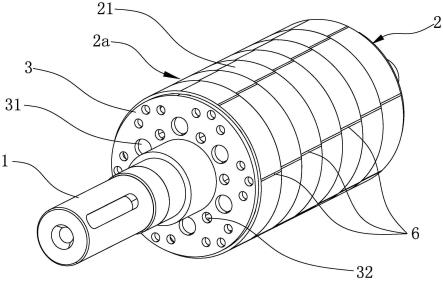
1.本技术涉及电机技术领域,尤其是涉及一种永磁电机的转子、该转子的装配工装及其装配方法。
背景技术:
2.永磁电机主要是由转子、端盖及定子等各部件组成。永磁电机的定子结构与普通的感应电动机的结构相似,转子结构与普通的感应电动机的最大不同是在转子上放有高质量的永磁体磁极,根据在转子上安放永磁体的位置的不同,永磁电机通常被分为表面式转子结构和内置式转子结构;永磁体的放置方式对永磁电机性能影响很大;表面式转子结构产生的异步转矩很小,仅适合于启动要求不高的场合,很少应用。内置式转子结构启动性能好,绝大多数永磁同步电动机都采用这种结构。
3.电机的电磁力一方面产生使电机旋转的转矩,另一方面会引起电机的定转子变形和振动,从而引起电机的振动,该种类型的振动是电机的一个寄生效应,只要电机发生旋转和产生转矩,就会带来相关的电磁振动。电机振动不仅会产生噪声,还会在电机的运行过程中出现转子偏心和转轴弯曲的情况。传统结构永磁电机中永磁体(磁钢)的排列法,启动和无负载时对转矩有较高的要求。其通常需要较大的转矩,即需要大电流,并产生较大的电磁振动。定子电流在启动过程中有较大的峰值,对应的电磁转矩也有较大的脉动,这会导致永磁电机在启动时发生振动,震动过大会恶化轴承工作环境,使转子和定子接触,电机失效。当电源电压过低又会致使发动转矩过小,启动过程存在电流冲击,当驱动功率较大或频繁起停时,对电网影响较大。
技术实现要素:
4.为了减小永磁电机的转矩脉动并提高其装配的高效性和稳定性,本技术提供一种永磁电机的转子、该转子的装配工装及其装配方法。
5.第一方面,本技术提供的一种永磁电机的转子采用如下的技术方案:一种永磁电机的转子,包括转轴和套设在所述转轴上的转子铁芯;所述转子铁芯包括至少三段,每一段转子铁芯由若干个硅钢片压装组成,相邻两段所述转子铁芯之间通过激光焊接固连;每一段所述转子铁芯内均具有安装孔,所述安装孔内嵌设有永磁体;任意相邻两段所述转子铁芯上相对应的永磁体均沿转子铁芯的周向顺时针或逆时针错开设置且错开的角度度数为α;α=360/[q*(n 1)] ;其中:q为转子铁芯对应的定子槽数,n为转子铁芯的段数。
[0006]
通过采用上述技术方案,转子铁芯分为多段且多段转子铁芯的冲片沿周向偏移一定的角度形成斜极;相对传统结构的永磁电机能够减少电机启动的启动力矩,即减少永磁电机启动时的转矩脉动和启动电流,降低永磁电机的振动和噪音,可实现平稳的启动电机,在确保启动阶段的转矩大、带载能力强的同时,确保启动电流不会过大。确保在频繁重载应
用场合下,电机在启动阶段转矩较高、电流较为平稳,实现电机的稳定启动,降低转矩脉动。
[0007]
理论上斜极方式可以完全消除电机的齿槽转矩。但是在实践中由于材料存在离散性、工艺存在差异性等因数造成电机不能完全消除齿槽转矩。本技术中通过无数次试验和实践经验,最终得出转子斜极中相应的参数,即转子铁芯沿周向顺时针或逆时针错开的角度与其对应的定子槽数以及转子铁芯的段数相关,并总结出相应计算公式,这样设置的电机斜极可以尽可能的减小永磁电机的转矩脉动,实现最优化的磁极方案,减少永磁电机的振动和磨损,提高其启动及运行的平稳可靠性。
[0008]
可选的,所述转子铁芯的段数为六段至九段,相邻两段所述转子铁芯上相对应的永磁体沿转子铁芯的周向错开0.6
°
~3
°
。
[0009]
作为优选方案,转子铁芯对应的定子槽数为24,转子铁芯的段数为8段,根据计算可得,相邻两段所述转子铁芯上相对应的安装孔以及永磁体沿转子铁芯的周向错开1.667
°
。具体的永磁电机中定子和转子相关的参数根据所需要的功率、实际安装空间等要求进行确定。通过采用上述技术方案,能够得到一个比较优化的配置,满足使用要求,并实现最佳性价比。
[0010]
可选的,每一段所述转子铁芯内的所述永磁体有若干组,若干组永磁体沿所述转子铁芯周向均匀间隔分布;每组所述永磁体有两个且呈v型设置,每组所述永磁体形成的v型结构的尖端均朝向所述转子铁芯的中心且每组所述永磁体形成的v型结构的夹角为120
°
~145
°
。
[0011]
内置式转子永磁电机的设计极力追求小气隙与小间隙隔磁桥,以增大磁阻转矩分量,实现基速点的最大转矩/电流控制与最高转速点的最大功率弱磁控制。在最大峰值转矩与高速工况运行时,由于强烈的磁路饱和与深度弱磁控制,使得电机的气隙磁场波形严重畸变,其径向分量可能导致定子铁芯和内置式转子产生较大的振动和形变。高速运行时,转子除受电磁径向力波外,还受到较大的离心应力和热应力,由此导致转子外径表面形变与气隙长度不对称。电机的转子磁路结构、电磁径向力波、转子离心应力与热应力、转子支撑系统引起的气隙偏心、转子硅钢片力学性能之间的相互制约限制了内置式转子电机最大安全运行转速的提高。本技术中通过采用上述技术方案,转子每极对应一组永磁体,每组永磁体包含两个,即电机总永磁体块数是电机极数的2倍,每极中两个永磁体形状和极性相同,相邻磁极的永磁体极性相反。每组永磁体形成v型结构,根据转子铁芯中硅钢片的抗拉强度大于屈服强度的特点,改变转子的应力分布,减小最大形变,并使得电机的转矩脉动最小。
[0012]
可选的,每一段所述转子铁芯中心具有用于安装所述转轴的中心孔;每一段所述转子铁芯上对应每一组所述永磁体均开设有辅助孔,所述辅助孔位于对应的一组永磁体形成的v型结构开口内;每一段所述转子铁芯上对应每一组所述永磁体还开设有通孔,所述通孔位于对应的所述永磁体形成的v型结构尖端与所述转子铁芯的中心孔之间;每一段所述转子铁芯上位于相邻两组所述永磁体之间还开设有定位孔;每一组所述永磁体中两个永磁体对应的安装孔之间具有加强支撑条;每个所述安装孔的两端还具有隔磁孔。
[0013]
通过采用上述技术方案,辅助孔和通孔能够尽可能减轻转子重量,降低离心力;同时还具有通风散热的作用;辅助孔设置在永磁体形成的v型结构开口内,能够控制气隙磁场
的波形,也能够有效地降低电机的振动和噪声,提高永磁体的聚磁效应与抗退磁能力,减小永磁体厚度,使直轴电抗增加,在相同电枢电流的情况下可以提高去磁能力,提高恒功率调速的范围。定位孔的设置便于转子铁芯的定位组装。每组永磁体对应的安装孔之间设置加强支撑条,结合永磁体v型结构布置,在改变转子外径表面形变的分布的同时,使得最大离心应力点转移到加强支撑条上。该最大离心应力性质为拉应力,受转子铁芯材料抗拉强度的制约,由于转子铁芯材料的抗拉强度大于屈服强度,故电机转子高速运行的机械性能显著地增强了。每个安装孔的两端均设有隔磁孔。隔磁孔连通安装孔。隔磁孔的形状可为长圆形、椭圆形或梯形,也可为方形或类方形。设置有隔磁孔,能有效的减少漏磁,改善气隙磁场的波形。
[0014]
可选的,最外层的两段转子铁芯外侧分别设置有前端板和后端板,所述转轴的两端分别穿过所述前端板和后端板,所述后端板的外侧还设有套设在所述转轴上的压环;所述前端板和后端板均开设有与所述安装孔相对应并连通的观测孔以及与所述通孔相对应并连通的通风孔。
[0015]
通过采用上述技术方案,观测孔用于观测安装孔内的永磁体是否损坏,通风孔用于转子铁芯内部空气对流均匀,有利于转子铁芯的散热。
[0016]
可选的,每一段所述转子铁芯的外周面上均具有若干个沿所述转子铁芯轴向的焊道,所述焊道贯穿至所述转子铁芯的两端端面;若干个所述焊道沿所述转子铁芯的周向间隔分布。
[0017]
作为优选方案,每一段所述转子铁芯的外周面上均具有8个焊道,8个焊道均匀间隔分布在转子铁芯的外周面上,相邻两段转子铁芯上的焊道一一对应设置。通过采用上述技术方案,便于转子铁芯的激光焊接,并保证其稳定牢固性,装配和连接更加精准可靠。
[0018]
第二方面,本技术提供一种永磁电机转子的装配工装,用于装配上述的永磁电机的转子,其采用如下的技术方案:一种永磁电机转子的装配工装,包括用于定位压装每一段转子铁芯的叠片组压装机构和用于将若干段转子铁芯压装在一起的转子旋压机构;所述叠片组压装机构包括底座、设置在所述底座上的下压板、竖向设置在所述下压板上的芯轴、能够套设在所述芯轴上端的上压板以及与第一液压机相连接且能够上下移动的推杆套筒;所述上压板上还设有能够穿过所述上压板和转子铁芯的定位孔并连接在所述下压板上的定位柱;所述转子旋压机构包括工作台和驱动电机,所述工作台上设置有转盘,所述驱动电机的输出轴与所述转盘相连接且能够带动所述转盘周向转动,所述转盘上方设有与第二液压机相连接且能够上下移动的顶板;所述顶板上设有用于固定电机转轴的定位结构。
[0019]
底座的一侧以及工作台的一侧均设置有激光焊接机,两台激光焊接机分别与叠片组压装机构和转子旋压机构配合使用,定位柱下端可以设置螺纹,下压板上设置与定位柱下端相配合的螺纹孔。通过采用上述技术方案,叠片组压装机构用于组装各段转子铁芯时,利用第一液压机将硅钢片叠压密实,再利用激光焊接机焊接各段转子铁芯中的各个硅钢片;转子旋压机构将各段转子铁芯压装到电机的转轴上,再利用激光焊接机将各段转子铁芯焊接固连,在此过程中,每增加一段转子铁芯,就通过制动伺服电机带动转盘转动预定的角度,从而形成斜极结构。整个装配工装能够提高电机转子装配的工作效率,并保证电机转
子装配的稳定可靠性以及精准性。
[0020]
可选的,所述叠片组压装机构还包括机架,所述机架上设有滑轨,所述滑轨上滑动设置有滑动板,所述底座固设在所述滑动板上,所述底座上开设有连接孔,所述下压板的底部具有能够嵌入所述连接孔的凸台;所述芯轴上端固连有吊环;所述工作台底部具有箱体,所述转盘中部具有贯穿孔,所述转盘底部具有伸入所述箱体内的连接筒,所述连接筒与所述工作台通过轴承周向转动连接,所述连接筒的中心上下两端贯穿且与所述贯穿孔相连通,所述连接筒上套设有从动轮;所述驱动电机为制动伺服电机,所述驱动电机固设在所述箱体内,所述驱动电机的输出轴上具有主动轮,所述主动轮与所述从动轮之间通过皮带或链条或齿轮啮合相连接。
[0021]
通过采用上述技术方案,每一段转子铁芯依次放置并定位在转盘上,顶板与电机的转轴上端固定连接,在第二液压机的带动下向下移动,转轴下移穿过转子铁芯到达预定位置后,转轴带着该段转子铁芯在第二液压机的带动下向上移动,再放入下一段转子铁芯,制动伺服电机带动转盘旋转预定的角度,并锁死防止角度发生变化,然后转轴再下移穿入该段转子铁芯,依次重复动作,最终将所有转子铁芯均套设在转轴上;在此过程中,还需要利用激光焊接机将相邻两段转子铁芯焊接固连。
[0022]
可选的, 所述定位结构可以是顶板上设置的能够螺接在电机转轴端部的连接螺栓。作为替代方案,所述定位结构还可以是三爪卡盘。这样便于顶板与电机转轴方便、快速、稳固的实现连接。
[0023]
第三方面,本技术提供一种永磁电机转子的加工方法,利用上述的装配工装装配上述的永磁电机的转子,上述的“每一段转子铁芯”可称之为“转子铁芯段”,其包括以下步骤:s1、加工转子铁芯的冲片:s11、加工每段转子铁芯的硅钢片冲片,根据每段永磁体的长度以及硅钢片冲片的厚度确认每段转子铁芯的硅钢片冲片的数量;s2、加工转子铁芯段,其中,加工转子铁芯段的步骤包括:s21、将叠片组压装机构中的芯轴放在下压板上;s22、将转子铁芯的硅钢片冲片套设在芯轴上,利用芯轴和定位柱定位;s23、启动第一液压机带动推杆套筒下移从而将多个硅钢片冲片压紧,再用螺钉紧固组成转子铁芯段;s24、用激光焊接机将转子铁芯段中的多个硅钢片冲片焊接牢固,再将转子铁芯段从芯轴和定位柱上脱离备用;s25、在焊接后的转子铁芯段的安装孔内塞入永磁体;s26、重复上述步骤s21至s25,加工出多个转子铁芯段;s3、多个转子铁芯段装配成转子铁芯,其中,将多个转子铁芯段组装成转子铁芯包括:s31、将电机的转轴的一端固定安装在转子旋压机构的顶板上,并使电机的转轴竖直朝下;s32、将转子的前端板和第一个嵌设有永磁体的转子铁芯段安装在转盘上,启动第二液压机带动顶板以及顶板上固连的转轴向下移动,使得转轴插入前端板和第一个转子铁
芯段中,前端板和第一个转子铁芯段压入转轴上至轴肩位置,定位销定位,设定此位置为起始角度0
°
;s33、启动制动伺服电机带动转盘转动预定角度,利用制动伺服电机的制动力锁定转盘,使待压装的转子铁芯段与已压装的转子铁芯段保持所需斜极角度;s34、启动第二液压机带动顶板、转轴以及已压装的转子铁芯段向上移动,在转盘上放入下一个转子铁芯段;s35、重复上述步骤,直至若干个转子铁芯段均压装在转轴上,最后压装后端板和压环,组成完整转子,然后拆卸下来。
[0024]
通过采用上述技术方案,能够高效的加工生产永磁电机的转子,并形成所需角度的斜极结构,同时提高了转子铁芯装配的精准可靠性。
[0025]
可选的,在上述步骤s11中,每个转子铁芯段的长度=每段永磁体的长度 (0.2~0.5)mm;在上述步骤s22中,将6~9个转子铁芯段的硅钢片冲片套设在芯轴上,每一组硅钢片冲片对应一个转子铁芯段,相邻两组硅钢片冲片之间用隔片隔开。
[0026]
通过采用上述技术方案,能够同时加工6~9个转子铁芯段,通过设置隔片将相邻两组硅钢片冲片隔开,防止多个转子铁芯段焊接粘连,这样能够提高加工效率。
[0027]
综上所述,本技术包括以下至少一种有益技术效果:1.本技术中的转子采用斜极结构,并具体限定了参数,其能够大大减少电机启动的启动力矩,降低电机振动和噪音,实现平稳的启动电机。可在确保启动阶段的转矩大、带载能力强的同时,确保启动电流不会过大。并能够确保在频繁重载应用场合下,电机在启动阶段转矩较高、电流较为平稳,实现电机的稳定启动。
[0028]
2.本技术中通过转子旋压机构将各段转子铁芯压装到电机的转轴上,再利用激光焊接机将各段转子铁芯焊接固连,在此过程中,每增加一段转子铁芯,就通过制动伺服电机带动转盘转动预定的角度,从而形成斜极结构。整个装配工装能够提高电机转子装配的工作效率,并保证电机转子装配的稳定可靠性以及精准性。
[0029]
3.本技术中加工转子的方法能够高效的加工生产永磁电机的转子,并形成所需角度的斜极结构,同时提高了转子铁芯装配的精准可靠性。
[0030]
4.本技术中加工转子的方法能够同时加工6~9个转子铁芯段,通过设置隔片将相邻两组硅钢片冲片隔开,防止多个转子铁芯段焊接粘连,从而大大提高了加工效率。
附图说明
[0031]
图1是本技术中转子的第一视角立体结构示意图。
[0032]
图2是本技术中转子的第二视角立体结构示意图。
[0033]
图3是本技术中转子的剖视结构示意图。
[0034]
图4是本技术中转子的爆炸结构示意图。
[0035]
图5是本技术中一个转子铁芯段的立体结构示意图。
[0036]
图6是本技术中叠片组压装机构的立体结构示意图。
[0037]
图7是本技术中叠片组压装机构的剖视结构示意图。
[0038]
图8是本技术中转子旋压机构的立体结构示意图。
[0039]
图9是本技术中转子旋压机构的剖视结构示意图。
[0040]
图中,1、转轴;2、转子铁芯;2a、转子铁芯段;21、硅钢片;22、安装孔;23、永磁体;24、中心孔;25、辅助孔;26、通孔;27、定位孔;28、加强支撑条;29、隔磁孔;3、前端板;31、观测孔;32、通风孔;4、后端板;5、压环;6、焊道;7、叠片组压装机构;71、底座;71a、连接孔;72、下压板;72a、凸台;73、芯轴;73a、吊环;74、上压板;75、推杆套筒;76、定位柱;77、机架;77a、滑轨;78、滑动板;8、转子旋压机构;81、工作台;81a、箱体;82、驱动电机;83、转盘;83a、贯穿孔;83b、连接筒;84、顶板;85、连接螺栓;86、从动轮;87、主动轮;88、皮带。
具体实施方式
[0041]
以下结合附图1-附图9,对本技术作进一步详细说明。
[0042]
实施例1参照图1和图2,本实施例中永磁电机的转子包括转轴1和套设在转轴1上的转子铁芯2;转子铁芯2包括至少三段,每一段转子铁芯2由若干个硅钢片21压装组成,每一段转子铁芯2可以称之为转子铁芯段2a;相邻两个转子铁芯段2a之间通过激光焊接固连,参照图3和图4,每一个转子铁芯段2a内均具有安装孔22,安装孔22内嵌设有永磁体23;任意相邻两个转子铁芯段2a上相对应的永磁体23均沿转子铁芯2的周向顺时针或逆时针错开设置且错开的角度度数为α;α=360/[q*(n 1)] ;其中:q为转子铁芯2对应的定子槽数,n为转子铁芯2的段数。
[0043]
进一步的,本技术中转子铁芯2的段数为六段至九段,相邻两个转子铁芯段2a上相对应的永磁体23沿转子铁芯2的周向错开0.6
°
~3
°
。更进一步的,转子铁芯2对应的定子槽数为24,转子铁芯2的段数为8段,根据计算可得,相邻两个转子铁芯段2a上相对应的安装孔22以及永磁体23沿转子铁芯2的周向错开1.667
°
。具体的永磁电机中定子和转子相关的参数根据所需要的功率、实际安装空间等要求进行确定。能够得到一个比较优化的配置,满足使用要求,并实现最佳性价比。每一段转子铁芯2内的永磁体23有若干组,若干组永磁体23沿转子铁芯2周向均匀间隔分布;每组永磁体23有两个且呈v型设置,每组永磁体23形成的v型结构的尖端均朝向转子铁芯2的中心且每组永磁体23形成的v型结构的夹角为120
°
~145
°
。内置式转子永磁电机的设计极力追求小气隙与小间隙隔磁桥,以增大磁阻转矩分量,实现基速点的最大转矩/电流控制与最高转速点的最大功率弱磁控制。在最大峰值转矩与高速工况运行时,由于强烈的磁路饱和与深度弱磁控制,使得电机的气隙磁场波形严重畸变,其径向分量可能导致定子铁芯和内置式转子产生较大的振动和形变。高速运行时,转子除受电磁径向力波外,还受到较大的离心应力和热应力,由此导致转子外径表面形变与气隙长度不对称。电机的转子磁路结构、电磁径向力波、转子离心应力与热应力、转子支撑系统引起的气隙偏心、转子硅钢片21力学性能之间的相互制约限制了内置式转子电机最大安全运行转速的提高。本技术中转子每极对应一组永磁体23,每组永磁体23包含两个,即电机总永磁体23块数是电机极数的2倍,每极中两个永磁体23形状和极性相同,相邻磁极的永磁体23极性相反。每组永磁体23形成v型结构,根据转子铁芯2中硅钢片21的抗拉强度大于屈服强度的特点,改变转子的应力分布,减小最大形变,并使得电机的转矩脉动最小。
[0044]
参照图4和图5,每一个转子铁芯段2a中心具有用于安装转轴1的中心孔24;每一个转子铁芯段2a上对应每一组永磁体23均开设有辅助孔25,辅助孔25位于对应的一组永磁体23形成的v型结构开口内;每一个转子铁芯段2a上对应每一组永磁体23还开设有通孔26,通
孔26位于对应的永磁体23形成的v型结构尖端与转子铁芯2的中心孔24之间;每一个转子铁芯段2a上位于相邻两组永磁体23之间还开设有定位孔27;每一组永磁体23中两个永磁体23对应的安装孔22之间具有加强支撑条28;每个安装孔22的两端还具有隔磁孔29。辅助孔25和通孔26能够尽可能减轻转子重量,降低离心力;同时还具有通风散热的作用;辅助孔25设置在永磁体23形成的v型结构开口内,能够控制气隙磁场的波形,也能够有效地降低电机的振动和噪声,提高永磁体23的聚磁效应与抗退磁能力,减小永磁体23厚度,使直轴电抗增加,在相同电枢电流的情况下可以提高去磁能力,提高恒功率调速的范围。定位孔27的设置便于转子铁芯2的定位组装。每组永磁体23对应的安装孔22之间设置加强支撑条28,结合永磁体23v型结构布置,在改变转子外径表面形变的分布的同时,使得最大离心应力点转移到加强支撑条28上。该最大离心应力性质为拉应力,受转子铁芯2材料抗拉强度的制约,由于转子铁芯2材料的抗拉强度大于屈服强度,故电机转子高速运行的机械性能显著地增强了。每个安装孔22的两端均设有隔磁孔29。隔磁孔29连通安装孔22。隔磁孔29的形状可为长圆形、椭圆形或梯形,也可为方形或类方形。设置有隔磁孔29,能有效的减少漏磁,改善气隙磁场的波形。
[0045]
参照图1和图2,最外层的两个转子铁芯段2a外侧分别设置有前端板3和后端板4,转轴1的两端分别穿过前端板3和后端板4,后端板4的外侧还设有套设在转轴1上的压环5;前端板3和后端板4均开设有与安装孔22相对应并连通的观测孔31以及与通孔26相对应并连通的通风孔32。观测孔31用于观测安装孔22内的永磁体23是否损坏,通风孔32用于转子铁芯2内部空气对流均匀,有利于转子铁芯2的散热。每一段转子铁芯2的外周面上均具有若干个沿转子铁芯2轴向的焊道6,焊道6贯穿至转子铁芯2的两端端面;若干个焊道6沿转子铁芯2的周向间隔分布。作为优选方案,每一个转子铁芯段2a的外周面上均具有8个焊道6,8个焊道6均匀间隔分布在转子铁芯2的外周面上,相邻两个转子铁芯段2a上的焊道6一一对应设置。便于转子铁芯2的激光焊接,并保证其稳定牢固性,装配和连接更加精准可靠。
[0046]
其实施例原理是:本技术中转子铁芯2分为多段且多个转子铁芯段2a的冲片沿周向偏移一定的角度形成斜极;相对传统结构的永磁电机能够减少电机启动的启动力矩,即减少永磁电机启动时的转矩脉动和启动电流,降低永磁电机的振动和噪音,可实现平稳的启动电机,在确保启动阶段的转矩大、带载能力强的同时,确保启动电流不会过大。确保在频繁重载应用场合下,电机在启动阶段转矩较高、电流较为平稳,实现电机的稳定启动,降低转矩脉动。
[0047]
理论上斜极方式可以完全消除电机的齿槽转矩。但是在实践中由于材料存在离散性、工艺存在差异性等因数造成电机不能完全消除齿槽转矩。本技术中通过无数次试验和实践经验,最终得出转子斜极中相应的参数,即转子铁芯2沿周向顺时针或逆时针错开的角度与其对应的定子槽数以及转子铁芯2的段数相关,并总结出相应计算公式,这样设置的电机斜极可以尽可能的减小永磁电机的转矩脉动,实现最优化的磁极方案,减少永磁电机的振动和磨损,提高其启动及运行的平稳可靠性。
[0048]
实施例2本实施例公开一种用于生产制造上述实施例1中永磁电机转子的装配工装,其包括用于定位压装每一段转子铁芯2的叠片组压装机构7和用于将若干段转子铁芯2压装在一起的转子旋压机构8。
[0049]
具体来说,参照图6和图7,叠片组压装机构7包括底座71、设置在底座71上的下压板72、竖向设置在下压板72上的芯轴73、能够套设在芯轴73上端的上压板74以及与第一液压机相连接且能够上下移动的推杆套筒75;上压板74上还设有能够穿过上压板74和转子铁芯2的定位孔27并连接在下压板72上的定位柱76。叠片组压装机构7还包括机架77,机架77上设有滑轨77a,滑轨77a上滑动设置有滑动板78,底座71固设在滑动板78上,底座71上开设有连接孔71a,下压板72的底部具有能够嵌入连接孔71a的凸台72a;芯轴73上端固连有吊环73a。
[0050]
参照图8和图9,转子旋压机构8包括工作台81和驱动电机82,工作台81上设置有转盘83,驱动电机82的输出轴与转盘83相连接且能够带动转盘83周向转动,转盘83上方设有与第二液压机相连接且能够上下移动的顶板84;顶板84上设有用于固定电机转轴1的定位结构。该定位结构可以是顶板84上设置的能够螺接在电机转轴1端部的连接螺栓85,也可以是三爪卡盘,这样便于顶板84与电机转轴1方便、快速、稳固的实现连接。工作台81底部具有箱体81a,转盘83中部具有贯穿孔83a,转盘83底部具有伸入箱体81a内的连接筒83b,连接筒83b与工作台81通过轴承周向转动连接,连接筒83b的中心上下两端贯穿且与贯穿孔83a相连通,连接筒83b上套设有从动轮86;驱动电机82为制动伺服电机,驱动电机82固设在箱体81a内,驱动电机82的输出轴上具有主动轮87,主动轮87与从动轮86之间通过皮带88或链条或齿轮啮合相连接。
[0051]
其实施例原理是:底座71的一侧以及工作台81的一侧均设置有激光焊接机,两台激光焊接机分别与叠片组压装机构7和转子旋压机构8配合使用,定位柱76下端可以设置螺纹,下压板72上设置与定位柱76下端相配合的螺纹孔。叠片组压装机构7用于组装各段转子铁芯2时,利用第一液压机将硅钢片21叠压密实,再利用激光焊接机焊接各段转子铁芯2中的各个硅钢片21;转子旋压机构8将各段转子铁芯2压装到电机的转轴1上,再利用激光焊接机将各段转子铁芯2焊接固连,在此过程中,每增加一段转子铁芯2,就通过制动伺服电机带动转盘83转动预定的角度,从而形成斜极结构。整个装配工装能够提高电机转子装配的工作效率,并保证电机转子装配的稳定可靠性以及精准性。使用时,每一段转子铁芯2依次放置并定位在转盘83上,顶板84与电机的转轴1上端固定连接,在第二液压机的带动下向下移动,转轴1下移穿过转子铁芯2到达预定位置后,转轴1带着该段转子铁芯2在第二液压机的带动下向上移动,再放入下一段转子铁芯2,制动伺服电机带动转盘83旋转预定的角度,并锁死防止角度发生变化,然后转轴1再下移穿入该段转子铁芯2,依次重复动作,最终将所有转子铁芯2均套设在转轴1上;在此过程中,还需要利用激光焊接机将相邻两段转子铁芯2焊接固连。
[0052]
实施例3本实施例公开一种利用上述实施例2中的装配工装装配上述实施例1中永磁电机转子的方法,其具体包括以下步骤:s1、加工转子铁芯2的冲片:s11、加工每段转子铁芯2的硅钢片21冲片,根据每段永磁体23的长度以及硅钢片21冲片的厚度确认每段转子铁芯2的硅钢片21冲片的数量;每段转子铁芯2的长度=每段永磁体23的长度 (0.2~0.5)mm;s2、加工转子铁芯段2a,其中,加工转子铁芯段2a的步骤包括:
s21、将叠片组压装机构7中的芯轴73放在下压板72上;s22、将转子铁芯2的硅钢片21冲片套设在芯轴73上,利用芯轴73和定位柱76定位;s23、启动第一液压机带动推杆套筒75下移从而将多个硅钢片21冲片压紧,再用螺钉紧固组成转子铁芯段2a;s24、用激光焊接机将转子铁芯段2a中的多个硅钢片21冲片焊接牢固,再将转子铁芯段2a从芯轴73和定位柱76上脱离备用;s25、在焊接后的转子铁芯段2a的安装孔22内塞入永磁体23;s26、重复上述步骤s21至s25,加工出多个转子铁芯段2a;s3、多个转子铁芯段2a装配成转子铁芯2,其具体步骤包括:s31、将电机的转轴1的一端固定安装在转子旋压机构8的顶板84上,并使电机的转轴1竖直朝下;s32、将转子的前端板3和第一个嵌设有永磁体23的转子铁芯段2a安装在转盘83上,启动第二液压机带动顶板84以及顶板84上固连的转轴1向下移动,使得转轴1插入前端板3和第一个转子铁芯段2a中,前端板3和第一个转子铁芯段2a压入转轴1上至轴肩位置,定位销定位,设定此位置为起始角度0
°
;s33、启动制动伺服电机带动转盘83转动预定角度,利用制动伺服电机的制动力锁定转盘83,使待压装的转子铁芯段2a与已压装的转子铁芯段2a保持所需斜极角度;s34、启动第二液压机带动顶板84、转轴1以及已压装的转子铁芯段2a向上移动,在转盘83上放入下一个转子铁芯段2a;s35、重复上述步骤,直至若干个转子铁芯段2a均压装在转轴1上,最后压装后端板4和压环5,组成完整转子,然后拆卸下来。
[0053]
在上述步骤s22中,将6~9个转子铁芯段2a的硅钢片21冲片套设在芯轴73上,每一组硅钢片21冲片对应一个转子铁芯段2a,相邻两组硅钢片21冲片之间用隔片隔开。
[0054]
本技术中的装配方法能够高效的加工生产永磁电机的转子,并形成所需角度的斜极结构,同时提高了转子铁芯2装配的精准可靠性。本技术中的装配方法能够同时加工6~9个转子铁芯段2a,通过设置隔片将相邻两组硅钢片21冲片隔开,防止多个转子铁芯段2a焊接粘连,这样能够提高加工效率。
[0055]
本具体实施方式的实施例均为本技术的较佳实施例,并非依此限制本技术的保护范围,其中相同的零部件用相同的附图标记表示。故:凡依本技术的结构、形状、原理所做的等效变化,均应涵盖于本技术的保护范围之内。
再多了解一些
本文用于创业者技术爱好者查询,仅供学习研究,如用于商业用途,请联系技术所有人。