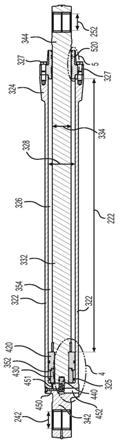
1.本实用新型总体上涉及一种用于重型机械的液压油缸,并且更具体地涉及一种具有满足机械的运动学、结构和载荷要求的特定性能尺寸的液压油缸。
背景技术:
2.重型机械(诸如挖掘机、平地机、前端装载机和推土机)上的常规液压系统可包括泵,所述泵从储罐中抽出低压流体,对流体加压,并且使加压流体可供多个不同的致动器使用以用于移动致动器。致动器可包括被专门设计为满足各种运动学、结构和载荷要求的液压油缸以在使用机器执行其被分配的任务时使机器的各种结构元件相对于彼此动。例如,一个或多个液压油缸可被专门设计为处理在操作特定机器以执行作业任务(诸如挖掘、移动土方、举起重物和搬运重物)时所需的液压压力、运动学特性、扭转应力、压缩应力、抗拉应力、环向应力、运动范围和运动速度。在各种示例性装置中,每个致动器的速度可通过选择性地节流(即,限制)从泵进入每个致动器的加压流体的流量而独立地控制。例如,为了以高速移动特定致动器,从泵到致动器中的流体流仅受到少量限制(或完全不受限制)。相反地,为了以低速移动同一致动器或另一致动器,增加对流体流的限制。尽管适合许多应用,但是使用流体限制以控制致动器速度可能导致压力损失,从而降低液压系统的整体效率。
3.替代类型的液压系统被称为闭环液压系统。闭环液压系统通常包括泵,所述泵以闭环方式连接到单个致动器或串联操作的一对致动器。在操作期间,泵从致动器的一个腔室中抽出流体,并且将加压流体排放到同一致动器的相对腔室中。例如,当液压油缸的杆缩回时,可将液压流体泵入液压油缸的杆端室并从与液压油缸中的杆附接的活塞的相对侧的头端室排出,并且在杆延伸时将液压流体泵入头端室并从杆端室排出。为了以更高速度移动致动器,泵以更快速率排出流体。为了以更低速度移动致动器,泵以更慢速率排出流体。闭环液压系统通常比常规液压系统更有效,因为致动器的速度通过泵操作而不是流体限制来控制。即,泵被控制以仅排出与使致动器以期望速度移动所需的一样多的流体,并且不需要对流体进行节流。
4.在izumi等人的美国专利4,369,625中公开了一种与一个或多个液压油缸结合使用的示例性闭环液压系统,所述专利公布于1983年1月25日('625专利)。在'625专利中,描述了一种具有流量组合功能性的多致动器无计量型液压系统。液压系统包括回转回路、动臂回路、斗杆回路、铲斗回路、左行进回路和右行进回路。回转、动臂、斗杆和铲斗回路中的每一者具有泵,所述泵以闭环方式连接到专用液压油缸。另外,第一组合阀连接在回转回路与斗杆回路之间,第二组合阀连接在斗杆回路与动臂回路之间,并且第三组合阀连接在铲斗回路与动臂回路之间。左右行进回路分别与铲斗和动臂回路的泵并联连接。在这种构造中,任何一个液压油缸都可从一个以上的泵接收加压流体,使得其速度不受单个泵的容量的限制。
5.尽管改进了现有的闭环液压系统,但是上述'625专利的闭环液压系统仍可能不是最佳的。具体地,系统的连接回路只能顺序地执行。另外,可能难以控制各种致动器的速度
和力。
技术实现要素:
6.本实用新型提供了一种致动器及机器,能够解决现有技术存在的致动器中的各部件尺寸相互关系设计未能优化影响机器综合性能的技术问题。
7.一种致动器,被构造成用于相对于机器上的第二结构元件致动所述机器上的第一结构元件,所述致动器包括:
8.管,所述管包括中心轴向延伸孔,所述中心轴向延伸孔限定在所述管中,在所述管的封闭远端与所述管的开口近端之间延伸;
9.杆,所述杆可滑动地安装在所述管内,所述杆通过头部密封总成可滑动地支撑在所述管的近端处;
10.活塞,所述活塞安装在所述杆的远端处;
11.活塞保持总成,所述活塞保持总成附接到所述杆的所述远端并且被构造成将所述杆的所述远端处的所述活塞保持在所述活塞保持总成与安装在所述杆的所述远端的直径减小部分上的衬套之间;
12.耳轴帽孔,所述耳轴帽孔被限定穿过所述管的所述封闭远端并且被构造成用于接纳耳轴销,所述耳轴销适于将所述管的所述远端枢转地连接到所述机器的所述第一结构元件;以及
13.杆眼孔,所述杆眼孔被限定穿过所述杆的近端并且被构造成用于接纳杆眼销,所述杆眼销适于将所述杆的所述近端枢转地连接到所述机器的所述第二结构元件;其中
14.当所述杆和所述活塞完全缩回到所述管中使得所述杆的所述远端位于所述管的所述封闭远端时,从所述耳轴帽孔的中心到所述杆眼孔的中心的缩回的销间尺寸等于1505mm
±
2.0 mm;
15.从所述活塞的与所述管的所述封闭远端相邻的第一完全缩回位置到所述活塞的在所述管的所述近端处与所述头部密封总成接触的第二完全延伸位置的冲程尺寸等于1015mm
±
2.0 mm;
16.所述杆眼孔直径等于80mm
±
0.5 mm;
17.所述耳轴帽孔直径等于60 mm
±
0.5 mm;
18.所述管的所述中心轴向延伸孔的直径等于105 mm
±
0.5 mm;
19.所述杆的直径等于75mm
±
0.5 mm。
20.供应给所述致动器的液压流体的压力是35,000 kpa
±
3,500 kpa。
21.所述机器为挖掘机,所述第一结构元件包括所述挖掘机的主体,所述第二结构元件包括所述挖掘机的动臂。
22.还包括阻尼总成,所述阻尼总成被布置在所述管的所述封闭远端处,当所述杆完全缩回到所述管中时邻近所述杆的所述远端。
23.所述阻尼总成从所述管的所述封闭远端的径向居中部分轴向地突出。
24.所述阻尼总成被构造成当所述杆完全缩回到所述管中时被接纳在形成于所述杆的所述远端中的配合盲孔内。
25.还包括阻尼总成,所述阻尼总成被保持在所述杆的所述远端中的盲孔内,所述阻
尼总成被构造成当所述杆完全缩回到所述管中时进入在所述管的所述封闭远端中的径向居中轴向孔中。
26.还包括延伸到所述管的所述封闭远端中的轴向释放孔,所述轴向释放孔平行于并偏离所述管的中心轴线延伸,穿透到所述管的所述封闭远端,并且与径向取向释放孔相交,所述径向取向释放孔在限定于所述管的所述远端中的压力释放室与管的外圆周外围之间延伸。
27.所述头部密封总成用螺栓连接到被设置在所述管的所述近端处的杆端凸台。
28.一种机器,包括多个结构元件和多个液压致动器,每个液压致动器互连所述结构元件中的两个,
29.其中每个液压致动器被构造成相对于所述机器上的第二结构元件致动所述机器上的第一结构元件,每个液压致动器包括:
30.管,所述管包括中心轴向延伸孔,所述中心轴向延伸孔限定在所述管中,在所述管的封闭远端与所述管的开口近端之间延伸;
31.杆,所述杆可滑动地安装在所述管内,所述杆通过头部密封总成可滑动地支撑在所述管的近端处;
32.活塞,所述活塞安装在所述杆的远端处;
33.活塞保持总成,所述活塞保持总成附接到所述杆的所述远端并且被构造成将所述杆的所述远端处的所述活塞保持在所述活塞保持总成与安装在所述杆的所述远端的直径减小部分上的衬套之间;
34.耳轴帽孔,所述耳轴帽孔被限定穿过所述管的所述封闭远端并且被构造成用于接纳耳轴销,所述耳轴销适于将所述管的所述远端枢转地连接到所述机器的所述第一结构元件;以及
35.杆眼孔,所述杆眼孔被限定穿过所述杆的近端并且被构造成用于接纳杆眼销,所述杆眼销适于将所述杆的所述近端枢转地连接到所述机器的所述第二结构元件;其中
36.当所述杆和所述活塞完全缩回到所述管中使得所述杆的所述远端位于所述管的所述封闭远端时,从所述耳轴帽孔的中心到所述杆眼孔的中心的缩回销间尺寸等于1505mm
±
2.0 mm;
37.从所述活塞的与所述管的所述封闭远端相邻的第一完全缩回位置到所述活塞的在所述管的所述近端处与所述头部密封总成接触的第二完全延伸位置的冲程尺寸等于1015 mm
±
2.0 mm;
38.所述杆眼孔直径等于80 mm
±
0.5 mm;
39.所述耳轴帽孔直径等于60 mm
±
0.5 mm;
40.所述管的所述中心轴向延伸孔的直径等于105 mm
±
0.5 mm;
41.所述杆的直径等于75mm
±
0.5 mm;并且
42.供应给所述致动器的液压流体的压力是35,000 kpa
±
3,500 kpa。
43.在一个方面,本实用新型涉及一种致动器,所述致动器被构造成相对于机器的第二结构元件来致动所述机器的第一结构元件。所述致动器可包括管,所述管包括中心轴向延伸孔,所述中心轴向延伸孔限定在所述管中,在所述管的封闭远端与所述管的开口近端之间延伸。杆可滑动地安装在所述管内,所述杆通过头部密封总成可滑动地支撑在所述管
的近端处。活塞可安装在所述杆的远端处,并且活塞保持总成可附接到所述杆的所述远端并且可被构造成将所述杆的所述远端处的所述活塞保持在所述活塞保持总成与安装在所述杆的所述远端的直径减小部分上的衬套之间。耳轴帽孔可被限定穿过所述管的所述封闭远端并且被构造成用于接纳耳轴销,所述耳轴销适于将所述管的所述远端枢轴地连接到所述机器的所述第一结构元件。杆眼孔可被限定穿过所述杆的所述近端并且被构造成用于接纳杆眼销,所述杆眼销适于将所述杆的所述近端枢转地连接到所述机器的所述第二结构元件。
44.在另一方面,本实用新型涉及一种包括多个结构元件和各自将所述两个结构元件中的两者互连的多个液压致动器的机器,其中每个液压致动器被构造成相对于所述机器上的第二结构元件致动所述机器上的第一结构元件。每个液压致动器可包括管,所述管具有中心轴向延伸孔,所述中心轴向延伸孔限定在所述管中,在所述管的封闭远端与所述管的开口近端之间延伸。杆可滑动地安装在所述管内,所述杆通过头部密封总成可滑动地支撑在所述管的近端处。活塞可安装在所述杆的远端处,并且活塞保持总成可附接到所述杆的所述远端并且可被构造成将所述杆的所述远端处的所述活塞保持在所述活塞保持总成与安装在所述杆的所述远端的直径减小部分上的衬套之间。耳轴帽孔可被限定穿过所述管的所述封闭远端并且被构造成用于接纳耳轴销,所述耳轴销适于将所述管的所述远端枢轴地连接到所述机器的所述第一结构元件。杆眼孔可被限定穿过所述杆的所述近端并且被构造成用于接纳杆眼销,所述杆眼销适于将所述杆的所述近端枢转地连接到所述机器的所述第二结构元件。
45.在又另一方面,本实用新型涉及一种液压油缸,所述液压油缸被构造成相对于机器上的第二结构元件来致动所述机器上的第一结构元件。所述液压油缸可包括管,所述管包括中心轴向延伸孔,所述中心轴向延伸孔限定在所述管中,在所述管的封闭远端与所述管的开口近端之间延伸。杆可滑动地安装在所述管内,所述杆通过头部密封总成可滑动地支撑在所述管的近端处。活塞可安装在所述杆的远端处,并且活塞保持总成可附接到所述杆的所述远端并且可被构造成将所述杆的所述远端处的所述活塞保持在所述活塞保持总成与安装在所述杆的所述远端的直径减小部分上的衬套之间。耳轴帽孔可被限定穿过所述管的所述封闭远端并且被构造成用于接纳耳轴销,所述耳轴销适于将所述管的所述远端枢轴地连接到所述机器的所述第一结构元件。杆眼孔可被限定穿过所述杆的所述近端并且被构造成用于接纳杆眼销,所述杆眼销适于将所述杆的所述近端枢转地连接到所述机器的所述第二结构元件。
46.本实用新型提供了一种致动器及机器,致动器的液压油缸被设计成具有特定性能尺寸的范围,所述范围通过广泛的分析与经验数据和其他以客户为中心的数据的组合来确定,所述广泛的分析包括基于物理学的方程的应用、有限元分析和考虑了在使用期间将施加在油缸上的运动学和结构应力的其他计算分析,所述数据旨在满足特定的工作要求并解决现有技术的一个或多个技术问题和/或现有技术的其他技术问题。这些技术问题包括部件应力、操作特性、疲劳寿命以及液压系统的总体效率低等问题。
47.此外,对于冲程、完全缩回时的销间长度、杆端销的直径以及油缸的头端的耳轴销的直径,液压油缸优选地被设计成具有特定的尺寸范围,这取决于特定的机器和将使用液压油缸的载荷应用。
48.另外,用于重型机械的液压油缸可得益于本实用新型公开的特定性能尺寸以及诸如阻尼装置和头部密封装置的特征的组合,所述数值特征组合形成的技术方案改进了在极端条件下的操作特性、疲劳寿命和综合性能。
49.本实用新型的液压油缸各数值及相互之间的关系,诸如冲程尺寸、销间尺寸、耳轴帽孔和耳轴销直径以及杆眼孔和杆眼销直径,该特定数值是通过广泛的数据分析来确定,所述数据包括经验数据和其他以客户为中心的数据。所述数据分析包括基于物理学的方程的应用、有限元分析,以及考虑到在使用期间将施加在液压缸上供给液压流体压力、运动学和结构应力的其他计算分析。由此得出所述数值能够满足操作作业要求并解决了现有技术问题中未能优化数值所带来的一个或多个技术问题。
50.可见,本实用新型公开的实施例可提供改进的能量使用和节约。另外,组合来自不同回路的流体流以满足各个致动器的需求的能力可允许减少液压系统内所需的泵的数量和/或这些泵的大小和容量。这些减少可减少泵损失,提高整体效率,改进液压系统的体积,和/或降低液压系统的成本。
附图说明
51.图1是所公开的示例性机器的插图。
52.图2是所公开的示例性液压油缸的插图,所述液压油缸可用作图1的机器上的致动器。
53.图3是图2的所公开的示例性液压油缸的横截面视图。
54.图4是图3的液压油缸的标记4部分的放大图,其示出了在液压油缸的活塞杆的第一端处的活塞保持总成;并且
55.图5是图3的液压油缸的标记5部分的放大图,其示出了在液压油缸的活塞杆端处的头部密封构造。
具体实施方式
56.图1示出了具有协作以完成作业任务的多个系统和部件的示例性机器10。机器10可体现为执行与诸如采矿、建筑、农业、运输等行业或本领域已知的另一行业相关联的某种类型的操作的固定或移动机器。例如,机器10可为土方机械,诸如挖掘机(如图1所示)、推土机、前端装载机、反铲机、平地机、自卸卡车或任何其他土方机械或其他重型机械。机器10可包括被构造成移动作业工具14的机具系统12、用于推进机器10的驱动系统16、向机具系统12和驱动系统16提供动力的动力源18以及被定位成用于手动控制机具系统12、驱动系统16和/或动力源18的操作员站20。
57.机具系统12可包括由流体致动器作用以移动作业工具14的连杆结构。具体地,机具系统12可包括动臂22,所述动臂22通过一对相邻的双作用液压油缸26(仅在图1中示出)相对于作业表面24围绕水平轴线(未示出)竖直地枢转。机具系统12还可包括斗杆28,所述斗杆28通过单个双作用液压油缸32围绕水平轴线30竖直枢转。机具系统12还可包括单个双作用液压油缸34,所述双作用液压油缸34可操作地连接在斗杆28与作业工具14之间以使作业工具14围绕水平枢转轴线36竖直地枢转。在所公开的实施例中,液压油缸34在头端34a处连接到斗杆28的一部分,并且在相对杆端34b处通过动力连杆37连接到作业工具14。动臂22
可枢转地连接到机器10的主体38。主体38可枢转地连接到底盘39,并且可通过液压回转马达43围绕竖直轴线41移动。斗杆28可通过轴线30和轴线36将动臂22枢转地连接到作业工具14。可预期,如果需要,可以与上述相同或不同的方式将不同数量和/或构造的致动器替代地包括在机具系统12中。
58.许多不同的作业工具14可附接到单个机器10并且是操作员可控的。作业工具14可包括用于执行特定任务的任何装置,诸如例如铲斗、叉形装置、铲刀、铲子、松土器、翻斗车厢、扫帚、吹雪机、推进装置、切割装置、抓取装置或本领域已知的任何其他任务执行装置。尽管在图1的实施例中连接成相对于机器10的主体38在竖直方向上枢转并且在水平方向上摆动,但是作业工具14可替代地或另外旋转、滑动、打开和关闭或以本领域已知的任何其他方式移动。此外,尽管图1中的示例性实施例示出了被构造成用于致动包括动臂、斗杆和铲斗的挖掘机的结构元件的液压油缸,但是本领域普通技术人员将认识到,液压油缸的所公开的实施例可在执行机器所设计的特定任务时在不同机器上的其他结构元件之间互连以相对于机器的另一结构元件来致动机器的任何结构元件。
59.驱动系统16可包括提供动力以推进机器10的一个或多个牵引装置。在所公开的示例中,驱动系统16包括位于机器10的一侧的左履带40l和位于机器10的相对侧的右履带40r。左履带40l可由左行进马达42l驱动,而右履带40r可由右行进马达42r驱动。可预期,驱动系统16可替代地包括除履带以外的牵引装置,诸如轮子、皮带或其他已知的牵引装置。机器10可通过在左行进马达42l与右行进马达42r之间产生速度和/或旋转方向差来转向,而直线行进可通过从左行进马达42l和右行进马达42r产生基本相等的输出速度和旋转方向来行进。
60.动力源18可体现为发动机,诸如例如柴油发动机、汽油发动机、气体燃料动力发动机或本领域中已知的任何其他类型的燃烧发动机。可预期,动力源18可替代地体现为非燃烧动力源,诸如燃料电池、动力存储装置、系留马达或本领域中已知的另一动力源。动力源18可产生机械或电功率输出,然后可被转换为液压动力以使液压油缸26、32、34和左行进马达42l、右行进马达42r和回转马达43移动。
61.操作员站20可包括从机器操作员接收指示期望的机器操纵的输入的装置。具体地,操作员站20可包括位于操作员座椅(未示出)附近的一个或多个操作员接口装置46,例如操纵杆、方向盘或踏板。操作员接口装置46可通过产生指示期望的机器操纵的位移信号来发起机器10的移动,例如行进和/或工具移动。随着操作员移动接口装置46,操作员可在期望方向上以期望速度和/或用期望的力来操作对应的机器移动。
62.如图2和图3所示,液压油缸26、32、34可各自包括管322和被布置在管322内的活塞420,以形成第一腔室352和相对第二腔室354。第一腔室352可被认为是头端室,并且第二腔室354可被认为是液压油缸26、32、34的杆端室。管322可包括中心轴向延伸孔326,所述中心轴向延伸孔326限定在管322中,在管322的封闭远端342与管322的开口近端之间延伸。管322的中心轴向延伸孔326可部分地限定第一或头端室352和相对的第二或杆端室354,并且还可包括直径328,所述直径328基本上沿着管322内部的长度延伸,所述长度与管322和杆332的中心轴线同轴对准。杆332还可包括外径334,所述外径334与管322的中心轴线同轴地对准并且基本上沿着杆332外部的长度从活塞420和活塞保持总成430延伸到杆332的近端344。杆332的外径334与管322的中心轴向延伸孔326的直径328之间的径向空隙、偏移或间
隙可部分地限定第二或杆端室354。图3和图4所示的活塞420和活塞保持总成430的示例性实施例可设置在杆332的远端处。活塞420在杆332的远端处可保持在活塞保持总成430与衬套410之间,如图4所示。衬套410可抵靠在杆332的远端的直径减小肩部上。在替代实施方式中,活塞保持总成430可与杆332的远端螺纹接合或按压配合到杆332的远端上,并且衬套410可以被省去或者由弹性减震构件代替,所述弹性减震构件被构造成辅助减少振动并吸收由于活塞420在每个冲程的底部撞击管322的封闭远端342而产生的任何震动。活塞420还可包括多个环形密封件422,所述环形密封件422沿着活塞420的外围间距隔开并且随着杆332和活塞420由于供应给头端室352和杆端室354并从其中释放的液压流体的压力和/或流速的变化在管322内往复移动而在活塞420与管322的内圆周表面之间形成可滑动密封件。
63.在一些示例性实施方式中,阻尼总成440可设置在管322的封闭远端342处,在活塞杆332的冲程的底部处邻近活塞杆的远端,如图3和图4所示。另外,活塞保持总成430可用螺纹附接或以其他方式固定到活塞杆332的远端,抵靠在活塞420的一个轴向端上,并且在每个冲程的底部处被接纳在形成于管322的封闭远端342附近的径向向内延伸肋325中。随着活塞420和活塞保持总成430在每个冲程的底部接近管322的封闭远端342,捕集在头端室352中的液压流体可被迫通过肋325与活塞保持总成430的外周表面之间的间隙,从而促进阻尼效果,所述阻尼效果在活塞杆332和活塞420与管322的封闭远端342碰撞之前减慢了活塞杆和活塞的行进。阻尼总成440还可被构造有内部通路,所述内部通路被设计成在活塞420和杆332的每个冲程的底部限制从头端室352逸出的液压流体的流量。
64.阻尼总成440可从管322的封闭远端342的径向居中位置轴向地突出,并且可被构造成在杆的冲程的底部处接纳在形成于杆332的远端中的配合盲孔内。每当杆332、活塞保持总成430和活塞420接近管322的封闭远端342时,阻尼总成440可进入杆332的远端中的盲孔。在替代实施方式中,阻尼总成440可被保持在杆332的远端中的盲孔内,其中一个或多个环形密封件460插置在阻尼总成440的外围表面与杆332的远端中的盲孔的内围表面之间。阻尼总成440可被构造成在每个冲程的底部进入管322的封闭远端342中的径向居中轴向孔。轴向取向释放孔451也可形成在管322的封闭远端342中,平行于并偏离管322和杆332的中心轴线延伸,其中轴向取向释放孔451穿透到管322的封闭远端342并且与径向取向释放孔450相交,所述径向取向释放孔450在形成于管322的远端342中的减压室452和管322的外圆周外围之间延伸。随着活塞420、活塞保持总成430和阻尼总成440在冲程的底部处接近管322的封闭远端342(或者随着活塞420和活塞保持总成430接近从远端342突出的阻尼总成440),阻尼总成440可被构造成进入杆332的远端中的盲孔。头端室352中的流体可被强制通过轴向取向释放孔451,进入压力释放室452中并从径向取向释放孔450中排出。阻尼总成440还可包括中心轴向取向释放孔446以及多个径向延伸且轴向间隔的通道442和444,所述通道从中心轴向取向释放孔446穿透到阻尼总成440的外围。阻尼总成440中的中心轴向取向释放孔446和径向延伸通道442和444可被构造成辅助调节可能随着活塞420和活塞保持总成430在冲程的底部处接近管322的封闭远端342而从头端室352逸出的液压流体的量和流速,因此用于调节阻尼效果并且防止杆332、活塞420和活塞保持总成430强烈撞击管322的封闭远端342的底部。
65.头端室352和杆端室354可各自被选择性地供应加压流体并且排出加压流体以使活塞420在管322内移位,由此改变液压油缸26、32、34的有效长度并移动作业工具14(参见
图1),或者以其他方式移动机器10的一个结构部件,活塞杆332的近端344或管322的远端342中的一个相对于机器10的另一结构部件可枢转地连接到所述一个结构部件。流入和流出腔室352、354的流体的流速可与液压油缸26、32、34的平移速度有关,而腔室352、354之间的压力差可与由液压油缸26、32、34施加在机具系统12的相关联的连杆结构的力有关。
66.如图3和图5所示,杆332的近端344可穿过头部密封总成520,所述头部密封总成520在管322近端处用螺栓连接或以其他方式附接到杆端凸台324。头部密封总成520可包括沿着头部密封总成520的内圆周外围的多个轴向间隔的密封件522,所述密封件522被构造成与杆332的近端344的外围形成可滑动密封件。多个螺栓327可将头部密封总成520固定到杆端凸台324,其中头部密封总成520的一部分从管322的杆端凸台324至少部分地径向向内延伸并且被构造成随着杆332和活塞420相对于管322往复运动而径向地支撑杆332的近端344。杆332的近端344可包括直径为252的杆眼孔,所述杆眼孔延伸穿过与杆332的中心轴线正交的杆332并且被构造成接纳杆眼销以用于将杆332的近端344枢转地附接到机器10的第一结构元件,诸如杆眼销,所述杆眼销通过动力连杆37将液压油缸34的杆端34b枢轴连接到作业机具14,如图1所示。管322的远端342可类似地包括直径为242的耳轴帽孔,所述耳轴帽孔正交于杆332和管322的中心轴线延伸穿过管322的远端342并且被构造成接纳耳轴销,所述耳轴销将管322的远端342枢转地附接到机器10的第二结构元件,诸如耳轴销,所述耳轴销被构造成将液压油缸34的头端34a枢转地连接到斗杆28的一部分,如图1所示。
67.至少部分地基于与销可枢转地附接的机器10的结构元件的大小以及这些元件在操作期间承受的载荷和结构应力(诸如剪切应力、扭转应力、压缩应力以及在每个液压油缸的致动期间在载荷下将承受的抗拉应力)来确定延伸穿过杆332的近端344的杆眼孔的直径252以及因此被构造成用于将每个液压油缸的杆332枢转地连接到机器10的结构元件的杆眼销的直径以及延伸穿过管322的远端342的耳轴帽孔的直径242以及因此被构造成将每个液压油缸的管322枢转地连接到机器10的另一结构元件的耳轴销的直径。至少部分地基于特定机器的结构元件(诸如每个机器10的动臂22、斗杆28和作业机具14))的大小、运动范围、工作载荷以及结构相互关系来确定图2所示的每个液压油缸的销间尺寸132。类似地至少部分地基于每个机器10的结构元件的大小、运动范围、工作载荷以及结构相互关系来确定图3所示的每个液压油缸的冲程222。杆332和活塞420在图3中被示为完全缩回到管322中,其中通过从当活塞420在管322的封闭远端342处触底时的这种完全缩回位置行进到当活塞420接触用螺栓连接到管322的杆端凸台324的头部密封总成520时杆332的完全延伸位置的距离来确定冲程222。在一个实施例中,可至少部分地基于液压油缸26、32、34特有的系统压力来确定销间尺寸132、冲程222、杆眼孔的直径252和耳轴帽的直径242中的一个或多个以及每个液压油缸26、32、34的各种另外公开的尺寸、特性和特征,如本说明书中进一步说明的。
68.如同液压油缸26、32、34一样,左行进马达42l、右行进马达42r和摆动马达43可各自由液压差驱动。具体地,这些马达中的每一个可包括位于对应泵送机构(诸如叶轮、柱塞或一系列活塞(未示出))任一侧的第一和第二腔室(未示出)。当第一腔室填充有加压流体并且第二腔室排出流体时,可促使泵送机构在第一方向上移动或旋转。相反地,当第一腔室排出流体并且第二腔室填充有加压流体时,可促使泵送机构在相反方向上移动或旋转。流入和流出第一和第二腔室的流体的流速可确定相应马达的输出速度,而跨泵机构的压力差
可确定输出扭矩。如果需要,左行进马达42l、右行进马达42r和/或回转马达43的位移可为可变的并且可为偏心类型。在替代实施例中,这些马达可被设置有控制件和设备以在改变位移方向时支撑载荷,使得对于所供应的流体的给定流速和/或压力,每个马达的速度和/或扭矩输出可被独立调整。
69.机器10可包括液压系统(未示出),所述液压系统具有多个回路,所述回路驱动上述流体致动器(液压油缸)以移动作业工具14(参考图1)和机器10。具体地,液压系统尤其并且作为一个示例性实施方式可包括第一回路、第二回路、第三回路、第四回路和第五回路。在一个示例性实施方式中,第一回路可主要与液压油缸32和右行进马达42r相关联。第二回路可主要与回转马达43相关联。第三回路可主要与液压油缸34相关联。第四回路可主要与左行进马达42l和液压油缸26相关联。第五回路可主要与辅助致动器(例如直接与作业工具14相关联的辅助马达或油缸(未示出))相关联。可预期,如果需要,示例性液压系统中可包括回路的附加和/或不同构造,诸如例如与第一至第五回路中的每一个相关联的充油回路,和/或与液压油缸26或34相关联的独立回路。
70.在所公开的实施方式中,回路中的每一个可为类似的,并且包括促进使用和控制相关联的致动器的多个互连和协作的流体部件。例如,回路中的每一个可包括泵,所述泵经由通过左侧通道和右侧通道形成的闭合回路流体地连接到其相关联的致动器。具体地,回路中的每一个可包括公共的左泵通道、公共的右泵通道、用于每个致动器的左致动器通道和用于每个致动器的右致动器通道。在具有线性致动器(例如,液压油缸26、32或34)的回路中,左右致动器通道通常分别被称为头端通道和杆端通道。在每个回路内,对应泵可经由左右泵通道和致动器通道的组合连接到其相关联的致动器。
71.为了使旋转致动器(例如,左行进马达42l、右行进马达42r、摆动和/或辅助马达43)在第一方向上旋转,特定回路的左致动器通道可填充有通过泵加压的流体,而对应的右致动器通道可填充有流出旋转致动器的流体。为了反转旋转致动器的方向,右致动器通道可填充有通过泵加压的流体,而左致动器通道可填充有流出旋转致动器的流体。
72.为了使线性致动器(例如,液压油缸26、32或34)缩回,特定回路的右致动器通道可填充有通过泵加压的流体,而对应的左致动器通道可填充有线性致动器返回的流体。相反地,为了使旋转致动器延伸,左致动器通道可填充有通过泵66加压的流体,而右致动器通道可填充有流出线性致动器的流体。
73.每个泵可具有可变排量并且被控制为从其相关联的致动器抽出流体并以指定高压将流体在单个方向上排放回致动器。即,泵可包括冲程调整机构,例如斜盘,其位置尤其基于致动器的期望速度而进行液压机械地调整,由此改变泵的输出(例如,排出速率)。可将泵的排量从基本上没有流体从泵排出的零排量位置调整到流体以最大速率从泵排出到右泵通道的最大排量位置。泵可通过例如副轴、皮带或以其他合适的方式可驱动地连接到机器10的动力源18。替代地,泵可经由变矩器、齿轮箱、电路或以本领域中已知的任何其他方式间接地连接到动力源18。可预期,如果需要,不同回路的泵可串联(例如,经由同一轴)或并联(经由齿轮系)连接到动力源18。
74.被构造成向液压致动器提供加压液压流体的泵也可被选择性地充当马达。更具体地,当相关联的致动器以超限状态进行操作时,从致动器排出的流体的压力的升高可高于对应泵的输出压力。在这种情况下,通过泵被引导回的致动器流体的高压可用于在有或没
有动力源18辅助的情况下驱动泵旋转。在一些情况下,泵甚至能够将能量施加到动力源18,由此提高动力源18的效率和/或容量。
75.液压油缸26、32、34中的每一个可接收被加压到系统压力的液压流体。可结合针对上面安装有液压油缸的每个特定型号和/或类型的作业机器的连杆标准和掘起力来确定被供应到液压油缸26、32、34中的每一个的液压流体的系统压力。系统压力可在机器10的操作期间波动,其中压力尖峰可为连杆标准和使用机器的特定应用的函数。连杆标准可包括如本文所公开的每个相应的液压油缸26、32、34的各种特性、特征和尺寸,所述各种特性、特征和尺寸根据期望的安全系数进行修改,所述期望的安全系数被设计成适应系统压力尖峰以及在机器操作期间可能影响油缸的其他可变属性和工作特性。连杆标准可包括以下一个或多个:销间尺寸132、冲程222、杆眼孔直径252、耳轴帽孔直径242、管322的中心轴向延伸孔326的直径328以及杆332的外径334。这些特性、特征和尺寸可直接并且在功能性上与被供应到每个相应的液压油缸26、32、34的液压流体的系统压力相关,并且可基于所述系统压力来建立,这可导致改进其性能。在一个示例性实施方式中,管322的中心轴向延伸孔326的直径328和杆332的外径334可各自被设计成具有至少部分基于销间尺寸132、冲程222、杆眼孔直径252、耳轴帽孔直径242以及液压油缸26、32、34的系统压力的尺寸。具体地并且在一个示例中,管322的中心轴向延伸孔326的直径328和杆332的外径334可被设计成使得在头端室352和杆端室354中的一个或多个内的特定系统压力导致液压油缸的期望致动。液压油缸的期望致动可包括使杆332从管322延伸,使杆332缩回到管322中或将杆332保持在相对于管322的多个特定位置中的任一位置中。对根据本实用新型公开的各个实施例的每个液压油缸的上述讨论的尺寸和系统压力的选择可导致致动每个相应的液压油缸26、32、34,使得在杆眼孔直径252和耳轴帽孔直径242处的连接以特定速度和/或加速度将特定机器的相关联的结构元件中的每一个(诸如吊杆22、斗杆28和作业工具14)移动到期望位置,以实现机器10的综合性能改进和提高。
76.在根据本实用新型公开的液压油缸的以下示例性实施例中的一个(诸如适于用作相对于动臂22致动斗杆28的液压油缸32的液压油缸)中,在杆332、活塞保持总成430和活塞420在管322的封闭远端342处触底而完全缩回时,液压油缸的销间尺寸132可等于xxxx mm
±
xx mm。用于该示例性斗杆油缸的冲程222可等于xxxx mm
±
xx mm。杆眼孔直径252可等于xxx mm
±
xx mm。耳轴帽孔直径242可等于xxx mm
±
xx mm。该示例性斗杆油缸的管322的中心轴向延伸孔326的直径328可等于xxxx mm
±
xx mm,并且该示例性斗杆油缸的杆332的外径334可等于xxxx mm
±
xx mm。被供应到该示例性斗杆油缸的液压流体的系统压力可等于xxxx kpa
±
xx kpa。基于以下一个或多个来为特定机器确定所公开的尺寸范围:基于物理学的方程式、有限元分析、经验证据和其他数据计算分析,所述其他数据计算分析考虑了如下因素:诸如机器上的斗杆与动臂之间的运动学相互关系、相应的结构部件的运动范围、在机器10操作期间液压油缸将承受的载荷、期望的疲劳寿命、液压流体压力和机械安全系数。在一个示例中,该示例性斗杆油缸的本实施例的销间尺寸132、冲程222、杆眼孔直径252、耳轴帽孔直径242、管322中心轴向延伸孔326的直径328以及杆332的外径334的所公开范围中的一个或多个可直接并且在功能性上与用于致动系统压力为xxxx的斗杆28的当前公开的液压油缸32相关,并且可基于所述液压油缸来建立,根据本实用新型公开的实施例中的任何个者或多个,这可导致改进和提高综合性能。
77.在根据本实用新型公开的液压油缸的以下示例性实施例中的另一个(诸如适于用作用于致动动臂22的液压油缸26的液压油缸)中,在杆332、活塞保持总成430和活塞420在管322的封闭远端342处触底而完全缩回时,液压油缸的销间尺寸132可等于xxxx mm
±
xx mm。用于该示例性动臂油缸的冲程222可等于xxxx mm
±
xx mm。杆眼孔直径252可等于xxx mm
±
xx mm。耳轴帽孔直径242可等于xxx mm
±
xx mm。该示例性动臂油缸的管322的中心轴向延伸孔326的直径328可等于xxxx mm
±
xx mm,并且该示例性动臂油缸的杆332的外径334可等于xxxx mm
±
xx mm。该示例性动臂油缸的系统压力可等于xxxx kpa
±
xx kpa。基于以下一个或多个来为特定机器确定所公开的尺寸范围:基于物理学的方程式、有限元分析、经验证据和其他数据计算分析,所述其他数据计算分析考虑了如下因素:诸如机器的动臂与主体之间的运动学相互关系、相应的结构部件的运动范围、在机器10操作期间液压油缸将承受的载荷、期望的疲劳寿命、液压流体压力和机械安全系数。在一个示例中,该示例性动臂油缸的本实施例的销间尺寸132、冲程222、杆眼孔直径252、耳轴帽孔直径242、管322中心轴向延伸孔326的直径328以及杆332的外径334的所公开范围中的一个或多个可直接并且在功能性上与用于致动系统压力为xxxx的动臂22的当前公开的液压油缸26相关,并且可基于所述液压油缸来建立,根据本实用新型公开的实施例中的任何一个或多个,这可导致改进和提高综合性能。
78.在根据本实用新型公开的液压油缸的以下示例性实施例中的又另一个(诸如适于用作用于相对于斗杆28致动铲斗14的液压油缸34的液压油缸)中,在杆332、活塞保持总成430和活塞420在管322的封闭远端342处触底而完全缩回时,液压油缸的销间尺寸132可等于xxxx mm
±
xx mm。用于该示例性铲斗油缸的冲程222可等于xxxx mm
±
xx mm。杆眼孔直径252可等于xxx mm
±
xx mm。耳轴帽孔直径242可等于xxx mm
±
xx mm。该示例性铲斗油缸的管322的中心轴向延伸孔326的直径328可等于xxxx mm
±
xx mm,并且该示例性铲斗油缸的杆332的外径334可等于xxxx mm
±
xx mm。该示例性铲斗油缸的系统压力可等于xxxx kpa
±
xx kpa。基于以下一个或多个来为特定机器确定所公开的尺寸范围:基于物理学的方程式、有限元分析、经验证据和其他数据计算分析,所述其他数据计算分析考虑了如下因素:诸如机器10的斗杆、互连连杆和铲斗或其他作业工具之间的运动学相互关系、相应的结构部件的运动范围、在机器10操作期间液压油缸将承受的载荷、期望的疲劳寿命、液压流体压力和机械安全系数。在一个示例中,以及该示例性铲斗油缸的本实施例的销间尺寸132、冲程222、杆眼孔直径252、耳轴帽孔直径242、管322中心轴向延伸孔326的直径328杆332的外径334的所公开范围中的一个或多个可直接并且在功能性上与用于相对于系统压力为xxxx的斗杆28致动铲斗14的当前公开的液压油缸34相关,并且可基于所述液压油缸来建立,根据本实用新型公开的实施例中的任何一个或多个,这可导致改进综合性能。
79.上述xxxx代表四位数,上述xx代表两位数。568ll动臂液压油缸(568ll boom cylinder)在根据本实用新型公开的液压油缸的另一个示例性实施例(诸如适于用作用于致动动臂22的液压油缸26的液压油缸)中,在杆332、活塞保持总成430和活塞420在管322的封闭远端342处触底而完全缩回时,液压油缸的销间尺寸132可等于2000 mm
±
2.0 mm。用于该示例性动臂油缸的冲程222可等于1345 mm
±
2.0 mm。杆眼孔直径252可等于110 mm
±
0.5 mm。耳轴帽孔直径242可等于100 mm
±
0.5 mm。该示例性动臂油缸的管322的中心轴向延伸孔326的直径328可等于170 mm
±
0.5 mm,并且该示例性动臂油缸的杆332的外径334可等于
110 mm
±
0.5 mm。该示例性动臂油缸的系统流体压力可等于35,000 kpa
±
3500 kpa。基于以下一个或多个来为特定机器确定所公开的尺寸范围:基于物理学的方程式、有限元分析、经验证据和其他数据计算分析,所述其他数据计算分析考虑了如下因素:诸如机器的动臂与主体之间的运动学相互关系、相应的结构部件的运动范围、在机器10操作期间液压油缸将承受的载荷、期望的疲劳寿命、液压流体压力和机械安全系数。在一个示例中,该示例性动臂油缸的本实施例的销间尺寸132、冲程222、杆眼孔直径252、耳轴帽孔直径242、管322中心轴向延伸孔326的直径328以及杆332的外径334的所公开范围中的一个或多个可直接并且在功能性上与用于致动系统流体压力为35,000 kpa
±
3500 kpa的动臂22的当前公开的液压油缸26相关,并且可基于所述液压油缸来建立,根据本实用新型公开的实施例中的任何一个或多个,这可促使改进和提高综合性能。
80.568ll斗杆液压油缸(568ll stick cylinder)在根据本实用新型公开的液压油缸的一个示例性实施例(诸如适于用作用于相对于动臂22致动斗杆28的液压油缸32的液压油缸)中,在杆332、活塞保持总成430和活塞420在管322的封闭远端342处触底而完全缩回时,液压油缸的销间尺寸132可等于2411 mm
±
2.0 mm。用于该示例性斗杆油缸的冲程222可等于1661 mm
±
2.0 mm。杆眼孔直径252可等于100 mm
±
0.5 mm。耳轴帽孔直径242可等于100 mm
±
0.5 mm。该示例性斗杆油缸的管322的中心轴向延伸孔326的直径328可等于180 mm
±
0.5 mm,并且该示例性斗杆油缸的杆332的外径334可等于130 mm
±
0.5 mm。该示例性斗杆油缸的系统流体压力可等于35,000 kpa
±
3500 kpa。基于以下一个或多个来为特定机器10确定所公开的尺寸范围:基于物理学的方程式、有限元分析、经验证据和其他计算分析,所述其他计算分析考虑了如下因素:诸如机器10上的斗杆与动臂之间的运动学相互关系、相应的结构部件的运动范围、在机器10操作期间液压油缸将承受的载荷、期望的疲劳寿命、液压流体压力和机械安全系数。在一个示例中,该示例性斗杆油缸的本实施例的销间尺寸132、冲程222、杆眼孔直径252、耳轴帽孔直径242、管322中心轴向延伸孔326的直径328以及杆332的外径334的所公开范围中的一个或多个可直接并且在功能性上与用于致动系统流体压力为35,000 kpa
±
3500 kpa的斗杆28的当前公开的液压油缸32相关,并且可基于所述液压油缸来建立,根据本实用新型公开的实施例中的任何一个或多个,这可促使改进和提高综合性能。
81.m315ngh cr动臂
‑
va液压油缸动臂(m315ngh cr boom
‑
va cylinder boom)在根据本实用新型公开的液压油缸的另一个示例性实施例(诸如适于用作用于致动动臂22的液压油缸26的液压油缸)中,在杆332、活塞保持总成430和活塞420在管322的封闭远端342处触底而完全缩回时,液压油缸的销间尺寸132可等于1500 mm
±
2.0 mm。用于该示例性动臂油缸的冲程222可等于974 mm
±
2.0 mm。杆眼孔直径252可等于80 mm
±
0.5 mm。耳轴帽孔直径242可等于60 mm
±
0.5 mm。该示例性动臂油缸的管322的中心轴向延伸孔326的直径328可等于105 mm
±
0.5 mm,并且该示例性动臂油缸的杆332的外径334可等于75 mm
±
0.5 mm。该示例性动臂油缸的系统压力可等于37,500 kpa
±
3750 kpa。基于以下一个或多个来为特定机器确定所公开的尺寸范围:基于物理学的方程式、有限元分析、经验证据和其他数据计算分析,所述其他数据计算分析考虑了如下因素:诸如机器10的动臂与主体之间的运动学相互关系、相应的结构部件的运动范围、在机器10操作期间液压油缸将承受的载荷、期望的疲劳寿命、液压流体压力和机械安全系数。在一个示例中,该示例性动臂油缸的本实施例的销
间尺寸132、冲程222、杆眼孔直径252、耳轴帽孔直径242、管322中心轴向延伸孔326的直径328以及杆332的外径334的所公开范围中的一个或多个可直接并且在功能性上与用于致动系统压力为37,500 kpa
±
3750pa的动臂22的当前公开的液压油缸26相关,并且可基于所述液压油缸来建立,根据本实用新型公开的实施例中的任何一个或多个,这可促使改进和提高综合性能。
82.m314 ngh 动臂
‑
1pc fa液压油缸动臂(m314 ngh boom
‑
1pc fa cylinder boom)在根据本实用新型公开的液压油缸的另一个示例性实施例(诸如适于用作用于致动动臂22的液压油缸26的液压油缸)中,在杆332、活塞保持总成430和活塞420在管322的封闭远端342处触底而完全缩回时,液压油缸的销间尺寸132可等于1533 mm
±
2.0 mm。用于该示例性动臂油缸的冲程222可等于912 mm
±
2.0 mm。杆眼孔直径252可等于80 mm
±
0.5 mm。耳轴帽孔直径242可等于60 mm
±
0.5 mm。该示例性动臂油缸的管322的中心轴向延伸孔326的直径328可等于105 mm
±
0.5 mm,并且该示例性动臂油缸的杆332的外径334可等于75 mm
±
0.5 mm。该示例性动臂油缸的系统压力可等于37,500 kpa
±
3750 kpa。基于以下一个或多个来为特定机器确定所公开的尺寸范围:基于物理学的方程式、有限元分析、经验证据和其他计算分析,所述其他计算分析考虑了如下因素:诸如机器的动臂与主体之间的运动学相互关系、相应的结构部件的运动范围、在机器操作期间液压油缸将承受的载荷、期望的疲劳寿命、液压流体压力和机械安全系数。在一个示例中,该示例性动臂油缸的本实施例的销间尺寸132、冲程222、杆眼孔直径252、耳轴帽孔直径242、管322中心轴向延伸孔326的直径328以及杆332的外径334的所公开范围中的一个或多个可直接并且在功能性上与用于致动系统压力为37,500 kpa
±
3750 kpa的动臂22的当前公开的液压油缸26相关,并且可基于所述液压油缸来建立,根据本实用新型公开的实施例中的任何一个或多个,这可促使改进和提高综合性能。
83.m314 ngh 动臂
‑
1pc液压油缸动臂(m314 nghboom
‑
1pc cylinder boom)在根据本实用新型公开的液压油缸的另一个示例性实施例(诸如适于用作用于致动动臂22的液压油缸26的液压油缸)中,在杆332、活塞保持总成430和活塞420在管322的封闭远端342处触底而完全缩回时,液压油缸的销间尺寸132可等于1533 mm
±
2.0 mm。用于该示例性动臂油缸的冲程222可等于932 mm
±
2.0 mm。杆眼孔直径252可等于80 mm
±
0.5 mm。耳轴帽孔直径242可等于60 mm
±
0.5 mm。该示例性动臂油缸的管322的中心轴向延伸孔326的直径328可等于105 mm
±
0.5 mm,并且该示例性动臂油缸的杆332的外径334可等于75 mm
±
0.5 mm。该示例性动臂油缸的系统压力可等于37,500 kpa
±
3750 kpa。基于以下一个或多个来为特定机器确定所公开的尺寸范围:基于物理学的方程式、有限元分析、经验证据和其他计算分析,所述其他计算分析考虑了如下因素:诸如机器10的动臂与主体之间的运动学相互关系、相应的结构部件的运动范围、在机器10操作期间液压油缸将承受的载荷、期望的疲劳寿命、液压流体压力和机械安全系数。在一个示例中,该示例性动臂油缸的本实施例的销间尺寸132、冲程222、杆眼孔直径252、耳轴帽孔直径242、管322中心轴向延伸孔326的直径328以及杆332的外径334的所公开范围中的一个或多个可直接并且在功能性上与用于致动系统压力为37,500 kpa
±
3750 kpa的动臂22的当前公开的液压油缸26相关,并且可基于所述液压油缸来建立,根据本实用新型公开的实施例中的任何一个或多个,这可促使改进和提高综合性能。
84.m319ngh cr动臂
‑
va cr液压油缸动臂(m319ngh crboom
‑
va cr cylinder boom)在根据本实用新型公开的液压油缸的另一个示例性实施例(诸如适于用作用于致动动臂22的液压油缸26的液压油缸)中,在杆332、活塞保持总成430和活塞420在管322的封闭远端342处触底而完全缩回时,液压油缸的销间尺寸132可等于1520 mm
±
2.0 mm。用于该示例性动臂油缸的冲程222可等于954 mm
±
2.0 mm。杆眼孔直径252可等于90 mm
±
0.5 mm。耳轴帽孔直径242可等于70 mm
±
0.5 mm。该示例性动臂油缸的管322的中心轴向延伸孔326的直径328可等于120 mm
±
0.5 mm,并且该示例性动臂油缸的杆332的外径334可等于85 mm
±
0.5 mm。该示例性动臂油缸的系统压力可等于37,500 kpa
±
3750 kpa。基于以下一个或多个来为特定机器确定所公开的尺寸范围:基于物理学的方程式、有限元分析、经验证据和其他计算分析,所述其他计算分析考虑了如下因素:诸如机器的动臂与主体之间的运动学相互关系、相应的结构部件的运动范围、在机器10操作期间液压油缸将承受的载荷、期望的疲劳寿命、液压流体压力和机械安全系数。在一个示例中,该示例性动臂油缸的本实施例的销间尺寸132、冲程222、杆眼孔直径252、耳轴帽孔直径242、管322中心轴向延伸孔326的直径328以及杆332的外径334的所公开范围中的一个或多个可直接并且在功能性上与用于致动系统压力为37,500 kpa
±
3750 kpa的动臂22的当前公开的液压油缸26相关,并且可基于所述液压油缸来建立,根据本实用新型公开的实施例中的任何一个或多个,这可促使改进和提高性能。
85.m318ng动臂
‑
1pc液压油缸动臂(m318ngh boom
‑
1pc cylinder boom)在根据本实用新型公开的液压油缸的另一个示例性实施例(诸如适于用作用于致动动臂22的液压油缸26的液压油缸)中,在杆332、活塞保持总成430和活塞420在管322的封闭远端342处触底而完全缩回时,液压油缸的销间尺寸132可等于1770 mm
±
2.0 mm。用于该示例性动臂油缸的冲程222可等于893 mm
±
2.0 mm。杆眼孔直径252可等于80 mm
±
0.5 mm。耳轴帽孔直径242可等于70 mm
±
0.5 mm。该示例性动臂油缸的管322的中心轴向延伸孔326的直径328可等于120 mm
±
0.5 mm,并且该示例性动臂油缸的杆332的外径334可等于85 mm
±
0.5 mm。该示例性动臂油缸的系统压力可等于37,500 kpa
±
3750 kpa。基于以下一个或多个来为特定机器10确定所公开的尺寸范围:基于物理学的方程式、有限元分析、经验证据和其他计算分析,所述其他计算分析考虑了如下因素:诸如机器10的动臂与主体之间的运动学相互关系、相应的结构部件的运动范围、在机器10操作期间液压油缸将承受的载荷、期望的疲劳寿命、液压流体压力和机械安全系数。在一个示例中,该示例性动臂油缸的本实施例的销间尺寸132、冲程222、杆眼孔直径252、耳轴帽孔直径242、管322中心轴向延伸孔326的直径328以及杆332的外径334的所公开范围中的一个或多个可直接并且在功能性上与用于致动系统压力为37,500 kpa
±
3750 kpa的动臂22的当前公开的液压油缸26相关,并且可基于所述液压油缸来建立,根据本实用新型公开的实施例中的任何一个或多个,这可促使改进和提高综合性能。
86.m317ngh cr斗杆 液压油缸 斗杆(m317ngh cr stick cylinder stick)在根据本实用新型公开的液压油缸的一个示例性实施例(诸如适于用作用于相对于动臂22致动斗杆28的液压油缸32的液压油缸)中,在杆332、活塞保持总成430和活塞420在管322的封闭远端342处触底而完全缩回时,液压油缸的销间尺寸132可等于1652 mm
±
2.0 mm。用于该示例性斗杆油缸的冲程222可等于1147 mm
±
2.0 mm。杆眼孔直径252可等于70 mm
±
0.5 mm。耳轴
帽孔直径242可等于70 mm
±
0.5 mm。该示例性斗杆油缸的管322的中心轴向延伸孔326的直径328可等于115 mm
±
0.5 mm,并且该示例性斗杆油缸的杆332的外径334可等于80 mm
±
0.5 mm。该示例性斗杆油缸的系统压力可等于37,500 kpa
±
3750 kpa。基于以下一个或多个来为特定机器10确定所公开的尺寸范围:基于物理学的方程式、有限元分析、经验证据和其他计算分析,所述其他计算分析考虑了如下因素:诸如机器10上的斗杆与动臂之间的运动学相互关系、相应的结构部件的运动范围、在机器10操作期间液压油缸将承受的载荷、期望的疲劳寿命、液压流体压力和机械安全系数。在一个示例中,该示例性斗杆油缸的本实施例的销间尺寸132、冲程222、杆眼孔直径252、耳轴帽的耳轴帽孔直径242、管322中心轴向延伸孔326的直径328以及杆332的外径334的所公开范围中的一个或多个可直接并且在功能性上与用于致动系统压力为37,500 kpa
±
3750 kpa的斗杆28的当前公开的液压油缸32相关,并且可基于所述液压油缸来建立,根据本实用新型公开的实施例中的任何一个或多个,这可促使改进和提高综合性能。
87.m317ngh cr 动臂
‑
va cr 液压油缸动臂(m317ngh cr boom
‑
va cr cylinder boom)在根据本实用新型公开的液压油缸的另一个示例性实施例(诸如适于用作用于致动动臂22的液压油缸26的液压油缸)中,在杆332、活塞保持总成430和活塞420在管322的封闭远端342处触底而完全缩回时,液压油缸的销间尺寸132可等于1520 mm
±
2.0 mm。用于该示例性动臂油缸的冲程222可等于954 mm
±
0.5 mm。杆眼孔直径252可等于90 mm
±
0.5 mm。耳轴帽孔直径242可等于70 mm
±
0.5 mm。该示例性动臂油缸的管322的中心轴向延伸孔326的直径328可等于115 mm
±
0.5 mm,并且该示例性动臂油缸的杆332的外径334可等于80 mm
±
0.5 mm。该示例性动臂油缸的系统压力可等于37,500 kpa
±
3750 kpa。基于以下一个或多个来为特定机器10确定所公开的尺寸范围:基于物理学的方程式、有限元分析、经验证据和其他计算分析,所述其他计算分析考虑了如下因素:诸如机器10的动臂与主体之间的运动学相互关系、相应的结构部件的运动范围、在机器10操作期间液压油缸将承受的载荷、期望的疲劳寿命、液压流体压力和机械安全系数。在一个示例中,该示例性动臂油缸的本实施例的销间尺寸132、冲程222、杆眼孔直径252、耳轴帽孔直径242、管322中心轴向延伸孔326的直径328以及杆332的外径334的所公开范围中的一个或多个可直接并且在功能性上与用于致动系统压力为37,500 kpa
±
3750 kpa的动臂22的当前公开的液压油缸26相关,并且可基于所述液压油缸来建立,根据本实用新型公开的实施例中的任何一个或多个,这可促使改进和提高综合性能。
88.m316ngh动臂
‑
va 液压油缸动臂(m316ngh boom
‑
va cylinder boom)在根据本实用新型公开的液压油缸的另一个示例性实施例(诸如适于用作用于致动动臂22的液压油缸26的液压油缸)中,在杆332、活塞保持总成430和活塞420在管322的封闭远端342处触底而完全缩回时,液压油缸的销间尺寸132可等于1490 mm
±
2.0 mm。用于该示例性动臂油缸的冲程222可等于916 mm
±
2.0 mm。杆眼孔直径252可等于90 mm
±
0.5 mm。耳轴帽孔直径242可等于70 mm
±
0.5 mm。该示例性动臂油缸的管322的中心轴向延伸孔326的直径328可等于115 mm
±
2.0 mm,并且该示例性动臂油缸的杆332的外径334可等于80 mm
±
0.5 mm。该示例性动臂油缸的系统压力可等于37,500 kpa
±
3750 kpa。基于以下一个或多个来为特定机器10确定所公开的尺寸范围:基于物理学的方程式、有限元分析、经验证据和其他计算分析,所述其他计算分析考虑了如下因素:诸如机器10的动臂与主体之间的运动学相互关系、相
应的结构部件的运动范围、在机器10操作期间液压油缸将承受的载荷、期望的疲劳寿命、液压流体压力和机械安全系数。在一个示例中,该示例性动臂油缸的本实施例的销间尺寸132、冲程222、杆眼孔直径252、耳轴帽孔直径242、管322中心轴向延伸孔326的直径328以及杆332的外径334的所公开范围中的一个或多个可直接并且在功能性上与用于致动系统压力为37,500 kpa
±
3750 kpa的动臂22的当前公开的液压油缸26相关,并且可基于所述液压油缸来建立,根据本实用新型公开的实施例中的任何一个或多个,这可促使改进和提高性能。
89.m3022ngh/m3024ngh动臂
‑
mh液压油缸动臂(m3022ngh/m3024ngh boom
‑
mh cylinder boom)在根据本实用新型公开的液压油缸的另一个示例性实施例(诸如适于用作用于致动动臂22的液压油缸26的液压油缸)中,在杆332、活塞保持总成430和活塞420在管322的封闭远端342处触底而完全缩回时,液压油缸的销间尺寸132可等于1517 mm
±
2.0 mm。用于该示例性动臂油缸的冲程222可等于983 mm
±
2.0 mm。杆眼孔直径252可等于100 mm
±
0.5 mm。耳轴帽孔直径242可等于80 mm
±
0.5 mm。该示例性动臂油缸的管322的中心轴向延伸孔326的直径328可等于130 mm
±
0.5 mm,并且该示例性动臂油缸的杆332的外径334可等于90 mm
±
0.5 mm。该示例性动臂油缸的系统压力可等于37,500 kpa
±
3750 kpa。基于以下一个或多个来为特定机器10确定所公开的尺寸范围:基于物理学的方程式、有限元分析、经验证据和其他计算分析,所述其他计算分析考虑了如下因素:诸如机器10的动臂与主体之间的运动学相互关系、相应的结构部件的运动范围、在机器10操作期间液压油缸将承受的载荷、期望的疲劳寿命、液压流体压力和机械安全系数。在一个示例中,该示例性动臂油缸的本实施例的销间尺寸132、冲程222、杆眼孔直径252、耳轴帽孔直径242、管322中心轴向延伸孔326的直径328以及杆332的外径334的所公开范围中的一个或多个可直接并且在功能性上与用于致动系统压力为37,500 kpa
±
3750 kpa的动臂22的当前公开的液压油缸26相关,并且可基于所述液压油缸来建立,根据本实用新型公开的实施例中的任何一个或多个,这可促使改进和提高综合性能。
90.m3022ngh/m3024ngh斗杆mh液压油缸斗杆(m3022ngh/m3024ngh stick
‑
mh cylinder stick)在根据本实用新型公开的液压油缸的一个示例性实施例(诸如适于用作用于相对于动臂22致动斗杆28的液压油缸32的液压油缸)中,在杆332、活塞保持总成430和活塞420在管322的封闭远端342处触底而完全缩回时,液压油缸的销间尺寸132可等于1733 mm
±
2.0 mm。用于该示例性斗杆油缸的冲程222可等于1226 mm
±
2.0 mm。杆眼孔直径252可等于90 mm
±
0.5 mm。耳轴帽孔直径242可等于90 mm
±
0.5 mm。该示例性斗杆油缸的管322的中心轴向延伸孔326的直径328可等于110 mm
±
0.5 mm,并且该示例性斗杆油缸的杆332的外径334可等于80 mm
±
0.5 mm。该示例性斗杆油缸的系统压力可等于37,500 kpa
±
3750 kpa。基于以下一个或多个来为特定机器10确定所公开的尺寸范围:基于物理学的方程式、有限元分析、经验证据和其他计算分析,所述其他计算分析考虑了如下因素:诸如机器10上的斗杆与动臂之间的运动学相互关系、相应的结构部件的运动范围、在机器10操作期间液压油缸将承受的载荷、期望的疲劳寿命、液压流体压力和机械安全系数。在一个示例中,该示例性斗杆油缸的本实施例的销间尺寸132、冲程222、杆眼孔直径252、耳轴帽孔直径242、管322中心轴向延伸孔326的直径328以及杆332的外径334的所公开范围中的一个或多个可直接并且在功能性上与用于致动系统压力为37,500 kpa
±
3750 kpa的斗杆28的当前公开
的液压油缸32相关,并且可基于所述液压油缸来建立,根据本实用新型公开的实施例中的任何一个或多个,这可促使改进和提高综合性能。
91.m320ngh动臂
‑
va液压油缸动臂(m320ngh boom
‑
va cylinder boo)在根据本实用新型公开的液压油缸的另一个示例性实施例(诸如适于用作用于致动动臂22的液压油缸26的液压油缸)中,在杆332、活塞保持总成430和活塞420在管322的封闭远端342处触底而完全缩回时,液压油缸的销间尺寸132可等于1500 mm
±
2.0 mm。用于该示例性动臂油缸的冲程222可等于906 mm
±
2.0 mm。杆眼孔直径252可等于100 mm
±
0.5 mm。耳轴帽孔直径242可等于80 mm
±
0.5 mm。该示例性动臂油缸的管322的中心轴向延伸孔326的直径328可等于130 mm
±
0.5 mm,并且该示例性动臂油缸的杆332的外径334可等于90 mm
±
0.5 mm。该示例性动臂油缸的系统压力可等于37,500 kpa
±
3750 kpa。基于以下一个或多个来为特定机器10确定所公开的尺寸范围:基于物理学的方程式、有限元分析、经验证据和其他计算分析,所述其他计算分析考虑了如下因素:诸如机器10的动臂与主体之间的运动学相互关系、相应的结构部件的运动范围、在机器10操作期间液压油缸将承受的载荷、期望的疲劳寿命、液压流体压力和机械安全系数。在一个示例中,该示例性动臂油缸的本实施例的销间尺寸132、冲程222、杆眼孔直径252、耳轴帽孔直径242、管322中心轴向延伸孔326的直径328以及杆332的外径334的所公开范围中的一个或多个可直接并且在功能性上与用于致动系统压力为37,500 kpa
±
3750 kpa的动臂22的当前公开的液压油缸26相关,并且可基于所述液压油缸来建立,根据本实用新型公开的实施例中的任何一个或多个,这可促使改进和提高综合性能。
92.m320ngh 动臂
‑
1pc液压油缸动臂(m320ngh boom
‑
1pc cylinder boom)在根据本实用新型公开的液压油缸的另一个示例性实施例(诸如适于用作用于致动动臂22的液压油缸26的液压油缸)中,在杆332、活塞保持总成430和活塞420在管322的封闭远端342处触底而完全缩回时,液压油缸的销间尺寸132可等于1440 mm
±
2.0 mm。用于该示例性动臂油缸的冲程222可等于906 mm
±
2.0 mm。杆眼孔直径252可等于100 mm
±
0.5 mm。耳轴帽孔直径242可等于80 mm
±
0.5 mm。该示例性动臂油缸的管322的中心轴向延伸孔326的直径328可等于130 mm
±
0.5 mm,并且该示例性动臂油缸的杆332的外径334可等于90 mm
±
0.5 mm。该示例性动臂油缸的系统压力可等于37,500 kpa
±
3750 kpa。基于以下一个或多个来为特定机器10确定所公开的尺寸范围:基于物理学的方程式、有限元分析、经验证据和其他计算分析,所述其他计算分析考虑了如下因素:诸如机器10的动臂与主体之间的运动学相互关系、相应的结构部件的运动范围、在机器10操作期间液压油缸将承受的载荷、期望的疲劳寿命、液压流体压力和机械安全系数。在一个示例中,该示例性动臂油缸的本实施例的销间尺寸132、冲程222、杆眼孔直径252、耳轴帽孔直径242、管322中心轴向延伸孔326的直径328以及杆332的外径334的所公开范围中的一个或多个可直接并且在功能性上与用于致动系统压力为37,500 kpa
±
3750 kpa的动臂22的当前公开的液压油缸26相关,并且可基于所述液压油缸来建立,根据本实用新型公开的实施例中的任何一个或多个,这可促使改进和提高综合性能。
93.m320ngh hav 液压油缸(m320ngh hav cylinder)在根据本实用新型公开的液压油缸的另一个示例性实施例(诸如适于用作用于致动动臂22的液压油缸26的液压油缸)中,在杆332、活塞保持总成430和活塞420在管322的封闭远端342处触底而完全缩回时,液压油
缸的销间尺寸132可等于1270 mm
±
2.0 mm。用于该示例性动臂油缸的冲程222可等于731 mm
±
2.0 mm。杆眼孔直径252可等于110 mm
±
0.5 mm。耳轴帽孔直径242可等于100 mm
±
0.5 mm。该示例性动臂油缸的管322的中心轴向延伸孔326的直径328可等于160 mm
±
0.5 mm,并且该示例性动臂油缸的杆332的外径334可等于85 mm
±
0.5 mm。该示例性动臂油缸的系统压力可等于37,500 kpa
±
3750 kpa。基于以下一个或多个来为特定机器10确定所公开的尺寸范围:基于物理学的方程式、有限元分析、经验证据和其他计算分析,所述其他计算分析考虑了如下因素:诸如机器10的动臂与主体之间的运动学相互关系、相应的结构部件的运动范围、在机器10操作期间液压油缸将承受的载荷、期望的疲劳寿命、液压流体压力和机械安全系数。在一个示例中,该示例性动臂油缸的本实施例的销间尺寸132、冲程222、杆眼孔直径252、耳轴帽孔直径242、管322中心轴向延伸孔326的直径328以及杆332的外径334的所公开范围中的一个或多个可直接并且在功能性上与用于致动系统压力为37,500 kpa
±
3750 kpa的动臂22的当前公开的液压油缸26相关,并且可基于所述液压油缸来建立,根据本实用新型公开的实施例中的任何一个或多个,这可导致改进性能。
94.m320ngh 斗杆
‑
va 液压油缸(m320ngh stick
‑
va cylinder)在根据实用新型本实用新型公开的液压油缸的另一个示例性实施例(诸如适于用作用于致动斗杆28的液压油缸32的液压油缸)中,在杆332、活塞保持总成430和活塞420在管322的封闭远端342处触底而完全缩回时,液压油缸的销间尺寸132可等于1775 mm
±
2.0 mm。用于该示例性斗杆油缸的冲程222可等于1205 mm
±
2.0 mm。杆眼孔直径252可等于80 mm
±
0.5 mm。耳轴帽孔直径242可等于80 mm
±
0.5 mm。该示例性斗杆油缸的管322的中心轴向延伸孔326的直径328可等于130 mm
±
0.5 mm,并且该示例性斗杆油缸的杆332的外径334可等于90 mm
±
0.5 mm。该示例性斗杆油缸的系统压力可等于37,500 kpa
±
3750 kpa。基于以下一个或多个来为特定机器10确定所公开的尺寸范围:基于物理学的方程式、有限元分析、经验证据和其他计算分析,所述其他计算分析考虑了如下因素:诸如机器10的斗杆与动臂主体之间的运动学相互关系、相应的结构部件的运动范围、在机器10操作期间液压油缸将承受的载荷、期望的疲劳寿命、液压流体压力和机械安全系数。在一个示例中,该示例性斗杆油缸的本实施例的销间尺寸132、冲程222、杆眼孔直径252、耳轴帽孔直径242、管322中心轴向延伸孔326的直径328以及杆332的外径334的所公开范围中的一个或多个可直接并且在功能性上与用于致动系统压力为37,500 kpa
±
3750 kpa的斗杆28的当前公开的液压油缸32相关,并且可基于所述液压油缸来建立,根据本实用新型公开的实施例中的任何一个或多个,这可导致改进性能。
95.m320ngh 斗杆
‑
1pc 液压油缸(m320ngh stick
‑
1pc cylinder)在根据本实用新型公开的液压油缸的另一个示例性实施例(诸如适于用作用于致动斗杆28的液压油缸32的液压油缸)中,在杆332、活塞保持总成430和活塞420在管322的封闭远端342处触底而完全缩回时,液压油缸的销间尺寸132可等于1775 mm
±
2.0 mm。用于该示例性动臂油缸的冲程222可等于1205 mm
±
2.0 mm。杆眼孔直径252可等于80 mm
±
0.5 mm。耳轴帽孔直径242可等于80 mm
±
0.5 mm。该示例性斗杆油缸的管322的中心轴向延伸孔326的直径328可等于140 mm
±
0.5 mm,并且该示例性斗杆油缸的杆332的外径334可等于100 mm
±
0.5 mm。该示例性斗杆油缸的系统压力可等于37,500 kpa
±
3750 kpa。基于以下一个或多个来为特定机器10确定所公开的尺寸范围:基于物理学的方程式、有限元分析、经验证据和其他计算分析,所述其他计算分析考虑了如下因素:诸如机器10的动臂与主体之间的运动学相互关系、相应的
结构部件的运动范围、在机器10操作期间液压油缸将承受的载荷、期望的疲劳寿命、液压流体压力和机械安全系数。在一个示例中,该示例性斗杆油缸的本实施例的销间尺寸132、冲程222、杆眼孔直径252、耳轴帽孔直径242、管322中心轴向延伸孔326的直径328以及杆332的外径334的所公开范围中的一个或多个可直接并且在功能性上与用于致动系统压力为37,500 kpa
±
3750 kpa的斗杆28的当前公开的液压油缸32相关,并且可基于所述液压油缸来建立,根据本实用新型公开的实施例中的任何一个或多个,这可促使改进和提高综合性能。
96.m320ngh 铲斗液压油缸(m320ngh bucket cylinder)在根据本实用新型公开的液压油缸的另一个示例性实施例(诸如适于用作用于致动铲斗14的液压油缸34的液压油缸)中,在杆332、活塞保持总成430和活塞420在管322的封闭远端342处触底而完全缩回时,液压油缸的销间尺寸132可等于1624 mm
±
2.0 mm。用于该示例性铲斗油缸的冲程222可等于1077 mm
±
2.0 mm。杆眼孔直径252可等于80 mm
±
0.5 mm。耳轴帽孔直径242可等于70 mm
±
0.5 mm。该示例性动臂油缸的管322的中心轴向延伸孔326的直径328可等于110 mm
±
0.5 mm,并且该示例性动臂油缸的杆332的外径334可等于80 mm
±
0.5 mm。该示例性铲斗油缸的系统压力可等于37,500 kpa
±
3750 kpa。基于以下一个或多个来为特定机器10确定所公开的尺寸范围:基于物理学的方程式、有限元分析、经验证据和其他计算分析,所述其他计算分析考虑了如下因素:诸如机器10的铲斗与斗杆之间的运动学相互关系、相应的结构部件的运动范围、在机器10操作期间液压油缸将承受的载荷、期望的疲劳寿命、液压流体压力和机械安全系数。在一个示例中,该示例性铲斗油缸的本实施例的销间尺寸132、冲程222、杆眼孔直径252、耳轴帽孔直径242、管322中心轴向延伸孔326的直径328以及杆332的外径334的所公开范围中的一个或多个可直接并且在功能性上与用于相对于系统压力为37,500 kpa
±
3750 kpa的致动铲斗14的当前公开的液压油缸34相关,并且可基于所述液压油缸来建立,根据本实用新型公开的实施例中的任何一个或多个,这可促使改进和提高综合性能。
97.mh3026ngh 动臂
‑
mh 液压油缸(mh3026ngh boom
‑
mh cylinder)在根据本实用新型公开的液压油缸的另一个示例性实施例(诸如适于用作用于致动动臂22的液压油缸26的液压油缸)中,在杆332、活塞保持总成430和活塞420在管322的封闭远端342处触底而完全缩回时,液压油缸的销间尺寸132可等于1529 mm
±
2.0 mm。用于该示例性动臂油缸的冲程222可等于967 mm
±
2.0 mm。杆眼孔直径252可等于110 mm
±
0.5 mm。耳轴帽孔直径242可等于80 mm
±
0.5 mm。该示例性动臂油缸的管322的中心轴向延伸孔326的直径328可等于140 mm
±
0.5 mm,并且该示例性动臂油缸的杆332的外径334可等于100 mm
±
0.5 mm。该示例性动臂油缸的系统压力可等于37,500 kpa
±
3750 kpa。基于以下一个或多个来为特定机器10确定所公开的尺寸范围:基于物理学的方程式、有限元分析、经验证据和其他计算分析,所述其他计算分析考虑了如下因素:诸如机器10的动臂与主体之间的运动学相互关系、相应的结构部件的运动范围、在机器10操作期间液压油缸将承受的载荷、期望的疲劳寿命、液压流体压力和机械安全系数。在一个示例中,该示例性动臂油缸的本实施例的销间尺寸132、冲程222、杆眼孔直径252、耳轴帽孔直径242、管322中心轴向延伸孔326的直径328以及杆332的外径334的所公开范围中的一个或多个可直接并且在功能性上与用于致动系统压力为37,500 kpa
±
3750 kpa的动臂22的当前公开的液压油缸26相关,并且可基于所述液压油缸来建立,根据本实用新型公开的实施例中的任何一个或多个,这可促使改进和提高综合
性能。
98.m3026ngh斗杆
‑
mh 液压油缸(m3026ngh stick
‑
mh cylinder)在根据本实用新型公开的液压油缸的另一个示例性实施例(诸如适于用作用于致动斗杆28的液压油缸32的液压油缸)中,在杆332、活塞保持总成430和活塞420在管322的封闭远端342处触底而完全缩回时,液压油缸的销间尺寸132可等于1834 mm
±
2.0 mm。用于该示例性斗杆油缸的冲程222可等于1305 mm
±
2.0 mm。杆眼孔直径252可等于90 mm
±
0.5 mm。耳轴帽孔直径242可等于90 mm
±
0.5 mm。该示例性斗杆油缸的管322的中心轴向延伸孔326的直径328可等于120 mm
±
0.5 mm,并且该示例性斗杆油缸的杆332的外径334可等于85 mm
±
0.5 mm。该示例性斗杆油缸的系统压力可等于37,500 kpa
±
3750 kpa。基于以下一个或多个来为特定机器10确定所公开的尺寸范围:基于物理学的方程式、有限元分析、经验证据和其他计算分析,所述其他计算分析考虑了如下因素:诸如机器10的斗杆与动臂之间的运动学相互关系、相应的结构部件的运动范围、在机器10操作期间液压油缸将承受的载荷、期望的疲劳寿命、液压流体压力和机械安全系数。在一个示例中,该示例性斗杆油缸的本实施例的销间尺寸132、冲程222、杆眼孔直径252、耳轴帽孔直径242、管322中心轴向延伸孔326的直径328以及杆332的外径334的所公开范围中的一个或多个可直接并且在功能性上与用于致动系统压力为37,500 kpa
±
3750 kpa的斗杆28的当前公开的液压油缸32相关,并且可基于所述液压油缸来建立,根据本文公开的实施例中的任何一个或多个,这可促使改进和提高综合性能。
99.m322ngh 动臂
‑
va液压油缸(m322ngh boom
‑
va cylinder)在根据本实用新型公开的液压油缸的另一个示例性实施例(诸如适于用作用于致动动臂22的液压油缸26的液压油缸)中,在杆332、活塞保持总成430和活塞420在管322的封闭远端342处触底而完全缩回时,液压油缸的销间尺寸132可等于1479 mm
±
2.0 mm。用于该示例性动臂油缸的冲程222可等于862 mm
±
2.0 mm。杆眼孔直径252可等于110 mm
±
0.5 mm。耳轴帽孔直径242可等于80 mm
±
0.5 mm。该示例性动臂油缸的管322的中心轴向延伸孔326的直径328可等于140 mm
±
0.5 mm,并且该示例性动臂油缸的杆332的外径334可等于100 mm
±
0.5 mm。该示例性动臂油缸的系统压力可等于37,500 kpa
±
3750 kpa。基于以下一个或多个来为特定机器10确定所公开的尺寸范围:基于物理学的方程式、有限元分析、经验证据和其他计算分析,所述其他计算分析考虑了如下因素:诸如机器10的动臂与主体之间的运动学相互关系、相应的结构部件的运动范围、在机器10操作期间液压油缸将承受的载荷、期望的疲劳寿命、液压流体压力和机械安全系数。在一个示例中,该示例性动臂油缸的本实施例的销间尺寸132、冲程222、杆眼孔直径252、耳轴帽孔直径242、管322中心轴向延伸孔326的直径328以及杆332的外径334的所公开范围中的一个或多个可直接并且在功能性上与用于致动系统压力为37,500 kpa
±
3750 kpa的动臂22的当前公开的液压油缸26相关,并且可基于所述液压油缸来建立,根据本实用新型公开的实施例中的任何一个或多个,这可促使改进和提高综合性能。
100.m322ngh hav 液压油缸(m322ngh hav cylinder)在根据本实用新型公开的液压油缸的另一个示例性实施例(诸如适于用作用于致动动臂22的液压油缸26的液压油缸)中,在杆332、活塞保持总成430和活塞420在管322的封闭远端342处触底而完全缩回时,液压油缸的销间尺寸132可等于1255 mm
±
2.0 mm。用于该示例性动臂油缸的冲程222可等于709 mm
±
2.0 mm。杆眼孔直径252可等于130 mm
±
0.5 mm。耳轴帽孔直径242可等于120 mm
±
0.5 mm。该示例性动臂油缸的管322的中心轴向延伸孔326的直径328可等于170 mm
±
0.5 mm,并
且该示例性动臂油缸的杆332的外径334可等于100 mm
±
0.5 mm。该示例性动臂油缸的系统压力可等于37,500 kpa
±
3750 kpa。基于以下一个或多个来为特定机器确定所公开的尺寸范围:基于物理学的方程式、有限元分析、经验证据和其他计算分析,所述其他计算分析考虑了如下因素:诸如机器的动臂与主体之间的运动学相互关系、相应的结构部件的运动范围、在机器操作期间液压油缸将承受的载荷、期望的疲劳寿命、液压流体压力和机械安全系数。在一个示例中,该示例性动臂油缸的本实施例的销间尺寸132、冲程222、杆眼孔直径252、耳轴帽孔直径242、管322中心轴向延伸孔326的直径328以及杆332的外径334的所公开范围中的一个或多个可直接并且在功能性上与用于致动系统压力为37,500 kpa
±
3750 kpa的动臂22的当前公开的液压油缸26相关,并且可基于所述液压油缸来建立,根据本文公开的实施例中的任何一个或多个,这可导致改进性能。
101.m322ngh斗杆液压油缸(m322nghstick cylinder)在根据本实用新型公开的液压油缸的另一个示例性实施例(诸如适于用作用于致动斗杆28的液压油缸32的液压油缸)中,在杆332、活塞保持总成430和活塞420在管322的封闭远端342处触底而完全缩回时,液压油缸的销间尺寸132可等于1968 mm
±
2.0 mm。用于该示例性斗杆油缸的冲程222可等于1408 mm
±
2.0 mm。杆眼孔直径252可等于80 mm
±
0.5 mm。耳轴帽孔直径242可等于80 mm
±
0.5 mm。该示例性斗杆油缸的管322的中心轴向延伸孔326的直径328可等于140 mm
±
0.5 mm,并且该示例性斗杆油缸的杆332的外径334可等于100 mm
±
0.5 mm。该示例性斗杆油缸的系统压力可等于37,500 kpa
±
3750 kpa。基于以下一个或多个来为特定机器10确定所公开的尺寸范围:基于物理学的方程式、有限元分析、经验证据和其他计算分析,所述其他计算分析考虑了如下因素:诸如机器10的斗杆与动臂之间的运动学相互关系、相应的结构部件的运动范围、在机器10操作期间液压油缸将承受的载荷、期望的疲劳寿命、液压流体压力和机械安全系数。在一个示例中,该示例性斗杆油缸的本实施例的销间尺寸132、冲程222、杆眼孔直径252、耳轴帽孔直径242、管322中心轴向延伸孔326的直径328以及杆332的外径334的所公开范围中的一个或多个可直接并且在功能性上与用于致动系统压力为37,500 kpa
±
3750 kpa的斗杆28的当前公开的液压油缸32相关,并且可基于所述液压油缸来建立,根据本实用新型公开的实施例中的任何一个或多个,这可促使改进和提高综合性能。
102.m322ngh铲斗液压油缸(m322ngh bucket cylinder)在根据本实用新型公开的液压油缸的另一个示例性实施例(诸如适于用作用于致动铲斗14的液压油缸34的液压油缸)中,在杆332、活塞保持总成430和活塞420在管322的封闭远端342处触底而完全缩回时,液压油缸的销间尺寸132可等于1684 mm
±
2.0 mm。用于该示例性铲斗油缸的冲程222可等于1104 mm
±
2.0 mm。杆眼孔直径252可等于90 mm
±
0.5 mm。耳轴帽孔直径242可等于70 mm
±
0.5 mm。该示例性动臂油缸的管322的中心轴向延伸孔326的直径328可等于120 mm
±
0.5 mm,并且该示例性动臂油缸的杆332的外径334可等于85 mm
±
0.5 mm。该示例性铲斗油缸的系统压力可等于37,500 kpa
±
3750 kpa。基于以下一个或多个来为特定机器10确定所公开的尺寸范围:基于物理学的方程式、有限元分析、经验证据和其他计算分析,所述其他计算分析考虑了如下因素:诸如机器10的铲斗与斗杆之间的运动学相互关系、相应的结构部件的运动范围、在机器10操作期间液压油缸将承受的载荷、期望的疲劳寿命、液压流体压力和机械安全系数。在一个示例中,该示例性铲斗油缸的本实施例的销间尺寸132、冲程222、杆眼孔直径252、耳轴帽孔直径242、管322中心轴向延伸孔326的直径328以及杆332的外径334
的所公开范围中的一个或多个可直接并且在功能性上与用于相对于系统压力为37,500 kpa
±
3750 kpa致动铲斗14的当前公开的液压油缸34相关,并且可基于所述液压油缸来建立,根据本实用新型公开的实施例中的任何一个或多个,这可促使改进和提高综合性能。
103.312 gx 斗杆液压油缸(312 gx stick cylinder)在根据本实用新型公开的液压油缸的另一个示例性实施例(诸如适于用作用于致动斗杆28的液压油缸32的液压油缸)中,在杆332、活塞保持总成430和活塞420在管322的封闭远端342处触底而完全缩回时,液压油缸的销间尺寸132可等于1676 mm
±
2.0 mm。用于该示例性斗杆油缸的冲程222可等于1194 mm
±
2.0 mm。杆眼孔直径252可等于60 mm
±
0.5 mm。耳轴帽孔直径242可等于60 mm
±
0.5 mm。该示例性斗杆油缸的管322的中心轴向延伸孔326的直径328可等于105 mm
±
0.5 mm,并且该示例性斗杆油缸的杆332的外径334可等于75 mm
±
0.5 mm。该示例性斗杆油缸的系统压力可等于35,000 kpa
±
3500 kpa。基于以下一个或多个来为特定机器10确定所公开的尺寸范围:基于物理学的方程式、有限元分析、经验证据和其他计算分析,所述其他计算分析考虑了如下因素:诸如机器10的斗杆与动臂之间的运动学相互关系、相应的结构部件的运动范围、在机器10操作期间液压油缸将承受的载荷、期望的疲劳寿命、液压流体压力和机械安全系数。在一个示例中,该示例性斗杆油缸的本实施例的销间尺寸132、冲程222、杆眼孔直径252、耳轴帽孔直径242、管322中心轴向延伸孔326的直径328以及杆332的外径334的所公开范围中的一个或多个可直接并且在功能性上与用于致动系统压力为35,000 kpa
±
3500 kpa的斗杆28的当前公开的液压油缸32相关,并且可基于所述液压油缸来建立,根据本实用新型公开的实施例中的任何一个或多个,这可促使改进和提高综合性能。
104.312 gx动臂液压油缸(312 gxboom cylinder)在根据本实用新型公开的液压油缸的另一个示例性实施例(诸如适于用作用于致动动臂22的液压油缸26的液压油缸)中,在杆332、活塞保持总成430和活塞420在管322的封闭远端342处触底而完全缩回时,液压油缸的销间尺寸132可等于1492 mm
±
2.0 mm。用于该示例性动臂油缸的冲程222可等于1002 mm
±
2.0 mm。杆眼孔直径252可等于80 mm
±
0.5 mm。耳轴帽孔直径242可等于60 mm
±
0.5 mm。该示例性动臂油缸的管322的中心轴向延伸孔326的直径328可等于95 mm
±
0.5 mm,并且该示例性动臂油缸的杆332的外径334可等于65 mm
±
0.5 mm。该示例性动臂油缸的系统压力可等于35,000 kpa
±
3750 kpa。基于以下一个或多个来为特定机器10确定所公开的尺寸范围:基于物理学的方程式、有限元分析、经验证据和其他计算分析,所述其他计算分析考虑了如下因素:诸如机器的动臂与主体之间的运动学相互关系、相应的结构部件的运动范围、在机器10操作期间液压油缸将承受的载荷、期望的疲劳寿命、液压流体压力和机械安全系数。在一个示例中,该示例性动臂油缸的本实施例的销间尺寸132、冲程222、杆眼孔直径252、耳轴帽孔直径242、管322中心轴向延伸孔326的直径328以及杆332的外径334的所公开范围中的一个或多个可直接并且在功能性上与用于致动系统压力为35,000 kpa
±
3500 kpa的动臂22的当前公开的液压油缸26相关,并且可基于所述液压油缸来建立,根据本实用新型公开的实施例中的任何一个或多个,这可促使改进和提高综合性能。
105.312 gx铲斗液压油缸(312 gxbucket cylinder)在根据本实用新型公开的液压油缸的另一个示例性实施例(诸如适于用作用于致动铲斗14的液压油缸34的液压油缸)中,在杆332、活塞保持总成430和活塞420在管322的封闭远端342处触底而完全缩回时,液压油缸的销间尺寸132可等于1392 mm
±
2.0 mm。用于该示例性铲斗油缸的冲程222可等于939 mm
±
2.0 mm。杆眼孔直径252可等于70 mm
±
0.5 mm。耳轴帽孔直径242可等于60 mm
±
0.5 mm。该示例性动臂油缸的管322的中心轴向延伸孔326的直径328可等于90 mm
±
0.5 mm,并且该示例性动臂油缸的杆332的外径334可等于65 mm
±
0.5 mm。该示例性铲斗油缸的系统压力可等于35,000 kpa
±
3500 kpa。基于以下一个或多个来为特定机器10确定所公开的尺寸范围:基于物理学的方程式、有限元分析、经验证据和其他计算分析,所述其他计算分析考虑了如下因素:诸如机器10的铲斗与斗杆之间的运动学相互关系、相应的结构部件的运动范围、在机器10操作期间液压油缸将承受的载荷、期望的疲劳寿命、液压流体压力和机械安全系数。在一个示例中,该示例性铲斗油缸的本实施例的销间尺寸132、冲程222、杆眼孔直径252、耳轴帽孔直径242、管322中心轴向延伸孔326的直径328以及杆332的外径334的所公开范围中的一个或多个可直接并且在功能性上与用于相对于系统压力为35,000 kpa
±
3500 kpa致动铲斗14的当前公开的液压油缸34相关,并且可基于所述液压油缸来建立,根据本实用新型公开的实施例中的任何一个或多个,这可促使改进和提高综合性能。
106.313 gx 斗杆液压油缸(313 gx stick cylinder)在根据本实用新型公开的液压油缸的另一个示例性实施例(诸如适于用作用于致动斗杆28的液压油缸32的液压油缸)中,在杆332、活塞保持总成430和活塞420在管322的封闭远端342处触底而完全缩回时,液压油缸的销间尺寸132可等于1675 mm
±
2.0 mm。用于该示例性斗杆油缸的冲程222可等于1197 mm
±
2.0 mm。杆眼孔直径252可等于60 mm
±
0.5 mm。耳轴帽孔直径242可等于60 mm
±
0.5 mm。该示例性斗杆油缸的管322的中心轴向延伸孔326的直径328可等于115 mm
±
0.5 mm,并且该示例性斗杆油缸的杆332的外径334可等于80 mm
±
0.5 mm。该示例性斗杆油缸的系统压力可等于35,000 kpa
±
3500 kpa。基于以下一个或多个来为特定机器10确定所公开的尺寸范围:基于物理学的方程式、有限元分析、经验证据和其他计算分析,所述其他计算分析考虑了如下因素:诸如机器10的斗杆与动臂之间的运动学相互关系、相应的结构部件的运动范围、在机器10操作期间液压油缸将承受的载荷、期望的疲劳寿命、液压流体压力和机械安全系数。在一个示例中,该示例性斗杆油缸的本实施例的销间尺寸132、冲程222、杆眼孔直径252、耳轴帽孔直径242、管322中心轴向延伸孔326的直径328以及杆332的外径334的所公开范围中的一个或多个可直接并且在功能性上与用于致动系统压力为35,000 kpa
±
3500 kpa的斗杆28的当前公开的液压油缸32相关,并且可基于所述液压油缸来建立,根据本实用新型公开的实施例中的任何一个或多个,这可促使改进和提高综合性能。
107.313 gx/316 gx 动臂液压油缸(313 gx/316 gx boom cylinder)在根据本实用新型公开的液压油缸的另一个示例性实施例(诸如适于用作用于致动动臂22的液压油缸26的液压油缸)中,在杆332、活塞保持总成430和活塞420在管322的封闭远端342处触底而完全缩回时,液压油缸的销间尺寸132可等于1505 mm
±
2.0 mm。用于该示例性动臂油缸的冲程222可等于1015 mm
±
2.0 mm。杆眼孔直径252可等于80 mm
±
0.5 mm。耳轴帽孔直径242可等于60 mm
±
0.5 mm。该示例性动臂油缸的管322的中心轴向延伸孔326的直径328可等于105 mm
±
0.5 mm,并且该示例性动臂油缸的杆332的外径334可等于75 mm
±
0.5 mm。该示例性动臂油缸的系统压力可等于35,000 kpa
±
3750 kpa。基于以下一个或多个来为特定机器10确定所公开的尺寸范围:基于物理学的方程式、有限元分析、经验证据和其他计算分析,所述其他计算分析考虑了如下因素:诸如机器10的动臂与主体之间的运动学相互关系、相应的结构部件的运动范围、在机器10操作期间液压油缸将承受的载荷、期望的疲劳寿命、液压流
体压力和机械安全系数。在一个示例中,该示例性动臂油缸的本实施例的销间尺寸132、冲程222、杆眼孔直径252、耳轴帽孔直径242、管322中心轴向延伸孔326的直径328以及杆332的外径334的所公开范围中的一个或多个可直接并且在功能性上与用于致动系统压力为35,000 kpa
±
3500 kpa的动臂22的当前公开的液压油缸26相关,并且可基于所述液压油缸来建立,根据本实用新型公开的实施例中的任何一个或多个,这可促使改进和提高综合性能。
108.316 gx 斗杆液压油缸(316 gx stick cylinder)在根据本实用新型公开的液压油缸的另一个示例性实施例(诸如适于用作用于致动斗杆28的液压油缸32的液压油缸)中,在杆332、活塞保持总成430和活塞420在管322的封闭远端342处触底而完全缩回时,液压油缸的销间尺寸132可等于1675 mm
±
2.0 mm。用于该示例性斗杆油缸的冲程222可等于1197 mm
±
2.0 mm。杆眼孔直径252可等于60 mm
±
0.5 mm。耳轴帽孔直径242可等于60 mm
±
0.5 mm。该示例性斗杆油缸的管322的中心轴向延伸孔326的直径328可等于120 mm
±
0.5 mm,并且该示例性斗杆油缸的杆332的外径334可等于85 mm
±
0.5 mm。该示例性斗杆油缸的系统压力可等于35,000 kpa
±
3500 kpa。基于以下一个或多个来为特定机器10确定所公开的尺寸范围:基于物理学的方程式、有限元分析、经验证据和其他计算分析,所述其他计算分析考虑了如下因素:诸如机器10的斗杆与动臂之间的运动学相互关系、相应的结构部件的运动范围、在机器10操作期间液压油缸将承受的载荷、期望的疲劳寿命、液压流体压力和机械安全系数。在一个示例中,该示例性斗杆油缸的本实施例的销间尺寸132、冲程222、杆眼孔直径252、耳轴帽孔直径242、管322中心轴向延伸孔326的直径328以及杆332的外径334的所公开范围中的一个或多个可直接并且在功能性上与用于致动系统压力为35,000 kpa
±
3500 kpa的斗杆28的当前公开的液压油缸32相关,并且可基于所述液压油缸来建立,根据本实用新型公开的实施例中的任何一个或多个,这可促使改进和提高综合性能。
109.316 gx 铲斗液压油缸(316 gx bucket cylinder)在根据本实用新型的液压油缸的另一个示例性实施例(诸如适于用作用于致动铲斗14的液压油缸34的液压油缸)中,在杆332、活塞保持总成430和活塞420在管322的封闭远端342处触底而完全缩回时,液压油缸的销间尺寸132可等于1392 mm
±
2.0 mm。用于该示例性铲斗油缸的冲程222可等于939 mm
±
2.0 mm。杆眼孔直径252可等于80 mm
±
0.5 mm。耳轴帽孔直径242可等于60 mm
±
0.5 mm。该示例性动臂油缸的管322的中心轴向延伸孔326的直径328可等于100 mm
±
0.5 mm,并且该示例性动臂油缸的杆332的外径334可等于70 mm
±
0.5 mm。该示例性铲斗油缸的系统压力可等于35,000 kpa
±
3500 kpa。基于以下一个或多个来为特定机器10确定所公开的尺寸范围:基于物理学的方程式、有限元分析、经验证据和其他计算分析,所述其他计算分析考虑了如下因素:诸如机器10的铲斗与斗杆之间的运动学相互关系、相应的结构部件的运动范围、在机器10操作期间液压油缸将承受的载荷、期望的疲劳寿命、液压流体压力和机械安全系数。在一个示例中,该示例性铲斗油缸的本实施例的销间尺寸132、冲程222、杆眼孔直径252、耳轴帽孔直径242、管322中心轴向延伸孔326的直径328以及杆332的外径334的所公开范围中的一个或多个可直接并且在功能性上与用于相对于系统压力为35,000 kpa
±
3500 kpa致动铲斗14的当前公开的液压油缸34相关,并且可基于所述液压油缸来建立,根据本实用新型公开的实施例中的任何一个或多个,这可促使改进和提高综合性能。
110.315 ngh pob 斗杆液压油缸(315 ngh pob stick cylinder)在根据本实用新型
的液压油缸的另一个示例性实施例(诸如适于用作用于致动斗杆28的液压油缸32的液压油缸)中,在杆332、活塞保持总成430和活塞420在管322的封闭远端342处触底而完全缩回时,液压油缸的销间尺寸132可等于332 mm
±
2.0 mm。用于该示例性斗杆油缸的冲程222可等于948 mm
±
2.0 mm。杆眼孔直径252可等于70 mm
±
0.5 mm。耳轴帽孔直径242可等于80 mm
±
0.5 mm(x 2个位置)。该示例性斗杆油缸的管322的中心轴向延伸孔326的直径328可等于115 mm
±
0.5 mm,并且该示例性斗杆油缸的杆332的外径334可等于80 mm
±
0.5 mm。该示例性斗杆油缸的系统压力可等于35,000 kpa
±
3500 kpa。基于以下一个或多个来为特定机器10确定所公开的尺寸范围:基于物理学的方程式、有限元分析、经验证据和其他计算分析,所述其他计算分析考虑了如下因素:诸如机器10的斗杆与动臂之间的运动学相互关系、相应的结构部件的运动范围、在机器10操作期间液压油缸将承受的载荷、期望的疲劳寿命、液压流体压力和机械安全系数。在一个示例中,该示例性斗杆油缸的本实施例的销间尺寸132、冲程222、杆眼孔直径252、耳轴帽孔直径242、管322中心轴向延伸孔326的直径328以及杆332的外径334的所公开范围中的一个或多个可直接并且在功能性上与用于致动系统压力为35,000 kpa
±
3500 kpa的斗杆28的当前公开的液压油缸32相关,并且可基于所述液压油缸来建立,根据本实用新型公开的实施例中的任何一个或多个,这可促使改进和提高综合性能。
111.315ngh pob 动臂液压油缸(315ngh pob boom cylinder)在根据本实用新型公开的液压油缸的另一个示例性实施例(诸如适于用作用于致动动臂22的液压油缸26的液压油缸)中,在杆332、活塞保持总成430和活塞420在管322的封闭远端342处触底而完全缩回时,液压油缸的销间尺寸132可等于1469 mm
±
2.0 mm。用于该示例性动臂油缸的冲程222可等于1014mm
±
2.0 mm。杆眼孔直径252可等于80 mm
±
0.5 mm。耳轴帽孔直径242可等于60 mm
±
0.5 mm。该示例性动臂油缸的管322的中心轴向延伸孔326的直径328可等于105 mm
±
0.5 mm,并且该示例性动臂油缸的杆332的外径334可等于75 mm
±
0.5 mm。该示例性动臂油缸的系统压力可等于35,000 kpa
±
3750 kpa。基于以下一个或多个来为特定机器10确定所公开的尺寸范围:基于物理学的方程式、有限元分析、经验证据和其他计算分析,所述其他计算分析考虑了如下因素:诸如机器10的动臂与主体之间的运动学相互关系、相应的结构部件的运动范围、在机器10操作期间液压油缸将承受的载荷、期望的疲劳寿命、液压流体压力和机械安全系数。在一个示例中,该示例性动臂油缸的本实施例的销间尺寸132、冲程222、杆眼孔直径252、耳轴帽孔直径242、管322中心轴向延伸孔326的直径328以及杆332的外径334的所公开范围中的一个或多个可直接并且在功能性上与用于致动系统压力为35,000 kpa
±
3500 kpa的动臂22的当前公开的液压油缸26相关,并且可基于所述液压油缸来建立,根据本实用新型公开的实施例中的任何一个或多个,这可促使改进和提高综合性能。
112.315ngh pob 液压油缸(315ngh pob cylinder)在根据本实用新型的液压油缸的另一个示例性实施例(诸如适于用作用于致动铲斗14的液压油缸34的液压油缸)中,在杆332、活塞保持总成430和活塞420在管322的封闭远端342处触底而完全缩回时,液压油缸的销间尺寸132可等于900 mm
±
2.0 mm。用于该示例性铲斗油缸的冲程222可等于404 mm
±
2.0 mm。杆眼孔直径252可等于80 mm
±
0.5 mm。耳轴帽孔直径242可等于80 mm
±
0.5 mm。该示例性动臂油缸的管322的中心轴向延伸孔326的直径328可等于120 mm
±
0.5 mm,并且该示例性动臂油缸的杆332的外径334可等于70 mm
±
0.5 mm。该示例性铲斗油缸的系统压力
可等于35,000 kpa
±
3500 kpa。基于以下一个或多个来为特定机器10确定所公开的尺寸范围:基于物理学的方程式、有限元分析、经验证据和其他计算分析,所述其他计算分析考虑了如下因素:诸如机器10的铲斗与斗杆之间的运动学相互关系、相应的结构部件的运动范围、在机器操作期间液压油缸将承受的载荷、期望的疲劳寿命、液压流体压力和机械安全系数。在一个示例中,该示例性铲斗油缸的本实施例的销间尺寸132、冲程222、杆眼孔直径252、耳轴帽孔直径242、管322中心轴向延伸孔326的直径328以及杆332的外径334的所公开范围中的一个或多个可直接并且在功能性上与用于相对于系统压力为35,000 kpa
±
3500 kpa致动铲斗14的当前公开的液压油缸34相关,并且可基于所述液压油缸来建立,根据本实用新型公开的实施例中的任何一个或多个,这可促使改进和提高综合性能。
113.313 ngh 斗杆液压油缸(313 ngh stick cylinder)在根据本实用新型公开的液压油缸的另一个示例性实施例(诸如适于用作用于致动斗杆28的液压油缸32的液压油缸)中,在杆332、活塞保持总成430和活塞420在管322的封闭远端342处触底而完全缩回时,液压油缸的销间尺寸132可等于1637 mm
±
2.0 mm。用于该示例性斗杆油缸的冲程222可等于1147 mm
±
2.0 mm。杆眼孔直径252可等于70 mm
±
0.5 mm。耳轴帽孔直径242可等于70 mm
±
0.5 mm。该示例性斗杆油缸的管322的中心轴向延伸孔326的直径328可等于115 mm
±
0.5 mm,并且该示例性斗杆油缸的杆332的外径334可等于80 mm
±
0.5 mm。该示例性斗杆油缸的系统压力可等于35,000 kpa
±
3500 kpa。基于以下一个或多个来为特定机器10确定所公开的尺寸范围:基于物理学的方程式、有限元分析、经验证据和其他计算分析,所述其他计算分析考虑了如下因素:诸如机器10的斗杆与动臂之间的运动学相互关系、相应的结构部件的运动范围、在机器10操作期间液压油缸将承受的载荷、期望的疲劳寿命、液压流体压力和机械安全系数。在一个示例中,该示例性斗杆油缸的本实施例的销间尺寸132、冲程222、杆眼孔直径252、耳轴帽孔直径242、管322中心轴向延伸孔326的直径328以及杆332的外径334的所公开范围中的一个或多个可直接并且在功能性上与用于致动系统压力为35,000 kpa
±
3500 kpa的斗杆28的当前公开的液压油缸32相关,并且可基于所述液压油缸来建立,根据本实用新型公开的实施例中的任何一个或多个,这可促使改进和提高综合性能。
114.313 ngh 动臂液压油缸(313 ngh boom cylinder)在根据本实用新型公开的液压油缸的另一个示例性实施例(诸如适于用作用于致动动臂22的液压油缸26的液压油缸)中,在杆332、活塞保持总成430和活塞420在管322的封闭远端342处触底而完全缩回时,液压油缸的销间尺寸132可等于1544 mm
±
2.0 mm。用于该示例性动臂油缸的冲程222可等于1026 mm
±
2.0 mm。杆眼孔直径252可等于80 mm
±
0.5 mm。耳轴帽孔直径242可等于60 mm
±
0.5 mm。该示例性动臂油缸的管322的中心轴向延伸孔326的直径328可等于105 mm
±
0.5 mm,并且该示例性动臂油缸的杆332的外径334可等于75 mm
±
0.5 mm。该示例性动臂油缸的系统压力可等于35,000 kpa
±
3750 kpa。基于以下一个或多个来为特定机器10确定所公开的尺寸范围:基于物理学的方程式、有限元分析、经验证据和其他计算分析,所述其他计算分析考虑了如下因素:诸如机器10的动臂与主体之间的运动学相互关系、相应的结构部件的运动范围、在机器10操作期间液压油缸将承受的载荷、期望的疲劳寿命、液压流体压力和机械安全系数。在一个示例中,该示例性动臂油缸的本实施例的销间尺寸132、冲程222、杆眼孔直径252、耳轴帽孔直径242、管322中心轴向延伸孔326的直径328以及杆332的外径334的所公开范围中的一个或多个可直接并且在功能性上与用于致动系统压力为35,000 kpa
±
mm
±
2.0 mm。杆眼孔直径252可等于80 mm
±
0.5 mm。耳轴帽孔直径242可等于60 mm
±
0.5 mm。该示例性动臂油缸的管322的中心轴向延伸孔326的直径328可等于105 mm
±
0.5 mm,并且该示例性动臂油缸的杆332的外径334可等于75 mm
±
0.5 mm。该示例性动臂油缸的系统压力可等于35,000 kpa
±
3750 kpa。基于以下一个或多个来为特定机器10确定所公开的尺寸范围:基于物理学的方程式、有限元分析、经验证据和其他计算分析,所述其他计算分析考虑了如下因素:诸如机器10的动臂与主体之间的运动学相互关系、相应的结构部件的运动范围、在机器10操作期间液压油缸将承受的载荷、期望的疲劳寿命、液压流体压力和机械安全系数。在一个示例中,该示例性动臂油缸的本实施例的销间尺寸132、冲程222、杆眼孔直径252、耳轴帽孔直径242、管322中心轴向延伸孔326的直径328以及杆332的外径334的所公开范围中的一个或多个可直接并且在功能性上与用于致动系统压力为35,000 kpa
±
3500 kpa的动臂22的当前公开的液压油缸26相关,并且可基于所述液压油缸来建立,根据本实用新型公开的实施例中的任何一个或多个,这可促使改进和提高综合性能。
118.317 ngh斗杆液压油缸(317 ngh stick cylinder)在根据本实用新型公开的液压油缸的另一个示例性实施例(诸如适于用作用于致动斗杆28的液压油缸32的液压油缸)中,在杆332、活塞保持总成430和活塞420在管322的封闭远端342处触底而完全缩回时,液压油缸的销间尺寸132可等于1827 mm
±
2.0 mm。用于该示例性斗杆油缸的冲程222可等于1331 mm
±
2.0 mm。杆眼孔直径252可等于70 mm
±
0.5 mm。耳轴帽孔直径242可等于70 mm
±
0.5 mm。该示例性斗杆油缸的管322的中心轴向延伸孔326的直径328可等于120 mm
±
0.5 mm,并且该示例性斗杆油缸的杆332的外径334可等于85 mm
±
0.5 mm。该示例性斗杆油缸的系统压力可等于35,000 kpa
±
3500 kpa。基于以下一个或多个来为特定机器10确定所公开的尺寸范围:基于物理学的方程式、有限元分析、经验证据和其他计算分析,所述其他计算分析考虑了如下因素:诸如机器10的斗杆与动臂之间的运动学相互关系、相应的结构部件的运动范围、在机器10操作期间液压油缸将承受的载荷、期望的疲劳寿命、液压流体压力和机械安全系数。在一个示例中,该示例性斗杆油缸的本实施例的销间尺寸132、冲程222、杆眼孔直径252、耳轴帽孔直径242、管322中心轴向延伸孔326的直径328以及杆332的外径334的所公开范围中的一个或多个可直接并且在功能性上与用于致动系统压力为35,000 kpa
±
3500 kpa的斗杆28的当前公开的液压油缸32相关,并且可基于所述液压油缸来建立,根据本实用新型公开的实施例中的任何一个或多个,这可促使改进和提高综合性能。
119.317 ngh 动臂液压油缸(317 ngh boom cylinder)在根据本实用新型公开的液压油缸的另一个示例性实施例(诸如适于用作用于致动动臂22的液压油缸26的液压油缸)中,在杆332、活塞保持总成430和活塞420在管322的封闭远端342处触底而完全缩回时,液压油缸的销间尺寸132可等于1693 mm
±
2.0 mm。用于该示例性动臂油缸的冲程222可等于1193 mm
±
2.0 mm。杆眼孔直径252可等于80 mm
±
0.5 mm。耳轴帽孔直径242可等于70 mm
±
0.5 mm。该示例性动臂油缸的管322的中心轴向延伸孔326的直径328可等于110 mm
±
0.5 mm,并且该示例性动臂油缸的杆332的外径334可等于80 mm
±
0.5 mm。该示例性动臂油缸的系统压力可等于35,000 kpa
±
3750 kpa。基于以下一个或多个来为特定机器10确定所公开的尺寸范围:基于物理学的方程式、有限元分析、经验证据和其他计算分析,所述其他计算分析考虑了如下因素:诸如机器10的动臂与主体之间的运动学相互关系、相应的结构部件的运动范围、在机器10操作期间液压油缸将承受的载荷、期望的疲劳寿命、液压流体压力和机械
安全系数。在一个示例中,该示例性动臂油缸的本实施例的销间尺寸132、冲程222、杆眼孔直径252、耳轴帽孔直径242、管322中心轴向延伸孔326的直径328以及杆332的外径334的所公开范围中的一个或多个可直接并且在功能性上与用于致动系统压力为35,000 kpa
±
3500 kpa的动臂22的当前公开的液压油缸26相关,并且可基于所述液压油缸来建立,根据本实用新型公开的实施例中的任何一个或多个,这可促使改进和提高综合性能。
120.317 ngh 铲斗液压油缸(317 ngh bucket cylinder)在根据本公开的液压油缸的另一个示例性实施例(诸如适于用作用于致动铲斗14的液压油缸34的液压油缸)中,在杆332、活塞保持总成430和活塞420在管322的封闭远端342处触底而完全缩回时,液压油缸的销间尺寸132可等于1559 mm
±
2.0 mm。用于该示例性铲斗油缸的冲程222可等于1039 mm
±
2.0 mm。杆眼孔直径252可等于80 mm
±
0.5 mm。耳轴帽孔直径242可等于70 mm
±
0.5 mm。该示例性动臂油缸的管322的中心轴向延伸孔326的直径328可等于105 mm
±
0.5 mm,并且该示例性动臂油缸的杆332的外径334可等于75 mm
±
0.5 mm。该示例性铲斗油缸的系统压力可等于35,000 kpa
±
3500 kpa。基于以下一个或多个来为特定机器10确定所公开的尺寸范围:基于物理学的方程式、有限元分析、经验证据和其他计算分析,所述其他计算分析考虑了如下因素:诸如机器10的铲斗与斗杆之间的运动学相互关系、相应的结构部件的运动范围、在机器10操作期间液压油缸将承受的载荷、期望的疲劳寿命、液压流体压力和机械安全系数。在一个示例中,该示例性铲斗油缸的本实施例的销间尺寸132、冲程222、杆眼孔直径252、耳轴帽孔直径242、管322中心轴向延伸孔326的直径328以及杆332的外径334的所公开范围中的一个或多个可直接并且在功能性上与用于相对于系统压力为35,000 kpa
±
3500 kpa致动铲斗14的当前公开的液压油缸34相关,并且可基于所述液压油缸来建立,根据本实用新型公开的实施例中的任何一个或多个,这可促使改进和提高综合性能。
121.317 ngh vab 动臂液压油缸(317 ngh vab boom cylinder)在根据本实用新型公开的液压油缸的另一个示例性实施例(诸如适于用作用于致动可变角动臂22的液压油缸26的液压油缸)中,在杆332、活塞保持总成430和活塞420在管322的封闭远端342处触底而完全缩回时,液压油缸的销间尺寸132可等于1310 mm
±
2.0 mm。用于该示例性动臂油缸的冲程222可等于865 mm
±
2.0 mm。杆眼孔直径252可等于70 mm
±
0.5 mm。耳轴帽孔直径242可等于70 mm
±
0.5 mm。该示例性可变角动臂油缸的管322的中心轴向延伸孔326的直径328可等于140 mm
±
0.5 mm,并且该示例性可变角动臂油缸的杆332的外径334可等于85 mm
±
0.5 mm。该示例性动臂油缸的系统压力可等于35,000 kpa
±
3500 kpa。基于以下一个或多个来为特定机器10确定所公开的尺寸范围:基于物理学的方程式、有限元分析、经验证据和其他计算分析,所述其他计算分析考虑了如下因素:诸如机器10的动臂与主体之间的运动学相互关系、相应的结构部件的运动范围、在机器10操作期间液压油缸将承受的载荷、期望的疲劳寿命、液压流体压力和机械安全系数。在一个示例中,该示例性可变角动臂油缸的本实施例的销间尺寸132、冲程222、杆眼孔直径252、耳轴帽孔直径242、管322中心轴向延伸孔326的直径328以及杆332的外径334的所公开范围中的一个或多个可直接并且在功能性上与用于致动系统压力为35,000 kpa
±
3500 kpa的动臂22的当前公开的液压油缸26相关,并且可基于所述液压油缸来建立,根据本实用新型公开的实施例中的任何一个或多个,这可促使改进和提高综合性能。
122.320gx斗杆液压油缸(320gxstick cylinder)在根据本实用新型公开的液压油缸
的另一个示例性实施例(诸如适于用作用于致动斗杆28的液压油缸32的液压油缸)中,在杆332、活塞保持总成430和活塞420在管322的封闭远端342处触底而完全缩回时,液压油缸的销间尺寸132可等于2064 mm
±
2.0 mm。用于该示例性斗杆油缸的冲程222可等于1504 mm
±
2.0 mm。杆眼孔直径252可等于80 mm
±
0.5 mm。耳轴帽孔直径242可等于80 mm
±
0.5 mm。该示例性斗杆油缸的管322的中心轴向延伸孔326的直径328可等于135 mm
±
0.5 mm,并且该示例性斗杆油缸的杆332的外径334可等于95 mm
±
0.5 mm。该示例性斗杆油缸的系统压力可等于35,000 kpa
±
3500 kpa。基于以下一个或多个来为特定机器10确定所公开的尺寸范围:基于物理学的方程式、有限元分析、经验证据和其他计算分析,所述其他计算分析考虑了如下因素:诸如机器10的斗杆与动臂之间的运动学相互关系、相应的结构部件的运动范围、在机器10操作期间液压油缸将承受的载荷、期望的疲劳寿命、液压流体压力和机械安全系数。在一个示例中,该示例性斗杆油缸的本实施例的销间尺寸132、冲程222、杆眼孔直径252、耳轴帽孔直径242、管322中心轴向延伸孔326的直径328以及杆332的外径334的所公开范围中的一个或多个可直接并且在功能性上与用于致动系统压力为35,000 kpa
±
3500 kpa的斗杆28的当前公开的液压油缸32相关,并且可基于所述液压油缸来建立,根据本文公开的实施例中的任何一个或多个,这可促使改进和提高综合性能。
123.320gx 动臂液压油缸(320gx boom cylinder)在根据本实用新型公开的液压油缸的另一个示例性实施例(诸如适于用作用于致动动臂22的液压油缸26的液压油缸)中,在杆332、活塞保持总成430和活塞420在管322的封闭远端342处触底而完全缩回时,液压油缸的销间尺寸132可等于1760 mm
±
2.0 mm。用于该示例性动臂油缸的冲程222可等于1260 mm
±
2.0 mm。杆眼孔直径252可等于80 mm
±
0.5 mm。耳轴帽孔直径242可等于80 mm
±
0.5 mm。该示例性动臂油缸的管322的中心轴向延伸孔326的直径328可等于120 mm
±
0.5 mm,并且该示例性动臂油缸的杆332的外径334可等于85 mm
±
0.5 mm。该示例性动臂油缸的系统压力可等于35,000 kpa
±
3750 kpa。基于以下一个或多个来为特定机器10确定所公开的尺寸范围:基于物理学的方程式、有限元分析、经验证据和其他计算分析,所述其他计算分析考虑了如下因素:诸如机器10的动臂与主体之间的运动学相互关系、相应的结构部件的运动范围、在机器10操作期间液压油缸将承受的载荷、期望的疲劳寿命、液压流体压力和机械安全系数。在一个示例中,该示例性动臂油缸的本实施例的销间尺寸132、冲程222、杆眼孔直径252、耳轴帽孔直径242、管322中心轴向延伸孔326的直径328以及杆332的外径334的所公开范围中的一个或多个可直接并且在功能性上与用于致动系统压力为35,000 kpa
±
3500 kpa的动臂22的当前公开的液压油缸26相关,并且可基于所述液压油缸来建立,根据本实用新型公开的实施例中的任何一个或多个,这可促使改进和提高综合性能。
124.320gx 铲斗液压油缸(320gx bucket cylinder)在根据本实用新型公开的液压油缸的另一个示例性实施例(诸如适于用作用于致动铲斗14的液压油缸34的液压油缸)中,在杆332、活塞保持总成430和活塞420在管322的封闭远端342处触底而完全缩回时,液压油缸的销间尺寸132可等于1684 mm
±
2.0 mm。用于该示例性铲斗油缸的冲程222可等于1104 mm
±
2.0 mm。杆眼孔直径252可等于80 mm
±
0.5 mm。耳轴帽孔直径242可等于70 mm
±
0.5 mm。该示例性动臂油缸的管322的中心轴向延伸孔326的直径328可等于115 mm
±
0.5 mm,并且该示例性动臂油缸的杆332的外径334可等于80 mm
±
0.5 mm。该示例性铲斗油缸的系统压力可等于35,000 kpa
±
3500 kpa。基于以下一个或多个来为特定机器10确定所公开的尺寸
范围:基于物理学的方程式、有限元分析、经验证据和其他计算分析,所述其他计算分析考虑了如下因素:诸如机器10的铲斗与斗杆之间的运动学相互关系、相应的结构部件的运动范围、在机器10操作期间液压油缸将承受的载荷、期望的疲劳寿命、液压流体压力和机械安全系数。在一个示例中,该示例性铲斗油缸的本实施例的销间尺寸132、冲程222、杆眼孔直径252、耳轴帽孔直径242、管322中心轴向延伸孔326的直径328以及杆332的外径334的所公开范围中的一个或多个可直接并且在功能性上与用于相对于系统压力为35,000 kpa
±
3500 kpa致动铲斗14的当前公开的液压油缸34相关,并且可基于所述液压油缸来建立,根据本实用新型公开的实施例中的任何一个或多个,这可促使改进和提高综合性能。
125.323gx 斗杆液压油缸(323gx stick cylinder)在根据本实用新型公开的液压油缸的另一个示例性实施例(诸如适于用作用于致动斗杆28的液压油缸32的液压油缸)中,在杆332、活塞保持总成430和活塞420在管322的封闭远端342处触底而完全缩回时,液压油缸的销间尺寸132可等于2064 mm
±
2.0 mm。用于该示例性斗杆油缸的冲程222可等于1504 mm
±
2.0 mm。杆眼孔直径252可等于80 mm
±
0.5 mm。耳轴帽孔直径242可等于80 mm
±
0.5 mm。该示例性斗杆油缸的管322的中心轴向延伸孔326的直径328可等于140 mm
±
0.5 mm,并且该示例性斗杆油缸的杆332的外径334可等于100 mm
±
0.5 mm。该示例性斗杆油缸的系统压力可等于35,000 kpa
±
3500 kpa。基于以下一个或多个来为特定机器10确定所公开的尺寸范围:基于物理学的方程式、有限元分析、经验证据和其他计算分析,所述其他计算分析考虑了如下因素:诸如机器10的斗杆与动臂之间的运动学相互关系、相应的结构部件的运动范围、在机器10操作期间液压油缸将承受的载荷、期望的疲劳寿命、液压流体压力和机械安全系数。在一个示例中,该示例性斗杆油缸的本实施例的销间尺寸132、冲程222、杆眼孔直径252、耳轴帽孔直径242、管322中心轴向延伸孔326的直径328以及杆332的外径334的所公开范围中的一个或多个可直接并且在功能性上与用于致动系统压力为35,000 kpa
±
3500 kpa的斗杆28的当前公开的液压油缸32相关,并且可基于所述液压油缸来建立,根据本实用新型公开的实施例中的任何一个或多个,这可促使改进和提高综合性能。
126.323gx 动臂液压油缸(323gx boom cylinder)在根据本实用新型公开的液压油缸的另一个示例性实施例(诸如适于用作用于致动动臂22的液压油缸26的液压油缸)中,在杆332、活塞保持总成430和活塞420在管322的封闭远端342处触底而完全缩回时,液压油缸的销间尺寸132可等于1760 mm
±
2.0 mm。用于该示例性动臂油缸的冲程222可等于1260 mm
±
2.0 mm。杆眼孔直径252可等于80 mm
±
0.5 mm。耳轴帽孔直径242可等于80 mm
±
0.5 mm。该示例性动臂油缸的管322的中心轴向延伸孔326的直径328可等于120 mm
±
0.5 mm,并且该示例性动臂油缸的杆332的外径334可等于85 mm
±
0.5 mm。该示例性动臂油缸的系统压力可等于35,000 kpa
±
3750 kpa。基于以下一个或多个来为特定机器10确定所公开的尺寸范围:基于物理学的方程式、有限元分析、经验证据和其他计算分析,所述其他计算分析考虑了如下因素:诸如机器10的动臂与主体之间的运动学相互关系、相应的结构部件的运动范围、在机器10操作期间液压油缸将承受的载荷、期望的疲劳寿命、液压流体压力和机械安全系数。在一个示例中,该示例性动臂油缸的本实施例的销间尺寸132、冲程222、杆眼孔直径252、耳轴帽孔直径242、管322中心轴向延伸孔326的直径328以及杆332的外径334的所公开范围中的一个或多个可直接并且在功能性上与用于致动系统压力为35,000 kpa
±
3500 kpa的动臂22的当前公开的液压油缸26相关,并且可基于所述液压油缸来建立,根据本实用
新型公开的实施例中的任何一个或多个,这可促使改进和提高综合性能。
127.323gx 铲斗液压油缸(323gx bucket cylinder)在根据本实用新型公开的液压油缸的另一个示例性实施例(诸如适于用作用于致动铲斗14的液压油缸34的液压油缸)中,在杆332、活塞保持总成430和活塞420在管322的封闭远端342处触底而完全缩回时,液压油缸的销间尺寸132可等于1684 mm
±
2.0 mm。用于该示例性铲斗油缸的冲程222可等于1104 mm
±
2.0 mm。杆眼孔直径252可等于80 mm
±
0.5 mm。耳轴帽孔直径242可等于70 mm
±
0.5 mm。该示例性动臂油缸的管322的中心轴向延伸孔326的直径328可等于120 mm
±
0.5 mm,并且该示例性铲斗油缸的杆332的外径334可等于85 mm
±
0.5 mm。该示例性铲斗油缸的系统压力可等于35,000 kpa
±
3500 kpa。基于以下一个或多个来为特定机器10确定所公开的尺寸范围:基于物理学的方程式、有限元分析、经验证据和其他计算分析,所述其他计算分析考虑了如下因素:诸如机器10的铲斗与斗杆之间的运动学相互关系、相应的结构部件的运动范围、在机器10操作期间液压油缸将承受的载荷、期望的疲劳寿命、液压流体压力和机械安全系数。在一个示例中,该示例性铲斗油缸的本实施例的销间尺寸132、冲程222、杆眼孔直径252、耳轴帽孔直径242、管322中心轴向延伸孔326的直径328以及杆332的外径334的所公开范围中的一个或多个可直接并且在功能性上与用于相对于系统压力为35,000 kpa
±
3500 kpa致动铲斗14的当前公开的液压油缸34相关,并且可基于所述液压油缸来建立,根据本实用新型公开的实施例中的任何一个或多个,这可促使改进和提高综合性能。
128.350 斗杆液压油缸(350 stick cylinder)在根据本实用新型公开的液压油缸的另一个示例性实施例(诸如适于用作用于致动斗杆28的液压油缸32的液压油缸)中,在杆332、活塞保持总成430和活塞420在管322的封闭远端342处触底而完全缩回时,液压油缸的销间尺寸132可等于2548 mm
±
2.0 mm。用于该示例性斗杆油缸的冲程222可等于1758 mm
±
2.0 mm。杆眼孔直径252可等于100 mm
±
0.5 mm。耳轴帽孔直径242可等于100 mm
±
0.5 mm。该示例性斗杆油缸的管322的中心轴向延伸孔326的直径328可等于190 mm
±
0.5 mm,并且该示例性斗杆油缸的杆332的外径334可等于130 mm
±
0.5 mm。该示例性斗杆油缸的系统压力可等于35,000 kpa
±
3500 kpa。基于以下一个个或多个个来为特定机器10确定所公开的尺寸范围:基于物理学的方程式、有限元分析、经验证据和其他计算分析,所述其他计算分析考虑了如下因素:诸如机器10的斗杆与动臂之间的运动学相互关系、相应的结构部件的运动范围、在机器10操作期间液压油缸将承受的载荷、期望的疲劳寿命、液压流体压力和机械安全系数。在一个示例中,该示例性斗杆油缸的本实施例的销间尺寸132、冲程222、杆眼孔直径252、耳轴帽孔直径242、管322中心轴向延伸孔326的直径328以及杆332的外径334的所公开范围中的一个个或多个个可直接并且在功能性上与用于致动系统压力为35,000 kpa
±
3500 kpa的斗杆28的当前公开的液压油缸32相关,并且可基于所述液压油缸来建立,根据本实用新型公开的实施例中的任何一个个或多个个,这可促使改进和提高综合性能。
129.350动臂液压油缸(350 boom cylinder)在根据本公开的液压油缸的另一个示例性实施例(诸如适于用作用于致动动臂22的液压油缸26的液压油缸)中,在杆332、活塞保持总成430和活塞420在管322的封闭远端342处触底而完全缩回时,液压油缸的销间尺寸132可等于2247 mm
±
2.0 mm。用于该示例性动臂油缸的冲程222可等于1575 mm
±
2.0 mm。杆眼孔直径252可等于110 mm
±
0.5 mm。耳轴帽孔直径242可等于110 mm
±
0.5 mm。该示例性动臂油缸的管322的中心轴向延伸孔326的直径328可等于160 mm
±
0.5 mm,并且该示例性动
臂油缸的杆332的外径334可等于110 mm
±
0.5 mm。该示例性动臂油缸的系统压力可等于35,000 kpa
±
3750 kpa。基于以下一个或多个来为特定机器10确定所公开的尺寸范围:基于物理学的方程式、有限元分析、经验证据和其他计算分析,所述其他计算分析考虑了如下因素:诸如机器10的动臂与主体之间的运动学相互关系、相应的结构部件的运动范围、在机器10操作期间液压油缸将承受的载荷、期望的疲劳寿命、液压流体压力和机械安全系数。在一个示例中,该示例性动臂油缸的本实施例的销间尺寸132、冲程222、杆眼孔直径252、耳轴帽孔直径242、管322中心轴向延伸孔326的直径328以及杆332的外径334的所公开范围中的一个或多个可直接并且在功能性上与用于致动系统压力为35,000 kpa
±
3500 kpa的动臂22的当前公开的液压油缸26相关,并且可基于所述液压油缸来建立,根据本实用新型公开的实施例中的任何一个或多个,这可促使改进和提高综合性能。
130.350 铲斗 tb 液压油缸(350 bucket tb cylinder)在根据本实用新型公开的液压油缸的另一个示例性实施例(诸如适于用作用于致动铲斗14的液压油缸34的液压油缸)中,在杆332、活塞保持总成430和活塞420在管322的封闭远端342处触底而完全缩回时,液压油缸的销间尺寸132可等于2013 mm
±
2.0 mm。用于该示例性铲斗油缸的冲程222可等于1356 mm
±
2.0 mm。杆眼孔直径252可等于100 mm
±
0.5 mm。耳轴帽孔直径242可等于90 mm
±
0.5 mm。该示例性动臂油缸的管322的中心轴向延伸孔326的直径328可等于160 mm
±
0.5 mm,并且该示例性动臂油缸的杆332的外径334可等于110 mm
±
0.5 mm。该示例性铲斗油缸的系统压力可等于35,000 kpa
±
3500 kpa。基于以下一个或多个来为特定机器10确定所公开的尺寸范围:基于物理学的方程式、有限元分析、经验证据和其他计算分析,所述其他计算分析考虑了如下因素:诸如机器10的铲斗与斗杆之间的运动学相互关系、相应的结构部件的运动范围、在机器10操作期间液压油缸将承受的载荷、期望的疲劳寿命、液压流体压力和机械安全系数。在一个示例中,该示例性铲斗油缸的本实施例的销间尺寸132、冲程222、杆眼孔直径252、耳轴帽孔直径242、管322中心轴向延伸孔326的直径328以及杆332的外径334的所公开范围中的一个或多个可直接并且在功能性上与用于相对于系统压力为35,000 kpa
±
3500 kpa致动铲斗14的当前公开的液压油缸34相关,并且可基于所述液压油缸来建立,根据本实用新型公开的实施例中的任何一个或多个,这可促使改进和提高综合性能。
131.350 铲斗 ub液压油缸(350ub)在根据本实用新型公开的液压油缸的另一个示例性实施例(诸如适于用作用于致动铲斗14的液压油缸34的液压油缸)中,在杆332、活塞保持总成430和活塞420在管322的封闭远端342处触底而完全缩回时,液压油缸的销间尺寸132可等于2089 mm
±
2.0 mm。用于该示例性铲斗油缸的冲程222可等于1396 mm
±
2.0 mm。杆眼孔直径252可等于110 mm
±
0.5 mm。耳轴帽孔直径242可等于100 mm
±
0.5 mm。该示例性动臂油缸的管322的中心轴向延伸孔326的直径328可等于170 mm
±
0.5 mm,并且该示例性铲斗油缸的杆332的外径334可等于110 mm
±
0.5 mm。该示例性铲斗油缸的系统压力可等于35,000 kpa
±
3500 kpa。基于以下一个或多个来为特定机器10确定所公开的尺寸范围:基于物理学的方程式、有限元分析、经验证据和其他计算分析,所述其他计算分析考虑了如下因素:诸如机器10的铲斗与斗杆之间的运动学相互关系、相应的结构部件的运动范围、在机器10操作期间液压油缸将承受的载荷、期望的疲劳寿命、液压流体压力和机械安全系数。在一个示例中,该示例性铲斗油缸的本实施例的销间尺寸132、冲程222、杆眼孔直径252、耳轴帽孔直径242、管322中心轴向延伸孔326的直径328以及杆332的外径334的所公开范围中的
一个或多个可直接并且在功能性上与用于相对于系统压力为35,000 kpa
±
3500 kpa致动铲斗14的当前公开的液压油缸34相关,并且可基于所述液压油缸来建立,根据本实用新型公开的实施例中的任何一个或多个,这可促使改进和提高综合性能。
132.工业实用性
133.本实用新型所公开的液压油缸可在针对冲程、销间长度、杆眼销直径、耳轴帽销直径、标称缸孔直径、标称活塞杆直径和被供应给每个液压油缸的液压流体的系统压力的特定性能尺寸的应用是至少地部分基于以下项的结果的任何机器上实施:基于物理学的方程式、有限元分析、经验数据、结构分析以及对执行某些任务所需的特定机器的各种结构元件(诸如通过液压油缸彼此相对致动的挖掘机的动臂、斗杆和作业工具)的运动学分析。可至少部分地基于各种计算分析来确定在特定机器上使用的每个液压油缸的特定性能尺寸,所述计算分析包括对载荷下结构元件的疲劳分析、连杆标准和运动学考虑因素,所述考虑因素包括液压油缸的头端和杆端将在其中枢转地连接的连杆点的相对位置、在每个液压油缸的各个部件上的液压系统压力、环向应力、扭转应力、剪切应力、压缩应力和抗拉应力,以及其他机械设计考虑因素。
134.在机器10的操作期间,位于站20内的操作员可通过接口装置46命令作业工具14沿在期望方向上以期望速度的特定运动。可将由接口装置46生成的一个或多个对应信号提供给电子控制器,所述信号指示由所公开的液压油缸中的一个或多个互连的结构部件的期望运动,以及机器性能信息,例如传感器数据,所述传感器数据包括液压流体压力数据、位置数据、速度数据、加速度数据、泵排量数据和本领域已知的其他数据。
135.响应于来自接口装置46的信号并且基于机器性能信息,控制器可生成被引导到泵、马达和/或阀的控制信号,所述控制信号控制在每个液压油缸的一侧上到头端室的液压流体流和在活塞的相对侧上到杆端室的液压流体流。在一个示例性实施方式中,为了使右行进马达42r在第一方向上以增加的速度旋转,控制器可生成控制信号,所述控制信号使第一回路的泵增加其排量并将流体以更大速率排出到右泵通道中。另外,控制器可生成控制信号,所述控制信号使切换阀移向两个穿流位置(flow
‑
passing position)中的一个和/或保持在其中。在来自右泵通道的流体进入并通过右行进马达42r之后,流体可经由左泵通道返回到泵。此时,右行进马达42r的速度可取决于泵的排出速率,并且取决于由切换阀对流过右行进马达42r的流体流量的限制量(如果有的话)。通过将切换阀移动到两个穿流位置中的另一个,可反转右行进马达42r的移动。
136.液压油缸32可与右行进马达42r同时和/或独立地移动。具体地,当右行进马达42r从泵接收流体时,可移动一个或多个计量阀以将一些流体转移到液压油缸32的头端室352或杆端室354中。同时,每个计量阀可被移动以将废液从液压油缸32引导回泵。当切换阀和适当的计量阀完全打开时,右行进马达42r和液压油缸32的移动可被连结并且取决于来自泵的流体的流速。
137.为了提供对右行进马达42r和液压油缸32的速度的独立控制,必须对流入和/或流出这些致动器中的至少一个个的流体进行计量。例如,切换阀和/或计量阀可移动到中间位置,此时流过其中的流体被限制到某种程度。当发生这种情况时,可根据需要调整致动器中的一个或两个的速度。液压油缸26和34以及左行进马达42l、回转马达43和辅助马达的操作可以与上述类似的方式来实施。因此,在本公开中将不描述这些致动器的单次移动的详细
描述。
138.在一些操作期间,从致动器的相关联的泵提供给各个致动器的流体的流速可能不足以满足操作员需求。例如,在通过液压油缸26进行的动臂提升操作期间,操作员可请求机器10的速度,所述速度将要求第四回路内的流体的流速超过相关联的泵的容量。在这种情况期间,控制器可例如使对应的组合阀的阀元件将流体从第二液压回路传递到第四液压回路,由此增加可供液压油缸26使用的流体的流速。此时,从液压油缸26排出的流体可经由组合阀返回到第四回路的泵和第二回路的泵。经由其他组合阀在其他回路之间的流量共享可以类似方式实施。
139.在液压回路之间将流体引导到特定液压油缸或其他致动器的流体共享可是特别有益的,这是由于特定回路需要附加流量的情况。具体地,在挖掘操作期间,液压油缸26可能需要额外的流量,并且与此同时,向行进马达提供加压的液压流体的回路的泵此时可能处于闲置。因此,在将加压液压流体供应到液压油缸的回路最需要时,闲置回路的全部容量(流量和压力控制)可用。对于其他回路,情况可能并非总是如此。例如,在非闲置的回路之间共享流体可能效率低下,几乎没有益处,和/或减少了对回路操作的控制。
140.当从一个致动器排出的流体量超过对应泵可有效消耗回流流体的速率时,也可选择性地实施流量共享。例如,在动臂22下降操作期间,当动臂22在重力作用下移动时,流体可在高压力下从液压油缸26的头端室352排出。这种排出流体中的一些流体可经由计量阀重新引导回到液压油缸26的杆端室354中。该操作可被称为再生,并且相对于将泵供应的流体引导到杆端室354中提高效率。然而,在再生期间,由于杆端室354中存在杆332的一部分,因此从头端室352排出的流体量大于进入杆端室354的流体量。因此,流出头端室352的这种额外流体必须在某处被消耗。在各种示例性实施方式中,在动臂下降移动期间从液压油缸26排出的额外流体可被引导通过与不同回路相关联的泵。这种超高压流体可用于将泵驱动为马达,由此将能量返回到液压系统。
141.在所公开的实施例中,由各种泵提供的流量在许多操作期间可基本上不受限制,使得在致动过程中不会不必要地浪费大量能量。因此,本实用新型公开的实施例可提供改进的能量使用和节约。另外,组合来自不同回路的流体流以满足各个致动器的需求的能力可允许减少液压系统内所需的泵的数量和/或这些泵的大小和容量。这些减少可减少泵损失,提高整体效率,改进液压系统的体积及包装,和/或降低液压系统的成本。以上说明的用于在机器上的某些液压回路与液压油缸之间共享加压液压流体以及用于在将能量返回到液压系统时进行再生的所有考虑因素也可能会纳入在确定每个液压油缸的性能尺寸(诸如冲程尺寸、销间尺寸、耳轴帽孔和耳轴销直径以及杆眼孔和杆眼销直径)时所使用的计算分析中。
142.本领域技术人员将显而易见的是,可对所公开的系统进行各种修改和改变。考虑说明书和所公开的系统的实践,其他实施例对于本领域技术人员是显而易见的。希望说明书和示例仅被认为是示例性的,其保护范围由所附权利要求书及其等同物确定。
再多了解一些
本文用于企业家、创业者技术爱好者查询,结果仅供参考。