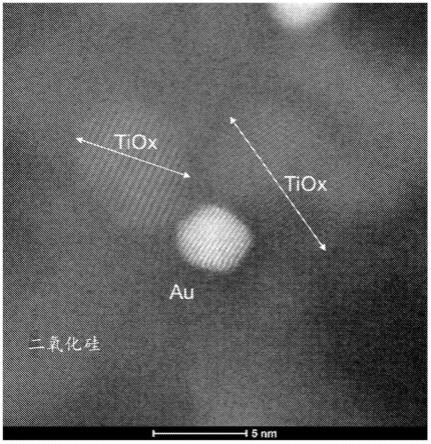
用长寿命催化剂进行氧化酯化的方法和催化剂
背景技术:
1.本发明涉及用于由甲基丙烯醛和甲醇制备甲基丙烯酸甲酯的催化剂和方法。
2.已知的是,具有集中在催化剂外部区域中的贵金属的非均相催化剂用于生产甲基丙烯酸甲酯,参见例如美国专利第6,228,800号。
3.wo 2019/057458公开了在催化剂颗粒存在下在液相中经由非均相催化由醛制备羧酸酯的方法。催化剂颗粒由以下组分组成:0.1重量%至3重量%的金、25重量%至99.8重量%的tio2、0重量%至50重量%的氧化硅、0重量%至25重量%的al2o3、0重量%至25重量%的碱金属、碱土金属、稀土金属和/或锆的至少一种氧化物、0重量%至20重量%的选自由氧化铁、氧化锌和氧化钴组成的组中的至少一种氧化物,以及0重量%至5重量%的至少一种其他组分。催化剂优选地主要或完全由金和tio2组成。
4.然而,需要一种用于生产甲基丙烯酸甲酯的改进的催化剂和方法,其在更长的生命周期内有效且具有活性。
技术实现要素:
5.本发明的一个方面涉及一种包含贵金属颗粒和含钛颗粒的催化剂,其中贵金属颗粒和含钛颗粒设置在载体的外表面上,其中贵金属颗粒的总重量的至少20重量%与至少一种含钛颗粒相邻,其中贵金属颗粒具有小于15nm的平均直径,并且其中催化剂具有至少200微米的平均直径。
6.本发明的另一方面涉及一种由甲基丙烯醛和甲醇制备甲基丙烯酸甲酯的方法;所述方法包括在反应器中使包含甲基丙烯醛、甲醇和氧气的混合物在包含贵金属颗粒和含钛颗粒的催化剂存在下接触,其中贵金属颗粒和含钛颗粒设置在载体的外表面上,其中贵金属颗粒的总重量的至少20重量%与至少一种含钛颗粒相邻,其中贵金属颗粒具有小于15nm的平均直径,并且其中催化剂具有至少200微米的平均直径。
附图说明
7.图1a和图1b是根据本发明实施方案的催化剂在不同放大倍数下的扫描tem图像。
8.图2a、图2b和图2c是根据本发明实施方案的催化剂在不同放大倍数下的扫描tem图像。
9.图3示出了根据本发明实施方案的催化剂的sem图像。
具体实施方式
10.除非另外指示,否则所有百分比组成都为重量百分比(wt%),并且所有温度都以℃为单位。除非另外指明,否则平均值是算术平均值。如本文所定义,术语“贵金属”是金、铂、铱、锇、银、钯、铑和钌中的任一种。超过一种贵金属可以存在于催化剂中,在这种情况下,限值应用于所有贵金属总体。“催化剂中心”是催化剂颗粒的质心,即,在所有坐标方向上所有点的平均位置。直径为穿过催化剂中心的任何线性尺寸,并且平均直径为所有可能
性直径的算术平均值。纵横比是最长直径与最短直径的比率。除非另外指明,否则颗粒的平均直径是指在制备催化剂之后和在使用催化剂之前的颗粒的平均直径。老化的催化剂是已被使用的催化剂。
11.本发明的催化剂包含贵金属颗粒和含钛颗粒,它们设置在载体的外表面上以形成催化剂颗粒。
12.贵金属颗粒和含钛颗粒优选地分散在载体的外表面上。不受理论的束缚,据信未共价结合到颗粒表面的颗粒可在颗粒表面周围迁移或移动。贵金属颗粒的活性可基于颗粒的尺寸而有很大变化。例如,随着颗粒尺寸的增加,金颗粒的催化活性降低。随着颗粒的迁移,贵金属颗粒可能会聚集,这会导致活性损失。本发明人已经发现,将贵金属颗粒分散在含钛颗粒中可以令人惊讶地使催化活性的损失最小化并提供更持久的催化剂。
13.优选地,贵金属颗粒的总重量的至少20重量%与含钛颗粒相邻。换句话讲,贵金属颗粒的总重量的至少20重量%与含钛颗粒物理接触。更优选地,贵金属颗粒的总重量的至少30重量%与含钛颗粒相邻。甚至更优选地,贵金属颗粒的总重量的至少40重量%与含钛颗粒相邻,并且还更优选地,贵金属颗粒的总重量的至少50重量%与含钛颗粒相邻。
14.含贵金属颗粒的平均直径小于15nm,优选地小于12nm,更优选地小于10nm,甚至更优选地小于8nm。
15.优选地,贵金属是金或钯,更优选地,贵金属包括金或由金组成。优选地,相对于贵金属的总量,贵金属包含至少75wt%的金。更优选地,相对于贵金属的总量,贵金属包含至少85wt%的金。
16.含钛颗粒可包含元素钛或氧化钛tio
x
。优选地,含钛颗粒包含氧化钛。
17.含钛颗粒的平均直径优选地小于贵金属颗粒平均直径的5倍,更优选地小于贵金属颗粒平均直径的4倍,甚至更优选地小于贵金属颗粒平均直径的3倍,还更优选地小于贵金属颗粒平均直径的2倍,并且还更优选地小于贵金属颗粒平均直径的1.5倍。
18.贵金属颗粒的重量相对于含钛颗粒的量可以在1:1至1:20范围内。优选地,贵金属颗粒与含钛颗粒的重量比为1:2至1:15,更优选地1:3至1:10,甚至更优选地1:3至1:6。
19.优选地,载体是能够承受在氧化酯化反应器中长期使用的难熔氧化物颗粒。能够长期使用的材料能够避免在使用期间被压碎或粉碎。例如,氧化钛(tio
x
)是高度耐酸的载体,但当它具有高表面积时,其机械性能会很弱。
20.优选地,载体是以下物质的颗粒:γ-、δ-或θ-氧化铝、二氧化硅、氧化镁、氧化锆、氧化铪、氧化钒、氧化铌、氧化钽、二氧化铈、氧化钇、氧化镧或它们的组合。优选地,载体包含γ-、δ-或θ-氧化铝、二氧化硅和氧化镁,由其组成,或基本上由其组成。更优选地,载体包含二氧化硅,由其组成或基本上由其组成。如本文关于载体所用,短语“基本上由
…
组成”排除了会降低载体机械强度的材料的存在。或者,“基本上由
…
组成”是指相对于载体的总重量,载体包含至少95wt%的所述材料。
21.优选地,载体的表面积大于10m2/g、优选地大于30m2/g、优选地大于50m2/g、优选地大于100m2/g、优选地大于120m2/g。
22.优选地,催化剂颗粒的纵横比不大于10:1,优选地不大于5:1,并且优选地不大于3:1。尽管形状不受限制,但催化剂颗粒的优选形状包括球形、圆柱形、矩形固体、环形、多叶形(例如,苜蓿叶形横截面)、具有多个孔的形状和“马车车轮”;优选球形。也可以使用不规
则形状。
23.优选地,至少90wt%的贵金属颗粒和含钛颗粒在催化剂体积(即平均催化剂颗粒的体积)的外部70%,优选地在催化剂体积的外部60%,优选地外部50%,优选地外部40%,优选地外部35%,优选地外部30%,优选地外部25%。优选地,对于具有沿着垂直于外表面的线测量的从其内表面到其外表面(催化剂颗粒的表面)的恒定距离的体积,计算任何颗粒形状的外部体积。例如,对于球形颗粒,体积的外部x%为球形壳体,其外表面为颗粒的表面并且体积为整个球形体积的x%。优选地,至少95wt%、优选地至少97wt%、优选地至少99wt%的贵金属颗粒和含钛颗粒在催化剂的外部体积中。优选地,至少90wt%(优选地至少95wt%、优选地至少97wt%、优选地至少99wt%)的贵金属颗粒和含钛颗粒距表面的距离不超过催化剂直径的30%、优选地不超过25%、优选地不超过20%、优选地不超过15%、优选地不超过10%、优选地不超过8%。沿着垂直于表面的线测量距表面的距离。优选地,贵金属颗粒和含钛颗粒在载体颗粒上形成蛋壳结构。蛋壳层可具有500微米或更小、优选地250微米或更小、更优选地100微米或更小的厚度。
24.优选地,催化剂颗粒的平均直径为至少60微米、优选至少100微米、优选至少200微米、优选至少300微米、优选至少400微米、优选至少500微米、优选至少600微米、优选至少700微米、优选至少800微米;优选不超过30mm、优选不超过20mm、优选不超过10mm、优选不超过5mm、优选不超过4mm。载体的平均直径和最终催化剂颗粒的平均直径没有明显不同。
25.优选地,以贵金属和载体的百分比计,贵金属的量为0.2wt%至5wt%、优选至少0.5wt%、优选至少0.8wt%、优选至少1wt%、优选至少1.2wt%;优选不超过4wt%、优选不超过3wt%、优选不超过2.5wt%。
26.根据至少一个实施方案,贵金属颗粒包含金,含钛颗粒包含氧化钛,载体为二氧化硅。
27.优选地,当本发明的催化剂用作氧化酯化反应催化剂时可长时间保持高活性。优选地,催化剂在使用100小时后,更优选地在使用500小时后,甚至更优选地在使用1000小时后,还更优选地在使用5000小时后,并且还更优选地在使用10,000小时后保持其初始活性的至少75%。或者,催化剂在使用以下实施例中所述的模拟方法模拟使用100小时后,更优选地在模拟使用500小时后,甚至更优选地在模拟使用1000小时后,还更优选地在模拟使用5000小时后,并且还更优选地在模拟使用10,000小时后保持其初始活性的至少75%。更优选地,催化剂在实际或模拟使用的100小时、500小时、1000小时、5000小时或10,000小时内保持其初始活性的至少80%。甚至更优选地,催化剂在实际或模拟使用的100小时、500小时、1000小时、5000小时或10,000小时内保持其初始活性的至少85%。还更优选地,催化剂在实际或模拟使用的100小时、500小时、1000小时、5000小时或10,000小时内保持其初始活性的至少90%。还更优选地,催化剂在实际或模拟使用的100小时、500小时、1000小时、5000小时或10,000小时内保持其初始活性的至少95%。如本文所用,活性被定义为时空产率(sty),单位为摩尔mma/小时-千克催化剂,如下文实施例中所述。
28.优选地,通过在载体存在下从金属盐的水溶液中沉淀贵金属和钛来生产催化剂。在一个优选的实施方案中,通过初步润湿技术生产催化剂,其中将合适的贵金属前体盐和钛盐的水溶液加入到多孔无机氧化物中,使得孔充满溶液,然后通过干燥除去水。然后通过煅烧、还原或本领域技术人员已知的其他预处理将所得材料转化为成品催化剂,以将贵金
属盐和钛盐分解成金属或金属氧化物。优选地,包含至少一个羟基或羧酸取代基的c
2-c
18
硫醇存在于溶液中。优选地,包含至少一个羟基或羧酸取代基的c
2-c
18
硫醇具有2至12个、优选地2至8个、优选地3至6个碳原子。优选地,硫醇化合物包含不超过4个、优选地不超过3个、优选地不超过2个总羟基和羧酸基团。优选地,硫醇化合物具有不超过2个,优选不超过一个的硫醇基。如果硫醇化合物包含羧酸取代基,则它们可以以酸形式、共轭碱形式或其混合物存在。特别优选的硫醇化合物包括硫代苹果酸、3-巯基丙酸、巯基乙酸、2-巯基乙醇和1-硫代甘油,包括它们的共轭碱。
29.在本发明的一个实施方案中,通过沉积沉淀生产催化剂,其中将多孔无机氧化物浸入包含合适贵金属前体盐和钛盐的水溶液中,然后通过调节溶液的ph值使盐与无机氧化物的表面相互作用。然后(例如通过过滤)回收所得的处理过的固体,然后通过煅烧、还原或本领域技术人员已知的其他预处理将贵金属盐和钛盐分解成金属或金属氧化物,从而转化为成品催化剂。
30.优选地,用于生产甲基丙烯酸甲酯(mma)的方法在氧化酯化反应器(oer)中进行。催化剂颗粒可存在于浆料或催化剂床中,优选催化剂床。催化剂床中的催化剂颗粒通常通过固体壁和通过筛子或催化剂载体网格保持在适当的位置。在一些配置中,筛网或网格在催化剂床的相对端上且固体壁在侧面上,尽管在一些配置中,催化剂床可被筛网完全包围。催化剂床的优选形状包括圆柱体、矩形固体和圆柱形壳体;优选圆柱体。oer还包含液相和气相,液相包含甲基丙烯醛、甲醇和mma,气相包含氧。液相还可以包含副产物,例如甲基丙烯醛二甲基缩醛(mda)和异丁酸甲酯(mib)。优选地,液相处于40℃至120℃的温度;优选地至少50℃,优选地至少60℃;优选地不超过110℃,优选地不超过100℃。优选地,催化剂床处于0psig至2000psig(101kpa至14mpa)的压力下;优选地不超过2000kpa,优选地不超过1500kpa。
31.oer通常产生mma,连同甲基丙烯酸和未反应的甲醇。优选地,以1:10到100:1、优选地1:2到20:1、优选地1:1到10:1的甲醇:甲基丙烯醛摩尔比将甲醇和甲基丙烯醛进料到反应器中。优选地,催化剂床还包含在催化剂上方和/或下方的惰性材料。优选的惰性材料包括例如氧化铝、粘土、玻璃、碳化硅和石英。优选地,惰性材料的平均直径等于或大于催化剂的平均直径,优选地不大于20mm。优选地,将反应产物进料到甲醇回收蒸馏塔,该蒸馏塔提供富含甲醇和甲基丙烯醛的塔顶料流;优选地,该流再循环回到oer。来自甲醇回收蒸馏塔的塔底料流包含mma、mda、甲基丙烯酸、盐和水。在本发明的一个实施方案中,mda在包含mma、mda、甲基丙烯酸、盐和水的介质中水解。mda可以在来自甲醇回收蒸馏塔的塔底料流中水解;所述流包含mma、mda、甲基丙烯酸、盐和水。在另一个实施方案中,mda在从甲醇回收底部物料流分离的有机相中水解。可能需要向有机相中添加水以确保存在足够的水用于mda水解;这些量可以容易地由有机相的组成确定。mda水解反应器的产物经相分离,并且有机相穿过一个或多个蒸馏塔以产生mma产物和轻质和/或重质副产物。在另一个实施方案中,水解可在蒸馏塔本身内进行。
32.一个优选实施方案为在再循环回路中具有冷却能力的再循环反应器。另一个优选实施方案为一系列反应器,在反应器之间具有冷却和混合能力。
33.优选地,反应器出口处的氧气浓度为至少0.5摩尔%、优选地至少2摩尔%、优选地至少3摩尔%;优选地不超过7摩尔%、优选地不超过6.5摩尔%、优选地不超过6摩尔%。
34.用于氧化酯化的固定床反应器的一个优选实施方案为滴流床反应器,其含有催化剂的固定床且使气体和液体进料均沿向下的方向穿过反应器。在滴流中,气相是连续的液相。因此,在固定床上方的反应器顶部的区域将充满氮气、氧气和挥发性液体组分在其各自的蒸气压下的气相混合物。在典型的操作温度和压力(50℃至90℃和60psig至300psig(400kpa至2000kpa))下,如果气体进料是空气,则该蒸气混合物在易燃包壳内。因此,仅需要点火源即可启动爆燃,这可能导致主安全壳的损失且损害附近的物理基础设施和人员。为了解决工艺安全性考虑,操作滴流床反应器同时避免易燃的顶部空间气氛的方法是用含足够低的氧气摩尔分数的气体进料进行操作,以确保蒸气顶部空间中的氧浓度低于极限氧浓度(loc)。
35.有关的燃料混合物、温度和压力需要了解loc。由于loc随着温度和压力的升高而降低,且考虑到甲醇给出的loc低于其他两种重要燃料(甲基丙烯醛和甲基丙烯酸甲酯),因此保守的设计选择一进料氧氮比,其确保具有低于在最高预期操作温度和压力下的loc的组成。例如,对于在高达100℃和275psig(2mpa)下操作的反应器,氮气中的进料氧浓度不应超过7.4mol%。
36.实施例
37.实施例#1
38.单程固定床鼓泡塔反应器操作:
39.将由20重量%的甲基丙烯醛、200ppm的抑制剂和余量甲醇组成的进料以40克/小时的速率进料到含有短前段硼硅玻璃珠、接着为5g的催化剂的3/8”(9.5毫米)不锈钢管式反应器中。使用催化剂#1。还以足以在排气口处获得4.5%o2的速率将在氮气中含有8%氧气的气体进料到反应器中。在60℃和160psig(400kpa)下操作反应器。将反应器的产物传送到液气分离器中,并将蒸气传送到冷凝器中,并使液体返回,并且使不可冷凝气体前往排气口。结果在下表中列出。以这种方式运行催化剂#1和催化剂#8。
40.催化剂#1制备:
41.通过初步润湿技术使用20g富士硅化学株式会社(fuji silysia chemical,ltd.)的cariact q-10二氧化硅载体作为起始材料,并将钛添加到载体材料中来制备#1催化剂。具体地说,将10.5g异丙醇钛以及3g冰乙酸添加到于旋转设备中的催化剂中以确保溶液向载体材料的均匀分布。当添加时,溶液处于40℃下。随后,将改性的载体材料在略微真空下在60℃下干燥4小时,并且随后在空气中在环境压力下通过以下进行煅烧:将温度以5℃/分钟从环境温度缓慢升温到125℃,保持1小时,并且随后以5℃/分钟缓慢升温到250℃并保持1小时,随后以5℃/分钟缓慢升温到350℃并保持1小时,并且最后以5℃/分钟缓慢升温到450℃并保持4小时。然后,在40℃下通过初步润湿技术利用含0.83g硫代硫酸金钠的10g去离子水将金添加到载体中。在空气中使用与上文相同的加热概况干燥并煅烧所得催化剂。用配备有能量色散光谱(eds)的扫描电子显微镜(sem)进行的催化剂分析清楚地表明,存在ti和au两者的蛋壳沉积,其中au优选地仅位于ti沉积之处。发现ti和au蛋壳厚度为约50微米或更小。在1mm直径催化剂的外部50微米中所估计的负载量为10mol%的情况下,钛的局部负载量根据ti/(ti si)估计为至多40mol%。
42.实施例#2
43.间歇循环固定床鼓泡塔反应器操作:
44.制备包含10wt%甲基丙烯醛、200ppm抑制剂和余量甲醇的150g进料溶液,并放置在充当气体分离容器的300ml 反应器中。将容器液体维持在约20℃的温度下。将液体进料以7ml/min的速度从气体分离容器中泵入垂直定向的固定床反应器的底部。将空气和氮气混合以获得7.8mol%的氧气,并将其与液体进料混合,之后进入固定床反应器。固定床反应器是带夹套的1/4”(6.4mm)不锈钢管,使用外部加热器维持在60℃。反应器自身装有2mm的玻璃珠以填充大约18英寸(45.7cm)的管,随后装有催化剂。反应器顶部的剩余空隙用3mm玻璃珠填充。将离开反应器顶部的液体和气体传送到冷凝器中,并排出不可冷凝气体,同时液体再循环回到气体分离容器中。以这种方式运行催化剂#2以及来自以下实施例#3、#4、#5、#7和#8的催化剂。
45.催化剂#2制备:
46.通过将4.1g硫代硫酸金钠溶解于100g水中以制备水溶液并随后置于100g富士硅化学株式会社的cariact q-20二氧化硅载体材料上的初步润湿来制备催化剂#2。将样品在120℃下干燥1小时,接着在400℃下煅烧4小时。
47.实施例#3
48.催化剂#3制备:
49.通过以下步骤制备催化剂#3。首先,将由51.7g异丙醇钛和28.5g冰乙酸组成的钛前体储备溶液混合并在环境温度下搅拌。随后,通过将27.9g上述钛储备溶液浸渍到20g富士硅化学株式会社cariact q-10二氧化硅载体材料的初步润湿点来制备载体材料。随后,将样品在125℃下干燥1小时,接着在250℃下煅烧1小时,在350℃下煅烧1小时,并在450℃下煅烧隔夜,其中在不同温度设定之间缓慢升温速率为5℃/分钟。通过将含有0.4g硫代硫酸金钠和16g去离子水的溶液浸渍到10g上述载体材料中,达到其初步润湿点来实现金沉积。然后将样品在120℃下干燥1小时,接着在400℃下煅烧4小时。用配备有能量色散光谱(eds)的扫描电子显微镜(sem)进行的催化剂分析清楚地表明,存在ti和au两者的蛋壳沉积,其中au优选地仅位于ti沉积之处。发现ti和au蛋壳厚度为约300微米或更小。
50.实施例#4
51.催化剂#4制备:
52.通过以下步骤制备催化剂#4。首先,通过将异丙醇钛浸渍到10g富士硅化学株式会社cariact q-10二氧化硅载体材料的初步润湿点来制备载体材料。随后,将样品在125℃下干燥1小时,接着在250℃下煅烧1小时,在350℃下煅烧1小时,在450℃下煅烧1小时并在550℃下煅烧12小时,其中在不同温度设定之间缓慢升温速率为5℃/分钟。通过将含有0.25g硫代硫酸钠金和9g去离子水的溶液浸渍到6g上述载体材料的初步润湿点来实现金沉积。然后将样品在120℃下干燥1小时,随后在400℃下煅烧4小时。
53.实施例#5
54.催化剂#5制备:
55.通过以下步骤制备催化剂#5。首先,通过将硝酸镁六水合物浸渍到10g富士硅化学株式会社的cariact q-10二氧化硅载体材料的初步润湿点来制备载体材料。随后,将样品在120℃下干燥1小时,接着在450℃下煅烧4小时,其中在不同温度设定之间缓慢升温速率为5℃/分钟。混合8.5g量的异丙醇钛和1.5g量的乙酸以得到钛前体溶液,并且随后将3.1g的钛前体溶液浸渍到上述经煅烧的mg-sio2中。随后,将样品在120℃干燥1小时,接着在550
℃下煅烧6小时,其中在不同温度设定之间缓慢升温速率为5℃/分钟。通过将含有0.3g硫代硫酸金钠和8g去离子水的溶液浸渍到8g上述载体材料的初步润湿点来实现金沉积。随后,将样品在120℃干燥1小时,接着在400℃下煅烧4小时。所得的样品在si上包含总计4.7wt%mg和4wt%ti,1.5wt%au负载于该材料上。未评估样品以确定是否存在蛋壳沉积。
56.表1:催化剂性能
[0057][0058]
*sty是以每千克催化剂每小时的mma摩尔数计的时空产率。sty是催化剂活性的量度。归一化mma选择率为以甲基丙烯醛反应物形式起源的产物中的mma百分比。
[0059]
新鲜催化剂与老化催化剂的比较:
[0060]
实施例#6
[0061]
进行中试装置操作,然后进行单程固定床鼓泡塔反应器操作:
[0062]
作为老化过程的第一步,催化剂#6在中试装置操作中运行2000小时。反应器是以向上流动鼓泡塔再循环模式操作的绝热固定床反应器。将空气和液体进料送入垂直排列的反应器的底部,2英寸(5.1cm)od和1.62英寸(4.1cm)id
×
108英寸(2.7m)长的绝热316ss管。液体通过3/8”(9.5mm)管线进入反应器的底部,同时经由1/8”(3.2mm)管线将气体引入底部。将产物再循环以向稀释反应器进料,从而降低绝热温升。在一系列四个带夹套的316ss管(3/8”(9.5mm)od内管和1”(2.5cm)od外管)上将液体进料预热至期望的设定点。带夹套区段中的每个为5英尺(1.5m)长。将反应器产物送至气液分离容器,该容器带有夹套并用冷却水将其冷却。将分离容器冷却以使不希望的均相化学物质最小化。在该阶段的典型操作条件下,容器内的温度在23℃至28℃之间变化。使用三个叶轮以100rpm的速度搅拌气液分离罐。离开分离罐的产物在送至分离系统之前通过0.1μm精制过滤器。在精制过滤器之后收集oer产物样品,同时从进料混合罐收集进料样品。典型的操作条件是入口温度为或接近50℃、280psig(2mpa)、进料中40wt%甲基丙烯醛以及抑制剂和余量甲醇,以及50%甲基丙烯醛转化成mma。反应器中总共使用了1900g催化剂。还以足以在排气口处获得5%o2的速率将空气进料到反应器中。
[0063]
在中试装置中操作2000小时后,去除催化剂并将5g催化剂置于单程固定床鼓泡塔反应器中。将由20wt%的甲基丙烯醛、200ppm的抑制剂和余量甲醇组成的进料以20g/h的速率进料到包含短前段硼硅玻璃珠、接着为5g催化剂的3/8”(9.5毫米)不锈钢管式反应器中。还以足以在排气口处获得5%o2的速率将在氮气中含有8%氧气的气体进料到反应器中。在65℃和160psig(1mpa)下操作反应器。将反应器的产物传送到液气分离器中,并将蒸气传送到冷凝器中,并使液体返回,并且使不可冷凝气体前往排气口。反应器已运行超过11个月。
[0064]
催化剂#6制备:
[0065]
催化剂是在2mm cariact q10(二氧化硅)球上的au,其中首先向该球添加了二氧化钛。催化剂由clariant生产。通过naa-icp测量的金属负载量为1.32 /-0.01wt%au和7.1 /-0.1wt%ti。催化剂分析包括透射电子显微镜(tem)、扫描电子显微镜(sem)和能量色散x射线光谱仪(eds)。新鲜催化剂结果表明新鲜金纳米颗粒的平均尺寸为2.8 /-1.3nm。中试装置和实验室反应器老化的催化剂结果表明,在2000小时中试装置阶段结束时,平均纳米颗粒尺寸增长至6.0 /-2.3nm。催化剂#6的结果示于下表2中。
[0066]
表2
[0067][0068]
*sty是以每千克催化剂每小时的mma摩尔数计的时空产率。sty是催化剂活性的量度。归一化mma选择率为以甲基丙烯醛反应物形式起源的产物中的mma百分比。
[0069]
实施例#7
[0070]
催化剂#7新鲜催化剂制备和扫描tem分析:
[0071]
制备由溶解在13.5g去离子水中的0.39g硫代硫酸金钠组成的溶液并搅拌30分钟。将该溶液施加到10g ti掺杂的cariact q-10二氧化硅上,其包含6.6wt%ti且由clariant公司制备。将浸渍的材料在120℃下干燥1小时,然后在具有50lph空气流的箱式炉中在450℃的温度(5℃/min升温)下煅烧以产生成品催化剂。通过扫描tem分析催化剂。
[0072]
如图1a和图1b所示,在金颗粒的边界上识别出尺寸为约4.1nm的tiox颗粒。在扫描tem图像中被看作亮点的金颗粒具有小于10nm的平均直径。
[0073]
催化剂#7gama老化的催化剂制备和扫描tem分析:
[0074]
使用金团聚和运动评估(gama)老化方法快速老化以上制备的用于扫描tem分析的新鲜催化剂,以确定在类似于中试装置老化的条件下催化剂是否失活。
[0075]
gama测试装置由45ml带特氟隆内衬的ss酸消化容器(额定压力为1800psi(12,410kpa))组成。将3g催化剂与30ml含有4wt%maa和6wt%h2o的甲醇溶液一起置于该容器中。将容器置于200℃的箱式烘箱中10天。
[0076]
将gama老化的结果与新鲜催化剂的结果进行比较,示于下表3中。新鲜催化剂具有4.1nm的平均金颗粒尺寸。gama老化的催化剂具有5.1nm的平均金颗粒尺寸。gama老化的催化剂的扫描tem图像示于图2a、图2b和图2c中。
[0077]
表3
[0078][0079]
*sty是以每千克催化剂每小时的mma摩尔数计的时空产率。sty是催化剂活性的量度。归一化mma选择率为以甲基丙烯醛反应物形式起源的产物中的mma百分比。
[0080]
催化剂#7sem分析:
[0081]
使用sem成像观察金纳米颗粒的迁移。通过煅烧含硫的金盐在催化剂表面上形成金颗粒(图3(a))。一旦在表面上,纳米颗粒开始迁移(图3(b))。金颗粒移动远离硫沉积物,最终从催化剂中浸出,并且当金颗粒到达二氧化钛颗粒时(图3(c)),它们变得锚固在二氧化钛上。
[0082]
实施例#8-比较例
[0083]
在间歇循环固定床鼓泡塔反应器中测量新鲜催化剂#8的活性,如实施例#2中首先描述的。在该测量之后,将催化剂进行gama老化。与催化剂#7一样,gama测试装置由45ml带特氟隆内衬的ss酸消化容器组成,向容器中置入3g催化剂和30ml含有4wt%maa和6wt%h2o的甲醇溶液。将容器置于200℃的箱式烘箱中10天。然后如上文实施例#1中所述在单程固定床鼓泡塔反应器中测量gama老化的催化剂的活性。通过扫描tem估计新鲜催化剂#8的平均金纳米颗粒尺寸为4.0nm。通过扫描tem估计gama老化的催化剂的平均金纳米颗粒尺寸为10.3nm。催化剂#8的结果示于下表4中。
[0084]
催化剂#8制备:
[0085]
通过将4.1g硫代硫酸金钠溶解于100g水中以制备水溶液并随后置于100g富士硅化学株式会社的cariact q-20c二氧化硅载体材料上的初始润湿来制备催化剂。将样品在120℃下干燥1小时,接着在400℃下煅烧4小时。
[0086]
表4
[0087][0088]
*sty是以每千克催化剂每小时的mma摩尔数计的时空产率。sty是催化剂活性的量度。归一化mma选择率为以甲基丙烯醛反应物形式起源的产物中的mma百分比。
[0089]
抗压强度:
[0090]
通过将颗粒压碎到机械故障点来直接测量催化剂或催化剂载体颗粒的机械强度。使用mecmesin m100ec进行抗压强度测试。将单个颗粒放置在平台上并使顶部柱塞按压颗粒直到负荷达到峰值并且材料失效为止。使用shimpo fge-100x计量器记录峰值负荷。对25
个单独颗粒进行重复测试以获得任何给定材料的抗压强度的统计平均值。结果示于下表5中。
[0091]
表5:机械强度
[0092]
再多了解一些
本文用于创业者技术爱好者查询,仅供学习研究,如用于商业用途,请联系技术所有人。