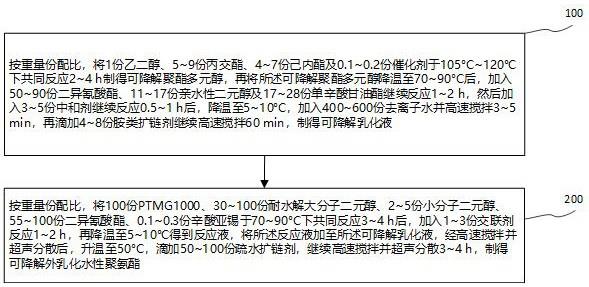
1.本发明涉及超纤革含浸领域,特别涉及一种可降解外乳化水性聚氨酯及其制备方法。
背景技术:
2.超纤革即超细纤维合成革,是超细纤维和聚氨酯构成的复合材料。传统超纤革制备工艺采用溶剂型聚氨酯含浸超细纤维无纺布,并在dmf-h2o溶液中凝固形成聚氨酯微孔,再经开纤、后整理等工艺,制备成超纤革基布,由于溶剂型聚氨酯需要使用大量溶剂dmf,对环境容易造成破坏且影响人们身体健康,逐渐被具有环保健康优势的水性聚氨酯所取代。
3.水性聚氨酯的制备方法分为外乳化法和自乳化法,其中,相关技术提供的自乳化水性聚氨酯在制备过程中加入大量亲水基团来保证其水溶性,导致其应用于超纤革含浸工艺后,超纤革的性能大幅下降;而相关技术提供的外乳化法制备所得水性聚氨酯采用小分子乳化剂,造成外乳化法水性聚氨酯性能不稳定,同样影响含浸后超纤革的性能稳定性。
技术实现要素:
4.本发明的主要目的在于提供一种可降解外乳化水性聚氨酯及其制备方法,用于解决现有水性聚氨酯应用于超纤革含浸工艺后,容易导致超纤革性能受损的技术问题。本发明的技术方案如下:根据本发明实施例的第一个方面,提供一种可降解外乳化水性聚氨酯的制备方法,所述制备方法包括:按重量份配比,将1份乙二醇、5~9份丙交酯、4~7份己内酯及0.1~0.2份催化剂于105
°
c~120
°
c下共同反应2~4 h制得可降解聚酯多元醇,再将所述可降解聚酯多元醇降温至70~90
°
c后,加入50~90份二异氰酸酯、11~17份亲水性二元醇及17~28份单辛酸甘油酯继续反应1~2 h,然后加入3~5份中和剂继续反应0.5~1 h后,降温至5~10
°
c,加入400~600份去离子水并高速搅拌3~5 min,再滴加4~8份胺类扩链剂继续高速搅拌60 min,制得可降解乳化液;按重量份配比,将100份ptmg1000、30~100份耐水解大分子二元醇、2~5份小分子二元醇、55~100份二异氰酸酯、0.1~0.3份辛酸亚锡于70~90
°
c下共同反应3~4 h后,加入1~3份交联剂反应1~2 h,再降温至5~10
°
c得到反应液,将所述反应液加至所述可降解乳化液,经高速搅拌并超声分散后,升温至50
°
c,滴加50~100份疏水扩链剂,继续高速搅拌并超声分散3~4 h,制得可降解外乳化水性聚氨酯。
5.优选的,所述催化剂为辛酸亚锡、氧化锌、氯化亚锡中的至少一种。
6.优选的,所述二异氰酸酯是异佛尔酮二异氰酸酯ipdi、1,6-己二异氰酸酯hdi、甲苯二异氰酸酯tdi、二环己基甲烷-4,4
’‑
二异氰酸酯(hmdi)中的至少一种;所述亲水性二元醇为二羟甲基丙酸、二羟甲基丁酸中的至少一种。
7.优选的,所述中和剂为氢氧化钾、氢氧化钠中的至少一种;所述胺类扩链剂为乙二
胺、二乙烯三胺、三亚乙基四胺中的至少一种。
8.优选的,所述耐水解大分子二元醇为聚环氧丙烷多元醇ppg、聚乙二醇peg、聚碳酸酯多元醇pcdl中的至少一种,所述耐水解大分子二元醇的数均分子量为500~2000。
9.优选的,所述小分子二元醇为乙二醇、1,4-丁二醇、2-甲基-1,3丙二醇、一缩二乙二醇、1,6-己二醇中的至少一种。
10.优选的,所述交联剂为三羟甲基丙烷、甘油中的至少一种。
11.优选的,所述疏水扩链剂为ptmg650、pcl500中的至少一种。
12.优选的,高速搅拌工序采用的转速为4000~5000 r/min。
13.根据本发明实施例的第二个方面,提供一种可降解外乳化水性聚氨酯,所述可降解外乳化水性聚氨酯由上述任意一项所述可降解外乳化水性聚氨酯的制备方法制备得到。
14.与现有技术相比,本发明提供的一种可降解外乳化水性聚氨酯及其制备方法具有以下优点:本发明提供的可降解外乳化水性聚氨酯及其制备方法,通过工艺设计的创新,首先制备高温强碱下可降解的乳化液,再将其作为外乳化剂应用于无亲水基团水性聚氨酯合成,制得可降解外乳化水性聚氨酯,其应用于超纤革含浸工艺后,可利用超纤革开纤工艺的高温强碱环境将乳化剂降解成为小分子并水洗去除,使得超纤革用水性聚氨酯薄膜中亲水基团降低,达到保护超纤维自身性能同时,提高其耐高温强碱性、降低吸水性且无三乙胺释放的技术效果。与此同时,整个合成过程不添加丙酮,更具有环保性。
附图说明
15.此处的附图被并入说明书中并构成本说明书的一部分,示出了符合本发明的实施例,并于说明书一起用于解释本发明的原理。
16.图1是一种可降解外乳化水性聚氨酯的制备方法的制备流程图。
17.图2是本发明实施例1中可降解乳化液的合成示意图。
18.图3是本发明实施例1中含浸固化后所得聚氨酯薄膜碱减量开纤过程中降解示意图。
19.图4是本发明实施例1中含浸可降解外乳化水性聚氨酯固化后定岛型超细纤维无纺布表面扫描电镜图。
20.图5是本发明实施例1制备的超纤革表面扫描电镜图。
具体实施方式
21.为了更清楚地说明本发明实施例中的技术方案,下面将对实施例描述中所需要使用的附图作简单地介绍,显而易见地,下面描述中的附图仅仅是本发明的一些实施例,对于本领域普通技术人员来讲,在不付出创造性劳动的前提下,还可以根据这些附图获得其他的附图。
22.为了便于理解本发明的技术效果,首先对现有自乳化水性聚氨酯应用于超纤革含浸工艺的缺陷进行说明:现有自乳化水性聚氨酯的制备工艺导致其产品往往含有大量亲水基团,且在超纤革含浸及后处理应用过程中无法脱除,造成超纤革性能大幅下降,导致超纤革具有以下具
体缺陷:(1)耐高温强碱性差:自乳化水性聚氨酯本身含有大量亲水基团,在高温强碱环境下,极易溶胀或降解,造成聚氨酯薄膜性能下降,难以应用于超纤革碱减量开纤工艺。
23.(2)绒感较差:自乳化水性聚氨酯本身含有大量的亲水基团,其库仑力和氢键作用较强,造成断裂伸长率降低,影响超纤革的绒感。
24.(3)吸水率过高:自乳化水性聚氨酯本身含有大量的亲水基团,使用过程中吸水率过高,造成超纤革性能下降。
25.(4)三乙胺挥发具有毒性:制备自乳化水性聚氨酯一般使用三乙胺对羧基进行中和,在自乳化水性聚氨酯固化成膜过程中,具有毒性的三乙胺挥发,即对环境造成污染,对人体造成危害。
26.(5)含有丙酮:自乳化水性聚氨酯合成过程中,一般加入一定量的丙酮使其粘度降低,增加工艺稳定性。但难以避免丙酮的挥发,造成环境污染。
27.为了避免上述缺陷,本发明提供了一种可降解外乳化水性聚氨酯的制备方法,该可降解外乳化水性聚氨酯的制备方法的制备流程图如图1所示,包括:步骤100:按重量份配比,将1份乙二醇、5~9份丙交酯、4~7份己内酯及0.1~0.2份催化剂于105
°
c~120
°
c下共同反应2~4 h制得可降解聚酯多元醇,再将所述可降解聚酯多元醇降温至70~90
°
c后,加入50~90份二异氰酸酯、11~17份亲水性二元醇及17~28份单辛酸甘油酯继续反应1~2 h,然后加入3~5份中和剂继续反应0.5~1 h后,降温至5~10
°
c,加入400~600份去离子水并高速搅拌3~5 min,再滴加4~8份胺类扩链剂继续高速搅拌60 min,制得可降解乳化液。
28.需要说明的是,本发明所用二元醇在使用前,均于110~130
°
c下抽真空脱水1~3 h进行前处理,使得二元醇含水率小于0.02%,抽真空工序采用的真空度为-0.08~-0.10 mpa。
29.优选的,所述催化剂为辛酸亚锡、氧化锌、氯化亚锡中的至少一种。
30.优选的,所述二异氰酸酯是异佛尔酮二异氰酸酯ipdi、1,6-己二异氰酸酯hdi、甲苯二异氰酸酯tdi、二环己基甲烷-4,4
’‑
二异氰酸酯(hmdi)中的至少一种;所述亲水性二元醇为二羟甲基丙酸、二羟甲基丁酸中的至少一种。
31.优选的,所述中和剂为氢氧化钾、氢氧化钠中的至少一种;所述胺类扩链剂为乙二胺、二乙烯三胺、三亚乙基四胺中的至少一种。
32.步骤200:按重量份配比,将100份ptmg1000、30~100份耐水解大分子二元醇、2~5份小分子二元醇、55~100份二异氰酸酯、0.1~0.3份辛酸亚锡于70~90
°
c下共同反应3~4 h后,加入1~3份交联剂反应1~2 h,再降温至5~10
°
c得到反应液,将所述反应液加至所述可降解乳化液,经高速搅拌并超声分散后,升温至50
°
c,滴加50~100份疏水扩链剂,继续高速搅拌并超声分散3~4 h,制得可降解外乳化水性聚氨酯。
33.优选的,所述耐水解大分子二元醇为聚环氧丙烷多元醇ppg、聚乙二醇peg、聚碳酸酯多元醇pcdl中的至少一种,所述耐水解大分子二元醇的数均分子量为500~2000。
34.优选的,所述小分子二元醇为乙二醇、1,4-丁二醇、2-甲基-1,3丙二醇、一缩二乙二醇、1,6-己二醇中的至少一种。
35.优选的,所述交联剂为三羟甲基丙烷、甘油中的至少一种。
36.优选的,所述疏水扩链剂为ptmg650、pcl500中的至少一种。
37.优选的,高速搅拌工序采用的转速为4000~5000 r/min。
38.为了便于理解本发明所提供可降解外乳化水性聚氨酯的优点,示出一种可降解外乳化水性聚氨酯在超纤革制备工艺中的示例性应用流程说明:(1)将涤纶与碱溶性聚酯共混制得的定岛型超细纤维无纺布,所述定岛型超细纤维无纺布中海相:岛相=3:7,克重为380 g/m2,厚度1.8 mm。
39.(2)将定岛型超细纤维无纺布采用槽体式含浸工艺进行含浸,调节含浸液中可降解外乳化水性聚氨酯的浓度为15%,压辊压力3 mpa,浸渍温度50
°
c,浸渍3 min后烘干固化。
40.(3)将含浸固化后的定岛型超细纤维无纺布置于入10% naoh溶液,于80
°
c开纤120 min,再升温至95
°
c开纤60 min,使所述定岛型超细纤维无纺布内可降解乳化剂完全降解为小分子。
41.(4)将开纤后所述定岛型超细纤维无纺布用50
°
c去离子水水洗60 min,水洗三次,使降解的小分子完全去除,再经干燥、片皮、磨面、染色、干法贴面、改色、压花、表处和揉纹等后处理工艺制备得到超纤革。
42.需要说明的是,本发明通过合成含有丙交酯及己内酯的二元醇,丙交酯及己内酯同时引入是为了防止单一丙交酯或者己内酯存在结晶链段而难以降解,使其于高温强碱环境下可降解;合成可降解乳化剂过程中加入亲水小分子,从而使其能在水中乳化;合成可降解乳化剂过程中加入单辛酸甘油酯,主要是聚氨酯后期扩链环境为疏水环境,添加单辛酸甘油酯有利于创造疏水环境。聚氨酯的后期扩链采用疏水性扩链剂,主要是聚氨酯后期扩链环境为疏水环境,因此疏水性扩链剂效果更好。
43.经测试,本发明制备所得可降解外乳化水性聚氨酯的储存稳定性≥6个月,应用于超纤革含浸工艺后所形成聚氨酯薄膜的拉伸强度较高(7.7~8.3 mpa),断裂伸长率较低(110%~140%),耐高温强碱性良好,特别适用于超纤革碱减量开纤工艺,且聚氨酯薄膜经过碱减量开纤工艺后吸水率大幅下降(≤2%),断裂伸长率提高(210%~260%);通过本发明所提供可降解外乳化水性聚氨酯制备的超纤革柔软度较好(9.6~11.4 mm),拉伸强度(经向)较好(15.6~16.9 mpa),拉伸强度(纬向)/ 较好(14.4~15.5 mpa),撕裂负荷(经向)较好(55.3-61.3 n/mm),撕裂负荷(纬向)较好(54.3-59.5 n/mm),绒感较好。
44.为了更好地说明本发明提供的一种可降解外乳化水性聚氨酯及其制备方法所带来的有益效果,示出下述实施例1、2、3进行说明:实施例1第一步:按重量份配比,将1份乙二醇、5份丙交酯、4份己内酯及0.1份辛酸亚锡于105
°
c下共同反应2 h制得可降解聚酯多元醇,再将所述可降解聚酯多元醇降温至70
°
c后,加入50份ipdi、11份二羟甲基丙酸及17份单辛酸甘油酯继续反应1h,然后加入3份氢氧化钠继续反应0.5 h后,降温至5
°
c,加入400份去离子水并高速搅拌3 min,再滴加4份乙二胺继续高速搅拌60 min,制得可降解乳化液。
45.第二步:按重量份配比,将100份ptmg1000、30份ptmg1000、2份乙二醇、55份ipdi、0.1份辛酸亚锡于70
°
c下共同反应3 h后,加入1份三羟甲基丙烷反应1 h,再降温至5
°
c得到反应液,将所述反应液加至所述可降解乳化液,经高速搅拌并超声分散后,升温至50
°
c,滴加50份ptmg650,继续高速搅拌并超声分散3h,制得可降解外乳化水性聚氨酯。
46.第三步:将涤纶与碱溶性聚酯共混制得的定岛型超细纤维无纺布,所述定岛型超
细纤维无纺布中海相:岛相=3:7,克重为380 g/m2,厚度1.8 mm。将定岛型超细纤维无纺布采用槽体式含浸工艺进行含浸,调节含浸液中可降解外乳化水性聚氨酯的浓度为15%,压辊压力3 mpa,浸渍温度50
°
c,浸渍3 min后烘干固化;将含浸后的定岛型超细纤维无纺布置于入10% naoh溶液,于80
°
c开纤120 min,再升温至95
°
c开纤60 min,使所述定岛型超细纤维无纺布内可降解乳化剂完全降解为小分子。将开纤后所述定岛型超细纤维无纺布用50
°
c去离子水水洗60 min,水洗三次,使降解的小分子完全去除,再经干燥、片皮、磨面、染色、干法贴面、改色、压花、表处和揉纹等后处理工艺制备得到超纤革。
47.示例性的,本发明实施例1中可降解乳化液的合成示意图如图2所示。
48.示例性的,本发明实施例1中含浸固化后所得聚氨酯薄膜碱减量开纤过程中降解示意图如图3所示。
49.示例性的,本发明实施例1中含浸可降解外乳化水性聚氨酯固化后定岛型超细纤维无纺布表面扫描电镜图如图4所示。
50.示例性的,本发明实施例1制备的超纤革表面扫描电镜图如图5所示。
51.实施例2第一步:按重量份配比,将1份乙二醇、6份丙交酯、4份己内酯及0.1份催化剂于110
°
c下共同反应3h制得可降解聚酯多元醇,再将所述可降解聚酯多元醇降温至80
°
c后,加入65份ipdi、13份二羟甲基丙酸及21份单辛酸甘油酯继续反应1.5 h,然后加入4份氢氧化钠继续反应0.8 h后,降温至8
°
c,加入500份去离子水并高速搅拌4 min,再滴加5份乙二胺继续高速搅拌60 min,制得可降解乳化液。
52.第二步:按重量份配比,将100份ptmg1000、50份ptmg1000、3份乙二醇、70份ipdi、0.2份辛酸亚锡于80
°
c下共同反应3.5h后,加入2份三羟甲基丙烷反应1.5 h,再降温至8
°
c得到反应液,将所述反应液加至所述可降解乳化液,经高速搅拌并超声分散后,升温至50
°
c,滴加70份ptmg650,继续高速搅拌并超声分散3.5 h,制得可降解外乳化水性聚氨酯。
53.第三步:将涤纶与碱溶性聚酯共混制得的定岛型超细纤维无纺布,所述定岛型超细纤维无纺布中海相:岛相=3:7,克重为380 g/m2,厚度1.8 mm。将定岛型超细纤维无纺布采用槽体式含浸工艺进行含浸,调节含浸液中可降解外乳化水性聚氨酯的浓度为15%,压辊压力3 mpa,浸渍温度50
°
c,浸渍3 min后烘干固化;将含浸固化后的定岛型超细纤维无纺布置于入10% naoh溶液,于80
°
c开纤120 min,再升温至95
°
c开纤60 min,使所述定岛型超细纤维无纺布内可降解乳化剂完全降解为小分子。将开纤后所述定岛型超细纤维无纺布用50
°
c去离子水水洗60 min,水洗三次,使降解的小分子完全去除,再经干燥、片皮、磨面、染色、干法贴面、改色、压花、表处和揉纹等后处理工艺制备得到超纤革。
54.实施例3第一步:按重量份配比,将1份乙二醇、9份丙交酯、7份己内酯及0.2份辛酸亚锡于120
°
c下共同反应4 h制得可降解聚酯多元醇,再将所述可降解聚酯多元醇降温至90
°
c后,加入90份ipdi、17份二羟甲基丙酸及28份单辛酸甘油酯继续反应2 h,然后加入5份氢氧化钠继续反应1 h后,降温至10
°
c,加入600份去离子水并高速搅拌5 min,再滴加8份乙二胺继续高速搅拌60 min,制得可降解乳化液。
55.第二步:按重量份配比,将100份ptmg1000、100份ptmg1000、5份乙二醇、100份ipdi、0.3份辛酸亚锡于90
°
c下共同反应4 h后,加入3份三羟甲基丙烷反应1~2 h,再降温至
10
°
c得到反应液,将所述反应液加至所述可降解乳化液,经高速搅拌并超声分散后,升温至50
°
c,滴加100份ptmg650,继续高速搅拌并超声分散3~4 h,制得可降解外乳化水性聚氨酯。
56.第三步:将涤纶与碱溶性聚酯共混制得的定岛型超细纤维无纺布,所述定岛型超细纤维无纺布中海相:岛相=3:7,克重为380 g/m2,厚度1.8 mm。将定岛型超细纤维无纺布采用槽体式含浸工艺进行含浸,调节含浸液中可降解外乳化水性聚氨酯的浓度为15%,压辊压力3 mpa,浸渍温度50
°
c,浸渍3 min后烘干固化;将含浸固化后的定岛型超细纤维无纺布置于入10% naoh溶液,于80
°
c开纤120 min,再升温至95
°
c开纤60 min,使所述定岛型超细纤维无纺布内可降解乳化剂完全降解为小分子。将开纤后所述定岛型超细纤维无纺布用50
°
c去离子水水洗60 min,水洗三次,使降解的小分子完全去除,再经干燥、片皮、磨面、染色、干法贴面、改色、压花、表处和揉纹等后处理工艺制备得到超纤革。
57.对比例1本对比例采用与实施例1相似的配方和方法合成可降解外乳化水性聚氨酯,区别在于:不添加单辛酸甘油酯。
58.单辛酸甘油酯的缺失导致产品后期难以进行乳液聚合,主要是聚氨酯后期扩链环境为疏水环境,添加单辛酸甘油酯有利于创造疏水环境。
59.对比例2本对比例采用与实施例1相似的配方和方法合成可降解外乳化水性聚氨酯,区别在于:采用亲水性扩链剂乙二胺取代疏水性扩链剂ptmg650。
60.乳液聚合后的可降解外乳化水性聚氨酯性能大幅下降,主要是聚氨酯后期扩链环境为疏水环境,因此疏水性扩链剂效果更好。
61.将实施例1、2、3合成的可降解外乳化水性聚氨酯及对应超纤革按照如下标准进行测试,具体测试结果见表1、表2及表3。
62.其中,采用的测试标准为:可降解外乳化水性聚氨酯测定标准储存稳定性测定:观察乳液有无沉淀、分层现象,记录乳液的稳定时间。
63.拉伸强度及断裂伸长率:按照gb/t1040-92的测试标准。
64.吸水率:将50 g水性聚氨酯固化形成涂膜,裁剪成5 cm
×
5 cm的方块形状,室温下称其质量为m0,然后将其放入去离子水中浸泡24 h后取出,用滤纸将涂膜表面的水分吸收后称其质量为m,吸水率由以下公式计算得到:(m﹣m0)/m0×
100%。
65.经过碱减量开纤后可降解外乳化水性聚氨酯薄膜性能碱减量开纤工艺:将可降解外乳化水性聚氨酯薄膜用10% naoh溶液于80
°
c反应120 min,再升温至95
°
c反应60 min,使可降解乳化剂完全降解。用50
°
c水进行水洗60 min,水洗三次,使降解的小分子完全去除,再烘干。
66.测定经过碱减量开纤后可降解外乳化水性聚氨酯薄膜拉伸强度、断裂伸长率及吸水率。
67.超纤革性能测定标准柔软度:按照iso 17235-2002的测试标准。
68.拉伸强度及断裂伸长率:按照qb/t 2710-2018的测试标准。
69.撕裂负荷:按照gb/t 3917.2-2009的测试标准。
70.绒感:根据预设数量体验用户对目标超纤革的体感评价。
71.表1 可降解外乳化水性聚氨酯薄膜性能项目实施例1实施例2实施例3储存稳定性/月≥6≥6≥6拉伸强度/mpa8.3
±
0.57.9
±
0.37.7
±
0.3断裂伸长率/0
±
10130
±
10140
±
15吸水率16.75.75 .76%表2可降解外乳化水性聚氨酯薄膜经过碱减量开纤后的性能项目实施例1实施例2实施例3拉伸强度/mpa7.9
±
0.47.5
±
0.37.3
±
0.2断裂伸长率/!0
±
20250
±
20260
±
25吸水率1.23%1.56%1.63%表3超纤革的性能项目实施例1实施例2实施例3柔软度/mm9.610.711.4拉伸强度(经向)/mpa15.6
±
1.416.5
±
1.316.9
±
1.4拉伸强度(纬向)/mpa14.4
±
1.515.2
±
1.415.5
±
1.3撕裂负荷(经向)/(n)55.3
±
2.158.5
±
2.561.3
±
2.9撕裂负荷(纬向)/(n)54.3
±
2.557.2
±
2.759.5
±
2.4断裂伸长率(经向)/0
±
10132
±
9129
±
11断裂伸长率(纬向)/2
±
8126
±
7121
±
9绒感良好良好良好通过表1的结果可以看出,采用本发明制得可降解外乳化水性聚氨酯的储存稳定性≥6个月,聚氨酯薄膜吸水率较高(16.75%~20.76%),聚氨酯薄膜拉伸强度较高(7.7~8.3 mpa),聚氨酯薄膜断裂伸长率较低(110%~140%)。
72.通过表2的结果可以得出,采用本发明制得可降解外乳化水性聚氨酯薄膜耐高温强碱性良好,特别适用于超纤革碱减量开纤工艺。经过碱减量开纤后聚氨酯薄膜吸水率大幅下降(≤2%),聚氨酯薄膜断裂伸长率提高(210%~260%)。
73.通过表3的结果可以看出,由本发明的超纤革用水性聚氨酯制备得到的超纤革柔软度较好(9.6~11.4 mm),拉伸强度(经向)较好(15.6~16.9 mpa),拉伸强度(纬向)/较好(14.4~15.5 mpa),撕裂负荷(经向)较好(55.3-61.3 n/mm),撕裂负荷(纬向)较好(54.3-59.5 n/mm),且绒感较好。
74.综上所述,本发明提供的可降解外乳化水性聚氨酯及其制备方法,通过工艺设计的创新,首先制备高温强碱下可降解的乳化液,再将其作为外乳化剂应用于无亲水基团水性聚氨酯合成,制得可降解外乳化水性聚氨酯,其应用于超纤革含浸工艺后,可利用超纤革开纤工艺的高温强碱环境将乳化剂降解成为小分子并水洗去除,使得超纤革用水性聚氨酯薄膜中亲水基团降低,达到保护超纤维自身性能同时,提高其耐高温强碱性、降低吸水性的技术效果。
75.虽然,前文已经用一般性说明、具体实施方式及试验,对本发明做了详尽的描述,但在本发明基础上,可以对之进行修改或改进,这对本领域技术人员而言是显而易见的。因此,在不偏离本发明精神的基础上所做的这些修改或改进,均属于本发明要求保护的范围。
76.本领域技术人员在考虑说明书及实践这里的发明的后,将容易想到本发明的其它实施方案。本发明旨在涵盖本发明的任何变型、用途或者适应性变化,这些变型、用途或者适应性变化遵循本发明的一般性原理并包括本发明未公开的本技术领域中的公知常识或惯用技术手段。应当理解的是,本发明并不局限于上面已经描述并在附图中示出的精确结构,并且可以在不脱离其范围进行各种修改和改变。
再多了解一些
本文用于创业者技术爱好者查询,仅供学习研究,如用于商业用途,请联系技术所有人。