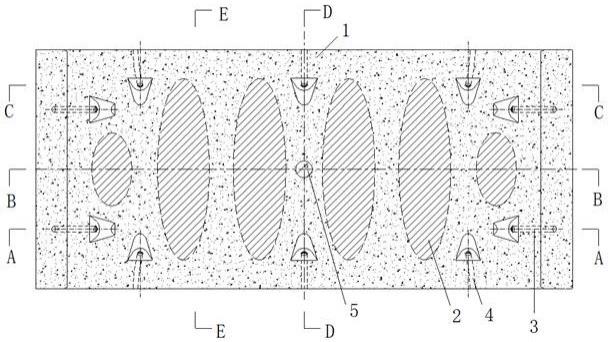
1.本发明涉及隧道结构技术领域,具体涉及一种闭腔薄壁超高性能混凝土盾构隧道管片。
背景技术:
2.随着我国轨道交通的飞速发展,地铁隧道一般采用盾构施工,盾构隧道衬砌管片的材料仍然是以普通混凝土材料为主。盾构隧道管片经常处于水位线以下,如氯和硫酸根等有害离子长期作用与管片上,而普通混凝土抗拉强度较低,在生产、搬运、施工过程中容易发生损坏和产生裂缝,混凝土产生裂缝将加剧渗透和对钢筋、螺栓的腐蚀作用;另外管片内壁由于二氧化碳浓度高,温度和湿度频繁变化,加剧内壁混凝土碳化。这些原因都严重影响了隧道管片衬砌的耐久性。普通混凝土管片比较笨重,在安装过程中也不易操作。
3.因此,亟需一种质量轻、耐久性好以及材料充分利用的新型盾构隧道管片,以提升盾构隧道衬砌结构的耐久性,合理利用材料,充分发挥材料的性能。
技术实现要素:
4.因此,本发明要解决的技术问题在于克服现有技术中的缺陷,从而提供一种质量轻、材料利用率高且耐久性好的闭腔薄壁超高性能混凝土盾构隧道管片,具体为一种闭腔薄壁超高性能混凝土盾构隧道管片。
5.本发明提供了一种闭腔薄壁超高性能混凝土盾构隧道管片,包括:超高性能混凝土层、椭圆腔、第一螺栓孔、第二螺栓孔、注浆孔、接缝凹槽以及钢筋笼;超高性能混凝土层包括弧形上表面、弧形下表面、翼缘以及扇环侧面;弧形上表面与弧形下表面之间存在间隔;翼缘为弧形上表面的延伸,且翼缘与弧形下表面连接;扇环侧面用于连接弧形上表面和弧形下表面;超高性能混凝土层用于包裹钢筋笼;椭圆腔布设于钢筋笼内;第一螺栓孔开设于翼缘上;第二螺栓孔开设于扇环侧面上;注浆孔开设于超高性能混凝土层上;接缝凹槽布置于翼缘上,接缝凹槽用于连接相邻的隧道管片;钢筋笼嵌设于超高性能混凝土层内。
6.优选的,超高性能混凝土层上开设有手孔,手孔贯穿弧形下表面,且手孔包括多个;第一螺栓孔贯穿翼缘,且与部分手孔连接;第二螺栓孔贯穿扇环侧面,且与剩余部分手孔连接。
7.优选的,椭圆腔的长轴方向垂直于扇环侧面,且椭圆腔的布置位置远离手孔的布置位置。
8.优选的,椭圆腔通过短钢筋绑扎于钢筋笼上,短钢筋的直径不小于10mm。
9.优选的,超高性能混凝土层包括超高性能混凝土,超高性能混凝土的抗压强度不小于120mpa。
10.优选的,椭圆腔中布置有泡沫混凝土,泡沫混凝土的强度等级不低于c30。
11.优选的,钢筋笼包括主筋和箍筋;主筋的配筋率为1.0%~1.5%,主筋的钢筋等级不低于hrb400,且相邻主筋之间的间距为150mm~300mm;箍筋的钢筋等级不低于hpb300,且相邻箍筋之间的间距为150mm~250mm。
12.优选的,还包括注浆孔螺旋钢筋,注浆孔螺旋钢筋安装于注浆孔内。
13.优选的,椭圆腔沿间隔方向的厚度不小于75mm,且椭圆腔沿超高性能混凝土层的幅宽方向的长度不小于200mm。
14.本发明技术方案,具有如下优点:1、从结构受力方面,设置的椭圆腔结构能够防止内部应力集中,受力性能更好,且减少了钢筋用量,大大减少了管片的重量,进而减少了管片的整体造价;且外部通过设置的超高性能混凝土层,既提高了管片的整体强度和刚度,又增强了接头局部承载能力;2、从结构耐久性能方面,管片主体采用超高性能混凝土层,其结构紧密,具有优越的抗渗性能和抗侵蚀能力。
附图说明
15.为了更清楚地说明本发明具体实施方式或现有技术中的技术方案,下面将对具体实施方式或现有技术描述中所需要使用的附图作简单地介绍,显而易见地,下面描述中的附图是本发明的一些实施方式,对于本领域普通技术人员来讲,在不付出创造性劳动的前提下,还可以根据这些附图获得其他的附图。
16.图1为本发明实施中闭腔薄壁超高性能混凝土盾构隧道管片的结构示意图;图2为沿图1中a-a方向的剖视图;图3为沿图1中b-b方向的剖视图;图4为沿图1中c-c方向的剖视图;图5为沿图1中d-d方向的剖视图;图6为沿图1中e-e方向的剖视图;图7为沿图1中b-b方向的剖面钢筋分布图;图8为沿图1中e-e方向的剖面钢筋分布图。
17.附图标记说明:1-超高性能混凝土层;11-弧形上表面;12-弧形下表面;13-翼缘;14-扇环侧面;2-椭圆腔;3-第一螺栓孔;4-第二螺栓孔;5-注浆孔;6-接缝凹槽;7-钢筋笼;8-手孔;9-泡沫混凝土;10-注浆孔螺旋钢筋。
具体实施方式
18.下面将结合附图对本发明的技术方案进行清楚、完整地描述,显然,所描述的实施例是本发明一部分实施例,而不是全部的实施例。基于本发明中的实施例,本领域普通技术人员在没有做出创造性劳动前提下所获得的所有其他实施例,都属于本发明保护的范围。
19.在本发明的描述中,需要说明的是,术语“中心”、“上”、“下”、“左”、“右”、“竖直”、“水平”、“内”、“外”等指示的方位或位置关系为基于附图所示的方位或位置关系,仅是为了便于描述本发明和简化描述,而不是指示或暗示所指的装置或元件必须具有特定的方位、以特定的方位构造和操作,因此不能理解为对本发明的限制。此外,术语“第一”、“第二”、“第三”仅用于描述目的,而不能理解为指示或暗示相对重要性。
20.在本发明的描述中,需要说明的是,除非另有明确的规定和限定,术语“安装”、“相连”、“连接”应做广义理解,例如,可以是固定连接,也可以是可拆卸连接,或一体地连接;可以是机械连接,也可以是电连接;可以是直接相连,也可以通过中间媒介间接相连,可以是两个元件内部的连通。对于本领域的普通技术人员而言,可以具体情况理解上述术语在本发明中的具体含义。
21.此外,下面所描述的本发明不同实施方式中所涉及的技术特征只要彼此之间未构成冲突就可以相互结合。
22.实施例1如图1-8所示,本实施例提供了一种闭腔薄壁超高性能混凝土盾构隧道管片,包括:超高性能混凝土层1、椭圆腔2、第一螺栓孔3、第二螺栓孔4、注浆孔5、接缝凹槽6;超高性能混凝土层1包括弧形上表面11、弧形下表面12、翼缘13以及扇环侧面14;弧形上表面11与弧形下表面12之间存在间隔;翼缘13为弧形上表面11的延伸,且翼缘13与弧形下表面12连接;扇环侧面14用于连接弧形上表面11和弧形下表面12;超高性能混凝土层1用于包裹钢筋笼7;椭圆腔2布设于钢筋笼7内;第一螺栓孔3开设于翼缘13上;第二螺栓孔4开设于扇环侧面14上;注浆孔5开设于超高性能混凝土层1上;接缝凹槽6布置于翼缘13上,接缝凹槽6用于连接相邻的隧道管片。
23.在本实施例中,椭圆腔2的长轴方向垂直于扇环侧面14。
24.如图1所示,第一螺栓孔3设置有四个,第二螺栓孔4设置有六个;该管片整体呈对称布置。
25.进一步的,超高性能混凝土层1上开设有手孔8,手孔8贯穿弧形下表面12,且手孔8包括十个。如图2所示,四个第一螺栓孔3均贯穿翼缘13,且分别与四个手孔8对应连接。
26.更进一步的,椭圆腔2的布置位置远离手孔8的布置位置。在本实施例中,椭圆腔2距离手孔8边缘不应小于50mm。
27.在本实施例中,各部分的参数如下:该管片的外径为6200mm,壁厚为350mm,环宽为1500mm。
28.椭圆腔2通过短钢筋绑扎于钢筋笼7上,短钢筋的直径不小于10mm。在本实施例中,短钢筋采用直径12mm的hrb400钢筋。
29.超高性能混凝土层1包括超高性能混凝土,超高性能混凝土的抗压强度不小于120mpa。
30.钢筋笼7包括主筋和箍筋;主筋的配筋率为1.0%~1.5%,主筋的钢筋等级不低于hrb400,且相邻主筋之间的间距为150mm~300mm;箍筋的钢筋等级不低于hpb300,且相邻箍
筋之间的间距为150mm~250mm。在本实施例中,主筋采用直径18mm的hrb400钢筋,箍筋采用直径8mm的hpb300钢筋。
31.椭圆腔2沿间隔方向的厚度不小于75mm,且椭圆腔2沿超高性能混凝土层1的幅宽方向的长度不小于200mm。在本实施例中,最小的椭圆腔2的厚度设置为75mm,且其沿超高性能混凝土层1的幅宽方向的长度设置为200。
32.如图3所示,注浆孔5开设于超高性能混凝土层1上;且在本实施例中,注浆孔5设置于该管片的中心位置。
33.如图4、图5所示,六个第二螺栓孔4均贯穿扇环侧面14,且分别与剩余的六个手孔8对应连接。
34.如图6所示,椭圆腔2中布置有泡沫混凝土9,泡沫混凝土9的强度等级不低于c30。
35.如图7、图8所示,钢筋笼7嵌设于超高性能混凝土层1内。且该管片还包括注浆孔螺旋钢筋10,注浆孔螺旋钢筋10安装于注浆孔5内。
36.管片主体内力复核:分别按受弯构件正截面承载力和大偏心受压构件正截面承载力计算进行内力复核,并进行环向主筋配筋面积计算,简化成i型结构。
37.1、受弯构件正截面承载力验算:
ꢀꢀ
(1)当满足公式(1)时:(2)此时,超高性能混凝土受压区高度由以下公式(3)确定,
ꢀꢀꢀꢀꢀ
(3)当不满足公式(1)时:此时,超高性能混凝土受压区高度由如下公式确定,其中,超高性能混凝土受压区高度需符合的条件为:以及;在上述公式中各参数含义如下:m表示管片主体弯矩设计值,单位为kn
·
m;
fc表示超高性能混凝土轴心抗压强度设计值,单位为n/mm2;f
t
表示超高性能混凝土轴心抗拉强度设计值,单位为n/mm2;fy、f
py
表示管片主体普通钢筋、预应力筋抗拉强度设计值,单位为n/mm2;f 'y、f '
py
表示管片主体普通钢筋、预应力筋抗压强度设计值,单位为n/mm2;a
s 、a's表示受拉区、受压区纵向普通钢筋的截面面积,单位为mm2;a
p
、a'
p
表示受拉区、受压区纵向预应力钢筋的截面面积,单位为mm2;α1表示等效矩形应力图系数;σ'
p0
表示受压区纵向预应力钢筋合力点处混凝土法向应力等于零时的预应力筋应力,单位为n/mm2;b表示截面的腹板宽度,单位为mm;bf表示受拉区翼缘的宽度,单位为mm;对于t形截面,b
f =b;b'f表示受压区翼缘的宽度,单位为mm;h0表示等效矩形截面有效高度,单位为mm;h f
,h' f
表示受拉区,受压区翼缘高度,单位为mm;ξb表示相对界限受压区高度;x表示混凝土受压区高度,单位为mm;
ɑs、
ɑ
p
表示受拉区纵向普通钢筋合力点、预应力钢筋合力点至截面受压边缘的距离,单位为mm;
ɑ
's、
ɑ
'
p
表示受压区纵向普通钢筋合力点、预应力钢筋合力点至截面受压边缘的距离,单位为mm;
ɑ
表示纵向普通受拉钢筋和预应力受拉钢筋的合力点至截面近边缘的距离,单位为mm。
38.2、大偏心受压构件正截面承载力验算:1.当时:时:2.当时:
,,在上述公式中各参数的含义如下:n表示管片主体轴向压力设计值,单位为kn;e表示轴向压力作用点至纵向普通受拉钢筋和预应力受拉钢筋合力作用点的距离,单位为mm;ei表示偏心受压构件正截面的初始偏心距,单位为mm;e0表示轴向压力作用点对截面重心的偏心距,单位为mm;当需要考虑二阶效应时,m应按国家标准《混凝土结构设计规范》(gb 50010-2010)规定计算;e
ɑ
表示附加偏心距,单位为mm,按偏心方向截面最大尺寸h
ɑ
确定,h
ɑ
=h:当h
ɑ
≤600mm时,e
ɑ
=20mm;当h
ɑ
》600mm时,;σs、σ
p
表示受拉边或受压较小边的纵向普通钢筋、预应力筋的应力,单位为n/mm2;m表示管片主体弯矩设计值,单位为kn
·
m;fc表示超高性能混凝土轴心抗压强度设计值,单位为n/mm2;f
t
表示超高性能混凝土轴心抗拉强度设计值,单位为n/mm2;fy、f
py
表示管片主体普通钢筋、预应力筋抗拉强度设计值,单位为n/mm2;f 'y、f '
py
表示管片主体普通钢筋、预应力筋抗压强度设计值,单位为n/mm2;a
s 、a's表示受拉区、受压区纵向普通钢筋的截面面积,单位为mm2;a
p
、a'
p
表示受拉区、受压区纵向预应力钢筋的截面面积,单位为mm2;α1表示等效矩形应力图系数;σ'
p0
表示受压区纵向预应力钢筋合力点处混凝土法向应力等于零时的预应力筋应力,单位为n/mm2;b表示截面的腹板宽度,单位为mm;bf表示受拉区翼缘的宽度,单位为mm;对于t形截面,b
f =b;b'f表示受压区翼缘的宽度,单位为mm;h0表示等效矩形截面有效高度,单位为mm;h f
,h' f
表示受拉区,受压区翼缘高度,单位为mm;ξb表示相对界限受压区高度;ξ表示相对受压区高度;x表示混凝土受压区高度,单位为mm;
ɑs、
ɑ
p
表示受拉区纵向普通钢筋合力点、预应力钢筋合力点至截面受压边缘的距离,单位为mm;
ɑ
's、
ɑ
'
p
表示受压区纵向普通钢筋合力点、预应力钢筋合力点至截面受压边缘的距离,单位为mm;
ɑ
表示纵向普通受拉钢筋和预应力受拉钢筋的合力点至截面近边缘的距离,单位为mm。
39.本实施例还提供了该管片的施工方法,包括如下步骤:步骤一:焊接、绑扎钢筋笼的主体框架;步骤二:在钢筋笼内部布设椭圆腔模具,而后在模具中浇筑泡沫混凝土,并在模具中插入短钢筋;步骤三:完成钢筋笼剩余部分焊接与绑扎,并将短钢筋固定在钢筋笼上,对泡沫混凝土进行养护,待其达到一定强度,脱去模具;步骤四:吊放钢筋笼与椭圆腔组合体于管片模具中,并安装注浆孔预留套筒,进行超高性能混凝土浇筑;步骤五:将浇筑好的管片随着模具送进蒸养室,蒸养结束后脱模、编号,检查管片是否有破损,如有破损进行修补后备用;步骤六:将管片吊运置于水池养护7~14天,出水后自然养护至28天。
40.在本实施例中,采用的超高性能混凝土是一种纤维增强水泥复合材料,具有高强度、高韧性、低孔隙率的特性,其本质是标准抗压强度不少于120mpa的一类混凝土的统称;因此其抗压强度远高于普通混凝土,同时又具有良好的防水、耐腐蚀性。在相同设计荷载下,超高性能混凝土结构比普通钢筋混凝土结构更加轻便。
41.从结构受力方面,椭圆腔能够防止内部应力集中,受力性能更好;外部采用超高性能混凝土,既提高管片的整体强度和刚度,又增强了接头局部承载能力;从结构耐久性能方面,管片主体采用超高性能混凝土,该材料自身颗粒细小,结构紧密,具有优越的抗渗性能和抗侵蚀能力,从根本上减少渗透路径,减缓了钢筋发生锈蚀速度,提高了管片耐久性能;从结构安全方面,由于超高性能混凝土较高抗压强度,管片整体承载能力有较大的提高,对比相同尺寸下的普通混凝土管片,本实施例的管片有较高的结构安全储备,适用于地下结构长期服役使用要求;从经济效益方面,本实施例在椭圆腔中填充了泡沫混凝土,减少了昂贵的超高性能混凝土用量;因超高性能混凝土中混杂钢纤维,可以抵抗一定程度拉应力,进而可以减少钢筋用量,从而实现管片整体造价;从施工便利方面看,由于内部填充了泡沫混凝土,从而大大减少了预制管片的重量,显著降低了装备施工中的托举和吊装要求,方便管片运输与安装,实现高效施工,管片重量减少可使得单块管片尺寸放大,相同直径的隧道结构接缝数量明显减少,可有效提高结构整体性能。
42.实施例2本实施例提供的闭腔薄壁超高性能混凝土盾构隧道管片的参数设置如下:该管片的外径为6200mm,壁厚为350mm,环宽为1500mm;该管片整体采用超高性能混凝土材料,混凝土等级为uc120,采用的钢筋型号为hrb400,混凝土保护层厚度取20mm,最小配筋率,设计载荷为最大正弯矩设
计值为277.0kn
·
m,对应轴力设计值为-1867.5kn。
43.本实施例提供了闭腔薄壁超高性能混凝土盾构隧道管片的设计方法,包括:步骤1:计算等效i型截面尺寸取值;宽度b=400mm,翼缘板宽度bf=b'f=1500mm,高度h=350mm,翼缘板高度hf=h'
f =75mm;步骤2:对管片按照矩形正截面进行内力复核;分别按受弯构件正截面承载力和大偏心受压构件正截面承载力计算进行内力复核,并进行环向主筋配筋面积的计算;2.1)受弯构件正截面承载力验算:设定满足以下条件:设定满足以下条件:若a's《0mm2,则按照最小配筋率配筋即a's=ρ
min
a;通过计算a's=-1851mm2《0mm2,按照最小配筋率则a's=ρ
min
a=1232.35mm2;as=3142.14mm2;因此该管片的配筋方案为:4a16 8a20;故可得:由上述公式可知,其满足验证条件。
44.2.2)大偏心受压构件正截面承载力验算:,174.9mm<275mm;
其中,此处未加预紧力钢筋,此处的as即为a。
45.经计算,a's=3312.89mm2》0mm2,as=3024.12mm2,因此闭腔薄壁超高性能混凝土盾构隧道管片配筋方案为6a18 6a20。
46.显然,上述实施例仅仅是为清楚地说明所作的举例,而并非对实施方式的限定。对于所属领域的普通技术人员来说,在上述说明的基础上还可以做出其它不同形式的变化或变动。这里无需也无法对所有的实施方式予以穷举。而由此所引伸出的显而易见的变化或变动仍处于本发明创造的保护范围之中。
再多了解一些
本文用于创业者技术爱好者查询,仅供学习研究,如用于商业用途,请联系技术所有人。