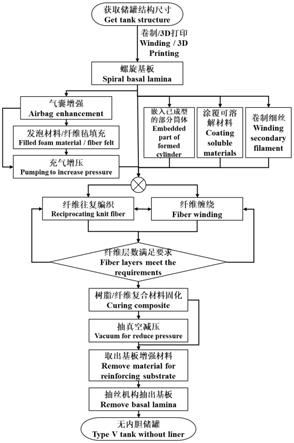
一种
ⅴ
型无内胆高压复合材料储罐成型工艺
技术领域
1.本发明涉及特种设备加工成型领域,具体涉及一种
ⅴ
型无内胆高压复合材料储罐成型工艺。
背景技术:
2.开发安全、轻质、高效的储氢瓶等高压储气罐已经成为目前一种重要的能源储运技术需求。针对于当前的能源储运需求,ⅳ型储氢瓶相比于ⅲ型储氢瓶具有更大的轻量化优势,其将储氢密度提升至5wt.%以上,很大程度上提高了能源的储运和利用效率。然而,内胆的存在仍然没有避开内胆塌陷、鼓包等失效问题。同时,作为储氢瓶的一种分工,储氢瓶的内胆主要用于阻隔气体,防止高压气体在瓶身处大量泄露;而外层的碳纤维复合材料作为承压层主要用于承受储氢瓶内外的大压差带来的应力。然而,碳纤维复合材料层虽然只用于承压,但是其也具有较小的气体渗漏系数,并且显示出较好的气体阻隔性能;而内胆作为阻隔层,通常在承压过程中基本不能分担多少压差带来的应力,而且还在储氢瓶的总体重量中占有较大的比例。不仅如此,因为内胆和碳纤维复合材料层的材料不同,其在各种物理性能例如热性能等方面都存在不同,这也会导致储氢瓶在使用过程中遇到环境因素导致的问题。因此,研究人员目前已经开发出了一种无内胆的
ⅴ
型储氢瓶,将气体阻隔和承压复合到碳纤维复合材料本身,不仅可以进一步提高储氢密度,还避免了多种材料性能不同导致的使用问题。
3.然而,
ⅴ
型储氢瓶是完全通过碳纤维复合材料丝束缠绕成型的,在没有内胆(成型基板)的情况下成型具有较大的挑战性。当前,仅美国的composites technology development(ctd)公司与美国空军研究实验室(wright
‑
patterson afb)和德克萨斯大学合作建造了可商用、全复合材料、无内衬的压力容器,其通过先制造一个可溶解的、与储氢瓶形状一致的成型基板,然后在成型基板上缠绕碳纤维复合材料并固化后溶解基板的方式成型
ⅴ
型储氢瓶。这种方法的效率较低,成本高,且成型前仍需要一套模具成型基板。当前,弹簧制造技术已经十分成熟,同时,简易螺旋结构的3d打印技术也趋于成熟,因此,可以利用瘫痪制造技术或3d打印技术制造
ⅴ
型储氢瓶成型基板,但目前无人开展相关研究。
4.除此之外,碳纤维复合材料的缠绕/铺设也是一大难点,目前高压储氢瓶等多采用的纤维缠绕方式是纤维束以一定角度在储氢瓶内胆上进行缠绕,最终获得碳纤维层。然而,碳纤维丝束单丝缠绕的方式成型的
ⅴ
型储氢瓶碳纤维复合材料层会存在未充分激发无机材料/碳纤维阻隔性能的问题。将碳纤维编织后可分配载荷、减轻微裂纹、空隙和制造引起的缺陷的生长以及可有效提高延展性、阻挡层抗损伤性。目前美国的composites technology development公司(专利号:us8074826b2)计划采用先编织材料再切割的方式在储氢瓶制造中在基板上铺设编织碳纤维,这种技术手段效率低,成本高,且切割位置容易出现不连续和薄弱点的问题,有可能导致一系列的连带问题。在纤维铺设过程中也计划采用手动方式铺设,这样效率低,成型精度差。而当前等直径圆管纤维编织技术已经趋于成熟,但还未被用于成型
ⅴ
型储氢瓶等变直径结构和成型往复结构。因此,其技术原理可被借
鉴用于成型编织碳纤维复合材料层。
技术实现要素:
5.本发明提出一种
ⅴ
型无内胆高压复合材料储罐成型工艺,通过创新设计加工结构和成型路径,利用弹簧卷制技术/3d打印技术按照所需储气瓶的形状快速成型一种新型的无内胆高压复合材料储罐旋制基板,再通过往复纤维编织技术与纤维缠绕技术在旋制基板上成型碳纤维复合材料层获得储气瓶。本发明可连续编织储气瓶状碳纤维复合材料层,并快速形成和拆除具有一定结构刚度的旋制基板,提高成型效率和实现基板的可重复利用。同时,本发明的工艺装备可适用于不同直径、长度、封头结构的
ⅴ
型无内胆高压复合材料储罐成型,具有较高的灵活性。
6.本发明一种
ⅴ
型无内胆高压复合材料储罐成型工艺,至少包括旋制基板成型、碳纤维复合材料编织/缠绕成型、旋制基板卸载等工艺。其工艺路径为:首先,弹簧卷制机将选定截面形状尺寸的丝材(金属丝或聚合物丝材)按照储气瓶内部结构形状和尺寸卷制成旋制基板,并在旋制基板上喷涂脱模剂。第二,通过纤维编织设备/纤维缠绕设备在旋制基板上从瓶口处开始按照预定交错角度沿旋制基板轴线方向编织/缠绕碳纤维复合材料;当碳纤维复合材料编织至旋制基板的另一端时,在端部编织纤维上紧密缠绕多圈碳纤维进行限位和固定;然后,通过纤维缠绕设备在已经编织好的纤维上缠绕预定层数的碳纤维复合材料;缠绕完成后,碳纤维编织设备开始沿旋制基板轴线向上一层编织碳纤维层的反方向继续编织碳纤维复合材料层;上述纤维复合材料编织和缠绕交替进行,直至满足编织层数要求。第三,将旋制基板和碳纤维复合材料层一同送入树脂固化装备中进行固化,待固化后取出制品。第四,通过抽丝机构,将成型旋制基板的金属丝拉直并缓慢抽出储气瓶,与此同时,制品需要跟随抽丝动作绕基板轴线旋转,防止在抽丝过程中因为金属丝的扭转而破坏储气瓶内表面。最终获得满足要求的储气瓶。
7.作为本发明一种
ⅴ
型无内胆高压复合材料储罐成型工艺的旋制基板成型补充说明:
8.本发明所述旋制基板也可采用3d打印技术成型,打印过程中成型旋制基板的塑料不需要完全熔融,只要塑料可以发生塑性形变或表面熔融可以简单熔接即可,便于后期取出基板。
9.本发明所述旋制基板的筒体直径、筒体长度、封头径高比等尺寸由储气瓶内部尺寸决定,卷制/打印过程中通过控制设备出口旋转角度制造。
10.本发明所述旋制基板成型过程中的丝材之间的螺旋导程按照具体需求确定,包括但不限于:所有位置导程一致;封头处导程小,筒体处导程大;各处导程变化不定或按照某种规律变化。
11.本发明所述旋制基板成型金属丝的直径不应超过瓶口直径,建议金属丝的直径在满足旋制基板刚度的要求下选用较小直径的金属丝材。
12.本发明所述旋制基板若未能满足表面精度需求或强度/刚度需求,可做以下补充工艺,下述工艺可不使用、单一选用、组合使用,均属于本发明范畴:其一,在丝材卷制/打印成型的旋制基板内加入可充气耐高温的弹性材料制成的气囊,在纤维复合材料编织/缠绕过程前向气囊中充入一定压力的安全气体,使气囊作为旋制基板的辅助支撑。其二,在气囊
中填充开孔泡沫材料或纤维毡材料,填充材料以颗粒的形式填充,在纤维编织/缠绕过程、树脂固化过程中,填充材料内保持一定压力的气体,在纤维复合材料固化完成后,对气囊抽真空并取出填充物和气囊。其三,为提高效率和保证筒体部分表面质量,也可以先利用与纤维复合材料一样的材料在圆柱形的芯轴上成型出一部分筒体结构,然后将筒体结构套在旋制基板上,再继续按照纤维编织/缠绕工艺成型外部主体纤维复合材料。其四,将旋制基板表面涂覆一层可溶解的固体材料,例如聚乙烯醇(pva,可用热水溶解)、聚丙烯腈(pan,可用二甲基亚砜dmso溶解)等,使基板外表面保持光滑,当碳纤维复合材料固化完成后,抽出旋制基板并溶解涂覆在旋制基板上的材料。其五,在较粗的金属丝卷制的旋制基板上再使用较细的金属丝卷制一层基板,以减小原旋制基板上的缝隙。其六,针对长径比较大的储气瓶成型,可在旋制基板轴线处增加一根芯轴,以提高成型过程中的刚度。
13.本发明所述旋制基板卷制使用的金属丝或旋制基板打印使用的聚合物丝的截面形状可设计为圆形、矩形、梯形、三角形等形状。
14.作为本发明一种
ⅴ
型无内胆高压复合材料储罐成型工艺的旋制基板成型的特殊补充说明:本发明建议以金属丝卷制成型的旋制基板作为基础基板,而在基础基板上进行上述的强度/刚度增强,以便于在碳纤维复合材料编织/缠绕过程中多层碳纤维复合材料层可紧密接触,不形成缺陷。作为特殊的增强手段,上述第二项增强工艺可在无基础旋制基板的条件下单独作为无内胆高压储气瓶成型基板使用,其也在本发明保护范畴:在气囊中填充开孔泡沫材料或纤维毡材料,填充材料以颗粒的形式填充,在纤维编织/缠绕过程、树脂固化过程中,填充材料内一直保持一定压力的气体,在纤维复合材料固化完成后,对气囊抽真空并取出填充物和气囊。
15.作为本发明一种
ⅴ
型无内胆高压复合材料储罐成型工艺的纤维编织/缠绕成型工艺补充说明:
16.本发明所述纤维编织/缠绕工艺优选在与基板接触的第一层就编织至少一层碳纤维复合材料。
17.本发明所述纤维编织/缠绕工艺中编织纤维层与缠绕纤维层在总层数中的占比可根据气瓶压力、结构尺寸等要求选择;在满足性能要求的条件下,可全部选用编织层或全部选用缠绕层;编织纤维层与缠绕纤维层的组合方式可选择交叠式(等比例重复)、阶梯式(比例逐渐变化)或其他自由组合形式。
18.本发明所述编织工艺中碳纤维复合材料的编织方式可采用纤维带两两交错编织方式,也可采用一跨二或一跨多条纤维束的编织方式,具体编织方式由储氢瓶性能要求决定。
19.作为本发明一种
ⅴ
型无内胆高压复合材料储罐成型工艺的旋制基板卸载工艺的补充说明:本发明优选在旋制基板卸载过程中制品与抽丝机构绕轴心发生相对旋转运动,防止旋制基板上的金属丝在被抽丝机构拉直并抽走的过程中金属丝发生扭转而破坏储气瓶内表面。
20.本发明一种
ⅴ
型无内胆高压复合材料储罐成型工艺可实现纤维精确、紧密编织/缠绕成型无内胆高压储罐,同时,本发明还可实现在纤维编织过程中连续纤维层无需裁剪、拼接等操作,不形成应力缺陷和气体渗漏缺陷。相比于现有的有内胆高压储罐成型工艺,本发明提出一种新的纤维往复编织工艺及理念。在无内胆高压储罐成型方面,本发明提出一
种形状可变、适应性强、高效、低成本、无污染、易回收的基板模型和成型工艺,同时提出多种弱刚度基板强度/刚度增强手段。
附图说明
21.图1所示为本发明一种
ⅴ
型无内胆高压复合材料储罐成型工艺的旋制基板与储气瓶成型位置示意图。
22.图2所示为本发明一种
ⅴ
型无内胆高压复合材料储罐成型工艺的不同导程旋制基板示意图。
23.图3所示为本发明一种
ⅴ
型无内胆高压复合材料储罐成型工艺的旋制基板与已成型的部分筒体结构安装示意图。
24.图4所示为本发明一种
ⅴ
型无内胆高压复合材料储罐成型工艺的旋制基板上涂覆可溶解固体材料的局部示意图。
25.图5所示为本发明一种
ⅴ
型无内胆高压复合材料储罐成型工艺的旋制基板上再使用较细的金属丝卷制一层基板的局部示意图。
26.图6所示为本发明一种
ⅴ
型无内胆高压复合材料储罐成型工艺的旋制基板通过气囊增强的结构示意图。
27.图7所示为本发明一种
ⅴ
型无内胆高压复合材料储罐成型工艺的往复纤维无损编织结构局部示意图。
28.图8所示为本发明一种
ⅴ
型无内胆高压复合材料储罐成型工艺的纤维复合材料编织形式示意图。
29.图9所示为本发明一种
ⅴ
型无内胆高压复合材料储罐成型工艺的工艺流程图。
30.图10所示为本发明一种
ⅴ
型无内胆高压复合材料储罐成型工艺的无旋制基板成型的成型流程图。
31.图中:1
‑
旋制基板;1
‑1‑
金属丝;2
‑
碳纤维复合材料层;2
‑1‑
编织纤维层;2
‑2‑
缠绕纤维层;3
‑
瓶口结构;4
‑
在芯轴上已提前成型的储气瓶部分筒体结构;5
‑
可溶解材料;6
‑
细金属丝;7
‑
气囊。
具体实施方式
32.如图9所示,本发明一种
ⅴ
型无内胆高压复合材料储罐成型工艺,至少包括旋制基板1成型、碳纤维复合材料层2编织/缠绕成型、旋制基板1卸载等工艺。如图1所示,其工艺路径为:首先,如图2所示,弹簧卷制机将选定直径的金属丝1
‑
1按照储气瓶内部结构形状和尺寸卷制成旋制基板1,并在旋制基板1上喷涂脱模剂。第二,如图7所示,通过纤维编织设备/纤维缠绕设备在旋制基板1上从瓶口3处开始按照预定交错角度沿旋制基板1轴线方向编织/缠绕碳纤维复合材料;当碳纤维复合材料编织至旋制基板1的另一端时,在端部编织纤维2
‑
1上紧密缠绕多圈碳纤维进行限位和固定;然后,通过纤维缠绕设备在已经编织好的纤维2
‑
1上缠绕预定层数的碳纤维复合材料2
‑
2;缠绕完成后,碳纤维编织设备开始沿旋制基板1轴线向上一层编织碳纤维层的反方向继续编织碳纤维复合材料层;上述纤维复合材料编织和缠绕交替进行,直至满足编织层数要求。第三,将旋制基板1和碳纤维复合材料层2一同送入树脂固化装备中进行固化,待固化后取出制品。第四,通过抽丝机构,将成型旋制基
板1的金属丝1
‑
1拉直并缓慢抽出储气瓶,与此同时,制品需要跟随抽丝动作绕旋制基板1轴线旋转,防止在抽丝过程中因为金属丝1
‑
1的扭转而破坏储气瓶内表面。最终获得满足要求的储气瓶。
33.如图9所示,作为本发明一种
ⅴ
型无内胆高压复合材料储罐成型工艺的旋制基板成型补充说明:
34.本发明所述旋制基板1也可采用3d打印技术成型,打印过程中成型旋制基板1的塑料不需要完全熔融,只要塑料可以发生塑性形变或表面熔融可以简单熔接即可。
35.如图1所示,本发明所述旋制基板1的筒体直径、筒体长度、封头径高比等尺寸由储气瓶内部尺寸决定,卷制/打印过程中通过控制设备出口旋转角度制造。
36.如图2所示,本发明所述旋制基板1成型过程中的丝材1
‑
1之间的螺旋导程按照具体需求确定,包括但不限于:所有位置导程一致,图2(a);封头处导程小,筒体处导程大,图2(b);各处导程变化不定或按照某种规律变化。
37.本发明所述旋制基板1若未能满足表面精度需求或强度/刚度需求,可做以下补充工艺,下述工艺可不使用、单一选用、组合使用,均属于本发明范畴:其一,如图6所示,在丝材卷制/打印成型的旋制基板内加入可充气耐高温的弹性材料制成的气囊7,在纤维复合材料编织/缠绕过程前向气囊7中充入一定压力的安全气体,使气囊7作为旋制基板1的辅助支撑。其二,在气囊7中填充开孔泡沫材料或纤维毡材料,填充材料以颗粒的形式填充,在纤维编织/缠绕过程、树脂固化过程中,填充材料内保持一定压力的气体,在纤维复合材料固化完成后,对气囊7抽真空并取出填充物和气囊7。其三,如图3所示,为提高效率和保证筒体部分表面质量,也可以先利用与纤维复合材料一样的材料在圆柱形的芯轴上成型出一部分筒体结构4,然后将筒体结构4套在旋制基板1上,再继续按照纤维编织/缠绕工艺成型外部主体纤维复合材料。其四,如图4所示,将旋制基板1表面涂覆一层可溶解的固体材料5,例如聚乙烯醇(pva,可用热水溶解)、聚丙烯腈(pan,可用二甲基亚砜dmso溶解)等,使旋制基板1外表面保持光滑,当碳纤维复合材料层2固化完成后,抽出旋制基板1并溶解涂覆在旋制基板上的材料5。其五,如图5所示,在较粗的金属丝1
‑
1卷制的旋制基板1上再使用较细的金属丝6卷制一层基板,以减小原旋制基板1上的缝隙。其六,针对长径比较大的储气瓶成型,可在旋制基板1轴线出增加一根芯轴,以提高成型过程中的刚度。
38.如图10所示,作为本发明一种
ⅴ
型无内胆高压复合材料储罐成型工艺的旋制基板1成型的特殊补充说明:本发明建议以金属丝1
‑
1卷制成型的旋制基板1作为基础基板,而在基础基板上进行上述的强度/刚度增强,以便于在碳纤维复合材料编织/缠绕过程中多层碳纤维复合材料层可紧密接触,不形成缺陷。作为特殊的增强手段,上述第二项增强工艺可在无基础旋制基板1的条件下单独作为无内胆高压储气瓶成型基板使用,其也在本发明保护范畴:在气囊7中填充开孔泡沫材料或纤维毡材料,填充材料以颗粒的形式填充,在纤维编织/缠绕过程、树脂固化过程中,填充材料内一直保持一定压力的气体,在纤维复合材料固化完成后,对气囊7抽真空并取出填充物和气囊7。
39.作为本发明一种
ⅴ
型无内胆高压复合材料储罐成型工艺的纤维编织/缠绕成型工艺补充说明:
40.如图7所示,本发明所述纤维编织/缠绕工艺中编织纤维层2
‑
1与缠绕纤维层2
‑
2在总层数中的占比可根据气瓶压力、结构尺寸等要求选择;在满足性能要求的条件下,可全部
选用编织层2
‑
1或全部选用缠绕层2
‑
2;编织纤维层2
‑
1与缠绕纤维层2
‑
2的组合方式可选择交叠式(等比例重复)、阶梯式(比例逐渐变化)或其他自由组合形式。
41.如图8所示,本发明所述编织工艺中碳纤维复合材料的编织方式可采用纤维带两两交错编织方式(a),也可采用一跨二(b)或一跨多条纤维束(c)的编织方式,具体编织方式由储氢瓶性能要求决定。
再多了解一些
本文用于企业家、创业者技术爱好者查询,结果仅供参考。