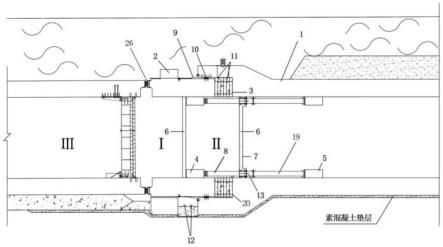
1.本发明涉及沉管隧道施工技术领域,具体涉及一种海底沉管隧道后浇带施工方法。
背景技术:
2.目前传统使用沉管隧道接头对接方案主要有止水模板法及v型块体方案。止水模板法主要是先在接头两侧管节的端部与管节同时制作焊接安设平堰板,待管节沉放完毕后,在前后两块平堰板左右两侧水中,安设一个圆形的钢围堰板,同时在衬砌的外边,用钢板把隧道内外隔开形成最终接头水下止水模板,再往围堰内灌筑水下混凝土,形成管节水下的连接。v型块体方案主要是在接头两侧相邻管节内均设置有端封墙,两侧相邻管节的两个端面设置呈双面楔形,且两个端面设置有接触面和橡胶止水带,最终接头呈双面楔形,形式v形故称为v形块体,v形最终接头块体的两侧也设置有接触面和橡胶止水带;相邻管节陈放安装完成后,通过吊装沉放预制好的v形最终接头块体与两侧管节对接止水带压紧,相邻管节与v形最终接头块体通过螺栓连接。
3.止水模板法需要进行大量水下焊接工作保证止水模板密闭,满足水下浇筑结构混凝土的需求,施工时间受水文条件影响及水下焊接作业影响大,作业时间不可控,模板焊接连接及混凝土浇筑都需要在水下进行,安全风险大,v型块体方案在施工过程中需要对两侧沉管及最终接头v形块体进行预制成楔形,安装精度不易控制,且需要4道止水带,安装控制较为复杂,尤其是运输、吊装过程中,v形块体自重小,水下吊装控制难度大、不易于操作,且由于需要在水下与两侧管节进行精准对接可能碰坏结构及止水带,对两侧已安装完成管节存在极大的施工风险。且以上两种方法由于水下对接安装过程中,模板支立难度及预制吊装安放精度不易控制,均存在最终接头对接精度控制难度大的问题。
技术实现要素:
4.本发明的目的是针对上述施工中存在的问题,提出一种海底沉管隧道后浇带施工方法。
5.为实现上述目的本发明采用的技术方案为:一种海底沉管隧道后浇带施工方法,其特征是:第一步:后浇带施工前结构安装确认外部套筒顶部阀门打开与海水连通实现顺利顶推,在外部套筒内,通过底部4台千斤顶同步将顶进节段推出,顶推轴线控制要求精度高,轴线偏差控制在1.5cm内。顶推千斤顶每台顶推力300t、油压350bar,回拉力150t、油压400bar,顶推行程为1.7m,单台千斤顶重3t 。使顶进节段端钢壳与最后一节沉管尾端gina止水带接触;外部套筒顶部进水孔直径为25cm,淹没深度为14.221m,进水能力为0.8m
³
/s,能满足最大顶推速度145mm/min;打开沉管管节最南侧的混凝土封门的人孔门进入顶进节段空腔,对顶进节段进行测量,确认顶进节段与沉管管节对接无误后方可进行下一步;在顶推千斤顶推出顶推节段时,顶底板的
其余临时止推钢支撑也被同时带出;在外部套筒内安装24道临时止推钢支撑,连接钢支撑长4.13m,具体长度需顶进节段顶推完成后确定,重量1.3t,圆管直径402mm,法兰直径600mm。通过24个扁平千斤顶锁定临时止推钢支撑,实现临时止推钢支撑与反力牛腿二的传力,扁平千斤顶顶推力:550t、油压362bar,行程40mm,具有机械锁功能600t,单台扁平千斤顶重500kg;顶推过程中潜水辅助测量,顶进节段顶推前后进行测尺、拉线测量顶进节段与最后一节沉管间距、错牙;顶推过程中潜水员在顶进节段两侧支撑梁侧墙位置就位,测量顶进节段侧墙与支撑梁侧墙间距,顶推过程中实时监测节段偏位情况;测控系统包含拉线位移计、摄像位移计、磁致位移传感器三种设备,每种设备均可独立完成高精度定位。测控系统以拉线仪为主,摄像位移计和磁致位移传感器作为校核,显示顶进节段三维姿态确保安装精度。安装过程中通过对后浇带两侧的混凝土封门进行变形及应力监测保证安装结构安全。
6.第二步:沉管隧道后浇带二次止水外部套筒进水阀关闭时,外部套筒混凝土封门压力表值为2.23bar,缓慢开启外部套筒混凝土封门处进气阀,开度为1/8圈,接合腔水由进气阀外排,排水量约0.066m
³
,接合腔内压力值由2.23bar变至0.73bar,此时接合腔内开始进气,扁平千斤顶顶板单台受力为244t,侧墙单台受力为204t,底板平均受力为171t;通过对可注浆止水带进行灌浆,完成沉管隧道后浇带二次止水;可注浆止水带材质为丁苯橡胶,密度1.16
±
0.03t/m
³
,拉伸强度≥16mpa,断裂伸长率≥400%,撕裂强度≥45n。
7.第三步:沉管隧道后浇带贯通测量顶进节段安装完成后最后一节沉管中管廊人孔打开,进行沉管隧道安装初始姿态定位偏差测量,确定沉管隧道安装偏差;待顶进节段与外部套筒封门人孔打开后,完成全线贯通;第四步:后浇带钢筋绑扎通过混凝土封门人孔门进入顶进节段空腔,后浇带的端面进行界面凿毛处理后进行后浇带钢筋绑扎,后浇带纵向钢筋主要通过两端顶进节段及外部套筒预留机械套筒进行连接,中间采用焊接固定,环向钢筋及箍筋正常进行机械连接及绑扎固定;环向钢筋最大半径为90cm,纵向预埋机械套筒连接1920个,纵向焊缝连接960个;第五步:后浇带模板支立沉管隧道后浇带模板支立采用盘扣式脚手架作为后浇带脚手架受力支撑及作业体系,局部与钢支撑冲突部位采用扣件式脚手架与盘扣式脚手架相结合的方式施作;盘扣式脚手架采用φ48.3mm型号,横杆标准步距为1.5m,立杆间距采用0.912m*0.912m,斜拉杆除避让钢支撑及人孔门位置均满布;在后浇带范围采用架体作为支撑受力体系,支撑架前方为作业平台相结合适应后浇带作业空间;顶板需要进行冲顶混凝土的泵送及钢支撑避让,模板整体受力及预埋泵管处的连接固定,充分考虑到作业人员的便捷与可操作性,进行分组散拼组合片式钢模板体系的应用,模板主梁采用双拼槽钢沿里程方向按顶托间距安放于脚手架顶托上,次梁也采用双拼槽钢沿结构宽度方向平均布设三道保证模板跨中及两侧拼缝处受力;次梁与组合片钢面板通过扣件固定;第六步:后浇带混凝土浇筑后浇带混凝土浇筑采用分层浇筑,底板与墙体进行一次浇筑至顶板加腋角处,模
板加固体系的满堂支架同时作为混凝土浇筑的作业平台;二次混凝土浇筑为顶板混凝土;在后浇带混凝土养护达到设计强度前,不得拆除临时止推钢支撑;后浇带混凝土采用如下配比:水灰比0.34砂率41%水泥335kg/m3砂子701kg/m3石子1009kg/m3用水量170kg/m3粉煤灰75kg/m3矿粉50kg/m3减水剂8.5kg/m3引气剂1.56kg/m3膨胀剂40kg/m3;达到自密实补偿收缩的工作性能:c50最后强度,p10抗渗等级,df80抗冻等级,该配合比适用于后浇带混凝土浇筑,无需振捣、混凝土流动性、粘聚性等工作性能良好,且强度增长较快,适应于后浇带支撑受力要求;在结构中间位置模板上预埋125mm冲顶混凝土泵管,综合考虑混凝土泵送影响因素管口距顶板40cm,在两个泵管之间埋设排气管保证后浇带作业腔内气体排出且为后续注浆密实留有通道;混凝土泵管上距底模板下50cm处设置一道截断式止回阀,排气管距底模板下30cm设置球阀止回;第七步:后浇带防水措施后浇带新老混凝土接缝处设置遇水膨胀止水胶与预埋式注浆管作为最后的防水措施;遇水膨胀止水胶在凿毛及水泥基涂刷完成后,需要保持基面干燥无水;涂抹厚度均匀连续达到10mm,距离结构边及注浆管控制在15cm;在后浇带顶板顶预留2根后注浆管,待顶板混凝土浇筑完成后进行灌浆充填密实保证整体结构密实;注浆从预埋式注浆管低端的注浆导管灌入浆液,使用手压加压设备将浆液向上挤压,为保证注浆效果使注浆液低压缓进;待另一端导管出浆后,封闭出浆导管,加压至0.8mpa,当压力保持5分钟无明显降低时即结束注浆。
8.所述施工方法后浇带浇筑后轴线偏差为1cm。
9.本发明采用完整详尽的整套海下顶进后浇的施工过程完成海底沉管隧道对接施工,通过沉管隧道后浇带结构体系,优化了传统沉管隧道水下作业量大、效率低、风险大、需要运输吊装操作,通过顶进节段顶推后形成后浇带作业腔,避免水下作业支立模板浇筑混凝土及接头v形块水下吊装安放的问题,仅通过20天作业时间就完成后浇带的作业形成沉管隧道最终贯通,作业期间无较大作业风险。且作业过程中及后浇带混凝土浇筑完成后基本可以做到滴水不漏。后浇带浇筑后轴线偏差为1cm,更解决对接精度控制难度大的问题。通过沉管隧道后浇带的施工过程的研究,大大简化了沉管隧道对接安装的控制难度,且后浇带结构混凝土现浇对于质量控制,施工效率也有极大的保证。
附图说明
10.图1为本发明沉管隧道后浇带结构纵断面示意图。
11.图2为本发明沉管隧道后浇带结构横断面示意图。
12.图3为本发明沉管隧道后浇带结构防水示意图。
13.图4为本发明沉管隧道后浇带施工内容示意图。
14.图中:1、外部套筒,2、顶进节段,3、后浇带结构,4、反力牛腿一,5、反力牛腿二,6、混凝土封门,7、人孔门,8、连接钢支撑,9、可伸缩止水带,10、可注浆止水带,11、后注浆管,12、底部后注浆管,13、临时止推钢支撑,14、凿毛及水泥基,15、遇水膨胀止水胶,16、预埋式注浆管,17、注浆导管,18、注浆管封口盒,19、千斤顶,20、预留机械套筒,21、套筒接驳器,22、后浇带底板钢筋,23、后浇带脚手架受力支撑及作业体系,24、组合式散拼钢模板及预埋注浆泵管体系,25、后浇带顶板钢筋,26、gina止水带,ⅰ、顶进节段空腔,ⅱ、顶进节段后浇内空腔,、最后一节沉管节段。
具体实施方式
15.下面结合附图与具体实施例对本发明进行详细说明。
实施例
16.如图1-图4所示,沉管隧道后浇带结构3位于沉管隧道顶进节段及外部套筒之间,呈全断面混凝土结构,待顶进节段2与最后一节沉管节段顶推对接后进行钢筋绑扎、混凝土浇筑及方式工程等作业。
17.第一步:后浇带施工前结构安装确认外部套筒1顶部阀门打开与海水连通实现顺利顶推,在外部套筒内,通过底部4台千斤顶19同步将顶进节段2推出,顶推轴线控制要求精度高。顶推千斤顶每台顶推力300t、油压350bar,回拉力150t、油压400bar,顶推行程为1.7m,单台千斤顶重3t 。使顶进节段端钢壳与最后一节沉管尾端gina止水带26接触;外部套筒顶部进水孔直径为25cm,淹没深度为14.221m,进水能力为0.8m
³
/s,能满足最大顶推速度145mm/min;打开沉管管节最南侧的混凝土封门6的人孔门7进入顶进节段空腔,对顶进节段进行测量,确认顶进节段与沉管管节对接无误后方可进行下一步;在顶推千斤顶推出顶推节段时,顶底板的其余临时止推钢支撑8也被同时带出;在外部套筒内安装24道临时止推钢支撑13,连接钢支撑长4.13m,重量1.3t,圆管直径402mm,法兰直径600mm。通过24个扁平千斤顶锁定临时止推钢支撑,实现临时止推钢支撑与反力牛腿一4、反力牛腿二5之间的传力,扁平千斤顶顶推力550t、油压362bar,行程40mm,具有机械锁功能600t,单台扁平千斤顶重500kg;顶推过程中潜水辅助测量,顶进节段顶推前后进行测尺、拉线测量顶进节段与最后一节沉管间距、错牙;顶推过程中潜水员在顶进节段两侧支撑梁侧墙位置就位,测量顶进节段侧墙与支撑梁侧墙间距,顶推过程中实时监测节段偏位情况;测控系统包含拉线位移计、摄像位移计、磁致位移传感器三种设备,每种设备均可独立完成高精度定位。测控系统以拉线仪为主,摄像位移计和磁致位移传感器作为校核,显示顶进节段三维姿态确保安装精度。安装过程中通过对后浇带两侧的混凝土封门进行变形及应力监测保证安装结构安全。
18.第二步:沉管隧道后浇带二次止水
减水剂8.5kg/m3引气剂1.56kg/m3膨胀剂40kg/m3;达到自密实补偿收缩的工作性能:c50最后强度,p10抗渗等级,df80抗冻等级,该配合比适用于后浇带混凝土浇筑,无需振捣、混凝土流动性、粘聚性等工作性能良好,且强度增长较快,适应于后浇带支撑受力要求;在结构中间位置模板上预埋125mm冲顶混凝土泵管,综合考虑混凝土泵送影响因素管口距顶板40cm,在两个泵管之间埋设排气管保证后浇带作业腔内气体排出且为后续注浆密实留有通道;混凝土泵管上距底模板下50cm处设置一道截断式止回阀,排气管距底模板下30cm设置球阀止回;第七步:后浇带防水措施后浇带新老混凝土接缝处设置遇水膨胀止水胶15与预埋式注浆管16作为最后的防水措施;遇水膨胀止水胶在凿毛及水泥基14涂刷完成后,需要保持基面干燥无水;涂抹厚度均匀连续达到10mm,距离结构边及注浆管控制在15cm;在后浇带顶板顶预留2根后注浆管,待顶板混凝土浇筑完成后进行灌浆充填密实保证整体结构密实;注浆从预埋式注浆管低端的注浆导管17灌入浆液,使用手压加压设备将浆液向上挤压,为保证注浆效果使注浆液低压缓进;待另一端导管出浆后,封闭出浆导管,加压至0.8mpa,当压力保持5分钟无明显降低时即结束注浆。施工过程中采用注浆管封口盒18密封避免灰浆进入,待顶板混凝土浇筑完成后进行灌浆充填密实保证整体结构密实。后浇带底部通过底部后注浆管12注浆密实。
20.本发明采用海下顶进后浇的结构形式完成海底沉管隧道的施工,待最后一个管节沉放完成,沉管隧道对接区域水下清理检查后,通过预留顶推装置将顶进节段推出,进行初始压接,然后排出管节接头隔腔内水完成水力压接;安装锁定构造,密封顶进节段空腔并排水;在顶进节段空腔内的空隙后浇带部位进行钢筋绑扎连接,模板支立,防水施工并灌注混凝土。海底沉管隧道后浇带的施工可为海底沉管隧道顶进节段正常顶进提供作业空间保证其顺利与最后一个沉管管节进行对接。并能保证沉管隧道顶进节段与沉管对接的姿态精准稳定,调整顶进节段与外部套筒的标高保证沉管隧道结构施工完成后的整体标高较少沉降差保证施工质量。
再多了解一些
本文用于创业者技术爱好者查询,仅供学习研究,如用于商业用途,请联系技术所有人。