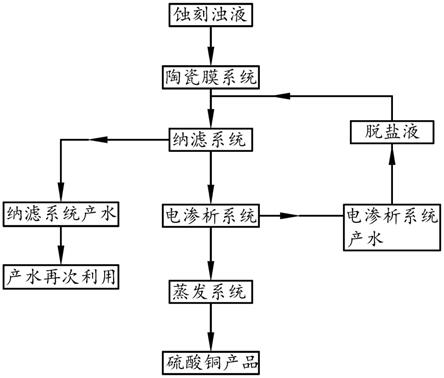
1.本发明属于资源回收技术领域,尤其涉及一种蚀刻废液中铜的资源化利用方法。
背景技术:
2.线路板蚀刻液中含有一定量的硫酸铜,如果直接排放,会对环境造成严重的污染。传统方法是采用电积技术,提取部分铜,然后排放。这样不仅浪费了大量的铜,同时对环境造成严重的污染。
3.申请号为cn201210304391.7的中国专利申请公开了一种酸性蚀刻液循环再生系统,包括依次连接的蚀刻生产线用水设备(1)、中转母液罐(2)、母液罐(3)、酸性蚀刻液循环再生设备组(7)、再生子液罐(8)、配液罐(9)、过滤器(10)、子液罐(11),所述相邻的两个部件之间还连接有高压泵。该发明设计的这种酸性蚀刻液循环再生系统,效率高,成本低,占地面积少,但是会产生氯气。
4.鉴于此种现状,本发明开发了一种蚀刻废液中铜资源化利用的新方法。经过小试及中试实验的验证,最终得到的硫酸铜产品纯度≥95%,可作为工业盐出售;同时,所有的水资源可以回用于生产中;不仅回收了硫酸铜,同时没有新的废水排放。在创造经济效益的同时,减轻了废水对环境的污染。
5.本发明实现了硫酸铜的回收,水资源的循环利用,没有废水的外排,是一种绿色环保技术。
技术实现要素:
6.本发明提供一种蚀刻废液中铜的资源化利用方法,旨在解决上述背景技术中提到的问题。
7.本发明是这样实现的,一种蚀刻废液中铜的资源化利用方法,包括:
8.s1,蚀刻废液进入陶瓷膜系统进水罐,经供料泵和循环泵将所述蚀刻废液泵入所述陶瓷膜系统,经过陶瓷膜过滤,去除废液中的大颗粒及悬浮物等杂质,得到的所述陶瓷膜系统产水进入所述陶瓷膜系统产水罐,
9.s2,将s1中,存储至所述陶瓷膜系统产水罐中的产水经纳滤系统供料泵和高压泵泵入纳滤系统,经过纳滤膜过滤,对s1中,所述陶瓷膜系统的产水进行浓缩,使所述纳滤系统浓水中硫酸铜的浓度提高到20-30g/l之间,接着,将纳滤浓水输送进入所述纳滤系统浓水罐,
10.s3,将s2中,所述纳滤系统产生的浓水经供料泵泵入电渗析系统,利用直流电源提供电场,通过电渗析膜使所述电渗析系统的浓水中硫酸铜的浓度达到150-200g/l之间,并将浓水输送进入蒸发系统进水罐,所述电渗析系统的淡水则返回至s1中的所述陶瓷膜系统产水罐,再经所述纳滤系统继续浓缩后进入所述电渗析系统进水罐,
11.s4,将s3中,所述电渗析系统的浓水经供料泵和循环泵泵入蒸发系统,通入蒸汽,对废水进行浓缩,再通过盐结晶系统和干燥系统,最终得到硫酸铜产品。
12.优选的,还包括s5,其具有:将经s2的所述纳滤系统的产水排入回用水罐,再通过回用水泵,泵至生产用水使用点,用以实现对水资源的循环利用。
13.优选的,在s1中,排入所述陶瓷膜系统进水罐中的所述蚀刻废液中含有悬浮物,且所述蚀刻废液中硫酸铜的含量在0.3-0.5g/l,并且,所述蚀刻废液的浊度在10-30ntu之间。
14.优选的,在s1中,所述陶瓷膜系统包含有:进水罐、产水罐、供料泵、循环泵和陶瓷膜等组件,其中,所述陶瓷膜为膜孔径5nm~5μm、操作压力 0-1.0mpa、操作温度15-60℃的无机膜。
15.优选的,在s2中,所述纳滤系统包含有:进水罐、产水罐、供料泵、高压泵和纳滤膜等组件,其中,所述纳滤膜的截留分子量为150-300da、操作压力为0.5-4.0mpa、操作温度为15-40℃,通过所述纳滤系统,用以分别得到纳滤系统浓水和产水,并且,所述纳滤系统中浓水内硫酸铜的浓度在20-30g/l之间,且所述纳滤系统中产水内硫酸铜的浓度小于20mg/l。
16.优选的,在s3中,所述电渗析系统包含有:脱盐液罐、浓缩液罐、极液罐、供料泵、循环泵、直流电源和电渗析膜等组件,其中,所述电渗析膜为截留分子量150-300da、操作压力为0.05-0.1mpa、操作温度为15-40℃的离子交换膜,并且,通过所述电渗析系统,分别得到经所述电渗析系统产生的浓水和淡水,所述电渗析系统浓水进入s4中的所述蒸发系统进水罐,所述电渗析系统淡水返回至s1中的所述陶瓷膜系统产水罐,所述电渗析系统中浓水内硫酸铜的浓度在 150-200g/l之间,且所述电渗析系统中淡水内硫酸铜的浓度在5g/l。
17.优选的,在s4中,所述蒸发系统包含有:进水罐、供料泵、循环泵、蒸汽系统、结晶系统和干燥系统等组件,其中,所述蒸发系统为单效、多效、mvr 系统或其它类型蒸发系统中的一种,通过所述蒸发系统最终得到硫酸铜产品,纯度≥95%。
18.与现有技术相比,本发明的有益效果是:本发明的一种蚀刻废液中铜的资源化利用方法:
19.经过本系统处理后,可以实现蚀刻废液中98%以上的硫酸铜回收,同时可以实现水资源的循环利用,没有新的废水产生,在创造一定经济效益的同时,大大减轻了环境污染。相比于其它技术,本发明具有以下优点:
20.s1中,采用陶瓷膜技术对蚀刻废液进行预处理,由于蚀刻液酸性强、成分复杂,相比于其它技术,陶瓷膜具有耐酸、耐碱、耐有机溶剂和耐高温等优良性能,可以保证系统的稳定运行,同时,陶瓷膜孔径为纳米级,过滤精度高,可以去除废液中的悬浮物杂质,陶瓷膜系统产水浊度<1ntu,满足后段纳滤系统进水要求,可以保证纳滤系统的稳定运行;
21.s2中,采用纳滤技术对硫酸铜进行浓缩,由于纳滤膜带负电,对二价阴离子截留率高(>98%),因此采用纳滤技术,可以实现蚀刻液中98%以上的硫酸铜回收,另外,相比于其它浓缩技术(如反渗透),纳滤膜结构疏松,过滤压力更低,因此能耗更低,且纳滤产水中硫酸铜的浓度小于20mg/l,水质较优,可以直接回用于生产;
22.s3中,采用电渗析技术对硫酸铜进一步浓缩,可以将浓水中的盐含量控制在150-200g/l之间。相比于其它盐浓缩技术,(如高压反渗透或dtro等),最高只能将盐浓度浓缩至100g/l。这样可以减少蒸发系统投资规模30%-50%,同时减少了蒸汽用量,节约蒸汽运行成本30%-40%。
23.与现有技术相比,本发明实现了所有资源的循环利用,没有废水、废气、废渣的外排,是一种绿色环保技术。
附图说明
24.图1为本发明的方法步骤流程图;
具体实施方式
25.为了使本发明的目的、技术方案及优点更加清楚明白,以下结合附图及实施例,对本发明进行进一步详细说明,应当理解,此处所描述的具体实施例仅仅用以解释本发明,并不用于限定本发明。
26.请参阅图1,本发明提供一种技术方案,
27.一种蚀刻废液中铜的资源化利用方法,包括以下方法步骤:
28.s1,蚀刻废液进入陶瓷膜系统进水罐,经供料泵和循环泵将所述蚀刻废液泵入所述陶瓷膜系统,经过陶瓷膜过滤,去除废液中的大颗粒及悬浮物等杂质,得到的所述陶瓷膜系统产水进入所述陶瓷膜系统产水罐;
29.s2,将s1中,存储至所述陶瓷膜系统产水罐中的产水经纳滤系统供料泵和高压泵泵入纳滤系统,经过纳滤膜过滤,对s1中,所述陶瓷膜系统的产水进行浓缩,使所述纳滤系统浓水中硫酸铜的浓度提高到20-30g/l之间,接着,将纳滤浓水输送进入所述纳滤系统浓水罐;
30.s3,将s2中,所述纳滤系统产生的浓水经供料泵泵入电渗析系统,利用直流电源提供电场,通过电渗析膜使所述电渗析系统的浓水中硫酸铜的浓度达到150-200g/l之间,并将浓水输送进入蒸发系统进水罐,所述电渗析系统的淡水则返回至s1中的所述陶瓷膜系统产水罐,再经所述纳滤系统继续浓缩后进入所述电渗析系统进水罐;
31.s4,将s3中,所述电渗析系统的浓水经供料泵和循环泵泵入蒸发系统,通入蒸汽,对废水进行浓缩,再通过盐结晶系统和干燥系统,最终得到硫酸铜产品。
32.还包括s5,其具有:将经s2的所述纳滤系统的产水排入回用水罐,再通过回用水泵,泵至生产用水使用点,用以实现对水资源的循环利用。
33.在s1中,排入所述陶瓷膜系统进水罐中的所述蚀刻废液中含有悬浮物,且所述蚀刻废液中硫酸铜的含量在0.3-0.5g/l,并且,所述蚀刻废液的浊度在 10-30ntu之间,所述陶瓷膜系统包含有:进水罐、产水罐、供料泵、循环泵和陶瓷膜等组件,其中,所述陶瓷膜为膜孔径5nm~5μm、操作压力0-1.0mpa、操作温度15-60℃的无机膜。
34.在s2中,所述纳滤系统包含有:进水罐、产水罐、供料泵、高压泵和纳滤膜等组件,其中,所述纳滤膜的截留分子量为150-300da、操作压力为 0.5-4.0mpa、操作温度为15-40℃,通过所述纳滤系统,用以分别得到纳滤系统浓水和产水,并且,所述纳滤系统中浓水内硫酸铜的浓度在20-30g/l之间,且所述纳滤系统中产水内硫酸铜的浓度小于20mg/l。
35.在s3中,所述电渗析系统包含有:脱盐液罐、浓缩液罐、极液罐、供料泵、循环泵、直流电源和电渗析膜等组件,其中,所述电渗析膜为截留分子量 150-300da、操作压力为0.05-0.1mpa、操作温度为15-40℃的离子交换膜,并且,通过所述电渗析系统,分别得到经所述电渗析系统产生的浓水和淡水,所述电渗析系统浓水进入s4中的所述蒸发系统进水罐,所述电渗析系统淡水返回至s1中的所述陶瓷膜系统产水罐,所述电渗析系统中浓水内硫酸铜的浓度在 150-200g/l之间,且所述电渗析系统中淡水内硫酸铜的浓度在5g/l。
36.在s4中,所述蒸发系统包含有:进水罐、供料泵、循环泵、蒸汽系统、结晶系统和干
燥系统等组件,其中,所述蒸发系统为单效、多效、mvr系统或其它类型蒸发系统中的一种,通过所述蒸发系统最终得到硫酸铜产品,纯度≥ 95%。
37.针对上述材料提出如下多种实施例:
38.实施例一:具体步骤如下:
39.1)将蚀刻废液先经过陶瓷膜系统处理,去除废液中的大颗粒及悬浮物等杂质,满足后续纳滤系统的进水要求,陶瓷膜孔径为50nm,操作压力为 0.1-0.3mpa,操作温度为20-40℃;具体数据如下表所示。
40.项目硫酸铜(g/l)浊度(ntu)蚀刻废液0.320陶瓷膜产水0.30.5
41.从表中可以看出,陶瓷膜系统对大颗粒及悬浮物等杂质去除效果较好,最终的系统产水浊度<1ntu,满足后续纳滤系统的进水要求,可以保证系统的稳定运行,同时,陶瓷膜对硫酸铜没有任何截留,不会对产品造成损失。
42.2)将步骤1)中陶瓷膜系统产水采用纳滤系统进行处理,对废液中的硫酸铜进行浓缩,使其浓度达到下一步工艺的要求,同时,保证纳滤系统产水水质满足回用水的要求。纳滤膜截留分子量150-300da,纳滤膜操作压力7-4.0mpa,操作温度20-35℃;具体数据如下表所示。
43.项目原液产水浓水硫酸铜0.30g/l10mg/l23g/l
44.从表中可以看出,纳滤系统浓水中硫酸铜浓度达到23g/l,满足后续电渗析系统的进水要求,同时,纳滤系统产水中硫酸铜含量只有10mg/l,满足回用水使用标准。
45.3)将步骤2)中纳滤系统浓水采用电渗析系统进行处理,对废液中硫酸铜进行浓缩,使其浓度达到下一步工艺的要求,电渗析膜截留分子量150-300da,操作压力0.05-0.1mpa,操作温度20-35℃;具体数据如下表所示。
46.项目原液产水浓水硫酸铜23g/l5g/l160g/l
47.从表中可以看出,电渗析系统浓水达到160g/l,达到预期,盐浓度提高60%;大大减少了后续蒸发系统的投资及运行成本;
48.4)将步骤3)中的电渗析系统浓水再经过蒸发系统处理,最终得到硫酸铜产品,经分析产品纯度为96.5%。
49.实施例二:具体步骤如下:
50.1)将蚀刻废液先经过陶瓷膜系统处理,去除废液中的大颗粒及悬浮物等杂质,满足后续纳滤系统的进水要求,陶瓷膜孔径为100nm,操作压力为 0.1-0.3mpa,操作温度为20-40℃;具体数据如下表所示。
51.项目硫酸铜(g/l)浊度(ntu)蚀刻废液0.525陶瓷膜产水0.50.5
52.从表中可以看出,陶瓷膜系统对大颗粒及悬浮物等杂质去除效果较好,最终的系
统产水浊度<1ntu,满足后续纳滤系统的进水要求,可以保证系统的稳定运行;同时,陶瓷膜对硫酸铜没有任何截留,不会对产品造成损失。
53.2)将步骤1)中陶瓷膜系统产水采用纳滤系统进行处理,对废液中的硫酸铜进行浓缩,使其浓度达到下一步工艺的要求,同时,保证纳滤系统产水水质满足回用水的要求,纳滤膜截留分子量150-300da,纳滤膜操作压力7-4.0mpa,操作温度20-35℃,具体数据如下表所示。
54.项目原液产水浓水硫酸铜0.50g/l15mg/l25g/l
[0055] 从表中可以看出,纳滤系统浓水中硫酸铜浓度达到25g/l,满足后续电渗析系统的进水要求;同时,纳滤系统产水中硫酸铜含量只有15mg/l,满足回用水使用标准。
[0056]
3)将步骤2)中纳滤系统浓水采用电渗析系统进行处理,对废液中硫酸铜进行浓缩,使其浓度达到下一步工艺的要求,电渗析膜截留分子量150-300da,操作压力0.05-0.1mpa,操作温度20-35℃,具体数据如下表所示。
[0057]
项目原液产水浓水硫酸铜25g/l5g/l180g/l
[0058]
从表中可以看出,电渗析系统浓水达到180g/l,达到预期;盐浓度提高80%;大大减少了后续蒸发系统的投资及运行成本;
[0059]
4)将步骤3)中的电渗析系统浓水再经过蒸发系统处理,最终得到硫酸铜产品,经分析产品纯度为97.3%。
[0060]
实施例三:具体步骤如下:
[0061]
1)将蚀刻废液先经过陶瓷膜系统处理,去除废液中的大颗粒及悬浮物等杂质,满足后续纳滤系统的进水要求,陶瓷膜孔径为20nm,操作压力为 0.1-0.3mpa,操作温度为20-40℃,具体数据如下表所示。
[0062]
项目硫酸铜(g/l)浊度(ntu)蚀刻废液0.4515陶瓷膜产水0.450.5
[0063]
从表中可以看出,陶瓷膜系统对大颗粒及悬浮物等杂质去除效果较好,最终的系统产水浊度<1ntu,满足后续纳滤系统的进水要求,可以保证系统的稳定运行,同时,陶瓷膜对硫酸铜没有任何截留,不会对产品造成损失。
[0064]
2)将步骤1)中陶瓷膜系统产水采用纳滤系统进行处理,对废液中的硫酸铜进行浓缩,使其浓度达到下一步工艺的要求,同时,保证纳滤系统产水水质满足回用水的要求。纳滤膜截留分子量150-300da,纳滤膜操作压力7-4.0mpa,操作温度20-35℃,具体数据如下表所示。
[0065]
项目原液产水浓水硫酸铜0.45g/l13mg/l25g/l
[0066]
从表中可以看出,纳滤系统浓水中硫酸铜浓度达到25g/l,满足后续电渗析系统的进水要求,同时,纳滤系统产水中硫酸铜含量只有13mg/l,满足回用水使用标准。
[0067]
3)将步骤2)中纳滤系统浓水采用电渗析系统进行处理,对废液中硫酸铜进行浓
缩,使其浓度达到下一步工艺的要求,电渗析膜截留分子量150-300da,操作压力0.05-0.1mpa,操作温度20-35℃,具体数据如下表所示。
[0068]
项目原液产水浓水硫酸铜25g/l5g/l170g/l
[0069]
从表中可以看出,电渗析系统浓水达到170g/l,达到预期,盐浓度提高70%,大大减少了后续蒸发系统的投资及运行成本,
[0070]
4)将步骤3)中的电渗析系统浓水再经过蒸发系统处理,最终得到硫酸铜产品,经分析产品纯度为95.5%。
[0071]
以上所述仅为本发明的较佳实施例而已,并不用以限制本发明,凡在本发明的精神和原则之内所作的任何修改、等同替换和改进等,均应包含在本发明的保护范围之内。
再多了解一些
本文用于企业家、创业者技术爱好者查询,结果仅供参考。