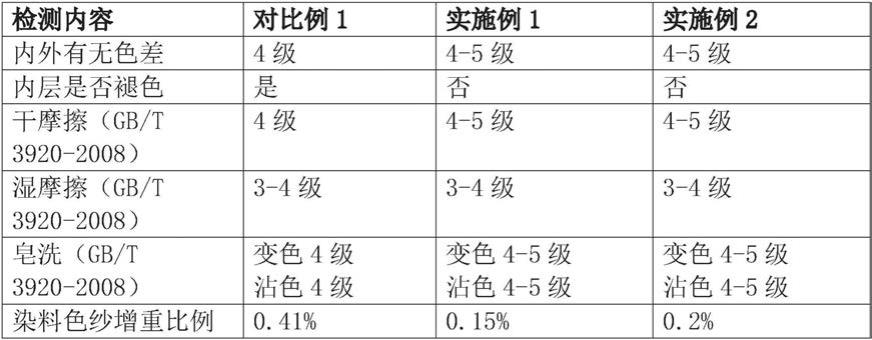
1.本发明涉及筒子纱染色技术领域,尤其涉及一种深红色的筒子纱染色方法。
背景技术:
2.据统计染整行业每年出口纺织线类约15万吨,工厂染色平均正品率为98.5%,其中深红色系的筒子纱染色过程中褪色及筒脚问题约占0.3-0.5个点,工厂成本浪费极大,质量改善刻不容缓。
3.现有针对深红色的涤纶筒子纱的染色方法主要包括进缸温度控制、中段温度控制,保温时间,后期高温控制及保温时间,然后再进行烧碱保险粉后处理,除浮色固色等,工艺时间耗时130分钟。其具体的染色方法采用侵染半浴方式,即半缸水,染料,助剂进缸后,进纱,直升温90度保温10分钟,在升温到130度保温30分钟,上色完成,排残液降温至70度后,进水,加后处理助剂,升温至90度保温15分钟第一次后处理完成,排出残留染液,在进水加入后处理助剂过酸升温到70度保温7分钟,第二次后处理完成,在进满浴水洗5分钟,排水,染色整道工序完成。但此种染色方法,染色工艺时间长,水电气成本高,且容易出现颜色色差、褪色、内层颜色层差等质量问题,后道生产静电及灰尘较多,影响员工工作环境,且此种染色方法在后处理过程中会使用化学物品,化学物品的使用对产品质量存在一定风险。
4.因此有必要对深红色的筒子纱的染色配方和染色方法进行改进,解决现有技术问题。
技术实现要素:
5.本发明要解决的技术问题在于解决此种染色方法,染色工艺时间长,水电气成本高,且容易出现颜色色差、褪色、内层颜色层差等质量问题,后道生产静电及灰尘较多,影响员工工作环境等技术问题,本发明解决其技术问题所采用的技术方案是:
6.一种深红色的筒子纱染色方法,包括如下步骤:
7.s1:选取重量规格为1.4kg/个的筒子纱,进行压边角处理;
8.s2:染色:采用侵染半浴正循环方式,半染缸水加入一定比例的染料、染色助剂后,加入经所述步骤s1处理过的筒子纱,其中染缸由初始温度50度升温到130度后保温30分钟,完成上色,排出残留染液;
9.其中;染料用量为待染筒子纱个重的1.54%;
10.其中;染色助剂用量为染缸浴量的2.7g/l;
11.s3:后处理:经所述步骤s2染色后的筒子纱,降温至70度后,进水,加后处理助剂,升温到90度后保温10分钟进行固色,排水,再满浴水洗一道,排水,染色完成;
12.其中;后处理助剂用量为染缸浴量的3g/l。
13.优选的,所述染料分别包括按待染筒子纱个重的0.0225%的200%se/4rf橙,1.52%的200%se/2gf红玉、0.0044%的200%hgf深蓝。
14.优选的,所述染色助剂包括用量为染缸浴量的0.7g/l的冰醋酸和2g/l高温匀染
剂。
15.优选的,所述后处理剂包括用量为染缸浴量的1g/l的冰醋酸和2g/l的还原剂。
16.优选的,所述步骤s2中的升温过程还包括先将初始温度直升温到90度保温5分钟后在由90度按每分钟升温2度到130度进行保温。
17.优选的,所述筒子纱的密度控制在0.44-0.46克/立方厘米之间,高度控制在15.5厘米,直径控制在16.5-17厘米之间。
18.优选的,所述步骤s2和所述步骤s3进行染色和后处理时,染缸内的泵力扬程为最大值。
19.优选的,所述步骤s2和所述步骤s3进行染色和后处理时,染缸内部压力控制在5kg以上。和现有技术相比,本发明的有益技术效果在于:
20.1、选用染料的色光(色光是指染料的鲜艳度,一定比例的相似度,其本身的浓度不同)、类型(分散染料的类型分为低温型、中温型和高温型,本发明中对比例和实施例中采用染料都属于高温型染料)一致,采用高力份染料取代低力份染料,有利于改善染色时间,降低劳动强度。
21.2、新染料配方的使用,使得染料的配方总用量下降约43.4%。
22.3、染色助剂用量不变,省去后处理过酸及保温时间等步骤,杜绝烧碱、保险粉的使用,工艺时间明显缩短,提升了染色工艺效率。
23.4、工艺调整后色纱染料残留物明显减少,之前测算普通染料色纱增重比例0.35%
‑‑
0.5%,随着配方用量的增减,色纱增重随之改变,目前测算得出同样颜色用200%红玉进行染色,色纱增重在0.15%-0.2%之间,染色残留物下降一倍。
24.5、后道作业环境及设备清洁度大为改善,筒子纱染色后存在的色纱褪色、筒脚等质量问题得到解决。
25.6、行业中普遍使用的是1kg/只或1.1kg/只的筒子纱染色,不仅生产效率低,成本高且污水排放也是居高不下,本方法采用1.4kg的筒子纱染色,提高生产效率,进一步有效降低水电气消耗成本。
具体实施方式
26.为了使本发明的目的、技术方案及优点更加清楚明白,下文将描述了实现本发明采用的实施例。应明白,还可使用其他的实施例,或者对本文所举的实施例进行结构和功能上的修改,而不会脱离本发明的范围和实质。
27.一种深红色的筒子纱染色方法,包括如下步骤:
28.s1:选取重量规格为1.4kg/个的筒子纱,进行压边角处理。
29.筒子纱进行压边角处理后,便于染色过程中染料与纱的接触,不会出现边角颜色色花。
30.s2:染色:采用侵染半浴正循环方式,半染缸水加入一定比例的染料、染色助剂后,加入经所述步骤s1处理过的筒子纱,其中染缸由初始温度50度升温到130度后保温30分钟,上色完成,排出残留染液,在进行后处理;
31.其中;染料用量按待染筒子纱的个重的1.54%加入;即需要染1000kg纱时需要15.4kg染料。
32.其中;染色助剂用量按染缸浴量的2.7g/l加入;即染缸浴量为1000l,则需要加入2700ml的染色助剂。
33.s3:后处理:经步骤s2染色后的筒子纱进行一道满浴水洗,在加入一定比例的后处理助剂升温到90度进行固色,在水洗一道,染色完成;
34.其中;后处理助剂用量按染缸浴量的3g/l加入,即染缸浴量为1000l,则需要加入3000ml的染色助剂。
35.进一步的,染料分别包括包括按待染筒子纱个重的0.0225%的200%se/4rf橙,1.52%的200%se/2gf红玉、0.0044%的200%hgf深蓝。
36.通过高力份染料取代低力份染料的使用,工艺的调整色纱染料残留物明显减少,之前测算普通染料色纱增重比例大约为0.35%-0.5%,随着配方用量的增减,色纱增重随之改变,测算得出同样颜色用200%红玉,筒子纱的色纱增重在0.15%-0.2%之间,染色残留物下降一倍,后道作业环境及设备清洁度大为改善,车间因色纱褪色、筒脚等质量问题也得到有效解决。
37.进一步的,染色助剂用量为染缸浴量的0.7g/l的冰醋酸和2g/l高温匀染剂。
38.进一步的,冰醋酸采用浓度为98%冰醋酸,高温匀染剂可采用sydiogen gk liq conc型高浓高温匀染剂。
39.进一步的,后处理剂用量为染缸浴量的1g/l的冰醋酸和2g/l的还原剂。
40.进一步的,冰醋酸采用浓度为98%冰醋酸,还原剂可采用江北粘合剂厂的酸性还原剂。
41.进一步的,步骤s2中的升温过程还包括先将初始温度50度直升温到90度保温5分钟后在由90度按每分钟升温2度到130度进行保温。
42.进一步的,筒子纱的密度控制在0.44-0.46克/立方厘米之间,高度控制在15.5厘米,直径控制在16.5-17厘米之间。
43.筒子纱密度过小会影响筒子纱直径的控制及产品成型,密度过大会严重影响染色质量,无法均匀染色造成次品,同时筒子纱密度成型控制好就可以达到筒子纱高度控制的要求,并且筒子纱的直径过长就是密度过小不利于染色产品成型,直径短就是密度过大不利于染色质量。因此,筒子纱密度、高度、直径的三个要素是环环相扣紧密相连的关系,任何一个环节出现问题,都会对质量造成不同程度的影响。
44.进一步的,步骤s2和步骤s3进行染色和后处理时,染缸内的泵力扬程为最大值,染缸扬程越高,水压就越大,染料对筒子纱穿透越好,可确保染液穿透纱层,均匀上色。
45.进一步的,步骤s2和步骤s3进行染色和后处理时,染缸内部压力控制在5kg以上,压力维持在5kg,对于涤纶材质的纱线的膨胀程度越有利,从而使分散染料可以充分的吸附到纱线上,进行上色。
46.对比例一
47.在本对比例一中,染料采用100%的s/4rf黄棕、100%的s/5bln红玉、200%的深蓝hgf,其中染料用量占筒子纱个重分别为0.03%、3.5%、0.0048%,当染100支1.4kg的筒子纱时,染缸浴量为850l,染色过程如下:
48.s1:选取重量规格为1.4kg/个的筒子纱,进行压边角处理,选用的筒子纱密度为0.46克/立方厘米,高度为15.5厘米,直径为16.6厘米;
49.s2:染色方法采用侵染半浴正循环方式,即半缸水,染料,染料助剂进缸后,进纱,直升温90度保温10分钟,在升温到130度保温30分钟,排残液、上色完成;
50.进一步的,初始温度50度直升温到90度保温10分钟后在由90度按每分钟升温2度到130度进行保温。
51.进一步的,染料助剂用量按染缸浴量的0.7g/l冰醋酸和2g/l高温匀染剂,即染缸浴量为850l,加入的冰醋酸为595ml,高温匀染剂为1700ml。
52.s3:后处理:降温至70度后,进水,加后处理助剂1,升温至90度保温15分钟第一次后处理完成,排出残留染液,在进水加入后处理助剂2过酸升温到70度保温7分钟,第二次后处理完成,在进满浴水洗5分钟,排水,染色整道完成。
53.具体的,加入的后处理助剂1为按染缸浴量的1g/l的冰醋酸、2g/l的还原剂、0.5g/l的氢氧化钠、0.5g/l的连二亚硫酸钠;即染缸浴量为850l,加入的冰醋酸为850ml,还原剂为1700ml,氢氧化钠为440ml,连二亚硫酸钠为440ml。
54.加入的后处理剂2为按染缸浴量的1g/l的冰醋酸,即染缸浴量为880l,加入的冰醋酸为880ml。
55.经上述步骤染成的筒子纱经测试,染料色纱增重比例为0.41%、内层颜色与外层颜色差异大,内层褪色,有0.35毫米筒脚纱需报废,里层杂质残留较多,灰尘大,存在质量隐患。
56.实施例一
57.在本实施例中,染料采用200%的s/4rf橙、200%的s/5bln红玉、200%的深蓝hgf,其中染料用量按筒子纱个重分别为0.0225%、1.52%、0.0044%,当染100只1.4kg的筒子纱时,染缸浴量为850l,染色过程如下:
58.s1:选取重量规格为1.4kg/个的筒子纱,进行压边角处理,选用的筒子纱密度为0.46克/立方厘米,高度为15.5厘米,直径为16.6厘米。
59.s2:染色方法采用侵染半浴正循环方式,即半缸水,染料,染料助剂进缸后,进纱,直升温90度保温5分钟,在升温到130度保温30分钟,排残液、上色完成。
60.具体的,初始温度50度直升温到90度保温5分钟后在由90度按每分钟升温2度到130度进行保温。
61.具体的,染料助剂按染缸浴量的0.7g/l冰醋酸和2g/l高温匀染剂,即染缸浴量为850l,加入的冰醋酸为595ml,高温匀染剂为1700ml。
62.s3:后处理:降温至70度后,进水,加后处理助剂,升温至90度保温10分钟进行固色,在水洗一道,染色完成。
63.具体的,加入的后处理助剂1为按染缸浴量的1g/l的冰醋酸、2g/l的还原剂;即染缸浴量为850l,加入的冰醋酸为850ml,还原剂剂为1700ml。
64.与对比例1相比,本实施例1采用高力份染料取代低力份染料,经上述步骤染成的筒子纱经测试,染料色纱增重比例为0.15%、内层颜色与外层颜色相差不大,无筒脚纱报废和褪色现象,里层少量杂质,与品质无影响。染料配方总用量下降,染色助剂用量不变,其染色过程中保温时长缩短,后处理时取消了烧碱、保险粉的使用,但仍可以满足产品的品质要求,相对比,整体提升了染色工艺效率并减少了产品化学品残留物,有效保障了产品品质,避免出现色纱褪色、筒脚等质量问题。
65.实施例二
66.在本实施例中,染料采用200%的s/4rf橙、200%的s/5bln红玉、200%的深蓝hgf,其中染料用量按筒子纱个重分别为0.0225%、1.52%、0.0044%,当染100只1.4kg的筒子纱时,染缸浴量为850l,染色过程如下:
67.s1:选取重量规格为1.4kg/个的筒子纱,进行压边角处理,选用的筒子纱密度为0.44克/立方厘米,高度为15.5厘米,直径为16.7厘米
68.s2:染色方法采用侵染半浴正循环方式,即半缸水,染料,染料助剂进缸后,进纱,直升温90度保温5分钟,在升温到130度保温30分钟,排残液、上色完成。
69.具体的,初始温度50度直升温到90度保温5分钟后在由90度按每分钟升温2度到130度进行保温。
70.具体的,染料助剂用量为染缸浴量的0.7g/l冰醋酸和2g/l高温匀染剂,即染缸浴量为850l,加入的冰醋酸为595ml,高温匀染剂为1700ml。
71.s3:后处理:降温至70度后,进水,加后处理助剂,升温至90度保温10分钟进行固色,在水洗一道,染色完成。
72.具体的,加入的后处理助剂1为按染缸浴量的1g/l的冰醋酸、2g/l的还原剂;即染缸浴量为850l,加入的冰醋酸为850ml,还原剂剂为1700ml。
73.与实施例1相比,本实施例更改了带染色筒子纱的密度、直径,其他染色程序不变,经上述步骤染成的筒子纱经测试,染料色纱增重比例为0.2%、内层颜色与外层颜色相差不大,无筒脚纱报废和褪色现象,里层少量杂质,与品质无影响,符合实际生产质量要求。
74.如下表1为对比例1、实施例1、实施例2筒子纱染色性能对比表:
[0075][0076]
表1
[0077]
以上所述仅为本发明的较佳实施例而已,本领域技术人员知悉,在不脱离本发明的精神和范围的情况下,可以对这些特征和实施例进行各种改变或等同替换。另外,在本发明的教导下,可以对这些特征和实施例进行修改以适应具体的情况及材料而不会脱离本发明的精神和范围。因此,本发明不受此处所公开的具体实施例的限制,所有落入本技术的权利要求范围内的实施例都属于本发明的保护范围。
再多了解一些
本文用于企业家、创业者技术爱好者查询,结果仅供参考。