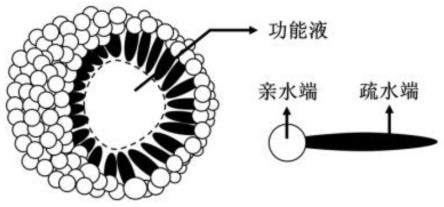
1.本发明涉及原油开采技术领域,尤其涉及一种微纳二氧化碳气水混液驱油方法。
背景技术:
2.透油气资源属于战略资源,其储存量在油气资源中占有举足轻重的地位。现阶段,低渗透油藏具有丰富的存储量,存在渗透机理复杂、开发难度大、采收效率低等问题。其中低渗透油藏的一个主要的开采方式就是注水开发,中低渗油藏注水井注水压力高、渗流阻力大,吸水能力差,注水启动压力梯度相当程度上是克服油藏岩石颗粒表面水膜的吸附阻力。因此常存在注水压力迅速上升,注水量快速下降,甚至注不进水的问题,造成注水井组中的采油井产油量的迅速递减。针对此种注采矛盾,现有技术中公开了二氧化碳驱油,但是仍存在驱油效率低的问题。
技术实现要素:
3.有鉴于此,本发明的目的在于提供一种微纳二氧化碳气水混液驱油方法。本发明降低注水压力,提高驱油效率。
4.为了实现上述发明目的,本发明提供以下技术方案:
5.本发明提供了一种微纳二氧化碳气水混液驱油方法,包括以下步骤:
6.将超临界co2和水通过co2气泡发生器,得到微纳米co2气水混液;
7.将所述微纳米co2气水混液与双疏流体溶液混合,得到混合液;
8.将所述混合液注入注水井进行原油驱替;
9.所述双疏流体溶液中的双疏流体由表面活性剂、助乳化剂、溶剂油、功能液和水制得,所述功能液为柠檬烯、二甲苯、石油醚、凝析油、煤油、汽油或柴油。
10.优选地,所述超临界co2和水的体积比为1~2:8~9。
11.优选地,所述微纳米co2气水混液与双疏流体的体积比为1:0.5~1。
12.优选地,所述双疏流体由包括以下步骤的方法制得:
13.将所述表面活性剂、助乳化剂和水混合后调节ph值为6~8,得到水相;
14.将溶剂油和功能液混合,得到油相;
15.将所述水相加入到油相中进行超声分散,得到所述双疏流体。
16.优选地,所述水相中表面活性剂、助乳化剂和水的质量比为1~5:1~3:100~150。
17.优选地,所述表面活性剂包括氟表面活性剂、氟硅表面活性剂和含氟聚硅氧烷表面活性剂中的一种或多种。
18.优选地,所述助乳化剂包括为甲基异丁基甲醇、正丁醇、正戊醇和聚甘油酯中的一种或多种。
19.优选地,所述油相中溶剂油和功能液的质量比为20~50:5~15。
20.优选地,所述水相与油相的质量比为128:40。
21.优选地,所述混合液的注入速度为1.5~2m3/h。
22.本发明提供了一种微纳二氧化碳气水混液驱油方法,包括以下步骤:将超临界co2和水通过co2气泡发生器,得到微纳米co2气水混液;将所述微纳米co2气水混液与双疏流体溶液混合,得到混合液;将所述混合液注入注水井进行原油驱替;所述双疏流体溶液中的双疏流体由表面活性剂、助乳化剂、溶剂油、功能液和水制得,所述功能液为柠檬烯、二甲苯、石油醚、凝析油、煤油、汽油或柴油。
23.本发明借助微纳米co2气水混液的弱酸性、减阻性、遇油膨胀特性,逐步扩大地层孔隙内的水流通道,降低近井地带注入压力,利用双疏流体的疏水、疏油特性,改变通道周围的岩石润湿性,使得注入流体所到之处,表界面张力都得到大幅降低,以此来达到不断降低近井地带注入压差,扩大水驱的波及面积和波及体积,进而达到提到剩余油挖潜和驱油的目的。
24.进一步地,本发明中所述双疏流体中的全氟硅氧烷表活剂吸附在岩石表面,可使岩石表面疏水疏油,一方面可降低水锁伤害,另一方面有利于凝析油的开采,防止蜡沉积;功能液的释放,可溶解石油沉淀物,从而达到清蜡的目的。
附图说明
25.图1为本发明双疏流体的结构示意图;
26.图2为本发明实施例所提供的微纳二氧化碳气水混液驱油流程图;
27.图3为实施例2中不同温度下co2溶解度;
28.图4为实施例2中浸泡过程中的应变变化;
29.图5为实施例2中微纳米co2气水混液对页岩弹性模量和泊松比的影响曲线;
30.图6为不同测量次数下的水相渗透率;
31.图7为不同测量次数下的进出口压差;
32.图8为孔隙度为22.22%的模拟岩芯经水基纳米溶液处理后水化膜厚度的变化;
33.图9为长35cm、孔隙度为22.22%的模拟岩芯经mgs-w处理后的有效孔隙度变化;
34.图10为长35cm、孔隙度为14.48%的模拟岩芯经mgs-w处理后的有效孔隙度变化;
35.图11为双疏流体1的tem照片;
36.图12为双疏流体1溶液的粒度分布图;
37.图13为地201-37井措施前后注水曲线;
38.图14为井组生产曲线;
39.图15为双疏流体1处理岩心前后效果对比图。
具体实施方式
40.本发明提供了一种微纳二氧化碳气水混液驱油方法,包括以下步骤:
41.将超临界co2和水通过co2气泡发生器,得到微纳米co2气水混液;
42.将所述微纳米co2气水混液与双疏流体溶液混合,得到混合液;
43.将所述混合液注入注水井进行原油驱替;
44.所述双疏流体溶液中的双疏流体由表面活性剂、助乳化剂、溶剂油、功能液和水制得,所述功能液为柠檬烯、二甲苯、石油醚、凝析油、煤油、汽油或柴油。
45.在本发明中,如无特殊说明,使用的原料均为本领域市售商品。
46.本发明将超临界co2和水通过co2气泡发生器,得到微纳米co2气水混液。
47.在本发明中,所述超临界co2和水的体积比优选为1~2:8~9。
48.在本发明中,所述微纳米co2气水混液中气体的直径优选为25~100nm。
49.得到微纳米co2气水混液后,本发明将所述微纳米co2气水混液与双疏流体溶液混合,得到混合液。
50.在本发明中,所述微纳米co2气水混液与双疏流体的体积比优选为1:0.5~1。
51.在本发明中,所述双疏流体溶液的质量分数优选为0.3%。
52.在本发明中,所述双疏流体优选由包括以下步骤的方法制得:
53.将所述表面活性剂、助乳化剂和水混合后调节ph值为6~8,得到水相;
54.将溶剂油和功能液混合,得到油相;
55.将所述水相加入到油相中进行超声分散,得到所述双疏流体。
56.在本发明中,所述水相中表面活性剂、助乳化剂和水的质量比优选为1~5:1~3:100~150,更优选为5:3:120。
57.在本发明中,所述表面活性剂优选包括氟表面活性剂、氟硅表面活性剂和含氟聚硅氧烷表面活性剂中的一种或多种。
58.在本发明中,所述氟表面活性剂优选为全氟癸基磺酸钠、全氟癸基磺酸钠或全氟壬烯氧基苯磺酸钠。
59.在本发明中,所述氟硅表面活性剂优选具有式i所示的结构:
[0060][0061]
式i中r为-(och2ch2)
x-ch3或-(och2ch2ch2)
x-ch3,其中x为5~10的整数。
[0062]
在本发明中,所述含氟聚硅氧烷表面活性剂优选具有式ii所示的结构:
[0063][0064]
式ii中r独立地为-(och2ch2)
x-ch3、-(och2ch2ch2)
x-ch3或x为5~10的整数;
[0065]
n=1~200。
[0066]
在本发明中,所述助乳化剂优选包括为甲基异丁基甲醇、正丁醇、正戊醇和聚甘油酯中的一种或多种。
[0067]
在本发明中,所述溶剂油优选为白油、液体石蜡、脱芳烃溶剂油或异构烷烃溶剂油。
[0068]
在本发明中,所述脱芳烃溶剂油优选为d40、d60、d80或d110。
[0069]
在本发明中,所述异构烷烃溶剂油优选为异构十二烷烃溶剂油或异构十四烷烃溶剂油。
[0070]
在本发明中,所述油相中溶剂油和功能液的质量比优选为20~50:5~15。
[0071]
在本发明中,所述水相与油相的质量比优选为128:40。
[0072]
在本发明中,所述双疏流体中的全氟硅氧烷表活剂吸附在岩石表面,可使岩石表面疏水疏油,一方面可降低水锁伤害,另一方面有利于凝析油的开采,防止蜡沉积;功能液的释放,可溶解石油沉淀物,从而达到清蜡的目的。
[0073]
在本发明中,所述双疏流体由表面活性剂、功能液和水相构成,是一种纳米尺寸的水包油型乳液,结构示意图如图1所示。
[0074]
得到混合液后,本发明将所述混合液注入注水井进行原油驱替。
[0075]
在本发明中,所述混合液的注入速度优选为1.5~2m3/h。
[0076]
在本发明中,优选利用撬装泵或泵车将所述混合液自注入井到产出井方向上注入并对原油进行驱替。
[0077]
在本发明中,所述混合液的注入量优选以单井正常生产时日配注量为准。
[0078]
为了进一步说明本发明,下面结合实例对本发明提供的微纳二氧化碳气水混液驱油方法进行详细地描述,但不能将它们理解为对本发明保护范围的限定。
[0079]
图2为本发明实施例所提供的微纳二氧化碳气水混液驱油流程图。通过在低渗透特性的注水井油藏地层中,将超临界co2和水,通过微纳米co2气泡发生器,产生微纳米co2气水混液,同时伴随双疏流体溶液,进入混合腔内,经过混合腔的混合液,沿管线通过泵车,泵注到注入井中。
[0080]
实施例1
[0081]
制备双疏流体1
[0082]
(1)水相准备:按质量份数比计,将5份表面活性剂、3份甲基异丁基甲醇、120份去离子水直接在烧杯中混合均匀,调节ph=7;
[0083]
(2)油相准备:按质量份数比计,将30份白油、10份柠檬烯搅拌混合均匀;
[0084]
(3)将水相配料加入到油相配料中得到混合液,在室温下将混合液超声分散15min得到双疏流体。
[0085]
其中,表面活性剂为1份全氟壬烯氧基苯磺酸钠与1份复配得到。
[0086]
制备双疏流体2
[0087]
(1)水相准备:按质量份数比计,将5份表面活性剂、3份甲基异丁基甲醇、120份去离子水直接在烧杯中混合均匀,调节ph=7;
[0088]
(2)油相准备:按质量份数比计,将30份白油、10份柠檬烯搅拌混合均匀;
[0089]
(3)将水相配料加入到油相配料中得到混合液,在室温下将混合液超声分散15min得到双疏流体。
[0090]
其中,表面活性剂为1份全氟壬烯氧基苯磺酸钠与1份复配得到,其中r为-(och2ch2)
10-ch3。
[0091]
制备双疏流体3
[0092]
(1)水相准备:按质量份数比计,将5份全氟壬烯氧基苯磺酸钠、3份正丁醇、120份去离子水直接在烧杯中混合均匀,调节ph=7;
[0093]
(2)油相准备:按质量份数比计,将30份白油、10份二甲苯搅拌混合均匀;
[0094]
(3)将水相配料加入到油相配料中得到混合液,在室温下将混合液超声分散15min得到双疏流体。
[0095]
制备双疏流体4
[0096]
(1)水相准备:按质量份数比计,将5份表面活性剂、3份甲基异丁基甲醇、120份去离子水直接在烧杯中混合均匀,调节ph=7;
[0097]
(2)油相准备:按质量份数比计,将30份白油、10份石油醚搅拌混合均匀;
[0098]
(3)将水相配料加入到油相配料中得到混合液,在室温下将混合液超声分散15min得到双疏流体。
[0099]
其中,表面活性剂为1份与1份复配得到,其中r为
[0100]
接触角测定:
[0101]
分别配制质量分数为0.3%的双疏流体1~4的溶液,在25℃下按标准sy/t5153-2007测定其接触角。测试结果如下表1所示,可知,制得的双疏流体可使岩石表面转变为中性润湿,从而达到疏水疏油的目的。
[0102]
表1双疏流体的接触角
[0103] 接触角θc双疏流体179
°
双疏流体277
°
双疏流体377
°
双疏流体478
°
[0104]
实施例2
[0105]
单独微纳二氧化碳气水混液驱油方法
[0106]
以油田注水井日注入20m3为基准,干线压力取值为18mpa,孔隙度17%,岩心渗透率取10md、岩心100mm
×
25mm。
[0107]
(1)微纳米co2水中溶解度
[0108]
根据实测数据(见图3),微纳米co2水中溶解度随着温度升高,溶解度逐步降低,在达到超临界后溶解度降低增加,本实验以地层温度为参考t=60℃、微纳米co2水中溶解为5.7g/100g。
[0109]
(2)天然砂岩岩心成分(用x射线衍射仪进行矿物成分分析)
[0110]
主要矿物成分,其中石英占50wt%,方解石占19wt%,白云石占18wt%,黏土矿物含量占10wt%,斜长石和黄铁矿含量较少,分别为2wt%和1wt%。本批岩心黏土矿物含量为10wt%,含量较高。
[0111]
(3)微纳米co2气水混液浸泡,条件为温度60℃和压力8mpa。将天然岩心成品放入岩心夹持器,注入微纳米co2气水混液浸泡并使其达到浸泡条件,岩心在碳酸水和二氧化碳环境中浸泡时间为120min,浸泡开始后连续记录浸泡期间岩心的应变变化。每隔5min取一组应变数据点,采用多次读数取平均值的方法,结果如图4,说明岩心具有非均质性,在微纳米co2气水混液浸泡作用下层理裂缝会发生一定的扩展,因此在岩心纵向上的应变会明显大于横向上的应变。碳酸对黏土组分收缩的影响很大,同时黏土组分对co2吸附作用也会导致空间收缩。
[0112]
(4)孔隙及应力变化
[0113]
图5为微纳米co2气水混液对页岩弹性模量和泊松比的影响曲线,微纳米co2气水混液浸泡使页岩弹性模量和泊松比均增大,弹性模量和泊松比平均增幅分别为43.4%和36.6%。在超临界二氧化碳临界点(临界压力7.38mpa,临界温度31.26℃)附近都发生明显的波动,这与二氧化碳在临界压力前后其性质变化有关,临界压力之后,整体变化趋势平稳。浸泡压力对天然裂缝和微孔隙造成的扩展作用、黏土组分的收缩反应和二氧化碳吸附造成的溶剂化力等综合作用对岩石结构影响复杂。
[0114]
(5)渗透率变化
[0115]
图6为不同测量次数下的水相渗透率,图7为不同测量次数下的进出口压差,可知,经过处理后的渗透率大幅降低,出口压差减小
[0116]
(6)水化模变化
[0117]
图8为孔隙度为22.22%的模拟岩芯经水基纳米溶液处理后水化膜厚度的变化,可知,水化膜厚度由2.71nm减小到2.35nm,表明纳米微粒可以吸附在岩石表面,将岩石表面的吸附水驱走,降低水化膜厚度,从而使注入水可以顺利通过。
[0118]
(7)有效孔隙度变化
[0119]
按照公式(1)计算孔隙度:
[0120][0121]
图9为长35cm、孔隙度为22.22%的模拟岩芯经mgs-w处理后的有效孔隙度变化,提高了34%,图10为长35cm、孔隙度为14.48%的模拟岩芯经mgs-w处理后的有效孔隙度变化,提高了56%。
[0122]
实施例3
[0123]
通过在低渗透特性的注水井油藏地层中,将超临界co2和水,通过微纳米co2气泡发生器,产生25~100nm微纳米co2气水混液,按气液体积比1:9进行混合进入混合腔,同时伴随质量分数为0.3%双疏流体1溶液,按注入co2气水混液与双疏流体的体积数1:1进行伴随进入混合腔内,经过混合腔的液体,沿管线通过泵车,泵注到注入井中,注入速率为1.5m3/h。
[0124]
图11为双疏流体1的tem照片,平均粒径为25nm。图15为双疏流体1处理岩心前后效果对比图,处理前岩心吸油、吸水,处理后岩心拒油、拒水。
[0125]
图12为双疏流体1溶液的粒度分布图,左侧是粒度区间分布占比百分数,右侧是纳米颗粒累积分布,可知,双疏流体1的溶液粒径主要集中在25nm左右。
[0126]
表2为不同矿井微纳二氧化碳气水混液驱油的数据,可知,通过此工艺可实现注水井注入压力降低,注入能力提高,水驱效果提高。
[0127]
表2不同矿井微纳二氧化碳气水混液驱油的数据
[0128]
[0129][0130]
图13为地201-37井措施前后注水曲线,可知,利用此工艺实现了注水压力降低,对比施工前注入量增加了3倍以上;图14为井组生产曲线,说明地201-37井在进行微纳二氧化碳气水混液驱油后体现了较好的提掖增油效果。
[0131]
实施例4
[0132]
在长庆油田微纳二氧化碳气水混液驱油
[0133]
长庆某油田区块,油层组以水下分流河道砂体沉积为主,粒间孔和长石溶孔构成了油藏,油层厚度5.3m,平均孔隙度为71%,平均渗透率为0.9
×
10-3
μm2,地层原油黏度为0.73mpa
·
s,原始气油比为85m3·
t-1
。地层水为cacl2水型,总矿化度为35.42g
·
l-1
。地层温
度为85℃,原始地层压力为19.74mpa,饱和压力为10.27mpa,压力系数为0.7,属于低压油藏。本次进行同一区块选择两个井组进行对比试验,具体数据如下:
[0134]
案例一:注水井2020年9月28日进行微纳二氧化碳气水混液驱油施工,将超临界co2和水,通过微纳米co2气泡发生器,产生25~100nm微纳米co2气水混液,按气液体积比1:9进行混合进入混合腔,同时伴随质量分数为0.3%双疏流体1溶液,按注入co2气水混液与双疏流体的体积数1:1进行伴随进入混合腔内,经过混合腔的液体,沿管线通过泵车,泵注到注入井中,注入速率为1.5m3/h,10月5日转注,措施前注水油压为12mpa,措施后注水油压为8.0mpa,下降了4.0mpa;措施前注水量为1m3/d,措施后注水量由5.8m3/d逐渐增加,已达15.7m3/d,平均注水量为8.65m3/d,11月份平均注水量为13.21m3/d,超过了配注要求。对应井组增油单井平均增油达到1.5t,井组累计日增油达7t。
[0135]
案例二:注水井2020年9月8日进行微纳二氧化碳气水混液驱油施工,将超临界co2和水,通过微纳米co2气泡发生器,产生25~100nm微纳米co2气水混液,按气液体积比2:8进行混合进入混合腔,同时伴随质量分数为0.3%双疏流体1溶液,按注入co2气水混液与双疏流体的体积数1:1.5进行伴随进入混合腔内,经过混合腔的液体,沿管线通过泵车,泵注到注入井中,注入速率为1.5m3/h,9月26日转注,措施前注水油压为13.2mpa,措施后注水油压为12.1mpa,下降了1.1mpa;措施前注水量为2.5m3/d,措施后注水量由4.6m3/d逐渐增加,已达8.9m3/d,日常配注注水量为9m3/d,基本达到配注要求。对应井组增油单井平均增油达到0.5t,井组累计日增油达3.5t。
[0136]
以上所述仅是本发明的优选实施方式,并非对本发明作任何形式上的限制。应当指出,对于本技术领域的普通技术人员来说,在不脱离本发明原理的前提下,还可以做出若干改进和润饰,这些改进和润饰也应视为本发明的保护范围。
再多了解一些
本文用于创业者技术爱好者查询,仅供学习研究,如用于商业用途,请联系技术所有人。