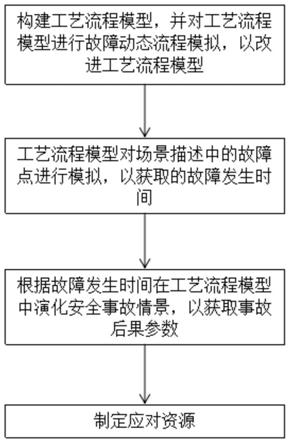
1.本发明涉及油站应急处置方法,更具体地说,它涉及一种输油站混油蒸馏装置安全生产的情景构建系统及方法。
背景技术:
2.管道运输因相比其他运输方式,具有安全性高、投资成本低、运输效率高、环境友好等特点,被世界各国广泛接收,并大量应用于内陆区域的成品油运输。如今,随着市场对石油产品的不断需求,输油管道建设已经成为国家的重点工程,对国民经济的发展有着重大影响。成品油输油管道系统主要由输油管线和输油站两大部分构成,成品油在起点输油站(首站)被收集并计量后,由输油泵提供动力向下游管道进行输送。若油品输送距离较长,则需要多级输油站提供输送动力,直至终点。我国成品油管道采用“从泵到泵”密闭、顺序输送工艺,把流向相同的几种油品沿一条管道输送,以使得经济效益最高。然而在顺序输油过程中,相邻批次油品必定产生混油,混油的处理是长距离成品油管道顺序输送和油品储存重要生产环节。当混油量小时,可以采取掺混处理;混油量大时,传统混油回掺的办法已经不能满足管道正常运行的需要,运至炼厂回炼成本太高。所以通过在输油末站配套蒸馏装置进行混油蒸馏成为了最有效的方式。
3.混油蒸馏装置为汽、柴混油蒸馏塔系统,主要由常压蒸馏塔、管式加热炉、列管式换热器、化工离心泵、回流罐、重沸炉、塔顶冷凝器、循环油管等设备组成。混油处理装置工艺流程较复杂、物料危险性高,属于甲类火灾危险装置。少数甚至单个设备问题、人员操作错误、突发外部环境变化等都可能进一步导致火灾、爆炸、毒气泄漏等大型事故,造成人员伤亡和重大经济损失。不仅如此,混油处理装置处于整个输油站生产作业系统,与其他重要区域直接或间接相连,其装置故障可能演化为更加严重的生产安全事故。由此可见,混油处理装置的事故风险管理是成品油管道运输行业安全生产与应急管理工作的重中之重,对维护国家成品油供应安全具有重要意义,必须高度予以关注。
4.然而,目前的重特大生产安全事故情景构建技术中,都聚焦于输油管道。面对输油站混油蒸馏装置这一具体对象时,不重视事故到底是如何发生的,尤其是大型化工设备这种具有明确工艺流程的对象。因此,现有方法和情景开发的侧重点并不适用于输油站混油蒸馏装置安全生产。总的来说,针对输油站内混油蒸馏装置的情景构建研究暂时还处于空白状态。
技术实现要素:
5.本发明要解决的技术问题是针对现有技术的不足,提供一种输油站混油蒸馏装置安全生产的情景构建系统及方法,解决了目前针对输油站内混油蒸馏装置的情景构建研究暂时还处于空白状态的问题。
6.本发明所述的一种输油站混油蒸馏装置安全生产的情景构建方法,包括:
7.工艺流程模型构建步骤,用于根据混油蒸馏装置,构建一工艺流程模型,对工艺流
程模型进行故障动态流程模拟,获取所述工艺流程模型的风险因素;并根据所述风险因素对工艺流程模型进行改进;
8.事故模拟步骤,用于根据历史事件对改进后的所述工艺流程模型进行场景描述,并设置所述场景描述中的故障点;所述工艺流程模型对故障点进行模拟,获取事故发生时间;
9.事故演化步骤,用于根据所述事故发生时间在工艺流程模型中演化安全事故情景,以获取事故后果参数。
10.通过工艺流程模型的构建,并以故障动态流程模拟以及事故演化获取混油蒸馏装置在实际事故过程中发生的事故后果。有效的分析了混油蒸馏装置事故形成的机理,验证了事故发生的可能性,同时科学地展现了工艺的发展规律以及危害结果,增强了对输油站混油蒸馏装置生产安全事故的认识。
11.所述故障动态流程模拟,具体包括,
12.通过所述工艺流程模型对混油蒸馏装置的进料流量扰动、塔顶冷凝器负荷故障和重沸炉扰动进行模拟分析,以获取所述工艺流程模型中存在的风险因素。
13.对混油蒸馏装置的进料流量扰动、塔顶冷凝器负荷故障和重沸炉扰动进行模拟分析,具体包括,
14.通过所述工艺流程模型对设定的进料流量的扰动值进行模拟运行,获取所述工艺流程模型在扰动值下的流量扰动变化曲线,根据所述流量扰动变化曲线判断工艺流程模型中存在的风险因素;
15.通过所述工艺流程模型对设定的塔顶冷凝器负荷变化值进行模拟运行,获取所述工艺流程模型在相应扰动值下的塔顶冷凝器负荷变化曲线,根据所述塔顶冷凝器负荷变化曲线判断工艺流程模型中存在的风险因素;
16.通过所述工艺流程模型对设定的重沸炉参数变化值进行模拟运行,获取所述工艺流程模型在重沸炉参数变化值下的热源流量变化曲线,根据所述热源流量变化曲线判断工艺流程模型中存在的风险因素。
17.获取所述事故发生时间的具体方法为,
18.根据所述混油蒸馏装置中循环油管的固有参数,计算所述循环油管的设计内压力;获取所述工艺流程模型运行在故障点时循环油管的内油品的参数变化曲线;根据所述设计内压力从参数变化曲线上查询事故发生时间。
19.所述设计内压力通过以下公式计算:
[0020][0021]
其中,p为设计内压力;d为管路平均直径;[σ]
t
为设计温度下材料的许用应力;t为壁厚。
[0022]
在故障动态流程模拟之前,还对工艺流程模型进行稳态流程模拟。
[0023]
所述稳态流程模拟具体包括:
[0024]
设定待处理油品的油品参数以及混油蒸馏装置的处理参数,通过所述工艺流程模型根据油品参数以及处理参数,对所述油品进行全流程稳定状态下的线上模拟,获取模拟参数;同时通过混油蒸馏装置实际处理所述油品,获取运行参数;将所述模拟参数与运行参
数进行比较,以验证所述模拟参数与运行参数的一致性。
[0025]
所述事故演化步骤还用于根据所述事故后果参数,制定所需的应对资源。
[0026]
所述应对资源包括专业救援处置资源、前期关键工艺处置资源、现场管理与协调资源、信息沟通与管理资源和应急保障资源。
[0027]
一种输油站混油蒸馏装置安全生产的情景构建系统,利用所述情景构建方法构建事故场景后进行事故模拟及演化,获取事故后果参数再输出至显示终端。
[0028]
有益效果
[0029]
本发明的优点在于:通过工艺流程模型的构建,并以故障动态流程模拟以及事故演化获取混油蒸馏装置在实际事故过程中发生的事故后果。有效的分析了混油蒸馏装置事故形成的机理,验证了事故发生的可能性,同时科学地展现了工艺的发展规律以及危害结果,增强了对输油站混油蒸馏装置生产安全事故的认识。同时针对事故后果可制定相应的应对资源,能更及时、快速、有效的控制火灾,并提供有效的救援力量,能大大的降低事故造成的损失。
附图说明
[0030]
图1为本发明的混油蒸馏装置安全生产的情景构建方法流程图;
[0031]
图2为本发明的工艺流程模型结构示意图;
[0032]
图3为本发明的工艺流程模型进料流量扰动对精馏塔柴油产品出料流量的影响;
[0033]
图4为本发明的工艺流程模型进料流量扰动对塔顶汽油产品出料流量的影响;
[0034]
图5为本发明的工艺流程模型进料流量扰动对精馏塔塔顶温度的影响;
[0035]
图6为本发明的工艺流程模型进料流量扰动对精馏塔塔顶压力的影响;
[0036]
图7为本发明的工艺流程模型塔顶冷凝器负荷减小85%时对塔底产品和塔顶产品流量的影响;
[0037]
图8为本发明的工艺流程模型塔顶冷凝器负荷降低85%对塔底和塔顶温度的影响;
[0038]
图9为本发明的工艺流程模型塔顶冷凝器负荷降低85%对塔顶压力的影响;
[0039]
图10为本发明的工艺流程模型重沸炉负荷降低90%时对塔底和塔顶产品流量的影响;
[0040]
图11为本发明的工艺流程模型重沸炉负荷降低90%时对塔底和塔顶温度的影响;
[0041]
图12为本发明的工艺流程模型重沸炉负荷降低90%时对塔顶压力的影响;图13为本发明的循环油管油品温度变化曲线图;
[0042]
图14为本发明的循环油管油品压力变化曲线图示意图;
[0043]
图15为本发明的应对资源结构示意图。
具体实施方式
[0044]
下面结合实施例,对本发明作进一步的描述,但不构成对本发明的任何限制,任何人在本发明权利要求范围所做的有限次的修改,仍在本发明的权利要求范围内。
[0045]
参阅图1,本发明的一种输油站混油蒸馏装置安全生产的情景构建方法,包括:
[0046]
工艺流程模型构建步骤,用于根据混油蒸馏装置,构建一工艺流程模型。对工艺流
程模型进行故障动态流程模拟,获取所述工艺流程模型的风险因素;并根据所述风险因素对工艺流程模型进行改进。
[0047]
工艺流程模型的构建是为了将混油蒸馏装置转移到线上,通过线上分析实现事故的演化,从而能从中获取相应的应对策略。本实施例的工艺流程模型是基于aspend plus软件构建的,主要基于实际的混油蒸馏装置的设备参数、工艺参数进行构建。其中,本实施例的工艺流程模型如图2所示。
[0048]
图2中,整个装置的核心设备是精馏塔t1001。混油从精馏塔t1001填料段的下部进料。辅助设备包括四台泵,分别是进料泵p1001、塔顶液回流泵p1002、塔釜出料及循环油泵p1003、燃油泵p1004;四台换热器,包括进料换热器e1004、进料换热器e1001、塔顶冷凝器e1002、塔釜产品冷却器e1003;还包括塔顶回流罐v1001、燃料油罐v1003和重沸炉f1001等。进料物流101经过泵p1001加压后经与e1004和e1001换热器换热两次后进入精馏塔t1001。塔顶物流经换热器e1004与进料物流换热降温后,经塔顶冷凝器e1002进一步水冷降温,进入回流罐v1001。回流罐出料经泵p1002加压后部分作为回流液回流入塔,部分作为汽油产品采出。塔底物料经泵p1003加压后部分经重沸炉加热后作为塔釜蒸汽进入塔下部,另一部分在e1001与进料换热降温后分出一小股进入燃料油罐,大部分经e1003进一步水冷降温后采出,作为塔釜柴油产品。燃料油罐内的燃油(主要是柴油)经燃油泵p1004输送,一部分进入重沸炉,作为燃料燃烧,使塔釜循环油管内柴油汽化,一部分回流至燃料油罐。可见,虽然整个精馏装置只有一股进料,两股出料,属于简单塔系统,但是辅助设备较多,且所处理物料是易燃易爆的汽、柴油产品,所以,装置操作危险性高,控制难度大。
[0049]
需要说明的是,由于aspen plus不能模拟重沸炉f1001内燃油燃烧过程,所以,本文将重沸炉f1001的热源改为与燃油燃烧炉火等温的高温空气流,利用高温空气物流加热循环油,产生精馏所需的蒸汽。
[0050]
为确保模拟结果的有效可靠,事故模拟步骤中,在故障动态流程模拟之前,还对工艺流程模型进行稳态流程模拟。稳态流程模拟的目的,一是考察模拟结果的可靠性;二是为动态流程模拟做准备。
[0051]
具体的,稳态流程模拟具体包括:
[0052]
设定待处理油品的油品参数以及混油蒸馏装置的处理参数。油品参数主要包括油品类别、组分信息等;处理参数主要包括混油蒸馏装置处理油品的物性方法、物流数据以及混油蒸馏装置的设备参数设定。通过工艺流程模型根据油品参数以及处理参数,对油品进行全流程稳定状态下的线上模拟,获取模拟参数。同时通过混油蒸馏装置实际处理油品,获取运行参数。将模拟参数与运行参数进行比较,以验证模拟参数与运行参数的一致性。若模拟参数与运行参数一致,则认为该工艺流程模型的模拟结果准确可靠;否则,其模拟参数将不能被采纳,工艺流程模型构建失败,需重新调整。
[0053]
优选的,运行参数为混油蒸馏装置对油品实际处理至少10次以上所获取的平均参数。采集混油蒸馏装置的实际运行次数越多,其参数的可信度越高,但同时也带来费时费力的问题。本实施例的实际处理次数优选为50次。
[0054]
而故障动态流程模拟,具体包括:
[0055]
通过工艺流程模型对混油蒸馏装置的进料流量扰动、塔顶冷凝器负荷故障和重沸炉扰动进行模拟分析,以获取工艺流程模型中存在的风险因素。风险因素即在工艺流程模
型运行时,不能很好的对工艺流程模型进行控制的位置或超出安全运行范围的扰动因素。改进时,只需对该位置进行重新设计改进或控制这些扰动因素即可避免混油蒸馏装置运行在具有故障风险的危险状态中。
[0056]
其中,对混油蒸馏装置的进料流量扰动、塔顶冷凝器负荷故障和重沸炉扰动进行模拟分析,具体包括,
[0057]
通过工艺流程模型对设定的进料流量的扰动值进行模拟运行,获取工艺流程模型在扰动值下的流量扰动变化曲线,根据流量扰动变化曲线判断工艺流程模型中存在的风险因素。
[0058]
混油由进料泵输入精馏塔t1001,在进料泵故障、电压波动或管道泄漏的情况下,可能导致进料流量发生变动,因此需要对其进行模拟分析。以下将以一具体实施例对其模拟分析的方法进行说明。
[0059]
首先将工艺流程模型的精馏塔t1001稳定运行流程2h,然后将进料流量增加10%或降低10%,继续运行流程,考察各流程变量随时间的变化规律。如图3-图6分别给出了进料流量扰动对精馏塔t1001柴油产品流量、塔顶汽油产品流量、塔顶温度及塔顶压力的影响。由图3可见,扰动发生后,精馏塔t1001产品流量均瞬时发生波动,波动方向与扰动方向一致,即进料流量增大,柴油产量也增大,反之亦然,并在2h内达到新的定态。相对于增加10%的扰动,进料流量减小10%对塔釜产品的流量影响更大。由图4可见,塔顶汽油产品流量在进料流量增加10%后很快达到新的定态。但是,塔顶产品流量在进料流量减小10%的扰动下,先瞬时下降到3000kg/h以下,之后缓慢升高,直到18h时刻仍未能达到新的定态。以上说明不同方向的扰动对产品流量的影响是不同的。由图5可见,在扰动发生时,塔顶温度瞬时朝与扰动相反的方向变化,之后迅速恢复到原定态值,且不再波动,说明塔顶温度控制器有很好的控制效果。由图6可见,随着进料量增加10%,塔顶压力瞬时减小,但减小幅度不大;之后,塔顶压力缓慢增加,并逐渐趋于定值。同时,在进料流量减小10%的情况下,塔顶压力先瞬时增大,而后随时间逐渐减小,但直到18h时刻仍未达到定值。由以上结果可见,进料扰动对精馏塔t1001运行有较大的影响,其中进料流量减小扰动的影响强于进料流量增加的影响,说明工艺流程模型中各控制器对不同方向的扰动的控制能力是不同的。相对而言,温度控制器有较强的控制能力,而压力控制器控制效果较差,特别是进料减小的情况下。不过压力减小一般不会对精馏塔t1001的安全运行产生严重影响。
[0060]
通过工艺流程模型对设定的塔顶冷凝器负荷变化值进行模拟运行,获取工艺流程模型在相应扰动值下的塔顶冷凝器负荷变化曲线,根据塔顶冷凝器负荷变化曲线判断工艺流程模型中存在的风险因素。
[0061]
对精馏塔t1001而言,塔顶冷凝器e1002是容易出现故障的设备。塔顶冷凝器e1002的故障主要是冷却介质泄露或流量不足导致塔顶冷凝器e1002负荷不够,冷凝效果变差。在对塔顶冷凝器e1002进行故障模拟分析时,首先使精馏塔t1001稳定运行2h,然后瞬时将塔顶冷凝器e1002e1002负荷减小85%,考察在故障工况下,精馏塔t1001的运行情况。如图7-图9分别给出了故障下塔顶产品流量、塔底产品流量、塔温及塔压随时间的变化。由图7可见,塔顶冷凝器e1002负荷减小时,塔顶汽油产品流量瞬时减小,并在1h内趋于稳定,最终稳态值低于初始值。由图8可见,塔顶冷凝器e1002负荷减小时,塔顶温度和塔釜温度均瞬时下降,但下降幅度不大,而后迅速上升并趋于稳定,最后稳态值和初值接近,说明温度控制器
tc1和温度控制器tc2也有很强的控制能力。由图9可见,随塔顶冷凝器e1002负荷减小,塔压迅速增加,且直到7h还未见稳定迹象,说明压力控制器还不能较好的控制塔压。因此,压力控制器即为工艺流程模型中存在的风险因素。所以,需对压力控制器进行调整,以使工艺流程模型运行得更加稳定。而对压力控制器的调整,可直接在aspen plus中进行操作。
[0062]
通过工艺流程模型对设定的重沸炉参数变化值进行模拟运行,获取工艺流程模型在重沸炉参数变化值下的热源流量变化曲线,根据热源流量变化曲线判断工艺流程模型中存在的风险因素。
[0063]
重沸炉f1001是精馏塔t1001热量的来源,是全塔温度最高的设备,也是最危险的设备之一。重沸炉f1001出现故障,要么使上升蒸汽不足,则不能得到合格的产品,且产品产量也会下降;要么上升蒸汽过量,且温度过高,也会导致出现液泛等危险工况,有时也会使塔压升高,甚至可能出现爆塔等极端危险事故。相对而言,重沸炉f1001负荷减小是更常见的故障,这可以由重沸炉f1001炉火由于某种原因突然熄灭引起,或者由于燃油泵p1004故障使燃油供应不足引起。针对重沸炉f1001故障的模拟分析,首先使精馏塔t1001稳定运行2h,然后,将重沸炉f1001热源流量减小90%,考察精馏塔t1001的运行情况。图10-图12分别给出了塔顶塔底产品流量、塔顶塔底温度及塔压随时间的变化情况。由图10可见,故障发生时,塔顶汽油产量先以较快的速度下降。运行4h后,其仍然呈下降趋势,但下降速度减慢。塔底柴油的产量变化则更为复杂。随着重沸炉f1001负荷降低,柴油产量瞬时减小,而后又瞬时上升;之后,又持续减小,在运行4h左右时其流量几乎降为0。接着,柴油流量很快上升并在5h左右达到新的稳态,新的稳态流量高于原稳态值。由于重沸炉f1001负荷降低,循环油温度降低,上升的蒸汽量必然减少,塔顶冷凝量也减少,回流罐液位下降,所以汽油产品流量持续降低。进料量不变的情况下,上升蒸汽减少,也使得塔釜柴油循环量增加,塔釜液位增加,最终使得柴油流量增加。但由于塔釜柴油流量受相连诸多管线流量的制约,所以在重沸炉f1001负荷突然降低时,在达到新的稳态前柴油流量呈现出较为复杂的变化趋势。
[0064]
图11给出了重沸炉f1001负荷降低90%时塔顶塔釜温度的变化。可见,塔顶塔釜温度均随着重沸炉负荷的下降而下降。图12给出了重沸炉f1001负荷降低90%时塔顶塔釜压力的变化。可见塔顶塔釜压力也随着重沸炉负荷的下降而下降。重沸炉f1001负荷降低90%时,塔底循环油温度下降,柴油汽化量显著减少,所以,全塔温度、压力必然都下降。温度、压力下降并不会对混油塔的安全运行造成严重影响,但是其也会导致所得产品不合格,所以也要尽可能避免。
[0065]
需要说明的是,故障动态流程模拟还可以包括对塔釜出料及循环油泵p1003、塔顶液回流泵p1002、进料换热器e1001等多个位置的多种动态变化、扰动进行模拟。但经试验分析,上述的进料流量扰动、塔顶冷凝器负荷故障和重沸炉扰动为对工艺流程模型影响较大的风险位置。因此,通过对进料流量扰动、塔顶冷凝器负荷故障和重沸炉扰动进行分析,可快速的得到工艺流程模型所存在的风险因素,且准确有效,大大的提高了对工艺流程模型的检验效率。
[0066]
再获得可靠的工艺流程模型后,即可进行事故模拟。
[0067]
事故模拟步骤,用于根据历史事件对改进后的所述工艺流程模型进行场景描述,并设置所述场景描述中的故障点。所述工艺流程模型对故障点进行模拟,获取事故发生时间。
[0068]
历史事件可参考国内外的油品蒸馏提炼的事故事件。根据历史事件,可获取混油蒸馏装置中易于产生故障的位置。如混油蒸馏装置的汽油泵易出现机封泄露、炉内超压等。据此,即可设一场景描述。如某月某日,混油蒸馏装置的汽油泵发生机封泄露。泄露的油品喷溅到高温柴油泵上,被迅速点燃,导致泵区起火。此时操控泵区停泵。燃油泵p1004因停泵失效,但重沸炉f1001炉火依然正常燃烧,炉管内停止流动的柴油将被迅速加热到高温并汽化。炉管内超过管道耐压极限发生破裂,油品泄露遇炉火发生爆炸。
[0069]
由于油品在爆炸时会产生喷射,因此,本实施例的场景描述中还增加了次生衍生灾害场景。如爆炸喷射的高温油滴落在事故现场附近的山林中,引燃灌木,导致上林起火。
[0070]
此外,场景描述中还预计工艺流程模型所产生的灾害参数。灾害参数包括预计人员伤亡情况、预计经济损失、预计恢复期限。根据现场的混油蒸馏装置,灾害参数可设为不同的值。
[0071]
获取事故发生时间的具体方法为,根据混油蒸馏装置中循环油管的固有参数,计算循环油管的设计内压力。
[0072]
其中,设计内压力通过以下公式计算:
[0073][0074]
其中,p为设计内压力;d为管路平均直径;[σ]
t
为设计温度下材料的许用应力;t为壁厚。以上均为循环油管的固有参数。
[0075]
通过以上公式计算出来的设计内压力即为循环油管的最大耐压值。当管内压力超出设计内压力时,管道即出现破裂漏油的故障,进而导致混油蒸馏装置出现爆炸安全事故。
[0076]
优选的,设计内压力应设一负误差值。负误差值的设定主要是考虑到循环油管在明火加热下长期使用,管出现氧化剥蚀,导致管壁变薄。因此其极限耐压能力必然会出现降低的情况。如直接采用计算出来的设计内压力,则会导致模拟出来的事故发生时间与实际发生时间出现延迟的现象,则不利于后续的应对资源布局。
[0077]
获取工艺流程模型运行在故障点时循环油管的内油品的参数变化曲线。本实施例的故障点为,将工艺流程模型的供油流量从正常值降为零。具体的,在工艺流程模型上模拟时,可通过设置模型中的柴油泵出口阀门开度来模拟泵的停运,进而考察工艺流程模型各模拟参数的变化规律。其关注重点在于循环油管内油品的温度变化以及压力变化。
[0078]
根据设计内压力从参数变化曲线上查询事故发生时间。即在参数变化曲线上查找出从停泵时刻起至循环油管内油压超出设计内压力时刻。这两个时刻间的时间即为事故发生时间。即,可认为从供油流量为零至循环油管发生爆炸所需时间为事故发生时间。
[0079]
如本实施例选用的是3mm壁厚的循环油管。其设计内压力计算值为4.7349mpa。进行误差取值后,其极限压力为4.73mpa。模拟后,其温度变化曲线如图13所示。当柴油泵停泵后,即流量为零时,循环油管内柴油的温度在5分钟即达到了460℃,5.5分钟达到了500℃。在通过图14的压力变化曲线可知,当柴油温度达到460℃时,管内压力将超过4mpa,已接近于管道极限。当温度在500℃时,管道压力已在5mpa以上。此时管道已发生破裂,事故已发生。
[0080]
事故演化步骤,用于根据事故发生时间和场景描述在工艺流程模型中演化安全事故情景,以获取事故后果参数。在事故发生时间以内,火灾仅限于泵区,可认为属于初期火
灾。如能在事故发生时间内将其扑灭,则不会带来较大的损失。但若不能扑灭,则将发生爆炸的安全事故。针对上述设定的场景描述,在预计的灾难参数内,即可获取事故后果参数。
[0081]
如3mm壁厚的循环油管在发生破裂导致重沸炉爆炸后,若预计人员伤亡为3人重伤、预计经济损失为3000万人民币、预计恢复期限为两个月。则通过工艺流程模型模拟得知,重沸炉内柴油体积为2.32m3,爆炸总能量为6.13
×
106kj,四五半径为15.22m,重伤范围为42.94m。据此,即可在初期火灾时进行有效的防控,以尽量降低事故进一步发展时造成的损伤。
[0082]
需要说明的是,事故后果参数的获取是根据“汽油储罐化学爆炸事故后果模拟分析”的指引进行模拟计算的。其为公开技术手段,本技术并不对其进行改进。
[0083]
事故演化步骤还用于根据事故后果参数,制定所需的应对资源。应对资源的制定能有效的确保在爆炸事故发生后起到即使灭火救援的作用,以将事故控制住,便于救灾抢险。其中,应对资源主要是结合输油站所在地区以及企业内部的相关应急预案,重点梳理应急预案中应急处置与救援、事故恢复与重建所应用的任务,最后将这些任务进行分类展开,形成如图15的应对资源结构示意图。图15中,应对资源包括专业救援处置资源、前期关键工艺处置资源、现场管理与协调资源、信息沟通与管理资源和应急保障资源。且每个资源下还包含有若干子资源。通过多资源关联的方式,能实现快速、有效、及时的灭火救灾。
[0084]
一种输油站混油蒸馏装置安全生产的情景构建系统,利用情景构建方法构建事故场景后进行事故模拟及演化,获取事故后果参数再输出至系统的显示终端。从而使工作人员能直观的获取事故后果参数。且系统还可通过事故后果参数制定所需的应对资源。通过应对资源,能有效的确保在爆炸事故发生后起到即使灭火救援的作用,以将事故控制住,便于救灾抢险。
[0085]
以上所述的仅是本发明的优选实施方式,应当指出对于本领域的技术人员来说,在不脱离本发明结构的前提下,还可以作出若干变形和改进,这些都不会影响本发明实施的效果和专利的实用性。
再多了解一些
本文用于企业家、创业者技术爱好者查询,结果仅供参考。