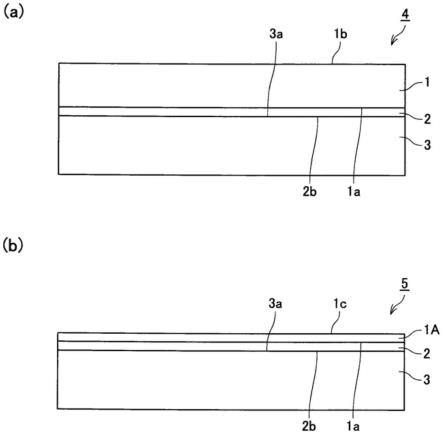
1.本发明涉及能够用于mems(micro electro mechanical system)镜等的将高刚性陶瓷振动板与支撑基板接合而成的接合体。
背景技术:
2.平视显示器(hud)是“以在将视线保持于前方的状态下将需要的信息映入视野的方式进行显示的装置”。在汽车的驾驶中,与看仪表面板、控制台面板上的信息的情形相比,能够在将视线保持于前方的状态下看到信息,因此,对防止漫不经心的驾驶有效,此外,眼睛的焦点移动减少,所以,能够减轻司机的疲劳并提高安全性。
3.对hud的原理进行说明。将荧光管、crt、液晶显示器的图像映入车的挡风玻璃或透明的屏幕(合路器)。此处,hud根据光学结构的不同而具有以下的2种方式。
4.(1)以挡风玻璃等为屏幕而直接投影图像的direct projection方式
5.(2)使挡风玻璃等作为反射镜发挥作用并在司机的视网膜上成像的virtual imaging方式
6.上述方式的最大区别在于:司机看到图像时的距离感。direct projection方式与普通的投影仪同样地在屏幕(合路器)上识别图像,而virtual imaging方式在司机的视线数米外的空间上识别图像。任一方式与不使用hud时相比较,司机在前方视野与仪表面板、控制台面板之间的视线移动都格外地减少。但是,virtual imaging方式中,通常驾驶时来自视野的焦点移动也减少,更能够将注意力集中于驾驶,减少疲劳。virtual imaging方式中,近年来正在开发扫描激光束进行绘制的新方式。
7.激光扫描型显示器将rgb3色的激光束利用称为合路器的光学元件进行合并,并将该1条射束利用微小镜进行反射而二维地进行扫描,由此进行绘制。虽然与crt的电子束扫描相似,但是,代替激发荧光体,在与其水平扫描线上的像素对应的位置,对各激光的脉冲宽度和输出功率进行控制,改变颜色和亮度,高速地进行像素点的绘制。可实现的分辨率取决于镜的振动频率和激光的调制频率。
8.作为该方式带来的主要的优点,举出以下内容。
9.(1)元器件数量较少,因此,能够实现小型化、低成本化、可靠性提高。
10.(2)按各像素所需要的亮度开启激光,因此,能够实现低耗电量。
11.(3)使用准直(平行光)的激光,因此,不需要进行焦点调整。
12.对于作为激光扫描型显示器的核心元器件的微镜,将si利用mems(micro electro mechanical system)技术进行加工,并蒸镀金属。镜的驱动方法有:利用静电引力进行驱动的静电方式、利用电磁力进行驱动的电磁方式、利用压电元件进行驱动的压电方式等。其中,对于压电方式,作为长处,可以举出高速驱动、低耗电量、大驱动力,作为短处,可以举出压电元件的成膜困难。例如,提出使用了soi基板的mems镜(专利文献1)。
13.现有技术文献
14.专利文献
15.专利文献1:日本特开2012-037578
16.专利文献2:日本特开2014-086400
技术实现要素:
17.要求hud在未来实现大屏幕化、广视角化,针对目前的7~8度视角,要求扩大至最大20度。为了实现大屏幕化及广视角,需要使mems镜的压电元件的频率、振幅及可靠性提高。特别是要求提高扫描的宽度及速度。但是,这对于以往的在si基板上通过成膜而形成的压电元件而言是无法实现的。
18.因此,对作为用于压电层之下的振动板采用高刚性陶瓷板进行了研究。但是,为了将高刚性陶瓷板用作上述振动板,需要将高刚性陶瓷板的厚度减薄至100μm以下的厚度,需要由此提高频率。但是,如果高刚性陶瓷板的厚度为100μm以下,则机械强度不足。因此,研究了:在将高刚性陶瓷板与支撑基板接合而得到接合体之后,将高刚性陶瓷板研磨加工至厚度100μm以下。
19.不过,实际尝试得知:由于高刚性陶瓷的难加工性,所以加工时的负荷(剪切应力)较大,产生剥离、开裂等问题。另外,研究了:为了提高振动板与支撑基板的接合强度,向振动板与支撑基板之间导入接合层,通过使振动板的表面变得粗糙来提高振动板与接合层的密合力,但是,认为:如果使振动板的表面变得粗糙,则振动板的弯曲强度降低。因此,在包含高刚性陶瓷的振动板与支撑基板的接合体中很难防止剥离、开裂。
20.本发明的课题在于:在厚度100μm以下的包含高刚性陶瓷的振动板与支撑基板的接合体的基础上,提供能够维持振动板的强度且防止振动板的剥离或开裂这样的结构。
21.本发明所涉及的振动板接合体具备:
22.支撑基板,该支撑基板包含硅;
23.振动板,该振动板包含高刚性陶瓷且厚度为100μm以下;以及
24.接合层,该接合层包含α-si,位于所述支撑基板与所述振动板之间,并与所述振动板的接合面接触,
25.所述振动板的所述接合面的算术平均粗糙度ra为0.01nm以上10.0nm以下,所述振动板的所述接合面的蚀坑密度为每100μm2有10个以上。
26.另外,本发明是振动板接合体的制法,其包括:
27.在包含高刚性陶瓷的高刚性陶瓷板的表面设置包含α-si的接合层的工序、
28.接下来将所述接合层的接合面和包含硅的支撑基板的接合面接合的工序、以及
29.接下来对所述高刚性陶瓷板进行加工而得到厚度100μm以下的振动板的工序,
30.所述振动板接合体的制法的特征在于,
31.所述高刚性陶瓷板的所述表面的算术平均粗糙度ra为0.01nm以上10.0nm以下,所述高刚性陶瓷板的所述表面的蚀坑密度为每100μm2有10个以上。
32.发明效果
33.如果在包含硅的支撑基板上直接键合块状的高刚性陶瓷板,则无法耐受将高刚性陶瓷板研磨到100μm以下的厚度时的研磨加工,发生高刚性陶瓷板的剥离或开裂。因此,本发明的发明人尝试了:在块状的高刚性陶瓷板上设置α-si的接合层,将该接合层与包含硅的支撑基板接合。设置α-si的接合层的目的在于:例如,在用于使振动板成为中空结构的蚀
刻工艺中能够抑制成本。包含α-si的接合层与包含硅的支撑基板的接合强度较高,理应能够耐受将高刚性陶瓷板的厚度研磨至100μm以下的加工。
34.但是,过去认为:进行研磨加工时,在高刚性陶瓷板与接合层的界面发生开裂或剥离的可能性较高。这是因为:高刚性陶瓷板需要弯曲强度,因此,需要使高刚性陶瓷板的表面平滑化。但是,如果高刚性陶瓷板表面平滑,则与在其表面设置的接合层(非晶质硅)的表面之间的密合性降低,因此,应该容易在高刚性陶瓷板与接合层的平滑界面发生剥离或开裂。
35.本发明的发明人在考虑以上因素的同时,尝试了使高刚性陶瓷板的表面(待设置接合层的接合面)的平滑性提高,结果发现,在某些情况下,即便接合面平滑,研磨加工时在与接合层的界面也不易发生剥离或开裂。
36.本发明的发明人对表现出上述超过预想的特性的振动板接合体进一步进行了研究。结果发现,即使高刚性陶瓷板的接合面的算术平均粗糙度(ra)极小的平滑面的情况下,也会因高刚性陶瓷板的物性而在接合面存在有由微细的空隙所引起的蚀坑,通过该表面蚀坑的作用而抑制了剥离,实现本发明。
37.即,振动板的接合面的算术平均粗糙度ra超过10.0nm的情况下,使其作为振动板进行振动时的弯曲强度较弱,无法耐受高振幅、高频的振动,因此,采用ra为10.0nm以下的超平滑面。发现即便在这种情况下,通过使振动板的接合面的蚀坑密度为每100μm2有10个以上,也能够防止研磨加工时的振动板的开裂或剥离。
附图说明
38.图1中,(a)表示在高刚性陶瓷板1的接合面1a设置有接合层2的状态,(b)表示将接合层2的表面2b用中性原子束活化后的状态,(c)表示将支撑基板3的接合面3a用中性原子束活化后的状态。
39.图2中,(a)表示高刚性陶瓷板1与支撑基板3的接合体4,(b)表示振动板1a与支撑基板3的接合体5。
40.图3是表示高刚性陶瓷板的接合面的表面蚀坑状态的afm测定图像。
具体实施方式
41.以下,适当参照附图,对本发明详细地进行说明。
42.如图1(a)所示,准备高刚性陶瓷板1。使高刚性陶瓷板的表面1a的算术平均粗糙度ra为0.01nm以上10.0nm以下,且使高刚性陶瓷板的表面的蚀坑密度为每100μm2有10个以上。1b为高刚性陶瓷板1的背面。
43.接下来,在高刚性陶瓷板1的表面1a上形成包含α-si的接合层2。接下来,如图1(b)所示,针对接合层2的接合面2a,像箭头a那样照射中性原子束,进行活化。另一方面,针对支撑基板3的接合面3a,像箭头b那样照射中性原子束,进行活化。
44.接下来,如图2(a)所示,使接合层2的被活化的接合面2b和支撑基板3的被活化的接合面3a接触,进行直接键合,由此得到接合体4。接下来,对接合体4的高刚性陶瓷板1的背面1b进行加工,由此,如图2(b)所示,使高刚性陶瓷板的厚度变小,形成厚度100μm以下的振动板1a,从而得到振动板接合体5。1c为加工面。
45.包含硅的支撑基板的厚度没有特别限定,从保持加工时的强度的观点考虑,优选为200μm以上,更优选为400μm以上。另外,对于支撑基板的接合面的算术平均厚度ra,从促进直接键合的观点考虑,优选为1nm以下,更优选为0.3nm以下。
46.所谓高刚性陶瓷,定义为:杨氏模量≥200gpa、且3点弯曲强度≥300gpa的陶瓷材料。
47.作为高刚性陶瓷,优选为硅铝氧氮陶瓷、堇青石、多铝红柱石、透光性氧化铝、氮化铝、氮化硅或碳化硅。
48.另外,对于高刚性陶瓷板的厚度,从基板的清洗、接合等工艺的操作性的观点考虑,优选为100μm以上,更优选为200μm以上。另外,高刚性陶瓷板的上限没有特别限制,从缩短加工所需时间的观点考虑,优选为300μm以下。
49.本发明中,振动板的表面(待设置接合层的表面)的算术平均粗糙度ra为0.01nm以上10.0nm以下,振动板的所述表面的蚀坑密度为每100μm2有10个以上。不过,振动板接合体中,在振动板上形成有接合层,因此,振动板的表面的ra及蚀坑密度与加工前的高刚性陶瓷板的表面的ra及蚀坑密度相同。
50.高刚性陶瓷板及振动板表面的算术平均粗糙度ra如下测定。首先,利用原子力显微镜(afm),以10μm
×
10μm的视野,对表面进行测定,按照jis b 0601计算出ra。另外,在与此相同的测定视野(面积100μm2)中,计数蚀坑数。此处,蚀坑的判定基准如下。即,将在表面观测到的凹部中的以下凹部设为蚀坑。
51.(1)凹部为φ50nm以上φ2000nm以下。
52.(2)凹部的深度为1nm以上。
53.本发明中,将振动板及高刚性陶瓷板的表面(待形成接合层的表面)的算术平均粗糙度ra设为0.01nm以上10.0nm以下,不过,从弯曲强度的观点考虑,更优选为7.0nm以下,特别优选为5.0nm以下。另外,从与接合层的密合性的观点考虑,将ra设为0.01nm以上,不过,更优选为0.02nm以上。
54.另外,振动板的所述表面的蚀坑密度设为每100μm2有10个以上,不过,更优选为20个以上。另外,振动板的所述表面的蚀坑密度通常可以设为每100μm2有200个以下,更优选为96个以下,特别优选为70个以下。
55.认为:在振动板及高刚性陶瓷板的面对接合层的所述表面所存在的蚀坑是由为了使高刚性陶瓷板致密烧结而添加的烧结助剂产生的。烧成时剩余的烧结助剂中的大部分以凝聚于陶瓷粒子的晶界的方式存在。将残留有烧结助剂的高刚性陶瓷进行晶片化并研磨为镜面时,烧结助剂凝聚的部分与高刚性陶瓷本身相比,研磨速度较快,因此,烧结助剂凝聚的部分成为蚀坑。据此,烧结助剂的添加量与蚀坑的数量具有相关性,可以通过烧结助剂的添加量来调整蚀坑数。
56.在得到高刚性陶瓷板的弯曲强度和较低的ra的基础上,高刚性陶瓷板的相对密度优选为95%以上,更优选为99%以上。另外,对于得到如上所述的ra和蚀坑密度而言适当的烧结助剂的种类及量根据待烧结的高刚性陶瓷的种类来适当选择。例如,作为烧结助剂,可例示:y2o3、cao、mgo、zro2。
57.本发明中,对于振动板及高刚性陶瓷板的背面(未形成接合层一侧的表面)的算术平均粗糙度ra,从弯曲强度的观点考虑,优选为0.01nm以上10.0nm以下。
58.作为高刚性陶瓷板的表面的研磨方法,利用例如#3000的磨石磨削至所期望的厚度后,以粒度3μm的金刚石浆料进行精研(lap),最后,利用化学机械研磨加工(cmp)进行镜面化。
59.在高刚性陶瓷板上成膜的接合层2的厚度没有特别限定,从制造成本的观点考虑,优选为0.01~10μm,更优选为0.05~0.5μm。
60.接合层2的成膜方法没有限定,可例示:溅射(sputtering)法、化学气相生长法(cvd)、蒸镀。
61.将接合层2的接合面、支撑基板的接合面平坦化的方法有:精研(lap)、化学机械研磨加工(cmp)等。
62.优选的实施方式中,通过中性原子束,能够将接合层2的表面2b、支撑基板3的表面3a活化。特别是,接合层2的表面2b、支撑基板3的表面3a为平坦面的情况下,容易直接键合。
63.在利用中性原子束进行表面活化时,优选使用专利文献2中记载那样的装置来产生中性束,进行照射。即,作为束源,使用鞍域型的高速原子束源。然后,向腔室中导入不活泼性气体,从直流电源向电极施加高电压。由此,利用在电极(正极)与壳体(负极)之间产生的鞍域型的电场,使得电子e运动,从而生成不活泼性气体的原子和离子的射束。到达栅格的射束中的离子束在栅格被中和,因此,中性原子的射束从高速原子束源射出。构成射束的原子种类优选为不活泼性气体(氩、氮等)。
64.利用射束照射进行活化时的电压优选为0.5~2.0kv,电流优选为50~200ma。
65.接下来,在真空气氛中,使活化面彼此接触,进行接合。此时的温度为常温,具体而言,优选为40℃以下,更优选为30℃以下。另外,接合时的温度特别优选为20℃以上25℃以下。接合时的压力优选为100~20000n。
66.接下来,对高刚性陶瓷板进行加工,由此得到厚度100μm以下的振动板。该振动板的厚度根据目标频率进行选择,因此,厚度的下限没有特别限制,从加工的容易度考虑,优选为1μm以上。作为该加工方法,例如利用#3000的磨石磨削至所期望的厚度后,以粒度3μm的金刚石浆料进行精研(lap)研磨,最后,利用化学机械研磨加工(cmp)进行镜面化。
67.实施例
68.(实施例1~8)
69.如参照图1~图2所说明那样,试制振动板接合体。
70.具体而言,将直径为4英寸、厚度为250μm的晶片形状的硅铝氧氮陶瓷基板用作高刚性陶瓷板1。将高刚性陶瓷板1的表面1a分别按算术平均粗糙度ra为表1、表2、表3给出的各数值的方式利用#3000的磨石磨削至所期望的厚度,然后,在表1所示的振动板表面(ra≤1nm)的情况下,以粒度3μm的金刚石浆料进行精研(lap),最后,利用化学机械研磨加工(cmp)进行镜面化。调整cmp研磨时的加工压力、加工时间,以便调整ra的数值。表2给出的振动板表面(ra》1nm)的情况下,以金刚石浆料进行精研(lap),进行镜面化。为了调整ra的数值,最后使用的金刚石浆料从粒度0.5μm至6μm之中选择使用。
71.另外,利用原子力显微镜(afm),以10μm
×
10μm的视野测定高刚性陶瓷振动板1的表面1a的ra。另外,此时通过原子力显微镜(afm)在10μm
×
10μm的视野中计数φ50nm以上的蚀坑数。不过,在测定高刚性陶瓷板1的表面1a的蚀坑数时,在晶片状的板1的中心点、自板1的定位边起算位于10mm内侧的点及自板1的与定位边相反一端起算10mm内侧的点、共3处分
别测定蚀坑密度,将3点测定值的平均值设为蚀坑密度,示于表1、表2、表3。
72.应予说明,图3中示出实施例4中使用的高刚性陶瓷板的表面状态(ra=0.07nm、10μm
×
10μm的视野中的蚀坑密度=58个)
73.另外,各例的高刚性陶瓷板的弯曲强度在接合后的基板中无法测定。因此,预先准备与各例的高刚性陶瓷基板1具有相同的材质、厚度、ra及蚀坑密度的各高刚性陶瓷板,从各高刚性陶瓷板中分别切出各试验片,测定3点弯曲强度。对于弯曲强度的测定方法,按照jis r 1601(精细陶瓷的室温弯曲强度试验方法)中的3点弯曲强度试验的标准进行测定。试验片的尺寸如下:样品长40.0mm、宽度4.0mm、厚度3.0mm。
74.接下来,通过直流溅射法,在高刚性陶瓷板1的表面1a形成接合层2。靶使用掺杂有硼的si。接合层2的厚度设为30~200nm。接合层2的表面2a的算术平均粗糙度ra为0.2~0.6nm。接下来,对接合层2进行化学机械研磨加工(cmp),使膜厚为20~150nm,使ra为0.08~0.4nm。
75.另一方面,作为支撑基板3,准备具有定向平面(of)部、直径为4英寸、厚度为500μm的包含硅的支撑基板3。支撑基板3的表面通过化学机械研磨加工(cmp)而进行了精加工,算术平均粗糙度ra为0.2nm。
76.接下来,对接合层2的表面2b和支撑基板3的表面3a进行清洗,去除污垢后,导入到真空腔室中。抽真空至大概10
-6
pa后,向各表面照射120秒钟的高速原子束(加速电压1kv、ar流量27sccm)。接下来,使接合层2的被活化的表面2b和支撑基板3的被活化的表面3a接触后,以10000n加压2分钟进行接合(图2(a))。接下来,将得到的各例的接合体4于100℃进行20小时加热。
77.接下来,对高刚性陶瓷板1的背面1b进行磨削及研磨,以使厚度从最初的250μm变成40μm(参照图2(b))。
78.【表1】
[0079][0080]
【表2】
[0081][0082]
【表3】
[0083][0084]
实施例1~8中,蚀坑密度为10~96个,所述ra为0.02~9.97nm,即便将振动板1a研磨至40μm的厚度,也完全没有发生剥离。并看到如下趋势,即,所述ra越大,陶瓷的弯曲强度越低,不过,即便在ra=9.97nm的情况下,弯曲强度的结果也为500mpa这一足够高的结果。
[0085]
(比较例1)
[0086]
比较例1中,没有在高刚性陶瓷板1形成包含α-si的接合层2。取而代之,对高刚性陶瓷板1的表面1a照射高速原子束,使高刚性陶瓷板1的被活化的表面1a和支撑基板3的被活化的表面3a接触,进行接合,得到接合体。但是,比较例1的高刚性陶瓷板1的表面1a的蚀坑数为51个,ra为0.03nm。另外,除了没有形成α-si的接合层以外,以与实施例1相同的条件进行制作。
[0087]
接下来,对得到的接合体的高刚性陶瓷板1的背面1b进行磨削及研磨加工,并尝试进行磨削及研磨以使厚度从最初的250μm减薄。在高刚性陶瓷板1的厚度达到110μm时,在高刚性陶瓷板与支撑基板的接合界面发生剥离。认为发生剥离是因为:接合体中的高刚性陶瓷板1与支撑基板3的接合强度低于实施例1~8中的接合强度,无法耐受对高刚性陶瓷板1进行研磨时的加工应力。
[0088]
(比较例2、3)
[0089]
比较例2、3的各接合体以与实施例1~8相同的条件进行制作。
[0090]
但是,比较例2中,高刚性陶瓷板1的表面1a的蚀坑数低至4个,表面1a的ra为0.01nm。这种情况下,利用磨削及研磨将高刚性陶瓷板1的背面减薄至厚度为100μm时,在高刚性陶瓷板1的表面与接合层2的界面发生剥离。认为这是因为:高刚性陶瓷板1与接合层2的密合强度无法耐受对高刚性陶瓷板1进行研磨时的加工应力。
[0091]
另一方面,即便在实施例1~4的陶瓷界面的表面ra低于0.2nm而足够小的情况下,也没有发生剥离,推测这是因为:在高刚性陶瓷板1的表面1a存在蚀坑,在蚀坑上成膜的接合层2因锚固效应而使得密合力提高。
[0092]
比较例3中,高刚性陶瓷振动板1的表面1a的蚀坑数为55个,不过,表面1a的ra为10.85nm。ra为10.85nm的情况下,高刚性陶瓷板的弯曲强度降低到300mpa。认为这是因为:应力集中于高刚性陶瓷板的表面所存在的凹凸,因此,弯曲强度变弱。
再多了解一些
本文用于企业家、创业者技术爱好者查询,结果仅供参考。