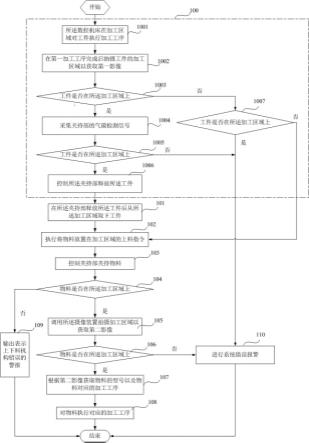
1.本发明涉及数控机床领域,特别涉及一种基于视觉控制的控制方法及数控机床。
背景技术:
2.随着我国工业总体方案的推进,单体机床传统的人工上下料方式越来越不能满足无人化,自动化的生产要求。尤其是现代加工领域,柔性化,碎片化已经成为智能加工的一种必然趋势,以前的自动上下料站通过上下料装置只能提供基本的工件松夹功能,尤其是气隙检测的方式对于工件是否在位,是否松夹完成很容易发生误判,形成危险。当物料种类繁多时,传统工件确认方式也缺乏有效的甄别手段,无法使机床准确确认工件类型并自动完成加工过程。
技术实现要素:
3.本发明要解决的技术问题是为了克服现有技术中数控机床容易发生误判,由此形成危险,工件缺乏有效的甄别手段,无法使机床准确确认工件类型并自动完成加工过程的缺陷,提供一种能够提高数控机床的智能性,提高生产效率以及生产质量,减少事故发生率的基于视觉控制的控制方法及数控机床。
4.本发明是通过下述技术方案来解决上述技术问题:一种基于视觉控制的控制方法,用于数控机床,所述数控机床包括一夹持部、一摄像装置、一上下料机构以及一控制模块,所述控制方法包括:所述数控机床在加工区域对工件执行加工工序;所述上下料机构在所述夹持部释放所述工件后从所述加工区域取下工件;所述上下料机构执行将物料放置在所述加工区域的上料指令;控制模块控制夹持部夹持物料;所述控制模块在上料指令完成后根据气隙检测信号判断物料是否在所述加工区域上,若是则调用所述摄像装置拍摄加工区域以获取第二影像;所述控制模块根据第二影像判断物料是否在所述加工区域上,若是则控制模块根据第二影像获取物料的型号以及物料对应的加工工序;所述控制模块控制所述数控机床对物料执行对应的加工工序。
5.较佳地,所述数控机床在加工区域对工件执行加工工序,包括:所述数控机床在加工区域对工件执行加工工序;所述摄像装置在第一加工工序完成后拍摄工件的加工区域以获取第一影像;所述控制模块根据第一影像判断工件是否在所述加工区域上,若是则采集夹持部的气隙检测信号;所述控制模块根据气隙检测信号判断工件是否在所述加工区域上,若是则控制所述夹持部释放所述工件。
6.较佳地,所述控制所述夹持部释放所述工件,包括:
所述控制模块通过第一电磁阀打开所述数控机床的机床侧门;所述控制模块判断所述机床侧门是否打开到位,若是则通过第二电磁阀控制所述夹持部释放所述工件;所述控制模块根据夹持部上的压力传感器判断工件是否释放到位,若是则通知所述上下料机构从所述加工区域取下工件。
7.较佳地,所述上下料机构执行将物料放置在所述加工区域的上料指令,包括:所述摄像装置在取下工件后拍摄加工区域以获取第三影像;所述控制模块根据第三影像判断所述加工区域上是否存在工件,若否则采集夹持部的气隙检测信号;所述控制模块根据气隙检测信号判断工件是否在所述加工区域上,若否则控制所述上下料机构执行将物料放置在所述加工区域的上料指令。
8.较佳地,所述数控机床在加工区域对工件执行加工工序,包括:所述控制模块根据第一影像判断工件是否在所述加工区域上,若否则采集夹持部的气隙检测信号;所述控制模块根据气隙检测信号判断工件是否在所述加工区域上,若是则进行系统错误报警,若否则通知上下料机构执行将物料放置在所述加工区域的上料指令。
9.较佳地,所述控制模块在上料指令完成后根据气隙检测信号判断物料是否在所述加工区域上,包括:所述控制模块在上料指令完成后根据气隙检测信号判断物料是否在所述加工区域上,若否则输出表示上下料机构错误的警报;若是则调用所述摄像装置拍摄加工区域以获取第二影像;所述控制模块根据第二影像判断物料是否在所述加工区域上,若否则进行系统错误报警。
10.较佳地,所述控制夹持部夹持物料,包括:所述控制模块通过第二电磁阀控制所述夹持部夹持所述物料,并通过第一电磁阀关闭所述数控机床的机床侧门;所述控制模块根据夹持部上的压力传感器判断物料是否夹持到位,若是则通知所述控制模块识别第二影像以获取物料的型号。
11.较佳地,所述摄像装置为三维摄像头,所述三维摄像头设于加工区域的上方,所述第二影像为三维点云影像,所述控制模块根据第二影像获取物料的型号以及物料对应的加工工序,包括:所述控制模块获取三维点云影像上的特征点;所述控制模块根据所述特征点在物料数据池中查找与特征点及特征点之间的实际距离匹配的物料设计数据;所述控制模块调整物料设计数据的数字化尺寸与方向使物料设计数据与特征点的位置对齐;所述控制模块根据对齐后的物料设计数据以及特征点的空间坐标获取物料在加工区域上的数字化物料模型;所述控制模块根据数字化模型获取物料的实际尺寸,根据物料的实际尺寸获取物
料的型号以及物料对应的加工工序。
12.较佳地,所述控制模块控制所述数控机床对物料执行对应的加工工序,包括:所述控制模块控制所述数控机床对物料执行对应的加工工序;所述摄像装置拍摄加工区域中物料加工后所得工件以获取第三影像,所述第三影像包括点云的反射率;所述控制模块根据加工工序以及所述数字化物料模型获取数字化工件模型;所述控制模块根据特征点的匹配获取第三影像以及所述数字化工件的匹配度;所述控制模块根据所述匹配度以及所述反射率获取工件的加工质量。
13.本发明还提供一种数控机床,所述数控机床用于执行如上所述的控制方法。
14.符合本领域常识的基础上,上述各优选条件,可任意组合,即得本发明各较佳实例。
15.本发明的积极进步效果在于:本发明能够提高数控机床的智能性,提高生产效率以及生产质量,减少事故发生率。
附图说明
16.图1为本发明实施例1的控制方法的流程图。
具体实施方式
17.下面通过实施例的方式进一步说明本发明,但并不因此将本发明限制在所述的实施例范围之中。
18.实施例1本实施例提供一种基于视觉控制的数控机床,所述数控机床包括一夹持部、一摄像装置、一上下料机构以及一控制模块。
19.所述数控机床的主轴用于在加工区域对工件执行加工工序;所述上下料机构用于在所述夹持部释放所述工件后从所述加工区域取下工件;所述上下料机构用于执行将物料放置在所述加工区域的上料指令;所述控制模块用于在上料指令完成后根据气隙检测信号判断物料是否在所述加工区域上,若是则调用所述摄像装置拍摄加工区域以获取第二影像;所述控制模块用于根据第二影像判断物料是否在所述加工区域上,若是则控制夹持部夹持物料;所述控制模块用于根据第二影像获取物料的型号以及物料对应的加工工序;所述控制模块用于控制所述数控机床对物料执行对应的加工工序。
20.进一步地,所述数控机床用于在加工区域对工件执行加工工序;所述摄像装置用于在第一加工工序完成后拍摄工件的加工区域以获取第一影像;所述控制模块用于根据第一影像判断工件是否在所述加工区域上,若是则采集夹持部的气隙检测信号;所述控制模块用于根据气隙检测信号判断工件是否在所述加工区域上,若是则控制所述夹持部释放所述工件。
21.所述控制模块用于通过第一电磁阀打开所述数控机床的机床侧门;所述控制模块用于判断所述机床侧门是否打开到位,若是则通过第二电磁阀控制所述夹持部释放所述工件;所述控制模块用于根据夹持部上的压力传感器判断工件是否释放到位,若是则通知所述上下料机构从所述加工区域取下工件。
22.所述摄像装置用于在取下工件后拍摄加工区域以获取第三影像;所述控制模块用于根据第三影像判断所述加工区域上是否存在工件,若否则采集夹持部的气隙检测信号;所述控制模块用于根据气隙检测信号判断工件是否在所述加工区域上,若否则控制所述上下料机构执行将物料放置在所述加工区域的上料指令。
23.所述控制模块用于根据第一影像判断工件是否在所述加工区域上,若否则采集夹持部的气隙检测信号;所述控制模块用于根据气隙检测信号判断工件是否在所述加工区域上,若是则进行系统错误报警,若否则通知上下料机构执行将物料放置在所述加工区域的上料指令。
24.所述控制模块用于在上料指令完成后根据气隙检测信号判断物料是否在所述加工区域上,若否则输出表示上下料机构错误的警报;若是则调用所述摄像装置拍摄加工区域以获取第二影像;所述控制模块用于根据第二影像判断物料是否在所述加工区域上,若是则控制夹持部夹持物料,若否则进行系统错误报警。
25.所述控制模块用于通过第二电磁阀控制所述夹持部夹持所述物料,并通过第一电磁阀关闭所述数控机床的机床侧门;所述控制模块用于根据夹持部上的压力传感器判断物料是否夹持到位,若是则通知所述控制模块识别第二影像以获取物料的型号。
26.所述摄像装置为三维摄像头,所述三维摄像头设于加工区域的上方,所述第二影像为三维点云影像。
27.所述控制模块用于获取三维点云影像上的特征点;所述控制模块用于根据所述特征点在物料数据池中查找与特征点及特征点之间的实际距离匹配的物料设计数据;所述控制模块用于调整物料设计数据的数字化尺寸与方向使物料设计数据与特征点的位置对齐;所述控制模块用于根据对齐后的物料设计数据以及特征点的空间坐标获取物料在加工区域上的数字化物料模型;所述控制模块用于根据数字化模型获取物料的实际尺寸,根据物料的实际尺寸获取物料的型号以及物料对应的加工工序。
28.进一步地,所述控制模块用于控制所述数控机床对物料执行对应的加工工序;所述摄像装置用于拍摄加工区域中物料加工后所得工件以获取第三影像,所述第三影像包括点云的反射率;所述控制模块用于根据加工工序以及所述数字化物料模型获取数字化工件模型;所述控制模块用于根据特征点的匹配获取第三影像以及所述数字化工件的匹配
度;所述控制模块用于根据所述匹配度以及所述反射率获取工件的加工质量。
29.参见图1,利用上述的数控机床,本实施例提供一种基于视觉控制的控制方法,所述控制方法包括:步骤100、所述数控机床在加工区域对工件执行加工工序;步骤101、所述上下料机构在所述夹持部释放所述工件后从所述加工区域取下工件;步骤102、所述上下料机构执行将物料放置在所述加工区域的上料指令;步骤103、控制夹持部夹持物料;步骤104、所述控制模块在上料指令完成后根据气隙检测信号判断物料是否在所述加工区域上,若是则执行步骤105,若否则执行步骤109步骤105、调用所述摄像装置拍摄加工区域以获取第二影像;步骤106、所述控制模块根据第二影像判断物料是否在所述加工区域上,若是则执行步骤107,若否则执行步骤110。
30.步骤107、所述控制模块根据第二影像获取物料的型号以及物料对应的加工工序;步骤108、所述控制模块控制所述数控机床对物料执行对应的加工工序,然后结束流程。
31.步骤109、输出表示上下料机构错误的警报,然后结束流程。
32.步骤110、进行系统错误报警,然后结束流程。
33.其中,步骤100具体包括:步骤1001、所述数控机床在加工区域对工件执行加工工序;步骤1002、所述摄像装置在第一加工工序完成后拍摄工件的加工区域以获取第一影像;步骤1003、所述控制模块根据第一影像判断工件是否在所述加工区域上,若是则执行步骤1004,若否则执行步骤1007步骤1004、采集夹持部的气隙检测信号;步骤1005、所述控制模块根据气隙检测信号判断工件是否在所述加工区域上,若是则执行步骤1006,若否则执行步骤110。
34.步骤1006、控制所述夹持部释放所述工件,然后执行步骤101。
35.步骤1007、采集夹持部的气隙检测信号,并根据气隙检测信号判断工件是否在所述加工区域上,若是则执行步骤110,若否则通知上下料机构执行将物料放置在所述加工区域的上料指令然后执行步骤102。
36.步骤1008、进行系统错误报警,然后结束流程。
37.其中步骤1006具体包括:所述控制模块通过第一电磁阀打开所述数控机床的机床侧门;所述控制模块判断所述机床侧门是否打开到位,若是则通过第二电磁阀控制所述夹持部释放所述工件;所述控制模块根据夹持部上的压力传感器判断工件是否释放到位,若是则通知所述上下料机构从所述加工区域取下工件。
38.其中步骤102具体包括:所述摄像装置在取下工件后拍摄加工区域以获取第三影像;所述控制模块根据第三影像判断所述加工区域上是否存在工件,若否则采集夹持部的气隙检测信号;所述控制模块根据气隙检测信号判断工件是否在所述加工区域上,若否则控制所述上下料机构执行将物料放置在所述加工区域的上料指令。
39.步骤103具体包括:所述控制模块通过第二电磁阀控制所述夹持部夹持所述物料,并通过第一电磁阀关闭所述数控机床的机床侧门;所述控制模块根据夹持部上的压力传感器判断物料是否夹持到位,若是则通知所述控制模块识别第二影像以获取物料的型号。
40.进一步地,所述摄像装置为三维摄像头,所述三维摄像头设于加工区域的上方,所述第二影像为三维点云影像,所述控制模块根据第二影像获取物料的型号以及物料对应的加工工序,包括:所述控制模块获取三维点云影像上的特征点;所述控制模块根据所述特征点在物料数据池中查找与特征点及特征点之间的实际距离匹配的物料设计数据;所述控制模块调整物料设计数据的数字化尺寸与方向使物料设计数据与特征点的位置对齐;所述控制模块根据对齐后的物料设计数据以及特征点的空间坐标获取物料在加工区域上的数字化物料模型;本实施例中的数字化物料模型为物料设计数据在加工区域的投射模型,物料设计数据是预存的可以获取的数据模型,利用三维设计软件生成或制作而成。数字化物料模型是将物料设计数据按照特征点的位置以及位置关系进行转换以生成的一个可以代替三维点云影像的数字化的、规范化的模型,此模型中各影像点的坐标已知,根据各影像点的已知的坐标能够使数控机床了解到当前物料的全方位尺寸、摆放位置等信息,方便后续的加工、夹持以及上下料的对接。
41.所述控制模块根据数字化模型获取物料的实际尺寸,根据物料的实际尺寸获取物料的型号以及物料对应的加工工序。
42.步骤108具体包括:所述控制模块控制所述数控机床对物料执行对应的加工工序;所述摄像装置拍摄加工区域中物料加工后所得工件以获取第三影像,所述第三影像包括点云的反射率;所述控制模块根据加工工序以及所述数字化物料模型获取数字化工件模型;所述控制模块根据特征点的匹配获取第三影像以及所述数字化工件的匹配度;所述控制模块根据所述匹配度以及所述反射率获取工件的加工质量。
43.虽然以上描述了本发明的具体实施方式,但是本领域的技术人员应当理解,这些仅是举例说明,本发明的保护范围是由所附权利要求书限定的。本领域的技术人员在不背离本发明的原理和实质的前提下,可以对这些实施方式做出多种变更或修改,但这些变更
和修改均落入本发明的保护范围。
再多了解一些
本文用于创业者技术爱好者查询,仅供学习研究,如用于商业用途,请联系技术所有人。