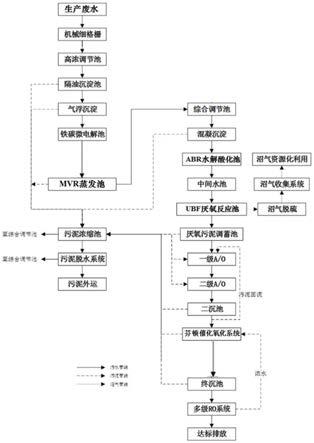
1.本发明属于环境保护技术领域中的污水处理行业,具体涉及一种头孢菌素类抗生素生产废水处理系统及处理工艺。
背景技术:
2.随着现代制药工艺不断发展的同时,制药废水的排放问题也越来越突出。其中,抗生素生产废水是一类高浓度、且含生物毒性物质的有机废水,由于其cod含量高、成分复杂、含多种难生化处理、难降解的有机化合物,b/c值一般为0.02-0.1,可生化性较差。欧美等国从20世纪40年代生产青霉素时就开始处理产生的废水,但一直未能有良好的解决办法。20世纪70年代起,发达国家将大宗常规药物生产向发展中国家转移,我国开始关注抗生素生产废水处理问题。
3.头孢类抗生素是目前广泛使用的一种抗生素,属于β-内酰胺类抗生素,是β-内酰胺类抗生素中的7-氨基头孢烷酸的衍生物。在我国,头孢类抗生素工业主要着重于低附加值的原料药、中间体的生产,生产过程原材料投入量大,产率低,废弃物产生量大。在生产链上,主要涉及到基础原料、头孢类抗生素中间体、头孢类抗生素原料药及制剂的生产,由此产生的高浓度废水主要为发酵废水、化学合成废水。由于基础原料主要通过生物发酵获得,所以主要污染环节是发酵液的提取结晶过程。在头孢类抗生素中间体、原料药及制剂的生产过程中则主要是采用化学反应、溶解-结晶、杀菌消毒等步骤获得最终的产品,废水中含有二甲基甲酰胺(dmf)、二氯甲烷、吡啶等可生化性极差的物质。因此,头孢菌素类抗生素生产废水具有cod高、成分复杂、可生化性差等特点。
4.专利文献201911068294.0公开了一种头孢制药的废水处理工艺,头孢废水依次经过母液调节池、mvc蒸发系统、冷却结晶脱水、缺氧反硝化池、好氧硝化池和沉淀池等处理单元。mvc浓缩液经冷却结晶脱水的结晶体外运处理,mvc蒸馏水进入生化系统,减轻了生化系统的运行负荷。但是,mvc蒸发系统无法完全降低废水生物毒性,废水可生化性提高幅度不明显,并且当水质水量发生变化,生化系统受到冲击时,废水将无法达标排放。
5.专利文献201810180806.1公开了一种头孢抗生素生产废水的处理方法,采用电渗析-mvr蒸发结晶-a/o生化处理相结合的方法,并且通过调整电渗析过程中浓缩浓水和生化淡水的电导率控制其含盐量。但是,本领域技术人员知晓,抗生素生产废水中含有较多的难降解有机物,cod含量较高,如果在预处理环节不对有机物进行部分降解,在后续水处理中很容易造成设备堵塞,减短处理设备使用年限。
6.专利文献200810162850.6公开了一种头孢合成制药生产废水的处理方法,由好氧接触氧化,缺氧水解酸化和膜生物反应器三部分构成,废水先由生物接触氧化池去除废水中可生化性较好的那部分有机物,而后在缺氧池中进行生物水解酸化。虽然生物接触氧化法对污染物的处理效果较好,但是抗生素制药废水可生化性很差,ph变化大,残余抗生素浓度较高,废水具有较强的抑菌性,使用来接触氧化的菌种难以培养和驯化,造成好氧或厌氧处理均有困难,致使许多现有的相关废水处理系统不能达标处理。
技术实现要素:
7.为了改善现有技术的缺陷,本发明提供一种头孢类抗生素生产废水处理系统,所述系统在预处理环节优选将mvr蒸发池替换为芬顿催化氧化系统,使在预处理环节就能有效降解废水中抗生素残留物和有机质,降低废水cod指数,有效缓解了后续生化处理过程中设备易堵塞问题。其次,本发明在常规废水处理工艺中加入了类芬顿反应系统,采用二沉池中的水制备类芬顿试剂,发明人预料不到的发现,通过控制反应发生器中的ph可以调节类芬顿试剂的产量,并且可以获得絮凝效果更好的类芬顿试剂。头孢类抗生素生产废水经过本发明所述的处理工艺处理后,出水水质符合《化学合成类制药工业水污染物排放标准》标准,实现无害排放。
8.第一方面,本发明提供一种头孢类抗生素生产废水处理系统,所述系统包括预处理单元和生化处理单元。其中,所述预处理单元依次包括机械细格栅、高浓调节池、隔油沉淀池、气浮沉淀池、铁碳微电解池、芬顿催化氧化系统或mvr蒸发池。
9.优选的,所述预处理单元依次包括机械细格栅、高浓调节池、隔油沉淀池、气浮沉淀池、铁碳微电解池、芬顿催化氧化系统。
10.其中,机械细格栅对生产废水进行初步过滤,高浓调节池进行均质均量调节,隔油沉淀池能对废水中的有机溶剂进行物理分离,气浮沉淀池通过加入复合絮凝剂去除分子量较大的悬浮物,铁碳微电解池利用fe
2
、fe
3
与废水中有色物质发生氧化反应,去除废水中分散的微小颗粒和有机大分子。mvr蒸发池对废水进行浓缩减量。芬顿催化氧化系统通过加入芬顿试剂对水中有机物质进行催化氧化反应,降解废水中残留抗生素和有机物,提高废水可生化性。
11.优选的,所述芬顿催化氧化系统中加入的废水质量0.1-0.2%的芬顿试剂,所述芬顿试剂为使用pvp或pam进行表面处理的fe/sba-15和双氧水按照体积比1:(2-3)混合得到。更优选的,所述芬顿试剂为使用pam进行表面处理的fe/sba-15和双氧水按照体积比1:3混合得到
12.所述表面处理的fe/sba-15通过如下方法制备得到:将fe/sba-15加入到0.1-0.5g/ml pvp或pam水溶液中,密封浸泡4-6小时,离心除上清液,将沉淀烘干分散,制备得到表面处理的fe/sba-15,分别命名为fe/sba-15@pvp和fe/sba-15@pam。
13.本发明申请人在先发明专利cn202110071953.7中公开的芬顿试剂为fe/sba-15和双氧水,在后续实际工作中,发明人发现sba-15虽然具有较好的负载能力,但将fe/sba-15加入废水中进行催化氧化的效率并不高,因为fe/sba-15容易发生聚集。为了改善这一现状,在本发明中,发明人将fe/sba-15使用聚乙烯吡咯烷酮(pvp)或聚丙烯酰胺(pam)进行表面处理,有效改善原来芬顿试剂易聚集沉淀的问题,增加芬顿试剂催化氧化效率。pvp和pam均是一种非离子型高分子聚合物,能降低原来芬顿试剂的表面张力,减缓其聚集沉淀的速度。另外,pam本来就具有絮凝作用,所以用pam表面处理的fe/sba-15作为芬顿试剂使用效果更好。
14.本发明所述的头孢类抗生素生产废水处理系统中生化处理单元依次包括综合调节池、混凝沉淀池、abr水解酸化池、中间水池、ubf厌氧反应池、厌氧污泥调蓄池、一级a/o好氧池、二级a/o好氧池、二沉池、芬顿催化氧化系统、终沉池、多级ro系统。
15.其中,综合调节池进行水质调节,使出水均匀,混凝沉淀池对水中大分子物质进一
步净化,污水进入abr水解酸化池在水解细菌产酸菌作用下对有机大分子进行降解,中间水池用于对浓度和温度进行调整,ubf厌氧反应池进行厌氧反应,厌氧污泥调蓄池用于进行泥水分离,一级a/o好氧池和二级a/o好氧池用于去除可生化降解的有机物和氨氮,二沉池进行沉淀,芬顿催化氧化系统用于再次将污水进行催化氧化,多级ro系统可对水进行过滤。
16.优选的,在二沉池后设置类芬顿反应系统,所述类芬顿反应系统包括类芬顿反应池、出水管、反应发生器、产物储存罐、产物输送管。
17.所述类芬顿反应系统工作方式为:通过出水管将二沉池的水注入反应发生器中,水量为反应发生器体积的1/2-2/3,向反应发生器中加入浓度为450-500g/l硫酸亚铁溶液,再向反应发生器中加入无机盐使反应发生器中(nh4)2so4、k2hpo4和mgso4浓度为0.1-1g/l,引入氧化亚铁硫杆菌开始反应,控制反应器中溶解氧在4-5ppm之间,温度为30-35℃,用硫酸调节反应体系ph为1.5-4,直至检测反应发生器中fe
2
浓度低于0.1%时为一个循环反应,继续添加硫酸亚铁溶液进行下一个循环反应。将反应器底部的沉淀排入产物储存罐中静置熟化3-5天,向产物储存罐中加入沉淀体积3-4倍的双氧水混合均匀,得到类芬顿试剂,通过产物输送管泵入类芬顿反应池。
18.经检测,通过上述方法制备得到的类芬顿试剂具有显著的类芬顿氧化混凝效果。发明人预料不到的发现,反应发生器中ph值的改变会显著影响类芬顿试剂的产量和类芬顿试剂的氧化混凝效果。目前大多数现有技术都会控制反应体系ph值在1.5-2之间,制备得到的类芬顿试剂量较少,且氧化混凝效果并不理想。本发明将反应体系ph控制在3-4之间,非常有利于类芬顿试剂的形成,并且得到的类芬顿试剂孔隙率大,絮凝效果好。
19.优选的,所述废水处理系统还包括污泥处理单元,所述污泥处理单元依次包括污泥浓缩池和污泥脱水系统。在预处理单元中,隔油沉淀池、气浮沉淀池、芬顿催化氧化系统产生的污泥流入污泥浓缩池。在生化处理单元中,厌氧污泥调蓄池、二沉池、类芬顿反应系统、芬顿催化氧化系统、终沉池中产生的污泥流入污泥浓缩池。污泥在污泥浓缩池浓缩后进入污泥脱水系统中进行脱水,上清液/滤液回流至综合调节池,形成的污泥外运处理。
20.优选的,所述废水处理系统还包括沼气处理单元,所述沼气处理单元依次包括沼气脱硫系统和沼气收集系统。从ubf厌氧反应池中产生的沼气进入沼气脱硫系统中进行脱硫,后进入沼气收集系统,收集的沼气再资源化利用。
21.第二方面,本发明提供一种头孢类抗生素生产废水处理工艺,包括如下处理过程:
22.(1)生产废水先经过机械细格栅进行初步过滤,出水流入高浓调节池进行均质均量调整;
23.(2)高浓调节池出水进入隔油沉淀池对废水中的有机溶剂进行处理,出水进入气浮沉淀池,向气浮沉淀池中加入复合絮凝剂去除悬浮物;
24.(3)气浮沉淀池出水进入铁碳微电解池对废水中的发色基团进行氧化,去除废水中分散的微小颗粒和有机大分子;
25.(4)铁碳微电解池出水进入mvr蒸发池进行浓缩减量处理,或者气浮沉淀池出水进入芬顿催化氧化系统中进行催化氧化;
26.(5)出水进入综合调节池进行水质调节,使出水均匀;
27.(6)综合调节池出水进入混凝沉淀池,加入混凝沉淀剂对水中大分子物质进一步净化;
28.(7)混凝沉淀池出水进入abr水解酸化池,在水解细菌产酸菌作用下对有机大分子进行降解;
29.(8)abr水解酸化池出水进入中间水池对浓度和温度进行调整;
30.(9)中间水池出水进入ubf厌氧反应池进行厌氧反应,出水进入厌氧污泥调蓄池进行泥水分离;
31.(10)厌氧污泥调蓄池出水分别经过一级a/o好氧池和二级a/o好氧池去除可生化降解的有机物和氨氮;
32.(11)出水进入二沉池沉淀,上清液流入芬顿催化氧化系统再次进行催化氧化;
33.(12)催化氧化后出水进行终沉池进行沉淀,上清液经过多级ro系统进行过滤,检测出水水质,达标排放。
34.优选的,所述步骤(2)气浮沉淀池中加入的复合絮凝剂为碳粉、铁粉、氯化铝、聚合氯化铝按照质量比为2:3:8:1复配得到,复合絮凝剂的加入量是生产废水质量的0.2%。
35.优选的,所述步骤(3)中铁碳微电解池,分为铁碳微电解池i和铁碳微电解池ii,铁碳微电解池i中填料为铁屑和焦炭,质量比为3:1-2;铁碳微电解池ii中填料为铁屑、铜和焦炭,质量比为3:(0.5-1):(1-2)。
36.在本发明的优选实施方式中,铁碳微电解池i中填料为铁屑和焦炭的质量比为3:2,ph为3-4;铁碳微电解池ii中填料为铁屑、铜粒和焦炭的质量比为3:0.5:2,ph为4-5。
37.优选的,所述步骤(4)为铁碳微电解池出水进入芬顿催化氧化系统中进行催化氧化。
38.优选的,所述步骤(6)中混凝沉淀系统中加入的混凝沉淀剂是聚合氯化铝和氧化钙按照4:1复配得到,混凝沉淀剂的加入量是废水质量的0.3%。
39.步骤(4)和步骤(11)使用的芬顿试剂相同,步骤(11)芬顿试剂的加入量是步骤(4)的2-3倍。
40.优选的,所述步骤(11)中二沉池的上清液进入类芬顿反应池,少量上清液通过出水管流入反应发生器,反应器中的沉淀进入产物储存罐,熟化,加入双氧水制备得到类芬顿试剂,通过产物输送管泵入类芬顿反应池进行氧化混凝反应,类芬顿反应池出水再流入芬顿催化氧化系统中进行催化氧化。
41.本发明提供的头孢类抗生素生产废水处理系统的优势如下:
42.1,常规的污水处理厂在预处理过程中选择使用mvr蒸发池对废水进行浓缩减量处理,但是对于头孢类抗生素生产废水并不适用。因为抗生素生产废水cod含量高,里面还有较多抗生素残留物质,如果直接进行浓缩减量特别容易对后续净化设备造成堵塞和腐蚀问题。在本发明中,发明人在废水预处理环节中将mvr蒸发系统替换为芬顿催化氧化系统,使用羟基自由基强氧化剂对残留抗生素和有机物质先进行氧化,大大减小了后续设备负荷,提高废水可生化性。
43.2,常规使用的芬顿试剂为铁负载于载体上制备得到,如fe/sba-15,但发明人发现fe/sba-15在实际使用过程中容易发生聚集沉淀,催化氧化效率不高。发明人使用非离子高分子聚合物pvp或pam对fe/sba-15进行表面处理,不仅不会影响原来芬顿试剂的催化氧化活性,而且能显著改善易聚集的缺点,提高其催化氧化效率。
44.3,本发明的发明人在原有生化处理工艺中创造性的加入类芬顿反应系统,最大限
度的利用污水处理厂原有的水、曝气系统等资源,自行制备得到类芬顿试剂,进一步对废水中没有处理的悬浮物等进行深度处理。并且,发明人预料不到的发现,通过控制类芬顿试剂反应体系的ph能制备得到氧化混凝效果更好的类芬顿试剂,同时增加类芬顿试剂的产量。
附图说明
45.图1废水处理系统示意图;
46.图2预处理流程改良的废水处理系统示意图;
47.图3生化处理流程改良的废水处理系统示意图。
具体实施方式
48.下面将对本发明实施例中的技术方案进行清楚、完整地描述,显然,所描述的实施例仅是本发明的部分实施例,而不是全部。基于本发明中的实施例,本领域普通技术人员在没有做出创造性劳动前提下所获得的所有其他实施例,都属于本发明保护的范围。
49.复合絮凝剂的制备
50.本发明实施例中使用的复合絮凝剂为碳粉、铁粉、氯化铝、聚合氯化铝按照质量比为2:3:8:1复配得到,复合絮凝剂的加入量是废水质量的0.2%。
51.铁碳微电解池的设置
52.本发明实施例中铁碳微电解池的设置为:铁碳微电解池i中填料为铁屑和焦炭的质量比为3:2,ph为3;铁碳微电解池ii中填料为铁屑、铜粒和焦炭的质量比为3:0.5:2,ph为4。
53.混凝沉淀剂的制备
54.本发明实施例中使用的混凝沉淀剂是聚合氯化铝和氧化钙按照4:1复配得到,混凝沉淀剂的加入量是入水质量的0.3%。
55.芬顿试剂的制备
56.s1:将购买的pvp或pam加水分别配制成质量浓度为0.5g/ml的水溶液,加入液体体积2/3的fe/sba-15密封浸泡6小时,500rpm离心除去上清,烘干沉淀,分散,得到fe/sba-15@pvp和fe/sba-15@pam;
57.s2:分别取fe/sba-15@pvp和fe/sba-15@pam,分别加入3倍体积的双氧水,备用。在本发明的具体实施例中,芬顿试剂均是现用现配。
58.某新建头孢类制药厂废水水质如下表1,废水排放量为600m3/d,废水主要来自工艺废水和碱洗塔排水。本发明实施例中均以所述制药废水为对象进行处理。
59.表1
[0060][0061]
头孢类抗生素生产废水的预处理过程
[0062]
实施例1
[0063]
所述制药生产废水的预处理流程为:生产废水—机械细格栅—高浓调节池—隔油
沉淀池—气浮沉淀池—铁碳微电解池—mvr蒸发池。
[0064]
s1:生产废水先经过机械细格栅进行初步过滤,出水流入高浓调节池进行均质均量调整;
[0065]
s2:高浓调节池出水进入隔油沉淀池对废水中的有机溶剂进行处理,出水进入气浮沉淀池,向气浮沉淀池中加入复合絮凝剂去除悬浮物;
[0066]
s3:气浮沉淀池出水进入铁碳微电解池对废水中的发色基团进行氧化,去除废水中分散的微小颗粒和有机大分子;
[0067]
s4:铁碳微电解池出水进入mvr蒸发池进行浓缩减量处理,检测出水水质。
[0068]
实施例2
[0069]
所述制药生产废水的预处理流程为:生产废水—机械细格栅—高浓调节池—隔油沉淀池—气浮沉淀池—铁碳微电解池—芬顿催化氧化系统。
[0070]
s1:生产废水先经过机械细格栅进行初步过滤,出水流入高浓调节池进行均质均量调整;
[0071]
s2:高浓调节池出水进入隔油沉淀池对废水中的有机溶剂进行处理,出水进入气浮沉淀池,向气浮沉淀池中加入复合絮凝剂去除悬浮物;
[0072]
s3:气浮沉淀池出水进入铁碳微电解池对废水中的发色基团进行氧化,去除废水中分散的微小颗粒和有机大分子;
[0073]
s4:铁碳微电解池水进入芬顿催化氧化系统,加入废水质量0.1%的芬顿试剂(fe/sba-15@pvp 3倍体积的双氧水)进行催化氧化,检测出水水质。
[0074]
实施例3
[0075]
制药生产废水的预处理流程同实施例2,区别仅在于步骤s4,具体为铁碳微电解池出水进入芬顿催化氧化系统,加入废水质量0.1%的芬顿试剂(fe/sba-15@pam 3倍体积的双氧水)进行催化氧化,检测出水水质。
[0076]
对比实施例1
[0077]
制药生产废水的预处理流程同实施例2,区别仅在于步骤s4,具体为铁碳微电解池出水进入芬顿催化氧化系统,加入废水质量0.1%的芬顿试剂(fe/sba-15 3倍体积的双氧水)进行催化氧化,检测出水水质。
[0078]
头孢类抗生素生产废水预处理出水检测
[0079]
上述预处理工艺的出水水质情况如下表所示:
[0080]
表2
[0081]
[0082][0083]
根据上表统计的与处理后出水水质情况可以看出,采用常规的mvr蒸发池进行废水预处理后,出水中的混悬物(ss)的改善程度很小,对于氯化物和硫酸根的减量也较小。将mvr蒸发池替换为芬顿催化氧化系统后,预处理实质可生化性明显增强,cod等有机质的降解明显,对悬浮物的减量也非常显著。通过实施例2和实施例3的数据可以看到,与fe/sba-15 双氧水作为芬顿试剂相比,采用pvp或pam表面处理的fe/sba-15 双氧水催化氧化效果更好。其中,使用pam进行表面处理的芬顿试剂效果最好,这是因为pam本身就具有絮凝作用,在絮凝大分子有机质和悬浮物时效果明显。
[0084]
头孢类抗生素生产废水的生化处理过程
[0085]
经过预处理流程优化,本发明后续生化处理过程均在实施例3所示的预处理流程基础上进行。
[0086]
实施例3a
[0087]
所述制药生产废水的生化处理流程为:预处理出水—综合调节池—混凝沉淀池—abr水解酸化池—中间水池—ubf厌氧反应池—厌氧污泥调蓄池—一级a/o好氧池—二级a/o好氧池—二沉池—芬顿催化氧化系统—终沉池—多级ro系统。
[0088]
s1:经过预处理的水进入综合调节池进行水质调节,使出水均匀;
[0089]
s2:综合调节池出水进入混凝沉淀池,加入混凝沉淀剂对水中大分子物质进一步净化;
[0090]
s3:混凝沉淀池出水进入abr水解酸化池,在水解细菌产酸菌作用下对有机大分子进行降解;
[0091]
s4:abr水解酸化池出水进入中间水池对浓度和温度进行调整;
[0092]
s5:中间水池出水进入ubf厌氧反应池进行厌氧反应,出水进入厌氧污泥调蓄池进行泥水分离;
[0093]
s6:出水分别经过一级a/o好氧池和二级a/o好氧池去除可生化降解的有机物和氨氮;
[0094]
s7:出水进入二沉池进行沉淀,上清液流入芬顿催化氧化系统,加入废水质量0.2%的芬顿试剂(fe/sba-15@pam 3倍体积的双氧水)再次进行催化氧化;
[0095]
s8:出水进行终沉池进行沉淀,上清液经过多级ro系统进行过滤,检测出水水质。
[0096]
实施例3b
[0097]
所述制药生产废水的生化处理流程为:预处理出水—综合调节池—混凝沉淀池—abr水解酸化池—中间水池—ubf厌氧反应池—厌氧污泥调蓄池—一级a/o好氧池—二级a/o好氧池—二沉池—类芬顿反应系统—芬顿催化氧化系统—终沉池—多级ro系统。类芬顿反应系统包括类芬顿反应池、出水管、反应发生器、产物储存罐、产物输送管。
[0098]
s1:经过预处理的水进入综合调节池进行水质调节,使出水均匀;
[0099]
s2:综合调节池出水进入混凝沉淀池,加入混凝沉淀剂对水中大分子物质进一步净化;
[0100]
s3:混凝沉淀池出水进入abr水解酸化池,在水解细菌产酸菌作用下对有机大分子进行降解;
[0101]
s4:abr水解酸化池出水进入中间水池对浓度和温度进行调整;
[0102]
s5:中间水池出水进入ubf厌氧反应池进行厌氧反应,出水进入厌氧污泥调蓄池进行泥水分离;
[0103]
s6:出水分别经过一级a/o好氧池和二级a/o好氧池去除可生化降解的有机物和氨氮;
[0104]
s7:出水进入二沉池进行沉淀,上清液流入类芬顿反应池,部分上清液通过出水管流入反应发生器,向反应发生器中加入浓度为500g/l硫酸亚铁溶液,再向反应发生器中加入无机盐使反应发生器中(nh4)2so4、k2hpo4和mgso4浓度为0.5g/l,引入氧化亚铁硫杆菌开始反应,控制反应器中溶解氧在4-5ppm之间,温度为30℃,用硫酸调节反应体系ph为1.5,直至检测反应发生器中fe
2
浓度低于0.1%时完成一个循环反应,将反应器底部的沉淀排入产物储存罐中静置熟化3天,向产物储存罐中加入沉淀3倍体积的双氧水混合均匀,得到类芬顿试剂,通过产物输送管泵入类芬顿反应池进行氧化混凝反应;
[0105]
s8:类芬顿反应池的出水流入芬顿催化氧化系统,加入废水质量0.2%的芬顿试剂(fe/sba-15@pam 3倍体积的双氧水)再次进行催化氧化;
[0106]
s9:出水进行终沉池进行沉淀,上清液经过多级ro系统进行过滤,检测出水水质。
[0107]
实施例3c
[0108]
抗生素生产废水的生化处理流程同实施例3b,区别仅在于步骤s7,用硫酸调节反应发生器中的反应体系ph为3,当反应器中fe
2
浓度低于0.1%时完成一个循环反应,将反应器底部的沉淀排入产物储存罐中静置熟化3天,向产物储存罐中加入沉淀3倍体积的双氧水混合均匀,得到类芬顿试剂,通过产物输送管泵入类芬顿反应池进行氧化混凝反应。剩余步骤均与实施例3b相同,经过多级ro系统过滤后检测出水水质。
[0109]
实施例3d
[0110]
抗生素生产废水的生化处理流程同实施例3b,区别仅在于步骤s7,用硫酸调节反应发生器中的反应体系ph为3.5,当反应器中fe
2
浓度低于0.1%时完成一个循环反应,将反应器底部的沉淀排入产物储存罐中静置熟化3天,向产物储存罐中加入沉淀3倍体积的双氧水混合均匀,得到类芬顿试剂,通过产物输送管泵入类芬顿反应池进行氧化混凝反应。剩余步骤均与实施例3b相同,经过多级ro系统过滤后检测出水水质。
[0111]
实施例3e
[0112]
抗生素生产废水的生化处理流程同实施例3b,区别仅在于步骤s7,用硫酸调节反应发生器中的反应体系ph为4,当反应器中fe
2
浓度低于0.1%时完成一个循环反应,将反应器底部的沉淀排入产物储存罐中静置熟化3天,向产物储存罐中加入沉淀3倍体积的双氧水混合均匀,得到类芬顿试剂,通过产物输送管泵入类芬顿反应池进行氧化混凝反应。剩余步骤均与实施例3b相同,经过多级ro系统过滤后检测出水水质。
[0113]
头孢类抗生素生产废水生化处理出水检测
[0114]
实施例3a-实施例3e所示的生化处理工艺的出水水质情况如下表所示:
[0115]
表3
[0116][0117]
根据上表数据可以看出,经过本发明提供的生化处理工艺进行处理后,废水中的有机质、混悬物、无机盐都明显改善,符合排放标准。其中,当在二沉池后增加类芬顿反应系统后对出水水质有了进一步提高,其中表现最明显的就是废水中混悬物量显著减少,且当反应发生器中ph值为3-4时,制备得到的类芬顿试剂效果更好。发明人还惊奇的发现,当反应发生器中ph值为3-4,与ph为1.5时相比,产生的类芬顿试剂的量更多。此外,发明人还发现实际上反应体系中除了氧化亚铁硫杆菌外还有其他产气菌,当ph为3-4时,产气菌更活跃,在沉淀累积时中间有更多气体,因此制备得到的类芬顿试剂孔隙率较大,絮凝效果更好。
[0118]
最后应说明的是:以上各实施例仅用以说明本发明的技术方案,而非对其限制。本领域的普通技术人员应当理解:其依然可以对前述实施例所记载的技术方案进行修改,或者对其中部分或者全部技术特征进行等同替换;而这些修改或者替换,并不使相应技术方案的本质脱离本发明各实施例技术方案的范围。
再多了解一些
本文用于企业家、创业者技术爱好者查询,结果仅供参考。