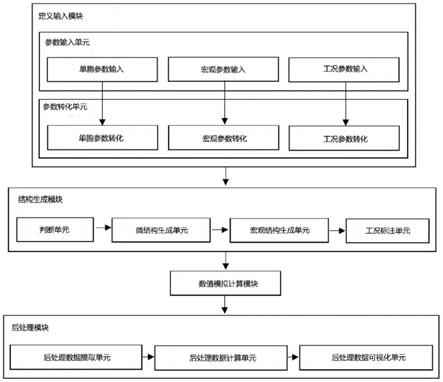
1.本发明涉及的是一种工程设计领域的技术,具体是一种针对杆结构的点阵晶格力学超材料结构的模型生成、工况设置、计算分析及结果处理的仿真模拟整流程自动化方法。
背景技术:
2.力学超材料(mechanical metamaterials)是一类通过人为设计的结构来获得独特机械性能的材料,在航空航天、机械制造、机器人、生物工程等高精尖领域具有广阔的应用前景。通过用合理方法设计力学超材料的单胞微观结构,并在空间上周期性或非周期性地排布单胞组成宏观结构,可以使力学超材料形成的结构具有超轻质量、超高比刚度、高柔性、负泊松比、可控热传导或受压扭转等独特的性质。常见的力学超材料单胞微观结构有基于杆件的、基于曲面的和基于空间填充的。
3.基于杆件的力学超材料结构是一类晶格、点阵结构(lattices,trusses structure),其表现出的性质因微观上的杆件的连接方式、尺寸参数(截面形状、长短、粗细)和材料分布,以及宏观上的单胞排布、结构设计和边界条件而异。在工程分析上需要根据这些参数建立数字模型对点阵晶格力学超材料结构的力学响应或特殊力学性质进行仿真分析,一次分析流程包括采样、cad建模、cae仿真、数据提取,且此数字化模型需要满足精度的要求。而面对这一实际需求,手动地对这类结构从微观上的单胞结构到宏观上的单胞排布进行逐步建模与设置,将耗费大量的时间成本甚至人工无法完成任务,且任何细小的结构设计上的改变将要重新进行建模,效率低下,实际操作中不可行。因此,需要高效可行的点阵晶格力学超材料结构仿真分析自动化方法来解决人工操作所带来的弊端。
技术实现要素:
4.本发明针对现有对结构直接离散的建模方法对计算机算力要求非常高且无法适用于单胞微结构复杂或庞大整体结构场景的缺陷,提出一种杆结构超材料结构多工况仿真自动化系统及方法,以定义微观、宏观结构的几何参数和结构的分析工况参数作为输入,通过结构生成算法生成点阵晶格力学超材料结构模型,自动进行相应工况的仿真分析,并根据需求自动进行后处理提取相关数据。
5.本发明是通过以下技术方案实现的:
6.本发明涉及一种杆结构超材料结构多工况仿真自动化系统,包括:定义输入模块、结构生成模块、数值模拟计算模块以及后处理模块,其中:定义输入模块对杆结构的点阵晶格力学超材料结构及分析工况的参数进行人为或采样定义并将设计参数转换至标准格式的数据后输出至结构生成模块;结构生成模块根据标准格式数据依次生成杆结构的点阵晶格力学超材料单胞的节点与单元信息、杆结构的点阵晶格力学超材料宏观结构的节点与单元信息后,通过赋予边界条件与载荷生成数值仿真模型并输出至数值模拟计算模块;数值模拟计算模块调用系统命令行在对应的数值仿真软件求解器中对杆结构的数值仿真模型进行计算,得到对应的杆结构数据文件并输出至后处理模块;后处理模块根据工况需求对
杆结构数据文件中的点阵晶格力学超材料结构的数值计算结果数据进行后处理及数据提取后进行结果可视化。
7.本发明涉及一种基于上述系统的杆结构超材料结构多工况仿真自动化方法,根据单胞微结构的杆结构端点的位置信息和端点的连接关系信息,通过结构生成算法对点阵晶格力学超材料单胞的拓扑形式进行解构,依次实现几何重构、网格划分、材料赋予;然后根据宏观上单胞的排布位置信息,通过结构生成算法对单胞进行空间排布并解决单胞连接性问题;最后根据工况参数,提取出目标边界信息,整合上述微、宏观几何信息生成结构的数值分析模型并自动通过系统命令行提交计算,仿真完成后针对数值分析软件返回的结果结合工况进行后处理并结果可视化。
8.所述的结构生成算法,具体包括:首先检测输入的定义单胞微结构几何形式和单胞宏观排布位置信息的参数是否合理,接着依次生成并存储目标超材料结构的单胞微结构信息和宏观结构信息,再生成需施加的边界条件与载荷信息,最后将上述信息数据生成点阵晶格力学超材料结构的数值分析模型文件。
9.所述的解构是指:根据参数生成单胞微结构中杆结构端点即关键点的坐标信息,生成杆结构两端端点两两匹配的坐标和编号。
10.所述的施加边界条件与载荷是指:根据工况提取标准化列表中的关键几何信息并加入标准化列表。
11.所述的关键几何信息包括:边界上的节点与单元的位置与编号信息、旋转中心坐标。
12.所述的定义单胞微结构几何形式包括:单胞尺寸、特征结构无量纲参数、杆结构信息(截面形状、长短、粗细等)、材料信息(材料密度、杨氏模量、泊松比等)、网格精度(分辨率),进而由此转换处理得到的单胞结构关键点的坐标信息、关键点间的连接关系、杆结构信息(截面形状、长短、粗细等)、材料信息(材料密度、杨氏模量、泊松比等)、网格精度(分辨率)。
13.所述的单胞宏观排布位置信息包括:宏观结构的形状、尺度因子和排布信息,其中:宏观结构的形状包括规则的六面体、圆柱体、球体,以及任意用数据记录的形状信息;尺度因子是指宏观结构整体尺寸最大值与单胞尺寸的比值;排布信息是对单胞在空间上的位置的定义,包括周期性排布和非周期性排布的定义,其通过以下方式得到:
①
将宏观结构形状定义表达为矩阵形式,
②
偏移单胞坐标与编号并进行查重,
③
在每个两两匹配的梁两端关键点之间根据分辨率划分网格,生成对应节点坐标和编号,
④
标准化列表用于目标仿真软件的输入文件的文本写入。
14.所述的工况是指力学方面的静态工况或动态工况,包括但不局限于单向拉伸、单项扭转、单向碰撞以及其他可能的组合工况。
15.所述的数值分析是指cae分析,其通过但不限于abaqus、ansys、ls-dyna等实现。
16.所述的后处理包括:提取节点位移数据、应力场分布、应变能变化、速度数据。技术效果
17.本方法通过采用简单且通用的结构定义形式,即直接定义杆结构的关键点几何信息可实现任意点阵晶格超材料结构的生成,并根据储存的几何信息数据在后处理时可直接索引到仿真模型目标节点或单元的计算结果。与现有技术相比,本发明适应参数输入或自
由定义两种输入类型,针对基于杆结构的点阵晶格力学超材料的多尺度结构,对其宏微观设计进行标准化处理,进而通过结构生成算法生成可直接用于数值分析的多尺度结构模型,并自动对返回的数据文件进行后处理,根据工况需求进行分析与提取对应数据,可实现点阵晶格力学超材料多尺度结构的设计生成分析一体化流程。对于基于点阵晶格力学超材料的复杂结构的快速生成与分析,或项目需要大量样本点的工程需求,本方法能实现人工无法胜任的高效和准确,具有实际的工程价值。
附图说明
18.图1为本发明系统示意图;
19.图2为本发明方法流程图;
20.图3为实施例生成的点阵晶格力学超材料结构示意图;
21.图中:(a)为点阵晶格力学超材料长方体结构,(b)为点阵晶格力学超材料单胞微结构,(c)为构成点阵晶格力学超材料的杆结构,(d)-(g)为给定拓扑结构时不同参数输入下不同的点阵晶格力学超材料单胞微结构;
22.图4为本发明点阵晶格力学超材料结构静态仿真及其力学响应的abaqus云图;
23.图5为后处理模块对实施例中的点阵晶格力学超材料结构的扭转角后处理结果示意图;
24.图中:(a)为静态仿真结构件边界条件与载荷示意图,(b)为后处理的单位应变扭转角与几何参数关系图;
具体实施方式
25.如图1所示,为本实施例涉及的一种点阵晶格力学超材料仿真多工况、全流程的自动化模块系统,包括:依次相连的定义输入模块、结构生成模块、数值模拟计算模块以及后处理模块,其中:定义输入模块将点阵晶格力学超材料结构及分析工况的参数进行人为或采样定义并将设计参数转换至标准格式的数据后输出至结构生成模块;结构生成模块根据标准格式数据依次生成点阵晶格力学超材料单胞的节点与单元信息、点阵晶格力学超材料宏观结构的节点与单元信息后,通过赋予边界条件与载荷生成数值仿真模型并输出至数值模拟计算模块;数值模拟计算模块以结构生成模块的仿真模型文件作为输入,调用系统命令行在对应的数值仿真软件求解器中对数值仿真模型进行计算,得到对应的数据文件并输出至后处理模块;后处理模块根据工况需求对数据文件中的点阵晶格力学超材料结构的数值计算结果数据进行后处理及数据提取后进行结果可视化。
26.所述的定义输入模块包括:参数输入单元和参数转化单元,其中:参数输入单元根据单胞参数输入、宏观参数输入和工况参数输入存储定义结构几何信息、边界条件与载荷的参数数据,参数转化单元根据输入的参数数据分别进行单胞参数转化、宏观参数转化和工况参数转化,生成标准的数据格式储存在通用的列表中。
27.所述的结构生成模块包括:依次相连的判断单元、微结构生成单元、宏观结构生成单元和工况标注单元,其中:判断单元识别来自定义输入模块的参数是否具有实际物理意义,对于合格的参数输入传递给微结构生成单元,生成杆结构端点坐标信息、端点连接关系信息并输出至宏观结构生成单元;宏观结构生成单元根据单胞排布的位置信息对微结构生
成单元的坐标信息进行相应的偏置,经过端点查重,构建整体的杆结构端点坐标信息和端点连接关系信息并输出至工况标注单元;工况标注单元根据所设置工况标记对应的边界处的杆结构端点信息和连接信息,进而通过文本编辑方法生成总体的仿真模型文件并输出至数值模拟计算模块。
28.所述的后处理模块包括:依次相连的后处理数据提取单元、后处理数据计算单元和后处理数据可视化单元,其中:后处理数据提取单元采用脚本文件读取来自数值模拟计算方法单元的数据文件,将模型各节点的位移、应力、应变信息读取并存储;后处理数据计算单元根据工况需求对数据进行计算转化;后处理可视化单元根据工况需求将数据可视化,生成图、表、模型。
29.如图3所示,为本实施例涉及的一种基于上述系统生成的点阵晶格力学超材料构成的多尺度结构件,其中图3(a)所示的长方体结构由图3(b)所示的点阵晶格力学超材料单胞进行周期性地3*3*5排布组成的,而单胞结构由图3(c)所示的杆结构作为基本结构构成。
30.本方法输入中的单胞结构定义可由给定拓扑形式的单胞参数化得到,也可由人为定义形式不限的结构获得。在本实施例中,采用给定拓扑形式的参数化单胞,具体而言,定义的几何参数有:单胞长度lc,特征正方形尺寸a和b,以及杆横截面直径d。如图3(d)-(g)所示,是变化参数的基于杆结构点阵晶格力学超材料单胞的结构设计。本实施例中,构成超材料的母材材料设置为钢,杨氏模量e=210000mpa,泊松比μ=0.3,密度ρ=7.9g/cm3。
31.本实施例的设计目标是研究该多尺度结构受压扭转性能随几何参数变化的规律。因此,数值分析计算的工况设置为:长方体结构件底部面为固定边界,顶部面则施加固定位移边界,其他面设置为自由边界。通过变化特征尺寸a、b,以及杆横截面直径d,由多尺度结构生成模块建立仿真模型,再提交多尺度结构数值计算模块进行仿真计算,通过后处理模块提取计算结果的位移数据,处理得到结构件的单位应变扭转角,输出绘制该点阵晶格力学超材料扭转性质分布图。
32.如图2所示,为本实施例涉及的一种基于上述系统的点阵晶格力学超材料结构仿真自动化方法,包括以下步骤:
33.步骤一、固定单胞长度lc,对特征尺寸a、b,以及杆横截面直径d进行均匀分布采样,采样点分别为na=20,nb=20,nd=4。令迭代变量i=1。分辨率res设置为1。
34.步骤二、结合宏观形状定义将所有样本点组成几何参数{pm}={(lc,a,b,d,3
×3×
5)}。从中选取一个参数水平pi,并依此通过matlab实现生成宏观结构形状的三维矩阵v=genstruct(pi)。
35.步骤三、检验是否符合设计要求,否则返回步骤二。
36.步骤四、生成单胞关键点坐标和编号x=getpoints(pi)。
37.步骤五、生成同一杆结构两端关键点的匹配信息[umatch,uid]=matchpoint(x,pi)。
[0038]
步骤六、令迭代变量j=1。
[0039]
步骤七、偏移单胞坐标与编号并进行查重[xmatch,xid]=latticematchpoint(umatch,uid,pi,vj),重复步骤七直到查重通过。
[0040]
步骤八、根据分辨率res划分网格,生成对应节点坐标和编号[xnode,nodeid]=getnodes(xmatch,xid,res)。
[0041]
步骤九、提取边界信息[blist,bid]=findboundary(xnode,nodeid),将长方体结构顶面、底面节点的编号和坐标存储。
[0042]
步骤十、通过matlab文本编辑写入input文件命名“i.inp”。inp文件声明了该结构的节点编号、节点集合、单元编号、单元集合、材料属性、边界条件和加载方式,其中材料为钢,杨氏模量e=210000mpa,泊松比μ=0.3,密度e=7.9g/cm3,固定位移u=0.1。
[0043]
步骤十一、通过matlab调用系统命令行cmd,命令行cmd将i.inp提交abaqus cae standard求解器进行无gui计算,返回数据文件“i.odb”。
[0044]
步骤十二、通过python获取i.odb历史数据,提取结构顶部边界所有节点位移场,计算获得单位应变扭转角。
[0045]
步骤十三、重复步骤二至步骤十二,直至获取所有样本点的分析结果。
[0046]
步骤十四、将单位应变扭转角与几何参数绘制成三维曲面图。
[0047]
经过具体实际实验,将上述点阵晶格力学超材料结构进行自动化仿真分析,在windows10环境下64核cpu中央处理器上运行上述方法计算仿真模型,得到单项压缩下的位移云图如图4;进行后处理和数据提取处理,得出的结构扭转角如图5所示,图中单胞的特征结构参数转换为无量纲参数v=a/lc,ω=b/lc,η=d/lc,应变云图与理论分析结果相符。一共1600个样本点的运行处理时间为133.34小时,人工无法胜任。
[0048]
与现有其他自动化技术相比,本方法实现了针对基于杆结构点阵晶格力学超材料单胞的任意拓扑形式的定义参数化;实现了点阵晶格力学超材料宏观结构的自由形状定义和单胞排布形式;实现了点阵晶格力学超材料结构的设计、生成、分析、后处理的仿真全流程自动化,大大提高了工作效率。
[0049]
上述具体实施可由本领域技术人员在不背离本发明原理和宗旨的前提下以不同的方式对其进行局部调整,本发明的保护范围以权利要求书为准且不由上述具体实施所限,在其范围内的各个实现方案均受本发明之约束。
再多了解一些
本文用于企业家、创业者技术爱好者查询,结果仅供参考。