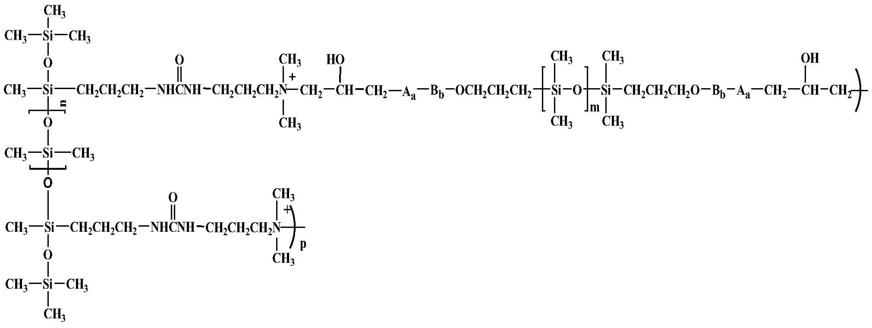
1.本技术涉及精细化工合成领域,尤其涉及一种树脂型聚硅氧烷高弹性硅油及其制备方法。
背景技术:
2.近10年来聚醚改性氨基硅油的发展已经到了高度成熟的阶段,到了存量市场的价格肉搏战阶段,很难通过性能的提升进行替代性的增量增长;硅油柔软剂由于合成工艺、核心原料、成本效果都高度透明、高度同质,迫使企业进行分子结构的创新进行性能效果的提升。近年来各种概念的嵌段硅油层出不穷,五元、六元多元共聚、聚氨酯聚醚嵌段硅油、t型结构的超支化硅油等等,但是其本质的结构没有改变,聚醚、氨基、有机硅核心的三元组分基本没有改变,很难在性能上有较大的改变。
技术实现要素:
3.本技术针对现有嵌段硅油在弹性方便不足的问题,提供一种树脂型聚硅氧烷高弹性硅油及其制备方法。
4.为达到以上目的,本技术提供一种树脂型聚硅氧烷高弹性硅油,结构式为:
5.其中,a为(-ch2ch2o-),b为n、m、a、b、p均为整数,且64≤n≤90,67≤m≤94,3≤a≤8,2≤b≤6,3≤p≤5。
6.本技术还提供一种树脂型聚硅氧烷高弹性硅油的制备方法,包括以下步骤:
7.s1,由二甲基硅油与含异氰酸酯基的硅烷偶联剂反应制得异氰酸酯基聚硅氧烷;
8.s2,将含有伯胺基与叔胺基的胺类接枝反应到异氰酸酯基聚硅氧烷上,然后再加入端环氧基聚醚硅油进行扩链反应得到树脂型聚硅氧烷高弹性硅油。
9.进一步地,所述步骤s1中,所述含异氰酸酯基的硅烷偶联剂为甲基-(3-异氰酸丙基)二甲基硅烷,所述二甲基硅油与所述甲基-(3-异氰酸丙基)二甲基硅烷的质量比为(12~18):1,所述二甲基硅油的数均分子量为1000~1500,反应在碱性催化剂作用下进行。
10.进一步地,所述步骤s1中,所述催化剂与所述甲基-(3-异氰酸丙基)二甲基硅烷的质量比为(0.1~0.2):1。
11.进一步地,所述催化剂选自氢氧化钾、氢氧化锂、四甲基氢氧化铵中的一种或多种的混合。
12.进一步地,所述二甲基硅油为加热、负压条件下低脱后的二甲基硅油,所述二甲基硅油与所述甲基-(3-异氰酸丙基)二甲基硅烷的反应过程中,先在加热、负压条件的下边脱低边反应,待反应一段时间后,撤去真空继续反应。
13.进一步地,所述步骤s2中,所述含有伯胺基与叔胺基的胺类的碳链长度为c3~c8,优选地,所述含有伯胺基与叔胺基的胺类为n,n-二甲基-1,3-丙二胺,所述异氰酸酯基聚硅氧烷与所述n,n-二甲基-1,3-丙二胺按照质量比(20~35):1进行反应,反应一段时间后加入端环氧基聚醚硅油、酸、异丙醇继续进行反应,其中所述端环氧基聚醚硅油的添加量为n,n-二甲基-1,3-丙二胺的18~35倍,所述端环氧基聚醚硅油的两端均为环氧基,数均分子量为6000~8000。
14.进一步地,所述酸选自甲酸、乙酸、月桂酸和油酸中的一种。
15.进一步地,所述端环氧基聚醚硅油、所述酸、所述异丙醇的质量比为(450~680):(24~114):(650~900)。
16.进一步地,所述异氰酸酯基聚硅氧烷与所述n,n-二甲基-1,3-丙二胺在氮气气氛中,于30~40℃下保温反应4~6小时,然后加入端环氧基聚醚硅油、酸、异丙醇,充分搅拌,升温至75~80℃,保温反应10~18小时后得到树脂型聚硅氧烷高弹性硅油。
17.与现有技术相比,本技术的有益效果在于:本技术以二甲基硅油、含异氰酸酯基的硅烷偶联剂为原料,制备异氰酸酯基聚硅氧烷,然后利用含有伯胺基与叔胺基的胺类对异氰酸酯基硅油进行改性,将得到的改性产物与端环氧聚醚硅油反应,制备一种树脂型聚硅氧烷高弹性硅油。本发明所得的树脂型聚硅氧烷高弹性硅油含有聚氨酯链段,利用聚氨酯优异的成膜性能和优异的记忆回复性能,使得产品具有高弹的特点,同时分子结构中含有大量的有机硅链段和氨基,能赋予织物优异的柔软滑爽手感。分子结构中含有大量的高活性脲基结构,其优异的自交联性能,能赋予产品具有优异的成膜性,能与织物更好的结合,与结构上的软-硬链段协同作用,赋予产品与传统嵌段硅油与众不同的风格。本发明工艺简单易操作,具有较好应用前景。
具体实施方式
18.下面,结合具体实施方式,对本技术做进一步描述,需要说明的是,在不相冲突的前提下,以下描述的各实施例之间或各技术特征之间可以任意组合形成新的实施例。
19.需要说明的是,本技术的说明书和权利要求书中的术语“第一”、“第二”等是用于区别类似的对象,而不必用于描述特定的顺序或先后次序。
20.本技术的说明书和权利要求书中的术语“包括”和“具有”以及他们的任何变形,意图在于覆盖不排他的包含,例如,包含了一系列步骤或单元的过程、方法、系统、产品或设备不必限于清楚地列出的那些步骤或单元,而是可包括没有清楚地列出的或对于这些过程、方法、产品或设备固有的其它步骤或单元。
21.本技术提供一种树脂型聚硅氧烷高弹性硅油,其结构式如下:
22.其中,a为(-ch2ch2o-),b为n、m、a、b、p均为整数,且64≤n≤90,67≤m≤94,3≤a≤8,2≤b≤6,3≤p≤5。
23.本技术的树脂型聚硅氧烷高弹性硅油的分子结构中兼具有机硅链段、高活性脲基和聚醚链段,三者能够协同作用,赋予织物柔软高弹的特点;此外,其分子结构中含有季铵盐结构和聚醚链段,两者协同作用,能够赋予织物较好的亲水、亲肤性能;本技术的树脂型聚硅氧烷高弹性硅油具有自乳化性能,无需乳化剂,可以采用高速分散机开稀使用。
24.本技术还提供一种树脂型聚硅氧烷高弹性硅油的制备方法,包括以下步骤:
25.s1制备异氰酸酯基聚硅氧烷:由二甲基硅油与含异氰酸酯基的硅烷偶联剂反应制得异氰酸酯基聚硅氧烷;
26.s2制备树脂型聚硅氧烷高弹性硅油:将含有伯胺基与叔胺基的胺类接枝反应到异氰酸酯基聚硅氧烷上,其中伯胺基与异氰酸酯基反应生成脲基;然后再加入端环氧基聚醚硅油,叔胺基与环氧基发生反应,扩链反应后得到树脂型聚硅氧烷高弹性硅油。
27.在一个实施例中,所述含异氰酸酯基的硅烷偶联剂为甲基-(3-异氰酸丙基)二甲基硅烷。
28.步骤s1可参考以下反应式:
29.其中x、n为整数,13≤x≤21,64≤n≤90。
30.在一个实施例中,所述含有伯胺基与叔胺基的胺类的碳链长度为c3~c8,优选地,所述含有伯胺基与叔胺基的胺类为n,n-二甲基-1,3-丙二胺。
31.步骤s2可参考以下反应式:
32.其中,a为(-ch2ch2o-),b为n、m、a、b、p均为整数,且64≤n≤90,67≤m≤94,3≤a≤8,2≤b≤6,3≤p≤5。
33.在一个优选实施例中,步骤s1中,二甲基硅油与甲基-(3-异氰酸丙基)二甲基硅烷的质量比为(12~18):1,二甲基硅油的数均分子量为1000~1500,反应在碱性催化剂作用下进行。
34.具体地,步骤s1中,先将二甲基硅油在110℃、真空负压为0.09~0.1mpa条件下脱低2小时,然后按比例将二甲基硅油与甲基-(3-异氰酸丙基)二甲基硅烷加入到装有温度计、搅拌器和冷凝回流的反应釜中,加入催化剂,升温至120~130℃,开启真空,在负压为0.07~0.08mpa条件下,一边脱低一边搅拌保温1~2小时,撤去真空,继续保温3~4小时后,降温至40℃以下,得到异氰酸酯基聚硅氧烷。
35.进一步地,步骤s1中,催化剂选自氢氧化钾、氢氧化锂、四甲基氢氧化铵中的一种。催化剂与甲基-(3-异氰酸丙基)二甲基硅烷的质量比为(0.1~0.2):1。
36.在一个优选实施例中,二甲基硅油、甲基-(3-异氰酸丙基)二甲基硅烷和催化剂的质量比为5740:380:50。
37.进一步地,步骤s2中,异氰酸酯基聚硅氧烷、n,n-二甲基-1,3-丙二胺与端环氧基聚醚硅油的质量比为(20~35):1:(18~35)。端环氧基聚醚硅油的两端均为环氧基,其数均分子量为6000~8000。
38.具体地,步骤s2中,将异氰酸酯基聚硅氧烷与n,n-二甲基-1,3-丙二胺按比例加入到装有温度计、搅拌器和冷凝回流的反应釜中,升温至30~40℃,并通入氮气,保温反应4~6小时,然后加入端环氧基聚醚硅油、酸、异丙醇,充分搅拌,升温至75~80℃,保温反应10~18小时后,降温至40℃以下,停止通入氮气,得到树脂型聚硅氧烷高弹性硅油。
39.进一步地,步骤s2中酸选自甲酸、乙酸、月桂酸和油酸中的一种,端环氧基聚醚硅油、酸、异丙醇的质量比为:(450~680):(24~114):(650~900)。
40.在一个优选实施例中,异氰酸酯基聚硅氧烷、n,n-二甲基-1,3-丙二胺、端环氧基聚醚硅油(分子量8000)、乙酸、异丙醇的质量比为:600:21:615:24:800。
41.步骤s1利用有机硅线性体和含异氰酸酯基的硅烷偶联剂在碱性催化剂条件下能反应重排制得异氰酸酯基聚硅氧烷。步骤s2利用氨基与异氰酸酯基能快速反应对异氰酸酯基聚硅氧烷进行改性,改性后产物中的叔胺基在酸的催化作用下与端环氧基聚醚硅油进行扩链反应,制得树脂型聚硅氧烷高弹性硅油。本技术利用聚氨酯结构能够赋予材料高弹性的原理,在有机硅软链段的基础上接入聚醚链段和聚氨酯结构,形成软硬嵌段结构,赋予材料优异的成膜性和弹性。本技术研制的树脂型聚硅氧烷高弹性硅油由于其结构上具有软-硬链段,从而其在织物处理上具有与众不同的风格特点。
42.此外,本技术制备树脂型聚硅氧烷高弹性硅油的工艺相对简单,反应过程容易控制,适合工业化生产。
43.【实施例1】
44.一种树脂型聚硅氧烷高弹性硅油的制备方法,包括以下步骤:
45.(1)将在110℃、真空负压0.09mpa条件下脱低2小时的二甲基硅油4690份与甲基-(3-异氰酸丙基)二甲基硅烷380份加入到装有温度计、搅拌器和冷凝回流的反应釜中,并加入50份的催化剂,升温至120℃,开启真空,在负压为0.07mpa条件下,一边脱低一边搅拌保温2小时,撤去真空,继续保温3小时后,降温至40℃以下,得到异氰酸酯基聚硅氧烷。
46.(2)将得到的异氰酸酯基聚硅氧烷500份和n,n-二甲基-1,3-丙二胺21份加入到装有温度计、搅拌器和冷凝回流的反应釜中,升温至30℃,并通入氮气,保温6小时后,加入460份的端环氧聚醚硅油(数均分子量为6000)、24份的乙酸和650份异丙醇,充分搅拌,升温至78℃,保温反应14小时后,降温至40℃以下,停止通入氮气,得到树脂型聚硅氧烷高弹性硅油。
47.【实施例2】
48.实施例2与实施例1的区别在于:步骤(2)中,端环氧聚醚硅油的数均分子量为8000,其添加量调整为615份;异丙醇的添加量调整为760份。
49.【实施例3】
50.实施例3与实施例1的区别在于:步骤(1)中,二甲基硅油的添加量调整为5740份;步骤(2)中,异氰酸酯基聚硅氧烷的添加量调整为600份;端环氧聚醚硅油的数均分子量为8000,其添加量调整为615份;异丙醇的添加量调整为800份。
51.【实施例4】
52.实施例4与实施例1的区别在于:步骤(1)中二甲基硅油的添加量调整为6740份;步骤(2)中,异氰酸酯基聚硅氧烷的添加量调整为700份;端环氧聚醚硅油的数均分子量为8000,其添加量调整为615份;异丙醇的添加量调整为870份。
53.【实施例5】
54.一种树脂型聚硅氧烷高弹性硅油的制备方法,包括以下步骤:
55.(1)将在110℃、真空负压0.09mpa条件下脱低2小时的二甲基硅油5740份与甲基-(3-异氰酸丙基)二甲基硅烷380份加入到装有温度计、搅拌器和冷凝回流的反应釜中,并加
入70份的催化剂,升温至130℃,开启真空,在负压为0.08mpa条件下,一边脱低一边搅拌保温2小时,撤去真空,继续保温3小时后,降温至40℃以下,得到异氰酸酯基聚硅氧烷。
56.(2)将得到的异氰酸酯基聚硅氧烷600份和n,n-二甲基-1,3-丙二胺21份加入到装有温度计、搅拌器和冷凝回流的反应釜中,升温至30℃,并通入氮气,保温6小时后,加入615份的端环氧聚醚硅油(数均分子量为8000)、24份的乙酸和800份异丙醇,充分搅拌,升温至78℃,保温反应14小时后,降温至40℃以下,停止通入氮气,得到树脂型聚硅氧烷高弹性硅油。
57.【实施例6】
58.实施例6与实施例5的区别在于:步骤(1)中,催化剂的添加量调整为40份。
59.【实施例7】
60.实施例7与实施例5的区别在于:步骤(1)中,催化剂的添加量调整为40份;步骤(2)中,将原保温反应14小时调整为保温反应18小时。
61.【实施例8】
62.实施例8与实施例5的区别在于:步骤(1)中,催化剂的添加量调整为40份;步骤(2)中,将24份的乙酸调整为20份的甲酸。
63.【实施例9】
64.实施例9与实施例5的区别在于:步骤(1)中,催化剂的添加量调整为40份;步骤(2)中,将24份的乙酸调整为81份的月桂酸。
65.【实施例10】
66.实施例10与实施例5的区别在于:步骤(1)中,催化剂的添加量调整为40份;步骤(2)中,将24份的乙酸调整为114份的油酸。
67.【对比例1】
68.一种高弹性树脂改性硅油(可参考本技术的于2020年1月20日申请的发明专利,申请号为202010069266.7),通过以下方法制备:
69.(1)将30份的聚乙二醇(数均分子量为150)加入到装有温度计、搅拌器和冷凝回流的反应釜中,升温至50℃,并通入氮气,将100份二苯甲烷二异氰酸酯通过恒压滴液漏斗缓慢的滴加到反应釜中,保温3小时后,降温至40℃以下,停止通入氮气,得到聚氨酯预聚体。
70.(2)将得到的200份的聚氨酯预聚体和63份的n,n-二甲基-1,3-丙二胺加入到装有温度计、搅拌器和冷凝回流的反应釜中,升温至40℃,并通入氮气,保温4小时后,加入2080份的端环氧聚醚硅油(数均分子量为9000)和1300份异丙醇,升温至75℃,保温反应10小时后,降温至40℃以下,停止通入氮气,得到高弹性树脂改性硅油。
71.各实施例和对比例1制得的硅油首先进行开稀工艺,将100质量份的树脂型聚硅氧烷高弹性硅油、200质量份的水、2质量份的醋酸在高速分散机中开稀,制得树脂型聚硅氧烷高弹性硅油乳液。选取法兰绒、涤纶、棉针织的面料浸轧工作液(硅油乳液30g/l,轧液率70%),然后在170℃下预烘焙15~45s,再回潮1h。
72.【对比例2】
73.市售的嵌段硅油a,生产厂家:张家港启江化工有限公司,s-600松厚型弹性体。
74.【对比例3】
75.市售的嵌段硅油b,生产厂家:张家港启江化工有限公司,s-700松软型弹性体。
76.将对比例2和对比例3的嵌段硅油按照其使用说明书的方式对织物进行整理。
77.采用手触摸法评定经整理的面料的柔软度、蓬松度、滑爽度、弹性:采用1~5分评判法,1分最差,5分最好,5人同时评定,取平均值。
78.表1为法兰绒类织物经整理后的性能评价结果。表1整理剂柔软度蓬松度爽滑度弹性实施例14444实施例244~554实施例34~54~555实施例44~5454~5实施例54~54~555实施例65444实施例74~5445实施例83~444~54实施例954~54~55实施例1044~554~5对比例13544对比例23433对比例34333
79.表2为涤纶织物经整理后的性能评价结果。表2整理剂柔软度蓬松度爽滑度弹性实施例14444实施例24454实施例354~555实施例44~5454~5实施例554~555实施例65444实施例74~5445实施例83~444~54实施例954~545实施例1044~544~5对比例13454对比例25343对比例33443
80.表3为棉织物经整理后的性能评价结果。表3整理剂柔软度蓬松度爽滑度弹性实施例14444
实施例244~554实施例34~54~555实施例44~5454~5实施例54~54~555实施例65444实施例74~5445实施例8444~54实施例94~54~545实施例1044~544~5对比例13544对比例2543~42对比例3443~42
81.从表1-表3的数据可以看出,本技术制得的树脂型聚硅氧烷高弹性硅油应用于各类织物的综合性能要优于对比产品,尤其是在弹性风格特点上。
82.此外,对比例1为申请人自制的一款高弹性树脂改性硅油,其主要优势在于提高织物的蓬松度,但是由于其主链结构中含有苯环,处理后织物的柔软性较差,而本技术制得的树脂型聚硅氧烷高弹性硅油处理后织物的柔软性较对比例1更好,弹性相当,较对比例1通用性更强。
83.另外,从实施例1和实施例2的数据可以发现,硅油合成过程中端环氧基聚醚硅油的分子量越大,整理后织物的爽滑性更好。
84.根据实施例2、实施例3和实施例4的数据可以发现,实施例3制得的产物整理后织物的柔软度和弹性会更好,说明硅油合成过程中当二甲基硅油与甲基-(3-异氰酸丙基)二甲基硅烷的质量比优选5740:380,异氰酸酯基聚硅氧烷的添加量优选为600份。
85.根据实施例6和实施例7的数据可以发现,硅油合成过程中,最后一步的反应时间会影响整理后织物的弹性,延长反应时间,有利于提高整理后织物的弹性。
86.根据实施例3、实施例8、实施例9和实施例10的数据可以发现,硅油合成过程中酸催化剂促进叔胺基与环氧基的反应,不同的酸对最终产物在织物上的性能有一定影响,与对比例3比较,使用甲酸会使整理后织物的综合手感风格略有下降;使用油酸和月桂酸会使整理后织物滑爽感会略有降低;但都在可接受范围内。
87.以上描述了本技术的基本原理、主要特征和本技术的优点。本行业的技术人员应该了解,本技术不受上述实施例的限制,上述实施例和说明书中描述的只是本技术的原理,在不脱离本技术精神和范围的前提下本技术还会有各种变化和改进,这些变化和改进都落入要求保护的本技术的范围内。本技术要求的保护范围由所附的权利要求书及其等同物界定。
再多了解一些
本文用于企业家、创业者技术爱好者查询,结果仅供参考。