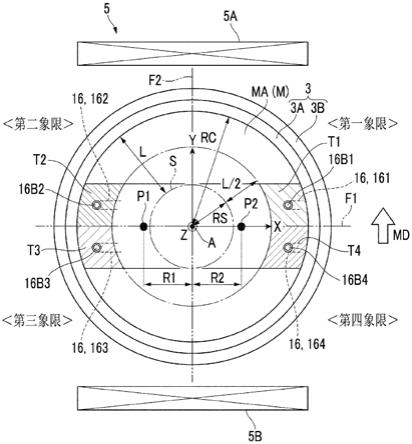
1.本发明涉及一种单晶硅的培育方法及单晶硅的提拉装置。
背景技术:
2.在单晶硅的制造中使用被称为提拉法(以下,称为cz法)的方法。在使用cz法的制造方法中,单晶硅的电阻率利用添加到硅熔液中的掺杂剂来调节。作为将掺杂剂添加到硅熔液中的方法,已知有通过在单晶硅的提拉过程中投下粒状掺杂剂来将晶体中的掺杂剂浓度保持为恒定的技术。现有技术文献专利文献
3.专利文献1:日本特开平3-247585号公报
技术实现要素:
发明所要解决的技术问题
4.然而,在现有的技术中,例如存在如下问题:经由导管向硅熔液中投下的粒状掺杂剂不熔融而附着于单晶硅,从而有时发生位错化。
5.本发明的目的在于提供一种能够防止在通过提拉法培育单晶硅时所投下的粒状掺杂剂在熔融前附着于单晶而发生位错化的单晶硅的培育方法及单晶硅的提拉装置。用于解决技术问题的方案
6.本发明的单晶硅的培育方法为基于提拉法的单晶硅的培育方法,其特征在于,具有:提拉工序,一边使所述单晶硅旋转一边进行提拉;及掺杂剂投下工序,在所述单晶硅的直体部的提拉过程中向硅熔液的液面上投下粒状掺杂剂,将所述粒状掺杂剂的投下位置设定于在所述硅熔液的液面上远离所述直体部的流动占主导的区域上。
7.在上述单晶硅的培育方法中,优选如下:具有:磁场施加工序,对所述硅熔液施加水平磁场,在所述掺杂剂投下工序中,在将所述硅熔液的液面的中心设为原点、将铅垂方向的上方设为z轴的正方向且将水平磁场施加方向设为y轴的正方向的右手系的xyz直角坐标系中,在包含所述原点且与所述水平磁场施加方向正交的磁场正交截面上存在具有从所述y轴的正方向观察时顺时针方向或逆时针方向的旋转方向的对流的状态下,根据从铅垂方向上方观察的所述单晶硅的旋转方向及所述对流的旋转方向来设定所述粒状掺杂剂的投下位置。
8.在上述单晶硅的培育方法中,优选如下:在所述掺杂剂投下工序中,当所述对流的旋转方向为顺时针方向且所述单晶硅的旋转方向为顺时针方向时,将所述投下位置设为由x轴和所述y轴构成的坐标平面的第四象限,当所述对流的旋转方向为逆时针方向且所述单晶硅的旋转方向为逆时针方向时,将所述投下位置设为所述坐标平面的第一象限,当所述对流的旋转方向为逆时针方向且所述单晶硅的旋转方向为顺时针方向时,将所述投下位置设为所述坐标平面的第二象限,当所述对流的旋转方向为顺时针方向且所述单晶硅的旋转
方向为逆时针方向时,将所述投下位置设为所述坐标平面的第三象限。
9.一种单晶硅的培育方法,其使用所述投下位置为由x轴和所述y轴构成的坐标平面的第一象限、第二象限、第三象限及第四象限中的一个的所述单晶硅的提拉装置,在上述单晶硅的培育方法中,优选如下:在所述磁场施加工序中,反复施加所述水平磁场,直至所述投下位置位于在所述硅熔液的液面上远离所述直体部的流动占主导的区域上。
10.在上述单晶硅的培育方法中,优选如下:若将所述直体部的直径设为rs且将所述投下位置的y轴坐标的绝对值设为ya,则所述投下位置设定为满足ya<rs。
11.本发明的单晶硅的提拉装置为基于提拉法的单晶硅的提拉装置,其特征在于,具备:石英坩埚;加热装置,对所述石英坩埚内的硅熔液进行加热;提拉轴,可旋转地提拉所述单晶硅;磁场施加装置,对所述硅熔液施加水平磁场;及掺杂剂投下装置,在将所述硅熔液的液面的中心设为原点、将铅垂方向的上方设为z轴的正方向且将水平磁场施加方向设为y轴的正方向的右手系的xyz直角坐标系中,分别向由x轴和所述y轴构成的坐标平面的第一象限、第二象限、第三象限及第四象限投下粒状掺杂剂。
12.根据本发明,能够防止所投下的粒状掺杂剂在熔融之前附着于单晶硅而发生位错化。
附图说明
13.图1是本发明的实施方式所涉及的提拉装置的概略剖视图。图2是沿图1的ii-ii线的截面上的主要部分的剖视图。图3是表示本发明的实施方式所涉及的温度测定装置的配置状态的示意图。图4是说明对流的旋转方向、单晶硅的旋转方向的示意图。图5a是表示本发明的实施方式中的水平磁场的施加方向与硅熔液的对流的方向的关系的示意图。图5b是表示本发明的实施方式中的水平磁场的施加方向与硅熔液的对流的方向的关系的示意图。图6是表示本发明的实施方式中的硅熔液的对流的变化的示意图。图7是表示对流的旋转方向为逆时针方向且单晶硅的旋转方向为顺时针方向时的投下位置的图。图8是说明对流的旋转方向为逆时针方向时的硅熔液的液面上的流动的图。
具体实施方式
14.以下,参考附图对本发明的优选实施方式进行详细说明。〔提拉装置〕图1是本发明的实施方式所涉及的提拉装置1的概略剖视图。图2是沿图1的ii-ii线的截面上的主要部分的剖视图。在图2中,为了简化,仅主要示出坩埚3和磁场施加装置5。并且,在图中,为了容易理解结构而示出相互正交的x轴、y轴及z轴(在其他图中也相同。)。x轴及y轴对应于水平方向,z轴对应于铅垂方向。另外,图1是从自y轴的负方向朝向正方向的方向观察的提拉装置1的概略剖视图,以下将“自y轴的负方向朝向正方向的方向”简称为“y轴的正方向”,将其相反的方向称为“y
轴的负方向”。在其他轴(x轴、z轴)上也相同。
15.提拉装置1为通过提拉法提拉单晶硅s并进行培育的装置。如图1及图2所示,提拉装置1具备构成外廓的腔室2、配置于腔室2的中心部的坩埚3、加热器4、磁场施加装置5、掺杂剂投下装置15及控制装置18。
16.坩埚3为从铅垂方向上方(z轴的负方向)观察时呈圆形的积存硅熔液m的容器。坩埚3为由内侧的石英坩埚3a和外侧的石墨坩埚3b构成的双重结构。坩埚3能够旋转及升降并固定于沿着z轴延伸的支承轴6的上端部。
17.加热器4为对坩埚3内的硅熔液m进行加热的加热装置。加热器4呈圆筒形状,在坩埚3的外侧与坩埚3的中心轴a同轴状地配置。加热器4为电阻加热式的所谓的碳加热器。在加热器4的外侧沿着腔室2的内表面设置有绝热材料7。
18.磁场施加装置5为对坩埚3内的硅熔液m施加水平磁场的装置。本实施方式的磁场施加装置5以水平磁场施加方向(以下,称为磁场方向md。)成为y轴的正方向的方式构成。水平磁场的磁场强度例如为0.18特斯拉~0.32特斯拉。磁场施加装置5具备分别由电磁线圈构成的第1磁性体5a及第2磁性体5b。第1磁性体5a及第2磁性体5b在腔室2的外侧以隔着坩埚3对置的方式设置。
19.在坩埚3的上方与支承轴6同轴状地配置有提拉轴8。提拉轴8由线材(wire)等形成。提拉轴8围绕轴向顺时针方向(cw)或逆时针方向(ccw)以规定的速度旋转。在提拉轴8的下端安装有籽晶sc。提拉轴8使籽晶sc(单晶硅s)向从铅垂方向上方(z轴的负方向)观察时顺时针方向或逆时针方向旋转。
20.在腔室2内配置有热屏蔽体9。热屏蔽体9呈筒状,在坩埚3内的硅熔液m的上方包围培育中的单晶硅s。热屏蔽体9针对培育中的单晶硅s屏蔽来自坩埚3内的硅熔液m或加热器4或坩埚3的侧壁的高温的辐射热。热屏蔽体9针对作为晶体生长界面的固液界面si附近承担如下作用:抑制热向外部扩散,并控制单晶中心部及单晶外周部的提拉轴方向的温度梯度。
21.在腔室2的上部设置有气体导入口10。气体导入口10将氩气等惰性气体g导入到腔室2内。在腔室2的下部设置有排气口11。排气口11通过未图示的真空泵的驱动而抽吸并排出腔室2内的气体。从气体导入口10导入到腔室2内的惰性气体g在培育中的单晶硅s与热屏蔽体9之间下降。接着,惰性气体g经过热屏蔽体9的下端与硅熔液m的液面之间的间隙之后,朝向热屏蔽体9的外侧,进一步朝向坩埚3的外侧流动。然后,惰性气体g在坩埚3的外侧下降,并从排气口11排出。
22.掺杂剂投下装置15为向坩埚3内的硅熔液m中投下粒状掺杂剂的装置。粒状掺杂剂为掺杂于单晶硅s中的掺杂剂,是将个体掺杂剂形成为粒状而成的添加物。作为掺杂剂的种类,若要制造的硅半导体为n型半导体,则可以举出磷(p)、锑(sb)、砷(as),若为p型半导体,则可以举出硼(b)。
23.掺杂剂投下装置15具有掺杂剂容纳部15a和多个导管16。本实施方式的掺杂剂投下装置15具有4根导管16(在图1中仅示出2根导管16。)。掺杂剂容纳部15a为在其内部容纳粒状掺杂剂的容器。掺杂剂容纳部15a例如能够经由未图示的支架配置于腔室2的上方。
24.导管16为将掺杂剂容纳部15a内的粒状掺杂剂导向硅熔液m的管状的部件。各个导
管16的其上端经由投下位置选择装置17连接于掺杂剂容纳部15a,其下端16b在硅熔液m的上方开口。容纳于掺杂剂容纳部15a中的粒状掺杂剂通过导管16向硅熔液m中投下。粒状掺杂剂的投下位置为导管16的下端16b的位置。
25.投下位置选择装置17具有将从掺杂剂容纳部15a供给的粒状掺杂剂导入到至少一个导管16的功能。投下位置选择装置17能够利用控制装置18来控制,例如能够由多个电磁阀构成。
26.接着,对各个导管16的下端16b的位置(粒状掺杂剂的投下位置)进行说明。如图2所示,在4根导管16中,第1导管161形成为,在将硅熔液m的液面ma的中心设为原点、将铅垂方向的上方设为z轴的正方向且将磁场方向md设为y轴的正方向的右手系的xyz直角坐标系的由x轴和y轴构成的坐标平面上,向硅熔液m的液面ma的第一象限投下粒状掺杂剂。第一象限为在由x轴和y轴构成的坐标平面上x和y均取正值的区域,第二象限为在由x轴和y轴构成的坐标平面上x取负值、y取正值的区域,第三象限为在由x轴和y轴构成的坐标平面上x和y均取负值的区域,第四象限为在由x轴和y轴构成的坐标平面上x取正值、y取负值的区域。
27.更具体而言,第1导管161的下端1681从上方(z轴的负方向)观察时配置于硅熔液m的液面ma的第一象限的区域内的、y轴坐标的绝对值不超出提拉十的单晶硅s的直体部的半径rs的区域。换言之,基于第1导管161的粒状掺杂剂的投下位置设定为,若将单晶硅s的直体部的半径设为rs且将投下位置的y轴坐标的绝对值设为ya,则满足ya《rs。
28.此外,若将石英坩埚3a的内周面与单晶硅s的外周面的距离设为l,则第1导管161的下端1681从上方观察时配置于在由x轴和y轴构成的坐标平面上比以原点为中心的半径rs l/2的圆更靠外侧的位置。
29.即,基于第1导管161的粒状掺杂剂的投下位置设定于由x轴和y轴构成的坐标平面的第一象限内的、y轴坐标的绝对值不超过提拉中的单晶硅s的直体部的半径rs的区域且在由x轴和y轴构成的坐标平面上比以原点为中心的半径rs l/2的圆更靠外侧的区域t1。
30.同样地,基于第2导管162的粒状掺杂剂的投下位置(第2导管162的下端1682)设定于由x轴和y轴构成的坐标平面的第二象限内的、y轴坐标的绝对值ya不超过提拉中的单晶硅s的直体部的半径rs的区域且在由x轴和y轴构成的坐标平面上比以原点为中心的半径rs l/2的圆更靠外侧的区域t2。基于第3导管163的粒状掺杂剂的投下位置(第3导管163的下端1683)设定于由x轴和y轴构成的坐标平面的第三象限内的、y轴坐标的绝对值ya不超过提拉中的单晶硅s的直体部的半径rs的区域且在由x轴和y轴构成的坐标平面上比以原点为中心的半径rs l/2的圆更靠外侧的区域t3。基于第4导管164的粒状掺杂剂的投下位置(第4导管164的下端1684)设定于由x轴和y轴构成的坐标平面的第四象限内的、y轴坐标的绝对值ya不超过提拉中的单晶硅s的直体部的半径rs的区域且在由x轴和y轴构成的坐标平面上比以原点为中心的半径rs l/2的圆更靠外侧的区域t4。
31.控制装置18与投下位置选择装置17电连接,将投下位置选择装置17控制成将从掺
杂剂容纳部15a供给的粒状掺杂剂导向4根导管16中的至少1根导管16。
32.提拉装置1具备测定硅熔液m的液面ma的温度的温度测定装置12。如图1、图3所示,温度测定装置12为了测定硅熔液m的液面ma上的两处的测定点p1、p2(p)而具有两个反射部13及两个辐射温度计14。温度测定装置12与控制装置18电连接。
33.反射部13设置于腔室2内部。如图3所示,反射部13优选设置成从其下端至硅熔液m的液面ma为止的距离(高度)k成为600mm以上且5000mm以下。并且,反射部13优选设置成反射面13a与水平面f所成的角度θf成为40
°
以上且50
°
以下。通过这种结构,从第1测定点p1、第2测定点p2向与重力方向相反的方向分别出射的辐射光rl的入射角θ1及反射角θ2之和成为80
°
以上且100
°
以下。
34.作为反射部13,从耐热性的观点考虑,优选使用对一面进行镜面抛光而制成反射面13a的硅反射镜(silicon mirror)。辐射温度计14设置于腔室2外部。辐射温度计14接收经由设置于腔室2的石英窗2a入射的辐射光rl并以非接触方式进行测定点p的温度的测定。
35.另外,虽未详细叙述,但控制装置18连接于加热器4、磁场施加装置5、支承轴6等并分别控制它们。
36.如图2所示,第1测定点p1及第2测定点p2设定于包含坩埚3的中心轴a且与磁场方向md正交的虚拟面f1上。第1测定点p1和第2测定点p2设定于相对于中心轴a对称的位置。在温度测定装置12中,当将从中心轴a至第1测定点p1为止的距离设为r1、从中心轴a至第2测定点p2为止的距离设为r2且将石英坩埚3a的内径的半径设为rc时,第1测定点p1优选设定于满足下式(1)的位置,且第2测定点p2优选设定于满足下式(2)的位置。0.375≤r1/rc<1
…
(1)0.375≤r2/rc<1
…
(2)r1/rc的值和r2/rc的值可以相同,也可以不同。
37.〔对流的旋转方向〕本发明人等发现,若如图4、图5a、图5b所示向石英坩埚3a中投入固体的多晶硅原料并使其熔解之后施加水平磁场,则在硅熔液m中产生对流cf。以下,对对流cf的机制进行说明。图4是说明单晶硅s的旋转方向及对流cf的旋转方向的示意图。
38.对流cf为在硅熔液m的液面ma与坩埚3的底面的中间,硅熔液m以沿磁场方向md延伸的虚拟轴线v为中心而围绕虚拟轴线v流动的辊状的流动。硅熔液m通过产生对流cf而成为稳定状态。对流cf的旋转方向具有以下两个模式:如图4及图5a所示,在xyz直角坐标系中,在包含原点且与磁场方向md正交的磁场正交截面上,从y轴的正方向观察时顺时针方向(cw)占优势的情况;如图4及图5b所示,逆时针方向(ccw)占优势的情况。
39.发明人等推测这种现象的发生基于以下机制。首先,在不施加水平磁场而不使石英坩埚3a旋转的状态下,在石英坩埚3a的外周附近,硅熔液m被加热,因此产生从硅熔液m的底部朝向液面ma的上升方向的流动。上升的硅熔液m在硅熔液m的液面ma上被冷却,在石英坩埚3a的中心返回到石英坩埚3a的底部,产生下降方向的流动。
40.在产生在外周部分上升且在中央部分下降的流动的状态下,因由热对流引起的不
稳定性而下降流的位置随机移动,并从中心偏离。这种下降流由如下温度分布而产生:硅熔液m的液面ma上的与下降流对应的部分的温度最低,随着朝向液面ma的外侧而温度逐渐升高。例如,在图6(a)的状态下,中心从石英坩埚3a的旋转中心偏离的第1区域a1的温度最低,且以位于其外侧的第2区域a2、第3区域a3、第4区域a4、第5区域a5的顺序温度升高。
41.而且,在图6(a)的状态下,若向磁场方向md施加水平磁场,则从石英坩埚3a的上方观察时的下降流df的旋转逐渐受到约束,如图6(b)所示,被约束在向与磁场方向md正交的水平方向偏移的位置。另外,认为下降流df的旋转受到约束是由于作用于硅熔液m的水平磁场的强度变得大于特定强度。因此,下降流df的旋转在水平磁场的施加刚开始之后不受约束,施加开始之后经过规定时间后受到约束。
42.己报道由磁场施加引起的硅熔液m内部的流动变化通常以由以下式(3)得到的无量纲数即magnetic number(磁数)m表示(jpn.j.appl.phys.,vol.33(1994)part.2 no.4a,pp.l487-490)。
43.[数式1]
[0044]
式(3)中,σ为硅熔液m的电导率,b0为所施加的磁通密度,h为硅熔液m的深度,p为硅熔液m的密度,v0为无磁场时的硅熔液m的平均流速。在本实施方式中,可知下降流df的旋转受到约束的水平磁场的特定强度的最小值为0.01特斯拉。0.01特斯拉下的magnetic number为1.904。认为即使在与本实施方式不同的硅熔液m的量或石英坩埚3a的直径时,根据magnetic number为1.904的磁场强度(磁通密度),也会产生基于磁场的下降流df的约束效果(制动效果)。
[0045]
若从图6(b)所示的状态进一步增大水平磁场的强度,则如图6(c)所示,下降流df的右侧和左侧的上升方向的流动的大小变化,若为图6(c),则下降流df的左侧的上升方向的流动占优势。最后,若磁场强度成为0.2特斯拉,则如图6(d)所示,下降流df的右侧的上升方向的流动消失,左侧成为上升方向的流动,右侧成为下降方向的流动,从而成为顺时针方向(cw)的对流cf。在顺时针方向的对流cf的状态下,如图5a所示,在磁场正交截面上,随着从硅熔液m十的右侧区域rr朝向左侧区域lr而温度逐渐升高。另一方面,若使图6(a)的最开始的下降流df的位置向石英坩埚3a的旋转方向偏离180
°
,则下降流df约束在与图6(c)相比相位偏离180
°
的左侧的位置,从而成为逆时针方向(ccw)的对流cf。在逆时针方向的对流cf的状态下,如图5b所示,随着从硅熔液m中的右侧区域rr朝向左侧区域lr而温度逐渐降低。只要不将水平磁场的强度设为小于0.2特斯拉,则这种顺时针方向或逆时针方向的硅熔液m的对流cf就会得到维持。
[0046]
〔单晶硅的培育方法〕接着,对使用本实施方式的单晶硅的提拉装置1的单晶硅的培育方法进行说明。本实施方式的单晶硅的培育方法是考虑粒状掺杂剂的投下位置而进行的。
单晶硅的培育方法依次具有加热工序、提拉工序、磁场施加工序、温度测定工序、对流旋转方向估计工序及掺杂剂投下工序。另外,关于工序的顺序,也可以适当变更。
[0047]
加热工序为在将腔室2内维持为减压下的惰性气体气氛的状态下使坩埚3旋转,并且在无磁场状态下熔融坩埚3内的硅原料,并对硅熔液m进行加热的工序。提拉工序为一边使单晶硅s旋转一边进行提拉的工序。磁场施加工序为一边保持硅熔液m的温度一边控制磁场施加装置5来对旋转中的石英坩埚3a内的硅熔液m施加水平磁场的工序。通过施加水平磁场,在硅熔液m中产生如图5a所示的在磁场正交截面上为顺时针方向(cw)的对流cf或如图5b所示的逆时针方向(ccw)的对流cf。
[0048]
温度测定工序为如图3、图5a、图5b所示,对流cf的旋转方向被固定之后,利用温度测定装置12测定硅熔液m的液面ma的温度的工序。另外,例如能够根据水平磁场的施加开始之后的经过时间来判断对流cf的旋转方向己被固定。
[0049]
对流旋转方向估计工序为根据由温度测定装置12测定的温度来估计对流cf的旋转方向的工序。当第1测定点p1的温度高于第2测定点p2的温度时,控制装置18估计为产生了在磁场正交截面上为顺时针方向(cw)的对流cf,当第1测定点p1的温度低于第2测定点p2的温度时,估计为产生了在磁场正交截面上为逆时针方向(ccw)的对流cf。
[0050]
掺杂剂投下工序为在单晶硅s的直体部的提拉过程中向硅熔液m中投下粒状掺杂剂的工序。在掺杂剂投下工序中,将粒状掺杂剂的投下位置设定于在硅熔液m的液面ma上远离单晶硅s的直体部的流动占主导的区域上。具体而言,在掺杂剂投下工序中,根据单晶硅s的旋转方向及对流cf的旋转方向,以如下表1所示的规则设定粒状掺杂剂的投下位置。
[0051]
[表1]
[0052]
即,当对流cf的旋转方向为顺时针方向且单晶硅s的旋转方向为顺时针方向时,控制装置18将投下位置选择装置17控制为向第4导管164导入粒状掺杂剂。由此,粒状掺杂剂的投下位置设定于由x轴和y轴构成的坐标平面的第四象限内的、y轴坐标的绝对值不超过提拉中的单晶硅s的直体部的半径rs的区域且在由x轴和y轴构成的坐标平面上比以原点为中心的半径rs l/2的圆更靠外侧的区域t4。
[0053]
当对流cf的旋转方向为逆时针方向且单晶硅s的旋转方向为逆时针方向时,控制装置18将投下位置选择装置17控制为向第1导管161导入粒状掺杂剂。由此,粒状掺杂剂的投下位置设定于由x轴和y轴构成的坐标平面的第一象限内的、y轴坐标的绝对值不超过提拉中的单晶硅s的直体部的半径rs的区域且在由x轴和y轴构成的坐标平面上比以原点为中心的半径rs l/2的圆更靠外侧的区域t1。
[0054]
当对流cf的旋转方向为逆时针方向且单晶硅s的旋转方向为顺时针方向时,控制装置18将投下位置选择装置17控制为向第2导管162导入粒状掺杂剂。由此,粒状掺杂剂的投下位置设定于由x轴和y轴构成的坐标平面的第二象限内的、y轴坐标的绝对值不超过提拉中的单晶硅s的直体部的半径rs的区域且在由x轴和y轴构成的坐标平面上比以原点为中心的半径rs l/2的圆更靠外侧的区域t2。
[0055]
当所述对流cf的旋转方向为顺时针方向且单晶硅s的旋转方向为逆时针方向时,控制装置18将投下位置选择装置17控制为向第3导管163导入粒状掺杂剂。由此,粒状掺杂剂的投下位置设定于由x轴和y轴构成的坐标平面的第三象限内的、y轴坐标的绝对值不超过提拉中的单晶硅s的直体部的半径rs的区域且在由x轴和y轴构成的坐标平面上比以原点为中心的半径rs l/2的圆更靠外侧的区域t3。
[0056]
接着,从所设定的投下位置(导管16)投下粒状掺杂剂,向硅熔液m中添加掺杂剂。
[0057]
接着,对上述实施方式的效果进行说明。在以下的说明中,对如图7所示当对流cf的旋转方向为逆时针方向(cow)且单晶硅s的旋转方向rd为顺时针方向(cw)时将投下位置设为区域t2所产生的效果进行说明。若对流cf的旋转方向为逆时针方向,则在硅熔液m的液面ma上产生如图8的箭头fl1~fl3所示的流动。其中,箭头fl2所示的流动为朝向单晶硅s的流动,箭头fl3所示的流动为远离单晶硅s的流动。
[0058]
在此,当向箭头fl2所示的流动中投下粒状掺杂剂时,粒状掺杂剂有时在熔融之前到达单晶硅s。若粒状掺杂剂未熔融而到达单晶硅s,则成为位错化的原因。另一方面,若向箭头fl3所示的流动中投下粒状掺杂剂,则粒状掺杂剂不朝向单晶硅s而朝向坩埚3内壁面流动之后,朝向坩埚3的底面钻入似地流动。由此,能够防止粒状掺杂剂未熔融而到达单晶硅s。
[0059]
并且,若假设从铅垂方向上方观察的单晶硅s的旋转方向rd为顺时针方向,则粒状掺杂剂的投下位置优选设为第二象限。这是因为,若向第二象限投下粒状掺杂剂,则粒状掺杂剂随着伴随单晶硅s的旋转产生的流动而向远离单晶硅s的方向流动。
[0060]
此外,粒状掺杂剂的投下位置优选与单晶硅s的外周面分开。这是因为,若粒状掺杂剂的投入位置靠近单晶硅s,则熔融前的粒状掺杂剂可能会到达单晶硅s。因此,如图7所示,通过将区域t2设定于比以原点为中心的半径rs l/2的圆更靠外侧的位置,也能够防止粒状掺杂剂未熔融而到达单晶硅s。
[0061]
另外,投下位置并不限于图7所示的区域t2。即,只要位于在硅熔液m的液面ma上远离单晶硅s的直体部的流动占主导的区域上,则可以适当变更区域。例如,可以向比图7所示的区域t2更靠近单晶硅s的位置投下粒状掺杂剂。
[0062]
并且,在本实施方式的提拉装置1中,通过具有4根导管16,能够将投下位置更可靠地设为硅熔液m的流动方向远离直体部的流动占主导的区域。
[0063]
〔其他实施方式〕另外,在上述实施方式中,作为掺杂剂投下装置15,使用了具有多个导管16且能够向从第一象限至第四象限为止的所有象限投下粒状掺杂剂的装置,但并不限于此。也可以将掺杂剂投下装置15例如设为具有2根导管16的装置,并将其设为仅根据对流cf的旋转方向来设定粒状掺杂剂的投下位置的结构。换言之,无需设为能够向从第一象限至第四象限为止的所有象限投下粒状掺杂剂的装置。
[0064]
并且,也可以设为可移动地设置1根导管16,并使导管16移动到所期望的象限位置的结构。并且,也可以将掺杂剂投下装置15设为例如具有1根导管16且仅向第一象限至第四象限中的一个象限投入粒状掺杂剂的装置。当在使用这种方式的提拉装置提拉单晶硅s的过程中投下粒状掺杂剂时,使用磁场施加装置5反复施加水平磁场,直至投下位置位于在硅熔液m的液面ma上远离单晶硅s的直体部的流动占主导的区域上。实施例
[0065]
接着,对本发明的实施例及比较例进行说明。另外,本发明并不限定于实施例。在实施例及比较例中,在使用如图1所示的提拉装置1提拉直径300mm的单晶硅s的过程中,使用掺杂剂投下装置15向硅熔液m中投下粒状掺杂剂,并比较了单晶硅s的位错化率。
[0066]
〔实施例1~4/比较例1~4〕在实施例1~4中,将粒状掺杂剂的投下位置设为与实施方式相同。在比较例1~4中,将粒状掺杂剂的投下位置设为与实施方式不同。作为一例,在实施例1中,当对流cf的旋转方向为顺时针方向且单晶硅s的旋转方向为顺时针方向时,向第四象限投下了粒状掺杂剂,但在比较例1中,向第三象限投下了粒状掺杂剂。并且,在实施例1~4、比较例1~4中,投下位置的y轴坐标的绝对值设定为大于单晶硅s的半径。即,在实施例1~4、比较例1~4中,向图8的箭头fl1所示的流动中投下了粒状掺杂剂。
[0067]
〔评价〕与本发明的实施方式同样地,在考虑对流cf的旋转方向及单晶硅s的旋转方向而设定了粒状掺杂剂的投下位置的实施例1~4中,与不考虑对流cf的旋转方向及单晶硅s的旋转方向而设定粒状掺杂剂的投下位置的比较例1~4相比,位错化率明显降低。根据以上能够确认到,通过考虑对流cf的旋转方向及单晶硅s的旋转方向而将粒状掺杂剂的投下位置设定于在硅熔液m的液面ma上远离单晶硅s的直体部的流动占主导的区域上,能够降低位错化率。
[0068]
[表2]
[0069]
〔实施例5~8/比较例5~8〕在实施例5~8中,将粒状掺杂剂的投下位置设为与实施方式相同。在比较例5~8中,将粒状掺杂剂的投下位置设为与实施方式不同。并且,在实施例5~8、比较例5~8中,将投入位置设定为投下位置的y轴坐标的绝对值不超过单晶硅s的半径。即,在实施例5~8、比较例5~8中,向图8的箭头fl2、fl3所示的流动中投下了粒状掺杂剂。
[0070]
〔评价〕与实施例1~4/比较例1~4同样地,通过考虑对流cf的旋转方向及单晶硅s的旋转方向来降低了位错化率。并且,通过将投入位置设定为投下位置的y轴坐标的绝对值不超过单晶硅s的半径,能够进一步降低了位错化率。
[0071]
[表3]
附图标记说明
[0072]
1-提拉装置,2-腔室,3-坩埚,4-加热器,5-磁场施加装置,12-温度测定装置,15-掺杂剂投下装置,16-导管,17-投下位置选择装置,18-控制装置,cf-对流,m-硅熔液,md-磁场方向,s-单晶硅,t1~t4-区域。
再多了解一些
本文用于企业家、创业者技术爱好者查询,结果仅供参考。