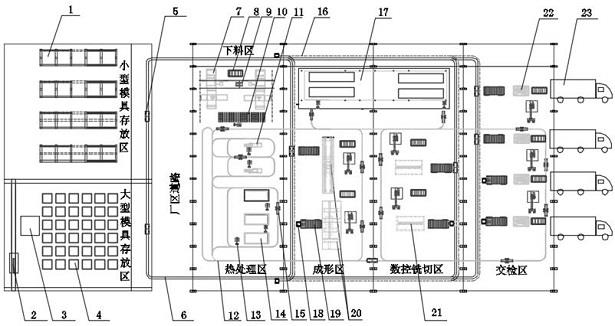
1.本发明公开了一种物流系统,具体公开了一种适用于钣金零件制造的智能物流系统和方法。
背景技术:
2.航空钣金零件在飞机零件中占据相当大的比重,是飞机主要零件类型之一。航空钣金零件具有品种多的特点,根据飞机大小,一架飞机上具有数千甚至数万项航空钣金零件,使得其成形工艺多种多样,主要有蒙拉成形、充液成形、橡皮囊液压成形、冲压成形、闸压成形等,而航空钣金零件的制造需要借助模具,大部分零件需要多套模具,品种多的特点使得其模具数量庞大。
3.大部分航空钣金零件需要进行热处理来提高强度或成形性能,而热处理(主要是固溶处理)会使得零件发生变形,这使得其制造工序流程较为复杂。航空钣金零件还具有小批量生产的特点,这要求生产期间原材料、模具、零件的周转频率很快,若没有一个高效的物流系统将导致生产现场拥挤不堪、物料配备滞后,严重影响生产效率。
4.当前,模具、原材料、零件的转运主要依靠汽车、平板车、三轮车、叉车等,物流方式落后,这使得整个航空钣金零件的生产处理离散状态。为了满足零件品种及数量不断增长的生产需求,主要通过增加物流车辆及频次、加班加点来完成物料的配送,当生产任务量达到一定程度后,这种物流方式使得生产现场物流通道拥堵不堪,反而降低了物流效率,影响零件生产。
技术实现要素:
5.本发明旨在解决现有技术中航空钣金零件生产效率低、现有生产方式离散、现场物流不畅、资源配备滞后等问题,提出了一种适用于航空钣金零件制造小批量、多品种的生产特点的智能物流系统和方法,提高钣金零件的生产效率。
6.本发明的目的是通过以下技术方案实现的:一种适用于钣金零件制造的智能物流系统,其特征在于,包括按加工制造工序划分的各个功能区域、围绕各个功能区域设置的物流运输线和用于调控物流运输过程的信息管理系统;所述物流运输线包括地轨、轨道小车、高空钢轨、吊轨、吊架及辅助转移设备;所述地轨连通各个功能区域,与配套的轨道小车运输大型模具;所述高空钢轨设置在地轨上方,与配套的轨道小车运输小型模具;所述吊轨的线路将各个功能区域连通,吊轨与吊架配合用于各功能区域之间的材料或半成品零件的转移,所述辅助转移设备根据工序的需要配备在各功能区域,用于功能区域内的上下料及半成品零件转移;轨道小车和吊架上分别设置有追踪编码,在其运动路径上对应设置有扫码器,扫码器通过扫描追踪编码将其对应运输的模具、材料或零件的位置信息反馈至信息管理系统。
7.进一步的,所述功能区域包括模具存放区、下料区、热处理区、成形区、数控铣切区和交检区;模具存放区又包括纵向并列设置的小型模具存放区和大型模具存放区,下料区、热处理区纵向并列且位于模具存放区的一侧,成形区、数控铣切区和交检区依次横向并列设置在热处理区的下游一侧。
8.进一步的,所述小型模具存放区内设置有立体模具库,立体模具库中的每个存放位置有唯一识别编码,立体模具库与托架配合实现小型模具的存取。
9.进一步的,所述大型模具存放区内设置有堆栈式立体库,所述堆栈式立体库划分为n个具有唯一识别编码的平面区域,且每个模具上有唯一模具编码,所述自动桁车上设置有定位器及模具编码识别装置。
10.进一步的,在成型区和数控铣切区设置有用于零件暂存冷却的立体自然时效库,所述立体自然时效库内设置有零件托盘及用于驱动零件托盘运动的承托机构,零件托盘用于存放时效零件且每个托盘有唯一时效编码,扫描唯一时效编码开始计算零件存放时间。
11.进一步的,包括如下步骤:模具出库步骤:信息管理系统接收到现场模具需求指令,驱动自动桁车或托架将模具存放区内的指定模具取出放置到轨道小车上,通过扫描模具编码和轨道小车编码将二者连接,实时上传更新模具位置;下料步骤:信息管理系统接收下料指令,控制下料区内的下料设备工作,并通过辅助转移设备将下好的料按需装入下料区上方的吊架中,扫描吊架编码将材料信息与吊架编码统一,并通过吊轨上的传感器将材料的物流信息传递给信息管理系统;热处理步骤:吊架装载下料区的材料进入热处理区,信息管理系统根据加工信息发出指令让吊架运行至指定加工设备旁,由热处理区的辅助转移设备将材料从吊架取出并装入加工设备,再将热处理完毕后的材料装入吊架,转移至下一工序;成型步骤:信息管理系统根据零件加工信息发出指令,使载有模具的轨道小车和载有热处理后材料的吊架运输至成型区的指定设备旁,由成型区的辅助转移设备将材料和模具取下,放置到成型设备上进行零件成形;时效控制步骤:零件成形完毕后,对于自然时效零件,通过吊架转入立体自然时效库中,完成时效后再通过吊架运至数控铣切区,对于人工时效零件,则通过吊架将其转入热处理区,完成人工时效后将零件运至数控铣切区;数控铣切步骤:数控铣切区的辅助转移设备将经过时效处理后的零件从吊架上取下,放置于铣夹上进行数控铣切;然后数控铣切区的辅助转移设备将铣切完成的零件转移至吊架,进入交检区。
12.进一步的,进入交检区后的物流过程如下:a)信息管理系统发出指令,通过轨道小车将模具运至检验工作台,大型模具通过自动上下模机移至检验台上,小型模具先通过升降台从高空钢轨上取下,再通过自动上下模机移至检验台上;b)信息管理系统发出指令,通过吊轨上的吊架将铣切完成后的零件移至检验台旁,再通过交检区的辅助转移设备将零件取下,放置于检验台上;c)检验合格后,辅助转移设备将零件放置于旁边的堆垛平台上,待同一批次零件检验完成后,再转入运输车交付给其他加工单位,并将信息反馈信息管理系统;
d)检验完成后,模具则通过辅助转移设备移至地轨或高空钢轨的轨道小车上,并将轨道小车编码反馈给信息管理系统,监控模具运输状态。
13.进一步的,立体自然时效库的运行过程包括:a)信息管理系统将零件运至某个位置时触发入库指令,立体自然时效库的运动机构移出空余的零件托盘;b)辅助转移设备从吊架上取下零件放入零件托盘,并扫描托盘时效编码传回信息管理系统,信息管理系统将零件与托盘时效编码统一,监控时效状态;c)时效完成后,信息管理系统向运动机构发出指令,运动机构将托盘移出,触发取件指令;d)辅助转移设备将零件放置于吊轨上的吊架,并扫描吊架编码,传回信息管理系统,信息管理系统将零件和挂架编码统一,实时监控零件状态。
14.进一步的,小型模具的出入库过程包括:模具出库时,信息管理系统接收模具需求指令,驱动立体模具库取出模具,并通过托架上的自动伸缩臂,将模具放置于轨道小车上,同时将轨道小车的追踪编码反馈给信息管理系统;模具入库时,通过托架上的自动伸缩臂将模具放置于托架上,并运至立体模具库空余位置存放,并将存放位置同过扫码反馈给信息管理系统。
15.进一步的,大型模具出入库过程包括:模具出库时,信息管理系统发出模具需求指令,驱动自动桁车取模;自动桁车从信息管理系统获得模具的唯一模具编码和位置信息,并移动到指定位置,抓取该模具并放置到运输轨道小车上,同时,扫描轨道小车的追踪编码并传递给信息管理系统;信息管理系统将模具编码和轨道小车的追踪编码连接,根据轨道小车在轨道上运行的位置实时更新模具位置;模具入库时,信息管理系统发出模具回收指令,轨道小车将模具运至堆栈式立体库时,自动桁车抓取模具,移动至堆放较少的位置,并将位置信息传递给信息管理系统,更新模具位置信息,完成模具回收。
16.本技术方案的有益效果如下:1. 本发明所述的柔性物流系统,其设计布局减少了生产现场模具、材料、零件的存放空间与时间,释放出生产空间,有利于提高现场整洁度及作业环境的安全性;2、本发明所述的柔性物流系统,通过各条物流运输险的协同配合,提高了模具、材料的配送准时率及零件的转运效率,从而提高零件的生产效率;3、本发明所述的柔性物流系统,将零件生产流程有效串联起来,不再是离散的生产方式,促进零件生产方式的转型升级。
附图说明
17.本发明的前述和下文具体描述在结合以下附图阅读时变得更清楚,附图中:图1是图1是本发明一种适用于航空钣金制造的智能物流系统示意图;图2是模具存放区物流系统示意图;图3是下料区物流系统示意图;
图4是热处理区物流系统示意图;图5是成形区/数控铣切区物流系统示意图;图6是交检区物流系统示意图;图中:1、立体模具库,2、自动桁车,3、缓存区,4、堆栈式立体库,5、轨道小车,6、地轨,7、自动下料机,8、堆垛平台,9、取料机,10、分料区,11、热处理炉,12、吊轨,13、自动上下料机器人,14、热处理槽,15、吊架,16、高空钢轨,17、立体自然时效库,18、模具升降台,19、自动上下模机,20、成形设备、21、数控铣切设备,22、检验台,23、运输车。
具体实施方式
18.下面通过几个具体的实施例来进一步说明实现本发明目的技术方案,需要说明的是,本发明要求保护的技术方案包括但不限于以下实施例。
19.实施例1本实施例公开了如图1-6所示的一种适用于航空钣金制造的智能物流系统,基于航空钣金零件的制造工艺流程,并配置合理的物流运输线及辅助转移设备,构成智能物流系统。
20.本发明的实施分为两个步骤:第一步为工艺布局设计;第二步为智能物流系统设计。
21.s1:工艺布局设计在厂区内按照加工工序划分为模具存放区、下料区、成形区、热处理区、数控铣切区、交检区。
22.基于模具尺寸,将模具存放区分为大型模具存放区和小型模具存放区,大型模具采用堆栈式存放,小型模具采用立体模具库1存放,若模具数量庞大而厂房规模有限,也可以将模具存放区布局在单独库房。
23.由于部分零件采用“一步法”(即下料
→
热处理
→
成形)成形,因此将下料区与热处理区布局在同一区域,降低物流成本。
24.航空钣金零件需要时效后才能进行数控铣切,部分零件为自然时效(即零件在自然状态下逐渐硬化,通常时间为24~72小时),为了防止零件堆积,在成形区及数控铣切区设计立体自然时效库17。
25.基于上述工艺布局进行智能物流系统的设计,如图1所示,其主要由物流运输线、辅助转移设备及中控系统组成。其中:物流线运输线包括地轨6、轨道小车5、高空钢轨16、吊轨12、吊架15。地轨6为大型模具运输线,与配套的轨道小车5运输大型模具;高空钢轨16为小型模具运输线(通常指重量<500kg且尺寸<1500*1200mm),为节省空间,将其设计在地轨6上方,与配套的轨道小车5运输小型模具;吊轨12及配套的吊架15则负责各区域之间材料及零件的运输。
26.物流线实现智能物流的“最后一公里”需要借助辅助转移设备,辅助转移设备主要包括自动桁车2、自动上下料机器人13、自动上下模机19、模具升降台18、分料区10、堆垛平台8。
27.信息管理系统是智能物流系统的“大脑”,一般在厂房设计单独的控制室,用于安
装信息管理系统的相关信息设备,其主要作用有:1、台账管理,包括零件加工信息、模具信息及实时位置信息、材料/零件加工状态及实时位置信息等;2、指令接收及发布功能,驱动相关设备运转;3、设备状态实时监控,用于判定当前设备状态(完好还是维修中)及负荷情况,以便系统判定并发出正确的物流指令。
28.各功能区的物流系统设计及运行场景如下:(1)模具存放区物流系统设计模具存放区的物流系统如图2所示,其设计及运行场景如下:1)小型模具存放于立体模具库1中,每个存放位置有唯一编码,信息管理系统收到模具需求指令时,驱动立体模具库1系统取出模具,通过托架上的自动伸缩臂,将模具放置于轨道小车5上,同时将轨道小车5编码反馈给信息管理系统,以便随时监控模具位置;同理,模具回收时,通过托架上的自动伸缩臂将模具放置于托架上,运至立体模具库1空余位置存放,并将存放位置反馈给信息管理系统。
29.2)大型模具存放于堆栈式立体库4中,其采用如下设计:a)将存放区划分为n个平面区域、每个平面区域有唯一编码;b)模具上标记有模具编码;c)自动桁车2上布置定位器及模具编码识别装置,自动桁车2存放模具时通过识别模具编码获取模具存放位置(平面位置n,高空位置z),并反馈给信息管理系统,同理,在需要取出模具时,通过信息管理系统精确获取模具位置信息;d)附近设计一个缓存区3,用于取模时该模具上方模具的临时存放。
30.运行场景如下:a)信息管理系统收到现场模具需求指令,驱动自动桁车2取模;b)自动桁车2接受到取模指令,并从信息管理系统获得模具的编码和位置信息,移动到指定位置,抓取该模具之上的模具,逐一转移到缓存区3;c)自动桁车2抓取该模具,并放置到运输轨道小车5,同时,扫描轨道小车5编码并传递给信息管理系统;d)信息管理系统将模具编码和轨道小车5追踪编码连接,根据轨道小车5在轨道6上运行的位置实时更新模具位置;e)自动桁车2逐一将缓存区3模具移回原位,并将模具的位置信息传递回信息管理系统,更正模具位置信息,至此完成模具出库;f)当信息管理系统发出模具回收指令,轨道小车5将模具运至库房时,自动桁车2抓取模具,移动至堆放较少的位置,并将位置信息传递给信息管理系统,信息管理系统更新模具位置信息,完成模具回收。
31.(2)下料区物流系统设计航空钣金原始材料均为标准尺寸整板,因此,需要根据不同零件需求切割成需要的尺寸。下料区物流系统如图3所示,其运行场景如下:a)信息管理系统接受下料指令,对n个零件进行下料,基于零件毛料信息,进行自动排料,将排料信息传递给自动下料机7;b)信息管理系统指令取料机9从堆垛平台8上取出整板原材料,并装入自动下料机7,自动下料机7按照排料信息进行下料;
c)取料机9将下好的料分类取出,并放置在分料区10,获取每种材料的位置信息,反馈给信息管理系统;d)下料完成,信息管理系统指令自动上下料机器人13从分料区10相应的位置取出材料,装入吊轨12的吊架15中,并扫描吊架15编码,将信息传递给信息管理系统;e)信息管理系统将材料信息与吊架15编码统一,通过吊轨12上的传感器实时监控材料的物流状态,并到达下一工序。
32.(3)热处理区物流系统设计热处理区物流系统如图4所示,其设计及运行场景如下:1)为了满足n种零件同时生产的需求,其采用如下设计:a)吊架15上有唯一身份编码,在吊轨12所有分叉节点前均安装扫码器,以便及时反馈材料或零件的位置给信息管理系统;b)设备周边设计环线,当设备来不及加工运至的材料或零件时,向信息管理系统发出满负荷状态信息,信息管理系统发出指令,使得吊架15在设备周边环线移动,这样既不影响主物流线的运转,又保证了每个加工单元在产能负荷上有一定的柔性。
33.2)其运行场景如下:a)吊架15装载材料或零件进入热处理区时,吊轨12上的扫码器扫描吊架15编码并反馈给信息管理系统;b)信息管理系统根据零件加工信息,判定对应的加工设备,并发出指令,让吊架15前行至加工设备旁;c)吊架15到达指定位置,传感器扫描吊轨12编码,信息管理系统向自动上下料机器人13发出指令,自动上下料机器人13将材料或零件从吊架15取出,装入设备,并将信息反馈信息管理系统,信息管理系统将吊架15编码与零件的联系断开;d)零件热处理完后,由自动上下料机器人13取出并装入吊架15,同时将信息反馈给信息管理系统,传入下一工序,信息管理系统将吊架15编码与零件连接;e)当设备周边加工零件较多时,挂架就一直在设备周边圆周运行。
34.(4)成形区/数控铣切区物流系统设计成形区与数控铣切区物流系统类似,如图5所示,其运行场景如下:1)立体自然时效库17运行场景:立体自然时效库17内有零件托盘及运动机构,零件托盘用于存放时效零件且每个托盘有唯一编码;运动机构负责零件托盘在库内的移动。
35.a)信息管理系统将零件运至某个位置时触发入库指令,立体时效库运动机构移出空余的零件托盘;b)自动上下料机器人13从吊架15上取下零件放入零件托盘,并扫描托盘编码,传回信息管理系统,信息管理系统将零件与托盘编码统一,监控时效状态;c)时效完成后,信息管理系统向运动机构发出指令,运动机构将托盘移出,触发取件指令;d)自动上下料机器人13将零件放置于吊轨12上的吊架15,并扫描吊架15编码,传回信息管理系统,信息管理系统将零件和吊架15编码统一,实时监控零件状态。
36.2)成形区及数控铣切区运行场景如下:
a)信息管理系统根据零件加工信息,发出指令,将模具运至指定设备旁;b)大型模具通过自动上下模机19将模具移至成形设备20上,小型模具则需要先通过升降台将模具从高空钢轨16上取下,再通过自动上下模机19移至成形设备20上;c)同时,信息管理系统发出指令,将对应材料吊架15运至指定成形设备20旁,自动上下料机器人13将材料从吊架15上取下,放置到成形设备20上进行零件成形;d)成形完成后,自动上下料机器人13将零件取下,放置于堆垛平台8,待同一批次零件成形完后,再通过自动上下料机器人13装入吊架15中,并将吊架15编码反馈给信息管理系统;大型模具通过自动上下模机19移至轨道6上的轨道小车5上,小型模具则需要先通过自动上下模机19将模具移至轨道小车5,再通过模具升降台18将轨道小车5连同模具移至高空钢轨16上,完成后将轨道小车5编码反馈给信息管理系统;e)信息管理系统根据零件加工信息判定零件是否需要热处理及二次成形,若需要,则系统发出指令让装载零件的吊架15转入热处理区进行热处理,再返回进行二次成形;f)零件成形完毕后,信息管理系统根据零件加工信息判定零件是否需要进行数控铣切加工,若不需要,则信息系统发出指令,将模具及零件通过轨道小车5和吊架15运至交检区;若需要,对于自然时效零件则通过吊架15转入立体自然时效库17中,完成时效后再运至数控铣切设备21,对于人工时效零件,则通过吊架15将其转入热处理区,完成人工时效后将零件运至数控铣切设备21;g)对于需要铣夹进行铣切的零件,大型铣夹则通过自动上下模机19将模具移至数控铣切设备21上,小型铣夹则需要先通过升降台将铣夹从高空钢轨16上取下,再通过自动上下模机19移至数控铣切设备21上;h)自动上下料机器人13将零件从吊架15上取下,放置于铣夹上进行数控铣切;i)铣切完成后,自动上下料机器人13将零件放在旁边的堆垛平台8上,待同一批次零件铣切完成后,通过自动上下料机器人13转入吊轨12上的吊架15,并反馈吊架15编码给信息管理系统,信息管理系统将零件与吊架15编码连接,监控运输状态。
37.(5)交检区物流系统设计大部分航空钣金零件需要100%检查,因此,设计交检区用于零件检验或下一工序的转运(如转运至表处单位进行喷漆或装配单位进行装配、铆接等)。交检区物流系统如图6所示,其运行场景如下:a)信息管理系统发出指令,通过轨道小车5将模具运至检验台22,对于大型模具则通过自动上下模机19将模具移至检验台22上,小型模具则需要先通过升降台将模具从高空钢轨16上取下,再通过自动上下模机19移至检验台22上;b)信息管理系统发出指令,通过吊轨12上的吊架15将零件移至检验台22旁,再通过自动上下料机器人13将零件取下,放置于检验台22上;c)检验合格后,自动上下料机器人13将零件放置于旁边的堆垛平台8上,待同一批次零件检验完成后,再转入运输车23交付给其他加工单位,并将信息反馈信息管理系统;d)检验完成后,模具则通过自动上下模机19移至地轨6或高空钢轨16的轨道小车5上(小型模具需要通过升降台移至高空钢轨16上),并将轨道小车5编码反馈给信息管理系统,监控模具运输状态。
38.实施例2
本实施例公开了一种用于航空钣金件制造的智能物流系统的使用方法,某航空钣金零件制造工艺流程为“下料
→
热处理(去应力退火)
→
成形
→
二次热处理(固溶处理)
→
二次成形
→
自然时效
→
数控铣切-检验”,模具为大型模具,以该零件为例进行说明。需要说明的是,信息管理系统实时监控并更新模具、材料、零件在物流系统中的状态,因此,以下实施例中不再特别说明信息需要反馈给信息管理系统。请参阅图1:1)信息管理系统收到零件加工指令后,根据零件毛料信息进行自动排料,并将排料信息传递给自动下料机7;2)信息管理系统驱动取料机9从堆垛平台8上取出整板原材料,放置于自动下料机7上,根据排料信息进行下料;3)取料机9将下好的料放入分料区10上,并将信息反馈给信息管理系统;4)自动上下料机器人13将材料取出,装入吊轨12上的吊架15中;5)信息管理系统驱动吊架15运至热处理炉11旁,自动上下料机器人13将材料从吊架15上取下,放置于热处理炉11中;6)热处理完成后,信息管理系统驱动自动上下料机器人13将材料移至吊架15上,并驱动吊架15移至成形设备20旁;7)信息管理系统驱动自动桁车2从堆栈式立体库4中取出模具(若模具不在最上层,则需要通过缓存区3来临时存放该模具上方的模具),放置于地轨6上的轨道小车5上;8)轨道小车5移至模具升降台18时,传感器扫描模具信息,并反馈给信息管理系统;9)信息管理系统根据模具台账信息,判定其为大型模具,则指令模具升降台18不启动,并命令轨道小车5移至成形设备20旁;10)自动上下模机19将模具移至成形设备20上,自动上下料机器人13将材料从吊架15上取下,放置于模具上,开始成形零件,成形后的零件临时放置于堆垛平台8上;11)一批次零件成形完成后,自动上下模机19将模具移至轨道小车5上,返回模具库,自动上下料机器人13将堆垛平台8上的零件转入吊架15中;12)信息管理系统根据零件加工信息判定需要进行二次热处理,指令装载零件的吊架15运至热处理炉11旁边,并通过自动上下料机器人13将零件转入热处理炉11中进行处理;13)完成后,自动上下料机器人13将零件从热处理炉11中转入吊架15中,运至热处理槽14中进行处理;14)完成后,自动上下料机器人13将零件从热处理槽14移至吊架15中,并指令吊架15移至成形设备20旁;15)重复7)~11)进行零件二次成形;16)信息管理系统基于零件加工信息判定零件需要自然时效,指令吊架15至立体模具库1,自动上下料机器人13将零件从吊架15中取下,装入立体模具库1中的零件托盘上;17)自然时效完后,装载时效零件的零件托盘移出立体自然时效库17,自动上下料机器人13将零件转入吊架15中;18)信息管理系统根据零件加工信息,判定零件需要进行数控铣切且需要大型铣夹(模具中的一种),需要重复7)~9),将大型铣夹移至数控铣切设备21旁,同时指令装载零
件的吊架15移至数控铣切设备21旁;19)信息管理系统指令自动上下模机19将大型铣夹移至数控铣切设备21上,同时指令自动上下料机器人13将零件从吊架15上取下,放置于大型铣夹上,进行零件铣切,铣切后的零件暂时存放于堆垛平台8上;20)一批次零件铣切完成后,自动上下模机19将模具移至轨道小车5上,返回模具存放区,自动上下料机器人13将堆垛平台8上的零件转入吊架15中;21)重复7)~9),将检验模具移至检验台22旁,指令装载零件的吊架15移至检验台22旁;22)自动上下模将检验模具移至检验台22上,自动上下料机器人13将零件从吊架15中取下放置于检验台22上,检验完成的零件暂时存放于堆垛平台8上。
39.23)一次零件检验完成后,自动上下模机19将检验模具移至轨道小车5上,返回模具存放区,零件则装入运输车23中,转运至下个生产单位。
再多了解一些
本文用于企业家、创业者技术爱好者查询,结果仅供参考。