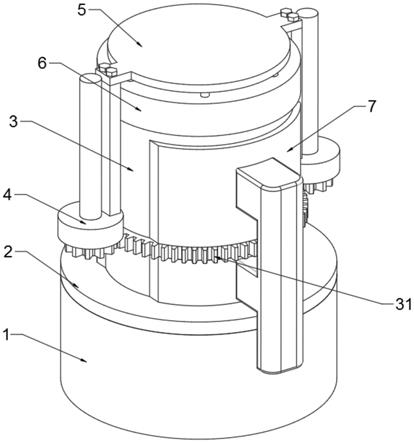
1.本发明涉及硅酸钠生产技术领域,具体为一种原硅酸钠生产方法及其生产装置。
背景技术:
2.原硅酸钠,又名正硅酸钠或原硅,广泛应用于配置各类洗剂、金属表面处理、陶瓷助磨剂、耐火剂原料、保塑保水剂原料、除油、纺织印染助剂及纸张脱墨剂等,目前针对原硅酸钠一般采用固体混合法,将偏硅酸钠与氢氧化钠进行混合,传统制备原硅酸钠的方法工艺流程长,设备多,能耗高,同时在混合时,由于在制备需要对反应釜进行多次升温,使得原料的混合物,容易粘接在反应釜内壁上,影响生产效率和成品质量。
3.为此,提出一种原硅酸钠生产方法及其生产装置。
技术实现要素:
4.本发明的目的在于提供一种原硅酸钠生产方法及其生产装置,以解决上述背景技术中提出的传统的制备方法工艺流程长,设备多,能耗高,同时在混合时,容易出现混合物粘接在反应釜内壁上的问题。
5.为实现上述目的,本发明提供如下技术方案:一种原硅酸钠生产方法及其生产装置,具体包括以下步骤,
6.s1、将固体氢氧化钠与硅微粉按照重量比2.5-3:1的比例加入反应炉中;
7.s2、通过加热组件一次升温,并启动搅拌机构,使固体氢氧化钠与硅微粉混合均匀;
8.s3、通过加热组件二次升温,使固体氢氧化钠完全熔融;
9.s4、通过加热组件三次升温,并启动搅拌机构,加快固体氢氧化钠与硅微粉反应,直至固体氢氧化钠与硅微粉完全反应后,停止加热,即得原硅酸钠粗品;
10.s5、将所述原硅酸钠粗品冷却至常温以下,使所述原硅酸钠粗品固化完全,即得原硅酸钠产品。
11.优选的,步骤s1中所述硅微粉的直径为0.2-0.6mm。
12.优选的,步骤s2中所述一次升温至100℃-120℃,保持当前温度5-10min。
13.优选的,步骤s3中所述二次升温至330-350℃,保持当前温度15-30min。
14.优选的,步骤s4中所述三次升温至450-550℃,保持当前温度1-2h。
15.一种原硅酸钠生产装置,包括底座,所述底座的上方设置有转盘,所述转盘的顶部固定连接有反应釜,所述反应釜外侧周表面上固定设置有齿圈,所述反应釜的两侧分别设置有传动机构且传动机构对称设于反应釜的两侧,所述反应釜的两侧均固定所述反应釜的内部的设置有搅拌机构,所述搅拌机构包括固定连接在反应釜中央处的定位柱,所述定位柱上活动套设有活动座,所述活动座外侧设置有刮环,所述反应釜的顶部活动连接有盖体,所述盖体的上方设置有连接盘。
16.优选的,所述活动座设于刮环上方,所述活动座和刮环之间设置有多个搅拌杆,所
述搅拌杆在反应釜的内部由上至下倾斜设置,所述搅拌杆两端分别与活动座的外壁和刮环的内壁固定连接。
17.优选的,所述连接盘两侧分别固定连接有连接部,所述连接盘底部设置有多个连接柱且多个连接柱对应刮环设置,所述连接柱顶部贯穿盖体并与转盘固定连接,所述连接柱的底部与刮环固定连接。
18.优选的,所述传动机构包括往复丝杆,所述往复丝杆底部固定连接有从动齿轮且从动齿轮与齿圈啮合连接,所述往复丝杆上套设有轴承座且所述轴承座与往复丝杆通过滚珠螺母副连接,所述轴承座一侧固定连接有连接杆,所述连接杆顶部延伸至与连接部固定连接。
19.优选的,所述底座的内部固定设置有驱动电机,所述驱动电机的输出端与转盘固定连接,所述底座两侧固定连接有多个支架,所述支架一侧固定连接有弧形加热板。
20.与现有技术相比,本发明的有益效果是:
21.1、本发明的相对于传统工艺的优点电量消耗低、工作人员少,体现出了生产流程步骤少,同时降低了人工成本,设备投资低,经济效益高;
22.2、本发明中由于反应釜内部的搅拌机构不受任何外力的驱动,而反应釜整体又是通过驱动电机带动转盘进行转动,而形成自转的,进而通过搅拌机构和反应釜的自转,反应釜的内部形成均匀搅拌的作用;
23.3、本发明中由反应釜的自转配合搅拌机构,对反应釜的内部形成搅拌,在搅拌的过程中,由于传动机构、连接盘和连接柱的设置,使得搅拌轮边搅拌进行往复的上下移动,从而通过刮环,可以对反应釜的内部形成刮蹭,避免反应釜受热固体氢氧化钠与硅微粉的混合物粘接在反应釜的内壁上;
24.4、本发明中两个弧形加热板的设置对反应釜形成半包覆,在实际使用中,由于反应釜的不断的自转的,从而通过两个弧形加热板对反应釜的四周进行均匀的升温加热,由于两个弧形加热板并非完全包覆反应釜的,从而相比较传统的,加热升温效果不变,减少了弧形加热板的实际使用面积,从而降低了设备的投资,同时也降低了能耗。
附图说明
25.图1为本发明的整体结构视图;
26.图2为本发明的反应釜的内部结构示意图;
27.图3为本发明的底座和弧形加热板的连接结构示意图;
28.图4为本发明的传动机构和反应釜的连接结构示意图;
29.图5为本发明的1转盘的结构示意图。
30.图中:
31.1、底座;
32.2、转盘;
33.3、反应釜;31、齿圈;32、搅拌机构;321、定位柱;322、活动座;323、刮环;324、搅拌杆;
34.4、传动机构;41、往复丝杆;42、轴承座;43、从动齿轮;
35.5、连接盘;51、连接柱;52、连接部;53、连接杆;
36.6、盖体;7、弧形加热板;8、驱动电机。
具体实施方式
37.下面将结合本发明实施例中的附图,对本发明实施例中的技术方案进行清楚、完整地描述,显然,所描述的实施例仅仅是本发明一部分实施例,而不是全部的实施例。基于本发明中的实施例,本领域普通技术人员在没有做出创造性劳动前提下所获得的所有其他实施例,都属于本发明保护的范围。
38.本发明提供一种原硅酸钠生产方法的技术方案:
39.实施例1:
40.一种原硅酸钠生产方法,具体包括以下步骤,
41.s1、将固体氢氧化钠与硅微粉按照重量比2.5-3:1的比例加入反应炉中,并且控制硅微粉的直径为0.2mm;
42.s2、通过加热组件一次升温至100℃,保持当前温度5min,并启动搅拌机构32,使固体氢氧化钠与硅微粉混合均匀;
43.s3、通过加热组件二次升温至330℃,保持当前温度15min,并通过搅拌机构32,使固体氢氧化钠完全熔融;
44.s4、通过加热组件三次升温至450℃,保持当前温度1h,并通过搅拌机构32,加快固体氢氧化钠与硅微粉反应,直至固体氢氧化钠与硅微粉完全反应后,停止加热,即得原硅酸钠粗品;
45.s5、将所述原硅酸钠粗品冷却至常温以下,使所述原硅酸钠粗品固化完全,即得原硅酸钠产品。
46.实施例2:
47.一种原硅酸钠生产方法,具体包括以下步骤,
48.s1、将固体氢氧化钠与硅微粉按照重量比2.5-3:1的比例加入反应炉中,并且控制硅微粉的直径为0.4mm;
49.s2、通过加热组件一次升温至110℃,保持当前温度10min,并启动搅拌机构32,使固体氢氧化钠与硅微粉混合均匀;
50.s3、通过加热组件二次升温至340℃,保持当前温度22min,使固体氢氧化钠完全熔融;
51.s4、通过加热组件三次升温至500℃,保持当前温度1.5h,并启动搅拌机构32,加快固体氢氧化钠与硅微粉反应,直至固体氢氧化钠与硅微粉完全反应后,停止加热,即得原硅酸钠粗品;
52.s5、将所述原硅酸钠粗品冷却至常温以下,使所述原硅酸钠粗品固化完全,即得原硅酸钠产品。
53.实施例3:
54.一种原硅酸钠生产方法,具体包括以下步骤,
55.s1、将固体氢氧化钠与硅微粉按照重量比2.5-3:1的比例加入反应炉中,并且控制硅微粉的直径为0.6mm;
56.s2、通过加热组件一次升温至120℃,保持当前温度10min,并启动搅拌机构32,使
固体氢氧化钠与硅微粉混合均匀;
57.s3、通过加热组件二次升温至340℃,保持当前温度30min,并通过搅拌机构32,使固体氢氧化钠完全熔融;
58.s4、通过加热组件三次升温至550℃,保持当前温度2h,并通过搅拌机构32,加快固体氢氧化钠与硅微粉反应,直至固体氢氧化钠与硅微粉完全反应后,停止加热,即得原硅酸钠粗品;
59.s5、将所述原硅酸钠粗品冷却至常温以下,使所述原硅酸钠粗品固化完全,即得原硅酸钠产品。
60.依据上述实施例1、实施例2和实施例3分别制备原硅酸钠时,同时分别记录三次制备原硅酸钠时,其中的二次升温时至体氢氧化钠完全熔融的时间、三次升温时至固体氢氧化钠与硅微粉完全反应后的时间和制备过程所用的电量能耗,并绘制成表1。
61.表1
[0062][0063][0064]
传统工艺与本发明的投资成本及能耗对比见表2:
[0065]
表2
[0066] 传统工艺本发明电量消耗/千瓦时600-700450-530设备操作/人4-81-3设备投资/万元150-20040-60
[0067]
综上所述,本发明提供的原硅酸钠生产方法,其生产流程短,根据表1和表2可以明显看出本发明的相对于传统工艺的优点电量消耗低、辅助工作人员少,地体现出了生产流程步骤少,同时降低了人工成本,设备投资低,经济效益高。
[0068]
实施例4,如图1-图5所示:
[0069]
一种原硅酸钠生产装置,包括底座1,其特征在于:所述底座1的上方设置有转盘2,所述转盘2的顶部固定连接有反应釜3,所述反应釜3外侧周表面上固定设置有齿圈31,所述反应釜3的两侧分别设置有传动机构4且传动机构4对称设于反应釜3的两侧,所述反应釜3的两侧均固定所述反应釜3的内部的设置有搅拌机构32,所述搅拌机构32包括固定连接在反应釜3中央处的定位柱321,所述定位柱321上活动套设有活动座322,所述活动座322外侧设置有刮环323,所述反应釜3的顶部活动连接有盖体6,所述盖体6的上方设置有连接盘5。
[0070]
作为本发明的一种实施例,如图2-图5所示,所述活动座322设于刮环323上方,所述活动座322和刮环323之间设置有多个搅拌杆324,所述搅拌杆324在反应釜3的内部由上至下倾斜设置,所述搅拌杆324两端分别与活动座322的外壁和刮环323的内壁固定连接。
[0071]
工作时,本发明中在反应釜3的设置搅拌机构32,由于搅拌机构32中的定位柱321
固定安装在反应釜3的内部中央处,且定位柱321底部活动套接有活动座322,在活动座322底部设置有刮环323,在实际安装中,刮环323设砸在活动座322的下方,并且在活动座322和刮环323设置有多个搅拌杆324,多个搅拌杆324沿定位柱321的轴线等距均匀分布,并且搅拌杆324的在反应釜3的内部成倾斜状设置,搅拌杆324两端分别与活动座322和刮环323固定连接,进而在反应釜3的内部由活动座322、刮环323和搅拌杆324拼接构成一个搅拌轮,通过搅拌轮可以在生产原硅酸钠时,将固体氢氧化钠与硅微粉在一次升温时,对二者进行均匀的混合。
[0072]
作为本发明的一种实施例,如图5所示,所述连接盘5两侧分别固定连接有连接部52,所述连接盘5底部设置有多个连接柱51且多个连接柱51对应刮环323设置,所述连接柱51顶部贯穿盖体6并与转盘2固定连接,所述连接柱51的底部与刮环323固定连接。
[0073]
工作时,本发明中在连接盘5的两侧分别固定连接有连接部52,在连接盘5的底部设置有连接柱51,连接柱51的顶部贯穿盖体6并延伸至于连接盘5固定连接,连接柱51的底部与刮环323固定连接,而由于活动座322是与定位柱321活动连接,进而当搅拌轮进行上下移动时,使得连接盘5和搅拌机构32整体之间发生联动关系。
[0074]
作为本发明的一种实施例,如图1、图2和图4所示,所述传动机构4包括往复丝杆41,所述往复丝杆41底部固定连接有从动齿轮43且从动齿轮43与齿圈31啮合连接,所述往复丝杆41上套设有轴承座42且所述轴承座42与往复丝杆41通过滚珠螺母副连接,所述轴承座42一侧固定连接有连接杆53,所述连接杆53顶部延伸至与连接部52固定连接。
[0075]
工作时,在反应釜3的两侧分别设置有传动机构4,传动机构4中的往复丝杆41底部固定连接从动齿轮43,并且从动齿轮43是与齿圈31啮合连接的,在实际安装传动机构4的过程中,可以使用外界的固定支撑组件如安装架或者支架将往复丝杆41与底座1进行固定安装,由于传动机构4上设置有轴承座42,由于轴承座42和往复丝杆41特殊的连接关系,使得当往复丝杆41发生转动时,轴承座42会沿着往复丝杆41进行往复的上下运动,在轴承座42固定连接有连接杆53,从而形成当轴承座42上下移动时,轴承座42通过连接杆53带动连接盘5进行上下移动,而连接盘5有通过连接柱51与搅拌轮连接,进而轴承座42、连接盘5和搅拌轮之间发生联动关系,即搅拌轮、轴承座42和连接盘5进行同步的上下高度上的位移。
[0076]
作为本发明的一种实施例,如图1和图3所示,所述底座1的内部固定设置有驱动电机8,所述驱动电机8的输出端与转盘2固定连接,所述底座1两侧固定连接有多个支架,所述支架一侧固定连接有弧形加热板7。
[0077]
工作时,由于底座1的内部固定设置有驱动电机8,而驱动电机8的输出端是与转盘2固定连接,而反应釜3是固定安装在转盘2上的,进而当转盘2通过驱动电机8带动进行转动时,转盘2上的反应釜3与转盘2同步转动,由于反应釜3通过转盘2进行转动,而实际安装中反应釜3又与其顶部的盖体6活动连接,从而形成反应釜3相对于盖体6发生了自转;
[0078]
由于反应釜3内部的搅拌机构32不受任何外力的驱动,而反应釜3整体又是发生自转的,进而通过搅拌机构32和反应釜3的自转,反应釜3的内部形成均匀搅拌的作用,反应釜3自转的同时,由于齿圈31的设置,而齿圈31与从动齿轮43为啮合连接,使得传动机构4中往复丝杆41通过从动齿轮43带动进行旋转,往复丝杆41转动,使得轴承座42沿着往复丝杆41的方向进行上下移动,从而轴承座42通过连接杆53带动连接盘5和搅拌轮进行转动,在实际安装中,搅拌轮中的刮环323外侧壁是贴合底座1的内壁设置的,进而形成由反应釜3的自转
配合搅拌机构32,对反应釜3的内部形成搅拌,在搅拌的过程中,由于传动机构4、连接盘5和连接柱51的设置,使得搅拌轮边搅拌进行往复的上下移动,从而通过刮环323,可以对反应釜3的内部形成刮蹭,从而防止在制备原硅酸钠时,反应釜3受热固体氢氧化钠与硅微粉的混合物粘接在反应釜3的内壁上;
[0079]
在底座1的上方通过支架固定连接有弧形加热板7,实际安装中,弧形加热板7可以贴合反应釜3的外壁设置,或者弧形加热板7与反应釜3的外壁之间设置一定的微小的间距,两个弧形加热板7的设置对反应釜3形成半包覆,在实际使用中,由于反应釜3的不断的自转的,从而通过两个弧形加热板7对反应釜3的四周进行均匀的升温加热,由于两个弧形加热板7并非完全包覆反应釜3的,从而相比较传统的,加热升温效果不变,减少了弧形加热板7的实际使用面积,从而降低了设备的投资,同时也降低了能耗,提高了弧形加热板7的使用率;
[0080]
在实际使用中反应釜3上开设有进料口和出料口(未图示),通过进料口向反应釜3中投入固体氢氧化钠与硅微粉。
[0081]
工作原理:工作时,启动驱动电机8,通过驱动电机8带动转盘2进行转动,转盘2上的反应釜3与转盘2同步转动,由于反应釜3通过转盘2进行转动,而实际安装中反应釜3又与其顶部的盖体6活动连接,从而形成反应釜3相对于盖体6发生了自转;
[0082]
由于反应釜3内部的搅拌机构32不受任何外力的驱动,而反应釜3整体又是发生自转的,进而通过搅拌机构32和反应釜3的自转,反应釜3的内部形成均匀搅拌的作用,反应釜3自转的同时,由于齿圈31的设置,而齿圈31与从动齿轮43为啮合连接,使得传动机构4中往复丝杆41通过从动齿轮43带动进行旋转,往复丝杆41转动,使得轴承座42沿着往复丝杆41的方向进行上下移动,从而轴承座42通过连接杆53带动连接盘5和搅拌轮进行转动;
[0083]
进而形成由反应釜3的自转配合搅拌机构32,对反应釜3的内部形成搅拌,在搅拌的过程中,由于传动机构4、连接盘5和连接柱51的设置,使得搅拌轮边搅拌进行往复的上下移动,从而通过刮环323,可以对反应釜3的内部形成刮蹭,避免反应釜3受热固体氢氧化钠与硅微粉的混合物粘接在反应釜3的内壁上;
[0084]
两个弧形加热板7的设置对反应釜3形成半包覆,在实际使用中,由于反应釜3的不断的自转的,从而通过两个弧形加热板7对反应釜3的四周进行均匀的升温加热,由于两个弧形加热板7并非完全包覆反应釜3的,从而相比较传统的,加热升温效果不变,减少了弧形加热板7的实际使用面积,从而降低了设备的投资,同时也降低了能耗。
[0085]
尽管已经示出和描述了本发明的实施例,对于本领域的普通技术人员而言,可以理解在不脱离本发明的原理和精神的情况下可以对这些实施例进行多种变化、修改、替换和变型,本发明的范围由所附权利要求及其等同物限定。
再多了解一些
本文用于企业家、创业者技术爱好者查询,结果仅供参考。