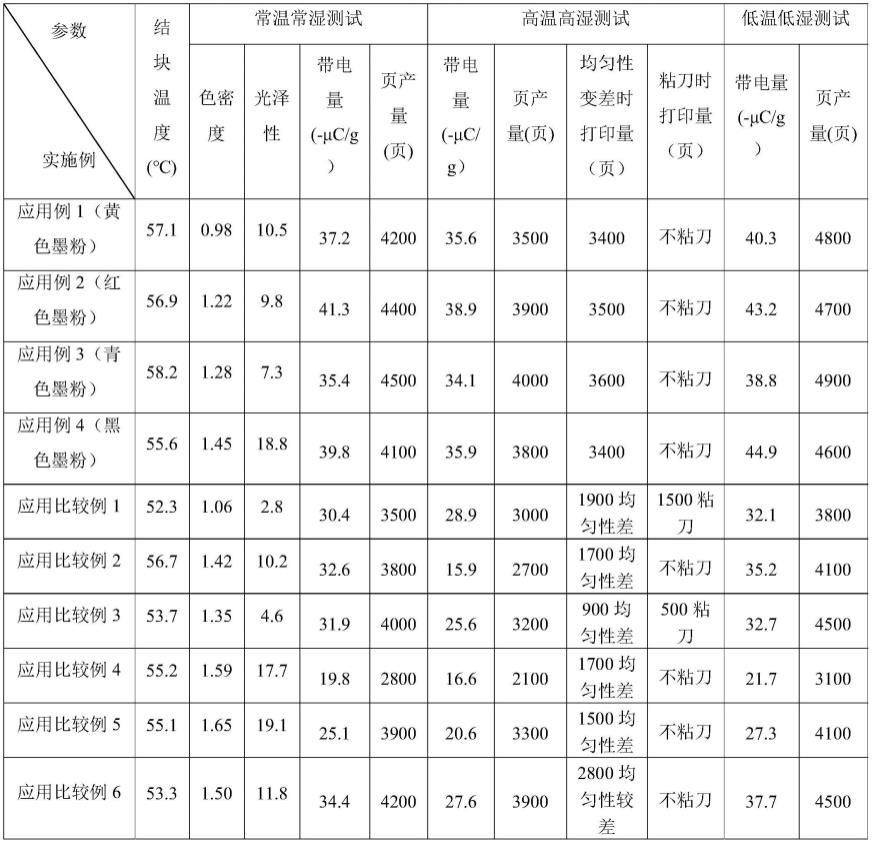
1.本发明属于激光打印机、复印机墨粉领域,涉及一种复合材料及其制备方法和在墨粉中作为添加剂的用途。
背景技术:
2.物理法墨粉是把粘结树脂、着色剂及其他内部添加剂进行熔融混炼,冷却压片形成片料后,再经过粉碎、分级,最后通过高速混合外部添加剂而得到的干式墨粉。与化学法墨粉相比,具有生产工艺成熟、生产批次稳定、无废液废渣、准入门槛低,从而具有很好的环境和成本优势以及良好的普及性。随着彩色激光打印机的普及,市场迫切需要一种打印品质接近或者超过化学法墨粉,但成本更低,生产更加安全的物理法彩色墨粉,而对于物理法彩色墨粉的光泽性、耐久性和耗粉量上的表现始终和化学法墨粉存在较大的差距,成为制约物理法彩色墨粉发展的瓶颈之一。目前针对光泽性的提高手段主要集中于对墨粉粘接树脂的优化改性上,但由于苯丙类树脂的熔点偏高,流动性偏低,导致其光泽性较差,因此基于苯丙类树脂墨粉提高光泽性的报道很少;研究主要集中于基于聚酯树脂的交联改性上,例如已授权专利cn108351609b和已公开专利cn107250919a,但是聚酯树脂相比苯丙类树脂而言,也有很多缺点,例如普遍存在环境适应性差,耐久性不足,容易粘刀,粘弹性高导致粉碎效率低下等问题。
3.从物理法彩色墨粉自身、特别是墨粉中的各种添加剂的角度分析,存在以下问题:
4.对于墨粉用内部添加剂而言,目前的内部添加剂之间缺乏必要的化学键合,且内部添加剂的粒径普遍处于微米或亚微米级,从而导致内部添加剂在树脂中的分散性能不够理想,尤其是酯蜡和苯丙类树脂内在的不相容性,会导致酯蜡在树脂中的分散性能变差,同时,酯蜡的分散粒径通常较大(微米级),最终导致墨粉的光泽性不高,不能满足彩色激光打印墨粉对光泽性的要求;此外,在长时间或高温存储过程中大尺寸的酯蜡具有更大的动能和界面作用力,从而更容易迁移到墨粉的表面,影响墨粉的荷电性能,且容易导致打印过程中粘出粉刮刀,产生纵向白线状的打印缺陷。
5.对于墨粉用外部添加剂而言,除了经常用到的小颗粒气相二氧化硅(原生粒径7nm~14nm)提供带电性能和流动性外,还需要辅助使用中大颗粒二氧化硅才能满足打印耐久性(即保持性,稿面均匀性)的要求。然而,这些中大颗粒硅(原生粒径≥16nm)由于比表面积显著减小,导致其电荷密度普遍较低,过多使用会导致墨粉的带电量明显下降,耗粉量升高,而用量不足时,墨粉的耐久性又会变差,尤其是在打印后期稿面均匀性变差,图案色彩分布不均匀,产生色差,此外,这些中大颗粒硅的成本普遍偏高,进一步提高了物理法彩色墨粉的制造成本。
技术实现要素:
6.基于现有技术中存在的不足,本发明提供了一种复合材料,其作为添加剂用于墨粉中,能够显著提高墨粉的光泽性、存储稳定性,并解决粘刀问题;还能够提高墨粉的带电
量,降低耗粉,改善墨粉的保持性,降低制造成本。
7.具体的,本发明提供如下技术方案:
8.一种复合材料,所述复合材料为二氧化硅包覆的蜡纳米粒子。
9.根据本发明的实施方案,所述二氧化硅包覆的蜡纳米粒子中,所述二氧化硅与所述蜡纳米粒子之间通过化学键连接,记为第一复合材料;或者,所述二氧化硅与所述蜡纳米粒子之间没有化学键,记为第二复合材料。
10.根据本发明的实施方案,所述二氧化硅对蜡纳米粒子的包覆率为80%~200%。
11.根据本发明的实施方案,所述蜡纳米粒子和二氧化硅的质量比为100:(10~300)。具体的,所述第一复合材料中,所述蜡纳米粒子和二氧化硅的质量比为100:(10~40),再例如为100:(20~40);所述第二复合材料中,所述蜡纳米粒子和二氧化硅的质量比为100:(50~300),还例如为100:(50~150),再例如为100:(50~100)。
12.根据本发明的实施方案,所述第二复合材料中,所述二氧化硅为气相二氧化硅。
13.根据本发明的实施方案,所述蜡纳米粒子中的蜡选自熔程在50℃~95℃的蜡。
14.根据本发明的实施方案,所述蜡纳米粒子中的蜡选自下述蜡中的至少一种,或由下述蜡中的至少一种经过共聚和/或改性的蜡:石蜡,精蜡,低密度聚烯烃蜡,米糠蜡,沙索蜡,费托蜡,酯蜡中的至少一种。
15.根据本发明的实施方案,所述蜡纳米粒子的平均粒径为50nm~250nm。
16.本发明还提供一种上述复合材料的应用,其作为墨粉中的添加剂使用。
17.根据本发明的实施方案,所述墨粉为彩色墨粉,具体的为物理法彩色墨粉或化学法彩色墨粉。
18.根据本发明的实施方案,所述第一复合材料在所述墨粉中作为内部添加剂使用,所述第二复合材料在所述墨粉中作为外部添加剂使用。
19.本发明还提供一种墨粉,所述墨粉包括添加剂,所述添加剂中包括上述的复合材料。
20.根据本发明的实施方案,所述墨粉为彩色墨粉;具体的,所述墨粉为物理法彩色墨粉,或者为化学法彩色墨粉。
21.根据本发明的实施方案,所述墨粉包括内部添加剂和外部添加剂;所述内部添加剂包括上述的第一复合材料;所述外部添加剂包括上述的第二复合材料。
22.根据本发明的实施方案,所述墨粉中,所述第一复合材料和第二复合材料的质量比为100:(5~20)。
23.本发明还提供一种上述墨粉的制备方法,所述制备方法为干式物理法,通过将所述复合材料与其他组分混合后,通过熔融混炼、挤出压片、粉碎分级、混合外部添加剂而得到所述墨粉。
24.根据本发明的实施方案,所述制备方法具体包括以下步骤:
25.a)预混合:将配方比例的粘结树脂、第一复合材料、颜料和电荷控制剂经过预混合后,得到混合物;
26.b)熔融混炼:将步骤a)得到的混合物熔融混炼后,挤出、冷却、压片,并经粗破碎得到粗颗粒;
27.c)连续粉碎-分级:将步骤b)得到的粗颗粒,经过连续粉碎和分级,得到墨粉分级
品;
28.d)混合外部添加剂:将步骤c)得到的墨粉分级品和第二复合材料先进行低速混合,再加入其他外部添加剂进行高速混合,得到所述墨粉。
29.与现有技术相比,本发明具有如下有益效果:
30.采用本发明的第一复合材料作为物理法彩色墨粉的内部添加剂时,能够显著提高墨粉的光泽性、存储稳定性,并解决粘刀问题;采用本发明的第二复合材料作为物理法彩色墨粉的外部添加剂时,能够进一步提高墨粉的带电量,降低耗粉,同时能够替代大颗粒硅,改善墨粉的保持性,降低制造成本。
31.本发明的复合材料的制备方法简单,条件可控,生产设备成熟,适合工业化生产,并具有良好的通用性。
具体实施方式
32.[复合材料]
[0033]
一种复合材料,所述复合材料为二氧化硅包覆的蜡纳米粒子。
[0034]
根据本发明的实施方案,所述二氧化硅包覆的蜡纳米粒子中,所述二氧化硅与所述蜡纳米粒子之间通过化学键连接,记为第一复合材料;或者,所述二氧化硅与所述蜡纳米粒子之间没有化学键,记为第二复合材料。
[0035]
根据本发明的实施方案,第一复合材料中,所述二氧化硅通过原位化学反应的方式包覆在所述蜡纳米粒子的表面。
[0036]
根据本发明的实施方案,第二复合材料中,所述二氧化硅通过物理共混的方式包覆在所述蜡纳米粒子的表面。
[0037]
根据本发明的实施方案,所述二氧化硅对蜡纳米粒子的包覆率为80%~200%,优选为100%~150%。
[0038]
根据本发明的实施方案,所述蜡纳米粒子和二氧化硅的质量比为100:(10~300)。具体的,所述第一复合材料中,所述蜡纳米粒子和二氧化硅的质量比为100:(10~40),再例如为100:(20~40);所述第二复合材料中,所述蜡纳米粒子和二氧化硅的质量比为100:(50~300),还例如为100:(50~150),再例如为100:(50~100)。
[0039]
根据本发明的实施方案,所述蜡纳米粒子中的蜡选自熔程在50℃~95℃的蜡。
[0040]
根据本发明的实施方案,所述蜡纳米粒子中的蜡选自下述蜡中的至少一种,或由下述蜡中的至少一种经过共聚和/或改性的蜡:石蜡,精蜡,低密度聚烯烃蜡,米糠蜡,沙索蜡,费托蜡,酯蜡中的至少一种。
[0041]
优选地,所述酯蜡选自合成酯蜡和/或天然酯蜡。示例性地,所述合成酯蜡例如包括单酯蜡(例如日油we-2,we-3)、多元醇酯蜡(例如日油we-5,we-15)、等中的至少一种。示例性地,所述天然酯蜡选自巴西棕榈蜡(例如t-1,t-3)等中的至少一种。
[0042]
根据本发明的实施方案,所述蜡纳米粒子的平均粒径为50nm~250nm,例如为50nm、100nm、150nm、200nm、250nm。
[0043]
根据本发明的实施方案,所述蜡纳米粒子通过水入蜡相反转工艺制备得到。
[0044]
具体地,所述水入蜡相反转工艺包括:将所述蜡加热融化后,加入乳化剂混合,加入超纯水乳化分散,得到蜡分散液;将所述蜡分散液离心分离得到所述蜡纳米粒子。
[0045]
根据本发明的实施方案,所述第一复合材料中,二氧化硅可通过如下方法得到:
[0046]
硅源在分散稳定剂和引发剂存在的条件下采用界面水解缩聚工艺得到所述二氧化硅。
[0047]
根据本发明的实施方案,所述硅源选自四乙氧基硅烷(teos)、硅酸钠、四氯化硅、四氟化硅。
[0048]
根据本发明的实施方案,所述分散稳定剂为聚乙烯亚胺(pei)。
[0049]
根据本发明的实施方案,所述引发剂选自γ-氨丙基三乙氧基硅烷(aptes)、双-[(三乙氧基硅烷基)-丙基]二硫化物(tespd)。
[0050]
根据本发明的实施方案,所述第二复合材料中,二氧化硅可通过如下方法得到:
[0051]
将气相二氧化硅经过至少一种下述处理剂进行表面改性得到所述二氧化硅:聚二甲基硅氧烷(pdms)、二甲基二氯硅烷(dds)和六甲基二硅氮烷(hmds)。
[0052]
根据本发明的实施方案,所述气相二氧化硅为疏水性二氧化硅。优选地,所述气相二氧化硅优选经过至少一种下述处理剂进行表面改性:聚二甲基硅氧烷(pdms)、二甲基二氯硅烷(dds)和六甲基二硅氮烷(hmds)。
[0053]
根据本发明的实施方案,所述气相二氧化硅的平均粒径为7nm~14nm,例如为7nm、8nm、9nm、10nm、11nm、12nm、13nm、14nm。示例性地,经pdms处理的二氧化硅例如为德固赛ry300、r202、ry200l,卡博特tg-7180中的至少一种。示例性地,经dds处理的二氧化硅例如为德固赛r972、德山化工reolosil dm-10等中的至少一种。示例性地,经hmds处理的二氧化硅例如为德固赛r812s、rx300、r8200,卡博特tg-811f,瓦克h2000t、h3004、h20tm、h30tm,德山化工hm-30st、zd-30st等中的至少一种。
[0054]
[第一复合材料]
[0055]
如前所述,本发明公开了一种第一复合材料,其可以作为墨粉的内部添加剂使用。
[0056]
根据本发明的实施方案,所述第一复合材料中,二氧化硅优选通过原位化学反应(水解缩聚)包覆在所述蜡纳米粒子的表面,且所述二氧化硅与所述蜡纳米粒子之间通过化学键连接。
[0057]
根据本发明的实施方案,将所述蜡纳米粒子和硅源混合后,硅源在分散稳定剂和引发剂存在的条件下得到所述二氧化硅,所述二氧化硅通过原位化学反应包覆在所述蜡纳米粒子的表面得到所述二氧化硅包覆的蜡纳米粒子、即所述第一复合材料。
[0058]
根据本发明的实施方案,所述蜡纳米粒子和硅源的质量比为100:(10~40),具体地为100:(20~40),例如为100:10、100:20、100:25、100:30、100:35或100:40。
[0059]
根据本发明的实施方案,所述二氧化硅对蜡纳米粒子的包覆率为80%~200%,优选为100%~150%,例如为100%、110%、120%、130%、140%、150%。
[0060]
[第一复合材料的制备方法]
[0061]
本发明还提供上述第一复合材料的制备方法,所述制备方法包括以下步骤:
[0062]
a1)采用水入蜡相反转工艺制备得到蜡纳米粒子;
[0063]
a2)将步骤a1)得到的蜡纳米粒子加入预混溶液中,再加入硅源混合均匀后,乳化得到蜡-硅混合乳液;
[0064]
a3)取上述步骤a2)中的蜡-硅混合乳液,并持续滴加引发剂,反应即到所述第一复合材料。
[0065]
根据本发明的实施方案,步骤a1)中,所述水入蜡相反转工艺具体包括:将所述蜡加热融化后,加入乳化剂混合,加入超纯水乳化分散,得到蜡分散液;将所述蜡分散液离心分离得到所述蜡纳米粒子。
[0066]
根据本发明的实施方案,所述乳化剂和蜡的质量比为1:(5~9),例如为1:5、1:6、1:7、1:8、1:9。
[0067]
根据本发明的实施方案,所述混合在搅拌条件下进行,例如在低速搅拌条件下。优选地,所述低速搅拌条件是指搅拌速率为1~20r/s,例如为20r/s。
[0068]
根据本发明的实施方案,加入所述超纯水时,先将超纯水加热至蜡的熔点温度及以上。
[0069]
根据本发明的实施方案,加入的超纯水的质量和蜡的质量比为(1~10):1,例如为4~6:1。
[0070]
根据本发明的实施方案,所述超纯水分多次加入,每次加入的超纯水和蜡的质量比为(0.9~1.2):1,例如为1:1。
[0071]
根据本发明的实施方案,所述乳化分散的条件包括:高速搅拌35~55min。优选地,所述高速搅拌是指搅拌速率为20~100r/s,例如为50r/s。
[0072]
根据本发明的实施方案,所述乳化剂选自表面活性剂,所述表面活性剂的亲水亲油平衡值(hlb)为10~19。
[0073]
根据本发明的实施方案,所述表面活性剂选自聚氧乙烯失水山梨醇单油酸酯(如乳化剂t-81),聚氧乙烯失水山梨醇三油酸酯(如乳化剂t-85),聚氧乙烯油醇醚(如乳化剂oe-10,oe-20),聚氧乙烯单月桂酸酯(如s-307),聚氧乙烯失水山梨醇单棕榈酸酯(如乳化剂t-40),聚氧乙烯单硬脂酸酯(如atlas g-2159)中的至少一种或两种及两种以上的混合物。
[0074]
根据本发明的实施方案,离心分离的条件为:转速为100~200r/s,例如为150r/s。进一步地,离心分离时间为1~60min,例如为30min。
[0075]
优选地,离心分离后,还包括:清洗和/或干燥。本发明中,所述清洗和/或干燥可选用本领域已知的方法进行。示例性地,所述清洗是指用超纯水冲洗。示例性地,所述干燥选用真空干燥,例如在50℃下真空干燥12h。
[0076]
根据本发明的实施方案,a1)中,所述蜡纳米粒子的平均粒径为50nm~250nm。
[0077]
根据本发明的实施方案,a2)中,所述预混溶液包括:十六烷基三甲基溴化铵(ctab)、分散稳定剂和溶剂,其质量比为(10~14):(5~15):1900。
[0078]
优选地,所述溶剂选自超纯水和下述有机溶剂中的至少一种:乙醇、丙醇、异丙醇、乙腈。优选地,所述溶剂包括超纯水和有机溶剂,两者的质量比为1500:(100~500)。示例性地,所述溶剂包括超纯水和乙醇,其质量比为1500:(100~500),例如为1500:400。
[0079]
优选地,所述分散稳定剂选自高分子阳离子表面活性剂。优选地,所述高分子阳离子表面活性剂为聚乙烯亚胺。进一步地,所述聚乙烯亚胺为聚乙烯亚胺的水溶液,其固含量为1wt%~50wt%,例如为50wt%。
[0080]
优选地,所述聚乙烯亚胺的分子量(m.w.)在600~10000。
[0081]
本发明中,所述高分子阳离子表面活性剂,能够良好地包裹在蜡纳米粒子,有利于降低二氧化硅在酯蜡表面的生成速率,从而产生更加致密的二氧化硅层,有利于改善二氧
化硅对酯蜡的包覆效果,提高核壳结构的稳定性。
[0082]
根据本发明的实施方案,a2)中,乳化可选用本领域已知的方法进行,例如在超高速搅拌条件下进行。优选地,所述超高速搅拌是指转速为100~300r/s,例如为300r/s。
[0083]
根据本发明的实施方案,a3)中,所述反应在搅拌条件下进行,例如在低速搅拌条件下进行。
[0084]
根据本发明的实施方案,a3)中,所述反应的条件包括:反应温度为50℃以上,例如为58℃;反应时间为2~4h。
[0085]
根据本发明的实施方案,所述硅源和引发剂的质量比为(20~40):(30~60)。
[0086]
根据本发明的实施方案,a3)中,反应完成后,还可以进行离心分离和/或干燥,所述离心分离和干燥具有如上文所述的含义。
[0087]
[第二复合材料]
[0088]
如前所述,本发明公开了一种第二复合材料,其可以作为墨粉的外部添加剂使用。
[0089]
根据本发明的实施方案,所述二氧化硅通过物理共混的方式包覆在所述蜡纳米粒子的表面,且所述二氧化硅与所述蜡纳米粒子之间没有化学键。
[0090]
根据本发明的实施方案,所述二氧化硅优选为气相二氧化硅。
[0091]
具体地,所述二氧化硅通过将气相二氧化硅经过至少一种下述处理剂进行表面改性得到:聚二甲基硅氧烷(pdms)、二甲基二氯硅烷(dds)和六甲基二硅氮烷(hmds)。
[0092]
根据本发明的实施方案,所述蜡纳米粒子和二氧化硅的质量比为100:(50~300),例如为100:50、100:80、100:100、100:150、100:200、100:250、100:300。
[0093]
根据本发明的实施方案,所述二氧化硅对蜡纳米粒子的包覆率为80%~200%,优选为100%~150%。
[0094]
[第二复合材料的制备方法]
[0095]
本发明还提供上述第二复合材料的制备方法,所述制备方法包括:
[0096]
b1)采用水入蜡相反转工艺制备得到蜡纳米粒子;
[0097]
b2)在高速搅拌机中依次加入步骤b1)制得的蜡纳米粒子、二氧化硅,物理共混后,所述二氧化硅包覆在所述蜡纳米粒子的表面,得到第二复合材料。
[0098]
根据本发明的实施方案,b1)中,所述水入蜡相反转工艺和蜡纳米粒子具有如上文所述的含义。
[0099]
根据本发明的实施方案,b2)中,所述蜡纳米粒子和二氧化硅的质量比为100:(50~300)。
[0100]
根据本发明的实施方案,所述二氧化硅通过将气相二氧化硅经过至少一种下述处理剂进行表面改性得到:聚二甲基硅氧烷(pdms)、二甲基二氯硅烷(dds)和六甲基二硅氮烷(hmds)。所述气相二氧化硅具有如上文所述的含义。
[0101]
根据本发明的实施方案,b2)中,所述物理共混具体包括:先低速搅拌10~200s后再进行高速搅拌200~500s、静置。
[0102]
根据本发明的实施方案,所述低速搅拌和高速搅拌具有如上文所述的含义。
[0103]
根据本发明的实施方案,b2)中,所述物理共混可重复进行1~5次,例如为3次。
[0104]
[应用]
[0105]
本发明还提供上述复合材料的应用,其作为墨粉中的添加剂使用。
[0106]
根据本发明的实施方案,所述墨粉为彩色墨粉,具体的为物理法彩色墨粉或化学法彩色墨粉。
[0107]
根据本发明的实施方案,所述第一复合材料在所述墨粉中作为内部添加剂使用,所述第二复合材料在所述墨粉中作为外部添加剂使用。
[0108]
根据本发明的实施方案,所述物理法彩色墨粉包括内部添加剂和外部添加剂;所述内部添加剂中包括所述第一复合材料;所述外部添加剂中包括所述第二复合材料。
[0109]
根据本发明的实施方案,以质量百分含量计,所述物理法彩色墨粉中,第一复合材料的含量为1%~15%;和/或,第二复合材料的含量为0.5%~4%。
[0110]
根据本发明的实施方案,所述化学法彩色墨粉包括外部添加剂,所述外部添加剂中包括所述第二复合材料。
[0111]
根据本发明的实施方案,以质量百分含量计,所述化学法彩色墨粉中,所述第二复合材料的含量为0.5%~4%。
[0112]
[墨粉]
[0113]
本发明还提供一种墨粉,所述墨粉包括添加剂,所述添加剂中包括上述的复合材料。
[0114]
根据本发明的实施方案,所述墨粉为彩色墨粉;具体的,所述墨粉为物理法彩色墨粉,或者为化学法彩色墨粉。
[0115]
根据本发明的实施方案,所述墨粉包括内部添加剂和外部添加剂;所述内部添加剂包括上述的第一复合材料;所述外部添加剂包括上述的第二复合材料。
[0116]
根据本发明的实施方案,所述墨粉中,所述第一复合材料和第二复合材料的质量比为100:(5~20)。
[0117]
根据本发明的实施方案,所述墨粉通过干式物理法制备得到。
[0118]
根据本发明的实施方案,所述墨粉包括所述复合材料、粘接树脂、颜料,以及任选的电荷控制剂和/或其他添加剂。
[0119]
根据本发明的实施方案,所述墨粉中,所述第一复合材料的质量百分含量为1%~15%,例如为1%、5%、10%、15%。
[0120]
根据本发明的实施方案,所述墨粉中,所述第二复合材料的质量百分含量为0.5%~4%,例如为0.5%、1%、2%、3%、4%。
[0121]
根据本发明的实施方案,所述粘结树脂选自苯丙类树脂、聚酯类树脂、苯丙-聚酯类共聚树脂中的至少一种。
[0122]
根据本发明的实施方案,所述墨粉中,所述粘结树脂的质量百分含量为66%~94%,例如为66%、70%、75%、80%、85%、90%、94%。
[0123]
根据本发明的实施方案,所述颜料选自本领域已知的颜料,所述颜料的颜色例如为黄色、洋红色、青色、黑色和金光红色中的至少一种。
[0124]
根据本发明的实施方案,所述颜料可以选自本领域已知的有机颜料和/或无机颜料。示例性地,黄色颜料包括但不仅限于c.i.颜料黄74、颜料黄93、颜料黄94、颜料黄155、颜料黄162、颜料黄180、颜料黄185。示例性地,洋红色颜料包括但不仅限于c.i.颜料红31、颜料红122、颜料红150、颜料红184、颜料红185、颜料红238、颜料红259等。示例性地,青色颜料包括但不仅限于c.i.颜料蓝15:1、颜料蓝15:2、颜料蓝15:3、颜料蓝15:4。示例性地,黑色颜
料主要包括炭黑和氧化铁混合物。示例性地,金光红色颜料包括但不仅限于c.i.颜料红53:1,颜料红57:1,颜料红48:2。
[0125]
根据本发明的实施方案,在墨粉中,所述颜料的质量百分含量为3%~9%,例如为3%、4%、5%、6%、7%、8%、9%。
[0126]
根据本发明的实施方案,所述电荷控制剂(cca)为白色粉末状水杨酸金属络合物,例如选自水杨酸锌、水杨酸铬、水杨酸锆和水杨酸钙中的至少一种。
[0127]
根据本发明的实施方案,在所述墨粉中,所述电荷控制剂的质量百分含量为0.5%~3%,例如为0.5%、1%、1.5%、2%、2.5%、3%。
[0128]
根据本发明的实施方案,所述其他添加剂选自气相二氧化硅和/或硬脂酸金属盐。
[0129]
根据本发明的实施方案,所述气相二氧化硅优选采用pdms和/或hmds处理。
[0130]
根据本发明的实施方案,所述气相二氧化硅的原生粒度范围为7nm~16nm,例如为7nm、10nm、11nm、12nm、12nm、14nm、15nm、16nm。
[0131]
根据本发明的实施方案,在墨粉中,所述气相二氧化硅的质量百分含量为0.95%~2.5%,例如为1%、1.5%、2%、2.5%。
[0132]
根据本发明的实施方案,所述硬脂酸金属盐选自硬脂酸钙、硬脂酸镁、硬脂酸锌和硬脂酸钡中的至少一种。
[0133]
根据本发明的实施方案,在所述墨粉中,所述硬脂酸金属盐的质量百分含量为0.05%~0.5%。
[0134]
[墨粉的制备方法]
[0135]
本发明还提供上述墨粉的制备方法,所述制备方法为干式物理法,通过将所述复合材料与其他组分(例如粘接树脂、电荷控制剂、颜料和其他添加剂)混合后,通过熔融混炼、挤出压片、粉碎分级、混合外部添加剂而得到所述墨粉。
[0136]
根据本发明的实施方案,所述制备方法具体包括以下步骤:
[0137]
a)预混合:将配方比例的粘结树脂、第一复合材料、颜料和电荷控制剂经过预混合后,得到混合物;
[0138]
b)熔融混炼:将步骤a)得到的混合物熔融混炼后,挤出、冷却、压片,并经粗破碎得到粗颗粒;
[0139]
c)连续粉碎-分级:将步骤b)得到的粗颗粒,经过连续粉碎和分级,得到墨粉分级品;
[0140]
d)混合外部添加剂:将步骤c)得到的墨粉分级品和第二复合材料先进行低速混合,再加入其他外部添加剂进行高速混合,得到所述墨粉。
[0141]
根据本发明的实施方案,步骤a)中,预混合的条件包括:先低速搅拌,再高速搅拌。本发明的预混合在本领域已知的装置中进行,例如在高速混合机中。进一步地,低速搅拌的时间为1~10min,例如为5min。进一步地,高速搅拌的时间为1~60min,例如为30min。
[0142]
根据本发明的实施方案,步骤b)中,混炼温度为70℃~120℃,例如为70℃、80℃、90℃、100℃、110℃、120℃。
[0143]
根据本发明的实施方案,步骤c)中,所述粗颗粒的平均粒径为0.1~5mm,例如为1.5mm。
[0144]
根据本发明的实施方案,步骤c)中,连续粉碎包括气流粉碎和/或细粉碎。本发明
中,所述气流粉碎、细粉碎和分级可选用本领域已知的方法,本发明中不做具体限定。
[0145]
根据本发明的实施方案,步骤c)中,所述墨粉分级品具有如下性能中的至少一种:体积d50为7μm~10μm,例如为7μm、8μm、9μm、10μm;颗粒d97为2.5μm~3.5μm,例如为2.5μm、3μm、3.5μm。
[0146]
根据本发明的实施方案,步骤d)中,混合具体包括:先将墨粉分级品和第二复合材料混合,低速搅拌、静置,再加入其他外部添加剂,如气相二氧化硅、硬脂酸金属盐等,进行高速搅拌。优选地,所述低速搅拌和高速搅拌具有如上文所述的含义。进一步地,本发明中对步骤d)中的低速搅拌和高速搅拌的时间不做具体限定,例如为5min、8min。
[0147]
根据本发明的实施方案,所述制备方法还包括下述步骤:
[0148]
e)后处理:所述墨粉还可以进一步过筛和/或包装。
[0149]
下文将结合具体实施例对本发明的技术方案做更进一步的详细说明。应当理解,下列实施例仅为示例性地说明和解释本发明,而不应被解释为对本发明保护范围的限制。凡基于本发明上述内容所实现的技术均涵盖在本发明旨在保护的范围内。
[0150]
除非另有说明,以下实施例中使用的原料和试剂均为市售商品,或者可以通过已知方法制备。
[0151]
实施例1
[0152]
本实施例提供一种复合材料,其可以用于物理法彩色墨粉的内部添加剂,其是按照以下制备工艺制得:
[0153]
a)将100g的酯蜡we-3加热至85℃融化后,在6r/s的搅拌速率下,加入20g混合乳化剂(t-81和t-85的质量比为1:1),混合15min,然后,在搅拌速率为30r/s的高速搅拌下分5次加入温度为85℃的超纯水,每次用量和蜡相等,乳化分散时间45min,得到蜡分散液;
[0154]
b)将上述蜡分散液采用超高速150r/s离心分离30min,得到白色沉淀,用超纯水冲洗4次,然后在50℃下真空干燥12h,得到平均粒径在57nm的酯蜡纳米粒子;
[0155]
c)取100g蜡纳米粒子,加入预混合好的含有10g十六烷基三甲基溴化铵(ctab),1500g超纯水,400g乙醇和15g pei的混合溶液中,再和20g四乙氧基硅烷(teos)混合均匀后,在超高速300r/s下乳化15min,得到蜡-硅混合乳液;
[0156]
d)取上述步骤中的蜡-硅混合乳液于反应器中,以5r/s机械搅拌,升温至58℃,并持续滴加30g aptes,反应2h;
[0157]
e)反应完成后,按b)步骤进行离心、干燥,得到复合材料,标记为cd-a1。
[0158]
比较例1
[0159]
除将分散稳定剂聚乙烯亚胺(pei)去掉外,其余配方和工艺参数与实施例1相同,得到的复合材料标记为c-cd-a1。
[0160]
实施例2
[0161]
本实施例提供一种复合材料,其用于物理法彩色墨粉的内部添加剂,其是按照以下制备工艺制得:
[0162]
a)将100g的酯蜡we-15加热至90℃融化后,在8r/s的搅拌速率下,加入17g乳化剂oe-20,混合15min,然后,在搅拌速率为35r/s的高速搅拌下分5次加入温度为90℃的超纯水,每次用量和蜡相等,乳化分散时间40min,得到蜡分散液;
[0163]
b)将上述蜡分散液采用超高速150r/s离心分离30min,得到白色沉淀,用超纯水冲
洗4次,然后在50℃下真空干燥12h,得到平均粒径在117nm的酯蜡纳米粒子;
[0164]
c)取100g酯蜡纳米粒子,加入预混合好的含有12g ctab,1500g超纯水,400g乙醇和11g pei的混合溶液中,再和30g teos混合均匀后,在超高速300r/s下乳化15min,得到蜡-硅混合乳液;
[0165]
d)取上述步骤中的蜡-硅混合乳液于反应器中,以5r/s机械搅拌,升温至58℃,并持续滴加45g aptes,反应3h;
[0166]
e)反应完成后,按b)步骤进行离心、干燥,得到复合材料,标记为cd-a2。
[0167]
实施例3
[0168]
本实施例提供一种复合材料,其用于物理法彩色墨粉的内部添加剂,其是按照以下制备工艺制得:
[0169]
a)将100g的酯蜡pets-4加热至75℃融化后,在5r/s的搅拌速率下,加入14g乳化剂s-307,混合15min,然后,在搅拌速率为20r/s的高速搅拌下分4次加入温度为75℃的超纯水,每次用量和蜡相等,乳化分散时间55min,得到蜡分散液;
[0170]
b)将上述蜡分散液采用超高速150r/s离心分离30min,得到白色沉淀,用超纯水冲洗4次,然后在50℃下真空干燥12h,得到平均粒径在212nm的酯蜡纳米粒子;
[0171]
c)取100g酯蜡纳米粒子,加入预混合好的含有13g ctab,1500g超纯水,400g乙醇和8g pei的混合溶液中,再和35g teos混合均匀后,在超高速300r/s下乳化15min,得到蜡-硅混合乳液;
[0172]
d)取上述步骤中的蜡-硅混合乳液于反应器中,以5r/s机械搅拌,升温至58℃,并持续滴加53g aptes,反应3.5h;
[0173]
e)反应完成后,按b)步骤进行离心、干燥,得到复合材料,标记为cd-a3。
[0174]
实施例4
[0175]
本实施例提供一种复合材料,其用于物理法彩色墨粉的内部添加剂,其是按照以下制备工艺制得:
[0176]
a)将100g的酯蜡t-1加热至95℃融化后,在4r/s的搅拌速率下,加入12g乳化剂atlas g-2159,混合15min,然后,在搅拌速率为40r/s的高速搅拌下分6次加入温度为95℃的超纯水,每次用量和蜡相等,乳化分散时间35min,得到蜡分散液;
[0177]
b)将上述蜡分散液采用超高速150r/s离心分离30min,得到白色沉淀,用超纯水冲洗4次,然后在50℃下真空干燥12h,得到平均粒径在86nm的酯蜡纳米粒子;
[0178]
c)取100g酯蜡纳米粒子,加入预混合好的含有14g ctab,1500g超纯水,400g乙醇和5g pei的混合溶液中,再和40g teos混合均匀后,在超高速300r/s下乳化15min,得到蜡-硅混合乳液;
[0179]
d)取上述步骤中的蜡-硅混合乳液于反应器中,以5r/s机械搅拌,升温至58℃,并持续滴加60g aptes,反应4h;
[0180]
e)反应完成后,按b)步骤进行离心、干燥,得到复合材料,标记为cd-a4。
[0181]
比较例2
[0182]
除将实施例4步骤a)中的100g蜡和500g水添加顺序互换,即将蜡加入水中进行分散外,其余工艺参数与实施例4相同。得到的复合材料的粒径增加至532nm,标记为c-cd-a4。
[0183]
实施例5
[0184]
本实施例提供一种复合材料,其用于物理法彩色墨粉的外部添加剂,其是按照以下制备工艺制得:
[0185]
在高速搅拌机中依次加入100g实施例1步骤b)所得酯蜡纳米粒子,200g气相二氧化硅r202,50g气相二氧化硅h2000t,调整转速20r/s持续120s,然后提高转速到60r/s持续300s,停60s,然后按上述混合步骤重复3次,得到复合材料,标记为cd-b1。
[0186]
实施例6
[0187]
除将酯蜡纳米粒子换为实施例2步骤b)的酯蜡纳米粒子,将气相二氧化硅型号替换为80g h3004外,其余工艺步骤和实施例5相同,得到复合材料,标记为cd-b2。
[0188]
实施例7
[0189]
除将酯蜡纳米粒子替换为实施例3步骤b)的酯蜡纳米粒子,将气相二氧化硅型号替换为50g ry200l和10g hm-30st外,其余工艺步骤和实施例5相同,得到复合材料,标记为cd-b3。
[0190]
实施例8
[0191]
除将酯蜡纳米粒子换为实施例4步骤b)的酯蜡纳米粒子,将气相二氧化硅型号替换为100g r812s外,其余工艺步骤和实施例5相同,得到复合材料,标记为cd-b4。
[0192]
比较例3
[0193]
除将实施例8中的分步高速混合变为一步高速混合,即先混合20r/s持续360s后,立即进行60r/s持续900s的高速混合外,其余工艺步骤和实施例8相同,得到复合材料,标记为c-cd-b2。
[0194]
应用例1(黄色墨粉)
[0195]
本实施例提供一种包含复合材料cd-a4和cd-b1的物理法黄色墨粉,其是按照以下制备工艺制得:
[0196]
a)预混合:将配方比例的苯丙树脂(84%)、颜料黄180(3%)、复合材料cd-a4(9.5%)和水杨酸钙(1.5%)依次加入高速混合机中,先低速搅拌5min,再高速搅拌15min,得到混合物;
[0197]
b)熔融混炼:将上述混合物通过连续式双螺杆挤出机进行熔融混炼,混炼温度120℃,随后对挤出料进行冷却、压片,并粗破碎为1.5mm左右的粗颗粒;
[0198]
c)连续粉碎-分级:将上述粗颗粒,先经过气流粉碎机进行粗粉碎,再逐级进行细粉碎和分级,直至得到体积d50=9.5μm,颗粒d97=3.4μm的墨粉分级品;
[0199]
d)混合外部添加剂:先加入上述步骤得到的墨粉分级品和复合材料cd-b1(0.5%),低速20r/s混合5min,然后静置1min,再加入气相二氧化硅ry300(0.45%)、rx300(0.5%)和硬脂酸钡(0.5%)进行高速50r/s混合8min;
[0200]
e)后处理:将混合好的墨粉经过筛、包装得到黄色墨粉成品。
[0201]
应用比较例1
[0202]
本应用比较例提供一种使用比较例1制备的c-cd-a1作为内部添加剂的黄色墨粉及制备方法,其是按照以下步骤制得:
[0203]
除使用比较例1制备的c-cd-a1等量替代cd-a4外,其余配方和工艺和应用例1相同,得到黄色墨粉。
[0204]
应用例2(红色墨粉)
[0205]
本实施例提供一种包含复合材料cd-a2和cd-b2的物理法红色墨粉,其是按照以下制备工艺制得:
[0206]
a)预混合:将配方比例的苯丙树脂(84%)、颜料红122(5%)、复合材料cd-a2(2%)和水杨酸锌(3%)依次加入高速混合机中,先低速搅拌5min,再高速搅拌15min,得到混合物;
[0207]
b)熔融混炼:将上述混合物通过连续式双螺杆挤出机进行熔融混炼,混炼温度100℃,随后对挤出料进行冷却、压片,并粗破碎为1.5mm左右的粗颗粒;
[0208]
c)连续粉碎-分级:将上述粗颗粒,先经过气流粉碎机进行粗粉碎,再逐级进行细粉碎和分级,直至得到体积d50=8.0μm,颗粒d97=3.3μm的墨粉分级品;
[0209]
d)混合外部添加剂:先加入上述步骤得到的墨粉分级品和复合材料cd-b2(4.0%),低速20r/s混合5min,然后静置1min,再加入气相二氧化硅h20tm(1.8%)和硬脂酸锌(0.2%)进行高速50r/s混合8min;
[0210]
e)后处理:将混合好的墨粉经过筛、包装得到红色墨粉成品。
[0211]
应用比较例2
[0212]
本应用比较例提供一种使用比较例3制备的c-cd-b2作为外部添加剂的红色墨粉及制备方法,其是按照以下步骤制得:
[0213]
除使用比较例3制备的c-cd-b2等量替代cd-b2外,其余配方和工艺和应用例2相同,得到红色墨粉。
[0214]
应用例3(青色墨粉)
[0215]
本实施例提供一种包含复合材料cd-a3和cd-b3的物理法青色墨粉,其是按照以下制备工艺制得:
[0216]
a)预混合:将配方比例的苯丙树脂(80%)、颜料蓝15:4(7%)、复合材料cd-a3(7%)和水杨酸锆(1%)依次加入高速混合机中,先低速搅拌5min,再高速搅拌15min,得到混合物;
[0217]
b)熔融混炼:将上述混合物通过连续式双螺杆挤出机进行熔融混炼,混炼温度70℃,随后对挤出料进行冷却、压片,并粗破碎为1.5mm左右的粗颗粒;
[0218]
c)连续粉碎-分级:将上述粗颗粒,先经过气流粉碎机进行粗粉碎,再逐级进行细粉碎和分级,直至得到体积d50=7.5μm,颗粒d97=3.0μm的墨粉分级品;
[0219]
d)混合外部添加剂:先加入上述步骤得到的墨粉分级品和复合材料cd-b3(2.7%),低速20r/s混合5min,然后静置1min,再加入气相二氧化硅tg-7180(1.2%)、h30tm(1.0%)和硬脂酸钙(0.1%)进行高速50r/s混合8min;
[0220]
e)后处理:将混合好的墨粉经过筛、包装得到青色墨粉成品。
[0221]
应用比较例3
[0222]
本应用比较例提供一种不使用本发明制备的复合材料(cd-a3)作为内部添加剂的青色墨粉及制备方法,其是按照以下步骤制得:
[0223]
除使用酯蜡pets-4等量替代cd-a3外,其余配方和工艺和应用例3相同,得到青色墨粉。
[0224]
应用例4(黑色墨粉)
[0225]
本实施例提供一种包含复合材料cd-a1和cd-b4的物理法黑色墨粉,其是按照以下
制备工艺制得:
[0226]
a)预混合:将配方比例的苯丙树脂(72%)、炭黑(9%)、复合材料cd-a1(14%)和水杨酸铬(0.5%)依次加入高速混合机中,先低速搅拌5min,再高速搅拌15min,得到混合物;
[0227]
b)熔融混炼:将上述混合物通过连续式双螺杆挤出机进行熔融混炼,混炼温度90℃,随后对挤出料进行冷却、压片,并粗破碎为1.5mm左右的粗颗粒;
[0228]
c)连续粉碎-分级:将上述粗颗粒,先经过气流粉碎机进行粗粉碎,再逐级进行细粉碎和分级,直至得到体积d50=7.0μm,颗粒d97=2.5μm的墨粉分级品;
[0229]
d)混合外部添加剂:先加入上述步骤得到的墨粉分级品和复合材料cd-b4(1.9%),低速20r/s混合5min,然后静置1min,再加入气相二氧化硅r812s(2.5%)和硬脂酸镁(0.05%)进行高速50r/s混合8min;
[0230]
e)后处理:将混合好的墨粉经过筛、包装得到黑色墨粉成品。
[0231]
应用比较例4
[0232]
本应用比较例提供一种不使用本发明制备的复合材料cd-b4作为外部添加剂的黑色墨粉及制备方法,其是按照以下步骤制得:
[0233]
除使用德固赛大颗粒硅ry40s(粒径80nm)等量替代cd-b4外,其余配方和工艺和应用例4相同,得到黑色墨粉。
[0234]
应用比较例5
[0235]
本应用比较例提供一种既不使用本发明制备的复合材料cd-b4,又不使用中大颗粒硅作为外部添加剂的黑色墨粉及制备方法,其是按照以下步骤制得:
[0236]
除将cd-b4去掉,将苯丙树脂用量提高到73.9%,将d)步骤中的“低速20r/s混合5min,然后静置1min”省去外,其余配方和工艺和应用例4相同,得到黑色墨粉。
[0237]
应用比较例6
[0238]
本应用比较例提供一种不使用pei作为分散稳定剂得到的复合材料(即比较例1中的c-cd-a1)的黑色墨粉及制备方法,其是按照以下步骤制得:
[0239]
除使用c-cd-a1等量替代cd-a1外,其余配方和工艺与应用例4相同,得到黑色墨粉。
[0240]
表1.彩色物理法墨粉制备实施例和比较例墨粉性能评估结果
[0241][0242]
对上述使用本技术制备的复合材料的黄、红、青、黑四色墨粉及相应的比较例的打印效果进行评估和对比。测试依照《gb/t29300-2012》实施,其中光泽性测试采用市售常规光泽度仪进行测量,所有打印均在相同的打印机和硒鼓上进行,所有墨粉的装粉量均为60g。测试结果如表1所示。
[0243]
应用例1和应用比较例1的对比可以发现,当调整工艺步骤a)为蜡入入水制备得到的复合材料c-cd-a1用于黄色墨粉时,由于制备的复合添加粒径过大(532nm),使其在苯丙树脂中的分散性变差,导致印品的光泽性从10.5显著下降到2.8,目视已无光泽,还出现了粘刀问题,页产量也有所下降,此外,结块温度降低使得存储稳定性变差,因此,不能满足高性能彩色墨粉的打印要求。
[0244]
应用例2和应用比较例2的对比可以发现,当使用一步混合得到的复合材料c-cd-b2(比较例3)替代cd-b2时,红色墨粉的带电量下降,导致页产量降低,稿面均匀性也出现明显下降,这是由于一步混合的强度过大,小颗粒硅容易打入蜡纳米粒子内部,从而使复合材料c-cd-b2自身的带电性能下降,因此,不能满足高性能彩色墨粉的打印要求。
[0245]
应用例3和应用比较例3的对比可以发现,当物理法青色墨粉内部添加剂中只使用常规的酯蜡pets-4时,除光泽性和结块温度显著降低外,在高温高湿下,打印500页就出现了严重的粘刀问题,这是由于采用常规手段无法达到对酯蜡在苯丙树脂中均匀分散的目
的,因此只有使用本应用例3的方案,才能获得高品质的青色墨粉。
[0246]
应用例4和应用比较例4的对比可以发现,当使用德固赛大颗粒硅ry40s(粒径80nm)等量替代cd-b4(应用例4)后制得的黑色墨粉,带电量显著降低,导致页产量不足,但保持性良好,这进一步说明了市售大颗粒硅普遍存在带电量低的问题,虽然具有提高墨粉保持性的优点,但会使墨粉的页产量下降,硒鼓的制造成本进一步升高。
[0247]
应用例4和应用比较例5的对比可以发现,当外部添加剂不使用cd-b4(应用例4)时得到的黑色墨粉,带电量显著下降,页产量严重不足,且稿面均匀性(保持性)显著下降,这说明复合材料cd-b4具有提高墨粉带电量和保持性的双重作用,这是市售大颗粒硅所无法同时满足的性能指标,具有突出的优势和显著的进步。
[0248]
应用例4和应用比较例6的对比可以发现,当使用c-cd-a1(比较例1,不使用pei作为分散剂)替代cd-a1得到的黑色墨粉,结块温度所有降低,存储稳定性变差,且光泽性显著下降,页产量也有所降低。这说明分散稳定剂pei在蜡纳米粒子制备过程中起着关键作用,能够使蜡纳米粒子的分散性更好,并使二氧化硅的包覆更加致密,从而提高蜡在墨粉树脂中的分散性,改善墨粉的综合性能,这是其他分散剂所无法满足的。
[0249]
综上可知,本发明实施例的用于干式物理法彩色墨粉的复合材料的制备方法简单,原料易得,制备出的第一复合材料用于墨粉的内部添加剂时,能够显著提高墨粉的光泽性和存储稳定性(提高结块温度)并防止粘刀的发生;制备出的复合材料用于墨粉的外部添加剂时,能够同时提高墨粉的带电量和保持性,从而提高页产量并降低制造成本,同时稿面的均匀性也能够在更高的打印量下保持一致,这对于彩色墨粉而言,是非常关键的指标,因为对于彩色激光打印机而言,是需要cmyk四色墨粉互相配合来呈现出彩色图案,当有一种颜色的墨粉均匀性提前下降时,势必会对图案的色彩还原产生致命的影响,因此就要求四色墨粉都能够在尽可能高的页数下保持良好的均匀性和稳定的输出表现。此外,由于复合材料本身不受墨粉制备工艺的限制,因此,做为外部添加剂使用时,既能够用于物理法彩色墨粉,又能够应用化学法彩色墨粉中,能够产生相同的效果。
[0250]
以上对本发明示例性的实施方式进行了说明。但是,本技术的保护范围不拘囿于上述实施方式。本领域技术人员在本发明的精神和原则之内,所做的任何修改、等同替换、改进等,均应包含在本发明的保护范围之内。
再多了解一些
本文用于创业者技术爱好者查询,仅供学习研究,如用于商业用途,请联系技术所有人。