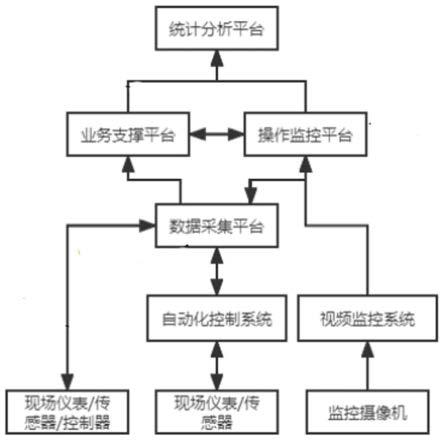
1.本发明涉及一种专门适用于管理、监督或预测目的的数据处理系统或方法,具体的说是一种适用于化工生产的操作管理系统及对应的管理方法。
背景技术:
2.化工是我国国民经济的基础产业和支柱产业,经过多年发展,已经覆盖了有机化学、无机化学、石油及制品、树脂、化学纤维、添加剂、日用化学品、试剂、染料、颜料、肥料、农药等诸多领域。化工生产涉及的危险品多,使用的原料、半成品和成品种类繁多,且绝大部分是易燃、易爆、易中毒、有腐蚀的危险化学品。生产工艺条件苛刻多数需要在高温、低温、高压、真空下进行。
3.目前我国许多化工生产企业已经从过去落后的手工操作、间歇性生产转变为自动化、连续化生产,但仍有大部分化工企业因为工艺原因、装备原因处于半自动、手动和间歇性生产,这在生产过程中的操作管理、能源管理、安全管理、环保管理都存在巨大的挑战,若操作人员未按规范要求操作,则很大程度上会引发安全、环保、质量事故和能源浪费。
4.经检索,中国专利申请号2011103941431公开了一种基于物联网的货物管理系统,包括货物登记模块,信息上传模块,服务器模块,统计小结模块和后台管理模块;该系统利用了物联网的方式,但只是针对货物管理,并不适用于化工操作管理。中国专利申请号2019105290465公开了一种基于物联网的安全管理方法,涉及企业安全生产管理领域,该方案关联了操作管理方法和设备设施管理方法,其利用各级安全责任人的指纹信息作为对应的安全责任节点,属于一种独特的管理模式。
技术实现要素:
5.本发明的目的是提供一种基于物联网的化工生产操作管理系统,解决的技术问题是:设计一套管理系统,便于化工生产更精细化管理,利用物联网能力对生产操作进行有效管理,从而避免生产过程的安全、质量事故的发生。
6.基于物联网的化工生产操作管理系统,包括数据采集平台、操作监控平台、业务支撑平台、统计分析平台;数据采集平台是指布置于生产现场内多个监测点的具有远传功能仪表所构成的一个平台用于生产现场的数据采集;现场仪表或传感器通过采集器或转换器或网关将数据传输至数据采集平台,亦可先将数据集中至自动化控制系统,再传输至数据采集平台处理并存储至服务器;操作监控平台用于对生产人员的生产操作过程进行监控及报警预警;业务支撑平台用于操作监控平台配套预设工艺操作模型、报警模型、报警处置模型,同时对操作监控平台反馈的信息进行判断是否触发模型;统计分析平台用于对生产过程的工序操作模型、报警模型、报警处置模型分别进行统计分析和评估;统计分析操作正确率、报警处置率,处置正确率、工艺点位平稳率从而
评估操作人员水平;其中:若工艺操作过程中工艺操作顺序、工艺参数控制、工艺时间控制与预设置存在偏离,则判定存在异常偏离,统计分析平台统计异常偏离的步骤数、预设置的总步数,此时操作正确率的统计公式为:;若报警处置时未严格按照参数、顺序以及时间要求处置,则判定此次报警处置异常,统计分析平台统计处置异常次数、报警总次数并计算处置正确率,此时处置正确率的统计公式为:;若在规定时间内无预设置的任何操作,则判定此次报警未处置,统计分析平台统计处置次数、报警总次数并计算报警处置率,此时报警处置率统计方式如下:;若在制定时间周期内,具体工艺点位存在报警,统计分析平台统计报警时间与总时间占比并计算工艺点位平稳率,此时工艺点位平稳率的统计公式为:。
7.所述仪表或传感器通过4-20ma模拟量或开关量或现场总线与采集器、转换器、网关、自动化控制系统相配置。
8.所述采集器、转换器、网关、自动化控制系统通过无线或有线方式与服务器之间实现数据交互。
9.所述自动化控制系统为固有型或集散型自动化控制系统。
10.所述操作监控平台包括现场视频监控,现场监控摄像机通过视频编码器、硬盘录像机与视频服务器匹配,视频服务器通过通讯网络与操作监控平台匹配。
11.基于物联网的化工生产操作管理办法,包括如下步骤:s1 :操作监控平台根据业务支撑平台预设置的工艺操作模型,提醒及引导操作人员按照工艺操作或控制同时形成操作记录,并将操作记录反馈至统计分析平台和业务支撑平台;s2 :在操作人员按照工艺操作过程中,根据业务支撑平台预设置的报警模型触发报警时,给与操作人员报警提醒;s3:当发生报警提醒后,操作监控平台将自动匹配业务支撑平台预设置的报警处置模型,提醒及引导操作人员报警处置,处置过程及结果反馈至统计分析平台和业务支撑
平台;s4 :业务支撑平台读取接收操作上述监控平台关于操作、控制、报警、处置的信息反馈,监控生产过程;s5:统计分析平台读取接收业务支撑平台及操作监控平台数据,对生产操作过程进行统计分析和评估。
12.所述提醒及引导是由数据采集平台接收并转发至自动化控制系统或现场控制器引导操作人员工艺操作或控制。
13.所述提醒及引导操作人员工艺操作或控制包括利用自动化控制系统操作执行控制和现场直接操作控制。
14.所述业务支撑平台预设置的报警模型包括工艺操作偏离报警、数据偏离报警、设备异常报警、用能异常报警;所述工艺操作偏离报警包括工艺操作顺序偏离、工艺参数控制偏离、工艺时间控制偏离;所述数据偏离报警包含数据超限、变化趋势过快过缓;所述设备异常报警包含设备故障、超负荷运行、异常停机、仪器仪表故障、离线;所述用能异常报警包含水、电、蒸汽、天然气的供能不平稳、供需不平衡、非必要用能。
15.本发明的有益效果是:1、利用数据采集平台将现场数据汇聚,通过操作监控平台是操作工人能够对化工生产过程中的工艺、安全进行有效的监控和控制,提高操作工人掌握生产现场情况的能力。
16.2、利用业务支撑系统预设置的操作模型能够对正常工艺操作进行提醒及引导,提高操作工人工艺操作能力。
17.3、利用业务支撑系统预设置的报警模型能够及时提醒现场生产的异常情况,提高操作工人生产现场异常感知能力。
18.4、利用业务支撑系统预设置的异常处置模型能够在生产异常时提醒及引导异常处置的方式,提高操作工人生产现场异常处置能力。
19.5、利用统计分析平台统计分析操作工人操作的正确率、报警率等,评估操作工人操作水平,同时可溯源整个生产过程的操作、工艺工况、报警信息。
20.6、基于物联网技术,通过生产过程监控、操作提醒、报警提醒、处置提醒等,促使操作工人规范性操作,提升产品质量、收率,提高安全生产能力。
附图说明
21.图1为本发明基于物联网化工生产操作管理系统的结构框图;图2为本发明基于物联网化工生产操作管理方法的流程图。
22.图3是报警模型的说明图;图4是操作模型的说明图。
具体实施方式
23.请参考图1至图4,图中的基于物联网的化工生产操作管理系统,主要用于生产过程管理,即生产过程中的工艺操作、安全等主要因素进行管理。该系统主要设计了四个平台,即数据采集平台、操作监控平台、业务支撑平台、统计分析平台。
24.数据采集平台对布置在车间生产线上对应多个监测点的远传功能仪表进行数据
采集,采集的方式可参考现有的modbus协议,同时利用有线方式进行数据交互。在实际应用中,也可应用在配电柜、仓库罐区、公用工程等生产现场,使用到的控制系统可以是固有型或集散型自控系统、现场控制器等设备进行数据采集和控制,采集及控制方式还可通过opc、profinet、profibus等常用工业协议,及利用有线的方式进行数据交互。上述仪表可通过4-20ma模拟量或开关量或现场总线与采集器、转换器、网关、自动化控制系统进行信息的处理。
25.操作监控平台实施对上述数据进行监控,从而判断生产人员的生产操作过程是否符合预定设定,如不符合则发出报警或预警动作。如可通过现场的视频监控,这样该视频监控将数据通过现有方式反馈至系统。
26.业务支撑平台先预设置各类模型,如工艺操作模型、报警模型、报警处置模型。如生产人员的生产操作与上述模型不对应即现有操作动作不符合事先设定操作动作,则表示未触发上述模型,操作监控平台发出报警或预警动作。
27.统计分析平台将操作监控平台、业务支撑平台的数据根据时间、批次等关键性节点分类同时进行统计分析和评估;统计分析操作正确率、报警处置率,处置正确率从而评估操作人员水平。
28.下面通过二个实施例来对上述内容进行阐述。
29.实施例1工序操作是生产过程的固定操作步骤,这些步骤通过业务支撑平台中的工序操作模型进行预设置,该模型可以规定操作的内容、操作的时间、操作的顺序。如:某产品工艺氯化反应工艺段操作要求打开氯气进料阀,调节至5%-10%,再打开进料泵,温度控制在50℃-60℃之间,保持反应50分钟-60分钟,完成后打开转料泵进入下一工艺段,则在工序操作模型中设置:步骤一:关联氯气进料阀点位,参数要求5%-10%;步骤二:关联进料泵点位,参数要求开;步骤三:关联反应釜温度点位,参数要求50℃-60℃,时间要求:50-60min;步骤四:关联转料泵点位,参数要求开。
30.当该产品开始生产到该步骤后,系统就根据预设置的操作要求通过操作监控平台进行持续式监测。操作工人在该产品开始生产到该步骤后,若实际操作中先打开进料泵,再将氯气进料阀调节至5%-10%,那么系统就会监测到氯气进料阀未调节至5%-10%区间时,进料泵的状态已经开启,则系统提示该步骤工艺操作顺序偏离。进入步骤三后,系统就会监测反应釜温度数据,若该数据未能够保持在50℃-60℃之间,则系统提示该步骤工艺参数控制偏离。进入步骤三后,系统就会进行计时,并持续监测转料泵状态,若计时时间未达到50分钟,转料泵已经打开,则系统提示该步骤工艺时间控制偏离。
31.实施例2a公司当前氯化苯车间具有氯化工艺、精馏工艺、干燥工艺、结晶工艺,以氯化工艺为例,氯化工艺相关控制及监测点位数据均接入dcs控制系统,包括进料泵启停/开关/能耗、进料调节阀开度/流量累计、反应釜温度/压力、冷冻水调节阀开度/温度、冷冻机组电流/振动。其中,氯化工艺操作要求为:先打开氯气进料阀,调节至5%-10%,再打开氯气进料泵,然后打开苯进料阀,调节至7%-8%,接着打开苯进料泵,在打开冷冻水调节阀,调节至
20%-25%之间,反应釜温度控制在-2℃-5℃之间,压力控制在0.5mpa-0.6mpa之间,保持反应50分钟-60分钟,完成后该工艺操作结束。若在反应釜温度控制不到位导致温度超过5℃时,需要将冷冻水调节阀调节至30%-35%。
32.通过数据采集系统,利用现有的opc、modbus等协议,对已接入dcs的数据进行采集处理及存储,并通过操作监控平台可视化展示。
33.根据氯化工艺操作要求,在业务支撑平台进行工艺操作模型预设置:步骤要求一:关联氯气进料阀点位,参数要求【5%-10%】;步骤要求二:关联氯气进料泵点位,参数要求【开】;步骤要求三:关联苯进料阀点位,参数要求【7%-8%】;步骤要求四:关联苯进料泵点位,参数要求【开】;步骤要求五:关联冷冻水调节阀点位,参数要求【20%-25%】;步骤要求六:关联反应釜温度点位,参数要求【-2℃-5℃】,关联反应釜压力点位,参数要求【0.5mpa-0.6mpa】,时间要求:【50-60min】;设置完成后,操作监控平台会根据步骤中关联点位的变化状态,自动提示下一步操作人员操作要求,如:系统监测氯气进料调节阀开度满足【5%-10%】时,系统自动提示下一操作【氯气进料泵:开】,以此引导操作工人正确操作。
34.按照工艺要求反应釜温度需控制在-2℃-5℃之间,若在反应釜温度控制不到位导致温度超过5℃时,按照处置要求需要将冷冻水调节阀调节至30%-35%。则在业务支撑平台异常处置模型预设置:处置要求一:关联冷冻水调节阀,参数要求【30%-35%】;处置要求一:关联反应釜温度点位,参数要求【-2℃-5℃】。
35.设置完成后,操作监控平台会根据处置要求,自动提示操作人员异常处置操作。
36.同时在生产过程中,还可以对其他影响生产的设备及相关数据,通过预设置报警模型,进行监控报警,如:冷冻设备故障时,严重影响制冷效果,导致反应釜温度无法控制在工艺要求内,则可以通过预设置报警模型:阈值报警:对冷冻机组出水温度设置对应阈值,温度超过阈值时,通过操作监控平台提示报警。
37.异常停机报警:对所有冷冻机组设置异常停机报警,如:3台冷冻机组必须开启一台,在全部关闭的情况下,通过操作监控平台提示报警。
38.超负荷运行报警:对冷冻机组设置超负荷运行报警,根据设备三向振动趋势,在振动频繁波动且位移幅度明显变大时,通过操作监控平台提示报警。
39.综上,根据操作模型设置的相关操作规范要求及监测的异常偏离次数即可统计操作正确率,若工艺操作过程中工艺操作顺序、工艺参数控制、工艺时间控制与预设置存在偏离,则判定存在异常偏离及统计异常偏离的步骤数、预设置的总步数,此时操作正确率的统计公式为:,如异常偏离的步骤数为1次,预设置的总步数为5次,则操作正确率为80%。
40.在化工生产过程中,有许多工艺参数点位是影响生产质量和安全,当这些工艺点
位发生异常时,需要通过人工干预处置。此时需要业务支撑系统预设置相关的报警模型,同时设置报警处置模型。报警模型中可配置常见的异常现象包括数据超限、设备异常停机等。
41.报警处置模型预设置与操作模型设置类似,可以规定处置的内容、处置的时间、处置的顺序。例:当某反应釜温度超高时,按照规范需要先关闭进料泵,然后打开循环水,若温度超过阈值2%时,循环水调节阀开度为25%,若温度超过阈值4%,循环水调节阀开度为50%, 若温度超过阈值6%,循环水调节阀开度为100%,处置过程须在5min中内完成,则在操作模型中设置前置条件:关联反应釜温度点位,计算反应釜温度数据超过阈值的百分比,并关联进料泵,参数要求为关,再关联循环水调节阀,参数要求根据计算的百分比设置对应的开度,设置整体处置要求5min。
42.若报警处置时未严格按照参数、顺序以及时间要求处置,则判定此次报警处置异常,统计分析平台统计处置异常次数、报警总次数并计算处置正确率,此时处置正确率的统计公式为:,如处置异常次数为5次,报警总次数为10次,则处置正确率为50%。
43.若在规定时间内无预设置的任何操作,则判定此次报警未处置,统计分析平台统计处置次数、报警总次数并计算报警处置率,此时报警处置率统计方式如下:,如处置次数为2次,报警总次数为2次,则报警处置率为100%。
44.若在制定时间周期内,具体工艺点位存在报警,统计分析平台统计报警时间与总时间占比并计算工艺点位平稳率,此时工艺点位平稳率的统计公式为:,如点位报警时长位1小时,总时长为2小时,则工艺点位平稳率为50%。
45.请参考图2,本案还涉及使用上述系统进行管理的方法,从工艺操作、安全的监控、预警、处置方面入手,上述方法包括如下步骤。
46.第一步:操作监控平台根据业务支撑平台预设置的模型如工艺操作模型、报警模型、报警处置模型,提醒及引导操作人员按照工艺操作或控制同时形成操作记录,并将操作记录反馈至统计分析平台和业务支撑平台。该步骤中,工艺操作模型预设置可以规范工艺的操作要求、参数要求、时间要求及顺序要求,根据现场操作数据反馈信息,分析操作人员是否按照规范要求操作,若操作人员未按要求操作将发出报警提示。例如:操作模型设置某产品工艺氯化反应工艺段操作要求【打开氯气进料阀,调节至5%-10%】-【打开进料泵】-【温度控制在50℃-60℃之间】-【保持反应50分钟-60分钟】-【打开转料泵进入下一工艺段】,若操作工人实际操作中先打开进料泵,再将氯气进料阀调节至5%-10%,则系统提示该步骤工
艺操作顺序偏离,若温度未能够保持在50℃-60℃之间,则系统提示该步骤工艺参数控制偏离,若反应时间未达到50分钟就打开转料泵,则系统提示该步骤工艺时间控制偏离。上述报警模型可以对生产过程中的设备异常、工艺工况异常、趋势异常、用能异常等规则进行预设置,当生产现状符合报警规则时及时报警提醒。例如:在废气处理工艺中碱洗塔主备风机在生产过程中必须开启任意一台,若两台同时关闭则系统提示碱洗塔风机异常停机,若两台同时开启持续时间超过规定时则系统发出节能提醒。
47.第二步:在操作人员按照工艺操作过程中,根据业务支撑平台预设置的报警模型触发报警时,给与操作人员报警提醒。
48.第三步:当发生报警提醒后,操作监控平台将自动匹配业务支撑平台预设置的报警处置模型,提醒及引导操作人员报警处置,处置过程及结果反馈至统计分析平台和业务支撑平台。
49.第四步:业务支撑平台读取接收操作上述监控平台关于操作、控制、报警、处置的信息反馈,监控生产过程。
50.第五步:统计分析平台读取接收业务支撑平台及操作监控平台数据,对生产操作过程进行统计分析和评估。
51.上述步骤中,业务支撑平台预设置的报警模型包括工艺操作偏离报警、数据偏离报警、设备异常报警、用能异常报警,实际应用中,还可增加其它模型。如图3所示,其中,工艺操作偏离报警,包含工艺操作顺序偏离、工艺参数控制偏离、工艺时间控制偏离以及其他非正常操作偏离;数据偏离报警,包含数据超限、变化趋势过快过缓以及其他非正常状态;设备异常报警,包含设备故障、超负荷运行、异常停机、仪器仪表故障、离线以及其他非正常状态;用能异常报警,包含水、电、蒸汽、天然气的供能不平稳、供需不平衡、非必要用能以及其他用能异常。同时,工艺参数可以包含现场的温度、压力、液位、浓度、流量、称重、电流以及其他影响生产的数据。设备可以包含仪器仪表、动力设备、压力容器、传热设备、传质设备、混合设备、分离设备、制冷设备、干燥设备、反应设备以及其他生产相关设备。
52.上述描述的具体实施例仅仅用以解释本技术方案,并不用于限定本技术方案。同时,在本技术方案的描述中,需要说明的是,除非另有明确的规定和限定,术语“固定”、“配合”、应做广义理解,例如,可以是固定连接,也可以是可拆卸连接,或一体地连接;可以是直接相连,也可以通过中间媒介间接相连,可以是两个元件内部的连通或两个元件的相互作用关系。对于本领域的普通技术人员而言,可以根据具体情况理解上述术语在本技术方案中的具体含义。
53.尽管已经示出和描述了本技术方案的实施例,对于本领域的普通技术人员而言,可以理解在不脱离本技术方案的原理和精神的情况下可以对这些实施例进行多种变化、修改、替换和变型,本技术方案的范围由所附权利要求及其等同物限定。
再多了解一些
本文用于创业者技术爱好者查询,仅供学习研究,如用于商业用途,请联系技术所有人。