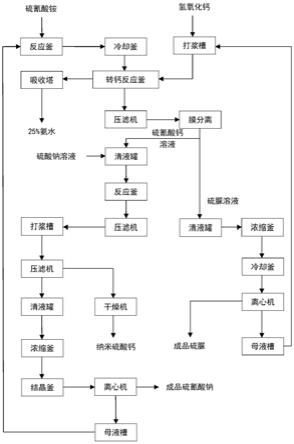
1.本发明涉及一种硫脲联产高纯硫氰酸钠和纳米硫酸钙的生产工艺。
背景技术:
2.近百年来,硫氰酸铵直接转化生产硫脲一直是困扰工业界的难题,目前一般公认需要解决的关键有两个:1、提高硫氰酸铵的转化率;2、提高硫氰酸铵和硫脲的分离效率。硫氰酸铵的转化率和温度、时间等条件密切相关,但更和杂质、溶剂等因素有重大关联。通常,工业界认为熔融是提高硫氰酸铵转化率的有效途径,目前可供借鉴的实验室最高转化率一般在45%,工业实践中转化率一般低于40%。本发明提供了一种转化率高达40%的简单液相合成方法,部分将原料转化为高纯硫脲,未反应的原料进一步间接转化为高纯硫氰酸钠和纳米硫酸钙,有效的解决了分离困难的问题,极大的提高了产品增值。
技术实现要素:
3.鉴于此,本发明的目的在于,提供一种硫脲联产高纯硫氰酸钠和纳米硫酸钙的生产工艺。
4.为了达到上述目的,进而采取的技术方案如下:
5.1.一种硫脲联产高纯硫氰酸钠和纳米硫酸钙的生产工艺,其特征在于:包括以下步骤:
6.(1)将硫氰酸铵用水溶解,硫氰酸铵和水的重量比为1:1~6:1,输送泵将溶液送至反应釜中,开启搅拌,通蒸汽加热至100~150℃,开始反应并维持0.5~8h;
7.(2)将氢氧化钙和水配制成浆料,氢氧化钙与水的重量比为1:1~5:1,通蒸汽预热温度为40~100℃,然后投入步骤(1)中的反应物料,反应0.5~8h,反应过程中,未反应完全的硫氰酸铵转化为硫氰酸钙,同时产生氨气,用水进行吸收,生产25%氨水,将剩余的料液进入分离工序,过程中硫脲不参与反应;
8.(3)将步骤(2)中生成的料液先通过一级过滤,然后通过纳滤,分别收集硫氰酸钙浓溶液和硫脲浓溶液;
9.(4)硫脲浓溶液进行蒸发浓缩,蒸发温度为50~135℃,然后降温结晶,结晶温度为20~40℃,硫脲大量析出,离心分离,分别收集高纯硫脲成品和滤液,滤液返回步骤(2)的转钙工序中用于配制浆料;
10.(5)将步骤(3)中生成的硫氰酸钙浓溶液与硫酸钠饱和溶液按摩尔比1:1.95~1:2.05进行反应,反应温度为40~100℃,反应时间为0.5~8h,产生硫氰酸钠和硫酸钙,压滤分离,分别收集硫氰酸钠清液和硫酸钙滤饼;
11.(6)收集步骤(5)中生成的硫氰酸钠清液蒸发浓缩,然后降温结晶,析出硫氰酸钠结晶,离心分离,分别收集硫氰酸钠成品和母液,母液蒸发浓缩返回步骤1中,其中,硫氰酸钠蒸发温度为100~135℃,结晶温度为40~60℃,母液蒸发温度为100~135℃;
12.(7)收集步骤(5)中生成的硫酸钙滤饼用冷凝水打浆,洗涤两次,压滤分离,二次收
集的硫酸钙滤饼送入双锥真空干燥机干燥,干燥温度为100~150℃,干燥完毕进摇料机粉碎,包装即为纳米硫酸钙成品,而洗涤水多次使用以后,送入步骤(2)转钙工序中用于配制浆料。
13.本发明的有益效果是:
14.本发明采用硫氰酸铵为原料,部分直接转化为硫脲,部分用氢氧化钙转化为硫氰酸钙和氨气,用反渗透膜分离成硫氰酸钙浓溶液和硫脲浓溶液后,然后用硫酸钠为原料将硫氰酸钙转化为硫氰酸钠和纳米硫酸钙,硫脲浓溶液直接浓缩生产高纯硫氰酸钠;
15.本发明方法相比于现有生产工艺,成本低廉、过程简单,反应条件温和、能耗较低,绿色环保,本发明生产的产品有高纯硫脲、高纯硫氰酸钠和纳米硫酸钙三种,高纯硫脲在农药医药中间体等领域,高纯硫氰酸铵在聚合物纤维抽丝剂等领域,纳米硫酸钙在填料等领域有广泛和重要的应用。
附图说明
16.构成本申请的一部分的附图用来提供对本发明的进一步理解,本发明的示意性实施例及其说明用于解释本发明,并不构成对本发明的不当限定。在附图中:
17.图1为本发明的工艺流程图。
具体实施方式
18.需要说明的是,在不冲突的情况下,本申请中的实施例及实施例中的特征可以相互组合。下面将参考附图并结合实施例来详细说明本发明。
19.为了使本技术领域的人员更好地理解本申请方案,下面将结合本申请实施例中的附图,对本申请实施例中的技术方案进行清楚、完整地描述,显然,所描述的实施例仅仅是本申请一部分的实施例,而不是全部的实施例。基于本申请中的实施例,本领域普通技术人员在没有做出创造性劳动前提下所获得的所有其他实施例,都应当属于本申请保护的范围。
20.请参考图1:
21.一种硫脲联产高纯硫氰酸钠和纳米硫酸钙的生产工艺,包括以下步骤:
22.(1)将硫氰酸铵用水溶解,硫氰酸铵和水的重量比为1:1~6:1,输送泵将溶液送至反应釜中,开启搅拌,通蒸汽加热至100~150℃,开始反应并维持0.5~8h;
23.(2)将氢氧化钙和水配制成浆料,氢氧化钙与水的重量比为1:1~5:1,通蒸汽预热温度为40~100℃,然后投入步骤(1)中的反应物料,反应0.5~8h,反应过程中,未反应完全的硫氰酸铵转化为硫氰酸钙,同时产生氨气,用水进行吸收,生产25%氨水,将剩余的料液进入分离工序,过程中硫脲不参与反应;
24.(3)将步骤(2)中生成的料液先通过一级过滤,然后通过纳滤,分别收集硫氰酸钙浓溶液和硫脲浓溶液;
25.(4)硫脲浓溶液进行蒸发浓缩,然后降温结晶,硫脲大量析出,离心分离,分别收集高纯硫脲成品和滤液,滤液返回步骤(2)的转钙工序中用于配制浆料;适宜的蒸发温度为50~135℃,适宜的降温结晶温度为20~40℃;
26.(5)将步骤(3)中生成的硫氰酸钙浓溶液与硫酸钠饱和溶液按摩尔比1:1.95~1:
2.05进行反应,反应温度为40~100℃,反应时间为0.5~8h,产生硫氰酸钠和硫酸钙,压滤分离,分别收集硫氰酸钠清液和硫酸钙滤饼;
27.(6)收集步骤(5)中生成的硫氰酸钠清液蒸发浓缩,然后降温结晶,析出硫氰酸钠结晶,离心分离,分别收集硫氰酸钠成品和母液,母液蒸发浓缩返回步骤1中;上述适宜的硫氰酸钠蒸发温度为100~135℃,适宜的结晶温度为40~60℃,适宜的母液蒸发温度为100~135℃;
28.(7)收集步骤(5)中生成的硫酸钙滤饼用冷凝水打浆,洗涤两次,压滤分离,二次收集的硫酸钙滤饼送入双锥真空干燥机干燥,适宜干燥温度为100~150℃,干燥完毕进摇料机粉碎,包装即为纳米硫酸钙成品,而洗涤水多次使用以后,送入步骤(2)转钙工序中用于配制浆料。
29.本发明采用硫氰酸铵为原料,部分直接转化为硫脲,部分用氢氧化钙转化为硫氰酸钙和氨气,用反渗透膜分离成硫氰酸钙浓溶液和硫脲浓溶液后,然后用硫酸钠为原料将硫氰酸钙转化为硫氰酸钠和纳米硫酸钙,硫脲浓溶液直接浓缩生产高纯硫氰酸钠。
30.以上所述仅为本发明的优选实施例而已,并不用于限制本发明,对于本领域的技术人员来说,本发明可以有各种更改和变化。凡在本发明的精神和原则之内,所作的任何修改、等同替换、改进等,均应包含在本发明的保护范围之内。
技术特征:
1.一种硫脲联产高纯硫氰酸钠和纳米硫酸钙的生产工艺,其特征在于:包括以下步骤:(1)将硫氰酸铵用水溶解,硫氰酸铵和水的重量比为1:1~6:1,输送泵将溶液送至反应釜中,开启搅拌,通蒸汽加热至100~150℃,开始反应并维持0.5~8h;(2)将氢氧化钙和水配制成浆料,氢氧化钙与水的重量比为1:1~5:1,通蒸汽预热温度为40~100℃,然后投入步骤(1)中的反应物料,反应0.5~8h,反应过程中,未反应完全的硫氰酸铵转化为硫氰酸钙,同时产生氨气,用水进行吸收,生产25%氨水,将剩余的料液进入分离工序,过程中硫脲不参与反应;(3)将步骤(2)中生成的料液先通过一级过滤,然后通过纳滤,分别收集硫氰酸钙浓溶液和硫脲浓溶液;(4)硫脲浓溶液进行蒸发浓缩,蒸发温度为50~135℃,然后降温结晶,结晶温度为20~40℃,硫脲大量析出,离心分离,分别收集高纯硫脲成品和滤液,滤液返回步骤(2)的转钙工序中用于配制浆料;(5)将步骤(3)中生成的硫氰酸钙浓溶液与硫酸钠饱和溶液按摩尔比1:1.95~1:2.05进行反应,反应温度为40~100℃,反应时间为0.5~8h,产生硫氰酸钠和硫酸钙,压滤分离,分别收集硫氰酸钠清液和硫酸钙滤饼;(6)收集步骤(5)中生成的硫氰酸钠清液蒸发浓缩,然后降温结晶,析出硫氰酸钠结晶,离心分离,分别收集硫氰酸钠成品和母液,母液蒸发浓缩返回步骤1中,其中,硫氰酸钠蒸发温度为100~135℃,结晶温度为40~60℃,母液蒸发温度为100~135℃;(7)收集步骤(5)中生成的硫酸钙滤饼用冷凝水打浆,洗涤两次,压滤分离,二次收集的硫酸钙滤饼送入双锥真空干燥机干燥,干燥温度为100~150℃,干燥完毕进摇料机粉碎,包装即为纳米硫酸钙成品,而洗涤水多次使用以后,送入步骤(2)转钙工序中用于配制浆料。
技术总结
本发明涉及一种硫脲联产高纯硫氰酸钠和纳米硫酸钙的生产工艺,包括以下步骤:将硫氰酸铵用水溶解,输送泵将溶液送至反应釜中,通蒸汽加热,开始反应;将氢氧化钙和水配制成浆料,通蒸汽预热,然后投入反应物料,反应过程中,未反应完全的硫氰酸铵转化为硫氰酸钙,同时产生氨气,用水进行吸收,生产25%氨水,将剩余的料液进入分离工序,生成的料液先通过一级过滤,然后通过纳滤,分别收集硫氰酸钙浓溶液和硫脲浓溶液。本发明方法相比于现有生产工艺,成本低廉、过程简单,反应条件温和、能耗较低,绿色环保,生产的高纯硫脲在农药医药中间体等领域,高纯硫氰酸铵在聚合物纤维抽丝剂等领域,纳米硫酸钙在填料等领域有广泛和重要的应用。应用。应用。
技术研发人员:孙益新 郭宇翔 杨俊文 郭懿馨
受保护的技术使用者:格林智慧环保科技(山西)有限公司
技术研发日:2021.11.11
技术公布日:2022/3/11
再多了解一些
本文用于企业家、创业者技术爱好者查询,结果仅供参考。