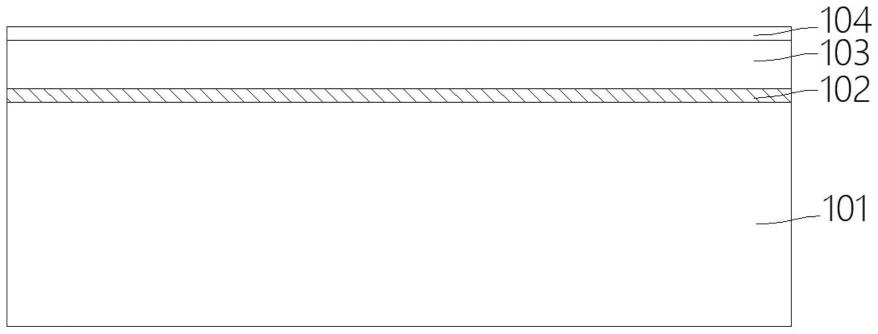
1.本发明涉及半导体制造技术领域,特别是涉及一种有源区顶角的形成方法及半导体结构。
背景技术:
2.以bcd、hvcmos、mcu、cis、eflash、iot memory等为代表的半导体器件,已经广泛应用于电源管理、显示驱动、led照明、汽车电子、摄像头模组、消费级电子等领域。例如在汽车电子领域,bcd、igbt、sic、mosfet、frd等工艺广泛应用于车灯控制、电源管理、新能源汽车逆变器、dcdc、obc、直流充电桩等关键零部件;在消费电子领域,bcd、cmos、bipolar、tvs、mosfet、bi-cmos等工艺平台,广泛应用于手机、笔记本电脑、智能家居、智能穿戴、物联网、5g等应用终端芯片的制造生产。
3.在半导体器件的制备工艺中,有源器件的制备工艺通常包括有源区的制备,有源区制备工艺即是针对浅沟槽隔离结构的刻蚀工艺,通过浅沟槽隔离出有源区,如图1-图5所示,其通常包括如下步骤:在衬底101上依次形成第一氧化层(通常为氧化硅)102、硬掩膜层(通常为氮化硅)103、及第二氧化层(通常为氧化硅)104;接着,在第二氧化层104上形成光刻胶并对其进行图案化;接着,以图形化的光刻胶层为掩膜,蚀刻所述第一氧化层102、硬掩膜层103、第二氧化层104、及衬底101,在所述衬底101中形成浅沟槽(sti)11,所述浅沟槽11隔离出有源区12;接着,采用磷酸回推(pull back)硬掩膜层103,以使得有源区12上的硬掩膜层103的线宽变得比有源区12小,从而使硬掩膜层103的外边缘能够显露下方的部分第一氧化层102,此时有源区12的顶部拐角为尖角形状。接着在所述浅沟槽11的底部及侧壁生长形成隔离氧化层201,接着,在所述浅沟槽11中沉积形成填充氧化层202。
4.在这个过程中,形成所述浅沟槽11的同时,会使有源区形成尖锐的顶角,有源区顶角的平缓程度对寄生器件的影响很大,顶角处越尖锐越容易引起寄生器件的双重开启。在后续形成所述隔离氧化层201的过程中,虽然该顶角在氧化作用下会变得圆润,但是其作用效果甚微,即使能将尖锐顶角圆角化,其形成圆角的曲率依然较大,且形成圆角的形状尺寸也很难控制,无法达到顶角圆角化的工艺要求。
5.因此,需要提出一种工艺方法,以稳定地将有源区顶角圆角化,同时圆角的形状尺寸还能够实现稳定可控。
6.需要说明的是,上面对技术背景的介绍只是为了方便对本技术的技术方案进行清楚、完整的说明,并方便本领域技术人员的理解而阐述的。不能仅仅因为这些方案在本技术的背景技术部分进行了阐述而认为上述技术方案为本领域技术人员所公知。
技术实现要素:
7.鉴于以上所述现有技术的缺点,本发明的目的在于提供一种有源区顶角的形成方法,稳定地将有源区顶角圆角化。
8.为实现上述目的及其他相关目的,本发明提供一种有源区顶角的形成方法,所述
形成方法包括如下步骤:
9.s1:提供半导体中间结构,所述半导体中间结构包括依次叠置的衬底、第一氧化层、硬掩膜层、第二氧化层,所述衬底中形成有浅沟槽,所述浅沟槽的底部及侧壁形成有隔离氧化层,填充氧化层填满于所述浅沟槽中;其中,所述浅沟槽隔离出位于所述衬底中的有源区,所述有源区上的硬掩膜层的线宽比有源区小,从而使所述硬掩膜层的外边缘能够显露下方的部分第一氧化层;
10.s2:采用湿法刻蚀所述填充氧化层、第一氧化层及隔离氧化层,使所述填充氧化层的上表面低于所述衬底的上表面,所述隔离氧化层高于所述填充氧化层的部分被去除,同时所述第一氧化层被所述硬掩膜层显露的部分也被去除,从而显露所述有源区的顶角。
11.优选地,所述形成方法还包括如下步骤:
12.s3:对所述有源区顶角进行氧化,形成牺牲氧化层,所述牺牲氧化层的内侧面为弧面;
13.s4:采用湿法刻蚀去除所述牺牲氧化层,使所述有源区的顶角形成为圆角形;
14.s5:在所述有源区的圆角形顶角处沉积形成覆盖氧化层,所述覆盖氧化层连接所述第一氧化层及所述隔离氧化层。
15.优选地,采用干法方式快速氧化所述有源区的顶角,以形成所述牺牲氧化层。
16.优选地,所述牺牲氧化层的刻蚀速率大于所述第一氧化层及所述隔离氧化层的刻蚀速率。
17.优选地,所述覆盖氧化层的厚度与所述第一氧化层及所述隔离氧化层的厚度相同。
18.优选地,采用炉管沉积形成所述覆盖氧化层。
19.优选地,所述半导体中间结构的形成过程包括:
20.s1-1:在所述衬底上依次形成所述第一氧化层、硬掩膜层、及第二氧化层;
21.s1-2:在所述第二氧化层上形成光刻胶并对其进行图案化,以图形化的光刻胶层为掩膜,蚀刻所述第一氧化层、硬掩膜层、第二氧化层形成图案化窗口,然后基于所述图案化窗口进一步刻蚀所述衬底形成所述浅沟槽;
22.s1-3:采用磷酸回推所述硬掩膜层,以使得所述有源区上的硬掩膜层的线宽变得比有源区小,从而使所述硬掩膜层的外边缘能够显露下方的部分第一氧化层;
23.s1-4:于所述浅沟槽的底部及侧壁生长形成隔离氧化层,然后在所述浅沟槽中填满所述填充氧化层。
24.优选地,所述填充氧化层采用高密度等离子体法沉积获得。
25.优选地,步骤s3中,利用具有氧化性的反应气体对所述有源区顶角进行氧化,反应温度为250~500摄氏度,所述反应气体包括氧气。
26.本发明还提供一种半导体结构,所述半导体结构包括:
27.衬底,所述衬底中形成有浅沟槽,所述浅沟槽隔离出位于所述衬底中的有源区,所述浅沟槽的底部及侧壁形成有隔离氧化层,填充氧化层填充于所述浅沟槽内,所述隔离氧化层的顶面与所述填充氧化层的顶面齐平,且低于所述衬底的上表面;
28.位于所述衬底上的第一氧化层,位于所述有源区上的第一氧化层的线宽比有源区小,从而使所述有源区的顶角显露出来,所述有源区的顶角为圆角形。
29.优选地,所述第一氧化层上依次叠置有硬掩膜层及第二氧化层。
30.优选地,所述填充氧化层采用高密度等离子体法沉积获得。
31.优选地,所述有源区的圆角形顶角处形成有覆盖氧化层,所述覆盖氧化层连接所述第一氧化层及所述隔离氧化层。
32.优选地,所述覆盖氧化层的厚度和第一氧化层及所述隔离氧化层的厚度相同。
33.优选地,采用炉管沉积形成所述覆盖氧化层。
34.如上所述,本发明提供一种有源区顶角的形成方法及半导体结构,该方法先对浅沟槽中的填充氧化层进行刻蚀,使其上表面低于衬底的上表面,从而为显露有源区的顶角区域做出准备,通过控制刻蚀后填充氧化层的厚度以来控制最终有源区顶角处形成的圆角尺寸大小;同时,对第一氧化层及隔离氧化层进行刻蚀,使有源区顶角部分的衬底材料彻底暴露出来。然后采用干法方式快速氧化有源区的顶角,形成牺牲氧化层,由于氧化速度的不同使得牺牲氧化层的内侧面形成为弧面,后续在去除牺牲氧化层进行去除后,自然地使有源区的顶角形成为圆角形。同时由于牺牲氧化层的质地较为疏松且密度较小,因此采用湿法刻蚀时,能够以较快的速度对其进行去除而不对其他氧化层造成影响。最后再使用炉管工艺在有源区的圆角形顶角处沉积形成圆弧状的覆盖氧化层。通过上述步骤能够有效地将有源区顶角圆角化,同时圆角的形状尺寸还能够实现稳定可控。
附图说明
35.图1显示为进行光刻前的截面示意图。
36.图2显示为光刻后形成浅沟槽的截面示意图。
37.图3显示为使用磷酸对氮化硅回推的截面示意图。
38.图4显示为在浅沟槽内形成隔离氧化层的截面示意图。
39.图5显示为在浅沟槽内形成填充氧化层的截面示意图。
40.图6显示为刻蚀后显露有源区顶角的截面示意图。
41.图7显示为在有源区顶角快速氧化形成牺牲氧化层的截面示意图。
42.图8显示为去除牺牲氧化层的截面示意图。
43.图9显示为形成覆盖氧化层的截面示意图。
44.图10显示为形成覆盖氧化层后在浅沟槽内再次形成填充氧化层的截面示意图。
45.元件标号说明
46.101
ꢀꢀꢀꢀꢀꢀꢀꢀꢀꢀꢀꢀꢀꢀꢀꢀꢀꢀꢀꢀꢀ
衬底
47.102
ꢀꢀꢀꢀꢀꢀꢀꢀꢀꢀꢀꢀꢀꢀꢀꢀꢀꢀꢀꢀꢀ
第一氧化层
48.103
ꢀꢀꢀꢀꢀꢀꢀꢀꢀꢀꢀꢀꢀꢀꢀꢀꢀꢀꢀꢀꢀ
硬掩膜层
49.104
ꢀꢀꢀꢀꢀꢀꢀꢀꢀꢀꢀꢀꢀꢀꢀꢀꢀꢀꢀꢀꢀ
第二氧化层
50.201
ꢀꢀꢀꢀꢀꢀꢀꢀꢀꢀꢀꢀꢀꢀꢀꢀꢀꢀꢀꢀꢀ
隔离氧化层
51.202
ꢀꢀꢀꢀꢀꢀꢀꢀꢀꢀꢀꢀꢀꢀꢀꢀꢀꢀꢀꢀꢀ
填充氧化层
52.203
ꢀꢀꢀꢀꢀꢀꢀꢀꢀꢀꢀꢀꢀꢀꢀꢀꢀꢀꢀꢀꢀ
牺牲氧化层
53.204
ꢀꢀꢀꢀꢀꢀꢀꢀꢀꢀꢀꢀꢀꢀꢀꢀꢀꢀꢀꢀꢀ
覆盖氧化层
54.11
ꢀꢀꢀꢀꢀꢀꢀꢀꢀꢀꢀꢀꢀꢀꢀꢀꢀꢀꢀꢀꢀꢀ
浅沟槽
55.12
ꢀꢀꢀꢀꢀꢀꢀꢀꢀꢀꢀꢀꢀꢀꢀꢀꢀꢀꢀꢀꢀꢀ
有源区
具体实施方式
56.以下通过特定的具体实例说明本发明的实施方式,本领域技术人员可由本说明书所揭露的内容轻易地了解本发明的其他优点与功效。本发明还可以通过另外不同的具体实施方式加以实施或应用,本说明书中的各项细节也可以基于不同观点与应用,在没有背离本发明的精神下进行各种修饰或改变。
57.如在详述本发明实施例时,为便于说明,表示器件结构的剖面图会不依一般比例作局部放大,而且所述示意图只是示例,其在此不应限制本发明保护的范围。此外,在实际制作中应包含长度、宽度及深度的三维空间尺寸。
58.为了方便描述,此处可能使用诸如“之下”、“下方”、“低于”、“下面”、“上方”、“上”等的空间关系词语来描述附图中所示的一个元件或特征与其他元件或特征的关系。将理解到,这些空间关系词语意图包含使用中或操作中的器件的、除了附图中描绘的方向之外的其他方向。此外,当一层被称为在两层“之间”时,它可以是所述两层之间仅有的层,或者也可以存在一个或多个介于其间的层。本文使用的“介于
……
之间”表示包括两端点值。
59.在本技术的上下文中,所描述的第一特征在第二特征“之上”的结构可以包括第一和第二特征形成为直接接触的实施例,也可以包括另外的特征形成在第一和第二特征之间的实施例,这样第一和第二特征可能不是直接接触。
60.需要说明的是,本实施例中所提供的图示仅以示意方式说明本发明的基本构想,遂图示中仅显示与本发明中有关的组件而非按照实际实施时的组件数目、形状及尺寸绘制,其实际实施时各组件的型态、数量及比例可为一种随意的改变,其组件布局型态也可能更为复杂。
61.现有技术中,有源区的顶角难以实现圆角化,且无法对圆角的形状尺寸进行调控,因此,本发明在现有技术的工艺基础上,通过对其进行快速氧化及湿法刻蚀等工艺,以实现顶角的圆角化及尺寸可控。
62.实施例一
63.如图1-图9所示,本实施例提供一种有源区顶角的形成方法,包括如下步骤:
64.s1:提供半导体中间结构,所述半导体中间结构包括依次叠置的衬底101、第一氧化层102、硬掩膜层103、第二氧化层104,所述衬底101中形成有浅沟槽11,所述浅沟槽的底部及侧壁形成有隔离氧化层201,填充氧化层202填满于所述浅沟槽11中;其中,所述浅沟槽11隔离出位于所述衬底101中的有源区12,所述有源区12上的硬掩膜层103的线宽比有源区12小,从而使所述硬掩膜层103的外边缘能够显露下方的部分第一氧化层102;
65.s2:采用湿法刻蚀所述填充氧化层202、第一氧化层101及隔离氧化层201,使所述填充氧化层202的上表面低于所述衬底101的上表面,所述隔离氧化层201高于所述填充氧化层202的部分被去除,同时所述第一氧化层102被所述硬掩膜层103显露的部分也被去除,从而显露所述有源区12的顶角;
66.s3:采用干法方式快速氧化所述有源区12的顶角,形成牺牲氧化层203;
67.s4:采用湿法刻蚀去除所述牺牲氧化层203,使所述有源区12的顶角形成为圆角形;
68.s5:在所述有源区12的圆角形顶角处使用炉管制程生长形成覆盖氧化层204,所述覆盖氧化层204连接所述第一氧化层102及所述隔离氧化层201。
69.s6:于所述浅沟槽11中再次填满所述填充氧化层202。
70.下面将结合附图详细说明本发明中所述半导体结构的制备过程。
71.如图1-图5所示,作为一种实施方式,步骤s1中所述半导体中间结构的形成具体包括如下步骤:
72.s1-1:在衬底101上依次形成第一氧化层102、硬掩膜层103、及第二氧化层104;
73.具体地,如图1所示,所述衬底101的材质可以是硅、锗、绝缘体上硅(soi)、或碳化硅衬底等,也可以是包括其他元素半导体或化合物半导体的衬底,例如砷化镓、磷化铟等,本实施例中优选为硅材料。所述第一氧化层102可利用氧化工艺生长的方式形成,其能够为后续硬掩膜层103提供缓冲,避免直接在衬底101上生长氮化硅等硬掩膜层103时会产生位错的缺点,从而起到保护衬底101的作用,本实施例中,所述第一氧化层102及第二氧化层104优选为氧化硅层,所述硬掩膜层103优选为氮化硅层。在其他实施例中,所述硬掩膜层103也可以是多层结构,例如包括氮化硅层及氮化硼层;
74.接着,参阅图2,进行步骤s1-2:在所述第二氧化层104上形成光刻胶并对其进行图案化,以图形化的光刻胶层为掩膜,蚀刻所述第一氧化层102、硬掩膜层103、第二氧化层104、及衬底101,在所述衬底101中形成浅沟槽11,所述浅沟槽11隔离出有源区12。
75.具体地,通过旋涂工艺在所述第二氧化层104上形成光刻胶,并通过曝光工艺及显影工艺对光刻胶进行处理,实现对所述光刻胶的图案化,图案化的光刻胶层限定出所述浅沟槽11的所在区域,基于图案化的光刻胶层于所述第一氧化层102、硬掩膜层103、第二氧化层104中形成图案化窗口,然后基于图案化窗口进一步刻蚀所述衬底101形成所述浅沟槽11,所述浅沟槽11隔离出有源区12。
76.接着,参阅图3,进行步骤s1-3:采用磷酸回推硬掩膜层103,以使得有源区12上的硬掩膜层103的线宽变得比有源区12小,也就是说有源区12上硬掩膜层103的投影位于所述第一氧化层102内,从而使硬掩膜层103的外边缘能够显露下方的部分第一氧化层102。具体地,可以将整个结构浸入磷酸中,磷酸对所述硬掩膜层103进行刻蚀,从而使得有源区12外边缘的第一氧化层102能够显露出来,从而为后续有源区12顶角的圆角化做出准备。
77.接着,参阅图4-图5,进行步骤s1-4:于所述浅沟槽11的底部及侧壁生长形成隔离氧化层201,然后在所述浅沟槽11中填充形成填充氧化层202。具体地,所述隔离氧化层201优选为氧化硅层,所述填充氧化层202同样为氧化硅,所述填充氧化层202优选采用高密度等离子体法(hdp)沉积获得,hdp能够实现非常好的台阶覆盖,特别适合填充高纵横比间隙,具有较好的填洞效果,其所淀积的绝缘介质膜具有高密度,低杂质缺陷等优点,同时对硅片有优良的粘附能力。所述填充氧化层202的形成同样是为了后续有源区12顶角的圆角化做出准备,在步骤s2中去除部分所述填充氧化层202后保留的部分能够用于限定有源区圆角的尺寸大小,例如,保留的所述填充氧化层202较厚时,显露的顶角区域较小,则最终圆角化处理后的圆角弧长也较短;若保留的所述填充氧化层202较薄时,显露的顶角区域较大,则最终圆角化处理后的圆角弧长也较长。从而通过所述填充氧化层202控制有源区圆角的尺寸大小
78.进一步地,如图6所示,作为一种实施方式,步骤s2中,采用湿法刻蚀所述填充氧化层202、第一氧化层101及隔离氧化层201,使所述填充氧化层202的上表面低于所述衬底101的上表面,同时所述隔离氧化层201高于所述填充氧化层202的部分被去除,所述第一氧化
层102被所述硬掩膜层103显露的部分也被去除,从而显露所述有源区12的顶角。
79.具体地,对所述填充氧化层202进行刻蚀,使其上表面低于所述衬底101的上表面,从而为显露有源区12的顶角区域做出准备。被隔离层202覆盖的隔离氧化层201因得到保护而不会被刻蚀掉,而未被所述隔离层202覆盖的位于所述有源区12顶角处的所述隔离氧化层201则会被刻蚀掉,因此,通过控制所述刻蚀后所述填充氧化层202的厚度能控制最终圆角的尺寸大小。同时所述第一氧化层102被所述硬掩膜层103显露的部分也被去除,从而使得所述有源区顶角部分的衬底材料彻底暴露出来。可选地,对于所述填充氧化层202、第一氧化层101及隔离氧化层201,三者可以基于同一工艺同时进行刻蚀去除。
80.进一步地,如图7所示,作为一种实施方式,步骤s3中,采用干法方式快速氧化所述有源区12的顶角,形成牺牲氧化层203,所述牺牲氧化层203的刻蚀速率大于所述第一氧化层102及所述隔离氧化层201的刻蚀速率;
81.具体地,通过步骤s2将所述有源区顶角部分的衬底材料彻底暴露出来,采用干法方式快速氧化的方法直接将衬底材料氧化形成所述牺牲氧化层203。应当理解的是,所述衬底101的材料为硅,则硅与氧气发生反应后形成的所述牺牲氧化层203为氧化硅。在形成所述牺牲氧化层203的过程中,暴露出的所述有源区顶角棱边处的衬底材料的氧化速度比所述浅沟槽11内壁上的隔离氧化层201的氧化速度快,自然地,所述牺牲氧化层203的厚度自棱边处向两侧逐渐变薄,因此所述牺牲氧化层203的内侧面形成为弧面。从而使后续步骤s4对所述牺牲氧化层203进行去除后,形成圆角形的顶角。步骤s3中,可以选用具有氧化性的反应气体对所述有源区顶角进行氧化形成所述牺牲氧化层203,反应温度为250~500摄氏度,所述反应气体包括高浓度的氧气,制程的反应时间可根据实际需要进行灵活调整,此处不作过多限定。
82.进一步地,如图8所示,作为一种实施方式,步骤s4中,采用湿法刻蚀去除所述牺牲氧化层203,使所述有源区12的顶角形成为圆角形。
83.具体地,由于在步骤s3中使用快速氧化法生成所述牺牲氧化层203,相较采用炉管沉积生长的氧化层,其质地较为疏松且密度较小,因此步骤s4中,采用湿法刻蚀时,能够以较快的速度对其进行去除而不对其他氧化层造成影响。因为步骤s3中形成的所述牺牲氧化层203的内侧面为弧面。在步骤s4中对所述牺牲氧化层203进行去除后,自然地使所述有源区12的顶角形成为圆角形。
84.进一步地,如图9所示,作为一种实施方式,步骤s5中,在所述有源区12的圆角形顶角处使用炉管工艺沉积形成覆盖氧化层204,所述覆盖氧化层204连接所述第一氧化层102及所述隔离氧化层201。
85.具体地,采用炉管工艺生成所述覆盖氧化层204,其薄膜成分和厚度易控,保证其具有稳定的化学性和电绝缘性,同时均匀性与重复性好,台阶覆盖能力好,操作方便,可通过沉积时间控制氧化层厚度。优选地,所述覆盖氧化层204的厚度和第一氧化层102及所述隔离氧化层201的厚度相同。通过上述有源区圆角化的步骤后,形成的所述覆盖氧化层204也为圆弧状,从而也避免了现有技术中有源区顶角处氧化层厚度不均的问题。
86.进一步地,如图10所示,作为一种实施方式,步骤s6中,于所述浅沟槽11中填满所述填充氧化层202。具体地,在形成所述覆盖氧化层204后,在所述浅沟槽11中重新填满所述填充氧化层202,从而用以后续制程。类似的,所述填充氧化层202同样优选采用高密度等离
子体法(hdp)沉积获得,从而实现较好的台阶覆盖以及填洞效果。此外,该步骤还可以包括退火的过程,以释放应力,并使填充氧化层致密化。
87.本实施例提供一种有源区顶角的形成方法,该方法先对浅沟槽中的填充氧化层进行刻蚀,使其上表面低于所述衬底的上表面,从而为显露有源区的顶角区域做出准备,通过控制刻蚀后填充氧化层的厚度以来控制最终有源区顶角处形成的圆角尺寸大小;同时,对第一氧化层及隔离氧化层进行刻蚀,使所述有源区顶角部分的衬底材料彻底暴露出来。然后采用干法方式快速氧化所述有源区的顶角,形成牺牲氧化层,由于氧化速度的不同使得所述牺牲氧化层的内侧面形成为弧面,后续在去除牺牲氧化层进行去除后,自然地使有源区的顶角形成为圆角形。同时由于牺牲氧化层的质地较为疏松且密度较小,因此采用湿法刻蚀时,能够以较快的速度对其进行去除而不对其他氧化层造成影响。最后再使用炉管工艺在有源区的圆角形顶角处沉积形成圆弧状的覆盖氧化层。通过上述步骤能够有效地将有源区顶角圆角化,同时圆角的形状尺寸还能够实现稳定可控。
88.实施例二
89.本实施例提供一种半导体结构,该半导体结构可以通过上述实施例一中的形成方法制作,但不限于上述形成方法,如图8所示,所述半导体结构具体包括:
90.衬底101,所述衬底中形成有浅沟槽11,所述浅沟槽11隔离出位于所述衬底101中的有源区12,所述浅沟槽11的底部及侧壁形成有隔离氧化层201,填充氧化层202填充于所述浅沟槽11内,所述隔离氧化层201的顶面与所述填充氧化层202的顶面齐平,且低于所述衬底101的上表面;
91.位于所述衬底上的第一氧化层102,位于所述有源区12上的第一氧化层102上的线宽比有源区12小,从而使所述有源区12的顶角显露出来,所述有源区12的顶角为圆角形。
92.进一步地,所述第一氧化层102上依次叠置有硬掩膜层103及第二氧化层10,位于所述有源区12上的硬掩膜层103及第二氧化层10的线宽与所述第一氧化层102相同。
93.具体地,所述衬底101的材质可以是硅、锗、绝缘体上硅(soi)、或碳化硅衬底等,也可以是包括其他元素半导体或化合物半导体的衬底,例如砷化镓、磷化铟等,本实施例中优选为硅材料。所述第一氧化层102可利用氧化工艺生长的方式形成,其能够为后续硬掩膜层103提供缓冲,避免直接在衬底101上生长氮化硅等硬掩膜层103时会产生位错的缺点,从而起到保护衬底101的作用,本实施例中,所述第一氧化层102及第二氧化层104优选为氧化硅层,所述硬掩膜层103优选为氮化硅层。在其他实施例中,所述硬掩膜层103也可以是多层结构,例如包括氮化硅层及氮化硼层;
94.具体地,所述浅沟槽11可以通过刻蚀形成,具体工艺过程为:通过旋涂工艺在所述第二氧化层104上形成光刻胶,并通过曝光工艺及显影工艺对光刻胶进行处理,实现对所述光刻胶的图案化,图案化的光刻胶层限定出所述浅沟槽11的所在区域,基于图案化的光刻胶层于所述第一氧化层102、硬掩膜层103、第二氧化层104中形成图案化窗口,然后基于图案化窗口进一步刻蚀所述衬底101形成所述浅沟槽11,所述浅沟槽11隔离出有源区12。
95.具体地,可采用磷酸回推硬掩膜层103,以使得有源区12上的硬掩膜层103的线宽变得比有源区12小,进而再对所述第一氧化层进行刻蚀,从而使得对于所述有源区12上的所述第一氧化层102、硬掩膜层103、第二氧化层104的线宽小于有源区12的线宽。
96.具体地,所述隔离氧化层201优选为氧化硅层,所述填充氧化层202同样为氧化硅,
所述填充氧化层202优选采用高密度等离子体法(hdp)沉积获得,hdp能够实现非常好的台阶覆盖,特别适合填充高纵横比间隙,具有较好的填洞效果,其所淀积的绝缘介质膜具有高密度,低杂质缺陷等优点,同时对硅片有优良的粘附能力。所述有源区顶角圆角化的过程可通过上述步骤s1-s4形成,所述填充氧化层202的厚度用于限定有源区圆角的尺寸大小,例如,保留的所述填充氧化层202较厚时,显露的顶角区域较小,则最终圆角化处理后的圆角弧长也较短;若保留的所述填充氧化层202较薄时,显露的顶角区域较大,则最终圆角化处理后的圆角弧长也较长。从而通过所述填充氧化层202控制有源区圆角的尺寸大小。
97.进一步地,所述有源区12的圆角形顶角处使用炉管制程生长形成覆盖氧化层204,所述覆盖氧化层204连接所述第一氧化层102及所述隔离氧化层201。
98.具体地,采用炉管工艺生成所述覆盖氧化层204,其薄膜成分和厚度易控,保证其具有稳定的化学性和电绝缘性,同时均匀性与重复性好,台阶覆盖能力好,操作方便,可通过沉积时间控制氧化层厚度。优选地,所述覆盖氧化层204的厚度和第一氧化层102及所述隔离氧化层201的厚度相同。通过上述有源区圆角化的步骤后,形成的所述覆盖氧化层204也为圆弧状,从而也避免了现有技术中有源区顶角处氧化层厚度不均的问题。
99.综上所述,本发明提供一种有源区顶角的形成方法及半导体结构,该方法先对浅沟槽中的填充氧化层进行刻蚀,使其上表面低于衬底的上表面,从而为显露有源区的顶角区域做出准备,通过控制刻蚀后填充氧化层的厚度以来控制最终有源区顶角处形成的圆角尺寸大小;同时,对第一氧化层及隔离氧化层进行刻蚀,使有源区顶角部分的衬底材料彻底暴露出来。然后采用干法方式快速氧化有源区的顶角,形成牺牲氧化层,由于氧化速度的不同使得牺牲氧化层的内侧面形成为弧面,后续在去除牺牲氧化层进行去除后,自然地使有源区的顶角形成为圆角形。同时由于牺牲氧化层的质地较为疏松且密度较小,因此采用湿法刻蚀时,能够以较快的速度对其进行去除而不对其他氧化层造成影响。最后再使用炉管工艺在有源区的圆角形顶角处沉积形成圆弧状的覆盖氧化层。通过上述步骤能够有效地将有源区顶角圆角化,同时圆角的形状尺寸还能够实现稳定可控。
100.上述实施例仅例示性说明本发明的原理及其功效,而非用于限制本发明。任何熟悉此技术的人士皆可在不违背本发明的精神及范畴下,对上述实施例进行修饰或改变。因此,举凡所属技术领域中具有通常知识者在未脱离本发明所揭示的精神与技术思想下所完成的一切等效修饰或改变,仍应由本发明的权利要求所涵盖。
再多了解一些
本文用于创业者技术爱好者查询,仅供学习研究,如用于商业用途,请联系技术所有人。