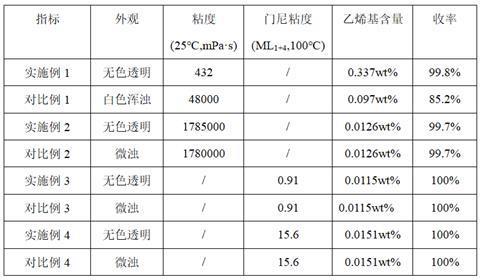
1.本发明属于氟硅橡胶制备领域,具体涉及一种乙烯基含氟聚硅氧烷及其制备方法。
背景技术:
2.近年来,氟硅橡胶已经越来越引起人们的重视。氟硅橡胶具有极其优异的耐油、溶剂和化学试剂的性能,良好的力学性能,卓越的耐高低温性能(-70~200℃),和较低的体积溶胀率,其中液体氟硅橡胶更是拥有加工优势,方便成型复杂零件,反应无副产物,对环境友好,是现代航空、火箭、导弹、宇航飞行等尖端科学技术及其它工业不可缺少的材料。乙烯基含氟聚硅氧烷,包括乙烯基氟硅油和乙烯基氟硅生胶是制备氟硅橡胶的基础聚合物,其制备方法一直是行业内的难题。
3.行业内制备乙烯基含氟聚硅氧烷的常用原料三氟丙基甲基环三硅氧烷(d3f)具有较大的空间结构,其产生的空间位阻效应会在聚合时对封端的si-vi产生一定的屏蔽作用,影响分子链的封端,同时由于d3f和封头剂不同的开环活性,导致得到的含氟聚合物的分子量远远超过设计值,粘度增大甚至失去加工性能。同时,如果将三氟丙基甲基硅氧烷链结直接连接到末端的si-vi时,三氟丙基较大的空间结构也会影响乙烯基的交联活性,导致氟硅橡胶固化困难,严重影响氟硅橡胶的力学性能。
4.中国专利文件cn105199106a公开了一种侧乙烯基氟硅油的制备方法,包括:加入60~70份d3f、0.4~0.5份vid4、0.2~0.3份mm于反应器中,50~70℃减压脱除低沸物,加入0.2~0.4份催化剂,使用氮气保护,反应温度60~80℃,反应时间40~60min,制得乙烯基氟硅油。但是,该方法制得乙烯基氟硅油的乙烯基仅位于分子链段内;此外,由于原料的不同开环活性,聚合过程中四甲基氢氧化铵碱胶催化剂对反应起到一种平衡作用,致使产品的收率很低;且加入的四甲基氢氧化铵碱胶催化剂加热分解不可避免的会产生有害或异味气体,对于硅油的品质也有一定影响。中国专利文件cn103642046a公开了一种端乙烯基硅油的制备方法,将端羟基氟硅油或端羟基氟硅油的丙酮溶液(n,n-二烷基氨基)二甲基乙烯基硅烷混合,于20~120℃下搅拌2~24h,减压蒸馏除去溶剂及残留的小分子,冷却后即得端乙烯基氟硅油。该方法采用二甲基乙烯基硅烷价格昂贵,丙酮溶剂会产生刺激性有害气味,且封端的端乙烯基链结直接与三氟丙基链结相连,交联活性低。专利cn102225997a中使用含氟乙烯基环体和三氟丙基甲基环三硅氧烷(d3f)为原料,锂硅醇盐为催化剂制备了氟硅生胶。该工艺制备了分子量和乙烯基可控的氟硅生胶,但只能制备侧链含乙烯基的生胶,无法制备端乙烯基氟硅生胶,端基不含乙烯基,硫化的过程中形成自由端,不能很好的固定分子链,导致产品硫化性能差。
技术实现要素:
5.针对目前制备乙烯基含氟聚硅氧烷的方法可控性差,以及所得产品交联活性低、硫化性能差等问题,本发明提供一种乙烯基含氟聚硅氧烷及其制备方法。该方法利用羟基
封端三氟丙基甲基聚硅氧烷作为基础原料进行聚合。
6.本发明的技术方案如下:一种乙烯基含氟聚硅氧烷,其特征在于,具有以下结构通式:,式中,m为0~5的整数,n为50~10000的整数。优选的,n为60~8000的整数。
7.优选的,当m n=50~3000的整数时,乙烯基含氟聚硅氧烷为乙烯基氟硅油,乙烯基含量为0.0117~0.342%,粘度为400~2000000mpa
·
s,当m n=3001~10000的整数时,乙烯基含氟聚硅氧烷为乙烯基氟硅生胶,乙烯基含量为0.0034~0.0115%,门尼粘度为0.9~25.0(ml
1 4
,100℃)。m n=3001~8100的整数,乙烯基含氟聚硅氧烷的门尼粘度为0.9~16.0(ml
1 4
,100℃)。
8.进一步优选的,乙烯基氟硅油为m n=300~500的整数,乙烯基含量为0.069~0.112%,粘度为20000~50000mpa
·
s;乙烯基氟硅生胶为m n=6000~8000的整数,乙烯基含量为0.0043~0.0057%,门尼粘度为7.0~15.0(ml
1 4
,100℃)。
9.本发明采用的短链乙烯基硅油封头剂为普通市售的短链端乙烯基硅油和多乙烯基硅油,根据实际乙烯基需求量来进行选择。如需制备端乙烯基氟硅油或端乙烯基氟硅生胶,则选择短链端乙烯基硅油作为封头剂;如需制备多乙烯基氟硅油或多乙烯基氟硅生胶,则选择短链多乙烯基硅油作为封头剂。含氟聚硅氧烷侧链含有乙烯基可以提高硅橡胶的交联网络结构,提高其力学强度。
10.一种乙烯基含氟聚硅氧烷的制备方法,包括如下步骤:(1)将羟基封端三氟丙基甲基聚硅氧烷和短链乙烯基硅油封端剂混合,搅拌均匀;(2)加热至130~150℃,加入线性氯化磷腈,搅拌反应3~5h;(3)保持反应温度,抽真空,进行脱水缩合反应2~4h;(4)恢复常压,加入终止剂0.5~1h后,终止反应,即得乙烯基含氟聚硅氧烷。
11.优选的,所述的羟基封端三氟丙基甲基聚硅氧烷与短链乙烯基硅油封端剂的质量比为100:(0.07~6)。进一步优选的,羟基封端三氟丙基甲基聚硅氧烷与短链乙烯基硅油封端剂的质量比为100:(0.13~5.6),产品为乙烯基氟硅油;羟基封端三氟丙基甲基聚硅氧烷与短链乙烯基硅油封端剂的质量比为100:(0.075~0.12),产品为乙烯基氟硅生胶。
12.短链乙烯基硅油封端剂为聚合度为5~10的端乙烯基硅油或多乙烯基硅油,根据产品中乙烯基含量需求进行选择,分子结构式如下:,
式中x=0~5。
13.步骤(1)中羟基封端三氟丙基甲基聚硅氧烷是从甲基三氟丙基二氯硅烷水解物中分离得到,为普通市售产品;其具有如下结构通式:,式中,a=5~20。
14.根据本发明优选的,步骤(2)所述的线性氯化磷腈的加入量是羟基封端三氟丙基甲基聚硅氧烷和封端剂总质量的0.0001~0.0005倍,进一步优选为0.0002~0.0003倍。
15.线性氯化磷腈的结构式为,,分子量为347.66。
16.根据本发明优选的,步骤(3)中抽真空至表压为-10~-5kpa,保持时间0.5~1.5h,然后使表压为-25~-15kpa,保持时间1.5~2.5h。反应过程中要严格控制压力,以防脱水反应过快,发生冲料现象。
17.根据本发明优选的,步骤(4)所述的终止剂加入量为线性氯化磷腈加入质量的1.2~2.0倍,优选为1.35~1.65倍。所述终止剂为n,n-二乙基-氨丙基甲基二甲氧基硅烷和甲基三氟丙基环三硅氧烷的共水解物,两者按照摩尔比1:1共水解,其中水的摩尔量是n,n-二乙基-氨丙基甲基二甲氧基硅烷的4倍。
18.本发明的有益效果如下:1、本发明首次采用羟基封端三氟丙基甲基聚硅氧烷和短链乙烯基硅油为主要原料制备得到分子量和乙烯基含量可控的乙烯基氟硅油或乙烯基氟硅生胶,所用原料均为聚合物,避免了小分子反应可能产生的生产安全问题。相比现有技术具有更好的工艺与成本优势,羟基封端三氟丙基甲基聚硅氧烷与封端剂都属于直链聚合物,在聚合时保持了相应的反应活性。利用短链乙烯基硅油封端剂可以制备侧链和端基同时含有乙烯基的产品,适用范围更加广泛。羟基封端三氟丙基甲基聚硅氧烷的生产相比于d3f更加节能环保,储存和运输也更加安全,符合当前发展趋势,本发明具有很好的前景;具有反应速度快、工艺简单、安全性好、收率高等优点。
19.2、本发明的制备过程简单,对于设备的要求不高,传统制备多乙烯基硅油的设备即可适用本工艺来制备多乙烯基硅油,首次利用线性氯化磷腈催化反应制备乙烯基含氟聚硅氧烷,相比于使用二甲基环体工艺催化效果更佳,单程收率接近100%,比使用暂时性催化剂四甲基氢氧化铵所制备的产品具有更环保,无气味(四甲基氢氧化铵有臭味)的优点。
20.3、本发明采用n,n-二乙基-氨丙基甲基二甲氧基硅烷和甲基三氟丙基环三硅氧烷的共水解物作为终止剂,相对于使用其它常用终止剂如氢氧化钾终止反应后产物不透明的情况,本终止剂与产物相容性优异,终止反应后产物完全透明。将所得产物乙烯基氟硅生胶
用于后续实验,所制得的氟硅混炼胶热稳定性更佳。
具体实施方式
21.下面结合实施例对本发明做进一步说明,但并不局限于此。以下实施例所使用的原料均为市购所得,均为所属技术领域的人员熟知原料,也可按现有技术制备得到。本发明具体实施例和对比例中使用的终止剂均为n,n-二乙基-氨丙基甲基二甲氧基硅烷和甲基三氟丙基环三硅氧烷的共水解物,其中两者摩尔比为1:1,水的摩尔量是n,n-二乙基-氨丙基甲基二甲氧基硅烷的4倍。
22.实施例1把1000g羟基封端三氟丙基甲基聚硅氧烷和55.6g端乙烯基硅油(x=0)加入到反应釜中,搅拌。加热至130℃,加入0.2216g线性氯化磷腈,搅拌反应3h。保持温度抽真空,进行脱水缩合,控制反应釜内表压为-10kpa,保持时间0.5h,然后使反应釜内表压-15kpa,保持时间1.5h。恢复常压,加入终止剂n,n-二乙基-氨丙基甲基二甲氧基硅烷和甲基三氟丙基环三硅氧烷的共水解物0.3102g继续搅拌0.5h,终止反应,即得端乙烯基氟硅油。
23.所得端乙烯基氟硅油结构式为:。
24.对比例1把1000g三氟丙基甲基环三硅氧烷(d3f)和55.6g端乙烯基硅油(x=0)加入到反应釜中,搅拌,加热至130℃。加入0.2216g线性氯化磷腈,搅拌反应3h,抽真空,控制反应釜内表压为-10kpa,保持时间0.5h。然后使反应釜内表压-15kpa,保持时间1.5h,恢复常压,加入终止剂n,n-二乙基-氨丙基甲基二甲氧基硅烷和甲基三氟丙基环三硅氧烷的共水解物0.3102g继续搅拌0.5h,终止反应,即得端乙烯基氟硅油。
25.实施例2把1000g羟基封端三氟丙基甲基聚硅氧烷和1.3003g端乙烯基硅油(x=0)加入到反应釜中,搅拌,加热至140℃。加入0.2113g线性氯化磷腈,搅拌反应4h,保持温度,抽真空,进行脱水缩合,控制反应釜内表压为-5kpa,保持时间1.0h。然后使反应釜内表压-20kpa,保持时间2.0h,恢复常压,加入终止剂n,n-二乙基-氨丙基甲基二甲氧基硅烷和甲基三氟丙基环三硅氧烷的共水解物0.2958g继续搅拌1h,终止反应,即得端乙烯基氟硅油。
26.所得端乙烯基氟硅油结构式为:
。
27.对比例2把1000g羟基封端三氟丙基甲基聚硅氧烷和1.3003g端乙烯基硅油(x=0)加入到反应釜中,搅拌,加热至140℃。加入0.2113g线性氯化磷腈,搅拌反应4h,保持温度,抽真空,进行脱水缩合,控制反应釜内表压为-8kpa,保持时间1.0h。然后使反应釜内表压-20kpa,保持时间2.0h,恢复常压,加入0.9861g终止剂koh水溶液(koh含量为30wt%)继续搅拌1h,终止反应,即得端乙烯基氟硅油。
28.实施例3把1000g羟基封端三氟丙基甲基聚硅氧烷、1.1876g端乙烯基硅油(x=0)加入到反应釜中,搅拌,加热至135℃。加入0.3003g线性氯化磷腈,搅拌反应3.5h,抽真空,进行脱水缩合,控制反应釜内表压为-10kpa,保持时间1h。然后使反应釜内表压-20kpa,保持时间2.5h,恢复常压,加入终止剂n,n-二乙基-氨丙基甲基二甲氧基硅烷和甲基三氟丙基环三硅氧烷的共水解物0.4806g继续搅拌1h,终止反应,即得端乙烯基氟硅生胶。
29.所得端乙烯基氟硅生胶结构式为:。
30.对比例3把1000g羟基封端三氟丙基甲基聚硅氧烷和1.1876g端乙烯基硅油(x=0)加入到反应釜中,搅拌,加热至135℃,加入0.3003g线性氯化磷腈,搅拌反应3.5h。抽真空,进行脱水缩合,控制反应釜内表压为-10kpa,保持时间1h,然后使反应釜内表压-20kpa,保持时间2.5h。恢复常压,加入1.6019g终止剂koh水溶液(koh含量为30wt%)继续搅拌1h,终止反应,即得端乙烯基氟硅生胶。
31.实施例4把1000g羟基封端的三氟丙基甲基聚硅氧烷和0.7901g多乙烯基硅油(x=5)加入到反应釜中,搅拌,加热至150℃,加入0.3000g线性氯化磷腈,搅拌反应5h。抽真空,进行脱水缩合,控制反应釜内表压为-10kpa,保持时间1.5h,然后使反应釜内表压-25kpa,保持时间2.5h。恢复常压,保持温度,加入终止剂n,n-二乙基-氨丙基甲基二甲氧基硅烷和甲基三氟丙基环三硅氧烷的共水解物0.4800g继续搅拌1h,终止反应,即得多乙烯基氟硅生胶。
32.所得多乙烯基氟硅生胶结构式为:。
33.对比例4把1000g羟基封端三氟丙基甲基聚硅氧烷和0.7901g多乙烯基硅油(x=5)加入到反应釜中,搅拌,加热至150℃,加入0.3000g线性氯化磷腈,搅拌反应5h。抽真空,进行脱水缩合,控制反应釜内表压为-10kpa,保持时间1.5h,然后使反应釜内表压-25kpa,保持时间2.5h。恢复常压,加入1.6000g终止剂koh水溶液(koh含量为30wt.%)中和1h,中和完毕,即得多乙烯基氟硅生胶。
34.实施例5氟硅混炼胶的制备:以乙烯基氟硅生胶的质量份计,取100份实施例4所制备的多乙烯基氟硅生胶和1.0份十二烷基苯磺酸钠、5.0份去离子水加入到真空捏合机里捏合15min,然后分5批加入共计45份改性纳米sio2,10份二甲氧基二甲基硅烷。每次加入sio2后捏合20min,全部加入完毕后升温170℃,釜内负压捏合2h后,得到氟硅混炼胶。取样分析:经硫化制成标准试样,并进行热稳定性测试对比试验,测试性能见表2。
35.对比例5氟硅混炼胶的制备:以乙烯基氟硅生胶的质量份计,取100份对比例4所制备的多乙烯基氟硅生胶和1.0份十二烷基苯磺酸钠、5.0份去离子水加入到真空捏合机里捏合15min,然后分5批加入共计45份改性纳米sio2,10份二甲氧基二甲基硅烷。每次加入sio2后捏合20min,全部加入完毕后升温170℃,釜内负压捏合2h后,得到氟硅混炼胶。取样分析:经硫化制成标准试样,并进行热稳定性测试对比试验,测试性能见表2。
36.将实施例1-4和对比例1-4制得的乙烯基含氟聚硅氧烷测试粘度、门尼黏度、乙烯基含量和收率,如表1所示。
37.表1乙烯基含氟聚硅氧烷的性能指标
由实施例1和对比例1的实验结果可以看出对比例1的外观较差,粘度不可控地升高,主要原因是本发明选用羟基封端三氟丙基甲基聚硅氧烷作为反应单体,从而避免了由于d3f与封端剂反应活性的不同而导致聚合失败。从实施例2~4与对比例2~4的结果可以看出,对比例的产品外观均微浊,这是因为本发明使用的终止剂与所得产品的相容性更好,极大地提高了产品的外观表现。
38.将实施例5和对比例5制得的氟硅混炼胶测试硬度、拉伸强度、断裂伸长率和抗撕裂强度,并测试其热稳定性(二段硫化后性能变化),如表2所示。
39.表2氟硅混炼胶的性能指标实施例5与对比例5的区别在于终止剂的不同,本发明选用的终止剂n,n-二乙基-氨丙基甲基二甲氧基硅烷和甲基三氟丙基环三硅氧烷的共水解物与产品的相容性更好,中和效果更佳,使得用该终止剂中和的硅油来制备的硅橡胶热稳定性更佳。对比例5由于中和效果不佳,中和并不完全,在二段硫化高温条件下对产品造成不可逆的损害,导致产品二段硫化后力学性能下降严重。
再多了解一些
本文用于创业者技术爱好者查询,仅供学习研究,如用于商业用途,请联系技术所有人。