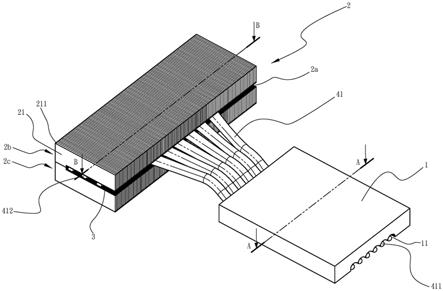
1.本发明涉及一种散热模块结构,尤指一种可改善散热或导热元件之间不易焊接结合的散热模块结构。
背景技术:
2.铜具有热传导效率高的特性,故现有散热模块结构常选用铜作为直接与发热源接触并吸收发热源所产生的热量的基座,并由铜基座再将所吸附的热量传递给作为加速热传导的热管及增加散热面积且散热效率较佳的鳍片,但以铜材质制成的基座及热管或鳍片其整体重量较重且材料成本较为昂贵,近年来已逐渐被质轻且成本较低的铝材质鳍片及铝基座所取代使用。
3.虽选用铝材质取代铜材质可改善了铜重量重及材料成本昂贵等问题,但铝材质并非不具有缺点,如铝表面易被氧化,在焊接过程中生成高熔点的氧化物,使焊缝金属难以完全熔合,给施焊带来困难。
4.若铜与铝直接进行焊接时,两材料直接对接的部位,在焊接后容易因为脆性大而产生裂纹,并且在铜与铝进行熔焊时,靠近铜材料这一侧的焊缝中很容易形成cual2等共晶,而cual2等共晶结构仅分布于材料的晶界附近,容易产生晶界间的疲劳或裂纹,又由于铜与铝两者的熔点温度及共晶温度相差甚大,在熔焊作业中,当铝熔化时而铜却保持固体状态,当铜熔化时,铝已熔化很多了,无法以共融或共晶状态共存,增加焊接难度,再者,焊缝易产生气孔,由于铜与铝的导热性都很好,焊接时熔池金属结晶快,高温时的冶金反应气体来不及逸出,故而容易产生气孔,故铜与铝材质间无法直接进行焊接,则必须对该铝材质表面进行表面改质后使得以进行后续与铜材质或其他材料焊接的作业,故为改善前述现有改用铝材质取代铜材质无法直接与铜或其他异材质进行焊接的缺失,则熟悉该项技艺的人士使用了无电镀镍作为表面改质的技术工法,并无电镀镍有三种:低磷、中磷、高磷。且无电镀沉积(electroless deposition)又可以称做化学镀(chemical deposition)或自催化镀法(autocatalytic plating),无电镀镍液可分为下列三种:(1)活化敏化 酸性镀浴ph植在4~6之间的属于酸性镀液,其特色是蒸发量所引起成分量的损失较少,虽然操作温度较高,但镀液较安全且容易控制,含磷量高、镀率高,常为工业界所使用。(2)活化敏化 碱性镀液碱性镀浴的ph植在8~10之间,因调整ph植的氨水容易挥发,在操作时须适时补充氨水来维持ph植的稳定,含磷量较少,镀液较不稳,操作温度较低。(3)hpm 碱性镀浴hpm是将硅晶片浸泡于di-water:h2o2(aq):hcl(aq)=4:1:1的混合液中利用硅晶表面形成的氧化层来取代敏化活化,在表面形成自我催化表面。
5.而无电镀镍制程中需使用大量的化学反应液体,并且在无电镀镍制程后将会产生大量含有重金属或化学物质的工业废液,而工业废液中都会产生大量的含有黄磷等有毒物质的废水,并且该废水无法在重复使用,也必须通过专责单位将该废水进行回收处理,不能将该废水直接排放避免环境收到污染。黄磷污水中含有50~390mg/l浓度的黄磷,黄磷是一种剧毒物质,进入人体对肝脏等器官危害极大。长期饮用含磷的水可使人的骨质疏松,发生
下颌骨坏死等病变。故现行各国已开始禁用此项制程,并推广无毒制程借以保护环境。
6.故如何提供一种可降低散热模块结构整体重量,以及取代化学镀镍作为改善铝材质无法与其他异材质焊接的表面改质工法,同时可有利于焊接作业进行又不额外产生环境污染物的方法,则为现阶段首重的目标。
技术实现要素:
7.如此,为有效解决上述的问题,本发明的主要目的,提供一种取代化学镀镍作为改善铝制散热元件与其他相异材质散热元件间无法直接进行焊接的散热模块结构。
8.为实现上述目的,本发明采用的技术方案是:
9.一种散热模块结构,其特征在于,包含:
10.一铝质基座,一侧具有至少一热管容置槽;
11.一散热装置,由复数散热鳍片相互扣接组成的一散热鳍片组,该散热鳍片组一侧具有一第一热管容置部,该散热装置与前述铝质基座水平方向并列设置;
12.一铜质置入层,设置于该热管容置槽表面;
13.复数热管,该复数热管是铜材质,该复数热管的一端具有一吸热段连接该热管容置槽,该复数热管另一端沿水平方向延伸一冷凝段并远端连接该散热装置的该第一热管容置部;
14.通过该铜质置入层的设置令该铝质基座及该散热装置与该复数热管能够直接进行焊接结合。
15.所述的散热模块结构,其中:所述散热装置具有一第一散热鳍片组及一第二散热鳍片组,该第一散热鳍片组、第二散热鳍片组是铝材质,该第一散热鳍片组具有复数散热鳍片并且每一散热鳍片具有至少一对折边,该复数散热鳍片通过该至少一对折边相互搭接组设,该第二散热鳍片组具有复数散热鳍片并且每一散热鳍片具有至少一对折边,该第二散热鳍片组的该复数散热鳍片通过第二散热鳍片组的该至少一对折边相互搭接组设,该第一散热鳍片组叠设于该第二散热鳍片组上方,该第一热管容置部形成于该第一散热鳍片组、第二散热鳍片组之间相对应但未相互结合处的一凹槽空间,所述热管具有复数第一热管,该复数第一热管的该吸热段设置于该铝质基座的热管容置槽中,该冷凝段设于前述第一热管容置部中呈松配合,该第一热管容置部表面设有该铜质置入层,令所述冷凝段与前述第一热管容置部能够直接进行焊接结合。
16.所述的散热模块结构,其中:所述冷凝段与前述第一热管容置部呈紧配方式结合,该第一热管容置部紧迫该冷凝段中。
17.所述的散热模块结构,其中:所述散热装置还具有一第三散热鳍片组及一第四散热鳍片组,并该第三散热鳍片组具有复数散热鳍片并且每一散热鳍片具有至少一对折边,该复数散热鳍片通过该至少一对折边相互搭接组设,该第四散热鳍片组具有复数散热鳍片并且每一散热鳍片具有至少一对折边,该第四散热鳍片组的该复数散热鳍片通过该第四散热鳍片组的该至少一对折边相互搭接组设,该第三散热鳍片组叠设于该第四散热鳍片组上方,该第三散热鳍片组、第四散热鳍片组设置于该第一散热鳍片组、第二散热鳍片组上方,该第四散热鳍片组与该第一散热鳍片组不相互接触,一第二热管容置部形成于该第三散热鳍片组、第四散热鳍片组之间相对应但未相互结合处的一凹槽空间,该复数热管还具有一
第二热管,该第二热管的该吸热段设置于该铝质基座的热管容置槽中,该冷凝段设于前述第二热管容置部中,该第三散热鳍片组、第四散热鳍片组是铝材质,所述冷凝段与前述第一热管容置部、第二热管容置部松配方式结合,该第一热管容置部、第二热管容置部表面设有该铜质置入层,令所述冷凝段与前述第一热管容置部、第二热管容置部能够直接焊接。
18.所述的散热模块结构,其中:所述铜质置入层在该铜质置入层的相反两面具有一植入面及一接触面,该植入面咬嵌入该热管容置槽及该第一热管容置部的表面,该接触面作为该铜质置入层的外露表面与一焊料层结合。
19.所述的散热模块结构,其中:还具有一焊料层,设置于该铜质置入层与该复数热管之间,将该铝质基座与该复数热管及该散热装置固定结合,并该铝质基座及该散热装置呈相同高度或不同高度平行并列设置。
20.一种散热模块结构,其特征在于,包含:
21.一铝质基座,一侧具有一热管容置槽;
22.一散热装置,具有至少一散热器,该散热器一侧具有一第一热管容置部,该散热装置与前述铝质基座水平方向并列设置;
23.一铜质置入层,设于该热管容置槽表面;
24.复数热管,该复数热管是铜材质,该复数热管的一端具有一吸热段连接该热管容置槽,该复数热管另一端沿水平方向延伸一冷凝段并远端连接该散热装置的该第一热管容置部;
25.通过该铜质置入层的设置令该铝质基座及该散热装置与该复数热管能够直接进行焊接结合。
26.所述的散热模块结构,其中:所述散热装置具有一第一散热器及一第二散热器,所述第一散热器、第二散热器是铝材质,该第一散热器具有一第一基座并一侧延伸有复数散热鳍片,该第二散热器具有一第二基座并一侧延伸有复数散热鳍片,该第一散热器通过该第一基座与该第二散热器的第二基座相互贴设,该第一热管容置部设于该第一基座、第二基座之间未相互贴设的处的一凹槽空间,所述热管具有复数第一热管,该复数第一热管的该吸热段设置于该铝质基座的热管容置槽中,该冷凝段设于前述第一热管容置部中呈松配合,该第一热管容置部表面设有该铜质置入层,令所述冷凝段与前述第一热管容置部能够直接进行焊接结合。
27.所述的散热模块结构,其中:所述冷凝段与前述第一热管容置部呈紧配方式结合,该第一热管容置部紧迫该冷凝段。
28.所述的散热模块结构,其中:所述散热装置还具有一第三散热器及一第四散热器,该第三散热器具有一第三基座并一侧延伸复数散热鳍片,该第四散热器具有一第四基座并一侧延伸复数散热鳍片,该第三散热器通过第三基座与该第四散热器的第四基座相互贴设,该第三散热器、第四散热器设置于该第一散热器、第二散热器上方,该第四散热器与该第一散热器不相互接触,一第二热管容置部设于该第三基座、第四基座之间未相互贴设的处的一凹槽空间,该复数热管还具有一第二热管,该第二热管的该吸热段设置于该铝质基座的热管容置槽中,该冷凝段设于前述第二热管容置部中,该第三散热器、第四散热器是铝材质,所述冷凝段与前述第一热管容置部、第二热管容置部松配方式结合,该第一热管容置部、第二热管容置部表面设有该铜质置入层,令所述冷凝段与前述第一热管容置部、第二热
管容置部能够直接焊接。
29.所述的散热模块结构,其中:所述铜质置入层在该铜质置入层的相反两面具有一植入面及一接触面,该植入面咬嵌入该热管容置槽及该第一热管容置部的表面,该接触面作为该铜质置入层的外露表面与一焊料层结合。
30.所述的散热模块结构,其中:该铝质基座及该散热装置呈相同高度或不同高度平行并列设置。
31.借由本发明以该铜质置入层取代化学镀镍,当有铝制散热元件欲与其他异材质的散热元件进行焊接时,可通过于该铝制散热元件与其他元件结合的部位的表面设置该铜质置入层,改善铝制导热或散热元件不易相互进行焊接的问题,由该铜质置入层取代传统化学镀镍镀层所衍生的缺失。
附图说明
32.图1是本发明的散热模块结构第一实施例分解图;
33.图2a是本发明的散热模块结构第一实施例组合剖视图;
34.图2b是本发明的散热模块结构第一实施例组合剖视图;
35.图3是本发明的散热模块结构第二实施例的组合图;
36.图4是本发明的散热模块结构第三实施例的组合图;
37.图5是本发明的散热模块结构第四实施例的组合图。
38.附图标记说明:铝质基座1;热管容置槽11;散热装置2;第一热管容置部2a;第一散热鳍片组2b;第二散热鳍片组2c;第三散热鳍片组2d;第四散热鳍片组2e;第二热管容置部2f;第一散热器2g;第一基座2ga;散热鳍片2gb;第二散热器2h;第三散热器2i;第四散热器2j;第二基座2ha;散热鳍片2hb;散热鳍片21;折边211;铜质置入层3;植入面31;接触面32;热管4;第一热管41;吸热段411;冷凝段412;第二热管42;吸热段421;冷凝段422;焊料层5。
具体实施方式
39.本发明的上述目的及其结构与功能上的特性,将依据所附图式的较佳实施例予以说明。
40.请参阅图1、图2a、图2b,是本发明的散热模块结构第一实施例的分解及组合剖视图,如图所示,本发明散热模块结构,包含:一铝质基座1、一散热装置2、一铜质置入层3、复数热管4、一焊料层5;
41.该铝质基座1一侧具有一至少热管容置槽11,该铝质基座1设置该热管容置槽11的一侧是与至少一发热源(图中未示)接触的吸热侧,并该热管容置槽11作为容设并结合该复数热管4使用,并该复数热管4置入该热管容置槽11可选择与该吸热侧切齐。
42.所述散热装置2由复数散热鳍片相互扣接组成的一散热鳍片组,并于其中央或下方处设置一第一热管容置部2a,该散热装置2与前述铝质基座1呈水平方向并列或水平对卧设置,另该铝质基座1及该散热装置2可呈相同高度或不同高度平行并列设置。
43.并为了进一步增加制造便利,可将所述散热装置2由一第一散热鳍片组2b及一第二散热鳍片组2c相互组合而成,该些第一散热鳍片组2b具有复数散热鳍片21并且每一散热鳍片21具有至少一对折边211,该复数散热鳍片21通过该些折边211相互搭接组设,该些第
二散热鳍片组2c具有复数散热鳍片21并且每一散热鳍片21具有至少一对折边211,该复数散热鳍片21通过该些折边211相互搭接组设,并该第一散热鳍片组2b叠设于该第二散热鳍片组2c上方,并于该第一散热鳍片组2b及该第二散热鳍片组2c两者之间形成可供该复数热管4组装容设的该第一热管容置部2a。
44.该复数热管4具有一吸热段411,该吸热段411设于前述热管容置槽11,该复数热管4另一端沿水平方向延伸一冷凝段412并远端连接该散热装置2的该第一热管容置部第一热管容置部2a。
45.该铜质置入层3(coppere mbedding layer)设置于该热管容置槽11及该第一热管容置部2a的表面,通过该铜质置入层3的设置令该铝质基座1及该散热装置2与该复数热管4不经化镍处理即可直接进行焊接结合。
46.于该铜质置入层3与该复数热管4间设置该焊料层5,可进一步增加该铝质基座1与该复数热管4及该散热装置2结合性。
47.所述铜质置入层3的相反两面分别具有一植入面31及一接触面32(用以焊接结合的用),该植入面31咬嵌深入该热管容置槽11及该第一热管容置部2a的表面渗入或深入基座本体内,该接触面32作为该铜质置入层3的外露表面与该焊料层5或直接与另一同材质或异材质元件焊接结合。
48.该复数热管4的冷凝段412也可通过串接的方式贯穿所述散热装置2的第一热管容置部2a进行组合(松配或紧配),当采用松配合时该散热装置2的第一热管容置部2a与该复数热管4的冷凝段412结合处必须先设置该铜质置入层3,借此令该复数热管4与该散热装置2得以直接焊接结合,当所述冷凝段412与前述第一热管容置部2a呈紧配方式结合时,则该第一热管容置部2a紧迫该冷凝段412。
49.所述铜质置入层3是通过高速喷涂、印刷、电镀、或机械加工等方式设置于该铝质基座1与该复数热管4对应结合的部位,该铜质置入层3是铜片或铜箔或铜粉粒或液态铜经过机械加工(例如高压挤压)或表面处理制程(喷涂、电镀或印刷)附着在该热管容置槽11及该第一热管容置部2a的表面,且部分该铜质置入层3在附着形成的过程中会直接咬合或植入或嵌入该热管容置槽11及该第一热管容置部2a的表面。借由这样该置入该铜质置入层3不仅附着在该热管容置槽11及该第一热管容置部2a的表面,该植入面31更咬合或植入或嵌入该热管容置槽11及该第一热管容置部2a作为该铜质置入层3的根基,加强该铜质置入层3与该该热管容置槽11及该第一热管容置部2a的结合力,更能防止该铜质置入层3从该热管容置槽11及该第一热管容置部2a剥离脱落。
50.请参阅图3,是本发明的散热模块结构第二实施例的组合图,如图所示,本实施例与前述第一实施例部份结构相同故在此将不再赘述,惟本实施例与前述第一实施例的不同处在于本实施例更具有复数第二热管42及一第三散热鳍片组2d及一第四散热鳍片组2e,本实施例该复数第一热管41的冷凝段412水平延伸后与该该第一、二散热鳍片组2b、2c结合,而该些第二热管42的冷凝段422略高于该第一、二散热鳍片组2b、2c的高度后延伸与该第三散热鳍片组2d及该第四散热鳍片组2e进行组合,即该些第三、四散热鳍片组2d、2e设置于高于该第一、二散热鳍片组2b、2c,并该第四散热鳍片组2e与该第一散热鳍片组2b不相互接触,一第二热管容置部2f形成于该第三、四散热鳍片组2d、2e之间相对应但未相互结合处的一凹槽空间,该些第二热管42的该些吸热段421设置于该铝质基座1的热管容置槽11中,该
些冷凝段422设于前述第二热管容置部2f中。
51.所述第三、四散热鳍片组2d、2e也可设置于该第一、二散热鳍片组2b、2c的左、右两侧并与其水平并列,再通过部分的第二热管42的冷凝段422与其连接组设。
52.请参阅图4,是本发明的散热模块结构第三实施例的组合图,如图所示,本实施例与前述第一实施例部份结构相同故在此将不再赘述,惟本实施例与前述第一实施例的不同处在于本实施例的散热装置2是至少一散热器,并于其中央或下方处设置一第一热管容置部2a。
53.并为了制造及组装的方便将该散热装置2由一第一散热器2g及一第二散热器2h所组成,并该第一散热器2g具有一第一基座2ga并一侧延伸有复数散热鳍片2gb,该第二散热器2h具有一第二基座2ha并一侧延伸有复数散热鳍片2hb,并该第一散热器2g通过该第一基座2ga与该第二散热器2h的第二基座2ha相互贴设,该第一热管容置部2a设于该第一、二基座2ga、2ha之间,所述热管4具有复数第一热管41,该复数第一热管41的该些吸热段411设置于该铝质基座1的热管容置槽11中,该些冷凝段412设于前述第一热管容置部2a中。
54.请参阅图5,所述第一、二散热器2g、2h是铝材质,也可如第二实施例相同将该第三、四散热鳍片组2d、2e替换为一第三散热器2i及一第四散热器2j,再由第二热管42的冷凝段422连结接合,并无论该复数热管4的冷凝段与该第一、二、三、四散热鳍片组2b、2c、2d、2e或第一、二、三、四散热器2g、2h、2i、2j进行连接组设,又或者该第一、二、三、四散热鳍片组2b、2c、2d、2e相互对应连结组合的部位及该第一、二、三、四散热器2g、2h、2i、2j相互对应连接的部位,都必须先通过设置该铜质置入层3后使得以通过焊接的焊料层5将该些第一、二、三、四散热鳍片2b、2c、2d、2e进行连结结合以及将该第一、二、三、四散热器2g、2h、2i、2j相互间进行连结结合或与该复数热管4进行结合。
55.上述图4、图5实施例中该铝质基座1及该散热装置2呈相同高度或不同高度平行并列设置。
56.上述各实施例中,所述散热装置2与该第一、二热管41、42结合的方式可为紧配或松配的方式组合,当若以松配方式结合时,则该第一、二热管容置部2a、2f表面设有该铜质置入层3,令所述冷凝段与前述第一、二热管容置部2a、2f可直接焊接,所述冷凝段与前述第一、二热管容置部2a、2f紧配方式结合时,则该第一、二热管容置部2a、2f紧迫该冷凝段。
57.传统散热模块结构制造时,使用了铝质基座及热管与铝散热鳍片组或铝散热器进行结合,热管与该铝散热鳍片组及铝散热器或铝散热鳍片组与铝散热鳍片组接合时必须通过焊接的方式进行结合,但铝材质无法直接进行焊接,必须先行于该铝散热鳍片组与另一铝散热鳍片组欲焊接处及该铝散热鳍片组与该复数热管欲焊接的部位先以化学镀镍的方式沉积一镍镀层,令该复数热管与该铝质散热鳍片组或铝质基座得以顺利进行焊接结合,又因该化学镀镍的工法所产生的环境污染已渐渐被重视且被要求改善,故本发明提供一种取代传统化学镀镍的结构方法,通过于该欲焊接结合的部位以设置铜质置入层的方式,令该复数热管及铝散热鳍片组与该铝质基座得以顺利焊接结合,故本发明通过铜质置入层改善了传统散热模块组合必须使用化学镀镍所衍伸的各种污染及其他的缺失。
再多了解一些
本文用于企业家、创业者技术爱好者查询,结果仅供参考。