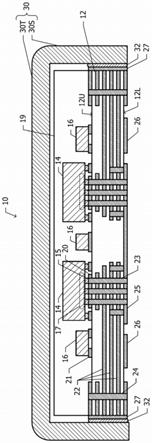
1.本发明涉及半导体封装件、半导体装置、半导体封装件搭载设备、以及半导体装置搭载设备。
背景技术:
2.移动终端等的发送电路的功率放大器使用半导体封装件。半导体封装件包含模块基板、和安装于该模块基板的半导体芯片以及表面安装部件等。半导体芯片经由设置于晶体管等的器件形成面的多个凸块安装于模块基板。半导体封装件安装于母基板,并与电源、其它的电子电路连接。
3.形成于半导体芯片的晶体管由于放大动作而自发热,随着温度上升晶体管的性能劣化。为了抑制晶体管的性能的劣化,优选高效地从作为发热源的晶体管向半导体芯片以及半导体封装件之外进行散热。在将半导体封装件安装于母基板(基底基板)的构成中,在半导体芯片产生的热量通过模块基板传导至母基板,并从母基板散热。
4.专利文献1:日本特开2006-120996号公报
5.若放大电路的输出变高,并且动作频率变高,则来自晶体管的发热量增大,所以期望进一步提高从半导体芯片的散热性。一般而言,来自半导体芯片的热量大部分经由母基板进行散热,所以提高从母基板向外部即装置的壳体、环境的散热性较重要。
6.但是,在一般的移动终端等中,不能说进行了在母基板与壳体之间得到足够的导热的设计。另外,由于母基板被封闭在壳体内的较窄的空间,所以也难以确保空气的对流带来的足够的散热量。
技术实现要素:
7.本发明的目的在于提供能够提高从半导体芯片的散热性的半导体封装件、半导体装置、半导体封装件搭载设备、以及半导体装置搭载设备。
8.根据本发明的一观点,提供一种半导体封装件,具备:
9.模块基板,具有相互朝向相反方向的上表面以及下表面;以及
10.半导体芯片,设置多个凸块,并经由上述凸块安装于上述模块基板的上表面,
11.上述模块基板包含配置于上述模块基板的下表面以及内层的至少一方的第一金属膜,上述第一金属膜与上述凸块电连接,并且到达上述模块基板的侧面,
12.还具备具有顶面部以及侧面部的金属部件,上述顶面部以上述模块基板的上表面为高度的基准配置在比上述半导体芯片高的位置,且在俯视时包含上述半导体芯片,上述侧面部从上述顶面部朝向上述模块基板延伸,
13.上述侧面部在上述模块基板的侧面与上述第一金属膜热结合。
14.根据本发明的其它的观点,提供一种半导体封装件,具备:
15.模块基板,具有相互朝向相反方向的上表面以及下表面;以及
16.半导体芯片,设置多个凸块,并经由上述凸块安装于上述模块基板的上表面,
17.上述模块基板包含:
18.金属焊盘,配置于在俯视时不与上述半导体芯片重合的区域的上表面;
19.第一金属膜,配置于上述模块基板的下表面以及内层的至少一方;以及
20.通孔导体,配置在俯视时与上述半导体芯片重合的位置,从上述模块基板的上表面到达下表面,并与上述凸块电连接,
21.上述金属焊盘经由上述第一金属膜与上述通孔导体电连接,
22.还具备具有顶面部以及侧面部的金属部件,上述顶面部以上述模块基板的上表面为高度的基准配置在比上述半导体芯片高的位置,且在俯视时包含上述半导体芯片,上述侧面部从上述顶面部朝向上述模块基板延伸,
23.上述侧面部与上述金属焊盘热结合。
24.根据本发明的其它的观点,提供一种半导体装置,具备:
25.半导体封装件,包含具有相互朝向相反方向的上表面以及下表面的模块基板、以及安装于上述模块基板的上表面的半导体芯片;以及
26.母基板,具有相互朝向相反方向的上表面以及下表面,在上表面安装上述半导体封装件,
27.上述母基板包含配置在上表面中不与上述半导体封装件重合的区域的金属焊盘、和配置于上述母基板的下表面以及内层的至少一方的第二金属膜,上述半导体封装件与上述金属焊盘经由上述第二金属膜电连接,
28.还具备具有顶面部以及侧面部的金属部件,上述顶面部以上述母基板的上表面为高度的基准配置在比上述半导体封装件高的位置,并且在俯视时包含上述半导体封装件,上述侧面部从上述顶面部朝向上述母基板延伸,
29.上述侧面部与上述金属焊盘热结合。
30.根据本发明的其它的观点,提供一种半导体封装件搭载设备,具备:
31.上述的半导体封装件;
32.壳体,收容上述半导体封装件;以及
33.热结合部件,使上述顶面部与上述壳体热结合。
34.根据本发明的其它的观点,提供一种半导体装置搭载设备,具备:
35.上述的半导体装置;
36.壳体,收容上述半导体装置;以及
37.热结合部件,使上述顶面部与上述壳体热结合。
38.形成从半导体芯片经由第一金属膜或者第二金属膜、以及金属部件的侧面部到达顶面部的导热路径。能够将顶面部利用为从半导体芯片到散热片的导热路径的一部分。其结果,能够提高从半导体芯片的散热性。
附图说明
39.图1是第一实施例的半导体封装件的剖视图。
40.图2是表示第一实施例的半导体封装件的各构成要素的俯视时的位置关系的图。
41.图3是搭载了第一实施例的半导体封装件的半导体封装件搭载设备的局部剖视
图。
42.图4是第一实施例的变形例的半导体封装件的剖视图。
43.图5是第一实施例的其它的变形例的半导体封装件的示意立体图。
44.图6是第二实施例的半导体封装件的剖视图。
45.图7是第二实施例的变形例的半导体封装件的剖视图。
46.图8是第三实施例的半导体封装件的剖视图。
47.图9是表示第三实施例的半导体封装件的各构成要素的俯视时的位置关系的图。
48.图10是第四实施例的半导体封装件的剖视图。
49.图11是将第四实施例的半导体封装件安装于母基板,并收容于壳体的状态的剖视图。
50.图12是第五实施例的半导体封装件的剖视图。
51.图13是第六实施例的半导体封装件的剖视图。
52.图14是第七实施例的半导体装置的剖视图。
53.图15是第七实施例的变形例的半导体装置的剖视图。
54.图16是第七实施例的其它的变形例的半导体装置的剖视图。
55.图17是第八实施例的半导体装置的剖视图。
56.图18是第八实施例的变形例的半导体装置的剖视图。
57.图19是第九实施例的半导体封装件搭载设备的剖视图。
58.图20是第九实施例的变形例的半导体封装件搭载设备的剖视图。
59.图21是第十实施例的半导体装置搭载设备的剖视图。
60.图22是第十一实施例的半导体装置搭载设备的剖视图。
61.图23是第十二实施例的放大电路的框图。
62.附图标记说明
63.10
…
半导体封装件,11
…
半导体装置,12
…
模块基板,12l
…
模块基板的下表面,12u
…
模块基板的上表面,14
…
半导体芯片,15
…
凸块,16
…
表面安装部件,17
…
发热源,19
…
密封树脂,19a
…
开口,20、21
…
上表面的金属焊盘,22
…
第一金属膜(接地层),22a
…
设置于第一金属膜的开口,23、24
…
通孔导体,25、26
…
下表面的金属焊盘,27
…
侧面金属膜,28
…
上表面的金属焊盘,29
…
下表面的金属焊盘,30
…
金属部件,30s
…
侧面部,30t
…
顶面部,32
…
导热接合材料,35
…
金属帽,35s
…
侧面部,35t
…
顶面部,40
…
背面金属膜,41
…
印刷电路基板,42、43
…
金属膜,44
…
通孔导体,45、46
…
焊料,47
…
导热板,50
…
金属膜,51
…
通孔导体,60
…
母基板,60l
…
母基板的下表面,60u
…
母基板的上表面,61
…
第二金属膜,63、64
…
通孔导体,65、66、67、68
…
母基板的金属焊盘,70、71、72、73
…
焊料,90
…
壳体,91、92、93
…
热结合部件,95、96、97
…
导热路径,98a
…
第一导热路径,98b
…
第二导热路径,101
…
驱动级放大器,102
…
功率级放大器,103、104
…
阻抗匹配电路,105
…
输入端子,106
…
输出端子,107、108
…
电感器,110、111
…
直流电源。
具体实施方式
64.[第一实施例]
[0065]
参照图1~图3的附图,对第一实施例的半导体封装件、以及半导体封装件搭载设
备进行说明。
[0066]
图1是第一实施例的半导体封装件10的剖视图。第一实施例的半导体封装件10包含模块基板12、多个半导体芯片14、以及金属部件30。模块基板12具有相互朝向相反方向的上表面12u以及下表面12l。在多个半导体芯片14各自的器件形成面设置多个凸块15。多个半导体芯片14经由多个凸块15倒置(face down)安装于模块基板12的上表面12u。在半导体芯片14的器件形成面形成有多个晶体管,多个晶体管成为发热源17。
[0067]
此外,也可以构成为将一个半导体芯片14安装于模块基板12。在模块基板12的上表面12u还安装电感器、电容器等多个表面安装部件16。
[0068]
在模块基板12的上表面12u设置有多个金属焊盘20、21。半导体芯片14的多个凸块15通过焊料等与多个金属焊盘20连接。多个表面安装部件16通过焊料等与其它的多个金属焊盘21连接。
[0069]
在模块基板12的内层配置有作为接地层的多个第一金属膜22。作为模块基板12,例如使用多层印刷电路基板。在模块基板12的内层也配置有第一金属膜22以外的其它的多个金属布线、金属膜等。
[0070]
多个第一金属膜22在俯视时在与半导体芯片14重合的区域内,经由配置在模块基板12内的多个通孔导体23与一部分的金属焊盘20连接。即,第一金属膜22与半导体芯片14的一部分的凸块15电连接。第一金属膜22所电连接的凸块15例如是半导体芯片14的接地用的凸块。第一金属膜22从在俯视时与半导体芯片14重合的位置通过与表面安装部件16重合的区域扩展至模块基板12的侧面,且第一金属膜22的端面在模块基板12的侧面露出。
[0071]
在模块基板12的下表面12l设置有金属焊盘25、26。连接第一金属膜22与半导体芯片14的凸块15的通孔导体23从模块基板12的上表面12u到达下表面12l,并与设置于下表面12l的金属焊盘25连接。多个第一金属膜22在模块基板12的侧面的附近,通过多个通孔导体24相互连接。多个通孔导体24到达模块基板12的上表面12u以及下表面12l,并与分别配置于上表面12u以及下表面12l的金属膜连接。
[0072]
多个通孔导体23、24例如既可以由填埋贯通模块基板12的贯通孔的金属部件形成,也可以由模块基板12内的布线层、和填埋设置于布线层间的绝缘膜的内通孔的金属部件形成。第一金属膜22、上表面12u的金属焊盘20、21、下表面12l的金属焊盘25、26、通孔导体23、24、以及其它的金属布线、金属膜例如能够使用铜。
[0073]
也可以将第一金属膜22配置于模块基板12的下表面12l,也可以将多个第一金属膜22配置在模块基板12的内层与下表面12l双方。即,第一金属膜22只要配置于模块基板12的内层以及下表面12l的至少一方即可。
[0074]
多个半导体芯片14以及多个表面安装部件16被密封树脂19密封。在模块基板12的侧面配置侧面金属膜27。例如通过将铜进行电镀形成侧面金属膜27。侧面金属膜27在模块基板12的侧面与第一金属膜22连接。
[0075]
帽状的金属部件30从密封树脂19侧覆盖在模块基板12上。金属部件30具有以模块基板12的上表面12u为高度的基准配置在比半导体芯片14高的位置的顶面部30t、以及从顶面部30t朝向模块基板12延伸的侧面部30s。在俯视时,顶面部30t包含多个半导体芯片14。
[0076]
金属部件30的侧面部30s通过导热接合材料32固定于侧面金属膜27。作为导热接合材料32,例如能够使用焊料、导热膏体等。由此,金属部件30的侧面部30s在模块基板12的
侧面,经由导热接合材料32以及侧面金属膜27与第一金属膜22热结合。这里,“热结合”是指两个部件不经由模块基板12的绝缘层、密封树脂等绝缘材料,而经由与绝缘材料相比导热率足够高的材料结合,或者直接结合。例如,在两个部件仅经由导热率在10w/m
·
k以上的材料结合的情况下,能够称为这两个部件热结合。另外,在两个导电部件电连接的情况下,这两个导电部件不能说热结合。
[0077]
图2是表示第一实施例的半导体封装件10的各构成要素的俯视时的位置关系的图。在图2中,省略信号布线的记载,对金属部件30的侧面部30s、以及第一金属膜22附加影线。此外,在图2示出图1所示的三层的第一金属膜22中一层的第一金属膜22。在长方形的模块基板12的内层配置有第一金属膜22。第一金属膜22具有在与模块基板12的四个顶点对应的位置切掉为正方形的外形,切掉的位置以外的边缘在模块基板12的四个侧面露出。在第一金属膜22的中央设置有长方形的开口22a。在开口22a的内部例如配置信号布线。
[0078]
将两个半导体芯片14配置为在俯视时夹着开口22a。并且,在模块基板12安装有多个表面安装部件16。例如,一个表面安装部件16配置在开口22a内,其它的多个表面安装部件16配置在与第一金属膜22重合的位置。在半导体芯片14设置有多个凸块15。在俯视时在半导体芯片14的内侧配置有多个通孔导体23,在模块基板12的侧面的稍靠内侧配置多个通孔导体24。一部分的凸块15分别配置在俯视时与通孔导体23重合的位置。
[0079]
在模块基板12的四个侧面分别配置有侧面金属膜27。侧面金属膜27与第一金属膜22连接。金属部件30的侧面部30s在俯视时从四方包围模块基板12。侧面部30s在模块基板12的四个侧面,通过导热接合材料32与侧面金属膜27连接。
[0080]
图3是搭载了第一实施例的半导体封装件10的半导体封装件搭载设备的局部剖视图。半导体封装件搭载设备例如是移动终端。母基板60具有相互朝向相反方向的上表面60u以及下表面60l。在母基板60的上表面60u设置有多个金属焊盘65、66、67。金属焊盘65在俯视时与半导体芯片14重合,金属焊盘67在俯视时与模块基板12的侧面重合。
[0081]
设置于模块基板12的多个金属焊盘25通过焊料70与母基板60的上表面60u的金属焊盘65连接。并且,半导体封装件10的多个金属焊盘26分别通过焊料71或者72与设置于母基板60的金属焊盘66或者67连接。通过将半导体封装件10的金属焊盘25、26与母基板60的金属焊盘65、66、67连接,半导体封装件10安装于母基板60。
[0082]
在母基板60的内层以及下表面60l配置有多个第二金属膜61。多个第二金属膜61通过从上表面60u到达下表面60l的多个通孔导体63相互连接,并且与上表面60u的金属焊盘65连接。
[0083]
半导体封装件10以及母基板60收容于壳体90。例如由铝等金属形成壳体90的一部分。金属部件30的顶面部30t通过热结合部件91安装于壳体90的内侧的表面例如金属部分的内侧的表面。金属部件30经由热结合部件91与壳体90热结合。作为热结合部件91,例如能够使用导热膏体、导热片等。
[0084]
接下来,与比较例的半导体封装件搭载设备比较,对第一实施例的优异的效果进行说明。
[0085]
在比较例的半导体封装件搭载设备中,未配置侧面金属膜27、导热接合材料32(图1、图2)、热结合部件91(图3)等。因此,在比较例中未形成导热路径95(图3)。在发热源17产生的热量经由凸块15、上表面12u的金属焊盘20、通孔导体23、下表面12l的金属焊盘25、焊
料70、母基板60的金属焊盘65、通孔导体63传导至配置在母基板60的内层以及下表面60l的第二金属膜61。未必能够确保从母基板60向壳体90、设备外的部件的足够的导热路径。
[0086]
与此相对在第一实施例的半导体封装件10中,形成从半导体芯片14的发热源17经由凸块15、金属焊盘20、通孔导体23、第一金属膜22、侧面金属膜27、导热接合材料32、金属部件30、以及热结合部件91到达壳体90的导热路径95。在发热源17产生的热量通过该导热路径95传导至壳体90,壳体90作为散热片发挥作用。这样,在第一实施例中,能够确保从发热源17到散热片的热阻较小的导热路径95。因此,能够抑制半导体芯片14的过度的温度上升,其结果,能够抑制半导体芯片14的自发热所引起的性能劣化。
[0087]
并且,在第一实施例中,金属部件30安装于模块基板12的侧面,不需要在模块基板12的上表面12u确保用于安装金属部件30的区域。因此,能够减小模块基板12的尺寸。
[0088]
接下来,参照图4对第一实施例的变形例进行说明。
[0089]
图4是第一实施例的变形例的半导体封装件10的剖视图。在第一实施例的半导体封装件10(图1)中,在以最短距离从半导体芯片14连接到模块基板12的侧面的线上配置有表面安装部件16。与此相对在本变形例中,在以最短距离从半导体芯片14连接到模块基板12的侧面的线上未配置表面安装部件16。从半导体芯片14到模块基板12的侧面的最短距离比第一实施例(图1、图3)的情况短。因此,从半导体芯片14到金属部件30的侧面部30s为止的导热路径95比第一实施例(图1、图3)的情况短。
[0090]
在本变形例中,由于导热路径95比第一实施例短,所以从半导体芯片14到金属部件30的导热路径95的热阻变小。其结果,能够更高效地使在半导体芯片14的发热源17产生的热量传导至作为散热片的壳体90(图3)。由此,能够提高从半导体芯片14的散热性。
[0091]
接下来,参照图5对第一实施例的其它的变形例的半导体封装件10进行说明。
[0092]
图5是第一实施例的其它的变形例的半导体封装件10的示意立体图。在第一实施例中,金属部件30的侧面部30s(图2)从四方包围模块基板12。与此相对在本变形例中,金属部件30的侧面部30s配置在与模块基板12的相互朝向相反方向的两个侧面对置的位置,在与其它的两个侧面对置的位置未配置侧面部30s。即,金属部件30由长方形或者正方形的顶面部30t、和分别在相互相反侧的两个边缘折弯并朝向模块基板12的两个侧面部30s构成。
[0093]
如本变形例那样,也可以在模块基板12的四个侧面中两个侧面使第一金属膜22(图1)与金属部件30的侧面部30s(图1)热结合。作为其它的构成,也可以在模块基板12的四个侧面中三个侧面使第一金属膜22(图1)与金属部件30的侧面部30s(图1)热结合。另外,不需要一定在模块基板12的各个侧面的从一端到另一端的大致整个区域使第一金属膜22(图1)与金属部件30的侧面部30s(图1)热结合。也可以在模块基板12的侧面各自的四周方向的一部分的区域使第一金属膜22(图1)与金属部件30的侧面部30s(图1)热结合。
[0094]
[第二实施例]
[0095]
接下来,参照图6对第二实施例的半导体封装件进行说明。以下,对与第一实施例的半导体封装件10(图1、图2、图3)相同的构成省略说明。
[0096]
图6是第二实施例的半导体封装件10的剖视图。在第一实施例中,半导体芯片14(图1)的与器件形成面相反侧的面被密封树脂19覆盖。与此相对在第二实施例中,在半导体芯片14的与器件形成面(朝向模块基板12的面)相反侧的面配置有背面金属膜40。背面金属膜40例如能够使用铜。
[0097]
在多个半导体芯片14的背面金属膜40之上配置有一个印刷电路基板41。在印刷电路基板41的朝向半导体芯片14的面及其相反侧的面分别设置有金属膜42、43。在印刷电路基板41的内部配置有从一方的面到达另一方的面的多个通孔导体44。背面金属膜40通过焊料45与印刷电路基板41的金属膜42连接。印刷电路基板41的相反侧的金属膜43不被密封树脂19覆盖,而从密封树脂19露出。
[0098]
印刷电路基板41的金属膜43通过焊料46与金属部件30的顶面部30t的内侧的表面连接。这样,印刷电路基板41包含配置在背面金属膜40与顶面部30t之间,并从一方的表面到达另一方的表面的金属部分即金属膜42、43以及多个通孔导体44。顶面部30t经由印刷电路基板41的金属部分与背面金属膜40热结合。形成从半导体芯片14的发热源17通过半导体芯片14的半导体基板、背面金属膜40、焊料45、印刷电路基板41的金属部分、以及焊料46到达顶面部30t的导热路径96。半导体芯片14的半导体基板的导热率比铜、铝等金属低,但与周围的密封树脂19等绝缘性树脂材料相比足够高。因此,半导体芯片14的半导体基板作为导热路径96的一部分发挥作用。
[0099]
接下来,对第二实施例的优异的效果进行说明。
[0100]
在第二实施例中,作为从半导体芯片14的发热源17通过金属部件30到达壳体90(图3)的导热路径,形成通过模块基板12内的导热路径95、和通过半导体芯片14的半导体基板内以及印刷电路基板41的导热路径96。因此,与第一实施例的情况相比能够进一步提高从发热源17的散热性。
[0101]
接下来,参照图7对第二实施例的变形例的半导体封装件进行说明。
[0102]
图7是第二实施例的变形例的半导体封装件10的剖视图。在本变形例中,代替第二实施例的半导体封装件10所使用的印刷电路基板41(图6),而在半导体芯片14与金属部件30的顶面部30t之间配置有导热板47。作为导热板47,例如使用铜等金属板。顶面部30t经由导热板47与背面金属膜40热结合。在本变形例中,导热板47构成导热路径96的一部分,所以与第二实施例相同,能够提高从发热源17的散热性。
[0103]
接下来,对第二实施例的其它的变形例进行说明。在顶面部30t与半导体芯片14之间,在第二实施例(图6)中配置有印刷电路基板41,在第二实施例的变形例(图7)中配置有导热板47。作为其它的变形例,也可以不配置印刷电路基板41或者导热板47,而通过焊料将背面金属膜40与顶面部30t直接连接。在将背面金属膜40与顶面部30t连接之前的状态下背面金属膜40从密封树脂19露出。在本变形例中,背面金属膜40经由焊料与顶面部30t热结合。在本变形例中,也能够提高从发热源17的散热性。
[0104]
[第三实施例]
[0105]
接下来,参照图8以及图9对第三实施例的半导体封装件进行说明。以下,对与第一实施例的半导体封装件10(图1、图2、图3)相同的构成省略说明。
[0106]
图8是第三实施例的半导体封装件10的剖视图。图9是表示第三实施例的半导体封装件10的各构成要素的俯视时的位置关系的图。在第一实施例(图1)中,在一个模块基板12安装有一个金属部件30。与此相对在第三实施例中,两个模块基板12安装于一个金属部件30。在图9中,对金属部件30的侧面部30s、以及第一金属膜22附加影线。
[0107]
在俯视时两个模块基板12使一个侧面彼此对置并配置在共同的假想平面上。分别在两个模块基板12安装有多个半导体芯片14以及多个表面安装部件16。包含模块基板12、
半导体芯片14、以及表面安装部件16的模块构成与第一实施例的半导体封装件10的模块基板12、半导体芯片14、以及表面安装部件16的模块构成相同。
[0108]
金属部件30与两个模块基板12对应地具有两个顶面部30t。侧面部30s分别与两个顶面部30t连续。分别与两个顶面部30t连续的侧面部30s在俯视时从四方包围对应的模块基板12。位于两个模块基板12之间的两个侧面部30s在其下端相互连续。即,金属部件30具有两个凹部,分别在两个凹部收容模块基板12。例如通过对一个金属板进行冲压加工形成金属部件30。包含两个模块基板12的半导体封装件10安装于母基板60。
[0109]
接下来,对第三实施例的优异的效果进行说明。
[0110]
在第三实施例中,也与第一实施例相同地通过使金属部件30的顶面部30t与壳体热结合,能够确保从半导体芯片14通过金属部件30到达壳体的导热路径。由此,能够抑制半导体芯片14的过度的温度上升所引起的性能劣化。并且,由于在一个金属部件30收容两个模块基板12,所以与独立地将两个模块基板12收容于金属部件的构成相比,能够降低在母基板60上的专有面积。
[0111]
[第四实施例]
[0112]
接下来,参照图10以及图11对第四实施例的半导体封装件进行说明。以下,对与第一实施例的半导体封装件10(图1、图2、图3)相同的构成省略说明。
[0113]
图10是第四实施例的半导体封装件10的剖视图。在第一实施例中,使用金属帽作为半导体封装件10(图1)的金属部件30。与此相对在第四实施例中,使用覆盖密封树脂19的表面以及模块基板12的侧面的金属制的覆盖膜,作为金属部件30。能够通过真空蒸镀或者电镀等形成该覆盖膜。另外,也可以通过在进行了真空蒸镀的金属膜之上实施电镀,来形成覆盖膜。
[0114]
金属部件30的顶面部30t覆盖密封树脂19的顶面,侧面部30s覆盖密封树脂19的侧面以及模块基板12的侧面。侧面部30s在模块基板12的侧面与第一金属膜22的端面直接连接。
[0115]
图11是将第四实施例的半导体封装件10安装于母基板60,并收容于壳体90的状态的剖视图。在一个母基板60安装有两个半导体封装件10。两个半导体封装件10的顶面部30t分别经由焊料等热结合部件91与壳体90热结合。形成从半导体芯片14的发热源17通过多个凸块15、配置在模块基板12的上表面12u的金属焊盘20、多个通孔导体23、多个第一金属膜22、金属部件30、以及热结合部件91并到达壳体90的导热路径95。
[0116]
接下来,对第四实施例的优异的效果进行说明。
[0117]
由于对各半导体封装件10确保了导热路径95,所以与第一实施例相同,能够抑制半导体芯片14的过度的温度上升所引起的性能劣化。在第一实施例中,需要用于将模块基板12收容于由金属帽构成的金属部件30的凹部的机械组装工序。该组装工序要求较高的对位精度。与此相对在第四实施例中,利用真空蒸镀或者电镀形成金属部件30,所以不需要要求较高的对位精度的机械组装工序。
[0118]
[第五实施例]
[0119]
接下来,参照图12对第五实施例的半导体封装件进行说明。以下,对与第四实施例的半导体封装件10(图10、图11)相同的构成省略说明。
[0120]
图12是第五实施例的半导体封装件10的剖视图。在第五实施例中,在半导体芯片
14的与器件形成面(朝向模块基板12的面)相反侧的面配置有背面金属膜40。在密封半导体芯片14的密封树脂19设置有从密封树脂19的顶面到达背面金属膜40的多个开口19a。金属部件30通过设置于密封树脂19的多个开口19a与背面金属膜40连接。由此,金属部件30与背面金属膜40热结合。
[0121]
接下来,对第五实施例的优异的效果进行说明。
[0122]
在第五实施例中,除了通过模块基板12内的导热路径95之外,还形成从发热源17通过半导体芯片14的半导体基板以及背面金属膜40到达金属部件30的顶面部30t的导热路径96。因此,与第四实施例(图10)相比,能够进一步提高从发热源17的散热性。
[0123]
[第六实施例]
[0124]
接下来,参照图13对第六实施例的半导体封装件进行说明。以下,对与第一实施例的半导体封装件10(图1、图2、图3)相同的构成省略说明。
[0125]
图13是第六实施例的半导体封装件10以及壳体90的剖视图。在第一实施例(图1)中,金属部件30的侧面部30s在模块基板12的侧面与第一金属膜22热结合。与此相对在第六实施例中,金属部件30的侧面部30s不与模块基板12的侧面热结合,而经由配置于上表面12u的金属焊盘28与第一金属膜22热结合。
[0126]
在第一实施例(图1)中,密封树脂19覆盖模块基板12的上表面12u的整个区域,但在第六实施例中,在模块基板12的上表面12u的周边部留有未被密封树脂19覆盖的区域。在模块基板12的上表面12u中不与半导体芯片14重合且未被密封树脂19覆盖的区域配置有金属焊盘28。金属焊盘28在俯视时包围密封树脂19。
[0127]
金属焊盘28经由通孔导体24与内层的第一金属膜22连接。第一金属膜22与第一实施例(图1)的情况相同,经由通孔导体23以及金属焊盘20与半导体芯片14的凸块15连接。金属部件30的侧面部30s的模块基板12侧的端部(下端)朝向外侧弯曲,且与模块基板12对置的面通过焊料、导热膏体等导热接合材料32固定于金属焊盘28。顶面部30t与第一实施例(图3)的情况相同,经由热结合部件91与壳体90热结合。形成从半导体芯片14的发热源17通过凸块15、金属焊盘20、通孔导体23、第一金属膜22、通孔导体24、金属焊盘28、导热接合材料32、金属部件30、以及热结合部件91并到达壳体90的导热路径95。
[0128]
接下来,对第六实施例的优异的效果进行说明。
[0129]
在第六实施例中也与第一实施例相同,在半导体芯片14的发热源17产生的热量通过导热路径95传导至壳体90,所以能够抑制半导体芯片14的自发热所引起的性能劣化。
[0130]
接下来,对第六实施例的变形例进行说明。在第六实施例的半导体封装件10中,也可以如第二实施例(图6)或者第二实施例的变形例(图7)那样,在半导体芯片14设置背面金属膜40,并使背面金属膜40与金属部件30的顶面部30t热结合。例如,也可以如第二实施例那样,在顶面部30t与半导体芯片14之间配置印刷电路基板41(图6),也可以如第二实施例的变形例那样,在顶面部30t与半导体芯片14之间配置导热板47(图7)。由此,与第二实施例及其变形例的情况相同,能够进一步提高从半导体芯片14的散热性。
[0131]
[第七实施例]
[0132]
接下来,参照图14对第七实施例的半导体装置进行说明。以下,对与第一实施例的半导体封装件10(图1、图2、图3)相同的构成省略说明。
[0133]
图14是第七实施例的半导体装置11的剖视图。在第一实施例(图1)中,金属部件30
固定于模块基板12的侧面。与此相对在第七实施例中,金属部件30不固定于模块基板12,而固定于安装了半导体封装件10的母基板60。半导体装置11包含半导体封装件10以及母基板60。
[0134]
第七实施例的半导体装置11所使用的半导体封装件10包含模块基板12、和安装于其上表面12u的多个半导体芯片14、多个表面安装部件16、以及密封树脂19。半导体芯片14的多个凸块15与配置于模块基板12的上表面12u的金属焊盘20连接。金属焊盘20经由多个通孔导体23与下表面12l的金属焊盘25连接。在俯视时通孔导体23配置在与半导体芯片14重合的位置。
[0135]
在母基板60的上表面60u配置有金属焊盘65、66、67。设置于模块基板12的下表面12l的金属焊盘25、26分别通过焊料70、71与母基板60的金属焊盘65、66连接,从而半导体封装件10安装于母基板60。金属焊盘67配置在俯视时不与半导体封装件10重合的位置。并包围半导体封装件10。
[0136]
在母基板60的内层以及下表面60l配置有多个第二金属膜61。此外,第二金属膜61只要配置于内层以及下表面60l的至少一方即可。多个第二金属膜61在俯视时从与半导体芯片14重合的区域扩展至与半导体封装件10的外侧的金属焊盘67重合的区域。多个第二金属膜61通过配置在与半导体芯片14重合的位置的多个通孔导体63相互连接,并且与配置于上表面60u的金属焊盘65连接。并且,多个第二金属膜61经由多个通孔导体64与金属焊盘67连接。即,半导体封装件10的下表面的金属焊盘25经由焊料70、母基板60的金属焊盘65、通孔导体63、第二金属膜61、以及通孔导体64与金属焊盘67电连接,并且热结合。
[0137]
金属部件30具有以母基板60的上表面60u为高度的基准配置在比半导体封装件10高的位置的顶面部30t、以及从顶面部30t朝向母基板60延伸的侧面部30s。在俯视时,顶面部30t包含半导体封装件10。侧面部30s在其下端通过焊料72与金属焊盘67连接并热结合。顶面部30t经由热结合部件91与壳体90热结合。
[0138]
接下来,对第七实施例的优异的效果进行说明。
[0139]
在第七实施例中,形成从半导体芯片14的发热源17通过凸块15、模块基板12的上表面12u的金属焊盘20、通孔导体23、模块基板12的下表面12l的金属焊盘25、焊料70、母基板60的上表面60u的金属焊盘65、通孔导体63、第二金属膜61、通孔导体64、母基板60的上表面60u的金属焊盘67、焊料72、金属部件30、以及热结合部件91到达壳体90的导热路径97。
[0140]
在以往的设备中,不能说确立了从母基板60到作为散热片发挥作用的部件为止的足够的导热路径。在第七实施例中,形成经由母基板60到达壳体90的导热路径97,所以能够抑制半导体芯片14的过度的温度上升,抑制半导体芯片14的自发热所引起的性能劣化。
[0141]
接下来,参照图15对第七实施例的变形例进行说明。
[0142]
图15是第七实施例的变形例的半导体装置11的剖视图。在本变形例中,与第二实施例(图6)的情况相同,在半导体芯片14的与器件形成面相反侧的面配置有背面金属膜40。在背面金属膜40与金属部件30的顶面部30t之间配置有印刷电路基板41。设置于印刷电路基板41的朝向下方的面的金属膜42与背面金属膜40通过焊料45连接。设置印刷电路基板41的朝向上方的面的金属膜43与顶面部30t通过焊料46连接。一方的面的金属膜42与另一方的面的金属膜43经由多个通孔导体44热结合。
[0143]
在本变形例中,与第二实施例(图6)的情况相同,除了导热路径97之外,还形成从
半导体芯片14的发热源17通过半导体芯片14的半导体基板、背面金属膜40、焊料45、设置于印刷电路基板41的金属膜42、43和通孔导体44、以及焊料46到达顶面部30t的导热路径96。因此,能够进一步提高从发热源17的散热性。
[0144]
接下来,参照图16对第七实施例的其它的变形例进行说明。
[0145]
图16是第七实施例的其它的变形例的半导体装置11的剖视图。在本变形例中,代替图15所示的变形例所使用的印刷电路基板41而配置导热板47。在本变形例中,导热板47成为导热路径96的一部分。在本变形例中,也与图15所示的变形例相同,能够进一步提高从发热源17的散热性。
[0146]
[第八实施例]
[0147]
接下来,参照图17对第八实施例的半导体装置进行说明。以下,对与第四实施例(图10、图11)所示的半导体封装件10以及母基板60相同的构成省略说明。
[0148]
图17是第八实施例的半导体装置11的剖视图。在第四实施例(图10)中,半导体芯片14与金属部件30经由模块基板12的内部或者下表面12l的第一金属膜22热结合。与此相对在第八实施例中,在模块基板12的内部以及下表面12l均未配置使半导体芯片14与金属部件30热结合的金属膜。半导体芯片14与金属部件30通过设置于母基板60的金属部件热结合。
[0149]
在第八实施例中,在模块基板12的下表面12l,除了金属焊盘25、26之外,还在下表面12l的周边部配置有金属焊盘29。并且,在模块基板12的周边部的内层配置有多个金属膜50。多个金属膜50到达模块基板12的侧面。多个金属膜50经由多个通孔导体51与下表面12l的金属焊盘29连接。
[0150]
与第四实施例(图10)的情况相同,安装于模块基板12的多个半导体芯片14以及多个表面安装部件16被密封树脂19密封。密封树脂19的表面以及模块基板12的侧面被金属部件30覆盖。多个金属膜50在模块基板12的侧面与金属部件30的侧面部30s热结合。
[0151]
母基板60的构成与第七实施例的半导体装置11的母基板60(图14)的构成大致相同。在母基板60的上表面60u中与模块基板12的周边部的金属焊盘29对置的位置配置有金属焊盘67。模块基板12的下表面12l的金属焊盘25、26、29分别通过焊料70、71、72与母基板60的上表面60u的金属焊盘65、66、67连接。
[0152]
接下来,对第八实施例的优异的效果进行说明。
[0153]
在第八实施例中,形成从半导体芯片14的发热源17通过凸块15、模块基板12的上表面12u的金属焊盘20、通孔导体23、模块基板12的下表面12l的金属焊盘25、焊料70、母基板60的上表面60u的金属焊盘65、通孔导体63、第二金属膜61、通孔导体64、母基板60的上表面60u的金属焊盘67、焊料72、模块基板12的下表面12l的金属焊盘29、通孔导体51、金属膜50、以及金属部件30的侧面部30s到达顶面部30t的导热路径97。
[0154]
顶面部30t与第四实施例(图11)的情况相同,经由热结合部件91与壳体90热结合。在收容于壳体90的状态下,形成从半导体芯片14到达壳体90的导热路径97。因此,与第七实施例相同,能够抑制半导体芯片14的过度的温度上升,抑制半导体芯片14的自发热所引起的性能劣化。
[0155]
接下来,参照图18对第八实施例的变形例进行说明。
[0156]
图18是第八实施例的变形例的半导体装置11的剖视图。在本变形例中,与第五实
施例(图12)的情况相同,在半导体芯片14的与器件形成面相反侧的面配置背面金属膜40,并且在密封树脂19设置多个开口19a。金属部件30的顶面部30t通过该开口19a内与背面金属膜40热结合。在本变形例中,与第五实施例(图12)的情况相同,形成通过开口19a的导热路径96,所以能够进一步提高从半导体芯片14的发热源17的散热性。
[0157]
[第九实施例]
[0158]
接下来,参照图19对第九实施例的半导体芯片搭载设备进行说明。以下,对与第四实施例的半导体封装件10(图10)以及半导体封装件搭载设备(图11)相同的构成省略说明。
[0159]
图19是第九实施例的半导体封装件搭载设备的剖视图。在第九实施例中也与第四实施例(图11)相同地在母基板60安装有两个半导体封装件10。半导体封装件10各自的构成与第四实施例的半导体封装件10(图10)的构成相同。在第九实施例中,在母基板60将金属帽35安装为覆盖两个半导体封装件10。
[0160]
金属帽35具有在俯视时包含两个半导体封装件10的顶面部35t、和从顶面部35t朝向母基板60延伸的侧面部35s。侧面部35s的下端通过焊料73与母基板60的上表面60u的金属焊盘68固定。金属焊盘68与模块基板12内的作为接地层发挥作用的第一金属膜22电连接。在母基板60的上表面除了半导体封装件10之外还安装有多个表面安装部件。此外,这些表面安装部件安装在脱离图19所示的剖面的范围的位置,而在图19中未显现。金属帽35也覆盖这些多个表面安装部件。
[0161]
覆盖两个半导体封装件10的密封树脂19的金属部件30的顶面部30t经由焊料等热结合部件92与金属帽35的顶面部35t热结合。金属帽35的顶面部35t经由焊料等热结合部件93与壳体90热结合。从半导体芯片14的发热源17到金属部件30的顶面部30t的导热路径95与第四实施例的半导体封装件10(图10)的导热路径95相同。在第九实施例中,导热路径95从顶面部30t经由热结合部件92、金属帽35的顶面部35t、以及热结合部件93到达壳体90。
[0162]
接下来,对第九实施例的优异的效果进行说明。
[0163]
在第九实施例中也与第四实施例(图10)的情况相同,能够使热量从半导体芯片14的发热源17通过经由模块基板12、金属部件30、以及金属帽35的导热路径95传导至壳体90。由此,能够抑制半导体芯片14的过度的温度上升,抑制自发热所引起的性能劣化。
[0164]
并且在第九实施例中,与作为接地层发挥作用的第一金属膜22电连接的金属帽35作为电磁屏蔽件发挥作用。因此,能够抑制来自安装于母基板60的半导体封装件10以外的表面安装部件的噪声的辐射以及对表面安装部件的噪声的影响。
[0165]
接下来,参照图20对第九实施例的变形例进行说明。
[0166]
图20是第九实施例的变形例的半导体封装件搭载设备的剖视图。在本变形例中,与第五实施例(图12)的情况相同,在半导体芯片14的与器件形成面相反侧的面配置背面金属膜40,在半导体封装件10的密封树脂19设置多个开口19a。金属部件30的顶面部30t通过开口19a与背面金属膜40连接。
[0167]
在本变形例中,与第五实施例(图12)相同,除了导热路径95之外,还形成从半导体芯片14的发热源17通过开口19a内并到达壳体90的导热路径96。因此,与第五实施例(图12)相同,能够进一步提高从发热源17的散热性。
[0168]
[第十实施例]
[0169]
接下来,参照图21对第十实施例的半导体装置搭载设备进行说明。以下,对与第九
实施例的半导体封装件搭载设备(图19)相同的构成省略说明。
[0170]
图21是第十实施例的半导体装置搭载设备的剖视图。在第九实施例(图19)中,模块基板12内的第一金属膜22构成从半导体芯片14到金属部件30的导热路径95的一部分。与此相对在第十实施例中,与第八实施例(图17)相同,不是模块基板12内的金属膜,而是母基板60内的第二金属膜61构成从半导体芯片14到金属部件30的导热路径97的一部分。并且,导热路径97与第九实施例(图19)的导热路径96相同,从金属部件30通过热结合部件92、金属帽35、以及热结合部件93到达壳体90。
[0171]
接下来,对第十实施例的优异的效果进行说明。
[0172]
在第十实施例中,在半导体芯片14的发热源17产生的热量通过在一部分包含母基板60内的第二金属膜61的导热路径97传导至壳体90。因此,与第八实施例(图17)的情况相同能够提高从发热源17的散热性。
[0173]
[第十一实施例]
[0174]
接下来,参照图22对第十一实施例的半导体装置搭载设备进行说明。以下,对与第一实施例的半导体封装件10(图1、图2、图3)相同的构成省略说明。
[0175]
图22是第十一实施例的半导体装置搭载设备的剖视图。在第一实施例(图3)中,从模块基板12内的通孔导体23到侧面金属膜27的导热路径95包含模块基板12内的第一金属膜22。在母基板60内未形成从模块基板12内的通孔导体23到侧面金属膜27的导热路径。与此相对在第十一实施例中,形成经由模块基板12内的第一金属膜22的第一导热路径98a、和经由母基板60内的第二金属膜61的第二导热路径98b。
[0176]
具体而言,第一导热路径98a从半导体芯片14经由凸块15、模块基板12的金属焊盘20、通孔导体23、第一金属膜22、侧面金属膜27、导热接合材料32、金属部件30、以及热结合部件91到达壳体90。
[0177]
在母基板60的上表面60u将金属焊盘67配置为在俯视时与半导体封装件10的侧面重合,并将金属焊盘65配置为与半导体芯片14重合。第二金属膜61配置于母基板60的下表面60l以及内层的至少一方,从在俯视时与半导体芯片14重合的位置扩展至半导体芯片14的外侧。第二金属膜61在俯视时到达与金属焊盘67重合的位置。
[0178]
第二金属膜61经由母基板60内的通孔导体63、上表面60u的金属焊盘65、焊料70、模块基板12的金属焊盘25与模块基板12内的通孔导体23连接。第二金属膜61在俯视时在半导体芯片14的外侧经由母基板60内的通孔导体64、上表面60u的金属焊盘67、焊料72、模块基板12的周边部的金属焊盘26、模块基板12内的通孔导体24与第一金属膜22连接。第二导热路径98b在通孔导体23从第一导热路径98a分支,并经由金属焊盘25、焊料70、金属焊盘65、通孔导体63、第二金属膜61、通孔导体64、金属焊盘67、焊料72、金属焊盘26、以及通孔导体24,在第一导热路径98a与第一导热路径98a合流。
[0179]
接下来,对第十一实施例的优异的效果进行说明。
[0180]
在第十一实施例中,在经由模块基板12内的第一导热路径98a的一部分并联连接经由母基板60内的第二导热路径98b。因此,降低从半导体芯片14到壳体90的导热路径的热阻。其结果,能够进一步提高从半导体芯片14的散热性。
[0181]
[第十二实施例]
[0182]
接下来,参照图23对第十二实施例的放大电路进行说明。第十二实施例的放大电
路使用第一实施例~第十一实施例的任意一个实施例的半导体封装件10或者半导体装置11。
[0183]
图23是第十二实施例的放大电路的框图。从输入端子105经由阻抗匹配电路103向驱动级放大器101输入高频信号。在驱动级放大器101进行了放大的高频信号输入到功率级放大器102。在功率级放大器102进行了放大的高频信号经由阻抗匹配电路104输出到输出端子106。
[0184]
从直流电源110经由电感器107对驱动级放大器101施加电源电压。从直流电源111经由电感器108对功率级放大器102施加电源电压。
[0185]
例如,利用半导体封装件10的半导体芯片14实现驱动级放大器101以及功率级放大器102。利用安装于模块基板12的表面安装部件16(图1)实现阻抗匹配电路103以及104的无源部件、电感器107、108。此外,也可以在半导体芯片14内形成阻抗匹配电路103、104的一部分或者全部的无源部件。另外,也可以在驱动级放大器101与功率级放大器102之间插入级间阻抗匹配电路。
[0186]
接下来,对第十二实施例的优异的效果进行说明。驱动级放大器101以及功率级放大器102能够使用第一实施例~第十一实施例的任意一个半导体封装件10或者半导体装置11,所以能够抑制驱动级放大器101以及功率级放大器102的过度的温度上升,抑制驱动级放大器101以及功率级放大器102的晶体管的自发热所引起的性能劣化。
[0187]
上述的各实施例为例示,当然能够进行不同的实施例所示的构成的部分的置换或者组合。并不对每个实施例依次提及多个实施例的相同的构成所带来的相同的作用效果。并且,本发明并不限定于上述的实施例。例如,本领域技术人员明确能够进行各种变更、改进、组合等。
再多了解一些
本文用于企业家、创业者技术爱好者查询,结果仅供参考。