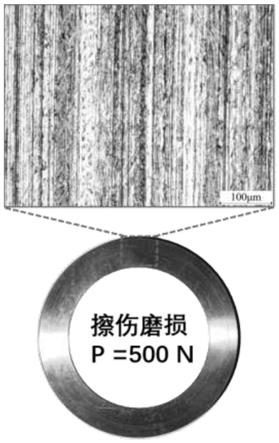
1.本发明涉及纳米润滑油技术领域。具体地说是一种能稳定存在的二硫化钼纳米润滑油及其制备方法。
背景技术:
2.现有研究表明,纳米润滑油相对于基础油,有着优良的极压性能和抗磨减摩性能,在高温、重载等条件下具有更高的承载能力和润滑性能,且纳米颗粒能够修复因局部凸峰接触产生的犁沟,从而提高表面的平整度。二硫化钼(mos2)与石墨烯相似,都具有明显的层状结构,且二硫化钼的润滑特性取决于自身特殊的晶体结构,其层与层之间仅靠微弱的范德华力联接,呈现出易剪切的特性。二硫化钼的层内为s-mo-s的三明治结构,沿厚度方向的面内刚度较强体现了其优异的承载能力。因此,mos2无论是作为润滑油纳米添加剂还是固体润滑材料均表现出优异的摩擦性能。
3.mos2纳米材料尽管摩擦性能优异,但由于mos2纳米颗粒的高比表面能和较高的表面原子活性,使得mos2纳米颗粒在润滑油中容易相互吸附发生聚集而影响润滑油品质,从而直接影响mos2纳米润滑油应用于实际工况。因此,研究出一种能稳定存在的mos2纳米润滑油,对改善接触部件的润滑与传热具有重大意义。
技术实现要素:
4.为此,本发明所要解决的技术问题在于提供一种能稳定存在的二硫化钼纳米润滑油及其制备方法,以解决现有mos2纳米润滑油中二硫化钼容易相互吸附发生聚集、悬浮稳定性差以及制备流程复杂等问题。
5.为解决上述技术问题,本发明提供如下技术方案:
6.一种能稳定存在的二硫化钼纳米润滑油,由二硫化钼粉末、分散剂混合液和基础油组成;所述二硫化钼纳米润滑油中,所述分散剂混合液的质量分数为8~15wt%,二硫化钼粉末的质量分数为0.1~1.0wt%;
7.所述分散剂混合液由油酸、油胺和正十二硫醇组成,油酸、油胺和正十二硫醇的质量之比为(0.8~1.2):(1.8~2.2):(0.8~1.2);油酸、油胺和正十二硫醇均可作为单一分散剂增加二硫化钼纳米润滑油的悬浮稳定性,但本发明通过研究发现,油酸、油胺和正十二硫醇单一使用时,其稳定效果并不理想,而当油酸、油胺和正十二硫醇按照上述比例混合得到的混合分散剂对二硫化钼颗粒具有最佳的分散性能,且有利于提高二硫化钼纳米润滑油的润滑特性。
8.上述能稳定存在的二硫化钼纳米润滑油,所述分散剂混合液的质量分数为12wt%,所述分散剂混合液中油酸、油胺和正十二硫醇的质量之比为1:2:1。在试验中发现,分散剂混合液的质量分数过大或过小,都不利于二硫化钼颗粒的分散,且当分散剂混合液质量分数为12wt%,油酸、油胺和正十二硫醇的质量之比为1:2:1时,二硫化钼纳米润滑油的悬浮稳定性和润滑性能均好于单一分散剂或任意两种分散剂混合的二硫化钼润滑油。
9.上述能稳定存在的二硫化钼纳米润滑油,二硫化钼粉末的粒径为50~200nm,所述二硫化钼粉末的质量分数为0.3~0.5wt%。二硫化钼粉末的粒径过小会增加润滑油的成本,粒径过大则容易降低其悬浮稳定性。若二硫化钼添加质量过少则难以提供足够的润滑效果,添加质量过多则容易由于颗粒聚集而沉降。
10.上述能稳定存在的二硫化钼纳米润滑油,所述基础油为工业级白油,所述基础油为32#基础油、46#基础油、68#基础油、100#基础油、150#基础油、250#基础油、300#基础油或400#基础油中的一种或两种及两种以上的组合。
11.上述能稳定存在的二硫化钼纳米润滑油,在40℃条件下:32#基础油的运动粘度为28~35mm2/s,46#基础油的运动粘度为42~50mm2/s,68#基础油的运动粘度为65~71mm2/s,100#基础油的运动粘度为95~105mm2/s,150#基础油的运动粘度为145~155mm2/s,250#基础油的运动粘度为240~260mm2/s,300#基础油的运动粘度为290~310mm2/s,400#基础油的运动粘度为380~420mm2/s。
12.一种能稳定存在的二硫化钼纳米润滑油的制备方法,包括如下步骤:
13.步骤a:将油酸、油胺和正十二硫醇按照质量之比为(0.8~1.2):(1.8~2.2):(0.8~1.2)的比例混合,得到分散剂混合液;
14.步骤b:将二硫化钼粉末加入到所述分散剂混合液中,得到混合反应体系;对所述混合反应体系加热并进行磁力搅拌,反应结束后自然冷却,得到分散剂修饰改性二硫化钼混合液;
15.步骤c:将所述分散剂修饰改性二硫化钼混合液与所述基础油混合,并进行超声分散处理,超声分散处理结束后,得到二硫化钼纳米润滑油;
16.所述二硫化钼纳米润滑油中,所述分散剂混合液的质量分数为8~15wt%,二硫化钼粉末的质量分数为0.1~1.0wt%。
17.上述能稳定存在的二硫化钼纳米润滑油的制备方法,所述二硫化钼纳米润滑油中,所述分散剂混合液的质量分数为12wt%,所述二硫化钼粉末的质量分数为0.3~0.5wt%;所述分散剂混合液中油酸、油胺和正十二硫醇的质量之比为1:2:1;二硫化钼粉末的粒径为50~200nm;
18.所述基础油为工业级白油,所述基础油为32#基础油、46#基础油、68#基础油、100#基础油、150#基础油、250#基础油、300#基础油或400#基础油中的一种或两种及两种以上的组合;
19.在40℃条件下:32#基础油的运动粘度为28~35mm2/s,46#基础油的运动粘度为42~50mm2/s,68#基础油的运动粘度为65~71mm2/s,100#基础油的运动粘度为95~105mm2/s,150#基础油的运动粘度为145~155mm2/s,250#基础油的运动粘度为240~260mm2/s,300#基础油的运动粘度为290~310mm2/s,400#基础油的运动粘度为380~420mm2/s。
20.上述能稳定存在的二硫化钼纳米润滑油的制备方法,步骤b中:控制所述混合反应体系温度为170~190℃,并进行磁力搅拌1.5~2.5h,磁力搅拌的转速为500~800r/min。若混合反应体系的反应温度过低,则修饰改性效果差甚至是难以实现,若反应温度过高,则容易导致混合反应体系焦化失效。另外,磁力搅拌时间和磁力搅拌转速也会影响二硫化钼的修饰改性效果,若磁力搅拌时间过短,则二硫化钼的修饰改性过程无法修饰改性完全,若搅拌时间过长,则增加操作时间,降低制备效率;若磁力搅拌转速过低,则不利于修饰改性反
应的进行,但若磁力搅拌转速过高又会导致液滴飞溅影响操作的安全。
21.上述能稳定存在的二硫化钼纳米润滑油的制备方法,步骤b中:控制所述混合反应体系温度为180℃,并进行磁力搅拌2h,磁力搅拌的转速为600r/min。在此反应条件下,二硫化钼颗粒表面修饰改性后更容易分散,制备得到的二硫化钼润滑油悬浮稳定性好,且具有较好的润滑特性。
22.上述能稳定存在的二硫化钼纳米润滑油的制备方法,步骤c中:超声分散的功率为1080w,超声分散的温度为110℃,温度过高容易导致润滑油结焦失效,温度过低则不利于超声分散;超声分散的工作模式为:超声分散1秒后,停顿1秒,接着继续超声分散1秒,停顿1秒;循环此超声分散工作模式并持续90min。此种超声模式分散效率高,若超声工作时间过长容易导致润滑油温度过高且不利于温度控制,超声工作时间过短则降低超声效率,分散效果不好。
23.本发明的技术方案取得了如下有益的技术效果:
24.本发明通过选择特定的分散剂,并控制分散剂中各组分的配比以及分散剂的添加量,实现对mos2纳米颗粒的表面修饰改性。相较于直接添加分散剂到基础油中,先一步对mos2纳米颗粒的表面修饰改性可以增加mos2纳米颗粒间排斥力并有效防止团聚发生,增强了mos2纳米颗粒在润滑油中的分散稳定性,从而发挥出纳米润滑油优异的润滑特性。本发明制备的mos2纳米润滑油可稳定存在,20天后没有明显聚集沉降现象;且相对基础油而言本发明制备的mos2纳米润滑油能够显著降低极压条件下的磨斑直径,同时在长磨条件下能够提高油膜的极限载荷、极限温度和极限速度(极限载荷、极限温度、极限速度表示摩擦副间油膜破裂之前的最大运行载荷、温度、速度),显著提升了基础油的润滑特性。
25.本发明使用的分散剂为质量之比为1:2:1的油酸、油胺和正十二硫醇,配方简单且成本较低,对环境友好,且其制备工艺简单、制备过程耗时较短。采用本发明方法配置的mos2纳米润滑油能够稳定存在,且该润滑油长时间放置后(一个月以上)仅需简单的机械摇晃即可继续保持其悬浮稳定性。
附图说明
26.图1本发明实施例1中步骤b的实验操作简图;
27.图2本发明实施例1中步骤c的实验操作简图;
28.图3本发明实施例1制备的二硫化钼纳米润滑油的实拍图;
29.图4本发明实施例1制备的二硫化钼纳米润滑油放置20天后的实拍图;
30.图5本发明对比例1制备的二硫化钼纳米润滑油的实拍图;
31.图6本发明对比例1制备的二硫化钼纳米润滑油放置3天后的实拍图;
32.图7本发明实施例1制备的二硫化钼纳米润滑油和32#基础油的荷载和摩擦系数随时间变化曲线图;
33.图8本发明实施例1制备的二硫化钼纳米润滑油极限荷载试验结果图;
34.图9 32#基础油的极限荷载试验结果图;
35.图10本发明实施例1制备的二硫化钼纳米润滑油和32#基础油的磨斑直径对比。
36.图11不同型号的基础油和其对应质量分数为0.5wt%的mos2纳米润滑油的磨斑直径对比。
具体实施方式
37.实施例1
38.本实施例中,能稳定存在的二硫化钼纳米润滑油,由二硫化钼粉末、分散剂混合液和基础油组成;二硫化钼纳米润滑油中,分散剂混合液的质量分数为12wt%,二硫化钼粉末的质量分数为0.5wt%;所述分散剂混合液由油酸(oleic acid,化学式c
18h34
o2)、油胺(oleylamine,化学式c
18h37
n)和正十二硫醇(1-dodecanethiol,化学式c
12h26
s)组成,油酸、油胺和正十二硫醇的质量之比为1:2:1;二硫化钼粉末的粒径为50~200nm;所述基础油为32#基础油,为工业级白油。
39.上述能稳定存在的二硫化钼纳米润滑油的制备方法包括如下步骤:
40.步骤a:将9g油酸、18g油胺和9g正十二硫醇一同加入到烧杯中进行混合,得到分散剂混合液;
41.步骤b:将1.5g二硫化钼粉末加入到所述分散剂混合液中,得到混合反应体系;用玻璃棒充分搅拌后将烧杯置于加热台表面,设定加热台温度为180℃。同时利用磁力搅拌进行分散,设置转速为600r/min,保持混合反应体系温度为180℃,磁力搅拌2h后反应结束,自然冷却至室温,即得到分散剂修饰改性二硫化钼混合液;图1为本步骤对mos2粉末进行修饰改性的实验操作简图;
42.步骤c:将上述分散剂修饰改性二硫化钼混合液与262.5g基础油【本实施例所用基础油为32#基础油,其在40℃条件下运动粘度为28~35mm2/s】混合,用玻璃棒充分搅拌后利用超声波处理器进行超声分散处理,超声分散的具体设置参数为额定功率1200w的90%,工作模式为:超声分散和间隔时间均为1秒(即超声分散1秒后,停顿1秒,接着继续超声分散1秒,停顿1秒,如此循环),超声分散时,控制其温度为110℃,持续分散90分钟后自然冷却至室温,得到二硫化钼纳米润滑油;图2为本步骤中实验操作简图。
43.图7至图9为32#基础油和实施1中mos2纳米润滑油的极限载荷对比。其中图7中横坐标表示实验持续时间,纵坐标分别为摩擦系数和载荷。载荷随着实验时间的增加而增加,32#基础油的临界载荷为50n,此时油膜破裂摩擦系数突增,并且摩擦表面出现严重的胶合磨损,如图8所示。mos2纳米润滑油的极限载荷为520n,且载荷为500n时摩擦表面仅为轻微的擦伤磨损,如图9所示。表明mos2纳米润滑油相较基础油能显著提升油膜的临界载荷(由50n增加到500n)的同时并减少摩擦表面的磨损。
44.图10为32#基础油和实施例1中mos2纳米润滑油的磨斑直径对比。在极压特性实验中,设置参数为载荷650n、转速1500r/min。由图可知mos2纳米润滑油的磨斑直径为0.74mm,磨斑直径相较于基础油1.31mm降低了约43%,表明二硫化钼的引入能显著降低极压特性下的磨斑直径。
45.对比例1
46.本对比例二硫化钼纳米润滑油的制备方法为:将1.5g二硫化钼粉末加入到36g基础油中,采用实施例1步骤b中相同的方法进行加热搅拌,得到二硫化钼分散液;然后采用实施例1步骤c中相同的方法,将二硫化钼分散液与262.5g基础油混合,进行超声分散处理,处理结束后,即得到的二硫化钼纳米润滑油。本对比例中所用的基础油与实施例1中的相同,所用的二硫化钼粉末与实施例1中的也相同。
47.图3至图6为实施例1和对比例1所制备的润滑油的稳定性测试结果。图3和图4为分
别为实施例1中制备的纳米润滑油和放置20天后的纳米润滑油实拍图,从图中可以看出,实施例1中制备的二硫化钼纳米润滑油在放置20天后,无明显聚集沉降现象,说明其具备优异的悬浮稳定性。而作为对比,图5和图6为对比例1中制备的纳米润滑油和放置3天后的纳米润滑油实拍图,从图中可以看出,放置3天后,对比例1中的纳米润滑油中的二硫化钼颗粒几乎完全沉降,上层为透明的基础油,说明其悬浮稳定性较差。另外,实施例1中的二硫化钼纳米润滑油长时间放置后(一个月以上),仅需简单的机械摇晃即可继续保持其悬浮稳定性,而对比例1中制备的润滑油在放置3天后,通过简单的机械摇晃也无法继续保持其悬浮稳定性。
48.实施例2
49.本实施例中,能稳定存在的二硫化钼纳米润滑油,由二硫化钼粉末、分散剂混合液和基础油组成;二硫化钼纳米润滑油中,分散剂混合液的质量分数为12wt%,二硫化钼粉末的质量分数为0.3wt%;所述分散剂混合液由油酸、(oleic acid,化学式c
18h34
o2)、油胺(oleylamine,化学式c
18h37
n)和正十二硫醇(1-dodecanethiol,化学式c
12h26
s)组成,油酸、油胺和正十二硫醇的质量之比为1:2:1;二硫化钼粉末的粒径为50~200nm;所述基础油为150#基础油,也为工业级白油。
50.上述能稳定存在的二硫化钼纳米润滑油的制备方法包括如下步骤:
51.步骤a:将9g油酸、18g油胺和9g正十二硫醇一同加入到烧杯中进行混合,得到分散剂混合液;
52.步骤b:将0.9g二硫化钼粉末加入到所述分散剂混合液中,得到混合反应体系;用玻璃棒充分搅拌后将烧杯置于加热台表面,设定加热台温度为180℃。同时利用磁力搅拌进行分散,设置转速为600r/min,保持混合反应体系温度为180℃,磁力搅拌2h后反应结束,自然冷却至室温,即得到分散剂修饰改性二硫化钼混合液;
53.步骤c:将上述分散剂修饰改性二硫化钼混合液与263.1g基础油【本实施例所用基础油为150#基础油,其在40℃条件下运动粘度为145~155mm2/s】混合,用玻璃棒充分搅拌后利用超声波处理器进行超声分散处理,超声分散的具体设置参数为额定功率1200w的90%,工作模式为:超声分散和间隔时间均为1秒(即超声分散1秒后,停顿1秒,接着继续超声分散1秒,停顿1秒,如此循环),超声分散时,控制其温度为110℃,持续分散90min后自然冷却至室温,得到二硫化钼纳米润滑油。
54.在其他一些实施例中,也可以采用46#基础油、68#基础油、100#基础油、250#基础油、300#基础油或400#基础油(xx#基础油代表的含义为:在40℃条件下,其运动粘度约为xxmm2/s)中的任意一种与分散剂修饰改性二硫化钼混合液混合制备得到二硫化钼纳米润滑油;均可以实现不容易聚集沉降、悬浮稳定性好的二硫化钼纳米润滑油,且长时间放置后(一个月以上)仅需简单的机械摇晃即可继续保持其悬浮稳定性。
55.图11为不同型号的基础油和采用不同型号基础油制备的质量分数0.5wt%的mos2纳米润滑油的磨斑直径对比。在极压特性实验中,设置参数为载荷650n、转速1500r/min,从低粘度基础油(32#基础油,40℃下运动粘度28~35mm2/s)到高粘度基础油(400#基础油,40℃下运动粘度380~420mm2/s),采用与实施例1相同的方法制备的mos2纳米润滑油均能显著降低钢球的平均磨斑直径,说明采用本发明的制备方法能够有效提升不同粘度的基础油的润滑特性。另外,粘度越高的基础油,制备得到的二硫化钼纳米润滑油的悬浮稳定性越好,
采用本发明的制备方法,即使采用粘度最小的32#基础油,制备得到的二硫化钼纳米润滑油也能保持20天以上的悬浮稳定性。
56.显然,上述实施例仅仅是为清楚地说明所作的举例,而并非对实施方式的限定。对于所属领域的普通技术人员来说,在上述说明的基础上还可以做出其它不同形式的变化或变动。这里无需也无法对所有的实施方式予以穷举。而由此所引伸出的显而易见的变化或变动仍处于本专利申请权利要求的保护范围之中。
再多了解一些
本文用于企业家、创业者技术爱好者查询,结果仅供参考。