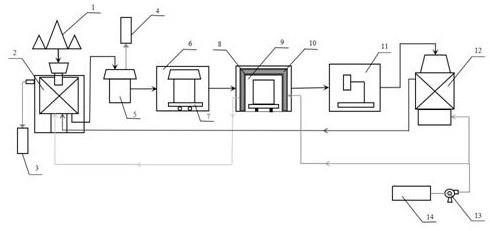
1.本发明涉及电熔镁砂冶炼领域,特别涉及一种高效的电熔镁坨余热回收设备及工艺。
背景技术:
2.由于我国工业化进程的不断推进,使得国内的能源需求日益增长。为了降低能源体系供给侧的压力,需提高能源利用效率,而减少能源浪费以提高能源效率是目前普遍采用的一种方法,其中,在菱镁矿冶炼工艺过程中,所生产的镁熔坨含有大量的显热和潜热,冶炼后的镁熔坨中心温度在2800℃以上,外表面皮砂的温度在1000℃~1200℃。
3.传统的电熔镁砂生产工艺是将冶炼结束后生产的电熔镁坨自然冷却5~7天,这不仅恶化了周边环境,而且还浪费了大量的热能,为响应国家节能减排的号召,提高能源利用率,需对冶炼结束后镁熔坨的余热进行回收。
4.目前国内对于电熔镁坨的余热回收方法主要可分为单纯的通风取热、通水取热以及通风与通水相结合取热三种方式,其中单纯的通风取热需要大量的风,会导致换热后的热风温度不高,进而影响物料预热效果,而若采用通水取热,由于镁坨皮砂外表面温度可以达到1200℃,若用几十度的热水对热量进行回收,不符合梯级能量利用原则,且回收的热水只能用于供暖,不能用于预热物料。
技术实现要素:
5.(一)解决的技术问题为增加电熔镁冶炼工艺过程中预热物料的可用能,提高取热后空气的温度,本发明设计了一种高效的电熔镁坨余热回收工艺及设备,其中在余热回收室内设有导热率高的al-si合金相变储热材料,电熔镁坨首先在余热回收室内与相变材料进行辐射换热,辐射换热后,对相变储热材料内的热量进行通风取热,可提高换热后的热风温度。
6.然后将换热后的镁坨进行破碎,破碎后的电熔镁砂被送高温热交换塔,以通风的方式对破碎后的电熔镁砂进行取热,取热后的热风用于预热物料。
7.通过此工艺流程基本实现镁熔坨内热量的全部利用,并且回收得到的热量全部用于预热物料,不仅增加了预热物料的可用能,而且提高了物料预热温度。
8.本发明所述的工艺流程中涉及的设备包括,一号除尘器、物料预热塔、三相电弧炉、二号除尘器、密封脱壳室、余热回收室、破碎装置、高温热交换塔、鼓风机,其中,物料预热塔摆放在电弧炉之前,电弧炉上部设有二号除尘器,冶炼过程产生的高温烟气经二号除尘器除尘后用于生产干冰,电弧炉之后摆放脱壳室,脱壳室之后摆放用于回收镁坨余热的余热回收室,余热回收室内设有相变储热材料,相变储热材料内设有通风管道,管道入口侧与鼓风机相连通,出口侧与物料预热塔底部相连通,物料预热塔顶部设有进料口,左上侧设有低温空气出风口,出风口与一号除尘器连通,换热后的低温空气经一号除尘器除尘后排入大气,余热回收室之后摆放破碎装置,破碎装置之后摆放高温热交换塔,高温热交换塔顶
部设有进料口,底部右侧设有进风口,进风口侧与鼓风机相连通,上部左侧设有出风口,出风口侧经管道与物料预热塔底部相连通。
9.一种高效的电熔镁坨余热回收工艺及设备,主要步骤如下:利用余热回收室以及高温热交换塔换热后的热风对物料进行供热,其中,熔炼后的高温镁坨被送入余热回收室,余热回收室中镁坨的左、右、上侧设有al-si合金相变储热材料,被送入余热回收室的镁坨与al-si合金相变储热材料进行辐射换热,经60小时辐射换热后,镁坨内部已结晶氧化镁平均温度降到1350℃,此时余热回收室内al-si合金相变储热材料已经全部熔化,其温度为576℃,之后将换热后的镁坨送入破碎装置进行破碎,破碎后的镁坨被送入高温热交换塔,之后鼓风机先将30℃的空气通入高温热交换塔,经4个小时的通风取热后,可以得到250℃~860℃的热风,破碎后的镁坨经换热后从高温热交换塔下部排出分选,排出的电熔镁温度为250℃,得到的热风经管道送入物料预热塔对物料进行预热,然后鼓风机将30℃的空通入相变储热材料内的管道,经8小时的通风取热后,可以得到380℃的热风,所获得的热风经管道送入物料预热塔,最终可将物料预热至350℃,物料预热塔前4小时的通风流量为4000nm3/h,后8小时的通风流量为8000nm3/h。
10.本发明的优点主要有以下几个方面。
11.镁坨内的余热得到了充分的利用,所获得的的热风用于预热物料,提高了预热物料的可用能;采用相变储热材料对镁熔坨的热量进行回收,相变储热材料导热率高,通风取热后能够得到较高风温,进而能够提高物料预热温度。
附图说明
12.图1是本发明的工艺流程图。
13.附图中:1、菱镁矿;2、物料预热塔;3、一号除尘器;4、二号除尘器;5、三相电弧炉;6、密封脱壳室;7、摆渡小车;8、紫铜外壳;9、余热回收室;10、al-si合金相变储热材料;11、破碎装置;12、高温热交换塔;13、鼓风机;14、30℃空气。
具体实施方式
14.下面结合附图对本发明进行进一步说明。
15.如图1所示,一种高效的电熔镁坨余热回收工艺及设备,所述的工艺流程中涉及的设备包括,一号除尘器3、物料预热塔2、三相电弧炉5、二号除尘器4、密封脱壳室6、摆渡小车7、余热回收室9、相变储热材料10、相变储热材料外壳8、破碎装置11、高温热交换塔12、鼓风机13,其中,物料预热塔2摆放在电弧炉5之前,电弧炉5上部设有二号除尘器4,冶炼过程产生的高温烟气经二号除尘器4除尘后用于生产干冰,电弧炉之后摆放脱壳室6,脱壳室6之后摆放用于回收镁坨余热的余热回收室9,余热回收室内设有相变储热材料10,相变储热材料10内设有通风管道,管道入口侧与鼓风机相连通,出口侧与物料预热塔2底部相连通,物料预热塔2顶部设有进料口,左上侧设有低温空气出风口,出风口与一号除尘器3连通,换热后的低温空气经一号除尘器3除尘后排入大气,余热回收室9之后摆放破碎装置11,破碎装置11之后摆放高温热交换塔12,高温热交换塔顶部设有进料口,底部右侧设有进风口,进风口侧与鼓风机相连通,上部左侧设有出风口,出风口侧经管道与物料预热塔2底部相连通。
16.使用中,经物料预热塔2预热后的菱镁矿1被送入三相电弧炉5中进行熔炼,熔炼过程产生的烟气经二号除尘器4除尘后用于生产干冰,熔炼结束后用摆渡小车7将电弧炉5送入脱壳室6进行脱壳,脱壳后的镁坨外表面皮砂为1200℃,之后将脱壳后的镁坨送入余热回收室9中,在余热回收室内,镁坨与al-si合金相变储热材料10进行辐射换热,换热后的镁坨被送入破碎装置11进行破碎,破碎后的电熔镁砂被送入高温热交换塔12中;然后通过鼓风机13将30℃的空气14通入通入高温热交换塔12中进行换热,换热后的热风通入物料预热塔2中对物料预热,热交换塔中的换热过程完成后,鼓风机13再将30℃的空气14通入al-si合金相变储热材料10中进行换热,,换热后的热风通入物料预热塔2中对物料预热,经换热后的低温空气从物料预热塔2左上端的出口排出,排出的低温空气经一号除尘器3除尘后排放到大气。
17.根据本发明的工艺流程,熔炼后的镁坨与相变储热材料的辐射时间为60小时,辐射完成后,22吨的相变储热材料几乎全部熔化,此时相变储热材料温度达到576℃,相变材料储存的热量占镁坨所含热量的70%,然后将镁坨破碎送入高温热交换塔,破碎过程热损失占镁坨所含热量6.2%,此时热交换塔中破碎后电熔镁砂所含热量镁坨所含热量的23.8%,高温热交换塔的通风时间为4小时,可得到250℃~860℃的热风,相变储热材料的通风时间为8小时,可得到380℃的热风,取热后的热风用于物料预热,可将物料预热至350℃,与未预热的物料相比,熔炼每吨菱镁矿可节约电量92.1kwh,预热后的物料可直接送至电弧炉熔炼,以所需原料15吨的菱镁矿工艺为例,熔炼一个电熔镁坨可节约电量1381.5kwh。
再多了解一些
本文用于企业家、创业者技术爱好者查询,结果仅供参考。