可以采用常规方法。
[0107]
冷轧
[0108]
对所得到的钢板实施冷轧。冷轧率没有限制,优选为15%以上且80%以下。通过以该范围实施冷轧,可得到充分地再结晶的期望的组织,延展性进一步提高。
[0109]
在ac3相变点-50℃以上的温度范围内保持20s以上且1800s以下
[0110]
在低于ac3相变点-50℃的温度范围内保持的情况下,mn富集在奥氏体中,在冷却中不发生马氏体相变,不能得到长径比大的残余奥氏体的核。由此,在之后的退火工序中,从晶界形成残余奥氏体,长径比小的残余奥氏体增加,得不到期望的组织。即使在ac3相变点-50℃以上的温度范围内而保持少于20s的情况下,没有进行充分的再结晶,得不到期望的组织,因此延展性降低。另一方面,保持超过1800s的情况下,有时最终退火处理后硬质的回火马氏体增加,延展性和弯曲性降低。
[0111]
冷却至马氏体相变开始温度以下的冷却停止温度
[0112]
在超过马氏体相变开始温度的冷却停止温度的情况下,发生相变的马氏体量少时,未相变奥氏体在最终冷却中全部发生马氏体相变,不能得到长径比大的残余奥氏体的核,在之后的退火工序中,从晶界形成残余奥氏体,长径比小的残余奥氏体增加,得不到期望的组织。优选为马氏体相变开始温度-250℃以上且马氏体相变开始温度-50℃以下。
[0113]
再加热至120℃以上且450℃以下的范围内的再加热温度后,在上述再加热温度下保持2s以上且600s以下
[0114]
在低于120℃的再加热温度的情况下,c没有在通过之后的退火工序形成的残余奥氏体中富集,得不到期望的组织。在超过450℃的再加热温度的情况下,长径比大的残余奥氏体的核分解,长径比小的残余奥氏体增加,得不到期望的组织。另外,保持少于2s的情况下也同样,不能得到长径比大的残余奥氏体的核,得不到期望的组织。此外,在保持超过600s的情况下,长径比大的残余奥氏体的核分解,长径比小的残余奥氏体增加,得不到期望的组织。该再加热和保持后冷却至室温。冷却的方法没有特别限定,优选例如进行空冷、气体冷却或喷雾冷却至200℃以下,进一步进行水冷。另外,可以根据需要进行酸洗。在进行酸洗的情况下可以采用常规方法。
[0115]
在ac1相变点以上且ac1相变点 150℃以下的温度范围内保持20s以上且600s以下
[0116]
在ac1相变点以上且ac1相变点 150℃以下的温度范围内保持20s以上且600s以下在本发明中是极其重要的发明技术特征。在低于ac1相变点的温度范围及少于20s的条件下保持的情况下,在升温中形成的碳化物未熔化完全,难以确保充分的面积率的回火马氏体和残余奥氏体,强度降低。另外,在超过ac1相变点 150℃的温度范围时,退火处理后马氏体
增加,最终退火处理后的回火马氏体变得过量,得不到期望的组织。另外,mn向奥氏体中的富集和c向奥氏体中的富集不充分,延展性和弯曲性降低,此外,得不到充分的面积率的残余奥氏体,延展性降低。优选为ac1相变点 100℃以下。此外,在保持超过600s的情况下,退火处理后马氏体增加,最终退火处理后的回火马氏体变得过量,得不到期望的组织。另外,mn向奥氏体中的富集和c向奥氏体中的富集不充分,延展性和弯曲性降低,此外,不能得到用于确保延展性的充分的面积率的残余奥氏体。
[0117]
冷却至100℃以下
[0118]
通过冷却至100℃以下,可形成能够确保拉伸强度的充分的马氏体量。作为冷却停止温度,鉴于制造成本,优选为约20℃以上且约50℃以下。
[0119]
镀锌处理
[0120]
在进行镀锌处理的情况下,在上述ac1相变点以上且ac1相变点 150℃以下的温度范围内保持20s以上且600s以下后进行冷却,在上述冷却至100℃以下之前进行。这种情况下的冷却以通过控制浸入镀浴的板温来确保镀覆性为目的,因此冷却至约镀锌浴温以上且约600℃以下即可。冷却方法没有特别限定,作为一例,有空冷、炉冷、气体喷射冷却。实施热镀锌处理时,将实施了上述退火处理的钢板浸渍在440℃以上且500℃以下的镀锌浴中,实施热镀锌处理,然后,通过气体擦拭等调整镀层附着量。需要说明的是,热镀锌中优选使用al量为0.08%以上且0.30%以下的镀锌浴。需要说明的是,除了热镀锌处理以外,还可以使用电镀锌处理等方法。
[0121]
进而,在实施镀锌层的合金化处理的情况下,在镀锌处理后,在450℃以上且600℃以下的温度范围内实施镀锌层的合金化处理。在超过600℃的温度下进行合金化处理时,未相变奥氏体相变为珠光体,有时不能确保期望的残余奥氏体的面积率,延展性降低。因此,在进行镀锌层的合金化处理的情况下,优选在450℃以上且600℃以下的温度范围内实施镀锌层的合金化处理。
[0122]
其他制造方法的条件没有特别限定,从生产率的观点出发,上述退火优选通过连续退火设备进行。另外,退火、热镀锌、镀锌层的合金化处理等一系列处理优选通过热镀锌线cgl(连续镀锌线,continuous galvanizing line)进行。
[0123]
在超过100℃且400℃以下的温度范围内保持10s以上
[0124]
作为最后的热处理(最终退火处理),在超过100℃且400℃以下的温度范围内保持10s以上,这在本发明中很重要。在100℃以下的温度范围内或少于10s的条件下保持的情况下,得不到充分的面积率的回火马氏体,此外,钢中扩散性氢不会从钢板放出,因此,不仅扩孔性降低,而且弯曲性也减小。另一方面,在超过400℃的温度范围内保持的情况下,由于残余奥氏体的分解,得不到充分的面积率的残余奥氏体,钢的延展性降低。
[0125]
需要说明的是,出于形状矫正、调整表面粗糙度等目的,可以对上述“高强度钢板”、在该高强度钢板的表面具有镀锌层的“高强度镀锌钢板”进行表皮光轧。表皮光轧的压下率优选为0.1%以上且2.0%以下的范围。小于0.1%时,效果小,也难以控制,因此将其作为良好范围的下限。另外,超过2.0%时,生产率显著降低,因此将其作为良好范围的上限。需要说明的是,表皮光轧可以在线进行,也可以离线进行。另外,可以一次性地进行目标压下率的表皮光轧,也可以分成多次进行。另外,也可以实施树脂或油脂涂布等各种涂装处理。
[0126]
实施例
[0127]
将具有表1所示的成分组成、余量由fe和不可避免的杂质构成的钢通过转炉熔炼,通过连铸法制成钢坯。将所得到的钢坯再加热至1250℃后,在表2、3所示的条件下得到板厚1.0mm以上且1.8mm以下的高强度冷轧钢板(cr)。进一步实施镀锌处理,得到热镀锌钢板(gi),对热镀锌钢板进行合金化处理,由此得到合金化热镀锌钢板(ga)。关于热镀锌浴,对于热镀锌钢板(gi)而言,使用含有0.19质量%的al的锌浴,对于合金化热镀锌钢板(ga)而言,使用含有0.14质量%的al的锌浴,浴温设定为465℃。镀层附着量设定为每单面45g/m2(双面镀覆),对于ga而言,调整成使镀层中的fe浓度为9质量%以上且12质量%以下。对所得到的钢板的截面钢组织、拉伸特性、扩孔性进行调査,将其结果示于表4、5、6中。
[0128][0129]
马氏体相变开始温度ms点以及ac1相变点和ac3相变点使用下式求出。
[0130]
马氏体相变开始温度ms点(℃)=550-350
×
(%c)-40
×
(%mn)-10
×
(%cu)-17
×
(%ni)-20
×
(%cr)-10
×
(%mo)-35
×
(%v)-5
×
(%w) 30
×
(%al)
[0131]
ac1相变点(℃)=751-16
×
(%c) 11
×
(%si)-28
×
(%mn)-5.5
×
(%cu)-16
×
(%ni) 13
×
(%cr) 3.4
×
(%mo)
[0132]
ac3相变点(℃)=910-203√(%c) 45
×
(%si)-30
×
(%mn)-20
×
(%cu)-15
×
(%ni) 11
×
(%cr) 32
×
(%mo) 104
×
(%v) 400
×
(%ti) 200
×
(%al)
[0133]
其中,(%c)、(%si)、(%mn)、(%ni)、(%cu)、(%cr)、(%mo)、(%v)、(%ti)、(%v)、(%w)、(%al)为各个元素的含量(质量%)。
[0134]
[0135][0136]
拉伸试验使用以拉伸方向为与钢板的轧制方向成直角的方向的方式裁取了样品的jis5号试验片依据jisz 2241(2011年)进行,测定ts(拉伸强度)、el(总伸长率)。另外,关
于机械特性,将下述情况判断为良好。
[0137]
ts:980mpa以上且小于1080mpa的情况下,el≥20%
[0138]
ts:1080mpa以上且小于1180mpa的情况下,el≥16%
[0139]
扩孔性依据jis z 2256(2010年)进行。将所得到的各钢板切割成100mm
×
100mm后,以12%
±
1%的间隙冲裁出直径10mm的孔后,使用内径75mm的模具以9吨的压边力按压的状态下,将60
°
圆锥的冲头压入孔中,测定龟裂产生极限时的孔直径,根据下述公式求出极限扩孔率λ(%),根据该极限扩孔率的值来评价扩孔性。
[0140]
极限扩孔率λ(%)={(d
f-d0)/d0}
×
100
[0141]
其中,df是龟裂产生时的孔径(mm),d0是初始孔径(mm)。需要说明的是,在本发明中,针对每种ts范围,将下述情况判断为良好。
[0142]
ts:980mpa以上且小于1080mpa的情况下,λ≥20%
[0143]
ts:1080mpa以上且小于1180mpa的情况下,λ≥15%
[0144]
关于弯曲试验,以轧制方向为弯曲轴(bending direction)的方式从各退火钢板上裁取宽度30mm、长度100mm的弯曲试验片,基于jis z2248(1996年)的v型块法实施测定。以100mm/秒的推压速度在各弯曲半径下实施n=3的试验,针对弯曲部外侧,利用立体显微镜判定有无龟裂,将不产生龟裂的最小的弯曲半径作为极限弯曲半径r。需要说明的是,在本发明中,将满足90
°
v型弯曲下的极限弯曲r/t≤2.5(t:钢板的板厚)的情况判定为钢板的弯曲性良好。
[0145]
本发明例的高强度钢板均得到了具有980mpa以上的ts、成形性优良的高强度钢板。另一方面,就比较例而言,ts、el、λ、弯曲性中的至少一种特性差。
[0146]
[表4]
[0147][0148]
下划线部分:表示在本发明范围外。
[0149]
f:铁素体、tm:回火马氏体、ra:残体奥氏体
[0150]
[表5]
[0151][0152]
下划线部分:表示在本发明范围外。
[0153]
f:铁素体、m:马氏体、ra:残余奥氏体、bf:贝氏体铁素体、p:珠光体、:碳化物(渗碳体等)
[0154]
产业上的可利用性
[0155]
根据本发明,可以得到具有980mpa以上的ts(拉伸强度)的成形性优良的高强度钢板。通过将本发明的高强度钢板应用于例如汽车结构构件,能够实现由车身轻量化带来的燃料效率改善,产业上的利用价值非常大。
再多了解一些
本文用于企业家、创业者技术爱好者查询,结果仅供参考。