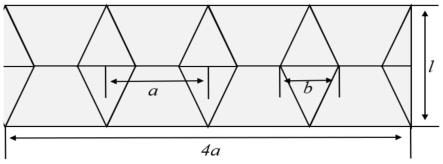
1.本发明涉及一种吸能结构智能识别优化方法,属于煤矿开采技术领域。
背景技术:
2.冲击地压又称岩爆,是指井巷或工作面周围岩体,由于弹性变形能的瞬时释放而产生突然剧烈破坏的动力现象,常伴有煤岩体抛出、巨响及气浪等现象。它具有很大的破坏性,冲击地压一直是煤矿面临的主要灾害之一。随开采深度不断增大,地层条件复杂,煤岩体中聚积的弹性能增加,冲击地压发生的可能性也随之增加,并引起严重事故。
3.金属薄壁结构能够将碰撞过程中的冲击动能转化为结构的塑性变形能,提高结构的耐冲撞性。能够在突发的碰撞事件中,依靠自身或附加装置的屈曲、断裂等破坏形式来减缓碰撞时的冲击荷载,耗散冲击能量。防冲吸能构件作为面对冲击地压时保护液压缸能够正常工作的核心构件,其支护效果是评判吸能防冲液压支架的重要标准之一。然而现有吸能防冲液压支架存在水平支护能力不足的问题,影响了吸能防冲液压支架在面对竖向冲击与水平冲击时的防冲性能,因此还需要对此做进一步的研究。
技术实现要素:
4.针对现有技术的不足,本发明的目的是提供一种吸能结构智能识别优化方法。
5.为了实现上述目的,本发明所采用的技术方案是:
6.一种吸能结构智能识别优化方法,包括以下步骤:
7.(1)防冲吸能构件设计:
8.防冲吸能构件是具有多边形截面的薄壁构件;
9.(2)构建有限元模型:
10.采用有限元软件abaqus对构件建立有限元模型;采用dynamic-explicit算法,在构件底部与顶部分别设置刚性板,顶部为可移动刚性板,底部为固定刚性板,构件与刚性板接触关系为通用接触;沿壳单元厚度方向取积分点,网格为四边形;数值模拟得到构件的承载力-位移曲线;
11.(3)构件等效塑性应变研究:
12.为进一步分析构件在形变过程中的塑性变形区,根据构件对称性,在构件梯形区域与三角区域均匀选取若干个分析区域;分析梯形与三角形截面各区域等效塑性应变与构件承载力-位移曲线图,得到二者加肋区;
13.(4)基于鱼群优化算法的优化流程:
14.优化流程分为三部分:第一部分修改py命令流、第二部分运行py命令流、第三部分结果处理;
15.1)第一部分:首先通过人工鱼群优化算法在设定范围内输出肋宽x、肋高y,其中设置的鱼群数为2,每次迭代会输出两组数据;通过matlab将输出的两组数据尺寸转化为绘制构件肋模型的节点坐标,并将节点坐标替换到py命令流的相应位置以此来修改肋尺寸;
16.2)第二部分:通过matlab程序调运abaqus来运行上述py命令流,得到加肋模型;
17.3)第三部分:通过matlab程序提取结果odb文件中步骤(2)数值模拟得到的承载力-位移曲线,取弹性阶段时的承载力最大值作为理想状态下承载力-位移曲线的恒阻值,来作为目标函数;将承载力-位移曲线恒阻值的后续数值与目标函数作差,设置差值与目标函数的允许误差为15%;
18.若满足则输出结果,不满足则选择两次计算结果中更靠近目标函数的一组计算结果,在该计算结果附近重新输出两组数据,代回第一部分重新计算。
19.(5)数值模拟模型:通过步骤(4)的优化流程不断迭代,输出最终计算得到的肋宽x、肋高y;构件与肋边缘通过命令tie绑定,以此模拟实际中的焊接。
20.步骤(1)所述多边形截面的薄壁构件的四个尖端处均分布一个钻石型凹角,从而形成预制折纹纹路;所述薄壁构件的多边形截面由完全相同的8个梯形与8个三角形组成,以中轴线对称排列组成;
21.在面对冲击时防冲吸能构件按照预先设定折纹进行塑性变形,从而在变形过程中为支架提供恒定的承载力。
22.在步骤(2)所述承载力-位移曲线上设置四个标志点,分别表示:弹性变形结束、衰减段开始、衰减段结束与承载力最低点。
23.步骤(4)所述人工鱼群优化算法的具体步骤如下:
24.①
初始化设置,包括种群规模n、每条人工鱼的初始位置、人工鱼的视野visual、步长step、拥挤度因子δ、重复次数trynumber;
25.②
计算初始鱼群中各个个体的适应度,取最优人工鱼状态及其目标函数值赋予公告牌;
26.③
根据参数的设置对鱼群中各个体执行相应的行为,生成新的鱼群;
27.④
评价新鱼群中所有个体,若某个体优于公告牌,则更改公告牌上的最优值;
28.⑤
当公告牌上的最优解达到算法的终止条件或达到迭代次数上限时,结束算法,否则转步骤
③
。
29.本发明有益效果:
30.本发明提供一种吸能结构智能识别优化方法,基于现在应用较为广泛的方形预折纹吸能构件进行数值模拟计算分析,采用abaqus、matlab、python多软件与鱼群优化算法协调计算对支架进行结构优化,得到吸能构件的加肋区,并与吸能装置结合,使吸能防冲液压支架在面对竖向冲击与水平冲击时的防冲性能提高。
31.实验结果表明,构件优化后压溃峰值承载力为3.199
×
103kn,相比优化前增长了14.8%;优化后构件平均压溃承载力为2.831
×
103kn,相比优化前增长了50.5%;优化后构件荷载波动系数为1.13,相比优化前降低了-24.6%;优化后构件总吸能为374.5
×
103j,相比优化前增加了54.3%;优化后构件比吸能为45.7
×
103j
·
kg-1,相比优化前增加了32.1%。
附图说明
32.图1构件展开平面图。
33.图2构件模型图。
34.图3构件数值模型图。
35.图4构件承载力-位移曲线图。
36.图5人工鱼群算法的基本寻优原理。
37.图6构件分析区域划分。
38.图7区域51-60等效塑性应变与承载力-位移曲线图。
39.图8截面加肋区。
40.图9人工鱼群优化算法中的迭代数据。
41.图10py命令流的修改。
42.图11运行py命令流后的加肋模型。
43.图12优化方法流程图。
44.图13优化后的构件加肋模型。
45.图14优化前(下)与优化后(上)构件形变过程图。
46.图15优化前与优化后承载力-位移曲线图。
具体实施方式
47.以下结合实施例对本发明的具体实施方式作进一步详细说明。实施例中所涉及的试验方法如无特别说明均为常规方法。
48.实施例
49.一种吸能结构智能识别优化方法,包括以下步骤:
50.(1)防冲吸能构件设计:防冲吸能构件是多边形截面的薄壁构件(以下简称构件),在其四个尖端处均分布一个钻石型凹角,来形成预制折纹纹路,以此在面对冲击时对构件屈曲变形进行诱导,当构件在变形过程中能够提供稳定承载力。构件是由完全相同的8个梯形与8个三角形组成,以中轴线对称排列组成。模型平面展开图如图1所示,构件如图2所示。构件宽a=180mm,高度l=168mm,凹角宽度b=100mm。在面对冲击时构件可以按照预先设定折纹进行塑性变形,从而在变形过程中为支架提供恒定的承载力。
51.(2)构建有限元模型:采用有限元软件abaqus对构件建立有限元模型,构件模型密度为7.85
×
103kg/m3、弹性模量为203gpa、泊松比为0.3、屈服强度为785mpa。采用dynamic-explicit算法,在构件底部与顶部分别设置刚性板,顶部为可移动刚性板,底部为固定刚性板,其质量为500kg,顶部刚性板冲击速度为8m/s,冲击距离为100mm,构件与刚性板接触关系为通用接触,摩擦系数为0.3。沿壳单元厚度方向取11个积分点,网格为四边形,如图3所示。
52.吸能构件计算结果:图4中深色曲线是数值模拟得到的构件承载力-位移曲线,浅色曲线是构件承载力-位移理想曲线。理想状态下吸能构件承载力-位移曲线,在模型弹性变形结束时承载力达到第一峰值点,并且在后续构件发生塑性变形时,承载力-位移曲线将不会发生波动。
53.为方便后续研究,在曲线上设置四个标志点,分别表示:弹性变形结束、衰减段开始、衰减段结束、与承载力最低点。
54.(3)基于鱼群优化算法的优化流程:在一片水域中,鱼往往能自行或尾随其它鱼,找到营养物质多的地方,因而鱼生存数目最多的地方一般就是本水域中营养物质最多的地
方。人工鱼群算法根据这一特点,通过构造人工鱼来模仿鱼群的觅食、聚群、追尾及随机行为,从而实现寻优。
55.1)觅食行为
56.觅食行为是鱼趋向食物的一种活动。人工鱼在其当前范围内选择另一种状态,如果得到新状态下目标函数的值小于当前状态下目标函数的值,则向新状态靠近一步,否则重新选取新状态。当选择次数达到一定数量后仍不满足条件,则随机移动。
[0057][0058]
式中:和分别为人工鱼第t次和第t 1次的尝试状态;xj为人工鱼的另一个状态;step为人工鱼的步长;rand为介于0与1之间的随机数。
[0059]
2)聚群行为
[0060]
聚群行为是鱼在进化过程中形成的一种生存方式,即大量或少量的鱼聚集成群,进行集体觅食和躲避敌害。人工鱼搜索当前邻域内的伙伴数量,并计算伙伴的中心位置,若其目标函数优于当前位置的目前函数且不拥挤,则该人工鱼向中心位置移动,否则执行觅食行为。
[0061][0062]
式中:xc为人工鱼的中心位置。
[0063]
3)追尾行为
[0064]
追尾行为是当某一条或几条鱼发现食物时,周围的伙伴会尾随至食物点。人工鱼通过感知邻域内鱼群的最优位置,当其目标函数值小于当前位目标函数值且不拥挤时,则该人工鱼向最优位置移动,基本公式同式(2),否则执行觅食行为。
[0065]
4)随机行为
[0066]
随机行为是觅食行为的一个缺省行为,指人工鱼在视野内随机移动。
[0067][0068]
式中:visual为人工鱼的视野。
[0069]
5)寻优过程
[0070]
人工鱼群算法的寻优原理如图5所示,具体步骤如下:
①
初始化设置,包括种群规模n、每条人工鱼的初始位置、人工鱼的视野visual、步长step、拥挤度因子δ、重复次数trynumber;
②
计算初始鱼群中各个个体的适应度,取最优人工鱼状态及其目标函数值赋予公告牌;
③
根据参数的设置对鱼群中各个体执行相应的行为,生成新的鱼群;
④
评价新鱼群中所有个体,若某个体优于公告牌,则更改公告牌上的最优值;
⑤
当公告牌上的最优解达到算法的终止条件或达到迭代次数上限时,结束算法,否则转步骤
③
。
[0071]
(4)构件等效塑性应变研究:由于构件通过等效塑性变形来吸收支架受到的冲击能量并提供支撑力,因此以构件等效塑性变形区作为主要研究内容。为进一步分析构件在形变过程中的塑性变形区,根据构件对称性,在构件梯形区域与三角区域均匀选取了110个分析区域,具体分区位置如图6所示。
[0072]
梯形区域坐标分区编号由左到右、由上到下编号依次递增共分82个分析区域;三角形区域坐标分区编号由上小下、由左到右编号依次增加共28个分析区域。
[0073]
通过分析区域0-110的等效塑性应变来确定构件的加肋区,图7为区域51-60的等效塑性应变与承载力-位移曲线图。
[0074]
确定加肋区:通过分析区域1-110在四个时刻的塑性应变曲线发现,时刻1弹性变形阶段结束区域63、64、71-82等效塑性应变出现小幅度增长,等效塑性应变均保持在0.05以下;时刻2衰减段开始区域53、54、61-65、70-82等效塑性应变发生突增,等效塑性应变范围保持在0.1-0.4之间;时刻3衰减段结束区域1、14、15、28、53、62、63、64、71、72、73-82等效塑性应变整体保持稳定变形,个别区域发生增长,等效塑性应变范围保持在0.1-0.5之间;时刻4承载力最低点区域1-3、13-16、27-30、39-44、46-53、62-64、71-82等效塑性变形存在较大形变,等效塑性应变整体保持在0.2-0.4之间。
[0075]
根据上述结果时刻1为弹性变形结束时刻,梯形截面整体等效塑性应变均保持在较低范围,表明应变可以很好的反应构件的形变情况。由时刻1到时刻2应变较大区域主要集中在梯形区域底部(构件中部),并且有沿两腰预折纹向顶部延伸趋势;时刻2到时刻3应变突增区域同样集中在梯形区域底部(构件中部),并沿两腰预导线向顶部延伸,同时顶部两端出现较大应变并有想下延伸趋势;时刻3到时刻4应变较大区域主要集中在梯形下底与两腰预导线附近,同时梯形中部纵向出现条状应变域。
[0076]
根据上述方法,分析梯形与三角形截面各区域等效塑性应变与构件承载力-位移曲线图,得到二者加肋区,如图8所示。
[0077]
(5)优化流程:优化流程主要分为三部分,第一部分修改py命令流、第二部分运行py命令流、第三部分结果处理。
[0078]
1)第一部分首先通过人工鱼群优化算法在范围0-24mm与0-15mm内输出肋宽x、肋高y,由于设置的鱼群数为2,所以每次迭代会输出两组数据计算两次,如图9所示。通过matlab将尺寸转化为绘制构件肋模型的十个节点坐标,并将坐标替换到py命令流的相应位置以此来修改肋尺寸,如图10所示。
[0079]
2)第二部分通过matlab程序调运abaqus来运行上述py命令流,得到加肋模型,如图11所示。
[0080]
3)通过matlab程序提取结果odb文件中的承载力-位移曲线,取弹性阶段时的承载力最大值作为理想状态下承载力-位移曲线的恒阻值来作为目标函数。将后续计算值与目标函数作差,设置其值与目标函数的允许误差为15%,若满足则输出结果,不满足则在两次计算结果中更靠近目标函数附近重新输出两组数据,代回第一部分重新计算。整体流程如图12所示。
[0081]
数值模拟模型:通过上述优化流程不断迭代,最终计算得到最优x=70mm,y=95mm。构件加肋后模型如图13所示,构件与肋边缘通过命令tie绑定,以此模拟实际中的焊接。
[0082]
(6)优化后计算结果:图14为构件优化前后形变过程图(上为优化后,下为优化前),从图中可以看出优化后构件在前期形变过程并无明显变化,均是构件中部首先发生形变。后续形变优化前构件则是上端发生形变随后下端发生形变直至压缩结束,而优化后构件则是上、下两端在最后时刻才发生形变。
[0083]
图15为优化前与优化后承载力-位移曲线图,根据图中曲线可以看出,优化后构件压溃峰值荷载f
max
相比较优化前压溃峰值荷载f
max
发生了轻微增长;力-位移曲线在弹性段
形变结束后的衰减程度得到了十分明显的降低;但优化后构件承载力出现了第二个波峰,且峰值荷载要大于初始峰值荷载;优化后承载力-位移曲线波动性相比优化前得到了降低。
[0084]
如表1所示,构件优化后压溃峰值承载力fmax为3.199
×
103kn,相比优化前增长了14.8%;优化后构件平均压溃承载力fmean为2.831
×
103kn,相比优化前增长了50.5%;优化后构件荷载波动系数δ为1.13,相比优化前降低了-24.6%;优化后构件总吸能e为374.5
×
103j,相比优化前增加了54.3%;优化后构件比吸能sea为45.7
×
103j
·
kg-1,相比优化前增加了32.1%。
[0085]
表1优化后构件支护性能指标
[0086][0087]
再多了解一些
本文用于企业家、创业者技术爱好者查询,结果仅供参考。