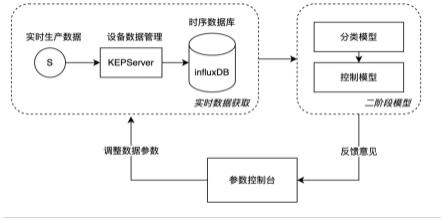
1.本发明涉及智能化水刺布生产技术领域,特别是涉及一种水刺布生产线智能控制系统。
背景技术:
2.如图1展示了目前水刺工艺生产线上的工艺流程部分片段。水刺布生产线本身具有较高的自动化和信息化水平,产线上的相关检测设备会持续进行质量指标数据的采集、解析和基础分析,产线工人可根据分析结果来决定相关环节生产设备的参数调整策略。
3.与克重指标关联性最高的“梳理成网”和“在线监测”的具体流程包括:一、梳理成网:纤维暂存设备稳定地向梳理成网设备输送纤维,经由梳理成网设备(气压棉箱、梳理机、交叉铺网机、多辊牵伸机等)形成纤网。铺网设备有两套,各自梳理一层纤网,然后上下两层纤网合并起来输送至后面的水刺工艺。喂棉速度参数可以进行人工控制,当增加喂棉速度时,会导致出产的无纺布的克重和厚度增加。二、在线监测:水刺布进入卷绕设备前设有检测设备(克重、水分、厚度、疵点检测),扫描器单程采样,并以目标值为基准用图形化的方式展示出来。其中,克重是波动比较频繁的指标,比如更换原材料、前方送棉不均匀、水分多寡等等原因都可能导致克重变化。
4.目前,生产线上对于克重的操作都是以人工主观判断为主,当曲线超出设定的阈值时,操作员会到铺网设备的控制台上调整喂棉量。有关克重的调整大约每天会出现十几次到数十次。
5.通过上述的介绍,可以看到对于水刺工艺生产线来说,根据监测数据进行设备参数调整的步骤需要人工干涉完成,根据调研,目前我国大多数水刺法非织造布生产线都是采用类似的半自动化生产。
6.人工干涉调整参数具有以下的缺陷:
7.效率不佳,具有延时性。克重指标的监视和因应调整占了生产过程中大多数的调整工作。并且,由于监视在线指标设备与调整克重的控制台距离较远,师傅来回往复不仅费力,也不够及时。
8.整不稳定。师傅调整参数的操作比较主观,基本是采用“调一调看一看”的方式。通过看在线扫描得出的曲线,如果“偏高”就“降低一点”喂棉参数,如果“高的厉害”就“多降一些”喂棉参数。想要解决人工干涉调整参数的缺陷,亟需一种水刺布生产线智能控制系统。
技术实现要素:
9.本发明的目的是提供一种水刺布生产线智能控制系统,以解决现有技术中,人工干涉调整参数效率不佳、调整不稳定等缺陷。
10.为实现上述目的,本发明提供了如下方案:
11.水刺布生产线智能控制系统,包括:
12.数据获取模块:用于实时获取并存储生产线数据,所述生产线数据包括喂棉罗拉
值、实时水分值、实时速度值、实时克重值;
13.数据处理模块:用于对所述生产线数据进行分类及控制处理,给出喂棉罗拉参数调整意见;
14.参数控制模块:用于对所述参数调整意见进行验证,并应用于所述控制系统中;
15.所述数据获取模块、所述数据处理模块、所述参数控制模块依次连接。
16.优选地,所述数据获取模块通过工艺产线上的传感器实时获取所述生产线数据,并将所述生产线数据通过kepserver保存至influxdb时序数据库中,用于供后续模块进行处理与分析。
17.优选地,所述数据获取模块中还包括预处理单元,所述预处理单元用于对所述生产线数据进行清洗、分割和提取,采用上采样或下采样方法进行数据增强处理,得到预处理后的数据,并将所述预处理后的数据保存至所述influxdb时序数据库中。
18.优选地,所述数据处理模块包括:
19.分类单元:用于通过分类模型预测未来超过克重阈值的概率;
20.控制单元:用于搭建自动化控制闭环,给出喂棉罗拉参数调整意见。
21.优选地,所述分类模型用于根据实时生产线数据进行分类,获得当前生产状态及分类结果,对所述分类结果定义标签种类,并根据所述分类结果判断是否需要进行调整操作的决策,若需要进行调整操作,则将所述分类结果输入到所述控制单元中继续进行处理,若不需要进行调整操作,则继续重新输入新的数据。
22.优选地,所述分类模型采用双层分类器,所述双层分类器包括第一分类器和第二分类器,将所述第一分类器的输出量作为所述第二分类器的输入量。
23.优选地,所述第一分类器采用随机森林模型,通过对历史克重窗口和历史喂棉罗拉窗口进行特征提取,输入到所述随机森林模型中,输出每个所述标签的预测百分比;所述第二分类器采用循环神经网络模型lstm,输入所述第一分类器的输出标签预测百分比的历史窗口,输出为生产状态的预测标签;所述lstm模型采用小批次梯度下降方法对历史数据进行训练,通过随机梯度下降对实时数据进行调整,通过softmax激活的全连接层,得到生产状态标签的概率。
24.优选地,所述控制单元包括:
25.预测模型:用于根据历史生产线数据和标签的预测百分比,预测系统未来输出的喂棉罗拉值;
26.优化控制子单元:用于通过克重变化量与喂棉罗拉变化量之间的预测模型,对喂棉罗拉值进行调整,通过所述分类模型输出的标签预测百分比,作为对所述生产状态分类的隶属度,基于模型转换,输出最优喂棉罗拉调整量。
27.优选地,所述参数控制模块包括反馈校正单元,所述反馈校正单元用于在每个新的采样时刻,进行重新预测,并利用实时信息对预测结果进行修正,然后再进行新的优化。
28.本发明的有益效果为:
29.本发明能够更好的建立克重变化与喂棉罗拉参数变化的关系,能够通过智能方式为工人输出参数调整的意见,并完成自动化调整工作,在保证调整准确性的基础上省去了许多人工工作,通过智能控制完成了一个“监测-调整-变更”的自动化闭环。
附图说明
30.为了更清楚地说明本发明实施例或现有技术中的技术方案,下面将对实施例中所需要使用的附图作简单地介绍,显而易见地,下面描述中的附图仅仅是本发明的一些实施例,对于本领域普通技术人员来讲,在不付出创造性劳动性的前提下,还可以根据这些附图获得其他的附图。
31.图1为本发明中现有技术流程示意图;
32.图2为本发明实施例的系统设计图;
33.图3为本发明实施例的克重正常趋势示例图;
34.图4为本发明实施例的克重异常趋势示例图;
35.图5为本发明实施例的喂棉罗拉数据清洗示例图;
36.图6为本发明实施例的下采样及上采样方法简要流程图;
37.图7为本发明实施例的模型设计图;
38.图8为本发明实施例的分类模型设计示意图;
39.图9为本发明实施例的lstm模型示意图;
40.图10为本发明实施例的传统控制系统结构图;
41.图11为本发明实施例的优化控制示意图;
42.图12为本发明实施例的控制模型结构图;
43.图13为本发明实施例的设计流程图。
具体实施方式
44.下面将结合本发明实施例中的附图,对本发明实施例中的技术方案进行清楚、完整地描述,显然,所描述的实施例仅仅是本发明一部分实施例,而不是全部的实施例。基于本发明中的实施例,本领域普通技术人员在没有做出创造性劳动前提下所获得的所有其他实施例,都属于本发明保护的范围。
45.为使本发明的上述目的、特征和优点能够更加明显易懂,下面结合附图和具体实施方式对本发明作进一步详细的说明。
46.本实施例提供一种水刺布生产线智能控制系统(如图2),包括:
47.数据获取模块:用于实时获取并存储生产线数据,所述生产线数据包括喂棉罗拉值、实时水分值、实时速度值、实时克重值;
48.数据处理模块:用于对所述生产线数据进行分类及控制处理,给出喂棉罗拉参数调整意见;
49.参数控制模块:用于对所述参数调整意见进行验证,并应用于所述控制系统中;
50.所述数据获取模块、所述数据处理模块、所述参数控制模块依次连接。
51.所述数据获取模块通过工艺产线上的传感器实时获取所述生产线数据,并将所述生产线数据通过kepserver保存至influxdb时序数据库中,用于供后续模块进行处理与分析。
52.数据获取模块中还包括预处理单元,所述预处理单元用于对所述生产线数据进行清洗、分割和提取,采用上采样或下采样方法进行数据增强处理,得到预处理后的数据,并将所述预处理后的数据保存至所述influxdb时序数据库中。
53.目前得到的水刺布生产线上的数据包括在线检测数据,水刺数据,梳理机数据。其中,克重数据会随着各种因素有正常的上下波动,当超出目标值时,现场工作人员会通过调整梳理机数据中的“喂棉罗拉”数据来保持克重数据在稳定范围之内。克重数据及喂棉罗拉数据情况由下表1、表2进行示意:
54.表1
55.平均克重目标克重时间35.2352022/2/27 23:10:0035352022/2/27 23:10:0035352022/2/27 23:10:0036352022/2/27 23:10:0036.6352022/2/27 23:10:0036.7352022/2/27 23:10:0036.2352022/2/27 23:10:0034.7352022/2/27 23:10:0034.9352022/2/27 23:10:0035.3352022/2/27 23:10:0035.2352022/2/27 23:10:00
56.表2
[0057][0058][0059]
为了更加直观地表现克重数据随时间变化的趋势,图3和图4分别选取了一段正常克重的时间序列与一段异常克重的时间序列进行图像绘制。可以看到,若将异常阈值设定在
±
2,图3的克重曲线始终在目标克重即35
±
2的范围内进行随机波动,而图4的克重曲线
在后半段明显以上升趋势不断提高,并且多次超过了阈值37(即目标克重35 阈值2),此时我们已经需要去通过调整喂棉罗拉参数来让克重曲线回到35上下。我们的目标就是能够在生产线实时监测的过程中,尽快识别出这样的异常趋势,并且给出喂棉罗拉的调整意见。
[0060]
对于水刺布生产线的数据来说,每一批材料品类不同,工况不同(例如,工人交接班时调整的次数变少,克重更加不稳定),都会对最后实际克重曲线结果造成影响。同时,由于生产线上情况复杂,对于机器的开关机操作以及传感器在其他异常情况下的读值并不会在获取的数据中直接标注出来,而在这些情况下获得的数据往往是无效的异常值。
[0061]
为了能够在训练模型时使用有效并且可靠的数据,在前期对获取的数据进行了清洗工作。主要内容有:1)根据生产线提供的稳定工况进行数据分割、提取;2)对于一些明显偏离平均值非常大的异常值,或是跳变非常大的一段时间内的数据进行数据清洗。
[0062]
图5展示了对于喂棉罗拉数据进行数据清洗的示例。可以看到在清洗前有一些段时间内的无意义跳变,在清洗时选择跳过这些跳变,对它们做了前后平均值的平滑处理。
[0063]
由于实际生产线上异常数据样本本身占很小的比例,大多数数据仍旧是在正常范围内波动,所以出现了数据不平衡问题,会导致训练出来的模型偏向于多数类的结果。同时,异常样本不足可能也会影响模型学习异常趋势的特征。所以本实施例中采用一些数据增强方法来解决这个问题。
[0064]
具体来说,在进行训练的过程中,使用下采样或者上采样的方法解决数据不平衡问题,使得不同标签的数据量达到一个基本平衡的状态,便于后续进行实际的模型分析。图6展示了下采样及上采样方法简要流程。
[0065]
数据处理模块包括:
[0066]
分类单元:用于通过分类模型预测未来超过克重阈值的概率;
[0067]
控制单元:用于搭建自动化控制闭环,给出喂棉罗拉参数调整意见。
[0068]
为了能够完成克重趋势的预测并给出相应调整意见,提出使用一个两阶段模型来完成这些工作,包括一个分类模型和一个控制模型,具体的模型设计图如图7所示。其中,分类模型定义了一个多分类问题,旨在根据目前的实时窗口数据来预测未来超过克重阈值的可能性。该模型首先使用永信工艺产线上的历史数据进行训练,通过历史数据提取出了与克重与喂棉罗拉相关的特征数据,搭建时间序列分类模型进行预测。控制模型利用历史的喂棉罗拉人工调整与相应的克重变化历史数据搭建模型,搭建自动化控制闭环,给出喂棉罗拉参数调整意见。
[0069]
所述分类模型用于根据实时生产线数据进行分类,获得当前数据状态及分类结果,对所述分类结果定义标签种类,并根据所述分类结果判断是否需要进行调整操作的决策,若需要进行调整操作,则将所述分类结果输入到所述控制单元中继续进行处理,若不需要进行调整操作,则继续重新输入新的数据。
[0070]
分类模型的目标旨在根据实时数据分类出当前数据的状态,再根据分类结果进行是否要进行调整操作的决策。
[0071]
由于得到的数据未经过人工标注,则需要通过一定的判断标准来进行数据的标注。根据水刺生产线上已有的经验,总结出了以下供考虑的经验性规则:
[0072]
1)小幅波动可以忽略、短时间的中小幅克重波动也可以忽略;
[0073]
2)分钟级的中小幅持续高于目标值需要关注,连续两三卷小幅高于目标值需要关
注;
[0074]
3)出于成本考虑持续高于目标值比持续低于目标值需要更多的关注。
[0075]
根据这些规则,对于是否要进行调整的判断很大程度依赖于一段时间窗口内是否有大幅持续高于目标值的情况,以及是否有小幅长时间高于目标值的情况。针对以上经验和实际生产性情况,在本实施例中设定异常样本超出目标值的阈值为
±
2,并将标签做了如表3所示的定义(标签定义仅作示例,会根据实际生产情况作变更)。
[0076]
表3
[0077]
标签含义判断标准vl强上超样本样本是否在未来20个时间点内平均值大于(目标值 2)l上超样本样本是否在未来20个时间点内平均值大于(目标值 1)n正常样本样本是否在未来20个时间点内始终在目标范围内波动s下超样本样本是否在未来20个时间点内平均值小于(目标值-1)vs强下超样本样本是否在未来20个时间点内平均值小于(目标值-2)
[0078]
由于希望能够通过历史窗口值来预测出未来克重趋势变化情况的标签,采用了如图8所示的分类模型设计。生产线本身对于模型敏感度要求高,同时也希望能够尽早对异常趋势进行调整,所以采用双层分类器,可以更好地增加分类的准确性。
[0079]
第一分类器采用随机森林模型。随机森林是通过集成学习的思想将多棵树集成的一种算法,它的基本单元是决策树,每棵决策树都是一个分类器,对于一个输入样本,n棵树会有n个分类结果。而随机森林集成了所有的分类投票结果,将投票次数最多的类别指定为最终的输出。随机森林能够有效的在大数据集上进行训练,具有训练速度快、准确率高的优点。
[0080]
具体来说,在特征提取阶段对历史克重窗口和喂棉罗拉历史窗口进行特征提取,输入到模型中,最后通过随机森林算法输出每个标签的预测百分比。
[0081]
第二分类器采用图9所示的循环神经网络模型lstm。输入为分类器1的输出标签置信度历史窗口,输出为定义的标签。
[0082]
lstm采用交叉熵损失函数,历史数据采用小批次梯度下降进行训练,实时数据采用随机梯度下降对参数进行微调。在最后一个时间步输出的hidden state聚合了所有时间步的信息,将其输入给softmax激活的全连接层,得到设置的各个标签的概率。
[0083]
lstm可以有效聚合多个时间步的信息,并利用深度网络的特征筛选功能自动提取重要的特征。lstm利用遗忘门与输出门控制每个时间步上特征的流通与损失,可以有效应对长时间步中的长期依赖问题,使得模型学习到早期的时间步对未来时间点的影响。
[0084]
所述控制单元包括:
[0085]
预测模型:用于根据历史生产线数据和标签的预测百分比,预测系统未来输出的喂棉罗拉值;
[0086]
优化控制子单元:用于通过克重变化量与喂棉罗拉变化量之间的预测模型,对喂棉罗拉值进行调整,通过所述分类模型输出的标签预测百分比,作为针对生产分类的隶属度,基于模型转换,输出最优喂棉罗拉调整量。
[0087]
在输入实时数据后,将输出调整意见供现场操作人员验证,最终调整意见将直接应用于工艺产线的控制系统,控制台会根据调整意见实时变更工艺产线上的具体参数。
[0088]
控制模型的目标是基于目前预测出的克重预测未来变化状态,进行喂棉罗拉参数的调整反馈,在此引入自动控制理论相关概念来帮助我们进行调整反馈的工作。
[0089]
在工业过程控制领域,长期以来,工业控制器主要采用基于反馈调节的控制方法,通过将传感器测量得到的系统响应反馈至控制器的输入,来实现系统响应跟踪设定值的功能,图10展示了传统控制系统结构。pid控制就是这样一种基于反馈调节的控制方法。传统的以pid为代表的控制方案虽然可以实现无差调节,但在大迟延、大惯性等复杂工况的控制中,控制的快速性、响应的及时性难以保障,不能满足我们的需求。
[0090]
参考模型预测控制和模糊控制的基本思想,本实施例提出的控制模型使用以下步骤进行控制:
[0091]
预测模型:预测模型是模型预测控制的基础。其主要功能是根据对象的历史信息和未来输入,预测系统未来的输出。由于在控制模型的前置步骤中,已经通过分类模型预测到了未来的输出状态,我们将会复用分类模型,作为我们预测模型的结果。这在在线检测中,也能够帮助我们节省模型运行的时间。
[0092]
优化控制:模型预测控制通过某一性能指标的最优来确定控制作用。在离线训练中,会通过克重与喂棉罗拉的历史数据建模克重变化量和喂棉罗拉变化量之间的数学模型,该模型将会作为进行喂棉罗拉调整的数值的依据。接着,通过分类模型输出的标签预测可能性,作为各个分类的隶属度,通过模型转换,找到最优的喂棉罗拉调整量,作为该优化步骤的输出。图11为优化控制示意图。
[0093]
所述参数控制模块包括反馈校正单元,所述反馈校正单元为了防止模型失配或者环境干扰引起控制对理想状态的偏离,在每个新的采样时刻,都会重新进行预测,并利用这一实时信息对基于模型的预测结果进行修正,然后再进行新的优化。
[0094]
控制模型总体结构如图12所示。更好的建立克重变化与喂棉罗拉参数变化的关系,能够通过智能方式为工人输出参数调整的意见,并完成自动化调整工作,在保证调整准确性的基础上省去了许多人工工作。
[0095]
图13展示了具体应用智能控制系统的工艺产线流程,其中步骤1使用分类模型进行未来一段时间内变化趋势的预测,步骤2和3采用反馈模型进行参数变更的预测工作。该流程优化了原先图1的人工干涉参数调整流程,通过智能控制完成了一个“监测-调整-变更”的自动化闭环。
[0096]
以上所述的实施例仅是对本发明优选方式进行的描述,并非对本发明的范围进行限定,在不脱离本发明设计精神的前提下,本领域普通技术人员对本发明的技术方案做出的各种变形和改进,均应落入本发明权利要求书确定的保护范围内。
再多了解一些
本文用于创业者技术爱好者查询,仅供学习研究,如用于商业用途,请联系技术所有人。