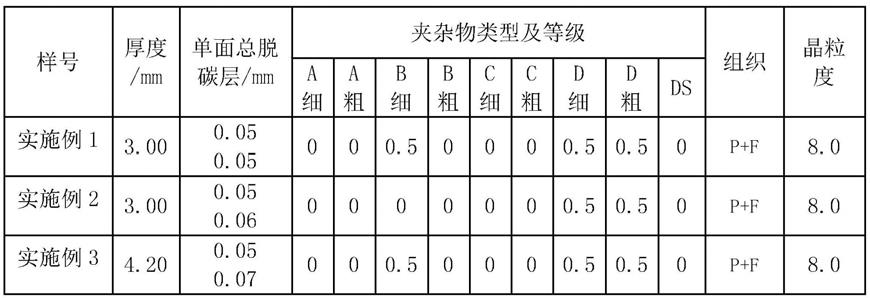
1.本发明涉及钢铁生产技术领域,特别是涉及一种弹性挡圈用钢热轧钢带的制备方法。
背景技术:
2.弹性挡圈又称卡簧,分为轴用弹性挡圈和孔用弹性挡圈,安装于槽轴上,用作固定零部件的轴向运动。
3.c67s弹性挡圈用钢是高碳钢,一般采用超高功率电弧炉冶炼,生产节奏快,采用偏心炉底留钢留渣出钢,其缺点是冶炼终点钢水氧含量难控制,氧含量波动大,出钢脱氧合金化时合金元素的收得率不稳定,到达lf精炼炉成分波动大,出钢口使用后期时出钢易下渣回p,lf精炼炉造还原渣和目标成分控制困难,同时钢水初始氧含量高,初始钢水夹杂物含量也高。同时,采用电炉生产大方坯-开坯-带钢轧制二火材工艺生产成本高。
技术实现要素:
4.本发明针对上述技术问题,克服现有技术的缺点,提供一种弹性挡圈用钢热轧钢带的制备方法,为提高市场竞争力,对生产工艺进行优化,采用100t转炉-lf-rh-七机七流小方坯-带钢一火材工艺生产,其中转炉采用高拉碳工艺、防止钢水过氧化,采用滑板挡渣出钢,提高转炉出钢脱氧合金化时合金的收得率,实现lf炉初始钢水成分稳定控制;lf精炼造白渣时间10min以内,白渣保持时间30min以上,终点成分精确调整实现窄成分控制;rh真空处理后软ar时间长,保证夹杂物充分上浮去除;连铸采用水模试验结构最优“稳流器 斜孔导流墙 开孔挡坝”的七机七流整体水口中间包,钢水在中间包停留时间长、死区少夹杂物上浮充分、成分和温度均匀性好的中间包结构。大包开浇前中包吹ar处理,防止钢水二次氧化。包括转炉冶炼、lf精炼、rh真空处理、连铸、加热、除鳞、轧制、冷却和卷取工序,
5.(1)转炉冶炼
6.采用转炉冶炼钢水,向炉内加入石灰和白云石,控制供氧量,采用高拉碳工艺,防止钢水过氧化,采用滑板挡渣出钢,控制出钢时钢水中c含量≥0.08%,p含量≤0.010%,钢水的氧含量≤400ppm;出钢加入300kg改性精炼渣;
7.(2)lf精炼
8.向炉内加入合金进行钢水合金化,加入高纯碳化硅进行扩散脱氧,加入石灰和萤石进行造渣,精炼时间40~70min,白渣保持时间30~50min,渣系采用cao-sio2-al2o3,二元碱度控制在2.0-3.0,精炼过程中根据炉渣碱度和流动性适当补加石灰和萤石;
9.(3)rh真空处理
10.真空度≤1mbar,处理时间10min以上,破真空后喂纯钙棒包心线100m,对夹杂物进行变形处理,喂纯钙棒包心线后软吹ar时间20min以上,保证夹杂物充分上浮去除;
11.(4)连铸
12.连铸采用水模试验结构最优稳流器 斜孔导流墙 开孔挡坝的七机七流整体水口
中间包,长水口ar封全保护浇铸,同时大包开浇前中间包吹ar处理,防止钢水二次氧化;使用高碳钢保护渣,中包过热度10-30℃,150*150mm连铸拉速2.0-2.2m/min、150*220mm连铸拉速1.3-1.5m/min,采用恒拉速浇铸工艺,使用结晶器和末端电磁搅拌,浸入式水口插入深度120-150mm;结晶器液面自动控制,液面波动≤
±
6mm;
13.(5)加热
14.采用三段连续推钢式加热炉加热小矩坯,加热段温度为1060~1160℃,均热段温度为1060~1120℃,小矩坯断面温差小于30℃;
15.(6)轧制
16.将加热后的小矩坯经高压水除鳞后进行轧制,包括粗轧、中精轧和终轧,粗轧采用往复式多道次轧制,开轧温度1020~1130℃;中精轧开轧温度950~1020℃,并通过agc系统控制厚度公差;终轧温度890~960℃;
17.(7)冷却和卷取
18.将轧制后的钢带空冷、卷取,卷取温度630~710℃。
19.本发明进一步限定的技术方案是:
20.前所述的一种弹性挡圈用钢热轧钢带的制备方法,步骤(1)中冶炼工序结束时,钢水的初始成分达到目标成分下限的70%~90%。
21.前所述的一种弹性挡圈用钢热轧钢带的制备方法,步骤(2)中lf精炼按钢水的目标成分进行微调,钢水的目标成分以重量百分比含量计为:c:0.65%~0.73%、si:0.15%~0.35%、mn:0.60%~0.90%、p≤0.015%、s≤0.010%、cr≤0.40%、ni≤0.40%、cu≤0.20%、mo≤0.10%、alt:0.010%~0.070%,其余为铁和微量元素。
22.前所述的一种弹性挡圈用钢热轧钢带的制备方法,步骤(2)中加入的合金为高碳锰铁合金和硅铁合金。
23.前所述的一种弹性挡圈用钢热轧钢带的制备方法,步骤(2)中加入的增碳剂为高纯石墨碳材。
24.前所述的一种弹性挡圈用钢热轧钢带的制备方法,步骤(5)中加热气氛为还原性气氛,控制烟气残氧量≤3%。
25.前所述的一种弹性挡圈用钢热轧钢带的制备方法,步骤(6)中精轧的厚度公差小于0.05mm。
26.本发明的有益效果是:
27.(1)本发明能够使弹性挡圈用钢的纯净度和组织均匀性得到极大改善,表面脱碳层少,提高弹性挡圈用钢的弹性;
28.(2)本发明中转炉冶炼工序通过控制供氧量,采用高拉碳工艺,防止钢水过氧化;采用滑板挡渣出钢,极大地减少下渣量,使钢水氧化性大大降低,既可以提高合金元素收得率,减少增碳剂用量,降低生产成本,又可减少钢中夹杂物含量,提高钢水纯净度;
29.(3)本发明中lf精炼采用高碳锰铁合金和硅铁合金进行钢水合金化,以高纯碳化硅或高纯石墨碳材进行脱氧,采用石灰和萤石渣系达到钢水快速脱s的效果,同时造泡沫渣实现渣埋弧操作,减少钢液的吸n量;
30.(4)本发明中连铸工序采用小方坯、小矩坯连铸,采用水模试验中包流场最优“稳流器 斜孔导流墙 开孔挡坝”七机七流小方坯连铸机浇铸,钢水混匀时间缩短,停留时间增
加,而且钢水在每个流的停留时间接近,夹杂物有效上浮时间增加,进而提高了浇铸钢坯的纯净度;
31.(5)本发明中加热工序采用还原性气氛下低温慢烧、高温快烧,控制烟气残氧量≤3%,减少铸坯表面脱碳;
32.(6)本发明所制得的钢带成品夹杂物含量低0.5级以内,化学成分波动小,不同批次材料性能稳定,成品表面脱碳少,组织细小均匀晶粒度8.0级,韧性好,加工弹性挡圈寿命高,在紧固件等领域具有非常广阔的推广前景。
附图说明
33.图1为七流中间包尺寸示意图。
具体实施方式
34.实施例1
35.一种c67s弹性挡圈用钢的制备方法,依次包括转炉冶炼、lf精炼、rh真空处理、连铸、加热、除鳞、轧制、冷却和卷取工序,具体步骤如下:
36.(1)转炉冶炼:转炉中加入25吨废钢和100吨铁水,冶炼钢水的过程中加入活性石灰4720kg、石灰石360kg和白云石1800kg,控制供氧量为5800m3,采用高拉碳工艺,使用滑板挡渣出钢,控制出钢时钢水中c含量0.15%,p含量0.010%,钢水的氧含量260ppm;转炉出钢过程中加入高碳锰铁700kg、硅铁170kg、高纯石墨碳材500kg、铝块110kg、石灰500kg、改性精炼渣300kg,钢水的初始成分达到目标成分下限的80%。
37.(2)lf精炼:向lf精炼炉内加入硅锰160kg、高碳铬铁合金200kg、高纯石墨碳材150kg进行钢水合金化,少量多批次加入高纯碳化硅120kg进行扩散脱氧,加入石灰250kg进行造渣,控制精炼时间50min,白渣保持时间在40min,控制炉渣二元碱度2.88;钢水的目标成分以重量百分比含量计为:c:0.68%、si:0.24%、mn:0.65%、p:0.015%、s:0.002%、cr:020%、ni:0.05%、cu:0.03%,alt:0.022%其余为铁和微量元素。
38.(3)rh真空处理:lf精炼的钢水成分合格后,进行rh真空脱气,真空度0.46mbar,处理时间10min,破真空后加大包覆盖剂,软吹氩气搅拌45min,静搅时渣面微动不见光。
39.(4)连铸:钢水rh真空处理后,吊包到小方坯6#连铸机浇铸,连铸采用水模试验结构最优“稳流器 斜孔导流墙 开孔挡坝”的七机七流整体水口中间包,采用整体水口连铸机、长水口ar封全保护浇铸,同时大包开浇前中间包吹ar处理,防止钢水二次氧化。如图1所示,过热度21℃,拉速1.40m/min恒拉速进行浇铸制得尺寸150mm
×
220mm的小矩坯。其中比水量为0.60l/kg,结晶器电磁搅拌频率3.50hz、电流350a;末端电磁搅拌频率8hz、电流300a;铸坯中心偏析、中心缩孔和中心疏松均低于1.0级。该中间包钢水停留时间长,每个流钢水停留时间接近,成分和温度均匀,死区体积小,非金属夹杂物能够充分碰撞长大上浮去除。
40.(5)加热:将150mm
×
220mm的小矩坯装入三段连续推钢式加热炉中,在还原性气氛中加热,烟气残氧量2.1%。加热炉加热段温度控制在1120℃,均热段温度控制在1070℃,钢坯断面温差小于30℃。
41.(6)轧制:将加热后的150mm
×
220mm小矩坯经高压水除鳞后送入轧制工序,包括粗
轧、中精轧和终轧。其中粗轧采用往复式φ650和φ500粗轧机组多道次轧制,开轧温度1085℃,经过6道次粗轧后中精轧;中精轧全线共计10架轧机,前3架中轧,后7架精轧,其形式为立-平-平-立-平-平-平-平-平-平,配备agc全自动测厚仪,控制厚度公差,中精轧开轧温度990℃;通过控制终轧速度来控制终轧温度,终轧温度870℃,终轧速度6m/s,然后经扭转,蛇形震荡抵平板链运输和冷却。
42.(7)冷却和卷取:将轧制后的钢带空冷,检查表面质量和尺寸公差,进行卷取、打包和入库,卷取温度680℃。
43.实施例2
44.一种c67s弹性挡圈用钢的制备方法,依次包括转炉冶炼、lf精炼、rh真空处理、连铸、加热、除鳞、轧制、冷却和卷取工序,具体步骤如下:
45.(1)转炉冶炼:转炉中加入26吨废钢和109吨铁水,冶炼钢水的过程中加入活性石灰4350kg、石灰石500kg和白云石2400kg,控制供氧量为6200m3,采用高拉碳工艺,使用滑板挡渣出钢,控制出钢时钢水中c含量0.23%,p含量0.008%,钢水的氧含量280ppm;转炉出钢过程中加入高碳锰铁710kg、硅铁175kg、高纯石墨碳材450kg、铝块110kg、石灰505kg、改性精炼渣300kg,钢水的初始成分达到目标成分下限的75%。
46.(2)lf精炼:向lf精炼炉内加入硅锰180kg、高碳铬铁合金195kg、高纯石墨碳材200kg进行钢水合金化,少量多批次加入高纯碳化硅120kg进行扩散脱氧,加入石灰300kg进行造渣,控制精炼时间50min,白渣保持时间在40min,控制炉渣二元碱度2.41;钢水的目标成分以重量百分比含量计为:c:0.69%、si:0.24%、mn:0.66%、p:0.012%、s:0.004%、cr:018%、ni:0.06%、cu:0.03%,alt:0.026%其余为铁和微量元素。
47.(3)rh真空处理:lf精炼的钢水成分合格后,进行rh真空脱气,真空度0.39mbar,处理时间10min,破真空后加大包覆盖剂,软吹氩气搅拌35min,静搅时渣面微动不见光。
48.(4)连铸:钢水rh真空处理后,吊包到小方坯6#连铸机浇铸,连铸采用水模试验结构最优“稳流器 斜孔导流墙 开孔挡坝”的七机七流整体水口中间包,长水口ar封全保护浇铸,同时大包开浇前中间包吹ar处理,防止钢水二次氧化,如图1所示,过热度21℃,拉速1.40m/min恒拉速进行浇铸制得尺寸150mm
×
220mm的小矩坯。其中比水量为0.60l/kg,结晶器电磁搅拌频率3.00hz、电流300a;末端电磁搅拌频率8hz、电流450a;铸坯中心偏析、中心缩孔和中心疏松均低于1.0级。该中间包钢水停留时间长,每个流钢水停留时间接近,成分和温度均匀,死区体积小,非金属夹杂物能够充分碰撞长大上浮去除。
49.(5)加热:将150mm
×
220mm的小矩坯装入三段连续推钢式加热炉中,在还原性气氛中加热,烟气残氧量2.1%。加热炉加热段温度控制在1115℃,均热段温度控制在1085℃,钢坯断面温差小于30℃。
50.(6)轧制:将加热后的150mm
×
220mm小矩坯经高压水除鳞后送入轧制工序,包括粗轧、中精轧和终轧。其中粗轧采用往复式φ650和φ500粗轧机组多道次轧制,开轧温度1075℃,经过6道次粗轧后中精轧;中精轧全线共计10架轧机,前3架中轧,后7架精轧,其形式为立-平-平-立-平-平-平-平-平-平,配备agc全自动测厚仪,控制厚度公差,中精轧开轧温度980℃;通过控制终轧速度来控制终轧温度,终轧温度910℃,终轧速度6m/s,然后经扭转,蛇形震荡抵平板链运输和冷却。
51.(7)冷却和卷取:将轧制后的钢带空冷,检查表面质量和尺寸公差,进行卷取、打包
和入库,卷取温度670℃。
52.实施例3
53.一种c67s弹性挡圈用钢的制备方法,依次包括转炉冶炼、lf精炼、rh真空处理、连铸、加热、除鳞、轧制、冷却和卷取工序,具体步骤如下:
54.(1)转炉冶炼:转炉中加入25吨废钢和108吨铁水,冶炼钢水的过程中加入活性石灰4100kg、石灰石1300kg和白云石3000kg,控制供氧量为6500m3,采用高拉碳工艺,使用滑板挡渣出钢,控制出钢时钢水中c含量0.31%,p含量0.004%,钢水的氧含量293ppm;转炉出钢过程中加入高碳锰铁720kg、硅铁200kg、高纯石墨碳材450kg、铝块110kg、石灰500kg、改性精炼渣300kg,钢水的初始成分达到目标成分下限的75%。
55.(2)lf精炼:向lf精炼炉内加入高碳锰铁190kg、硅锰120kg、高碳铬铁合金215kg、高纯石墨碳材170kg进行钢水合金化,少量多批次加入高纯碳化硅120kg进行扩散脱氧,加入石灰200kg进行造渣,控制精炼时间50min,白渣保持时间在40min,控制炉渣二元碱度2.71;钢水的目标成分以重量百分比含量计为:c:0.69%、si:0.24%、mn:0.66%、p:0.012%、s:0.004%、cr:018%、ni:0.06%、cu:0.03%,alt:0.026%其余为铁和微量元素。
56.(3)rh真空处理:lf精炼的钢水成分合格后,进行rh真空脱气,真空度0.39mbar,处理时间10min,破真空后加大包覆盖剂,软吹氩气搅拌35min,静搅时渣面微动不见光。
57.(4)连铸:钢水rh真空处理后,吊包到小方坯6#连铸机浇铸,连铸采用水模试验结构最优“稳流器 斜孔导流墙 开孔挡坝”的七机七流整体水口中间包,长水口ar封全保护浇铸,同时大包开浇前中间包吹ar处理,防止钢水二次氧化,如图1所示,过热度21℃,拉速1.40m/min恒拉速进行浇铸制得尺寸150mm
×
220mm的小矩坯。其中比水量为0.60l/kg,结晶器电磁搅拌频率3.00hz、电流300a;末端电磁搅拌频率8hz、电流450a;铸坯中心偏析、中心缩孔和中心疏松均低于1.0级。该中间包钢水停留时间长,每个流钢水停留时间接近,成分和温度均匀,死区体积小,非金属夹杂物能够充分碰撞长大上浮去除。
58.(5)加热:将150mm
×
220mm的小矩坯装入三段连续推钢式加热炉中,在还原性气氛中加热,烟气残氧量2.1%。加热炉加热段温度控制在1115℃,均热段温度控制在1085℃,钢坯断面温差小于30℃。
59.(6)轧制:将加热后的150mm
×
220mm小矩坯经高压水除鳞后送入轧制工序,包括粗轧、中精轧和终轧。其中粗轧采用往复式φ650和φ500粗轧机组多道次轧制,开轧温度1075℃,经过6道次粗轧后中精轧;中精轧全线共计10架轧机,前3架中轧,后7架精轧,其形式为立-平-平-立-平-平-平-平-平-平,配备agc全自动测厚仪,控制厚度公差,中精轧开轧温度980℃;通过控制终轧速度来控制终轧温度,终轧温度910℃,终轧速度6m/s,然后经扭转,蛇形震荡抵平板链运输和冷却。
60.(7)冷却和卷取:将轧制后的钢带空冷,检查表面质量和尺寸公差,进行卷取、打包和入库,卷取温度670℃。
61.本发明实施例1~3制得的弹性挡圈用钢c67s热轧钢带的组分特征见表1。检测实施例1~3所制得弹性挡圈用热轧钢带的厚度、其单面总脱碳层厚度、夹杂物类型等级以及钢带冷轧成品淬火回火处理后的力学性能,所得结果见表2。
62.表1实施例1~3制得的弹性挡圈用热轧钢带各组分的重量百分比
63.样号csimnpscrnicualt
实施例10.680.240.650.0150.0020.200.050.030.024实施例20.690.240.660.0120.0040.180.060.030.026实施例30.690.240.650.0090.0030.190.060.030.024
64.表2实施例1~3所制得弹性挡圈用热轧钢带的综合性能
[0065][0066]
表3夹杂物类型及等级的协议控制标准
[0067]
夹杂物类型a类硫化物b类氧化物c类硅酸盐d类球状氧化物细系≤2.0≤2.0≤2.0≤2.0粗系≤2.0≤2.0≤2.0≤2.0
[0068]
由表1可以看出,本发明所制备的弹性挡圈用钢热轧钢带成品的化学成分波动小。
[0069]
脱碳层厚度的行业控制标准为钢带厚度≤3.00mm时,单面总脱碳层≤0.08mm;钢带厚度>3.00mm时,单面总脱碳层≤实际厚度的2.5%。由表2可以看出,本发明制得的钢带厚度≤3.00mm时,单面总脱碳层为0.05mm和0.06mm;钢带厚度>3.00mm时,单面总脱碳层为0.05mm和0.07mm,可见本发明制备的弹簧钢热轧钢带成品的表面脱碳层少,优于现有的协议控制标准。
[0070]
夹杂物类型分为a类硫化物、b类氧化物、c类硅酸盐、d类球状氧化物及ds类大颗粒夹杂物,其中a类、b类、c类和d类夹杂物又分为细系和粗系,夹杂物级别越低,钢的纯净度越高,具体的协议控制标准见表3。从表2的检验结果可以看出,本发明制备的钢带夹杂物只有b类细系、d类细系和粗系为0.5级,其余都是0级,说明本发明所制备的弹性挡圈用热轧钢带成品的夹杂物含量低,不同批次间材料的组织、晶粒度细小性能稳定、弹性好。可广泛应用于汽车配件等领域。
[0071]
除上述实施例外,本发明还可以有其他实施方式。凡采用等同替换或等效变换形成的技术方案,均落在本发明要求的保护范围。
再多了解一些
本文用于企业家、创业者技术爱好者查询,结果仅供参考。