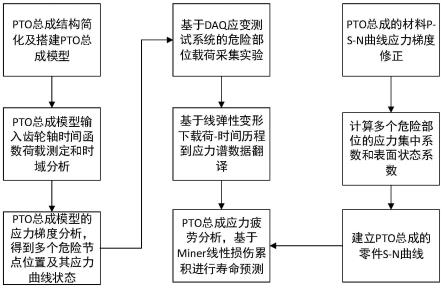
一种针对水田动力机械pto总成疲劳寿命预测方法
技术领域
1.本发明涉及传动机构整体疲劳寿命预测分析的技术领域,尤其涉及一种针对水田动力机械pto总成疲劳寿命预测方法。
背景技术:
2.中国南方地区多山地丘陵,特别是岭南一带,大多数水稻种植模式为区块化、隔带化,大规模的水稻种植面积区还没生成,随着农业机械化的不断发展和产品更迭,水田轻型动力机械更适应于目前的种植环境,并且农机的一机多用和简单可操作性更是广大农户群体所极力欣赏的,所以为了实现水田动力机械的一机多用,其动力输出装置(power take off,简称pto总成)需要满足不同机具在不同实际工况下的疲劳寿命要求,防止整机工作过程中机械核心零件破坏、水田直播过程中机器停罢和安全事故的发生等。传动啮合齿轮作为pto总成传动过程中的核心构件,它的疲劳变形决定着整个pto总成动力传动的效能和可靠性。因此,为保证水田动力机械pto总成结构满足整机实际工况的疲劳寿命要求,需要对传动轴和传动齿轮这类结构进行充分的、科学的寿命预测和校核,必须发展一种规范化的水田动力机械pto总成整体结构疲劳寿命分析技术。
3.pto总成的输入转矩为发动机通过变速箱输出的转矩,同时要受到底盘架构的振动激励,这种振动激励包括粗犷地形、颠簸路面以及水田泥脚不齐等外在复杂环境对pto总成的外在载荷影响,在啮合齿轮高速传动下为了精确分析疲劳寿命还需考虑惯性力和阻尼对pto的影响,这样就需要对pto展开瞬态动力学分析,这种复杂动态载荷输入下对总成结构进行的瞬态动力学分析可以很全面的仿真其所受应力大小和应力分布状态。目前国内外诸多学者主要针对核心零部件在理论和试验的基础上对结构疲劳进行了深入研究,建立了大量的疲劳寿命预测方法。赵雪彦基于传统的应力场强法对零件的疲劳分析方法做了优化,并且将优化后的应力场强法和传统的应力场强法、名义应力法和局部应变法四者之间进行了实验验证对比,得出优化后的疲劳分析方法的适用性。杨子涵针对传统传动系载荷谱编制过程中雨流计数及雨流域外推方法的局限性,提出基于pot模型的大功率拖拉机传动轴载荷时域外推方法,载荷谱的编制过程中可以获得任意历程的载荷时间序列,并能够极大程度保留实测载荷循环的次序。这些基于实测试验的疲劳分析方法和载荷谱测定方法等都优化了理论方法,但缺少了对整体式传动系统有针对性的试验设计和疲劳分析施展步骤,也缺少了在疲劳分析过程中考虑材料结构尺寸、应力集中、表面状态和温度等对整体结构的影响,并且像pto总成这样的整体结构在疲劳寿命预测的过程中田间试验测试系统测得载荷数据对pto总成关键部位位置确定和定点疲劳分析是关键的,那么这样室内台架实验往往在某种程度上是不能达到预期效果的,从而无法对结构或机械的疲劳寿命做出准确的分析。
4.综上所述,目前现有的针对pto总成整体结构的疲劳寿命分析方法仍有一定的局限性,从实验最开始的受力数据采集和载荷谱编制到疲劳分析方法的优化,均少有综合考虑应力水平、应力集中、表面状态、温度等影响因素。随着从零部位到整体式结构疲劳寿命
分析理论的进一步完善和发展,对pto总成结构整体进行疲劳寿命分析将是一个迫切需要解决的关键问题,这也对工程实际中水田动力机械的寿命分析和结构完整性具有重要意义。
技术实现要素:
5.本发明的目的是为了克服以上现有技术存在的不足,提供了一种针对水田动力机械pto总成疲劳寿命预测方法。
6.本发明的目的通过以下的技术方案实现:一种针对水田动力机械pto总成疲劳寿命预测方法,包括以下步骤:
7.s1、将pto总成的结构简化并形成三维模型,所述三维模型利用有限元分析软件建立pto总成模型;
8.s2、针对所述pto总成模型进行时间函数载荷试验测定和瞬态动力学分析,得到瞬态动力学分析结果;
9.s3、根据所述瞬态动力学分析结果,对所述pto总成模型进行应力梯度分析,得到多个危险节点位置及其应力曲线状态;
10.s4、根据多个危险节点位置及其应力曲线状态,基于daq应变测试系统,在所述pto总成中选择多个危险部位,对多个所述危险部位进行载荷采集实验,得到载荷-时间历程谱;
11.s5、基于线弹性变形下,选取多个危险节点位置的荷载时间历程,对所述载荷-时间历程谱进行翻译,得到实测应力谱数据;
12.s6、针对pto总成的材料进行p-s-n曲线应力梯度修正得到材料疲劳寿命曲线;
13.s7、根据步骤s4中的多个所述危险部位计算,得到应力集中系数和表面状态系数;
14.s8、根据步骤s6中的所述p-s-n曲线、步骤s7中的所述应力集中系数和所述表面状态系数,建立所述pto总成的零件s-n曲线;
15.s9、根据步骤s5中所述实测应力谱数据和步骤s8中的所述s-n曲线,所述pto总成进行应力疲劳分析,基于miner线性损伤累积预测所述pto总成的疲劳寿命。
16.更优的选择,步骤s2包括以下步骤:
17.s201、对所述pto总成模型进行模态分析,得到模态分析结果;
18.s202、根据所述模态分析结果确定所述pto总成模型的固定频率,根据所述固定频率,在瞬态动力学分析下,所述pto总成模型的时间步长限定平动范围;
19.s203、所述pto总成结构安装有扭矩传感器,所述扭矩传感器收集的信号经过数据处理模块处理得到转矩-时间历程载荷谱;
20.s204、所述转矩-时间历程载荷谱输入瞬态动力学分析中,得到所述瞬态动力学分析结果。
21.更优的选择,步骤s4包括以下步骤:
22.s401、所述daq应变测试系统包括无线应变传感器系统、数据调离采集模块、数据采集卡和数据分析系统,所述无线应变传感器系统安装于多个所述危险部位;
23.s402、所述无线应变传感器系统将信号数据传输给数据调离采集模块,所述数据调离采集模块对信号数据修正并放大后传输到数据采集卡;
24.s403、所述数据采集卡将信号数据传输到所述数据分析系统,所述数据分析系统处理得到所述载荷-时间历程谱。
25.更优的选择,步骤s401中的所述无线应变传感器系统包括微型电源、应变传感器和信号发射器,所述应变传感器和所述信号发射器均与所述微型电源连接,所述应变传感器安装于多个所述危险部位,所述应变传感器通过所述信号发射器与所述数据调离采集模块连接。
26.更优的选择,步骤s6中的所述p-s-n曲线的公式为:
27.lgn
p
=α
p-b
p
lg(1 k)σ)
28.其中,所述np为存活率为p时的所述pto总成的材料疲劳寿命,所述α
p
和所述b
p
为与存活率有关的所述pto总成的材料常数,所述k为调整系数,所述σ为考虑所述危险部位的应力梯度修正系数后的应力值。
29.更优的选择,步骤s4中的所述危险部位的数量在4个以上。
30.更优的选择,步骤s8中的所述s-n曲线符合公式:
[0031][0032]
其中,所述kt为所述s7中的所述应力集中系数,所述p为误差系数,所述β为步骤s7中的所述表面状态系数,所述a为引入表面状态调整系数。
[0033]
本发明相对现有技术具有以下优点及有益效果:
[0034]
本发明通过一种针对水田动力机械pto总成疲劳寿命预测方法,优化了结构疲劳可靠性分析过程,对整体式结构动力传动疲劳分析引入田间实测载荷数据,通过搭建daq应变测试系统对结构内部应力和应变做实际测量,将测量结果运用到有限元动力学分析中,保证结果可靠,疲劳寿命具有可参考性,可以保证pto总成在后期实际工作中的寿命要求,本发明还优化了疲劳寿命预测系数,让原来的寿命预测值和实际值更接近,可为复杂整体结构进行疲劳寿命预测提供科学理论依据。
附图说明
[0035]
图1是本发明一种针对水田动力机械pto总成疲劳寿命预测方法的流程示意图;
[0036]
图2是本发明一种针对水田动力机械pto总成疲劳寿命预测方法的pto总成结构三维模型示意图;
[0037]
图3是本发明一种针对水田动力机械pto总成疲劳寿命预测方法的固定棘爪换挡齿轮(齿数为15个)和中间轴换挡齿轮(齿数为34个)的网格划分局部图;
[0038]
图4是本发明一种针对水田动力机械pto总成疲劳寿命预测方法的7个危险节点位置粘贴应变传感器的示意图;
[0039]
图5是本发明一种针对水田动力机械pto总成疲劳寿命预测方法的应力梯度修正后的p-s-n曲线示意图;
[0040]
图6本发明一种针对水田动力机械pto总成疲劳寿命预测方法的关键传动齿轮疲劳寿命分析流程图;
[0041]
附图标记:1、输入齿轮轴;2、固定棘爪换挡齿轮;3、离合器固定棘爪;4、离合器轴;5、中间轴换挡齿轮;6、中间齿轮轴;7-13、危险节点位置。
具体实施方式
[0042]
下面结合附图和具体实施例对本发明的发明目的作进一步详细地描述,实施例不能在此一一赘述,但本发明的实施方式并不因此限定于以下实施例。
[0043]
如图1所示,一种针对水田动力机械pto总成疲劳寿命预测方法,包括以下步骤:
[0044]
s1、本实施例中以穴距16cm的啮合齿轮为例,忽略不参与传动的齿轮对轴的作用力,轮齿接触处利用泛函数法配合,将pto总成结构简化并装配组成三维模型,如图2所示,利用有限元(ansys workbench)软件进行网格划分,定义单元属性、单元实常数和材料属性参数等,完成建立pto总成模型。具体步骤如下:首先定义单元类型为实体solid类型,材料类型为线弹性材料,弹性模量为2.09
×
10
11
g/cm^2,泊松比为0.269,密度为7.85g/cm3,网格划分选择四面体单元,在齿轮啮合处和齿轮与轴的结合处对网格加密优化处理,尽可能控制结构危险部位的网格精密度,图3为固定棘爪换挡齿轮和中间轴换挡齿轮的网格划分局部图。根据模型形状特点以及可能出现较大应力区域,针对性优化网格,选择网格大小为2mm,其余地方保持默认,尽量控制网格数量在十五万个左右,保证有限元分析精度的同时也能有较快的运算速度。
[0045]
s2、对pto总成模型的pto总成模型的输入齿轮轴进行时间函数载荷试验测定和时域分析,得到瞬态动力学分析结果。
[0046]
设计时间函数载荷试验来测定输入齿轮轴的动态转矩-时间历程,包括田间实测载荷试验平台搭建和数据处理,在pto总成模型的变速箱输出轴和pto输入轴的靠近pto端上安装扭矩传感器,将试验过程中采集的信号通过降噪滤波和低通滤波信号处理后传输到数据处理模块,利用实验室虚拟仪器工程平台(labview)数据分析软件对所采集的数据进行处理得到转矩-时间历程载荷谱,用于瞬态动力学分析下的载荷输入。将该动态时间载荷历程载荷谱加载到labview软件的分析模块作为外部载荷输入,分析过程中必须限制总成结构在x、y和z三个轴上的平动;步骤s2包括以下具体步骤:
[0047]
s201、对pto总成模型进行模态分析,得到模态分析结果。
[0048]
将步骤s1中的pto总成模型输入到模态分析中,设置45号钢的弹性模量ex和密度dens,并且完全忽略材料的非线性特性,添加约束条件为三个轴向的转动,限制三个轴向的平动,进行求解。
[0049]
s202、根据模态分析结果,确定pto总成模型的固定频率和振型,用于估算求解控制参数。根据固定频率,在瞬态动力学分析下,pto总成结构的时间步长达到精度要求的同时在一个相对较小的范围内。pto总成结构在模态分析中需要定义材料的弹性模量、泊松比以及材料密度,边界条件的施加需要限制x、y和z三个方向上的平动。
[0050]
结合pto总成在实际工况下的自身振动对输入载荷响应的影响,通过模态分析确定总成整体传动过程中的固有频率wi,该固有频率用于确定瞬态动力学分析的合理时间步长,假设振动为自由振动并且不考虑阻尼的情况下所述方程为:
[0051]
[0052][0053]
其中,[m]表示质量矩阵,[k]表示刚度矩阵,[c]表示阻尼矩阵,{μ}为固有频率下的振型,为振动变形下的加速度,ω为结构固有频率,f为自然频率。可通过固有频率ω计算机构的振动频率f。
[0054]
s203、瞬态动力学分析施加的载荷为时间-载荷历程,通过pto总成结构输入齿轮轴时间函数载荷试验进行测定,第一载荷步为简谐载荷输入,第二载荷步为实测动态载荷,可通过对比分析处水稻直播机在实际工作的过程中其振动对pto结构部位的振动激励。pto总成结构的变速箱输出轴和pto输入轴靠近pto端上安装扭矩传感器,扭矩传感器收集的信号通过降噪滤波和低通滤波信号处理后传输到数据处理模块处理得到转矩-时间历程载荷谱,用于瞬态动力学分析的载荷输入。瞬态动力学分析载荷输入将分两段位进行记载,第一载荷加载为已知频率和幅值的简谐载荷,第二载荷加载为试验实测动态载荷。
[0055]
s204、转矩-时间历程载荷谱输入瞬态动力学分析中,得到瞬态动力学分析结果;
[0056]
pto总成整体结构在实际工况下受到交变应力的作用而产生疲劳损伤,同时整机最开始的激振对pto结构的影响也不可以忽略,输入载荷为动态应力—时间历程,分析过程中必须限制总成在x、y、z三个轴上的平动。所述时域分析方程为:
[0057][0058]
其中,[m]为质量矩阵,[c]为阻尼矩阵,[k]为刚度矩阵,{s}为位移矢量,为速度矢量,为加速度矢量,{f(t)}为输入力矢量,这里第一加载里程f(t)=fsin(ωt),第二加载历程为实测动态载荷。
[0059]
s3、根据瞬态动力学分析结果,对pto总成模型受应力最大的多个危险节点位置,在多个危险节点位置中选择7个应力较大的危险节点位置作为基于daq应变测试系统的危险节点载荷谱采集实验,如图4所示的7个危险节点位置。首先对7个危险节点位置的仿真应力谱进行分析,确定危险节点位置的应力梯度进行求解和分析,得到应力梯度。然后确定pto总成模型的受应力较大区域位置和应力较大区域的应力分布云构成,得到应力曲线状态。应力梯度的大小可以通过以下公式进行计算:
[0060][0061]
该方程计算得出,其中,σ
xy
为应力张量,χz为z方向的长度,x,y,z表示坐标系方向。
[0062]
应力梯度大小和方向的确定方法为:可以根据步骤2中的模态分析结果(即应力分布云图)和局部应力梯度分布选择合理位置粘贴应变传感器。
[0063]
s4、daq应变测试系统包括无线应变传感器系统、数据调离采集模块、数据采集卡和数据分析系统,无线应变传感器系统包括微型电源、应变传感器和信号发射器。基于daq
应变测试系统,对在pto总成的7个危险部位进行载荷采集实验,得到7个危险部位的载荷-时间历程谱,步骤s4包括以下具体步骤:
[0064]
s401、通过步骤s3中的多个危险节点位置及其应力曲线状态,确定pto总成模型受较大应力的局部区域和局部区域处的应力分布云图。在pto总成中选定至少4个危险部位(本实施例中选择7个危险部位)并依次标定序号,无线应变传感器系统的应变传感器安装在pto总成的接触表面的7个危险节点位置;在pto总成结构的齿轮啮合处的粘贴需要对齿轮侧壁平整处理,同时微型电源和信号发射器一同粘贴在pto总成的齿轮侧壁。
[0065]
s402、将数据调离采集模块、数据采集卡和数据分析系统依次连接。labview数据采集软件安装在计算机内组成数据分析系统。无线应变传感器系统的应变传感器通过信号发射器将应变信号数据发射出去。信号接收器接收应变信号数据,应变信号数据经过数据调离采集模块修正,被修正后的应变信号数据经过信号放大器输入到数据采集卡内,数据采集卡通过i/o接口将应变信号数据传输到计算机内。
[0066]
s403、计算机内的labview数据采集软件对应变信号数据进行采集和分析,通过低通滤波对高频噪声进行过滤,进行处理得到载荷-时间历程谱。
[0067]
s5、基于线弹性变形下,选取7个危险节点位置的荷载时间历程,载荷-时间历程谱进行翻译,得到实测应力谱数据,根据胡可定律在线弹性变形下的应力应变关系式为:
[0068]
σ=eε
[0069]
其中,e为弹性模量,σ为考虑危险部位应力梯度修正系数后的应力值,ε表示正向应变,是指在外力作用下的相对形变(相对伸长dl/l)它反映了物体形变的大小。得到应力随时间的动态历程。通过对比分析有限元仿真和实测载荷结果,在数据高度吻合的情况下从多个危险节点位置中选取应力最大的危险节点位置(即是对应于pto总成上对应的危险部位)作为疲劳分析研究对象对pto总成进行疲劳寿命分析计算,本实施例中选择危险节点位置为应力最大危险节点进行疲劳可靠性分析。
[0070]
s6、对pto总成的材料(即是45号钢材料)p-s-n曲线关系进行修正,得到材料疲劳寿命曲线,如附图5所示;
[0071]
步骤s6中的p-s-n曲线的公式为:
[0072]
lgn
p
=α
p-b
p
lg((1 k)σ)
[0073]
其中,np为存活率为p时的材料疲劳寿命,α
p
和b
p
为与存活率有关的pto总成的材料常数,45号钢在p=50%时α
p
为45.4561,b
p
为-15.6866,p=95%时α
p
=41.5280,b
p
为-13.8957,k为调整系数,该系数综合考虑应力集中、光滑试件的表面状态等对材料p-s-n的影响,σ为考虑危险部位应力梯度修正系数后的应力值。这里不能用应力均值简单的对循环n进行计算,引入调整系数k可以消除一部分曲线误差对寿命的影响。
[0074]
s7、根据步骤s2中的瞬态动力学分析结果(即是应力分布云图),通过分析pto总成结构的应力变化最大位置,得到应力集中系数,其公式为:
[0075][0076]
其中,kt为扭转、剪切下的应力集中系数,τ
max
为最大剪切应力,τ为名义剪切应力,可通过设计手册查得;
[0077]
同时,在pto总成的材料p-s-n曲线翻译成为pto总成的零件s-n曲线时候引入表面
状态系数β,得到其公式为:
[0078][0079]
其中,β为表面状态系数,δ
β
为实际pto总成结构45号钢材料的疲劳极限,δ为标准光滑试件45号钢材料的疲劳极限。
[0080]
s8、根据步骤s6中的材料p-s-n曲线翻译成零件s-n曲线,根据步骤s6中的p-s-n曲线和步骤s7中的应力集中系数和表面状态系数的计算,建立pto总成的零件s-n曲线;该零件受到局部应力集中影响,零件表面状态在实际工况下会发生变化,此时零件的s-n曲线不完全是光滑试件实验下的材料s-n曲线,这里需要强调的是对于pto总成的高强度齿轮的s-n曲线的转折点n1值远远小于其材料s-n曲线的n1值,不能用材料s-n曲线的n1值代替零件s-n曲线的n1值。通过对材料p-s-n曲线考虑表面粗糙不一和局部应力,以及尺寸状态对p-s-n曲线的影响,引入综合调整系数k;
[0081]
步骤s8中的s-n曲线符合公式:
[0082][0083]
其中,kt为步骤s7中的计算结果应力集中系数,p为误差系数,β为步骤s7中的表面状态系数,a为引入表面状态调整系数;
[0084]
此时的pto总成结构的s-n曲线满足:
[0085]
c=(sk)an0[0086]
其中,a和c均为与pto总成的材料有关的常数参数,s为应力,n0为零件寿命。疲劳损伤往往与材料和应力集中有关,该公式引入对应力集中、表面状态的综合调整系数修正,可以得到较为准确的疲劳分析结果,对pto总成的寿命预测也更为准确。
[0087]
s9、根据步骤s5中实测应力谱数据和步骤s8中的零件寿命,所述pto总成进行应力疲劳分析,基于miner线性损伤累积计算得到pto总成疲劳寿命n。损伤在各应力水平下随循环次数增加而线性增加,损伤率d为
[0088][0089]
其中n为实际载荷作用次数,n为零件材料发生循环破坏的次数。
[0090]
各级载荷作用下使得pto总成损伤累积达到极限时损伤率d=1,可视为该零件结构破坏失效。不同载荷施加产生的损伤是线性叠加的,最后发生疲劳破坏时候损伤率有
[0091][0092]
pto总成疲劳寿命n的估算,可通过实测载荷实验以及miner线性损伤理论计算求的,miner线性损伤理论指出,发生疲劳破坏时候的损伤率d=1,有
[0093][0094]
其中,nj为第j个载荷下循环数,nj为在实测应力下零件发生破坏的循环数;所述s4和s5基于daq应变测试系统的危险部位载荷采集实验应变谱到应力谱翻译得到实测应力载荷谱,可以确定的值,nj可通过pto总成的零件材料的s-n曲线得出,最后可分析预测估算pto总成疲劳寿命。
[0095]
上述具体实施方式为本发明的优选实施例,并不能对本发明进行限定,其他的任何未背离本发明的技术方案而所做的改变或其它等效的置换方式,都包含在本发明的保护范围之内。
再多了解一些
本文用于创业者技术爱好者查询,仅供学习研究,如用于商业用途,请联系技术所有人。