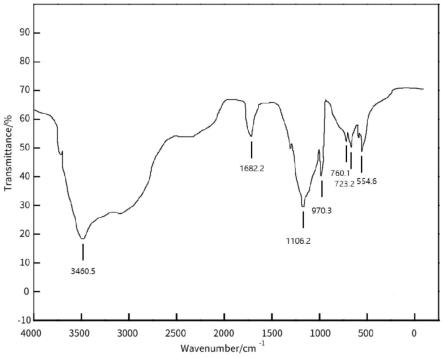
1.本发明涉及铜冶炼炉渣资源综合利用技术领域,更具体的是涉及利用铜冶炼炉渣制备聚硅酸硫酸铁铝絮凝剂技术领域。
背景技术:
2.铜位于元素周期表第四周期ib族,是人类最早使用的金属。铜具有优异的性能,易于加工和广泛的用途,被广泛应用于电气、轻工、机械制造、建筑工业、国防工业等领域,在我国有色金属材料的消费中仅次于铝。
3.火法炼铜是当今产铜的主要方法,铜矿石经过采矿、选矿得到含铜品位较高的铜精矿,然后送冶炼厂炼铜。火法炼铜工艺流程一般有造锍熔炼得到冰铜;转炉吹炼得到粗铜;火法精炼得到阳极铜;电解精炼得到阴极铜。火法炼铜每天会产生大量的炉渣,每生产一吨铜大概要产生将近两吨炉渣,其中大量的铁硅元素没有得到有效的利用。选矿浮选是目前主要的铜冶炼炉渣处理方法,得到渣精矿和尾渣,前者回炉进行有价金属回收,后者进行其他处理。
4.申请号cn201510042614.0公开了一种适用于同时选别铜冶炼电炉渣与转炉渣的工艺方法,它包括以下步骤:若原矿为电炉渣,则进入两段连续磨矿~浮选流程,若原矿为转炉渣,则进入两段磨矿~两段浮选流程;该发明的有益效果是分别研究并提出了电炉渣、转炉渣选别最佳的工艺流程;在转炉渣选别中采用“水玻璃、碳酸氢钠 硫化钠”组合用药取得了尾矿含铜0.188的选别指标。该发明可以根据矿石类型,调节连接,满足电炉渣两段连续磨矿~浮选流程和转炉渣两段磨矿~两段浮选流程,获得铜精矿铜回收率小于80%。
5.上述专利存在的问题是选矿浮选回收有价金属的工艺复杂,难度高,成本也高。
技术实现要素:
6.本发明的目的在于:为了解决上述现有选矿浮选回收有价金属的难度高,成本也高技术问题,本发明提供利用铜冶炼炉渣制备聚硅酸硫酸铁铝絮凝剂的方法。
7.本发明为了实现上述目的具体采用以下技术方案:利用铜冶炼炉渣制备聚硅酸硫酸铁铝絮凝剂的方法,包括如下步骤:
8.步骤1、将炉渣加入硫酸溶液中,在50~70℃下搅拌冲洗,直至溶解完成,得到混浊原液;
9.步骤2、将混浊原液在50~70℃下,静置2~4小时进行沉淀,后转移沉淀后的上清液a;
10.步骤3、在上述上清液a中加入双氧水,搅拌活化后得上清液b,向上清液b中加入氢氧化铝,反应结束后用硫酸调节ph至3以下;
11.步骤4、用硫酸调节ph至3以下后陈化,再水洗过滤得聚硅酸硫酸铁铝絮凝剂半成品,烘干后得聚硅酸硫酸铁铝絮凝剂成品。
12.本技术的技术方案中,利用炉渣含有高铁高二氧化硅的特点,炉渣含铁25~45%,
含二氧化硅20~40%,同时利用铜冶炼烟气中的二氧化硫回收生产的硫酸即自产硫酸进行酸洗酸浸溶解活化,然后进行沉淀,沉淀后的清液加入双氧水和氢氧化铝进行搅拌,反应完全后静置陈化足够时间,即可得到聚硅酸硫酸铁铝絮凝剂。下沉沉淀经过低温烘干/风干后,可送去选矿浮选,作为生产渣精矿的原料,进行有价金属的回收。既利用了炉渣,同时铜冶炼系统自身生产硫酸,可用于炉渣的酸洗酸浸溶解,自产自销,充分利用系统自身产物,生产成本具有很大优势,综合利用炉渣进行聚硅酸硫酸铁铝絮凝剂的生产,生产有价值的新产品,生产过程简单且全为湿法,没有烟气和废液废渣,所有产物闭路没有额外产出,同时减少炉渣的总量,减少了在物料倒运过程中的能源浪费,及物料洒落对周围环境的污染和影响,且降低了下游(回收有价金属)选矿浮选的处理难度和处理量。
13.进一步的,步骤1中将1~1.5t炉渣加入1.8~2.5t的30%硫酸溶液。
14.进一步的,步骤3中,每吨上清液a中加入500~600kg双氧水(双氧水可过量1.2~1.5倍,反应速度更快)。
15.进一步的,步骤3中搅拌活化的时间为1~2小时。
16.进一步的,每吨上清液b中加入200~300kg氢氧化铝(以达到铝离子浓度120~200mg/l为佳)。
17.进一步的,步骤4中陈化的时间为8~10小时,烘干的温度为90~110℃。
18.进一步的,硫酸溶液获取方法如下:将冶炼原料铜精矿(含20%~30%的硫)经冶炼炉反应燃烧后(大部分硫在1100℃以上与工业风中的氧反应生成二氧化硫),烟气(烟气夹杂着大量的烟尘,是不能随意排放的,否则会严重污染环境)经过余热锅炉和电收尘除尘降温后,进入制酸系统,经制酸系统净化、干吸、转化后制成硫酸溶液。
19.进一步的,步骤2中的沉淀在95~105℃下搅拌烘干后(送去选矿浮选)作为生产渣精矿的原料,回收有价金属(有价金属包括铜、金和银)。
20.本发明的有益效果如下:
21.1、资源综合利用:利用炉渣中高浓度的铁和二氧化硅,炉渣含铁25~45%,含二氧化硅20~40%,铜冶炼系统每生产一吨铜,约产生2~3吨炉渣,以一个20万吨产能的铜冶炼系统为例,年产生炉渣50万吨左右;同时利用了铜冶炼烟气中的二氧化硫回收生产的硫酸,以一个20万吨产能的铜冶炼系统为例,年产生硫酸75万吨(折合100%硫酸)左右,原料非常充足;
22.2、降低了生产成本:既利用了炉渣,同时铜冶炼系统自身生产硫酸,可用于炉渣的酸洗酸浸溶解,自产自销,充分利用系统自身产物,生产成本具有很大优势;
23.3、减少了炉渣总量:综合利用炉渣进行聚硅酸硫酸铁铝絮凝剂的生产,估算可以减少炉渣总量1/4~1/3左右,减少了环境污染。且降低了下游选矿浮选的处理难度和处理量;
24.4、环保效益:生产过程简单且全为湿法,没有烟气和废液废渣,所有产物闭路没有额外产出。同时减少炉渣的总量,减少了在物料倒运过程中的能源浪费,及物料洒落对周围环境的污染和影响,具有一定的社会和环保效益;
25.5、经济效益:产出的聚硅酸硫酸铁铝是一种高效的净水絮凝剂,既具有不低的经济价值,同时对资源综合利用的意义也很大。
附图说明
26.图1是本发明利用铜冶炼炉渣制备聚硅酸硫酸铁铝絮凝剂的方法的流程图;
27.图2是实施例2生产的聚硅酸硫酸铁铝絮凝剂样品图;
28.图3是实施例2生产的聚硅酸硫酸铁铝絮凝剂xrd衍射谱图;
29.图4是实施例2生产的聚硅酸硫酸铁铝絮凝剂傅里叶红外光谱图。
具体实施方式
30.为使本发明实施例的目的、技术方案和优点更加清楚,下面将结合本发明实施例对本发明实施例中的技术方案进行清楚、完整地描述,显然,所描述的实施例是本发明一部分实施例,而不是全部的实施例。
31.因此,基于本发明中的实施例,本领域普通技术人员在没有作出创造性劳动前提下所获得的所有其他实施例,都属于本发明保护的范围。
32.实施例1
33.如图1所示,本实施例提供利用铜冶炼炉渣制备聚硅酸硫酸铁铝絮凝剂的方法,包括如下步骤:
34.制备硫酸溶液:由于冶炼原料铜精矿中含有约20%~30%的硫,经过冶炼炉反应燃烧后,大部分硫在1100℃以上与工业风中的氧反应生成二氧化硫,烟气夹杂着大量的烟尘,是不能随意排放的,否则会严重污染环境。经过余热锅炉和电收尘除尘降温后,进入制酸系统用于生产硫酸。经过制酸系统净化、干吸、转化三个主要工序,制成纯度很高的浓硫酸,稀释到30%左右用于聚硅酸硫酸铁铝絮凝剂的制备。
35.步骤1、将1t炉渣加入1.8t的30%硫酸溶液中,在50℃下搅拌冲洗,直至溶解完成,得到混浊原液;
36.步骤2、将混浊原液在50℃下,静置2小时进行沉淀,后转移沉淀后的上清液a;沉淀在95℃下搅拌烘干后(送去选矿浮选)作为生产渣精矿的原料,回收有价金属(有价金属包括铜、金和银);
37.步骤3、在上述上清液a中加入双氧水,每吨上清液a中加入500kg双氧水,搅拌活化1小时后得上清液b,向上清液b中加入氢氧化铝,每吨上清液b中加入200kg氢氧化铝,反应结束后用硫酸调节ph至3以下;
38.步骤4、用硫酸调节ph至3以下后陈化8小时,再水洗过滤得聚硅酸硫酸铁铝絮凝剂半成品,烘干后得聚硅酸硫酸铁铝絮凝剂成品,烘干的温度为90℃。
39.实施例2
40.如图1-4所示,步骤1、将1.2t炉渣加入2.2t的30%硫酸溶液中,在60℃下搅拌冲洗,直至溶解完成,得到混浊原液;
41.步骤2、将混浊原液在60℃下,静置3小时进行沉淀,后转移沉淀后的上清液a;沉淀在100℃下搅拌烘干后(送去选矿浮选)作为生产渣精矿的原料,回收有价金属(有价金属包括铜、金和银);
42.步骤3、在上述上清液a中加入双氧水,每吨上清液a中加入550kg双氧水,搅拌活化1.5小时后得上清液b,向上清液b中加入氢氧化铝,每吨上清液b中加入250kg氢氧化铝,反应结束后用硫酸调节ph至3以下;
43.步骤4、用硫酸调节ph至3以下后陈化9小时,再水洗过滤得聚硅酸硫酸铁铝絮凝剂半成品,烘干后得聚硅酸硫酸铁铝絮凝剂成品,烘干的温度为100℃。其中硫酸的制备如实施例1所述。
44.本实施例制备的聚硅酸硫酸铁铝絮凝剂成品经过xrd衍射仪分析,得到特征谱图如图3,可以观察到衍射峰主要为硫酸铁,但强度不高,说明发生了部分聚合;没有观察到硫酸铝的峰,说明这部分聚合较完全。
45.本实施例制备的聚硅酸硫酸铁铝絮凝剂成品经过傅里叶红外光谱仪分析,得到光谱图如图4,可以观察到3400~3500cm-1
范围的宽吸收峰为si-oh的伸缩振动吸收峰,1600~1700cm-1
范围的吸收峰为样品中未完全烘干的h2o,1000~1150cm-1
附近的吸收峰为si-o-si的伸缩振动吸收峰,500~650cm-1
附近的吸收峰为o-si-o的吸收峰,由于硫酸参与活化过程,900~1000cm-1
附近的峰为硫酸根的吸收峰,与大吸收峰部分交叠导致不太明显,而700~800cm-1
附近的比较接近的两个峰为fe-o-si和al-o-si的振动峰。可以判断样品是以聚合硅酸为基础,结合了铁、铝的高分子聚合物,所得产物为聚硅酸硫酸铁铝。
46.实施例3
47.如图1所示,步骤1、将1.5t炉渣加入2.5t的30%硫酸溶液中,在70℃下搅拌冲洗,直至溶解完成,得到混浊原液;
48.步骤2、将混浊原液在70℃下,静置4小时进行沉淀,后转移沉淀后的上清液a;沉淀在105℃下搅拌烘干后(送去选矿浮选)作为生产渣精矿的原料,回收有价金属(有价金属包括铜、金和银);
49.步骤3、在上述上清液a中加入双氧水,每吨上清液a中加入600kg双氧水,搅拌活化2小时后得上清液b,向上清液b中加入氢氧化铝,每吨上清液b中加入300kg氢氧化铝,反应结束后用硫酸调节ph至3以下;
50.步骤4、用硫酸调节ph至3以下后陈化10小时,再水洗过滤得聚硅酸硫酸铁铝絮凝剂半成品,烘干后得聚硅酸硫酸铁铝絮凝剂成品,烘干的温度为110℃。其中硫酸的制备如实施例1所述。
51.实施例4
52.应用实例:
53.步骤1、取铜冶炼闪速炉炉渣200g,炉渣成分:(铜1.15%,铁35.04%,硫1.04%,硅27.69%,氧14.80%,铝7.67%,钙4.15%,铅1.326%,锌0.783%,砷0.174%)。用铜冶炼硫酸系统自产98%酸(硫酸含量98.85,灰分0.012,铅0.000020%,铁0.00048,砷0.00061,透明度170mm,色度不深于标准色度,下同),稀释至30%浓度,取360g(约295ml)。在70℃水浴锅中冲洗搅拌,直至反应溶解完全,得到混浊原液;
54.步骤2、保持水浴锅恒温70℃,静置4小时进行沉淀,使用布氏漏斗加中速滤纸进行抽滤,得到澄清液a,称重395g,约280ml;过滤后的沉淀放入105℃
±
5℃烘箱烘干2小时得到沉淀,称重146g;
55.步骤3、在澄清液a中,加入240g双氧水(30%),用自动搅拌器搅拌,活化1.5h,再加入氢氧化铝(ar分析纯)160g,继续搅拌至反应结束后,用30%硫酸调节ph至2.9,得到混浊液体积约890ml;
56.步骤4、混浊液陈化8.5h,用布氏漏斗加中速滤纸进行抽滤,边过滤边用约10ml水
洗涤,过滤得到的沉淀放入烘箱,105℃
±
5℃烘干2h,称重得到92g浅黄色粉状固体,即为聚硅酸硫酸铁铝絮凝剂成品。
57.步骤5、取露天应急水池精矿粉尘冲洗废水(含不溶精矿粉尘28.32g)500ml于1000ml烧杯中,取步骤4中制得的聚硅酸硫酸铁铝10g加入烧杯并轻轻搅匀后放置约25分钟;
58.步骤6、溶液上部澄清,下半部有铜精矿粉深色絮状物,检测不溶铜精矿矿粉去除率98.03%。
再多了解一些
本文用于企业家、创业者技术爱好者查询,结果仅供参考。