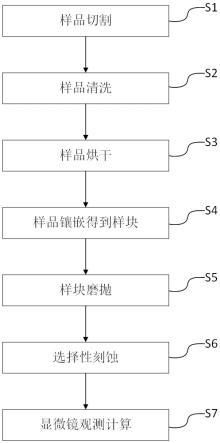
1.本发明涉及非金属材料加工制造技术领域,具体而言,涉及一种非金属材料亚表面损伤深度的表征方法。
背景技术:
2.非金属材料由于切割时表面受到机械、激光等外力作用,会产生沿切割面向内纵向延伸的裂纹,业内通常将之称为加工的亚表面损伤层。亚表面损伤层中在受到外力作用时,会由于应力集中造成材料破碎,从而影响材料的机械、物理性能。在半导体芯片制造行业中,亚表面损伤层裂纹间隙所储存的颗粒和金属离子不易去除,严重干扰制程的洁净度,因此需要对亚表面损伤深度进行表征。
3.目前,亚表面损伤的检测技术包括破坏性和非破坏性检测,破坏性检测方法具有操作方便,结果直观,检测准确度高的优点,因此使用更加广泛。常见的破坏性检测方法包括截面显微法和锥度抛光法,截面显微法是直接对待测截面进行研磨、抛光,直接观察损伤结构,该方法操作简单,但检测精度较低;锥度抛光法是对待测面进行锥度抛光,使损伤信息以腐蚀坑的形式在一个斜面上显示,斜面起到了放大作用,因此可以提高检测精度。但锥度抛光样品制作比较复杂,如中国专利cn108534732a公开的技术,需要切割斜面,但斜面加工精度不易保证,加工过程中容易产生微观尺度的损伤,且斜面角度略有偏差,就会对检测结果产生很大影响;又如中国专利cn112834304a采用在样品底部粘接斜面的方式使样品倾斜,但粘接的样品需要使样品边界与斜面边界重合,对样品加工尺寸精度要求较高,对齐操作比较麻烦,且样品与斜面之间的粘接层容易出现厚度不均的情况,进而影响样品的倾斜角度,因此该方法的检测准确性无法保证。
技术实现要素:
4.针对现有技术的不足,本发明所要解决的技术问题是如何提高非金属材料亚表面损伤深度的检测准确性和精度。
5.为解决上述问题,本发明提供一种非金属材料亚表面损伤深度的表征方法,包括以下步骤:s1、将待测样品沿待测面垂直方向切割成方块;s2、将切割好的样品放入含有表面活性剂的清洗剂中,进行超声清洗;s3、清洗后的样品进行真空烘干;s4、将样品放置在镶嵌模具内,镶嵌模具底部安装顶面倾斜角度为θ的垫块,模具内加入镶嵌树脂并固化,脱模得到样块;s5、采用金相磨抛机,将固化好的样块依次进行表面粗磨、精磨和抛光;s6、将研磨好的样块置于选择性刻蚀液中浸泡;s7、用显微镜对处理好的样块表面的待观测区进行测量,沿观测线进行观察,找到观测处最深的损伤点,此损伤点到树脂与损伤层交界处的垂直距离称为损伤层深度测量
值,使用显微镜测量出该值,记为h
测
,计算损伤层深度实际值h
实
=h
测
*sinθ。
6.相对于现有技术,本发明提供了一种新的非金属材料亚表面损伤深度表征方法,将切割、样品清洗、真空烘干、样块镶嵌、磨抛、选择性刻蚀等步骤有机结合,特别是采用镶嵌树脂固定样品的方式可以保证待测面的倾斜角度精确,在后续磨抛过程中不会发生移位,从而提高了损伤深度检测结果的准确性和精度,为评估加工工艺的优劣,优化加工工序,实现材料表面“零损伤”的处理工艺提供数据支持。
7.进一步地,所述步骤s4中,所述镶嵌树脂的硬度≥80hsd,体积收缩率≤5%。选择具有合适硬度和体积收缩率的镶嵌树脂,保证对样块的位置限定作用,提高损伤深度检测结果的准确度。
8.进一步地,所述步骤s4中,所述镶嵌树脂包括质量比为2:1的环氧树脂和固化剂,固化温度为120℃,固化时间为2h。该镶嵌树脂具有固化温度低,固化时间短,固化后硬度高,体积收缩率小的有点,是一种合适的镶嵌树脂。
9.进一步地,所述步骤s4中,垫块顶面的倾斜角度θ介于5
°
~10
°
之间。此倾斜角度对于损伤深度具有很好的放大作用,提高检测精度。
10.进一步地,所述步骤s5中,粗磨步骤采用金刚石研磨盘快速去除多余部分树脂,使样块接近观察表面,去除厚度为d1;精磨步骤采用柔软的聚合物研磨垫配合二氧化硅微粒研磨液进行初步抛光,所述二氧化硅微粒粒径为5~10um,去除厚度为d2;抛光步骤采用聚合物研磨垫配合纳米颗粒进行镜面抛光,将损伤层暴露出来,所述纳米颗粒粒径<1um,去除厚度为d3;其中d1》10d2》100d3。磨抛步骤包括粗磨、精磨和抛光,通过三种不同方式的磨抛处理可以将损伤层充分暴露,通过限定粗磨、精磨和抛光的厚度关系可以将样块精确加工至待测位置,防止研磨过程对真实结果的干扰,同时节省研磨处理时间。
11.进一步地,所述步骤s5中,金相磨抛机转速为300rpm,研磨压力为20n。控制金相磨抛机的运行参数,保证磨抛过程中不会产生新的损伤,同时兼顾工作效率。
12.进一步地,所述待测样品为单晶硅材料,所述步骤s6中,所述选择性刻蚀液中各成分的质量比为 hf:hno3:h2o=1:10:20,刻蚀时间为10min。采用该选择性刻蚀液可以增加裂纹宽度,但不会改变深度,便于显微镜观测。
13.进一步地,所述步骤s1中,采用砂轮锯片或者激光切割,切割尺寸精度≤50um;所述步骤s7中,采用的显微镜放大倍数≥200x。由于斜面的放大作用和选择性刻蚀液的增宽作用,用较低放大倍数的显微镜就能准确测量损伤层深度,降低了对于设备的要求,利于本方法推广应用。
14.进一步地,所述步骤s1中,采用砂轮锯片或激光切割,切割尺寸精度≤50um;所述步骤s2中,超声波清洗频率为40khz,超声波清洗时间为15 min,清洗温度为60℃;所述步骤s3中,烘干温度为105℃,烘干时间20 min,真空度为5~10kpa。对切割后的样品进行清洗可以去出样品表面的油脂和灰尘,在烘干去除水分,避免杂质对于镶嵌和显微镜观察的干扰,提高检测结果准确性。
15.进一步地,所述步骤s2中,所述表面活性剂选自十二烷基苯磺酸盐、氢氧化钠、乙二醇醚中的一种或多种。清洗剂中加入表面活性剂,对于油脂具有更好的清洗效果。
附图说明
16.图1为本发明具体实施方式中非金属材料亚表面损伤深度的表征方法的流程图;图2为本发明具体实施方式中样品镶嵌样脱模得到的样块的结构示意图;图3为本发明具体实施方式中样块磨抛处理后的结构示意图;图4为本发明具体实施方式中样块表面观测方式示意图;图5为本发明实施例1中显微镜的观测图。
17.附图说明:1-样品,2-亚表面损伤层,3-镶嵌树脂,4-垫块。
具体实施方式
18.为使本发明的上述目的、特征和优点能够更为明显易懂,下面结合附图对本发明的具体实施例做详细的说明。需要说明的是,以下各实施例仅用于说明本发明的实施方法和典型参数,而不用于限定本发明所述的参数范围,由此引申出的合理变化,仍处于本发明权利要求的保护范围内。
19.需要说明的是,在本文中所披露的范围的端点和任何值都不限于该精确的范围或值,这些范围或值应当理解为包含接近这些范围或值的值。对于数值范围来说,各个范围的端点值之间、各个范围的端点值和单独的点值之间,以及单独的点值之间可以彼此组合而得到一个或多个新的数值范围,这些数值范围应被视为在本文中具体公开。
20.本发明的具体实施方式提供一种非金属材料亚表面损伤深度的表征方法,结合图1至图4所示,表征方法包括以下步骤:s1、样品切割首先将待测样品1切割成方块,沿亚表面损伤层2的待测面垂直方向切割,保留待测面。切割方法可以使用砂轮锯片或者激光切割,切割尺寸精度≤50um,切成合适的大小,以便后续的显微镜下观察。
21.s2、样品清洗将切割好的样品1放入含有表面活性剂的清洗剂中,进行超声清洗,去除样品1表面的油脂和灰尘。表面活性剂主要成分为十二烷基苯磺酸盐、氢氧化钠、乙二醇醚等,用于提高油脂的清洗效果。具体实施方式中,超声清洗的工艺参数如下,频率为40khz,清洗时间为15min,清洗温度为60℃。
22.s3、样品烘干清洗后的样品1进行真空烘干,确保亚表面损伤层2中的水分彻底干燥。具体实施方式中,真空烘干的工艺参数如下,烘干温度为105℃,烘干时间20 min,真空度为5~10kpa。
23.s4、样品镶嵌将样品1放置在镶嵌模具内,镶嵌模具底部安装顶面倾斜角度为θ的垫块4,模具内加入镶嵌树脂3并固化,脱模得到样块,样块的结构如图2所示。
24.具体实施方式中,模具使用前喷涂脱模剂,便于树脂固化后脱离;镶嵌治具为了能更方便准确的观测到检测结果,需使研磨平面和待测面呈一定倾斜夹角θ,因此需要设置顶面倾斜角度为θ的垫块4,θ介于5
°
~10
°
之间。此倾斜角度对于损伤深度具有很好的放大作用,提高检测精度。镶嵌方法如下:将垫块4置于镶嵌模具底部正中心位置,样品1待测面朝
上置于支架上,将混合好的镶嵌树脂3缓慢倒入至浸没样品1,将样品1放入烘箱加热固化,固化条件取决于不同树脂类型。镶嵌树脂3需要有较大的硬度(>80hsd)和较小的体积收缩率(<5%),优选地,镶嵌树脂3由环氧树脂和固化剂组成,环氧树脂和固化剂的质量比为2:1,采用该树脂时固化温度为120℃,固化时间为2h。
25.s5、样块磨抛采用金相磨抛机,将固化好的样块依次进行表面磨抛,磨抛包括粗磨、精磨和抛光三个步骤。具体地,粗磨步骤采用金刚石研磨盘快速去除多余部分树脂,使样块接近观察表面,去除厚度为d1;精磨步骤采用柔软的聚合物研磨垫配合二氧化硅微粒研磨液进行初步抛光,二氧化硅微粒粒径为5~10um,去除厚度为d2;抛光步骤采用聚合物研磨垫配合纳米颗粒进行镜面抛光,将损伤层暴露出来,纳米颗粒粒径<1um,去除厚度为d3;其中d1》10d2》100d3,通过限定粗磨、精磨和抛光的厚度关系可以将样块精确加工至待测位置,防止研磨过程对真实结果的干扰,同时节省研磨处理时间。磨抛处理后的样块结构如图3所示。
26.进一步地,本步骤中控制金相磨抛机转速为300rpm,研磨压力为20n,保证磨抛过程中不会产生新的损伤,同时兼顾工作效率。
27.s6、样块选择性刻蚀将研磨好的样块置于选择性刻蚀液中浸泡,使损伤裂纹清晰的显现出来,根据样品1材质,选择不同的刻蚀液。当材料为晶体时,刻蚀的原则是只增加裂纹宽度,不改变深度;当材料为非晶体时,刻蚀原则为只显示出裂纹,不改变其宽度和深度。比如待测样品1为单晶硅材料,则选择性刻蚀液为氢氟酸和硝酸混合液,其中各成分的质量比为 hf:hno3:h2o=1:10:20,刻蚀时间为10min,采用该选择性刻蚀液可以增加裂纹宽度,但不会改变深度,便于显微镜观测。
28.s7、显微镜观测计算用显微镜对处理好的样块表面的待观测区进行测量,如图4所示,沿观测线进行观察,观测线与待观测区垂直,找到观测处最深的损伤点,此损伤点到树脂与损伤层交界处的垂直距离称为损伤层深度测量值,使用显微镜测量出该值,记为h
测
,计算损伤层深度实际值h
实
=h
测
*sinθ。由于斜面的放大作用和选择性刻蚀液的增宽作用,用较低放大倍数的显微镜就能准确测量损伤层深度,本步骤中采用的显微镜放大倍数≥200x即可。
29.上述非金属材料亚表面损伤深度表征方法将切割、样品清洗、真空烘干、样块镶嵌、磨抛、选择性刻蚀等步骤有机结合,特别是采用镶嵌树脂固定样品的方式可以保证待测面的倾斜角度精确,在后续磨抛过程中不会发生移位,从而提高了损伤深度检测结果的准确性和精度,为评估加工工艺的优劣,优化加工工序,实现材料表面“零损伤”的处理工艺提供数据支持。
30.实施例1本实施例测试单晶硅材料的亚表面损伤深度,方法步骤如下:使用砂轮锯片将待测样品切割成10mm*10mm的方块,沿亚表面损伤层的待测面垂直方向切割,切割尺寸精度≤50um。
31.将切割好的样品放入含有十二烷基苯磺酸盐的清洗剂中,进行超声清洗,超声波频率为40khz,清洗时间为15min,清洗温度为60℃。
32.清洗后的样品进行真空烘干,烘干温度为105℃,烘干时间20 min,真空度为5~
10kpa。
33.将样品放置在镶嵌模具内,模具使用前喷涂脱模剂,镶嵌模具底部安装顶面倾斜角度为10
°
的垫块,模具内加入镶嵌树脂并固化,镶嵌树脂由质量比为2:1的环氧树脂和固化剂组成,固化温度为120℃,固化时间为2h,固化后脱模得到样块。
34.采用金相磨抛机,先进行粗磨,采用金刚石研磨盘快速去除多余部分树脂,使样块接近观察表面;再进行精磨,采用柔软的聚合物研磨垫配合二氧化硅微粒研磨液进行初步抛光,二氧化硅微粒粒径为5~10um;最后进行抛光,采用聚合物研磨垫配合纳米颗粒进行镜面抛光,将损伤层暴露出来,纳米颗粒粒径<1um。上述步骤中金相磨抛机转速为300rpm,研磨压力为20n。
35.将研磨好的样块置于选择性刻蚀液中浸泡,选择性刻蚀液中各成分的质量比为 hf:hno3:h2o=1:10:20,刻蚀时间为10min。
36.s7、显微镜观测计算用放大倍数200x的显微镜对处理好的样块表面的待观测区进行测量,沿观测线进行观察,观测图像如图5所示,找到观测处最深的损伤点,此损伤点到树脂与损伤层交界处的垂直距离称为损伤层深度测量值,使用显微镜测量出该值,记为h
测
=8.3μm,计算损伤层深度实际值h
实
=h
测
*sin10
°
=1.44μm。
37.实施例2本实施例测试非晶体硅材料的亚表面损伤深度,方法步骤如下:使用激光将待测样品切割成5mm*5mm的方块,沿亚表面损伤层的待测面垂直方向切割,切割尺寸精度≤20um。
38.将切割好的样品放入含有乙二醇醚的清洗剂中,进行超声清洗,超声波频率为40khz,清洗时间为15min,清洗温度为60℃。
39.清洗后的样品进行真空烘干,烘干温度为105℃,烘干时间20 min,真空度为10kpa。
40.将样品放置在镶嵌模具内,模具使用前喷涂脱模剂,镶嵌模具底部安装顶面倾斜角度为5
°
的垫块,模具内加入镶嵌树脂并固化,镶嵌树脂由质量比为2:1的环氧树脂和固化剂组成,固化温度为120℃,固化时间为2h,固化后脱模得到样块。
41.采用金相磨抛机,先进行粗磨,采用金刚石研磨盘快速去除多余部分树脂,使样块接近观察表面;再进行精磨,采用柔软的聚合物研磨垫配合二氧化硅微粒研磨液进行初步抛光,二氧化硅微粒粒径为5~10um;最后进行抛光,采用聚合物研磨垫配合纳米颗粒进行镜面抛光,将损伤层暴露出来,纳米颗粒粒径<1um。上述步骤中金相磨抛机转速为300rpm,研磨压力为20n。
42.将研磨好的样块置于选择性刻蚀液中浸泡,选择性刻蚀液中各成分的质量比为 hf:hno3:h2o=1:1:5,刻蚀时间为5min。
43.s7、显微镜观测计算用放大倍数1000x的显微镜对处理好的样块表面的待观测区进行测量,沿观测线进行观察,找到观测处最深的损伤点,此损伤点到树脂与损伤层交界处的垂直距离称为损伤层深度测量值,使用显微镜测量出该值,记为h
测
=1.6μm,计算损伤层深度实际值h
实
=h
测
*sin10
°
=0.14μm。
44.虽然本发明披露如上,但本发明并非限定于此。任何本领域技术人员,在不脱离本发明的精神和范围内,均可作各种更动与修改,因此本发明的保护范围应当以权利要求所限定的范围为准。
再多了解一些
本文用于创业者技术爱好者查询,仅供学习研究,如用于商业用途,请联系技术所有人。