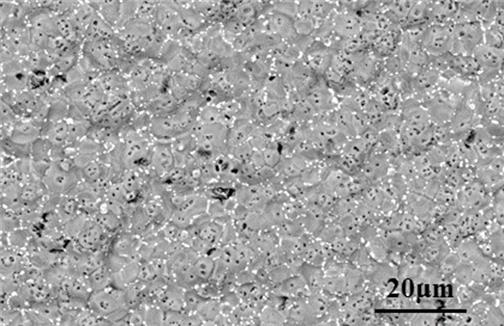
1.本发明属于热障涂层的等离子物理气相沉积制备技术领域,具体为涉及一种单晶叶片上的热障涂层制备方法。
背景技术:
2.热障涂层用于燃气轮机,尤其是航空发动机的高温热端部件,配合气膜冷却技术,可以提高热端部件的使用寿命,典型的热障涂层分金属粘结层和陶瓷面层,金属粘结层一般使用mcraly(m为ni,co或ni和co)或者ptal涂层,陶瓷面层一般采用ysz材料。目前随着航空发动机的推重比提高,涡轮前温度已经高达1500-2000℃,所用高温合金表面的温度高达1150℃,普通的定向高温合金已经无法承受如此高的温度,目前都采用了单晶高温合金来提高热端部件的使用温度,但是超过1100℃后,mcraly粘结层中的cr元素会氧化为cro3,挥发后会形成孔洞,降低粘结层和陶瓷层的结合力,造成热障涂层的失效。为了提高热端部件的长期抗氧化性能,目前一般使用al含量更高的铂铝涂层,陶瓷面层一般采用大气等离子喷涂和电子束物理气相沉积技术制备,但是这两种工艺都有其缺点,大气等离子喷涂是层状结构,隔热性能更好,但是热震寿命较差,而电子束物理沉积是柱状结构,热震性能好,但隔热性能较差。等离子物理气相沉积技术是兼具了两种传统技术的优点,既有较好的热震寿命,也有较好的隔热性能,并且还具备非视线沉积等独特的优势。因此新型的热障涂层发展趋势是采用铂铝涂层 等离子物理气相沉积面层的技术路线。
3.目前铂铝涂层的主要制备方法是采用电镀和物理沉积等方法先制备一层铂,然后高温扩散,再进行渗铝,渗铝根据工艺不同分为包埋渗、料浆渗、气相渗和cvd渗铝等方法,其中包埋渗和料浆渗制备的涂层致密性差,表面有污染物,需要后继清洗工艺,并且无法对内腔进行渗铝,因此目前主要采用的渗铝工艺是气相渗和cvd渗铝,渗铝后的组织有单相β-niptal和双相ptal2 β-niptal。根据渗铝温度高低,又分为高温低活性渗铝和低温高活性渗铝,这里活性是指al和ni的相对活性,现有研究表明,当温度大于1000℃时,ni的活性比al高,ni向往扩散快,渗铝层向外生长为主,容易形成单相β-niptal涂层,当温度低于1000℃时,ni的活性比al低,al向内扩散快,渗铝层向内生长为主,容易形成双相ptal2 β-niptal涂层。
4.目前的主流渗铝工艺采用在1040-1080℃温度范围内进行高温渗铝,这样有利于形成外向生长型的单相β-niptal涂层,普遍认为单相β-niptal涂层的抗氧化和与陶瓷面层匹配性能更好,如cn105624522b中采用电镀1-15微米的铂,然后1000-1100℃做镀铂后扩散热处理,在900-1100℃采用包埋渗或者气相渗铝,渗铝后在1000-1200℃进行渗铝后的热处理,可以制备出单相β-niptal涂层。但是在叶片的实际生产过程发现,高温热处理和渗铝工艺会影响叶片,尤其是单晶叶片的力学性能。在dd6单晶高温合金上,使用1080℃,6hcvd渗铝后,1100℃,130mpa下的高温持久性能从原来》100h,降低到不到60h;在ic21单晶高温合金上,使用1000℃,6h 气相渗铝后,980℃的高温拉伸性能从原来》600mpa,降低到不到400mpa。
技术实现要素:
5.基于现有技术的不足,本发明提出了一种低温制备铂铝涂层,然后在铂铝涂层表面采用少量喷涂介质和工业盐混合处理的方法,处理过程中喷涂介质不会堵住气膜冷却孔,并且经过处理后的表面再等离子物理气相沉积制备陶瓷涂层后,具有更好的寿命。
6.本发明完整的技术方案包括:一种单晶叶片上的热障涂层制备方法,包括如下步骤;步骤(1):制备低温渗铝的铂铝涂层:在单晶叶片基体上电镀1-7微米的铂层,随后在900℃温度下进行扩散热处理4h,再在800-850℃下进行气相渗铝或者cvd渗铝;步骤(2):对渗铝粘结层表面进行喷盐处理;采用粒度为80-500目的工业食盐和白刚玉的混合物作为喷盐介质,工业食盐和白刚玉的混合比例为(6~9.5):1,以上比例为重量比;将混合好的喷盐介质加入喷砂机,调节压缩空气的压力0.1-0.6mpa,对工件表面进行喷盐处理,喷盐过程中的角度为45-90
°
;步骤(3):在喷盐后对叶片进行水洗,再进行等离子物理气相沉积方法制备陶瓷层。
7.步骤(1)中铂层厚度为3微米。
8.步骤(2)中所述喷盐介质粒度为300目。
9.步骤(2)中工业食盐和白刚玉的混合比例为9:1,以上比例为质量比。
10.步骤(2)中所述压缩空气的压力为0.2mpa。
11.步骤(2)中所述喷盐过程中的角度为70
°
。
12.相比现有技术,本发明具有如下优点:1. 本发明针对具有大量气膜冷却孔的叶片工件,采用湿喷砂后会使刚玉砂进入气膜冷却孔内引起堵孔的问题,将传统的喷砂处理改成混合可溶性盐类的喷盐工艺,在保证去除疏松层效果的前提下,可以通过后续水洗程序将刚玉砂清除,不会造成堵孔,工艺可以使用普通干喷砂设备进行,采用的喷盐介质成本低,无毒害,容易实现批量生产。
13.2. 本发明采用低温渗铝工艺制备粘结层,处理后的粘结层,在后继采用等离子物理气相沉积的方法制备陶瓷层不会发生剥落,另外对单晶叶片的力学性能高温持久性能和高温拉伸性能等没有影响。
附图说明
14.图1为低温渗铝后粘结层的表面疏松层显微表面照片;图2为低温渗铝后粘结层的表面疏松层显微横截面照片;图3为低温渗铝后粘结层喷盐去除疏松层后的横截面照片。
具体实施方式
15.下面将结合本技术实施方式中的附图,对本技术的实施方式中的技术方案进行清楚、完整的描述,显然,所描述的实施方式仅仅是作为例示,并非用于限制本技术。
16.先进航空发动机叶片一般采用单晶高温合金铸造,并且为了使用更高温度,表面都有大量的气膜冷却孔,一般在表面制备粘结层 陶瓷层的热障涂层体系,配合气膜冷却技术,可以隔热100-300℃,常用的粘结层制备工艺包括采用先电镀铂再渗铝的工艺形成铂铝
涂层,现有的铂铝涂层渗铝工艺分为高温渗铝(高于1000℃)和低温渗铝(低于1000℃)工艺,在高温渗铝的情况下,涂层会向外生长,和al形成涂层,此时铂铝涂层较为致密,但是高温渗铝会影响合金力学性能。而采用低温渗铝涂层一般以内扩散为主,低温渗铝工艺得到的铂铝涂层表面比高温渗铝工艺要疏松,在后继等离子物理气相沉积制备陶瓷层过程中发现氧化膜在疏松表面结合力不好而发生剥落。
17.现有技术中可以通过湿喷砂来进行表面处理,以去除工件表面的氧化层等,但是该方式不适用于本实施方式中应用的叶片,因为叶片上有大量气膜冷却孔,采用湿喷砂后会使刚玉砂进入气膜冷却孔内引起堵孔。因而如何对低温渗铝的叶片粘结层表面进行有效地处理,成为制约该工艺在产业上应用的瓶颈问题。本发明在实践过程中,尝试在喷砂后采用水洗的方式去除气膜冷却孔内的刚玉砂,但通过研究发现,在进入气膜冷却孔内的刚玉砂数量不多时,可以在水洗过程中被冲洗掉,但当进入气膜冷却孔内的刚玉砂超过孔体积的一定比例后,通过水洗的方法就无法将孔内的砂子去除。针对上述问题,本发明采用控制进入孔内的刚玉砂量的技术思路,具体为采用刚玉砂和易溶于水的盐类(如氯化钠)的混合物作为介质进行喷盐处理,硬质的刚玉砂去除低温渗铝表面的疏松层,氯化钠随着刚玉砂进入气膜冷却孔内,并占据孔内绝大部分空间,在后续水洗时,氯化钠溶于水,孔内剩余的空间增大,刚玉砂会被冲洗出来。采用这种方法既可以去除低温渗铝表面的疏松层,又可以防止堵孔发生。在经过处理后的低温渗铝表面再等离子物理气相沉积制备陶瓷层,就不会再发生剥落的问题。
18.该方案的实现具体包括以下步骤:步骤一、制备低温渗铝的铂铝涂层:具体包括在基体上电镀1-7微米,优选3微米的铂层,随后在900℃温度下进行扩散热处理4h,再在800-950℃下进行气相渗铝或者cvd渗铝,所述渗铝过程中al向内扩散快,渗铝层以向内生长为主,形成双相ptal2 β-niptal涂层。
19.步骤二、对低温渗铝粘结层表面进行喷盐处理,采用80-500目,优选300目的工业食盐和白刚玉的混合物作为喷盐介质,在喷盐介质的粒度和混合比例选择上,本发明考虑以能有效去除叶片表面疏松层,不损伤叶片内部组织,且后续能顺利水洗掉为综合考虑因素。根据实践结果发现,采用300目的工业食盐和白刚玉的混合物的喷盐效果较好,同时经过验证发现,在采用上述介质时,需要使进入气膜冷却孔内的刚玉砂不超过孔体积的40%,因此比例设置时需要遵循上述原则,综合考虑到工业食盐和白刚玉的密度和在喷砂机中的装填特性,本发明选择工业食盐和白刚玉的混合比例为(6~9.5):1,重量比,优选为9:1。对混合好的喷盐介质加入喷砂机,调节压缩空气的压力0.1-0.6mpa,优选0.2mpa,对工件表面进行喷盐处理,喷盐过程中的角度为45-90
°
,优选的70
°
,喷涂时间以表面喷涂均匀,并用光学放大镜检查表面,以疏松表面完全去除为准。
20.步骤三、在喷盐后对叶片进行水洗以去除表面和气膜冷却孔中的喷盐介质,再进行等离子物理气相沉积制备陶瓷层。
21.本发明针对在低温渗铝表面进行等离子物理气相沉积制备的陶瓷层的叶片存在制备后剥落和泡水剥落的问题,提出了一种喷盐的表面处理方法。该发明的特点是经过处理的叶片表面不堵气膜冷却孔,制备陶瓷层后无泡水剥落的问题,且使用的设备简单,喷盐介质无毒害,适合于批量生产,具有广阔的应用前景。
22.以上申请的仅为本技术的一些实施方式。对于本领域的普通技术人员来说,在不脱离本技术创造构思的前提下,还可以做出若干变型和改进,这些都属于本技术的保护范围。
再多了解一些
本文用于企业家、创业者技术爱好者查询,结果仅供参考。