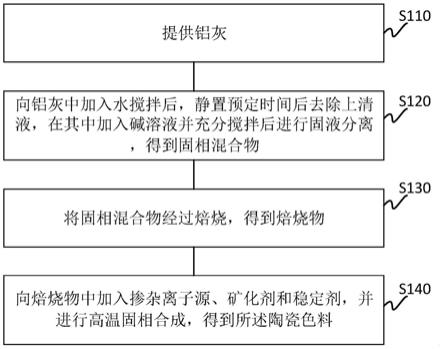
1.本发明涉及陶瓷技术领域,具体地,涉及一种陶瓷色料的制备方法及陶瓷色料。
背景技术:
2.铝灰渣是电解铝、铸铝等铝工业生产、使用、回收利用过程中产生的一种固体废弃物。铝灰渣的成分随企业生产原料、操作条件的不同而有差异。与原料所含污染物、覆盖剂、造渣剂、精炼剂等有直接关系,同时还与铸造炉内气氛有关,一般成分是金属铝、氧化铝和铁的氧化物,钾、钠、钙和镁的氯化物等。
3.目前铝灰渣的处理方式主要是堆存或填埋,铝灰中的有毒有害离子会渗入地下,对土壤和地下水造成污染。另外,天气炎热潮湿时,铝灰中的氮化铝、碳化铝等物质与水反应,生成氨气、甲烷等气体,对空气造成污染。因此,把铝灰中的有用组分转变成高附加价值的产品,以获得原材料,同时,解决了有害废料填埋导致的污染问题。
技术实现要素:
4.有鉴于此,本发明提供了一种陶瓷色料的制备方法,该方法工艺简单,能够将废弃的铝灰渣进行利用,得到较高附加价值的陶瓷色料。
5.本发明采用以下技术方案:
6.根据本发明实施例的陶瓷色料的制备方法,包括以下步骤:
7.步骤1,提供铝灰;
8.步骤2,向所述铝灰中加入水搅拌后,静置预定时间后去除上清液,再在其中加入碱溶液并充分搅拌后进行固液分离,得到固相混合物;
9.步骤3,将所述固相混合物经过焙烧,得到焙烧物;
10.步骤4,向所述焙烧物中加入掺杂离子源、矿化剂和稳定剂,并进行高温固相合成,得到所述陶瓷色料。
11.优选地,相对于所述铝灰、所述掺杂离子源、所述矿化剂和所述稳定剂的总量,所述铝灰的质量百分比为30wt%-85wt%。
12.优选地,所述步骤2中,所述铝灰与所述水的质量比为1:(1-7),所述铝灰与所述碱溶液的质量比为1:(1-3)。
13.优选地,所述碱溶液为氢氧化钠水溶液,所述氢氧化钠水溶液的浓度为0.5-40wt%。
14.优选地,所述步骤3中,所述焙烧温度为500-1100℃。
15.优选地,所述步骤4中,所述高温固相合成温度为1000-1350℃
16.优选地,所述步骤4中,所述掺杂离子源中所含的掺杂离子为锰离子、锌离子、铬离子和钴离子中的一种或多种。
17.优选地,所述矿化剂的质量百分比为1-5wt%,所述矿化剂为化合物氯化钠、氟化钠和氯化铵中的一种或多种。
18.优选地,所述稳定剂的重量百分比1-10wt%,所述稳定剂为硼酸、碳酸钙、氯化钙和磷酸氢二钾中的一种或多种。
19.本发明还提供一种陶瓷色料,所述陶瓷色料为上述实施例的所述陶瓷色料的制备方法制备得到。
20.本发明的上述技术方案至少具有如下效果之一:
21.根据本发明的陶瓷色料的制备方法,通过提纯固体危险废弃物铝灰将之转化为氧化铝或氢氧化铝,再引入掺杂离子,并加入特定的矿化剂以促使固相反应的进行,加入稳定剂以隐蔽钙、镁、硅等元素对固相反应的干扰,采取固相合成法来制备的陶瓷色料及其方法。该方法实现了铝灰在陶瓷色料领域的资源化利用,避免了铝灰的随意处理对环境的危害,该方法大大降低了传统化工工艺生产成本、工艺过程简单、环境友好,满足工业生产要求。
附图说明:
22.图1为本发明的一个实施例的陶瓷色料的制备方法的流程图;
23.图2为本发明的一个实施例1中对应的红色色料粉体的x射线衍射图;
24.图3为本发明的一个实施例1中的红色色料粉体的实物外观图;
25.图4为本发明的一个实施例2中对应的桃红色色料粉体的x射线衍射图;
26.图5为本发明的一个实施例2中的桃红色色料粉体的实物外观图;
27.图6为本发明的一个实施例3中对应的蓝色色料粉体的x射线衍射图;
28.图7为本发明的一个实施例3中的蓝色色料粉体的实物外观图。
具体实施方式
29.为使本发明实施例的目的、技术方案和优点更加清楚,下面将结合本发明实施例对本发明实施例的技术方案进行清楚、完整地描述。显然,所描述的实施例是本发明的一部分实施例,而不是全部的实施例。基于所描述的本发明的实施例,本领域普通技术人员所获得的所有其他实施例,都属于本发明保护的范围。
30.陶瓷色料是陶瓷制品装饰领域中的一个重要组成部分,它是陶瓷制品彩饰色剂和瓷釉或坯料中的重要组成部分,其中铝系色料应用较广泛,主要有锰红色料、铬铝红色料、钴蓝色料等。
31.铝灰中主要含有金属铝、氧化铝、氢氧化铝等物质。发明人发现铝灰渣中的氧化铝和氢氧化铝可作为原料制备陶瓷色料,尤其利用固体危害性的铝灰渣为原料生产陶瓷色料的方法,不仅可以得到高价值的陶瓷色料,还可以使得铝灰渣得到较好的利用。
32.下面具体描述根据本发明实施例的陶瓷色料的制备方法及陶瓷色料。
33.如图1所示,根据本发明实施例的陶瓷色料的制备方法,包括以下步骤:
34.s110,提供铝灰。
35.在本技术的一个实施例中,铝灰是以铝灰渣为原料。优选地,对铝灰渣经过粉碎、筛分,筛分的网孔可以采用80-325目,进一步优选为80-140目,得到筛下物铝灰。由此,去除大块金属铝等杂质,得到粒径均匀一致的颗粒,有利于提高色料的均匀性和稳定性。
36.在筛选的过程中,筛出的粉尘和大块金属铝可以进一步回收。
37.s120,向铝灰中加入水搅拌后,静置预定时间后去除上清液,再在其中加入碱溶液并充分搅拌后进行固液分离,得到固相混合物。
38.也就是说,在本步骤中,首先加水充分搅拌,并静置一定时间以让其中的可溶性盐能够充分溶解,并通过固液分离(即去除上清液)而去除。在本发明的实施例中,铝灰与水的添加比例,按照质量比可以为1:1到1:7,优选地可以1:5。该比例可以有效的除去铝灰渣中的可溶性盐。
39.在铝灰中,通常还混入有一定量的氮元素,这部分氮元素通常以aln的形式存在。而氮元素的存在将影响后续的固相反应,从而影响色料的稳定性。此外,铝灰中还混入有部分未反应的al。
40.为此,在去除其中的可溶性盐之后,还通过引入碱溶液来一方面使其中的铝发生水解以形成氢氧化铝。
41.另一方面,通过添加碱溶液例如氢氧化钠水溶液,能够有效去除其中的氮。其反应机理如下:
42.aln h2o
→
al(oh)3 nh343.aln naoh h2o
→
naalo2 nh344.在本发明的一个实施例中,铝灰与碱溶液的添加比例,按照质量比为1:1至1:3。优选地,可以为1:2,该比例可以达到最优去除氮元素的碱添加量,除氮率高达94.19%。
45.在本发明的一个实施例中,碱溶液可以选取氢氧化钠溶液,浓度可以为0.5-40%,该浓度可以有效除去铝灰中以氮化铝形式存在的氮元素。
46.在一些实施例中,向去除了上清液的铝灰中缓慢加入氢氧化钠溶液,加热搅拌预定时间,其中,加热温度为50-125℃,预定时间可以为2-4小时。加热搅拌预定时间后,进行固液分离,得固相混合物。
47.s130,将固相混合物经过焙烧,得到焙烧物。
48.通过焙烧,一方面可以将铝灰中的残留的少量金属铝氧化,碳杂质氧化,另一方面,还可以使部分氢氧化铝脱水。
49.在本发明第一个实施例中,经过低温富氧焙烧,其中,富氧焙烧温度500-1100℃,优选地,温度可以为500-850℃之间,经过富氧焙烧后得到焙烧物。该焙烧物为氧化铝及氢氧化铝的混合物。
50.s140,向所述焙烧物中加入掺杂离子源、矿化剂和稳定剂,并进行高温固相合成,得到陶瓷色料。
51.其中,高温固相合成是指高温下掺杂离子掺杂到氧化铝晶格中以形成固溶体,以形成稳定的陶瓷色料。在本发明的一个实施例中,高温固相合成的温度在1000-1350℃之间。
52.在本发明的一个实施例中,掺杂离子源中的掺杂离子可以为锰离子、锌离子、铬离子和钴离子中的一种或多种,这些锰离子、铬离子、锌离子、钴离子均作为掺杂元素或色料配方成分。掺杂离子可以根据所要形成的陶瓷色料的颜色进行相应选择,例如可以通过引入锰离子来形成红色色料,通过引入铬离子形成桃红色色料,通过引入钴离子来形成蓝色色料等,此外,还可以通过同时引入多种掺杂离子。
53.在本发明的一个实施例中,矿化剂的质量百分比可以为1-5wt%,矿化剂为化合物
氯化钠、氟化钠和氯化铵中的一种或多种。
54.在本发明的一个实施例中,稳定剂的重量百分比1-10wt%,稳定剂为硼酸、碳酸钙、氯化钙和磷酸氢二钾中的一种或多种。
55.根据本发明实施例的陶瓷色料的制备方法,能够对固体危险废弃物铝灰渣的二次利用,同时结合固相法,减少其对环境的危害,同时促进了铝灰在陶瓷色料领域的资源化利用,使得该发明具有工艺简单、易于控制、易生产、环境友好并且大大降低了生产成本的优点。
56.为使本领域的技术研究人员能够更好的理解本发明的技术方案,下面结合具体实施例对本发明作进一步详细说明。
57.实施例1
58.1)将铝灰渣(固体危险废弃物铝灰)过140目筛,再按照水灰比5:1进行混合,搅拌,静置,去除上清液;
59.2)按照碱灰比2:1,向上述1)中的处理后的铝灰中加入质量分数20%的氢氧化钠溶液,加热至80℃,搅拌2小时,冷却,得固相混合物;
60.3)将上述得到的固相混合物在700℃下进行低温富氧焙烧,得氧化铝及氢氧化铝的混合物;
61.4)向上述3)中得到的混合物中加入碳酸锰、氯化钙、氟化钠、氯化铵,其中,按照质量份计,混合物87份、碳酸锰7份、氟化钠2份、氯化钙3份、氯化铵1份,在1050℃下进行高温固相合成,即得到红色色料粉体。
62.该样品表征结果见表1:
63.表1表征结果
[0064][0065]
红色色料添加量为5%的通体陶瓷砖样板,经辊道窑煅烧后色度值见表2:
[0066]
表2色度值表
[0067][0068]
其中,表中的l*、a*、b*为评价色料的指标,分别表示明度值、红绿值、黄蓝值;其中l*值越大,说明色料越亮,a*值为正说明色料为红色,为负则为绿色,b*为正说明色料为黄色、为负则为蓝色;数据中的a*值大于b*,说明样品呈红色;数据中a*值、b*值均为负值,且a*值的绝对值小于b*值,则说明样品呈蓝色。由此,本发明的方案可以得到色料较亮的红色陶瓷砖。
[0069]
图2为实施例1中样品对应的xrd图,锰红色料的xrd图谱基本与pdf卡片相对应,说
明锰离子成功掺杂到氧化铝晶格中。实物图可参见图3。
[0070]
实施例2
[0071]
1)将固体危险废弃物铝灰过140目筛,再按照水灰比5.0与水混合,搅拌,静置;
[0072]
2)按照碱灰比2.0,向上述处理后的铝灰中加入质量分数30%的氢氧化钠溶液,加热至100℃,搅拌3小时,冷却,得固相混合物;
[0073]
3)将上述得到的固相混合物在750℃下进行低温富氧焙烧,得氧化铝及氢氧化铝的混合物;
[0074]
4)向上述得到的混合物中加入氧化铬、氧化锌、硼酸,其中,按照质量份计,混合物50份、氧化铬7份、氧化锌35份、硼酸8份,在1250℃下进行高温固相合成,即得到桃红色色料粉体。
[0075]
该样品表征结果见表3:
[0076]
表3表征结果
[0077][0078]
其中,实施例二的xrd图可见图4,说明铬离子成功掺杂到氧化铝晶格中实物图可参见下图5。
[0079]
桃红色色料添加量为5%的通体陶瓷砖样板,经辊道窑煅烧后色度值见表4:
[0080]
表4色度值表
[0081][0082]
由表4,本发明的方案可以得到色料较亮的桃红色陶瓷砖。
[0083]
实施例3
[0084]
1)将固体危险废弃物铝灰过140目筛,再按照水灰比5:1进行混合,搅拌,静置,备用;
[0085]
2)按照碱灰比2:1,向上述处理后的铝灰中加入质量分数40%的氢氧化钠溶液,加热至120℃,搅拌4小时,冷却,得固相混合物;
[0086]
3)将上述得到的固相混合物在850℃下进行低温富氧焙烧,得氧化铝及氢氧化铝的混合物;
[0087]
4)向上述得到的混合物中加入氧化钴、氯化钙、硼酸,其中,按照质量份计,混合物75份、氧化钴20份、硼酸5份,在1200℃下进行高温固相合成,即得到蓝色色料粉体。
[0088]
该样品表征结果见表5:
[0089]
表5表征结果
[0090][0091][0092]
其中,图6示出了实施例三的xrd图,说明钴离子成功掺杂到氧化铝晶格中,实物图可参见下图7。
[0093]
钴蓝色料添加量为5%的通体陶瓷砖样板,经辊道窑煅烧后色度值见表6:
[0094]
表6色度值表
[0095][0096]
由表6,本发明的方案可以得到钴蓝色陶瓷砖。
[0097]
上述实施例中铝灰成分分析(xdf)见表7:
[0098]
表7铝灰成分分析(xdf)结果
[0099][0100]
上述实施例中通体陶瓷砖样板的基础陶瓷为陶瓷厂常用的陶瓷配方,其成分分析(xdf)见表8:
[0101]
表8通体陶瓷样板成分分析(xdf)结果
[0102][0103]
虽然已参考具体的实施方式描述了本发明,但本领域技术人员将理解,在不偏离本发明的范围下,可进行各种变化,并且等价物可替代其要素。因此,本发明不局限于所公开的具体的实施方式,而是其包括落入所附权利要求范围内的所有实施方式。
再多了解一些
本文用于企业家、创业者技术爱好者查询,结果仅供参考。