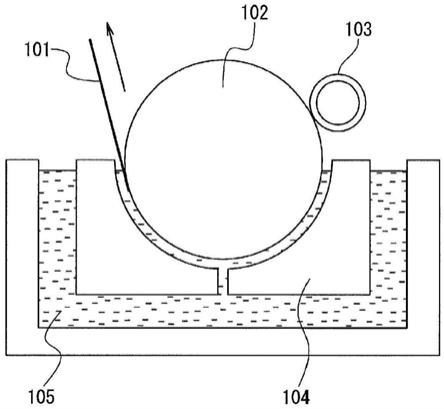
1.本发明涉及一种适合于印刷电路板(特别是具有高密度布线电路(精细图案)的印刷电路板)等的微细布线加工性、与树脂制基板的密合性优异的表面处理铜箔,使用了该表面处理铜箔的覆铜层叠板以及印刷电路板。
背景技术:
2.作为用于覆铜层叠板、印刷电路板的铜箔,使用通过将在电解析出装置的鼓析出的铜箔从鼓剥离而得到的电解铜箔。从鼓剥离的电解铜箔的电场析出开始面(以下,记为“鼓面”)相对平滑,作为相反一侧的面的电解析出结束面(以下,记为“析出面”)通常具有凹凸。在电解铜箔的析出面上配置树脂制基板并进行热压接来制造覆铜层叠板,通常,通过对析出面实施粗化处理将其粗化,来提高与树脂制基板的粘接性。
3.最近,在铜箔的粗化面预先贴合环氧树脂等粘接用树脂,将该粘接用树脂作为半固化状态(b阶段)的绝缘树脂层而制成的带树脂的铜箔用作表面电路形成用的铜箔,将该铜箔的绝缘树脂层的一侧热压接于绝缘基板来制造印刷电路板(尤其是增层电路板(build up circuit board))。对于增层电路板,期望将各种电子零件高度集成化,与此对应,对于布线图案也要求高密度化,逐渐变为要求微细的线宽、线间间距的布线图案、所谓精细图案的印刷电路板。例如,在服务器、路由器、通讯基站、车载基板等所使用的多层基板、或智能手机用多层基板中,要求具有高密度极微细布线的印刷电路板(以下,记为“高密度电路板”)。
4.任意层(anylayer)(利用配置的自由度高的激光通孔将层间连接)的高密度电路板主要用于智能手机的主板,但近年来微细布线化不断推进,要求线宽和线间的间距(以下,记为“l&s”)分别为例如30μm以下的布线。
5.然而,由于布线微细化而因高密度电路板的树脂所吸收的水分的影响导致布线与树脂的密合性下降的吸湿劣化问题明显化。特别是在最近的智能手机中,由于随着消耗电力的增加而发热上升,存在吸湿劣化加速的倾向,变得不容易维持布线与树脂的密合性。
6.专利文献1中公开了通过使粗化粒子的形状尖锐而与高耐热性树脂的密合性优异的铜箔,但在用于形成布线的蚀刻时,尖锐形状的粗化粒子容易溶解残留(根部残留),微细布线加工性恐怕会变得不充分。
7.专利文献2中公开了鼓面的粗糙度小、微细布线加工性优异的铜箔,但没有应对树脂制基板所吸收的水分的措施,因此在高温高湿环境下铜箔与树脂制基板的密合性恐怕会下降。
8.专利文献3中公开了对表面凹凸形状的变化的陡峭度进行了控制的高频特性优异的铜箔,但在制作具有l&s分别为例如30μm以下的微细布线的高密度电路板的情况下,高温高湿环境下的铜箔与树脂制基板的密合性恐怕会下降。
9.现有技术文献
10.专利文献
11.专利文献1:日本专利公开公报2010年第236058号
12.专利文献2:日本专利公开公报2018年第76601号
13.专利文献3:国际公开第2018/198905号
技术实现要素:
14.发明所要解决的问题
15.本发明的技术问题在于提供一种具有微细布线加工性,并且与树脂制基板的密合性优异的表面处理铜箔。此外,本发明的技术问题还在于提供一种具有微细布线加工性的覆铜层叠板以及能够形成高密度极微细布线的印刷电路板。
16.用于解决问题的方案
17.本发明的一个方案的表面处理铜箔是在表面具有利用粗化处理而形成的粗化面的表面处理铜箔,其主旨在于:粗化面的最小自相关长度sal为1.0μm以上且8.5μm以下,均方根高度sq为0.10μm以上且0.98μm以下。
18.此外,本发明的另一方案的覆铜层叠板的主旨在于:具备上述一个方案的表面处理铜箔和层叠于该表面处理铜箔的粗化面的树脂制基板。
19.进而,本发明的另一方案的印刷电路板的主旨在于:具备上述另一方案的覆铜层叠板。
20.发明效果
21.本发明的表面处理铜箔具有微细布线加工性,并且与树脂制基板的密合性优异。此外,本发明的覆铜层叠板具有微细布线加工性。进而,本发明的印刷电路板能够形成高密度极微细布线。
附图说明
22.图1是对使用电解析出装置来制造电解铜箔的方法进行说明的图。
具体实施方式
23.对本发明的一个实施方式进行说明。需要说明的是,以下所说明的实施方式表示本发明的一个例子。此外,在本实施方式中可以加入各种变更或改良,这种加入了变更或改良的方式也可以包含在本发明中。
24.本发明的一个实施方式的表面处理铜箔是在表面具有利用粗化处理而形成的粗化面的表面处理铜箔,其中,粗化面的最小自相关长度sal为1.0μm以上且8.5μm以下,均方根高度sq为0.10μm以上且0.98μm以下。
25.根据此种构成,本实施方式的表面处理铜箔具有能够应对高密度电路板的微细布线加工性,并且与树脂制基板的常态下的密合性和高温高湿环境下(例如压力锅试验后)的密合性优异。因此,本实施方式的表面处理铜箔能优选用于制造覆铜层叠板、印刷电路板。若使用本实施方式的表面处理铜箔,则能制造具有微细布线加工性的覆铜层叠板。进而,若使用本实施方式的表面处理铜箔,则能制造具有高密度极微细布线的印刷电路板。需要说明的是,本发明中所谓“常态”是指表面处理铜箔置于常温常湿(例如温度23
±
2℃,湿度50
±
5%rh)下的状态。
26.最小自相关长度sal是iso25178中所规定的值,定义为表面形状的自相关函数(参照下述式1)衰减至相关值s为止的面内的最短距离(只要无特别说明,则是指s从1衰减至0.2的最短距离),例如可以通过三维白光干涉型显微镜或激光显微镜进行测定。最小自相关长度sal可以用作在铜箔中,由铜箔的表面的起伏等而产生的、表面凹凸形状的变化的陡峭度的指标。即,最小自相关长度sal的值越小,高低差以越短的距离变化,因此可以说表面凹凸形状的变化陡峭。
[0027][0028]
均方根高度sq是iso25178中所规定的值,如下述式2所示,定义为距离平均面的距离的标准偏差,例如可以通过三维白光干涉型显微镜或激光显微镜进行测定。均方根高度sq表示在铜箔中,由粗化形状等而产生的表面形状的凹凸的不均。此外,式1、式2中的z(x,y)表示x,y坐标下的高度方向的坐标。
[0029][0030]
以下,对本实施方式的表面处理铜箔进一步详细地进行说明。
[0031]
本发明人等进行了深入研究,结果发现,压力锅试验(以下,记为“pct”)中的高温高湿环境下的吸湿现象存在来自树脂制基板的表面的吸湿和来自铜箔与树脂制基板的界面的吸湿两种,针对pct后的树脂制基板与铜箔的密合性的下降,来自铜箔与树脂制基板的界面的吸湿的贡献度大。可认为:若水分渗入铜箔与树脂制基板的界面,则偶联剂等提高密合性的化学成分发生水解,或因水分的影响而氧化膜在铜箔的表面生长,由此铜箔与树脂制基板的界面的结合力下降,铜箔与树脂制基板的密合性下降。
[0032]
就最小自相关长度sal为1.0μm以上且8.5μm以下的表面处理铜箔的粗化面而言,由于起伏适度地陡峭变化,因此表面处理铜箔与树脂制基板的界面处的水分的扩散速度变慢。因此,即使在高温高湿环境下(例如pct后)表面处理铜箔与树脂制基板的界面也保持正常,因此容易维持表面处理铜箔与树脂制基板的密合性为高的状态。
[0033]
若表面处理铜箔的粗化面的最小自相关长度sal超过8.5μm,则起伏平缓,因此表面处理铜箔与树脂制基板的界面处的水分的扩散速度快,在高温高湿环境下表面处理铜箔与树脂制基板的密合性恐怕会下降。另一方面,若表面处理铜箔的粗化面的最小自相关长度sal小于1.0μm,则起伏过度地陡峭变化,因此容易在表面处理铜箔与树脂制基板的界面形成间隙。于是,在高温高湿环境下容易在所述间隙积存水分,因此表面处理铜箔与树脂制基板的密合性恐怕会下降。
[0034]
此外,在高密度电路板中,为了兼顾高温高湿环境下的表面处理铜箔与树脂制基板的密合性和微细布线加工性,需要控制表面处理铜箔的粗化面的起伏形状,并且控制微细凹凸的粗糙度。
[0035]
若表面处理铜箔的粗化面的最小自相关长度sal为1.0μm以上且8.5μm以下,并且均方根高度sq为0.10μm以上且0.98μm以下,则会以高水准兼顾高温高湿环境下的表面处理铜箔与树脂制基板的密合性和微细布线加工性。
[0036]
粗化面的均方根高度sq为0.10μm以上且0.98μm以下的表面处理铜箔的微细凹凸
的高度适度地一致,因此利用蚀刻形成布线时,表面处理铜箔稳定地溶解,容易得到蚀刻因子高的图案(即,布线的截面形状容易成为接近矩形的形状)。
[0037]
若表面处理铜箔的粗化面的均方根高度sq超过0.98μm,则恐怕会在利用蚀刻形成布线时,表面处理铜箔的局部高的凸部在树脂制基板上溶解残留(即,产生根部残留),而蚀刻因子下降。若表面处理铜箔的粗化面的均方根高度sq小于0.10μm,则微细凹凸过小,因此常态和高温高湿环境下的表面处理铜箔与树脂制基板的密合性恐怕会下降。
[0038]
需要说明的是,粗化面的最小自相关长度sal优选为1.3μm以上且6.5μm以下,更优选为1.7μm以上且5.7μm以下。此外,粗化面的均方根高度sq优选为0.21μm以上且0.72μm以下,更优选为0.28μm以上且0.54μm以下。
[0039]
进而,使用接触式表面粗糙度测定机所测定出的粗化面的十点平均粗糙度rz优选为1.2μm以上且3.8μm以下。若粗化面的十点平均粗糙度rz在上述范围内,则起到通过锚定效应(anchor effect)而常态下的密合性提高的效果。
[0040]
进而,本实施方式的表面处理铜箔可以通过对电解铜箔的表面实施粗化处理而制成粗化面来制造,实施粗化处理的表面可以是鼓面,也可以是析出面。例如,如果对电解铜箔的鼓面实施粗化处理,则粗化面形成于电解铜箔的鼓面。
[0041]
以下,对本实施方式的表面处理铜箔进一步详细地进行说明。首先,对表面处理铜箔的制造方法的一个例子进行说明。
[0042]
(1)关于电解铜箔的制造方法
[0043]
电解铜箔例如可以使用如图1所示的电解析出装置来制造。图1的电解析出装置具备:不溶性阳极104,由包覆有铂族元素或其氧化物的钛构成;钛制阴极鼓102,其与不溶性阳极104对置设置;以及抛光轮103,其对阴极鼓102进行研磨而去除在阴极鼓102的表面产生的氧化膜。
[0044]
在阴极鼓102与不溶性阳极104之间供给电解液105(硫酸
‑
硫酸铜水溶液),一边使阴极鼓102以一定速度旋转,一边在阴极鼓102与不溶性阳极104之间接通直流电流。由此,铜在阴极鼓102的表面上析出。将所析出的铜从阴极鼓102的表面剥离,连续地进行卷取,由此得到电解铜箔101。
[0045]
制造电解铜箔时,也可以在电解液105中添加添加剂。作为添加剂,可以使用各种添加剂,例如可列举出:亚乙基硫脲、聚乙二醇、四甲基硫脲、聚丙烯酰胺等。在此,通过增加亚乙基硫脲、四甲基硫脲的添加量,能提高常态下的电解铜箔的拉伸强度以及在220℃下加热2小时后在常温下测定出的电解铜箔的拉伸强度。
[0046]
需要说明的是,在电解液105中,也可以添加钼。通过添加钼,能提高铜箔的蚀刻性。通常,在电解析出中,电解液105的铜浓度(硫酸铜中不考虑硫酸成分的仅铜的浓度)是13~72g/l,电解液105的硫酸浓度为26~133g/l,电解液105的液温为18~67℃,电流密度是3~67a/dm2,处理时间为1秒以上且1分钟55秒以下。
[0047]
(2)关于电解铜箔的表面处理
[0048]
<起伏加工处理>
[0049]
起伏加工处理是为了调整铜箔的表面的最小自相关长度sal和均方根高度sq而实施的处理。为了使表面处理铜箔的粗化面的最小自相关长度sal设为上述数值范围,需要通过起伏加工处理来控制电解铜箔的表面的起伏形状。
[0050]
作为起伏加工处理的一个例子,可列举出将含有高浓度的磷酸、硫酸等的溶液用作电解浴的pr(periodic reverse:周期换向)电解。在pr电解中,通过在反向电流(负电流)下利用阳极反应溶解出铜,而在铜箔的表面附近形成电阻和电解浴不同的粘合层。可认为:在流通正向电流(正电流)时,与起伏的凹部相比,在起伏的凸部处粘合层的厚度变薄,电阻变小,因此镀敷电流选择性地集中于凸部,得到陡峭的起伏形状。
[0051]
此外,作为起伏加工处理的另一例子,可列举出将添加有水溶性丙烯酸聚合物、瓜尔胶、聚氧化乙烯等聚合物的硫酸铜溶液用作电解浴,在铜箔中流通反向电流的脉冲电流的脉冲电解。可认为:通过在聚合物附着于起伏的凸部的基础上,流通高电流密度的反向电流的脉冲电流,起伏的凹部会选择性地溶解,得到陡峭的起伏形状。
[0052]
<粗化处理>
[0053]
出于提高与树脂制基板的密合性的目的,对实施有起伏加工处理的电解铜箔的表面实施粗化处理而制成粗化面。通过对电解铜箔的表面实施粗化处理,能将表面处理铜箔的粗化面的均方根高度sq设为上述数值范围。
[0054]
作为粗化处理的一个例子,可列举出在添加有钴(co)、铁(fe)、钼(mo)、锡(sn)、镍(ni)等金属的硫酸铜溶液中,一边通过氮气鼓泡来搅拌硫酸铜溶液,一边对电解铜箔进行电镀的方法。添加至硫酸铜溶液中的金属的种类可以为一种,也可以为两种以上。
[0055]
当通过如上所述的电镀来进行粗化处理时,在铜箔的表面形成粗化粒子而制成粗化面,表面处理铜箔的粗化面也可以具备三个以上粗化粒子凝聚而成的凝聚体。该凝聚体的形状复杂,因此若在粗化面存在凝聚体,则更进一步抑制了表面处理铜箔与树脂制基板的界面处的水分扩散,更进一步抑制了高温高湿环境下的表面处理铜箔与树脂制基板的密合性下降。可认为:若凝聚体由三个以上粗化粒子构成,则由凝聚体构成的凸部高于凝聚体的周边,粗化面的凹凸形状的变化变得陡峭,因此更进一步抑制了表面处理铜箔与树脂制基板的界面处的水分扩散。
[0056]
<镍层、锌层、铬酸盐处理层的形成>
[0057]
在本实施方式的表面处理铜箔中,也可以在利用粗化处理而形成的粗化面上,进一步依次形成镍层、锌层。
[0058]
锌层发挥如下作用:将表面处理铜箔与树脂制基板进行热压接时,防止因表面处理铜箔与树脂制基板的反应而产生的树脂制基板的劣化、表面处理铜箔的表面氧化,提高表面处理铜箔与树脂制基板的密合性。此外,镍层在将表面处理铜箔与树脂制基板进行热压接时,防止锌层的锌向表面处理铜箔中进行热扩散。即,镍层发挥用于使锌层的上述功能有效地发挥的、作为锌层的基底层的作用。
[0059]
需要说明的是,这些镍层、锌层可以应用公知的电镀法、无电镀法来形成。此外,所述镍层可以由纯镍形成,也可以由含磷镍合金形成。
[0060]
此外,若在锌层上进一步进行铬酸盐处理,则在表面处理铜箔的表面形成抗氧化层,因此优选。作为所应用的铬酸盐处理,可以使用公知的方法,例如可列举出日本专利特开昭60
‑
86894号公报中所公开的方法。通过使换算为铬量为0.01~0.3mg/dm2左右的铬氧化物和其水合物等附着,能对表面处理铜箔赋予优异的抗氧化功能。
[0061]
<硅烷处理>
[0062]
也可以对经铬酸盐处理的表面进一步进行使用了硅烷偶联剂的表面处理(硅烷处
理)。通过使用了硅烷偶联剂的表面处理,对表面处理铜箔的表面(与树脂制基板的接合侧的表面)赋予与粘接剂的亲和力强的官能团,因此表面处理铜箔与树脂制基板的密合性进一步提高,表面处理铜箔的防锈性、吸湿耐热性也进一步提高。
[0063]
作为硅烷偶联剂,可以使用各种硅烷偶联剂,例如可列举出:乙烯基系硅烷、环氧基系硅烷、苯乙烯基系硅烷、甲基丙烯酰氧基系硅烷、丙烯酰氧基系硅烷、氨基系硅烷、脲基系硅烷、氯丙基系硅烷、巯基系硅烷、硫化物系硅烷、异氰酸酯系硅烷等硅烷偶联剂。
[0064]
这些硅烷偶联剂通常制成0.001质量%以上且5质量%以下的浓度的水溶液来使用。通过将该水溶液涂布于表面处理铜箔的表面后进行加热干燥,能进行硅烷处理。需要说明的是,使用钛酸酯系、锆酸酯系等偶联剂来代替硅烷偶联剂,也能得到同样的效果。
[0065]
(3)关于覆铜层叠板、印刷电路板的制造方法
[0066]
首先,在由玻璃环氧树脂、聚酰亚胺树脂等构成的电绝缘性的树脂制基板的一方或双方的表面重叠放置表面处理铜箔。这时,使表面处理铜箔的粗化面与树脂制基板对置。然后,当一边对重叠的树脂制基板和表面处理铜箔进行加热,一边施加层叠方向的压力使树脂制基板与表面处理铜箔接合时,可得到带载体或无载体的覆铜层叠板。本实施方式的表面处理铜箔拉伸强度高,因此即使无载体,也能充分应对。
[0067]
接着,对覆铜层叠板的铜箔表面例如照射co2气体激光,进行开孔。即,对铜箔的形成有激光吸收层的面照射co2气体激光,进行形成贯通表面处理铜箔和树脂制基板的贯通孔的开孔加工。然后,若通过常规方法在表面处理铜箔形成高密度布线电路等电路,则能得到印刷电路板。
[0068]
〔实施例〕
[0069]
以下,示出实施例和比较例,进一步具体地说明本发明。
[0070]
(a)电解铜箔
[0071]
作为用于制造实施例1~15和比较例1~5的表面处理铜箔的原料铜箔,使用古河电气工业株式会社制的特殊电解铜箔ws。该电解铜箔的鼓面的十点平均粗糙度rz是0.9μm,析出面的十点平均粗糙度rz为1.0μm。这些十点平均粗糙度rz是使用后述的接触式表面粗糙度测定机而测定出的。
[0072]
(b)起伏加工处理
[0073]
首先,对电解铜箔的鼓面或析出面(参照表1)实施起伏加工处理。作为起伏加工处理,进行使用含有硫酸铜和磷酸的电解浴的pr电解、或使用含有硫酸铜、硫酸以及聚合物的电解浴的脉冲电解。需要说明的是,针对比较例1~3,对电解铜箔不实施起伏加工处理,直接进行作为下一步骤的粗化处理。
[0074]
[表1]
[0075][0076]
pr电解的电解浴中的铜和磷酸的浓度如表1所示。此外,作为脉冲电解的电解浴中的聚合物,使用了水溶性丙烯酸聚合物(东亚合成株式会社制)、瓜尔胶(三昌株式会社制)或聚氧化乙烯(住友精化株式会社制)。脉冲电解的电解浴中的铜、硫酸、水溶性丙烯酸聚合物、瓜尔胶以及聚氧化乙烯的浓度如表1所示。需要说明的是,pr电解的电解浴和脉冲电解的电解浴中添加有硫酸铜五水合物,但在表1中示出作为金属铜的浓度。
[0077]
将pr电解和脉冲电解的条件,即,实施有起伏加工处理的面(处理面)、电解条件、处理时间、电解浴的温度示于表1。在表1中的电解条件下,ion1表示第一阶段的脉冲电流密度,ion2表示第二阶段的脉冲电流密度,ton1表示第一阶段的脉冲电流施加时间,ton2表示第二阶段的脉冲电流施加时间。
[0078]
(c)粗化处理
[0079]
接着,对电解铜箔的实施有起伏加工处理的面实施将表面制成粗化面的粗化处理,来制造表面处理铜箔。具体而言,通过实施在电解铜箔的表面使微细的铜粒子电极沉积的电镀作为粗化处理,制成由铜粒子形成微细凹凸的粗化面。用于电镀的镀液含有硫酸铜和硫酸,并且含有钴或铁,铜浓度、硫酸浓度、钴浓度、铁浓度如表2所示。需要说明的是,镀液中添加有硫酸铜五水合物,但在表2中示出作为金属铜的浓度。
[0080]
将电镀的条件,即,实施有粗化处理的面(处理面)、电流密度i、处理时间、镀浴的温度以及镀浴有无氮气鼓泡示于表2。
[0081]
[表2]
[0082][0083]
(d)镍层(基底层)的形成
[0084]
接着,对表面处理铜箔的粗化面以下述所示的镀ni条件进行电镀,由此形成了镍层(ni的附着量0.33mg/dm2)。用于镀镍的镀液含有硫酸镍、过硫酸铵((nh4)2s2o8)、硼酸(h3bo3),镍浓度为7.5g/l,过硫酸铵浓度为40.0g/l,硼酸浓度为19.5g/l。此外,镀液的温度为28.5℃,ph值为3.8,电流密度为1.8a/dm2,镀敷处理时间为1秒~2分钟。
[0085]
(e)锌层(耐热处理层)的形成
[0086]
进而,在镍层上以下述所示的镀zn条件进行电镀,由此形成了锌层(zn的附着量0.10mg/dm2)。用于镀锌的镀液含有硫酸锌七水合物、氢氧化钠,锌浓度为1~30g/l,氢氧化钠浓度为25~220g/l。此外,镀液的温度为5~60℃,电流密度为0.1~10a/dm2,镀敷处理时间为1秒~2分钟。
[0087]
(f)铬酸盐处理层(防锈处理层)的形成
[0088]
进而,在锌层上以下述所示的镀cr条件进行电镀,由此形成了铬酸盐处理层(cr的附着量0.03mg/dm2)。用于镀铬的镀液含有铬酸酐(cro3),铬浓度为2.2g/l。此外,镀液的温度为15~45℃,ph值为2.5,电流密度为0.3a/dm2,镀敷处理时间为1秒~2分钟。
[0089]
(g)硅烷偶联剂层的形成
[0090]
进而,进行下述所示的处理,在铬酸盐处理层上形成了硅烷偶联剂层。即,在硅烷偶联剂水溶液中添加甲醇或乙醇,调整为规定的ph,得到了处理液。将该处理液涂布于表面处理铜箔的铬酸盐处理层,保持规定时间后,利用热风使其干燥,由此形成了硅烷偶联剂层。
[0091]
(h)评价
[0092]
如上所述,分别制造出实施例1~15和比较例1~5的表面处理铜箔。这些表面处理铜箔的箔厚如表3所记载。对所得到的各表面处理铜箔进行了各种评价。
[0093]
<蚀刻因子>
[0094]
通过减成法(subtractive process),在以如上所述的方式得到的实施例1~15和比较例1~5的表面处理铜箔上,形成了l&s为30/30μm的抗蚀剂图案。然后,进行蚀刻而形成
布线图案。作为抗蚀剂,使用干式抗蚀剂膜,作为蚀刻液,使用含有氯化铜和盐酸的混合液。然后,测定所得到的布线图案的蚀刻因子(ef)。
[0095]
蚀刻因子是指,将铜箔的箔厚设为h,将所形成的布线图案的底部宽度设为b,将所形成的布线图案的顶部宽度设为t时,以下式表示的值。
[0096]
ef=2h/(b
‑
t)
[0097]
在本实施例和比较例中,将蚀刻因子为2.5以上的情况设为良品,将小于2.5的情况设为不良品。
[0098]
若蚀刻因子小,则布线图案中的侧壁的垂直性崩塌,在线宽较窄的微细布线图案的情况下,在邻接的布线图案之间产生铜箔的溶解残留,存在发生短路的危险性、与断线有关的危险性。在本试验中,针对成为蚀刻到位(just etch)位置(抗蚀剂的端部的位置与布线图案的底部的位置对齐)时的布线图案,利用显微镜测定底部宽度b和顶部宽度t,计算出蚀刻因子。将结果示于表3。
[0099]
〔常态下的密合性〕
[0100]
在表面处理铜箔的粗化面接合树脂制基板而制成覆铜层叠板。作为树脂制基板,使用市售的fr4(flame retardant type 4)系树脂的sumitomo bakelite株式会社制的ei
‑
6765,接合时的固化温度设为170℃,固化时间设为2小时。
[0101]
对所制作出的覆铜层叠板的表面处理铜箔进行蚀刻加工,形成宽度1mm的电路布线而制成印刷电路板,将该印刷电路板作为密合性的测定用样品。
[0102]
接着,将测定用样品的树脂制基板侧利用双面胶带固定在不锈钢板上,以50mm/分钟的速度将电路布线沿90度方向拉伸而剥离,测定了密合性(kn/m)。测定进行五次,将所得到的五个测定值的平均值作为常态下的密合性。密合性的测定使用万能材料试验机(株式会社a&d制的tensilon)来进行。在本实施例和比较例中,将常态下的密合性为0.6kn/m以上的情况设为良品,将小于0.6kn/m的情况设为不良品。将结果示于表3。
[0103]
〔高温高湿环境下的密合性〕
[0104]
使用与常态下的密合性的测定中使用的上述测定用样品同样的测定用样品,测定了高温高湿环境下的密合性。首先,使用压力锅试验机,将测定用样品在温度121℃、湿度100%rh、气压2atm的环境下保持48小时,进行了pct。接着,以与常态下的密合性的测定同样的方式测定pct后的测定用样品的密合性(kn/m)。测定进行五次,将所得到的五个测定值的平均值作为pct后的密合性。在本实施例和比较例中,将pct后的密合性为0.2kn/m以上的情况设为良品,将小于0.2kn/m的情况设为不良品。将结果示于表3。
[0105]
〔最小自相关长度sal、均方根高度sq的测定〕
[0106]
使用bruker公司的三维白光干涉型显微镜wyko contourgt
‑
k,测定实施例1~15和比较例1~5的表面处理铜箔的粗化面的表面形状,进行了形状解析,求出最小自相关长度sal和均方根高度sq。表面形状的测定在各表面处理铜箔的任意五处进行,分别对五处进行形状解析,求出五处各自的最小自相关长度sal和均方根高度sq。然后,将所得到的五处的结果的平均值作为各表面处理铜箔的最小自相关长度sal和均方根高度sq。
[0107]
形状解析是使用高分辨率ccd(charge coupled device:电荷耦合器件)相机以vsi(vertical scanning interferometry:垂直扫描干涉)测定方式(垂直扫描型干涉法)进行。条件设为:光源为白光、测定倍率为10倍、测定范围为477μm
×
357.8μm、横向取样
(lateral sampling)为0.38μm、速度(speed)为1、反向扫描(backscan)为10μm、长度(length)为10μm、阈值(threshold)为3%,进行项目移除(terms removal)(缸筒与倾斜(cylinder and tilt))、数据恢复(data restore)(方法:遗留(legacy)、迭代(iterations)5)、统计滤波器(statistic filter)(滤波器尺寸(filter size):3,滤波器类型(filter type):中值(median))、傅立叶滤波器(fourier filter)(高频通过(high freq pass)、傅立叶滤波窗(fourier filter window):高斯(gaussian),频率截止(frequency cutoff):高频截止(high cutoff)=12.5mm
‑1)的滤波处理后,进行数据处理。将结果示于表3。
[0108]
〔十点平均粗糙度rz的测定〕
[0109]
针对实施例1~15和比较例1~5的表面处理铜箔的粗化面,依照jis b 0601:1994的规定测定了十点平均粗糙度rz(μm)。测定在各表面处理铜箔的任意五处进行,将其平均值设为十点平均粗糙度rz。此外,作为测定装置,使用株式会社小阪研究所制接触式表面粗糙度测定机surfcorder se1700。测定条件为测定长度4.8mm、取样长度4.8mm、截止(cutoff)值0.8mm。将结果示于表3。
[0110]
〔凝聚体〕
[0111]
使用扫描式电子显微镜,以倍率5000倍拍摄实施例1~15和比较例1~5的表面处理铜箔的粗化面的sem图像的三个视野(纵13.9μm、横18.6μm),确认是否存在三个以上粗化粒子凝聚而成的凝聚体。将结果示于表3。
[0112]
[表3]
[0113][0114]
根据表3可知,实施例1~15的表面处理铜箔的蚀刻因子(ef)大,除了具有微细布线加工性以外,常态下的密合性和pct后的密合性优异。
[0115]
附图标记说明
[0116]
101:电解铜箔;102:阴极鼓;104:不溶性阳极;105:电解液。
再多了解一些
本文用于企业家、创业者技术爱好者查询,结果仅供参考。