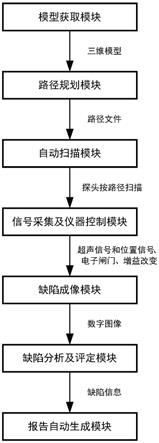
1.本发明属于复杂模锻件超声波自动无损检测技术领域,具体涉及一种复杂模锻件超声波自动检测装置。
背景技术:
2.复杂模锻件通常具有多台阶、变厚度、变曲率轮廓等不规则特征,且种类多样,传统的基于直角坐标系构建的超声自动检测设备已不能准确的对该类复杂模锻件实施自动成像检测,以类半球形模锻件为例,该锻件具有柱面、变厚度变曲率类球面、平面等结构,采用传统自动扫查设备检测时,存在着扫查路径复杂难以自动实现规划、成像困难的难题。
3.目前针对复杂模锻件仍缺少必要的全自动超声检测设备,如专利文献cn112730633a公开了一种不规则曲面工件的超声自动检测装置和方法,使用时先将待检测工件放置在传送带上的工件夹具之间,然后通过第一伺服电机驱动传送带匀速运动,传送带上方的阵列式激光传感器通过激光测得工件各个位置的高度,形成整个工件表面的形状信号,控制模块将形状信号转化为控制信号,控制第二伺服电机以及超声探测机构的第一电动推杆、第二电动推杆和第三电动推杆根据控制信号适时调节超声探头的位置和状态,保证待检测工件通过时超声探头能够完全贴合在待检测工件表面对其进行检测。但是该发明对于含多种结构(如上述类半球形模锻件)或曲率变化较大的结构不能很好获取形状信息,且该发明未见实现自动成像和缺陷自动分析评定。
技术实现要素:
4.本发明的目的在于提供一种复杂模锻件超声波自动检测装置,以实现复杂模锻件的全自动智能化检测,解决复杂模锻件结构复杂、多样带来的扫描路径规划困难、成像困难、缺陷分析评定困难等难题,并进一步降低缺陷评定难度,并提高检测效率。
5.实现本发明目的的技术解决方案为:
6.一种复杂模锻件超声波自动检测装置,包括:
7.模型获取模块,用于自动扫描获取锻件的三维数字模型;
8.路径规划模块,用于将锻件的三维数字模型转换成超声波探头扫描路径;
9.扫描模块,用于按照规划的扫描路径执行对锻件的超声波扫描;
10.信号采集及仪器控制模块,用于实时采集扫描过程中的超声波信号和探头位置信号;
11.缺陷成像模块,用于将信号采集模块获得的超声信号和探头位置信号实时转换成c扫描和b扫描数字图像;
12.缺陷分析及评定模块,用于对获得的数字图像进行处理,获取缺陷信息,并评判产品合格性。
13.本发明与现有技术相比,其显著优点是:
14.(1)结合三维激光扫描技术和机器人离线编程技术,实现了复杂模锻件扫描路径
的便捷快速自动规划。
15.(2)通过超声波仪器在线控制技术实现电子闸门、增益的实时在线控制,解决了变厚度复杂模锻件超声扫描误触发闸门的问题。
16.(3)结合超声波c扫描成像、b扫描成像和图像处理技术,实现了缺陷的自动分析及基于产品验收标准进行自动评定。
附图说明
17.图1是本发明系统组成框图。
18.图2是本发明硬件部分结构及连接关系示意图。
19.图3是本发明超声探头扫描过程及成像方法示意图。
具体实施方式
20.下面结合附图及具体实施例对本发明做进一步的介绍。
21.结合图1、图2、图3所示,本实施例的一种复杂模锻件超声波自动检测装置,针对种复杂模锻件的缺陷进行检测,该复杂模锻件为设有内腔且外径逐渐减小的回转体结构,具体的该检测装置包括模型获取模块、路径规划模块、自动扫描模块、信号采集及仪器控制模块、缺陷成像模块、缺陷分析及评定模块、报告自动生成模块。
22.所述模型获取模块用于自动扫描获取复杂锻件的三维数字模型;所述路径规划模块将获取的复杂锻件三维模型自动转换成超声波探头扫描路径;所述扫描模块自动按照规划的扫描路径执行对复杂锻件的超声波扫描;所述信号采集及仪器控制模块实时采集扫描过程中的超声波信号和探头位置信号,并按需要实时在线控制数字超声波仪器的电子闸门、增益;所述缺陷成像模块将信号采集模块获得的超声信号(回波波幅、声程)和探头位置信号实时自动转换成c扫描数字图像或b扫描图像坐标系中对应点处的像素值,c扫描图像中的像素值代表的是波幅、b扫描图像中的像素值代表的是声程;所述缺陷分析及评定模块自动对获得的数字图像进行降噪处理、缺陷识别分析,并依据产品验收标准和分析结果自动评判产品合格性;所述报告自动生成模块将缺陷分析和评定结果按格式自动生成检测报告。
23.所述超声波探头扫描路径具体为:
24.超声波探头在世界坐标系xyoz中沿回转形复杂模锻件底部外圆上任一点p
w1,1
(x
w1,1
,y
w1,1
,z
w1,1
)作为起始点,由机器人带动做周向扫描(获得一个扫描圆),扫描一周后回到起始点,该一周扫描圆上等间隔的获得n个扫描点:p
w1,1
、p
w1,2
、
…
p
w1,j
、
…
、p
w1,n
;扫描一周后沿母线向上步进距离d到点p
w2,2
(x
w2,1
,y
w2,2
,z
w2,2
),然后继续做周向扫描,同样获得n个扫描点:p
w2,1
、p
w2,2
、
…
、p
w2,n
;扫描一周后继续向上步进第i个距离d,同理获得第i个扫描圆的n个扫描点:p
wi,1
、p
wi,2
、
…
、、p
wi,j
…
、p
wi
,n;如此重复上述扫描直至整件模锻件扫描结束。其中i=1,2
…
m,i表示第i个扫描圆,m为扫描圆的总个数,j=1,2
…
n,j表示单个扫描圆上的第j个扫描点,n为单个扫描圆上的扫描点的总数。扫描路径点位p
wi,j
、p
wi,j 1
、
…
、p
wi,n
由机器人离线编程单元根据复杂模锻件三维模型在世界坐标系xyoz中的空间位置按机器人运动学方程计算给出,并将该系列空间点位及复杂模锻件模型第i个扫描圆上的几何中心点pi(x
wi
,y
wi
,z
wi
)自动保存在txt路径文件中。
25.所述c扫描和b扫描数字图像是通过近似环形成像实现的,具体实现过程为:
26.通过机器人控制器经上位机采集及仪器控制单元实时获取超声波探头在世界坐标系xyoz中的i个扫描圆的第j个扫描点p
wi,j
(x
wi,j
,y
wi,j
,z
wi,j
),再由缺陷成像模块读取txt路径文件中的复杂模锻件模型第i个扫描圆上的几何中心点后经计算得出该点的横截面外径ri,然后将第i个扫描圆上的横截面坐标系xioiyi下的第j个扫描点p
wi,j
(x
wi,j
,y
wi,j
)经顺时针90度旋转、缩小d倍、横向偏移-ri、纵向偏移-ri变换为图像坐标系uo
t
v下的点p’ti,j
(u
ti,j
,v
ti,j
),同时将成像画板上该点p’ti,j
处的像素值置为0~255中的某个数字,该数字与此处的超声波幅或超声波声程成正比;循环以上过程直至扫描结束,即可完成整个复杂模锻件的成像;其中每个扫描圆都对应有一个横截面坐标系,第i个扫描圆上的横截面坐标系的圆心pi(x
wi
,y
wi
,z
wi
)为该扫描圆的几何中心,横、纵坐标分别沿该扫描圆的径向,且相互垂直。
27.第i个扫描圆的横截面外径横截面坐标系xiyioizi到图像坐标系uo
t
v的变换过程为:
[0028][0029]
结合图1、图2所示,所述的模型获取模块包括三维激光扫描仪4、夹持工装3、模型自动扫描单元、模型处理单元,三维激光扫描仪4通过夹持工装3与六轴工业机器人2末端连接,并通过电缆与模型处理单元连接,在模型自动扫描单元控制下由机器人2带动三维激光扫描仪4对复杂模锻件9实施球形覆盖扫描,然后由模型处理单元实时将激光扫描信息转换成三维模型,并经优化处理后生成特定格式(如.stp、.stl)的三维数字模型文件;用于批量产品检测时,该功能模块只需在首件检测时使用,使用后将三维激光扫描仪从夹持工装3上拆卸以便于后续超声波扫描。
[0030]
结合图1、图2、图3所示,所述的路径规划模块包括机器人离线编程软件、路径优化单元,实施时将三维数字模型文件导入机器人离线编程软件中,并放置在工作台相应位置处,由单元根据机器人2末端的超声波探头7、喷水耦合水套6、复杂模锻件9、环形工作台1三维模型之间的相对位置和扫描路径间隔要求自动规划超声波探头7的扫描路径并生成路径文件,再由路径优化单元将路径文件中的不必要的动作(如退刀、起始停顿)优化掉并生成机器人控制器可执行的扫描路径文件;所述的机器人离线编程软件可以是商业软件,也可以是自编软件。
[0031]
结合图1、图2所示,所述的自动扫描模块包括六轴工业机器人2、机器人控制器、环形工作台1、探头夹持工装3、喷水耦合水套6、超声波探头7、水循环装置8、扫描控制单元,超声波探头7安装于喷水耦合水套6内,喷水耦合水套6固定在探头夹持工装3底部,探头夹持工装3顶部通过螺栓连接在六轴工业机器人2末端,六轴工业机器人2安装在环形工作台1中心,两者旋转中心相同,六轴工业机器人2通过电缆与机器人控制器连接,机器人控制器通过tcp/ip总线电缆与上位机扫描控制单元连接,水循环装置通过水管与喷水耦合水套6连接,扫描时由六轴工业机器人在上位机扫描控制单元控制下带动超声波探头按照扫描路径
文件要求自动对复杂模锻件进行覆盖式扫描。
[0032]
结合图1、图2所示,所述的信号采集及仪器控制模块包括数字超声波仪器、高速信号采集卡、位置编码器、超声波电缆、usb通讯电缆、采集电缆、上位机信号采集及仪器控制单元(含计算机),数字超声波仪器通过超声波电缆与超声波探头7连接,高速信号采集卡一端通过采集电缆与数字超声波仪器的模拟io口连接,另一端通过采集电缆上的总线(如usb、pci、pxi)接口与上位机采集及仪器控制单元(含计算机)连接,数字超声波仪器通过usb通讯电缆与上位机采集及仪器控制单元(含计算机)连接,位置编码器位于机器人2各轴电机内,经机器人控制器通过tcp/ip总线与上位机采集及仪器控制单元(含计算机)连接,在探头7对复杂模锻件9进行自动扫描过程中,由高速信号采集卡实时完成超声波信号(如波幅、声程)采集、由单元通过tcp/ip协议查询机器人位置编码器位置实时获得位置信号,并根据复杂模锻件9的厚度变化在线控制数字超声波仪器的电子闸门宽度、增益等参数。
[0033]
结合图1、图2所示,所述的缺陷成像模块将采集到的超声波信号(波幅、声程)和位置信号同时按c扫描和b扫描显示方式实时由单元画图成像,图像的横纵坐标分别表示探头的平面位置和扫描路径间隔,图像灰度值(或彩色值)表示超声波波幅高度或声程;超声波幅高度f转换为8bit图像灰度值超声波声程d转换为8bit图像灰度值8bit灰度图像转换为彩色图像按r=g=b=p进行。其中,fsh表示数字超声波仪器满屏高度,rg表示数字超声波仪器时基(水平)范围,r、g、b表示三原色值、p表示8bit灰度值。
[0034]
结合图1、图2所示,所述的缺陷分析及评定模块包括图像滤波子模块、缺陷分割提取校正子模块、缺陷统计分析模块、缺陷评定子模块,扫描结束后,首先采用3*3中值滤波模板算法由图像滤波子模块自动对c扫描和b扫描图像进行降噪处理,然后由缺陷分割提取校正子模块对图像上灰度大于阈值pthd的聚集区域分割提取出来,并按校正算法对缺陷进行自动校正处理,再由缺陷统计分析模块自动统计计算缺陷区域面积、长度、宽度、长宽比、埋深、当量平底孔直径、平面位置,最后由缺陷评定子模块依据产品验收标准自动判定缺陷的合格性及缺陷性质;所述阈值pthd是由c扫描图像的灰度直方图进行自动确定的;所述校正算法的依据是超声声束线移到缺陷边缘时波高约为声束轴线在中部时波高一半且灰度与幅值成正比;所述缺陷性质是指线性缺陷、点状缺陷,判断方法为图像上缺陷长宽比大于3时判定为线性缺陷,反之判定为点状缺陷;所述当量平底孔直径是由c扫描图像中灰度值反向计算出波高f=(p1/255)
×
fsh,按公式反向计算出声程d=(p2/255)
×
rg,再由波高、声程与数字超声波仪器上的dac曲线进行比较自动获取缺陷的当量平底孔直径,用φ1.2mm xxdb表示。c扫描图像中缺陷区域中所有像素的个数即为缺陷面积;对c扫描图像中缺陷区域进行逐行扫描,搜索属于缺陷区域中的像素,找出该缺陷区域坐标x、y分别对应的最大和最小的x
max
、x
min
、y
max
、y
min
,并由这些坐标构建出该缺陷区域的定位外切矩形,该外切矩形的长和宽表示缺陷的长度和宽度;埋深是指缺陷距工件表面的实际深度,是通过b扫描图像中灰度值由上述公式反向计算得到超声波声程获得;平面位置指缺陷区域的质心,x向和y向坐标分别由长度方向和宽度方向的总像素个数分别除以面积得到。
[0035]
结合图1、图2所示,所述的报告自动生成模块包括报告编号、日期、产品信息(名称、代号、批次号、材料类型、规格)、检测标准、验收标准、缺陷信息(面积、长度、宽度、长宽比、深度、当量平底孔直径、平面位置等)、结论、编制人员等,报告生成是在缺陷分析及评定之后通过点击单元按钮自动进行的。
再多了解一些
本文用于企业家、创业者技术爱好者查询,结果仅供参考。