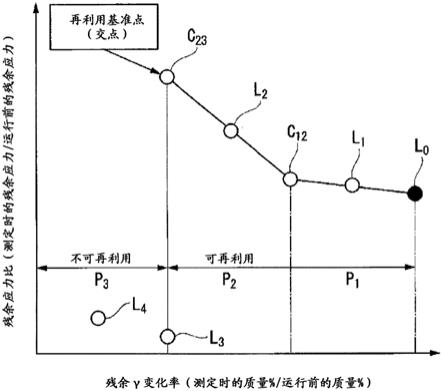
1.本发明涉及齿轮的再利用可否判定方法及齿轮的再利用可否判定系统。
背景技术:
2.构成减速机等的齿轮零部件由于价格昂贵且在难以入手的环境中使用的情况多,因此要求将从运行了一定时间的减速机取出并经规定的评价认为健全的齿轮再利用。在目前的工序中,仅较低负荷的齿轮零部件由作业人员目视确认齿面上有无玻璃、进行再利用的可否判断,无齿面剥离的齿轮的大约一半被再利用。对于高负荷的齿轮零部件,在经过规定的运行期间的阶段一律被废弃。
3.在专利文献1中,公开了由使用x射线衍射法得到的观测峰值的半值宽度推定残余寿命的方法。在专利文献2中,公开了由使用残余应力的变化的剩余寿命评价算式诊断轴承零部件的寿命的方法。在专利文献3中,公开了针对轴承零部件的疲劳损伤度,对残余γ相及半值宽度、表面粗糙度的变化量进行评价并推定残余寿命的方法。在专利文献4中,公开了利用涡流探伤测定残余γ相的变化量的方法。
4.现有技术文献
5.专利文献
6.专利文献1:日本特开2019-20249号公报
7.专利文献2:日本特开2018-40771号公报
8.专利文献3:国际公开第2011/074654号
9.专利文献4:日本特开2012-122993号公报
技术实现要素:
10.发明要解决的课题
11.关于在高负荷下使用规定时间的齿轮零部件,即使在无齿面剥离的健全状态下也全部被抛弃(废弃)。齿轮零部件的再利用率降低关系到工程/矿山现场的再生工序的成本升高。因此,要求基于保证品质的科学依据确立合理的再利用可否判断基准,以能够实现再利用率提高。
12.本发明是鉴于上述情况提出的,目的在于提供能够针对使用中或使用后的齿轮判定可否再利用并提高再利用比率的齿轮的再利用可否判定方法及齿轮的再利用可否判定系统。
13.用于解决课题的手段
14.本技术发明人通过定量测定齿轮的表层组织的变化而明确了可再利用的齿轮与不可再利用的齿轮的组织存在差异。具体来说,作为齿轮无伤的方法采用x射线衍射法来测定残余γ相的比例。其结果,发现残余γ相在齿轮的表层组织中根据运行中的负荷而减少。残余γ相减少被认为是由加工诱发马氏体相变引起。另外,由于因从残余γ相向马氏体相的相变而发生体积膨胀,因此能够预测残余应力变化。因而,使用x射线衍射法测定残余应
力的结果,发现运行后的残余应力的绝对值与运行前相比增加。此外,本技术发明人着眼于残余γ相的减少率与残余应力比的增加率的相关关系,发现能够基于此来判定齿轮的再利用可否。本发明提供以下方案。
15.(1)本发明一实施方式的齿轮的再利用可否判定方法为使用中或使用后的齿轮的再利用可否判定方法,其具有:残余γ相测定工序,在该工序中,测定所述齿轮中的残余γ相的含量;残余γ相变化率计算工序,在该工序中,计算所述残余γ相的含量的变化率;残余应力测定工序,在该工序中,测定施加于所述齿轮的残余应力;残余应力比计算工序,在该工序中,计算所述残余应力比;再利用可否判定工序,在该工序中,基于所述残余γ相变化率计算工序及所述残余应力比计算工序中的计算结果判定所述齿轮可否再利用,在所述再利用可否判定工序中,在所述齿轮的状态与第一阶段或第二阶段相当的情况下判定为可再利用,在与第三阶段相当的情况下判定为不可再利用,其中,在所述第一阶段,以所述齿轮使用开始时的状态为基准,随着所述残余γ相的含量的变化率减少而所述残余应力的变化率,所述第二阶段在所述第一阶段后,在所述第二阶段,随着所述残余γ相的含量的变化率减少,所述残余应力的变化率从所述第一阶段急剧增加,所述第三阶段在所述第二阶段后,在所述第三阶段,所述残余应力的变化率相对于所述第二阶段断续减少。
16.(2)本发明一实施方式的齿轮的再利用可否判定系统为使用中或使用后的齿轮的再利用可否判定系统,其包括:测定装置,其具有测定所述齿轮中的残余γ相的含量的残余γ相测定部及测定施加于所述齿轮的残余应力的残余应力测定部;以及判定装置,其具有计算所述残余γ相的含量的变化率的残余γ相变化率计算部、计算所述残余应力比的残余应力比计算部及进行所述齿轮可否再利用的判定的判定部,所述判定部基于残余γ相变化率计算部、所述残余应力比计算部的计算结果判定所述齿轮的状态与第一阶段、第二阶段及第三阶段中的哪个阶段相当,其中,在所述第一阶段,以所述齿轮使用开始时的状态为基准,随着所述残余应力的变化率增大而所述残余γ相的含量的变化率减少,所述第二阶段在所述第一阶段后,在所述第二阶段,随着所述残余γ相的含量的变化率减少,所述残余应力的变化率从所述第一阶段急剧增加,所述第三阶段在所述第二阶段后,在所述第三阶段,所述残余应力的变化率相对于所述第二阶段断续减少。
17.(3)根据前述(2)所述的齿轮的再利用可否判定系统,也可以是,所述判定装置还具有数据库,所述数据库保存与所述残余γ相的含量和所述残余应力的相关关系相关的已知数据。
18.发明效果
19.根据本发明,能够基于从残余γ相的减少率和残余应力的增加率的相关关系导出的再利用可否判定的基准点合理地判定齿轮的再利用可否。另外,根据本发明,能够实现基于无伤检查的再利用可否的判定。其结果,将此前连外观检查也未实施便全部抛弃的齿轮零部件也包含在内,能够简单且客观地进行再利用判定,能够构建可靠性高的品质管理技术并大幅减少抛弃率、削减零部件成本。
附图说明
20.图1是示意性示出本发明一实施方式的齿轮的再利用可否判定系统的构成图。
21.图2a是示出本发明一实施方式的两个齿轮彼此一边相互啮合一边旋转的情形的
图。
22.图2b是将图2a的齿轮的局部放大并清晰示出最大应力负荷区域的图。
23.图3a是说明齿轮产生的龟裂的传播机制的图。
24.图3b是说明齿轮产生的龟裂的传播机制的图。
25.图3c是说明齿轮产生的龟裂的传播机制的图。
26.图3d是说明齿轮产生的龟裂的传播机制的图。
27.图4是示出齿轮的各运行状态下的残余γ相变化率与残余应力比的关系的曲线图。
28.图5a是示出本发明一实施方式的齿轮的再利用可否判定方法中包含的工序的流程的图。
29.图5b是示出本发明其他实施方式的齿轮的再利用可否判定方法中包含的工序的流程的图。
30.图6a是在运行前的阶段得到的齿轮截面的sem图像。
31.图6b是在运行后的阶段得到的齿轮截面的sem图像。
32.图6c是在运行后的另一阶段得到的齿轮截面的sem图像。
33.图7是齿轮的各运行状态下的残余γ相的粒度面积的柱状图。
34.附图标记说明
35.100 齿轮的再利用可否判定系统
36.101 测定装置
37.102 判定装置
38.103 残余γ相测定部
39.104 残余应力测定部
40.105 残余γ相变化率计算部
41.106 残余应力比计算部
42.107 判定部
43.108 报知控制器
44.109 数据库
45.110 报知部
46.10 齿
47.1 齿高方向的中央区域
48.2 齿根部的中央区域
49.3 齿高方向
50.4 齿宽方向
51.5、5a、5b 残余γ相
52.6 马氏体相
53.8 加工诱发马氏体相
54.a、b 齿轮
55.c
12
、c
23 拐点
56.d 旋转方向
57.p
1 第一阶段
58.p
2 第二阶段
59.p
3 第三阶段
具体实施方式
60.以下,使用附图详细说明作为应用本发明的实施方式的齿轮的再利用可否判定方法及齿轮的再利用可否判定系统。需要说明的是,为了使特征清楚易懂,方便起见,以下说明使用的附图存在将成为特征的部分放大示出的情况,不限于各构成要素的尺寸比率等与实际相同。另外,以下说明中例示的材料、尺寸等为一例,本发明并非限定于此,能够在不脱离其要旨的范围内适当变更实施。
61.<第一实施方式>
62.图1是示意性示出本发明第一实施方式的齿轮的再利用可否判定系统100的构成的图。齿轮的再利用可否判定系统100为使用中或使用后的齿轮的再利用可否判定系统,其主要包括测定装置101和判定装置102。测定装置101主要具有残余γ相测定部103及残余应力测定部104。判定装置102主要具有残余γ相变化率计算部105、残余应力比计算部106及判定部107。
63.残余γ相测定部103为测定齿轮中的残余γ(奥氏体)相(面心立方晶格)的含量的测定装置。残余γ相认为是渗碳处理的回火马氏体组织,有助于强韧化。整个试料的残余γ相的单位面积为0.005μm2~50μm2左右,该残余γ相存在比为35质量%以下。关于残余γ相的含量,例如,针对齿轮的最大应力范围的区域进行x射线衍射测定,根据各相的峰值强度比计算存在比(单位:质量%)并进行评价。
64.残余应力测定部104为测定施加于齿轮的残余应力的测定装置。作为残余应力测定部104能够使用x射线衍射装置。残余应力因各齿轮在旋转中与其他齿轮啮合而变化。图2a是示出两个齿轮a、b一边相互啮合一边旋转的情形的图。图2b是将构成齿轮b的一个齿10放大并清晰示出最大应力负荷区域的图。在使齿轮a沿方向d相对于齿轮b旋转的情况下,齿轮b的各区域承受残余应力,齿轮b的各齿10中的作为与齿轮a啮合的齿面啮合部的齿高方向3的中央区域1及齿根部的中央区域2为最大应力负荷区域。若齿10的形状在齿轮的厚度方向上相同,则齿10承受的残余应力在齿宽方向4上相同。
65.残余γ相变化率计算部105为计算残余γ相的含量的变化率(残余γ相变化率)的计算装置。残余应力比计算部106为计算残余应力比的计算装置。此处的残余γ相变化率、残余应力比表示以作为齿轮运行前的状态(初始状态、刚刚制造后的无损伤的新品状态、作为齿轮未使用的状态)为基准的比率。即,残余γ相变化率表示测定时的残余γ相的含量/运行前的残余γ相的含量,同样地,残余应力比表示测定时的残余应力/运行前的残余应力。
66.判定部(比较判定部)107为具有判定机构的装置,该判定机构基于残余γ相变化率计算部105、残余应力比计算部106的计算结果进行齿轮的状态是可再利用的状态还是不可再利用的状态的判定。
67.该判定着眼于齿轮产生的龟裂的传播由残余γ相的含量和残余应力引起而进行。图3a~图3d是说明齿轮产生的龟裂的传播机制的图。
68.如图3a所示,初始状态的齿轮a中存在多个残余γ相5和马氏体相(α’相)6。在使该齿轮a运行时,外部负荷施加于齿轮a。由此,在运行的第一阶段,如图3b所示,初始状态的齿轮含有的残余γ相5中的面积或尺寸较大的部分5a相变为具有更大构造(体积)的加工诱发马氏体相(αγ’相、体心立方晶格)。作为其结果,整体而言,残余γ相5的含量与初始状态相比减少。
69.在接下来的第二阶段,如图3c所示,面积或尺寸较小的残余γ相5b的一部分相变为加工诱发马氏体相,但也进行面积或尺寸较大的残余γ相5a向加工诱发马氏体相的相变,整体而言,残余γ相5的含量减少。
70.在之后的第三阶段,如图3d所示,面积或尺寸较小的残余γ相5b的大部分相变,整体而言,残余γ相5的含量与第二阶段相比进一步减少。残余γ相5的大致全部相变为加工诱发马氏体相,体积膨胀被约束而产生内部应力δσ。同时,由于产生龟裂、内部应力被释放而残余应力变化率急剧减少。
71.需要说明的是,应力放大系数δk、内部应力δσ、残余γ相的最大面积sr满足由下述式(1)表示的关系,δk为约5.7mpa
·m1/2
,而下限应力放大系数范围δkth为约5mpa
·m1/2
。因此,认为仅是由相变产生的内部应力不会使龟裂发展。但是,在施加了外部应力(外部负荷)的情况下,认为由于与相变了的残余γ的内部应力叠加而容易超过δkth,龟裂发展。
72.δk=δσ√sr
ꢀꢀꢀ
(1)
73.图4是示出各齿轮中的残余γ相的含量与残余应力的关系的曲线图。曲线的横轴表示相对于初始状态的残余γ变化率,曲线的纵轴表示相对于初始状态的残余应力比。由残余γ变化率及残余应力比规定的齿轮状态以在曲线中标记的方式与三个阶段(第一阶段p1、第二阶段p2、第三阶段p3)中的某一个相当。各标记按照从残余γ变化率为1的初始状态(运行时间)l0经过的运行时间与运行中的负荷的合计的乘积(l1、l2、l3、l4)的顺序排列。
74.第一阶段p1为以齿轮的使用开始时的状态(初始状态)为基准,随着残余γ相的含量的变化率减少而残余应力的变化率增加的阶段。在第一阶段p1,主要是1μm2以上的大的残余γ相相变为加工诱发马氏体相。
75.第二阶段p2为第一阶段p1后随着残余γ相的含量的变化率减少而残余应力的变化率从第一阶段p1急剧增加的阶段。在第二阶段p2,大部分大的残余γ相完成相变,外部负荷作用于小于0.5μm2的小的残余γ相。
76.第三阶段p3为第二阶段p2后残余应力的变化率相对于第二阶段p2断续减少的阶段。第三阶段p3的残余应力的变化率存在随着残余γ相的含量的变化率减少而进一步连续或断续持续减少的情况或维持恒定值的情况。在第三阶段p3,主要是小于0.5μm2的小的残余γ相也相变为加工诱发马氏体相。
77.第一阶段p1、第二阶段p2、第三阶段p3的标记分别沿着各分布直线l1、l2、l3分布。在第一阶段p1与第二阶段p2的边界、第二阶段p2与第三阶段p3的边界分别存在分布直线的斜率变为不连续的拐点c
12
、c
23
。也就是说,在拐点c
12
的前后、拐点c
23
的前后,各齿轮的劣化状态不同。拐点c
12
、c
23
的位置按齿轮的材质决定。
78.在拐点c
23
前的第一阶段p1、第二阶段p2,与初始状态相比,加工诱发马氏体相增加而体积膨胀被约束,但齿轮内部未破损,未发生无法目视确认的剥离等,齿轮成为可再利用的状态。另一方面,在拐点c
23
后的第三阶段p3,齿轮内部发生破损而表现为内部应力被释
放,齿轮成为不适合再利用的状态。因此,关于齿轮,能够将拐点c
23
设为再利用基准点,若是拐点c
23
前的状态,则能够判定为可再利用,若是拐点c
23
后的状态,则能够判定为不可再利用。
79.齿轮的再利用可否判定系统100也可以进一步具有保存与残余γ相的含量和残余应力的相关关系相关的已知数据的数据库109。在该情况下,即使是测定得到的数据仅为残余γ相和残余应力中的某一方,也能够通过参照保存有二者的相关关系的数据库来推定拐点c
23
,因此能够更简单地判定可否再利用。另外,齿轮的再利用可否判定系统100具有存储残余γ相的含量、残余应力等测定值的测定值存储部107,通过该参照该测定值存储部中蓄积的残余γ相的含量和/或残余应力,从而残余γ相变化率计算部105和/或残余应力比计算部106能够掌握残余γ相的含量和/或残余应力的经时变化。由此,能够判定各测定值处于哪个阶段或这些阶段间的哪个拐点。另外,齿轮的再利用可否判定系统100也可以具有用于报知再利用可否判定的结果的报知控制器108、报知部110。
80.图5a是示出本发明一实施方式的齿轮的再利用可否判定方法中包含的工序的流程的图。齿轮的再利用可否判定方法针对使用中或使用后的齿轮使用上述齿轮的再利用可否判定系统实施,主要具有残余γ相测定工序s1、残余γ相变化率计算工序s2、残余应力测定工序s3、残余应力比计算工序s4及再利用可否判定工序s5。
81.在残余γ相测定工序s1中,使用x射线衍射法测定齿轮的最大应力负荷区域中的残余γ相的含量。接下来,在残余γ相变化率计算工序s2中,计算测定得到的残余γ相的含量相对于初始(齿轮的运行前)的残余γ相的含量的变化率。接下来,在再利用可否判定工序s5中,确认基于计算结果的齿轮的状态与上述第一阶段p1、第二阶段p2、第三阶段p3中的哪个相当。在齿轮的状态与第三阶段相当的情况下,判定该齿轮不可再利用。在齿轮的状态与第一阶段p1或第二阶段p2相当的情况下,进入接下来的残余应力测定工序s3。
82.在残余应力测定工序s3中,使用x射线衍射法测定齿轮的最大应力负荷区域中的残余应力。接下来,在残余应力比测定工序s4中,计算测定得到的残余γ相的含量相对于初始(齿轮的运行前)的残余γ相的含量的变化率。接下来,在再利用可否判定工序s5中,确认基于计算结果的齿轮的状态与上述第一阶段p1、第二阶段p2、第三阶段p3中的哪个相当。在齿轮的状态与第三阶段p3相当的情况下,判定该齿轮不可再利用。在齿轮的状态与第一阶段p1或第二阶段p2相当的情况下,判定该齿轮可再利用。
83.需要说明的是,残余γ相测定工序s1、残余γ相变化率计算工序s2、残余应力测定工序s3及残余应力比计算工序s4的顺序也可以调换。另外,也可以在残余γ相变化率计算工序s2及残余应力比计算工序s4后仅进行一次再利用可否判定工序s5。
84.图5b是示出本发明其他实施方式的齿轮的再利用可否判定方法中包含的工序的流程的图。齿轮的再利用可否判定方法主要具有测定残余γ相和残余应力中的某一方的工序s6、计算残余γ相变化率和残余应力比中的某一方的工序s7、数据库参照工序s8及再利用可否判定工序s9。
85.在测定残余γ相和残余应力中的某一方的工序s6中,使用x射线衍射法测定齿轮的最大应力负荷区域中的残余γ相的含量和残余应力中的某一方。接下来,在计算残余γ相变化率和残余应力比中的某一方的工序s7中,计算相对于初始(齿轮的运行前)的残余γ相的含量或残余应力的测定得到的残余γ相的含量的变化率或残余应力比。接下来,在再
利用可否判定工序s8中,确认基于计算结果的齿轮的状态与上述第一阶段p1、第二阶段p2、第三阶段p3中的哪个相当。在齿轮的状态与第三阶段p3相当的情况下,判定该齿轮不可再利用。在齿轮的状态与第一阶段p1或第二阶段p2相当的情况下,进入接下来的数据库参照工序s8。
86.在数据库参照工序s8中,使用存储有对应的残余γ相的含量与残余应力的相关关系的数据的数据库,对残余γ相和残余应力中的一方或双方的数据进行插补。在此基础上,在再利用可否判定工序s9中,确认基于计算结果的齿轮的状态与上述第一阶段p1、第二阶段p2、第三阶段p3中的哪个相当。在齿轮的状态与第三阶段p3相当的情况下,判定该齿轮不可再利用。在齿轮的状态与第一阶段p1或第二阶段p2相当的情况下,判定该齿轮可再利用。
87.如上所述,根据本实施方式,能够基于从残余γ相的减少率和残余应力的增加率的相关关系导出的再利用可否判定的基准点,合理地判定齿轮的再利用可否。另外,根据本实施方式,能够实现基于无伤检查的再利用可否的判定。其结果,能够将连此前外观检查也未实施便全部抛弃的齿轮零部件也包含在内,简单且客观地进行再利用判定,能够构建可靠性高的品质管理技术并大幅减少抛弃率、削减零部件成本。
88.实施例
89.以下,基于实施例使本发明的效果更加清楚。需要说明的是,本发明不限定于以下实施例,能够在不变更其要旨的范围内适当变更实施。
90.针对运行前及运行后的齿轮进行电解研磨,使残余γ相在齿轮的齿面露出,使用扫描电子显微镜(sem)使残余γ相的分布状态图像化。图6a~图6c分别是运行前、运行后回收齿轮1、运行后回收齿轮2的sem图像(组织写真)。采用距离齿面表层的深度为约20μm、沿着齿面表层的宽度为约25μm的视野。能够从该sem图像中确认以板状排列的马氏体相6。另外,在该马氏体相6中,碳化物7作为白色粒状物也被确认。另一方面,残余γ相5由于不包含碳化物,因此成为平坦且单一的对比度。
91.如图6a所示,在运行前存在大量残余γ相5,其小的粒度面积为0.005μm2左右,大的粒度面积达到50μm2。该状态与上述第一阶段p1相当。
92.如图6b所示,在运行后回收齿轮1中,残余γ相5的存在比减少。特别是,超过2μm宽度的粗大的残余γ相被分割。残余γ相5的一部分相变为加工诱发马氏体相8。该状态与上述第二阶段p2相当。
93.如图6c所示,在运行后回收齿轮2中,残余γ相5的存在比进一步显著减少,使用sem图像确认的其他微细的残余γ相自身显著减少。大部分变为加工诱发马氏体相8。该状态与上述第三阶段p3相当。
94.关于图6a~图6c的各sem图像中的25μm
×
20μm的区域中包含的残余γ相,计算各粒度面积的个数。图7是将加工计算结果汇总的柱状图,横轴表示残余γ相的粒度面积(μm2),纵轴表示残余γ相的个数。就运行前的残余γ相而言,0.5μm2以下最多,粒度面积越大则越少。运行后的残余γ相的这一倾向也相同,特别是在运行后回收齿轮2中,微细的粒度面积的残余γ相的减少变得显著。
再多了解一些
本文用于企业家、创业者技术爱好者查询,结果仅供参考。