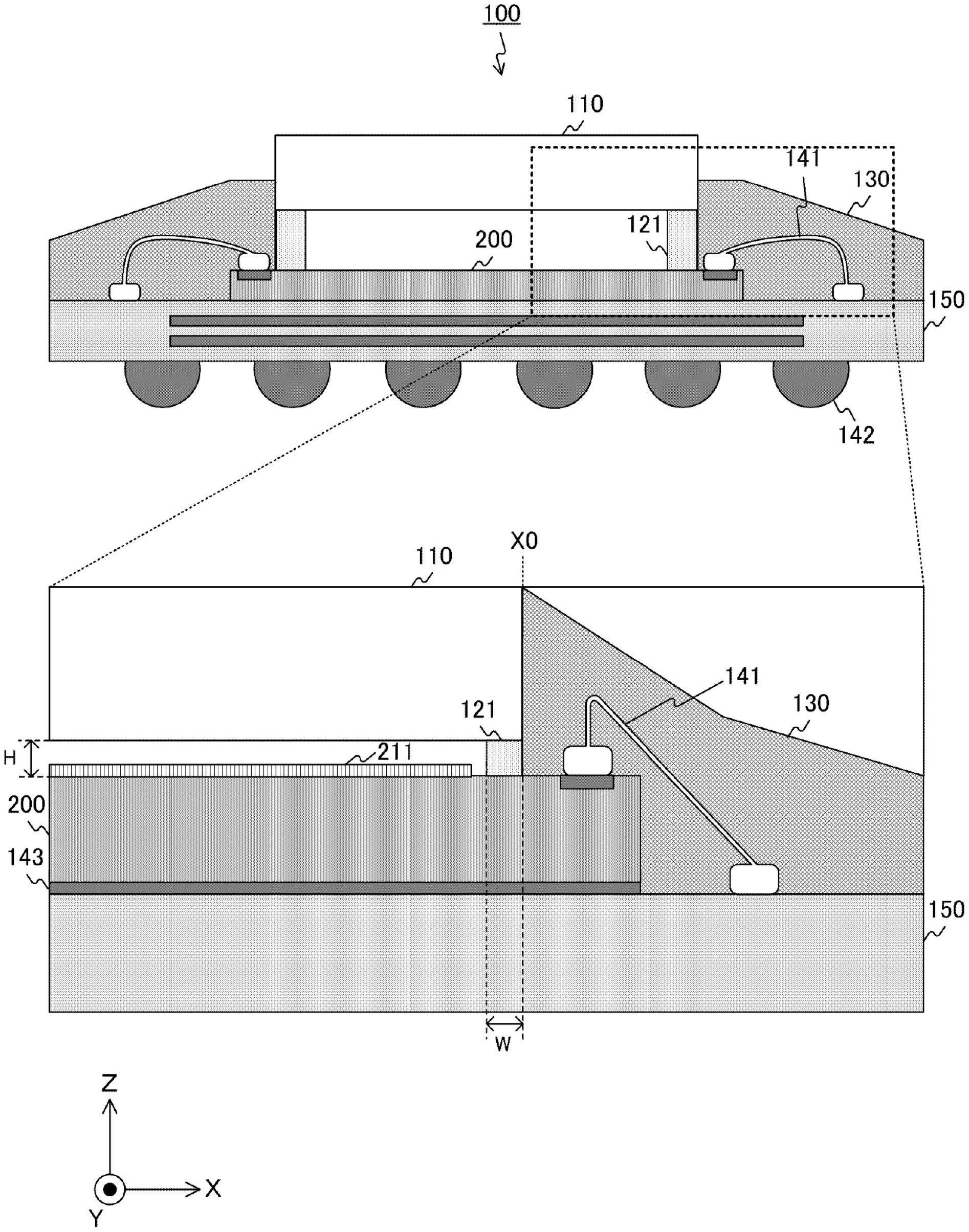
1.本技术涉及半导体封装。具体地,本技术涉及具有芯片上玻璃(goc:glass on chip)结构的半导体封装和该半导体封装的制造方法。
背景技术:
2.近年来,随着摄像装置中器件的晶圆堆叠技术的发展,逻辑和像素配线通常被配置在芯片的下层中,并且像素占用率增大。另一方面,以封装的小型化为目的的goc结构的应用主要在车载封装中普及(例如,参见专利文献1)。这里,goc结构是以下结构:其中将半导体芯片裸片接合(die-bonded)到中介层,通过引线接合等进行电气连接,将粘合树脂涂布到芯片上,在粘合树脂上安装盖玻璃,并且通过密封树脂或模塑树脂保护半导体芯片。在摄像元件被布置为半导体芯片的情况下,将粘合树脂涂布到除像素部以外的部分上。
3.引文列表
4.专利文献
5.专利文献1:日本专利申请特开第2016-72266号
技术实现要素:
6.本发明要解决的问题
7.在上述传统技术中,goc结构实现了半导体封装的小型化。然而,当涂布粘合树脂时,考虑到涂布位置精度、取决于诸如触变性和粘性等树脂物理性能的涂布稳定性和安装玻璃时的树脂扩散等,需要确保具有足够尺寸的接合部分,使得粘合树脂不会干涉像素。因此,难以进一步减小尺寸。
8.本技术是鉴于这种情况而提出的,并且本技术的目的是使设置有像素的半导体封装的小型化变得容易。
9.问题的解决方案
10.本技术是为了解决上述问题而提出的,并且其第一方面是一种半导体封装,包括:透明部件;半导体芯片,其中像素被排列在芯片平面的一部分上;感光性肋部,其是布置在所述芯片平面中不对应于所述像素的区域和所述透明部件之间的感光性树脂;和中介层,其电气连接到所述半导体芯片。这带来了易于小型化的效果。
11.此外,在第一方面中,还可以包括将所述感光性肋部与所述半导体芯片接合的粘合树脂。这带来了感光性肋部在完全固化状态下进行接合的效果。
12.此外,在第一方面中,还可以包括限位件,其中,所述半导体芯片可以被布置在所述透明部件和所述中介层之间,在将从所述中介层到所述透明部件的方向设定为向上方向的情况下,所述感光性肋部可以形成在所述透明部件的下表面上的与所述像素相对的预定区域周围,并且所述限位件可以形成在所述下表面的所述预定区域和所述感光性肋部之间。这带来了抑制渗出物侵入到像素中的效果。
13.此外,在第一方面中,所述感光性肋部可以形成为与所述透明部件和所述半导体
芯片两者紧密接触。这带来了不需要粘合树脂的效果。
14.此外,在第一方面中,所述透明部件可以是透镜。这带来了不需要盖玻璃的效果。
15.此外,在第一方面中,所述感光性肋部的截面形状可以是锥形形状。这带来了抑制反射光入射到像素上的效果。
16.此外,在第一方面中,所述半导体芯片可以包括:硅基板;和有机膜,其形成在所述硅基板的基板表面的一部分上,其中,所述感光性肋部可以被布置在所述基板表面的未形成所述有机膜的区域和所述透明部件之间。这带来了避免由于有机膜的剥离而导致的缺陷的效果。
17.此外,在第一方面中,所述半导体芯片可以具有开口部,并且所述开口部的端部到所述有机膜的距离可以不小于200微米。这带来了避免由于有机膜的剥离而导致的缺陷的效果。
18.此外,在第一方面中,以朝向所述像素的方向作为内侧方向,所述感光性肋部的内壁形状可以是通过连接多个三棱柱而获得的形状。这带来了提高光学特性的效果。
19.此外,在第一方面中,所述感光性肋部的相对于内壁的外壁的形状可以是通过连接多个三棱柱而获得的形状。这带来了提高光学特性的效果。
20.此外,在第一方面中,还可以包括:坝部;和密封树脂,其密封所述半导体芯片、所述透明部件和所述中介层,其中,所述半导体芯片可以被布置在所述透明部件和所述中介层之间,并且在将从所述中介层到所述透明部件的方向设定为向上方向的情况下,所述坝部可以形成在所述透明部件的上表面上的位于所述像素正上方的光接收区域周围。这带来了防止树脂突出的效果。
21.此外,在第一方面中,所述密封树脂的一部分可以遮蔽所述透明部件的所述上表面中的位于所述透明部件的外周和所述坝部之间的区域。这带来了防止密封树脂突出的效果。
22.此外,在第一方面中,还可以包括模塑树脂,其遮蔽所述透明部件的所述上表面中的位于所述透明部件的外周和所述坝部之间的区域。这带来了防止模塑树脂突出的效果。
23.此外,本技术的第二方面是一种半导体封装的制造方法,所述方法包括:将其中像素被排列在预定芯片平面的一部分上的半导体芯片与中介层电气连接的连接过程;在透明部件的两个表面中的一个表面的不与所述像素相对的区域中形成感光性树脂作为感光性肋部的感光性肋部形成过程;和将其上形成有所述感光性肋部的所述透明部件放置在所述半导体芯片上的放置过程。这带来了易于小型化的效果。
24.此外,在第二方面中,还可以包括:将抗蚀剂涂布到包括硅基板和形成在所述硅基板的基板表面上的有机膜的所述半导体芯片上的涂布过程;去除所述抗蚀剂的一部分的抗蚀剂去除过程;和去除所述有机膜中未涂布所述抗蚀剂的部分的有机膜去除过程,其中,所述连接过程可以是在所述有机膜去除过程之后执行的。这带来了避免由于有机膜的剥离而导致的缺陷的效果。
附图说明
25.图1是根据本技术第一实施方案的半导体封装的截面图的示例。
26.图2是根据本技术第一实施方案的透明部件和半导体芯片的平面图的示例。
27.图3是用于说明根据本技术第一实施方案的抑制眩光等的效果的图。
28.图4是第一比较例中的半导体封装的截面图的示例。
29.图5是用于说明根据本技术第一实施方案的半导体封装的制造方法的图。
30.图6是用于说明根据本技术第一实施方案的从裸片接合到密封的步骤的图。
31.图7是用于说明根据本技术第一实施方案的透明部件的制造方法的图。
32.图8是示出根据本技术第一实施方案的半导体封装的制造方法的流程图的示例。
33.图9是示出根据本技术第一实施方案的透明部件的制造方法的流程图的示例。
34.图10是示出根据本技术第一实施方案的第一变形例的感光性肋部的截面形状的示例的图。
35.图11是根据本技术第一实施方案的第二变形例的透明部件的平面图的示例。
36.图12是根据本技术第一实施方案的第三变形例的半导体封装的截面图的示例。
37.图13是用于说明根据本技术第一实施方案的第三变形例的从裸片接合到密封的步骤的图。
38.图14是示出根据本技术第一实施方案的第三变形例的透明部件的制造方法的流程图的示例。
39.图15是根据本技术第一实施方案的第四变形例的半导体封装的截面图的示例。
40.图16是用于说明根据本技术第一实施方案的第四变形例的直到放置透明部件为止的制造方法的图。
41.图17是示出根据本技术第一实施方案的第四变形例的透明部件的制造方法的流程图的示例。
42.图18是根据本技术第二实施方案的半导体封装的截面图的示例。
43.图19是第二比较例中的半导体封装的截面图的示例。
44.图20是用于说明根据本技术第二实施方案的直到去除抗蚀剂为止的步骤的图。
45.图21是用于说明根据本技术第二实施方案的直到对硅基板进行开口为止的步骤的图。
46.图22是根据本技术第三实施方案的透明部件的仰视图的示例。
47.图23是根据本技术第三实施方案的感光性肋部的立体图的示例。
48.图24是用于说明根据本技术第三实施方案的透明部件的制造方法的图。
49.图25是根据本技术第三实施方案的变形例的透明部件的仰视图的示例。
50.图26是根据本技术第四实施方案的半导体封装的截面图和平面图的示例。
51.图27是第三比较例中的半导体封装的截面图的示例。
52.图28是用于说明根据本技术第四实施方案的半导体封装的制造方法的图。
53.图29是根据本技术第四实施方案的变形例的半导体封装的截面图的示例。
具体实施方式
54.在下文中说明用于实施本技术的方式(在下文中,被称为实施方案)。将按照以下顺序进行说明。
55.1.第一实施方案(其中感光性肋部形成在透明部件的下表面上的示例)
56.2.第二实施方案(其中感光性肋部形成在透明部件的下表面上并且去除了感光性
肋部下方的有机膜的示例)
57.3.第三实施方案(其中感光性肋部形成在透明部件的下表面上并且其内壁呈锯齿状的示例)
58.4.第四实施方案(其中感光性肋部形成在透明部件的下表面上并且坝部形成在感光性肋部的上表面上的示例)
59.《1.第一实施方案》
60.[半导体封装的构成例]
[0061]
图1是根据本技术第一实施方案的半导体封装100的截面图的示例。半导体封装100是安装在摄像装置等上的半导体封装,并且包括透明部件110、半导体芯片200和中介层150。
[0062]
半导体芯片200拍摄图像数据。在半导体芯片200的芯片平面的一部分上排列有多个像素211。例如,使用固态摄像元件作为半导体芯片200。
[0063]
在下文中,将垂直于半导体芯片200的芯片平面的轴称为“z轴”,并且将平行于芯片平面的预定轴称为“x轴”。将垂直于x轴和z轴的轴称为“y轴”。该图是从y轴方向观察时的截面图。此外,半导体芯片200被布置在中介层150和透明部件110之间,并且将从中介层150到透明部件110的方向设定为向上方向。
[0064]
此外,虽然在该图中,部分区域设置有图案,但是这些图案仅是为了容易识别区域的范围而设置的,并且与实际的外观和材料无关。此外,具有相同图案的部分不一定由相同材料制成。这同样适用于以下附图。
[0065]
中介层150是在半导体芯片200和半导体封装100外部的电路之间中继信号的基板。使用陶瓷、有机材料、柔性印刷电路(fpc:flexible printed circuit)、玻璃或硅等作为中介层150的材料。此外,中介层150的上表面的一部分通过裸片附着材料143接合到半导体芯片200的下表面。
[0066]
使用环氧基、丙烯酸基或硅酮基膏状材料或裸片附着膜(daf:die attach film)作为裸片附着材料143。
[0067]
此外,在中介层150的上表面的未接合到半导体芯片200的区域中设置接合焊盘(未示出),并且接合焊盘通过引线141电气连接(即,引线接合)到半导体芯片200。注意,代替引线接合,中介层150和半导体芯片200也可以通过侧面配线或倒装芯片安装来电气连接。
[0068]
此外,在中介层150的下表面上排列有多个焊球142。利用这些焊球142,半导体封装100被安装在外部基板等上。如此安装的半导体封装也被称为球栅阵列(bga:ball grid array)封装。
[0069]
注意,代替bga封装,诸如地网阵列(lga:land grid array)或有引线芯片载体(lcc:leaded chip carrier)等除bga以外的表面安装型封装也可以用作半导体封装100。可选择地,代替表面安装型,诸如双列直插式封装(dip:dual in-line package)、单列直插式封装(sip:single in-line package)或针栅阵列(pga:pin grid array)等引线插入型封装也可以用作半导体封装100。
[0070]
例如,透明部件110是盖玻璃,并被放置为其下表面与半导体芯片200的上表面相对。可以使用硼硅酸盐玻璃、晶体板或树脂透明板作为透明部件110。注意,代替盖玻璃,也
可以放置透镜作为透明部件110。
[0071]
此外,通过光刻在透明部件110的下表面的不与像素211相对的区域中形成感光性树脂。在下文中,该感光性树脂被称为“感光性肋部121”。注意,可以在透明部件110的上表面上进一步形成抗反射(ar:anti-reflection)涂层、红外(ir:infra-red)截止涂层或可见光截止涂层等。
[0072]
作为感光性肋部121(即,感光性树脂)的材料,使用在用紫外线照射时产生使单体固化的成分的感光性材料或者在用紫外线照射时固化以显现负性的材料。作为后者,使用环氧硅酮材料或环氧丙烯酸材料。另外,优选光刻图案化之后具有较少脱气量的材料。例如,组装时在200℃加热10分钟的过程中的脱气量优选为5000至20000ppm。另外,优选具有良好的图案化性能和粘合性的材料。
[0073]
此外,感光性肋部121在x轴方向和y轴方向上形成在从透明部件110的端部(诸如该图中的右端x0)开始的一定范围内的区域中。注意,在该图中,感光性肋部121的右端与透明部件110的右端一致,但是感光性肋部121的右端可以与透明部件110的右端分离。
[0074]
此外,感光性肋部121的截面形状为矩形。将感光性肋部121在平行于半导体芯片200的芯片平面的方向(x轴方向或y轴方向)上的尺寸定义为“宽度”,并且将感光性肋部121在z轴方向上的尺寸定义为“高度”。例如,感光性肋部121的宽度w为0.05毫米(mm)以上,并且高度h为0.01至0.03毫米(mm)。
[0075]
此外,感光性肋部121(感光性树脂)在成型阶段没有完全反应而留下未固化部分,并且当放置透明部件110时通过热施加而与半导体芯片200紧密接触。此时,为了使感光性树脂追随半导体芯片200的凹凸而产生充分的粘合,期望将未固化部分的弹性模量设定为100兆帕(mpa)以下。
[0076]
密封树脂130密封并保护透明部件110、半导体芯片200和中介层150。使用环氧树脂、丙烯酸树脂或硅酮树脂作为密封树脂130。
[0077]
注意,在形成密封树脂130之后,可以进一步形成模塑树脂,以进行保护。另外,透明部件110、半导体芯片200和中介层150可以被布置在其中通过分隔壁和中介层150预先形成空腔而无需设置模塑树脂的半导体封装100中。
[0078]
如上所述,其中半导体芯片200电气连接到中介层150,透明部件110(盖玻璃)安装在半导体芯片200上,并且通过密封树脂130或模塑树脂保护半导体芯片的结构对应于goc结构。
[0079]
此外,感光性肋部121(即,感光性树脂)被布置在半导体芯片200的芯片平面中不对应于像素211的区域和透明部件110之间。由于与涂布膏状粘合树脂的情况相比,感光性树脂可以通过曝光或显影以高精度成型,因此接合部分的设计缩小变得可能。此外,通过设定曝光条件使得在热压接合到半导体芯片200时树脂不会变形(换句话说,树脂不会扩散),在设计时就不需要考虑树脂的突出量。
[0080]
图2是根据本技术第一实施方案的透明部件110和半导体芯片200的平面图的示例。在该图中,a是放置前的透明部件110的仰视图。在该图中,b是半导体芯片200的俯视图。
[0081]
该图的a中的粗线表示透明部件110的外周。灰色部分表示形成感光性肋部121的部分。如该图的a所示,感光性肋部121形成在矩形开口区域111周围。
[0082]
如该图的b所示,矩形摄像单元210形成在半导体芯片200的芯片平面(即,上表面)
上。在摄像单元210中,多个像素211以二维格子状排列。每个像素211对入射光进行光电转换,以生成像素信号。然后,通过后级的信号处理电路(未示出)对像素信号进行处理,并生成图像数据。
[0083]
开口区域111包括当放置透明部件110时与摄像单元210相对的区域。开口区域111中由虚线包围的区域表示与摄像单元210相对的区域。优选地,在与摄像单元210相对的区域和感光性肋部121之间设置预定余量。例如,摄像单元210的右端x3和左端x4在x轴方向上位于开口区域111的左端x1和右端x2之间。这同样适用于y轴方向。
[0084]
如该图所示,感光性肋部121形成在除与像素211相对的区域(即,该图中由虚线包围的区域)以外的透明部件110的下表面上。
[0085]
图3是用于说明本技术第一实施方案中的抑制眩光的效果的图。优选地,将感光性肋部121(感光性树脂)的透过率设定为98%以上,并且将反射率设定为0.01%至1%。因此,入射到半导体芯片200的上表面上的反射光可以在感光性肋部121中透过,并且可以抑制不需要的光的再次入射。由此,抑制了眩光和重影的出现。
[0086]
注意,如该图所示,感光性肋部121的右端可以与透明部件110的右端分离。这同样适用于左端。
[0087]
这里,假设以下构成作为第一比较例:其中用膏状粘合树脂代替感光性肋部121将透明部件110接合到半导体芯片200。
[0088]
图4是第一比较例中的半导体封装的截面图的示例。在第一比较例中,将半导体芯片200裸片接合到并电气连接到中介层150,然后在除像素部以外使用分配器等涂布粘合树脂,并且将透明部件110安装在半导体芯片200上。此时,需要考虑涂布到半导体芯片200上的粘合树脂的涂布位置精度、取决于诸如触变性和粘性等树脂物理性能的涂布稳定性和安装玻璃时的树脂扩散等来进行器件设计。特别是,需要进行器件设计以确保其中粘合树脂不会干涉像素部的足够尺寸。这是使可以缩小器件的晶圆堆叠技术的优点降低的一个因素。例如,粘合树脂的宽度需要为0.5毫米(mm)以上。
[0089]
此外,在粘合树脂的透过率较低且反射率较高的情况下,当粘合树脂和像素之间的距离变短时,入射到半导体芯片200上的光可能会被粘合树脂反射,并且可能会出现眩光或重影。
[0090]
另一方面,在图1的半导体封装100中,感光性肋部121(感光性树脂)被布置在芯片平面中不对应于像素211的区域和透明部件110之间。由于感光性树脂可以通过曝光或显影以高精度成型,因此可以缩小接合部分。例如,感光性肋部121的宽度w可以被设定为大约0.05毫米(mm)。
[0091]
此外,通过布置具有高透过率和低反射率的感光性肋部121,可以抑制眩光和重影。
[0092]
[半导体封装的制造方法]
[0093]
图5是用于说明根据本技术第一实施方案的半导体封装100的制造方法的图。如该图的a所示,制造系统制造多个半导体芯片200。如该图的b所示,制造系统通过裸片附着材料143将每个半导体芯片200裸片接合到中介层150。
[0094]
然后,如该图的c所示,制造系统通过引线141将每个半导体芯片200和中介层150电气连接。如该图的d所示,制造系统将具有形成在下表面上的感光性肋部121的透明部件
110放置在半导体芯片200的上表面上。
[0095]
然后,如该图的e所示,制造系统利用密封树脂130进行密封。如该图的f所示,制造系统将每个焊球142附接到中介层150的下表面。将该结构分离成多个部分,并且制造出多个半导体封装100。
[0096]
图6是用于说明根据本技术第一实施方案的从裸片接合到密封的步骤的图。在该图中,a至d是图5中的b、c、d和e的放大图。
[0097]
如图6的a所示,制造系统执行裸片接合,并且如图6的b所示,执行电气连接。然后,如该图的c所示,制造系统将具有感光性肋部121(感光性树脂)的透明部件110热压接合到芯片表面上的除像素211以外的区域。感光性树脂在曝光时未完全固化,在半固化状态下形成形状,并且保留粘合功能。通过在热压接合时将弹性模量(100mpa以下等)设定为追随器件的凹凸,可以抑制未接合部分。
[0098]
然后,如该图的d所示,制造系统形成密封树脂130。此外,还可以形成模塑树脂160。
[0099]
图7是用于说明根据本技术第一实施方案的透明部件110的制造方法的图。该图中的步骤是在图6中的c之前执行的。图6和图7中的各个步骤可以并行执行,或者可以按顺序执行。
[0100]
如图7的a所示,制造系统将感光性树脂涂布到玻璃晶圆上。该图的a中的灰色部分表示感光性树脂。如该图的b所示,制造系统在掩盖与像素211相对的部分的同时,对感光性树脂进行曝光和显影。如该图的c所示,制造系统针对每个芯片分割玻璃晶圆。通过这些步骤,形成具有感光性肋部121的透明部件110。
[0101]
如该图所示,通过在透明部件110(玻璃)侧形成感光性树脂膜,可以在不考虑对半导体芯片200侧的损坏的情况下执行显影。因此,可以减少树脂的残留物,从而提高成品率。此外,由于感光性树脂是从树脂侧进行曝光而不是通过透明部件110进行曝光,因此不需要考虑由于盖玻璃或涂层的类型而导致的波长衰减。
[0102]
此外,通过设定曝光条件使得在热压接合到半导体芯片200时树脂不会变形(换句话说,树脂不会扩散),在设计时就不需要考虑树脂的突出量。
[0103]
图8是示出根据本技术第一实施方案的半导体封装的制造方法的流程图的示例。
[0104]
制造系统将每个半导体芯片200裸片接合到中介层150(步骤s901),并且将每个半导体芯片200和中介层150电气连接(步骤s902)。然后,制造系统将其上形成有感光性肋部121的透明部件110安装在半导体芯片200的上表面上(步骤s903),并用密封树脂130密封上表面(步骤s904)。制造系统附接焊球142(步骤s905),并将结构分离成多个(步骤s906)。在步骤s906之后,制造系统结束半导体封装100的制造过程。
[0105]
图9是示出根据本技术第一实施方案的透明部件110的制造方法的流程图的示例。
[0106]
制造系统将感光性树脂涂布到玻璃晶圆上(步骤s911)。制造系统在掩盖与像素211相对的部分的同时,对感光性树脂进行曝光和显影(步骤s912)。制造系统针对每个芯片分割玻璃晶圆(步骤s914)。在步骤s914之后,制造系统结束透明部件110的制造过程,并开始后续处理。
[0107]
如上所述,根据本技术的第一实施方案,由于感光性肋部121(感光性树脂)被布置在半导体芯片200的不对应于像素的区域和透明部件110之间,因此与使用粘合树脂的情况
相比,可以缩小接合部分。这使半导体封装100的小型化变得容易。
[0108]
[第一变形例]
[0109]
在上述第一实施方案中,感光性肋部121的截面形状被形成为矩形,但是感光性肋部121的截面形状不限于矩形。根据第一实施方案的第一变形例的半导体封装100与第一实施方案的不同之处在于,感光性肋部121的截面形状是锥形形状。
[0110]
图10是示出根据本技术第一实施方案的第一变形例的感光性肋部121的截面形状的示例的图。如该图的a所示,在第一实施方案的第一变形例中,感光性肋部121的上表面的面积小于下表面的面积。因此,感光性肋部121在向上方向上变细(换句话说,变为锥形)。
[0111]
注意,如该图的b所示,可以使感光性肋部121的上表面的面积大于下表面的面积,以在向下方向上变为锥形。
[0112]
眩光和重影的出现方式根据入射光的角度(光路)而不同。在感光性树脂中,可以通过调整曝光时的焦点来控制形状,并且如该图所示,可以根据用途来选择形状。
[0113]
此外,虽然对于抑制眩光和重影有效的透过率和反射率根据将要安装的模块而不同,但是可以对感光性树脂本身进行着色,从而可以将透过率和反射率控制为期望值。
[0114]
此外,通过形成锥形形状,可以减少被感光性肋部121反射的反射光,并且可以抑制反射光入射到像素上。
[0115]
如上所述,根据本技术第一实施方案的第一变形例,可以通过感光性肋部121的锥形分配来抑制反射光入射到像素上。
[0116]
[第二变形例]
[0117]
在上述第一实施方案中,感光性肋部121形成在矩形开口区域111周围,但是感光性肋部121也可以形成在除矩形的周边以外的区域中。根据第一实施方案的第二变形例的半导体封装100与第一实施方案的不同之处在于,透明部件110中形成有感光性肋部121的区域的形状是不同的。
[0118]
图11是根据本技术第一实施方案的第二变形例的透明部件110的平面图的示例。该图中的灰色部分表示形成有感光性肋部121的区域。
[0119]
如该图的a所示,在第一实施方案的第二变形例中,开口区域111的四个角部被倒圆以形成圆角方形。感光性肋部121形成在圆角方形周围。通过对四个角部倒圆,可以减轻施加到接合部分的应力。
[0120]
近年来,为了应对回流安装,封装结构通常要求具有高耐热性。通过使用感光性树脂,可以稳定地制造能减轻施加到接合部分的应力的尺寸和形状(圆角方形等)。此外,由于通过曝光形成,因此可以应对通过膏状材料无法实现的复杂树脂形状。
[0121]
例如,如该图的b所示,感光性肋部121可以形成在多个同心矩形区域中。
[0122]
可选择地,如该图的c所示,在一个半导体芯片200上配置多个矩形摄像单元210的情况下,也可以以避开摄像单元210的岛状形状形成感光性肋部121。该图的c中由虚线包围的区域表示与摄像单元210相对的区域。
[0123]
如该图所示,感光性肋部121可以根据用途被设计成具有诸如圆角方形的周边、同心多边形和岛状形状等各种形状。
[0124]
如上所述,根据本技术第一实施方案的第二变形例,由于感光性肋部121形成在圆角矩形周围,因此可以减轻施加到接合部分的应力。
[0125]
[第三变形例]
[0126]
在上述第一实施方案中,感光性肋部121通过热压接合接合到半导体芯片200,但是感光性肋部121和半导体芯片200也可以用其他粘合树脂接合。根据第一实施方案的第三变形例的半导体封装100与第一实施方案的不同之处在于,感光性肋部121和半导体芯片200用粘合树脂接合。
[0127]
图12是根据本技术第一实施方案的第三变形例的半导体封装100的截面图的示例。根据第一实施方案的第三变形例的半导体封装100与第一实施方案的不同之处在于,感光性肋部121的下表面和半导体芯片200的上表面通过粘合树脂122接合。
[0128]
图13是用于说明根据本技术第一实施方案的第三变形例的从裸片接合到密封的步骤的图。
[0129]
如该图的a所示,制造系统执行裸片接合,并且如该图的b所示,执行电气连接。然后,如该图的c所示,制造系统放置其上预先使感光性肋部121完全固化的透明部件110。然后,制造系统从透明部件110的外部涂布具有低粘性的粘合树脂122,并利用毛细管现象执行渗透粘合。因此,如该图的d所示,粘合树脂122被填充在感光性肋部121的下表面和半导体芯片200的上表面之间。
[0130]
图14是示出根据本技术第一实施方案的第三变形例的透明部件的制造方法的流程图的示例。
[0131]
制造系统将感光性树脂涂布到玻璃晶圆上(步骤s911),并执行曝光和显影(步骤s912)。然后,制造系统执行硬烘以使感光性树脂完全固化(步骤s913)。在固化之后,感光性树脂可以用作间隔物。然后,制造系统针对每个芯片分割玻璃晶圆(步骤s914)。
[0132]
如上所述,根据本技术第一实施方案的第三变形例,由于感光性肋部121和半导体芯片200通过粘合树脂122接合,因此可以在放置透明部件110之前预先使感光性肋部121完全固化。
[0133]
[第四变形例]
[0134]
在上述第一实施方案的第三变形例中,感光性肋部121和半导体芯片200通过粘合树脂122接合,但是可能会出现粘合树脂122中的液体添加剂漏出的现象(即,渗出),并且液体可能会进入像素。根据第一实施方案的第四变形例的半导体封装100与第一实施方案的不同之处在于,通过限位件防止渗出物侵入到像素中。
[0135]
图15是根据本技术第一实施方案的第四变形例的半导体封装100的截面图的示例。在第一实施方案的第四变形例的透明部件110的下表面上进一步形成有限位件123。
[0136]
限位件123是形成在透明部件110的下表面上的与像素211相对的区域和感光性肋部121之间的感光性树脂。限位件123可以防止渗出物侵入到像素中。此外,在第一实施方案的第四变形例中,通过多次涂布感光性树脂并重复进行曝光和显影来形成z轴方向上的尺寸比限位件123更大的感光性肋部121。
[0137]
图16是用于说明根据本技术第一实施方案的第四变形例的直到放置透明部件110为止的制造方法的图。
[0138]
如该图的a所示,制造系统将感光性树脂涂布到玻璃晶圆的上表面上。该图的a中的灰色部分表示感光性树脂。如该图的b所示,制造系统通过掩盖对除感光性肋部121的下部和限位件123以外的部分进行曝光和显影。此外,制造系统执行硬烘以使感光性树脂完全
固化。因此,形成了感光性肋部121的下部和限位件123。
[0139]
然后,如该图的c所示,制造系统再次涂布感光性树脂。如该图的d所示,制造系统掩盖除感光性肋部121的上部以外的部分,对该部分进行曝光,并对该部分进行显影。此外,制造系统执行硬烘以使感光性树脂完全固化。因此,形成了感光性肋部121的上部。
[0140]
然后,制造系统针对每个芯片分割玻璃晶圆,并且如该图的e所示,将透明部件110上下颠倒地放置在半导体芯片200上。然后,制造系统使用粘合树脂122执行渗透粘合。
[0141]
注意,制造系统执行两次从感光性树脂的涂布到曝光和显影的步骤,但是也可以执行三次以上。
[0142]
图17是示出根据本技术第一实施方案的第四变形例的透明部件110的制造方法的流程图的示例。
[0143]
制造系统将感光性树脂涂布到玻璃晶圆的上表面上(步骤s911),并且执行曝光和显影(步骤s912)。制造系统执行硬烘以使感光性树脂完全固化(步骤s913)。
[0144]
然后,制造系统再次涂布感光性树脂(步骤s921),并且执行曝光和显影(步骤s922)。此外,制造系统执行硬烘(步骤s923),并且针对每个芯片分割玻璃晶圆(步骤s914)。
[0145]
如上所述,根据本技术第一实施方案的第四变形例,由于限位件123形成在透明部件110的下表面上的与像素211相对的区域和感光性肋部121之间,因此可以抑制渗出物侵入到像素211中。
[0146]
《2.第二实施方案》
[0147]
在上述第一实施方案中,在半导体芯片200中没有形成有机膜,但是像素的光电转换膜或微透镜等可以通过有机膜形成。然而,由于有机膜通常具有比无机膜更弱的粘合力,因此可以通过应力剥离形成有感光性肋部121的部分处的有机膜。第二实施方案的半导体封装100与第一实施方案的不同之处在于,去除了感光性肋部121下方的有机膜。
[0148]
图18是根据本技术第二实施方案的半导体封装100的截面图的示例。在该图下侧的放大图中,省略了密封树脂130和引线141。
[0149]
第二实施方案的半导体芯片200包括硅基板240和有机膜230。有机膜230形成在硅基板240的基板表面的一部分上。有机膜230包括像素中的光学部(诸如微透镜等)和光电转换部。用于引线接合的焊盘241形成在硅基板240上,并且焊盘241的从基板表面上的坐标x5到坐标x6的上部在z轴方向上开口。有机膜230和硅基板240被二氧化硅(sio2)等的无机膜220覆盖。
[0150]
此外,第二实施方案的感光性肋部121被布置在硅基板240的基板表面的没有形成有机膜230的区域和透明部件110之间。例如,有机膜230未形成在从开口部左端的坐标x6到坐标x9的区域中。感光性肋部121被布置在该区域中从坐标x7到坐标x8的范围内。
[0151]
例如,从开口部的端部(诸如x6等)到有机膜230的距离l被设定为200微米(μm)以上。
[0152]
这里,假设以下构成作为第二比较例:其中在感光性肋部121的接合部分处形成有机膜230。
[0153]
图19是第二比较例中的半导体封装的截面图的示例。在第二比较例中,有机膜230形成在从左侧开口部的左端的坐标x6到右侧开口部的右端(未示出)的范围内。感光性肋部121接合到有机膜230。通常,由于有机膜具有比无机膜更弱的粘合力,因此在该图的结构
中,可以通过在感光性肋部121的接合部分处产生的应力来剥离有机膜230。
[0154]
另一方面,在图18所示的半导体封装100中,由于去除了感光性肋部121的接合部分处的感光性肋部121,因此可以避免由于有机膜230的剥离而导致的缺陷。
[0155]
图20是用于说明根据本技术第二实施方案的直到去除抗蚀剂为止的步骤的图。如该图的a所示,制造系统通过常规的cmos图像传感器(cis:cmos image sensor)处理形成在整个表面上具有有机膜230的晶圆。
[0156]
如该图的b所示,制造系统将抗蚀剂300涂布到整个晶圆上。然后,如该图的c所示,制造系统通过蚀刻和清洗去除焊盘241周围的抗蚀剂300。例如,去除该图中坐标x9的左侧区域中的抗蚀剂300。
[0157]
随后,如该图的d所示,制造系统通过蚀刻和清洗去除已经去除了抗蚀剂300的区域(诸如坐标x9的左侧等)中的有机膜230。
[0158]
图21是用于说明根据本技术第二实施方案的直到对硅基板进行开口为止的步骤的图。该图中的步骤是在去除有机膜230的步骤之后执行的。
[0159]
如该图的a所示,制造系统在整个表面上形成无机膜220。然后,如该图的b所示,制造系统涂布抗蚀剂300。
[0160]
随后,如该图的c所示,制造系统仅对焊盘的上部(从坐标x5到坐标x6的区域)进行图案化,并且如该图的d所示,通过蚀刻对焊盘的上部进行开口。
[0161]
在图20和图21所示的步骤之后,对晶圆进行单片化,并执行图5中的b以后的步骤。
[0162]
如上所述,根据本技术的第二实施方案,由于去除了感光性肋部121的接合部分处的有机膜230,因此可以避免由于有机膜230的剥离而导致的缺陷。
[0163]
《3.第三实施方案》
[0164]
在上述第一实施方案中,感光性肋部121形成在透明部件110的下表面上的与像素相对的区域周围,但是在像素周围反射的光会进入像素,并且像素的光学特性可能会劣化。根据第三实施方案的半导体封装100与第一实施方案的不同之处在于,感光性肋部121的内壁是锯齿状的以提高光学特性。
[0165]
图22是根据本技术第三实施方案的透明部件110的仰视图的示例。该图中由虚线包围的矩形区域表示与像素211(未示出)相对的区域。将朝向像素211的方向称为“内侧方向”。该图中的箭头表示内侧方向。此外,灰色部分表示形成有感光性肋部121的区域。在感光性肋部121的侧壁中,将内侧壁表面称为“内壁”,并且将外侧壁表面称为“外壁”。
[0166]
在第三实施方案中,在感光性肋部121的内壁中形成有多个三角形凹口。由于这些凹口,感光性肋部121的内壁具有多个三棱柱连接而成的形状。换句话说,当从z轴方向观察时,感光性肋部121的内壁是锯齿状的。
[0167]
通过具有多个三棱柱连接而成的形状的感光性肋部121的内壁,光在三棱柱之间的凹口处被衰减,并且反射光减少。因此,可以提高像素的光学特性。该图中的点划线表示反射光的光路。
[0168]
图23是根据本技术第三实施方案的感光性肋部121的立体图的示例。例如,由形成在内壁中的三角形凹口形成的角度r1等于或小于90度。此外,该图中的粗线是连接由凹口形成的三棱柱的下表面的顶点和其上表面的顶点的线段。虚线箭头表示沿着该线段的直线(即,三角形中的母线)方向。例如,如该图的a所示,由母线和平行于透明部件110的平面的
轴(诸如x轴等)形成的角度r2为90度。
[0169]
注意,如该图的b所示,三棱柱的母线可以是倾斜的,并且由母线和平行于平面的轴(诸如x轴等)形成的角度r2可以被设定为除90度以外的角度。这种倾斜的棱柱被称为斜棱柱。
[0170]
图24是用于说明根据本技术第三实施方案的透明部件110的制造方法的图。如该图的a所示,制造系统放置将成为透明部件110的玻璃晶圆,并且如该图的b所示,将感光性树脂涂布到玻璃晶圆的上表面上。该图中的灰色部分表示感光性树脂。然后,如该图的c所示,制造系统通过曝光和显影对感光性肋部121进行图案化,并将感光性肋部上下颠倒。在该图中的这些步骤之后,执行图5中的d以后的步骤。
[0171]
该图中的d、e和f是在该图中的a、b和c的玻璃晶圆的平面中被单片化后的部分的示例。如该图的f所示,在图案化时形成具有锯齿状内壁的感光性肋部121。
[0172]
注意,第二实施方案可以应用于第三实施方案。
[0173]
如上所述,根据本技术的第三实施方案,由于感光性肋部121的内壁具有多个三棱柱连接而成的形状,因此可以减少反射光以提高像素的光学特性。
[0174]
[变形例]
[0175]
在上述第三实施方案中,感光性肋部121的内壁可以是锯齿状的,但是外壁也可以是锯齿状的。根据第三实施方案的变形例的半导体封装100与第三实施方案的不同之处在于,感光性肋部121的外壁也是锯齿状的。
[0176]
图25是根据本技术第三实施方案的变形例的透明部件110的仰视图的示例。根据第三实施方案的变形例的透明部件110与第三实施方案的不同之处在于,感光性肋部121的相对于内壁的外壁具有多个三棱柱连接而成的形状。通过使外壁呈锯齿状,来自外部的不需要的光在外壁的凹口处被衰减,并且可以进一步提高光学特性。
[0177]
如上所述,根据本技术第三实施方案的变形例,由于感光性肋部121的外壁具有多个三棱柱连接而成的形状,因此可以减少来自外部的光,并且可以进一步提高像素的光学特性。
[0178]
《4.第四实施方案》
[0179]
在上述第一实施方案中,利用密封树脂130进行密封,但是为了抑制眩光,可以使用密封树脂130的一部分在透明部件110的上表面上形成遮光膜。然而,当通过密封树脂130形成遮光膜时,密封树脂130可能会突出到像素正上方的区域,并且遮光膜不能以期望的形状形成。根据第四实施方案的半导体封装100与第一实施方案的不同之处在于,在透明部件110的上表面上形成有坝部,以防止树脂突出。
[0180]
图26是根据本技术第四实施方案的半导体封装100的截面图和平面图的示例。在该图中,a示出了半导体封装100的截面图,并且b示出了透明部件110的俯视图。
[0181]
如该图的a所示,第四实施方案的半导体封装100与第一实施方案的不同之处在于,在透明部件110的上表面上形成有坝部124。在透明部件110的上表面中,将摄像单元210正上方的矩形区域定义为光接收区域。
[0182]
如该图的b所示,坝部124通过感光性树脂形成在光接收区域周围。该图的b中由虚线包围的区域表示光接收区域,并且浅灰色区域表示坝部124。此外,密封树脂130的一部分覆盖透明部件110的外周和坝部124之间的区域,并且该部分用作遮光膜。该图的b中的粗线
表示透明部件110的外周。
[0183]
例如,在x轴方向上,将透明部件的左端的坐标设定为x10,并且将其右端的坐标设定为x13。此外,将摄像单元210的左端的坐标设定为x11,并且将其右端的坐标设定为x12。坝部124形成在从坐标x10到坐标x11的区域以及从坐标x12到坐标x13的区域中。密封树脂130覆盖透明部件110的上表面上的从坐标x10到坝部124以及从坐标x13到坝部124,以进行遮光。
[0184]
如该图所示,通过用密封树脂130遮蔽透明部件110的外周附近,可以防止其中在视角的端部处被除半导体芯片200以外的部件反射的杂散光入射到半导体芯片200上的眩光。
[0185]
这里,假设以下构成作为第三比较例:其中坝部124没有形成在透明部件110的上表面上。
[0186]
图27是第三比较例中的半导体封装的截面图的示例。在第三比较例中,当形成密封树脂130时,密封树脂130可能会突出到光接收区域,以产生渐晕。
[0187]
另一方面,在图26所示的第四实施方案中,由于坝部124形成在光接收区域周围,因此可以防止密封树脂130突出到光接收区域。因此,可以抑制渐晕。
[0188]
图28是用于说明根据本技术第四实施方案的半导体封装100的制造方法的图。如该图的a所示,制造系统制造多个半导体芯片200,并且如该图的b所示,将半导体芯片裸片接合到中介层150。
[0189]
然后,如该图的c所示,制造系统将每个半导体芯片200和中介层150电气连接。如该图的d所示,制造系统将具有形成在下表面上的感光性肋部121的透明部件110放置在半导体芯片200的上表面上,并且利用感光性树脂在透明部件110的上表面上形成坝部124。
[0190]
然后,如该图的e所示,制造系统利用密封树脂130进行密封。此时,密封树脂130的一部分覆盖透明部件110的外周附近并且遮光。
[0191]
如该图的f所示,制造系统将每个焊球142附接到中介层150的下表面,并且如该图的g所示,对焊球进行单片化。
[0192]
注意,第二和第三实施方案也可以应用于第四实施方案。
[0193]
如上所述,根据本技术的第四实施方案,由于坝部124形成在透明部件110的上表面上的光接收区域周围,因此当光被密封树脂130遮蔽时,可以防止树脂突出到光接收区域。
[0194]
[变形例]
[0195]
在上述第四实施方案中,通过密封树脂130形成遮光膜,但是也可以通过模塑树脂160形成遮光膜。根据第四实施方案的变形例的半导体封装100与第四实施方案的不同之处在于,通过模塑树脂160形成遮光膜。
[0196]
图29是根据本技术第四实施方案的变形例的半导体封装100的截面图的示例。根据第四实施方案的变形例的半导体封装100与第四实施方案的不同之处在于,进一步形成有模塑树脂160。
[0197]
在第四实施方案的变形例中,密封树脂130不覆盖透明部件110的上表面。取而代之的是,模塑树脂160的一部分覆盖透明部件110的外周和坝部124之间的区域,并且该部分用作遮光膜。
[0198]
如上所述,根据本技术第四实施方案的变形例,由于坝部124形成在透明部件110的上表面上的光接收区域周围,因此当光被模塑树脂160遮蔽时,可以防止树脂突出到光接收区域。
[0199]
注意,上述实施方案分别说明了用于体现本技术的示例,并且这些实施方案中的事项和权利要求中的发明特定事项具有对应关系。类似地,权利要求中的发明特定事项和由相同名称表示的本技术实施方案中的事项具有对应关系。然而,本技术不限于这些实施方案,并且可以通过在不脱离本技术主旨的情况下对实施方案进行各种变形来体现。
[0200]
注意,本说明书中所述的有益效果仅是示例,并且本技术的有益效果不限于此,并且可以包括其他效果。
[0201]
注意,本技术还可以如下所述地被构造。
[0202]
(1)一种半导体封装,包括:
[0203]
透明部件;
[0204]
半导体芯片,其中像素被排列在芯片平面的一部分上;
[0205]
感光性肋部,其是布置在所述芯片平面中不对应于所述像素的区域和所述透明部件之间的感光性树脂;和
[0206]
中介层,其电气连接到所述半导体芯片。
[0207]
(2)根据上述(1)所述的半导体封装,还包括:
[0208]
将所述感光性肋部与所述半导体芯片接合的粘合树脂。
[0209]
(3)根据上述(2)所述的半导体封装,还包括:
[0210]
限位件,其中,
[0211]
所述半导体芯片被布置在所述透明部件和所述中介层之间,
[0212]
在将从所述中介层到所述透明部件的方向设定为向上方向的情况下,所述感光性肋部形成在所述透明部件的下表面上的与所述像素相对的预定区域周围,并且
[0213]
所述限位件形成在所述下表面的所述预定区域和所述感光性肋部之间。
[0214]
(4)根据上述(1)所述的半导体封装,其中,
[0215]
所述感光性肋部形成为与所述透明部件和所述半导体芯片两者紧密接触。
[0216]
(5)根据上述(1)至(4)中任一项所述的半导体封装,其中,
[0217]
所述透明部件是透镜。
[0218]
(6)根据上述(1)至(5)中任一项所述的半导体封装,其中,
[0219]
所述感光性肋部的截面形状为锥形形状。
[0220]
(7)根据上述(1)至(6)中任一项所述的半导体封装,其中,
[0221]
所述半导体芯片包括:
[0222]
硅基板;和
[0223]
有机膜,其形成在所述硅基板的基板表面的一部分上,并且
[0224]
所述感光性肋部被布置在所述基板表面的未形成所述有机膜的区域和所述透明部件之间。
[0225]
(8)根据上述(7)所述的半导体封装,其中,
[0226]
所述半导体芯片具有开口部,并且
[0227]
所述开口部的端部到所述有机膜的距离不小于200微米。
[0228]
(9)根据上述(1)至(8)中任一项所述的半导体封装,其中,
[0229]
以朝向所述像素的方向作为内侧方向,所述感光性肋部的内壁形状是通过连接多个三棱柱而获得的形状。
[0230]
(10)根据上述(9)所述的半导体封装,其中,
[0231]
所述感光性肋部的相对于内壁的外壁的形状是通过连接多个三棱柱而获得的形状。
[0232]
(11)根据上述(1)至(10)中任一项所述的半导体封装,还包括:
[0233]
坝部;和
[0234]
密封树脂,其密封所述半导体芯片、所述透明部件和所述中介层,其中,
[0235]
所述半导体芯片被布置在所述透明部件和所述中介层之间,并且
[0236]
在将从所述中介层到所述透明部件的方向设定为向上方向的情况下,所述坝部形成在所述透明部件的上表面上的位于所述像素正上方的光接收区域周围。
[0237]
(12)根据上述(11)所述的半导体封装,其中,
[0238]
所述密封树脂的一部分遮蔽所述透明部件的所述上表面中的位于所述透明部件的外周和所述坝部之间的区域。
[0239]
(13)根据上述(11)所述的半导体封装,还包括:
[0240]
模塑树脂,其遮蔽所述透明部件的所述上表面中的位于所述透明部件的外周和所述坝部之间的区域。
[0241]
(14)一种半导体封装的制造方法,所述方法包括:
[0242]
将其中像素被排列在预定芯片平面的一部分上的半导体芯片与中介层电气连接的连接过程;
[0243]
在透明部件的两个表面中的一个表面的不与所述像素相对的区域中形成感光性树脂作为感光性肋部的感光性肋部形成过程;和
[0244]
将其上形成有所述感光性肋部的所述透明部件放置在所述半导体芯片上的放置过程。
[0245]
(15)根据上述(14)所述的半导体封装的制造方法,还包括:
[0246]
将抗蚀剂涂布到包括硅基板和形成在所述硅基板的基板表面上的有机膜的所述半导体芯片上的涂布过程;
[0247]
去除所述抗蚀剂的一部分的抗蚀剂去除过程;和
[0248]
去除所述有机膜中未涂布所述抗蚀剂的部分的有机膜去除过程,其中,
[0249]
所述连接过程是在所述有机膜去除过程之后执行的。
[0250]
附图标记列表
[0251]
100 半导体封装
[0252]
110 透明部件
[0253]
111 开口区域
[0254]
121 感光性肋部
[0255]
122 粘合树脂
[0256]
123 限位件
[0257]
124 坝部
[0258]
130 密封树脂
[0259]
141 引线
[0260]
142 焊球
[0261]
143 裸片附着材料
[0262]
150 中介层
[0263]
160 模塑树脂
[0264]
200 半导体芯片
[0265]
210 摄像单元211像素220无机膜230有机膜240硅基板241焊盘300抗蚀剂
再多了解一些
本文用于创业者技术爱好者查询,仅供学习研究,如用于商业用途,请联系技术所有人。