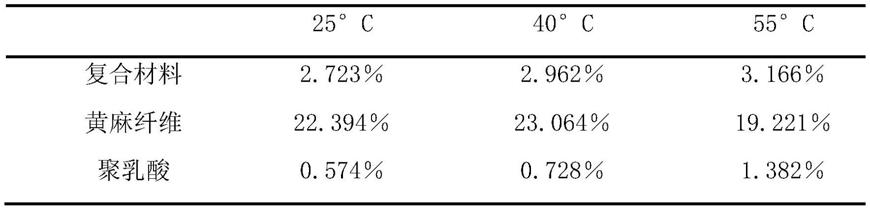
1.本发明属于复合材料的检测技术领域,具体涉及一种基于细观建模的植物纤维/聚乳酸复合材料湿热老化性能多尺度预测方法。
背景技术:
2.可降解是植物纤维增强复合材料最重要的优点之一。然而由于植物纤维的吸湿性和聚乳酸的可降解特性,其在湿度、湿热等服役环境下的耐久能力仍面临巨大挑战。目前面向汽车服役工况的复合材料老化研究主要集中在传统合成纤维增强树脂,例如碳纤维、玻璃纤维增强环氧树脂、酚醛树脂等。而对于植物纤维增强聚乳酸复合材料,由于植物纤维特有的亲水性和典型的多尺度多层次微观结构,以及聚乳酸自身的可降解特征,导致了其环境老化研究更加复杂和困难。
3.植物纤维增强复合材料的力学性能对湿热环境非常敏感。实验研究表明,吸湿和水热老化都会显著降低植物纤维增强复合材料的力学性能,影响其使用寿命。在植物纤维中,负责吸收水分的成分主要是半纤维素,半纤维素含量越高,水分吸收和降解程度越高,而不同的植物纤维结构形态也对水分扩散存在影响。通常在室温下的植物纤维增强复合材料的吸水规律遵循fickian扩散规律,初始呈线性变化,长时间后吸水性逐渐变缓,趋于饱和。而在较高的温度下,吸湿行为显著加快,水分饱和时间大大缩短。
4.由于植物纤维的亲水性和复杂结构特点,以及聚乳酸基体的可降解性,长期湿热环境作用往往会引起复合材料中各组分(纤维、基体和纤维-基体界面)性能均发生改变,而目前关于老化预测模型及方法的研究大都只针对纤维和基体,忽略了纤维/基体自身降解及其所带来的界面分离现象,不能从微-细-宏观层面多尺度充分反应分析短植物纤维增强复合材料中纤维、基体及界面各组分衰退对材料力学性能的影响。
技术实现要素:
5.针对低碳汽车轻量化零部件设计需求,本发明提供一种基于细观建模的植物纤维/聚乳酸复合材料湿热老化性能多尺度预测方法,为植物纤维/聚乳酸绿色复合材料在实际工程中的设计应用中提供参考和指导。
6.为实现上述发明目的,本发明提供以下技术方案:一种基于细观建模的植物纤维/聚乳酸复合材料湿热老化性能多尺度预测方法,包括以下步骤:
7.1)制备植物纤维/聚乳酸复合材料,分别对复合材料、聚乳酸基体和植物纤维进行老化试验:选取典型植物纤维作为填充相,可降解聚乳酸作为基体材料,制备植物纤维/聚乳酸复合材料;参考汽车行业零部件加速老化标准,把事先干燥好的植物纤维、聚乳酸基体、植物纤维\聚乳酸复合材料放入不同温度的恒温水槽中进行人工加速老化,得到不同老化温度和老化时间的老化材料;
8.2)建立不同温度下的各材料吸水率随老化时间变化规律函数:对步骤1)中得到的
老化材料进行吸水率测试,聚乳酸基体和植物纤维\聚乳酸复合材料的吸水率可以直接通过电子秤测量,植物纤维的吸水率由聚乳酸基体和复合材料的吸水率间接计算,对各温度下材料吸水率随老化时间变化规律进行拟合,得到三种材料的吸水率(m)与老化温度(t)和老化时间(t)之间的函数,分别为纤维mf(t,t),聚乳酸基体mm(t,t)和复合材料mi(t,t);
9.3)建立不同温度下的各组分强度随老化时间变化规律函数:对步骤1)中得到的老化材料进行强度测试:其中,对聚乳酸基体进行哑铃拉伸试验,对植物纤维进行单纤维拉伸试验,对复合材料进行单纤维拔出试验,分别得到不同温度下聚乳酸基体、植物纤维、复合材料三者强度随老化时间变化的函数:sm(t,t),sf(t,t)和si(t,t);
10.4)分别建立聚乳酸基体、植物纤维、复合材料各组分强度与吸水率、温度之间关系函数:对前面获得的数据进行整合,通过拟合数据分别得到植物纤维、聚乳酸基体和纤维-基体界面三者强度随吸水率和老化温度变化的函数,分别为纤维sf(m,t),基体sm(m,t)和纤维-基体界面si(m,t);
11.5)复合材料细观rve模型建立:从未老化植物纤维/聚乳酸复合材料中采样,进行x射线断层扫描,获得包含材料微观结构信息的断层灰度图像;对断层图像进行三维可视化分析,建立三维视图并完成纤维及聚乳酸基体的几何简化清理,将重构几何模型导入有限元分析软件,建立植物纤维/聚乳酸复合材料的细观rve模型;
12.6)环境退化因子定义与引入:编写植物纤维、聚乳酸基体、复合材料界面模拟单元本构关系,对复合材料细观rve模型进行属性定义,构建基于强度变化函数的各组分环境退化因子(d)函数,
[0013][0014]
其中s(m
′
,t
′
)是温度为t
′
,吸湿度为m
′
时的强度,s(m0,t0)是材料初始强度。由上式可以得到纤维的退化因子函数df(m,t),基体的退化因子函数dm(m,t)和纤维-基体界面的退化因子函数di(m,t);
[0015]
7)复合材料弹性性能计算:引入退化因子,对各组分弹性性能参数进行修正;在周期性边界条件下,对rve模型施加线性不相关位移载荷并进行仿真,获得不同温度和吸水率的宏观复合材料弹性性能;
[0016]
8)复合材料失效强度计算:针对细观模型中的植物纤维、聚乳酸基体和复合材料界面三个组分,分别定义对应的初始失效准则和损伤扩展准则,引入退化因子,对失效参数进行修正,并进行数值模拟,得到不同吸水率和温度下的宏观复合材料失效强度;
[0017]
9)宏观复合材料湿热老化性能预测:建立复合材料拉伸、三点弯曲试件宏观模型,将基于细观rve模型仿真得到的依赖吸水率和温度变化的复合材料宏观弹性性能函数和失效强度函数,代入到宏观模型中,设置湿热环境进行有限元分析,对湿热老化工况下不同老化程度的植物纤维/聚乳酸复合材料力学性能进行预测。
[0018]
步骤1)中,所述植物纤维/聚乳酸复合材料由黄麻纤维和聚乳酸颗粒通过注塑成型制备得到。
[0019]
步骤5)中,所述有限元软件为abaqus软件;所述三维可视化分析采用avizo9.0软件。
[0020]
步骤8)中,纤维的失效准则采用最大应力准则;聚乳酸基体失效准则采用广义的
mises失效准则;对复合材料中纤维-基体界面采用二次应力准则。
[0021]
与现有技术相比,本发明的有益效果为:
[0022]
1)本发明围绕我国“碳达峰”、“碳中和”建设目标,针对当前节能减排和环境保护的时代需求,进行面向低碳汽车的植物纤维/聚乳酸绿色复合材料老化性能多尺度预测方法研究,探索农作物原料化新路径,破解石油能源危机困局,为植物纤维/聚乳酸绿色复合材料在汽车零部件领域的进一步应用提供参考和基础。
[0023]
2)目前关于短植物纤维/聚乳酸复合材料的湿热老化研究更多关注水分扩散理论模型的建立和完善、以及结构内应力分析等,尚未形成系统有效的老化后力学性能预测模型及方法。本发明从考虑各组分性能的细观建模出发,构建依赖吸水率变量的纤维、基体以及界面性能修正函数,实现多个因素耦合影响下的短植物纤维/聚乳酸复合材料老化后弹性性能及失效强度预测,为复合材料的性能预测提供新思路。
[0024]
3)在长期服役过程中,受到环境、载荷、磨损等因素的影响,汽车零部件结构存在不同程度的老化现象,需要定期进行更新和维护。相较于金属和传统塑料等材质,植物纤维/聚乳酸复合材料对服役工况更加敏感,老化现象更加明显。如果超过部件服役寿命,则可能丧失使用功能,甚至造成严重的安全事故。而未达到使用寿命极限就提前更新维护,同样会造成人力和材料的极大浪费,显著增加使用成本。本发明所提供的老化性能模拟及寿命预测方法能够有效支撑绿色复合材料零部件结构设计理论,为制定合理的维护周期及方式提供参考,从而减少经济成本。
附图说明
[0025]
图1是本发明基于细观建模的植物纤维/聚乳酸复合材料湿热老化性能多尺度预测方法的工艺流程图。
具体实施方式
[0026]
对本发明的基于细观建模的植物纤维/聚乳酸复合材料湿热老化性能多尺度预测方法作进一步详细说明:
[0027]
一种基于细观建模的植物纤维/聚乳酸复合材料湿热老化性能多尺度预测方法,如图1所示,包括以下步骤:
[0028]
1)植物纤维/聚乳酸复合材料制备及老化试验:本发明选用黄麻纤维作为填充相,选用可降解聚乳酸作为基体材料,将黄麻纤维和聚乳酸颗粒在真空干燥箱中去除水分,用碱/硅烷偶联剂处理黄麻纤维,并按照1:9的比例(本实施例中所述比例仅仅为了说明模型建立,本发明适用于任何比例)将黄麻纤维和聚乳酸颗粒充分混合得到黄麻纤维/聚乳酸复合材料。通过双螺杆挤出机制备黄麻纤维/聚乳酸颗粒,经烘干处理后,再通过塑料注射成型机制备所需要的试样;同时采用上述方法分别制备纯黄麻纤维试样和聚乳酸试样,分别选取25℃、40℃、55℃水浴作为老化工况,对聚乳酸、黄麻纤维和复合材料进行湿热加速老化,老化完成后对试样干燥;
[0029]
2)建立不同温度下的各老化材料吸水率随老化时间变化规律函数:通过电子秤称重法计算纯聚乳酸基体和复合材料的吸水率,通过定期监测黄麻纤维/聚乳酸复合材料、黄麻纤维和纯聚乳酸三者的平均吸水率,直到达到fickian式中的平衡吸水率m
∞
,复合材料和
纯聚乳酸材料中的吸水率m按照astm d5229标准来计算。
[0030][0031]
纤维的吸水率通过下式获得
[0032]
δmc=δmf×vf
δwm(1-vf)
[0033]
通过实验分别得到黄麻纤维/聚乳酸复合材料、黄麻纤维和纯聚乳酸三者不同温度下的饱和吸水率,
[0034]
表1不同温度下的各老化材料的饱和吸水率
[0035][0036]
整合试验数据分别得到不同老化温度下复合材料、聚乳酸基体和黄麻纤维吸水率随老化时间变化的规律;
[0037]
3)建立不同温度下的各组分强度随老化时间变化规律函数:选取不同老化温度和老化时间的材料进行力学性能试验,对复合材料进行单纤维拔出试验、对纤维进行单纤维拉伸试验、对聚乳酸基体进行哑铃拉伸试验,分别得到三个组分达到饱和吸水率时的强度下降比例,如下表所示:
[0038]
表2不同温度下各组分强度变化情况(相比于初次强度下降百分比)
[0039][0040]
通过对试验获得的数据整合分别得到基体-纤维界面的强度随老化温度、老化时间变化的规律,纤维强度随老化温度、老化时间变化的规律,聚乳酸基体强度随老化温度、老化时间变化的规律;
[0041]
4)分别建立聚乳酸基体、纤维、复合材料各组分强度与吸水率、温度之间关系函数:对前面获得的数据进行整合,通过拟合数据分别得到植物纤维、聚乳酸基体和纤维-基体界面三者强度随吸水率和老化温度变化的函数
[0042]
sf(m,t)=14.82787 0.9456t-0.03143m-0.01163t
2-0.02714m
2-0.00991mt
[0043]
sm(m,t)=42.16438 0.49302t-17.52793m-0.0065t
2-24.68074m2 0.37515mt
[0044]
si(m,t)=-1.23196 3.11211t 9.87753m-0.03748t
2-1.82922m
2-0.3378mt
[0045]
5)复合材料细观rve模型建立:从未老化植物纤维/聚乳酸复合材料中采样,进行x射线断层扫描,获得包含材料微观结构信息的断层灰度图像;采用avizo9.0软件对植物纤维/聚乳酸复合材料的断层图像进行三维可视化分析。为了去除图像中杂质的影响,首先采
用中值滤波技术对原始图像进行过滤简化处理;然后采用avizo 9.0软件中的修复功能对天然纤维表面孔洞进行闭合清理,并对修复完成的植物纤维体素模型进行表面平滑处理;最后将重构的几何模型导入有限元分析软件abaqus软件,建立复合材料的细观rve模型;
[0046]
6)环境退化因子定义与引入:编写纤维、基体、界面模拟单元本构关系,对复合材料细观rve模型进行属性定义。构建基于强度变化函数的各组分环境退化因子(d)函数
[0047][0048]
分别得到纤维的退化因子函数
[0049]df
(m,t)=0.46337 0.02955t-0.00098m-0.00036t
2-0.00085m2 0.00031mt,
[0050]
基体的退化因子函数
[0051]dm
(m,t)=0.84329 0.00986t-0.35056m-0.00013t
2-0.49361m2 0.00750mt,
[0052]
纤维-基体界面的退化因子函数
[0053]di
(m,t)=-0.02124 0.05366t 0.17030m-0.00065t
2-0.03154m
2-0.00582mt,
[0054]
并将退化因子引入对应本构,实现基于老化效应的各组分本构参数修正;
[0055]
7)复合材料弹性性能计算:通过引入退化因子,对各组分弹性性能参数进行修正;在周期性边界条件下,对rve模型施加线性不相关位移载荷并进行仿真,获得不同温度和吸水率条件下的宏观复合材料弹性性能;
[0056]
8)复合材料失效强度计算:由于在细观状态下研究尺度很小,所以在细观模型中将短植物纤维视为各向同性材料,将植物纤维表示为线弹性本构,纤维的失效准则采用最大应力准则;聚乳酸基体通常考虑为各向同性弹塑性材料,失效准则采用广义的mises失效准则;对纤维-基体界面采用内聚力本构,采用二次应力准则;对失效参数进行修正,并进行数值模拟,得到不同吸水率和温度下的宏观复合材料失效强度;
[0057]
9)宏观复合材料湿热老化性能预测:建立复合材料拉伸、三点弯曲试件宏观模型,其中,复合材料拉伸标准采用iso 527-2,三点弯曲标准采用en iso14125,将基于细观rve模型仿真得到的依赖吸水率变化的复合材料宏观弹性性能和失效强度,代入到宏观模型中,设置湿热环境进行有限元分析,对湿热老化工况下不同老化程度的植物纤维/聚乳酸复合材料力学性能进行预测,结果显示拉伸实验误差为7.86%,三点弯曲试验误差为8.13%,这表明本发明预测方法在植物纤维/聚乳酸复合材料湿热老化性能预测上具有一定的实际意义。
再多了解一些
本文用于企业家、创业者技术爱好者查询,结果仅供参考。