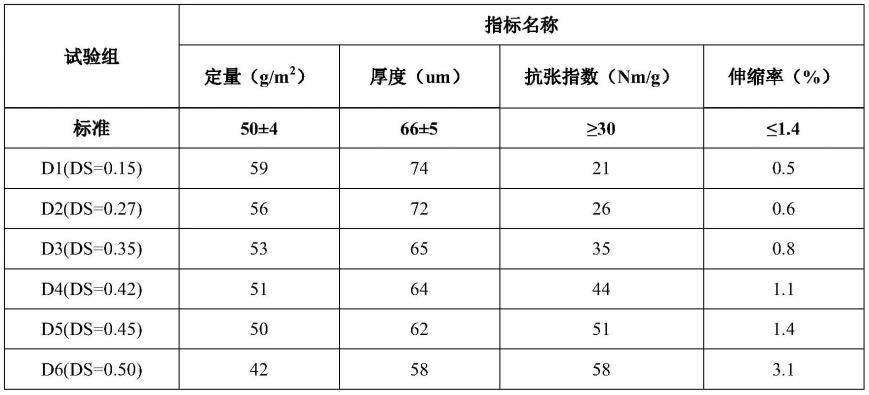
1.本发明属于造纸领域,涉及应用与印刷技术-热转印技术,具体涉及一种无涂层热转印印花纸及其制备方法。
背景技术:
2.热转印技术是一种间接转移的特种印刷技术,是一项新兴的印刷工艺,具有污染小、能耗低、创意灵活、生产便捷等特点。目前主要用于纺织印染、陶瓷贴花、金属塑料制品等行业。热转移印刷由电脑设计图案,利用热转移油墨打印到以纸为基材的特殊涂层上,然后通过热转印设备施加温度和压力将图案从纸再转移到布料等承印物上。
3.传统的热转印纸的生产工艺是先生产原纸,再在原纸的基础上涂布热转印涂料,不仅工艺繁琐、操作复杂、能耗高,而且纸病多,如漏涂、涂布量不均、刮线、翘曲等,成品a级率较低。热转印印花纸的涂层是热转移效果的关键,传统的热转印印花纸,转移涂层需要达到10克/平方米以上的涂布量才能承载高墨量,不仅耗费原料多而且容易出现起拱、折印等其他问题,因此低克重,高承载量成为热转印印花纸的生产新趋势。例如,中国专利文献cn110130142a公布一种低克重数码喷墨转移印花原纸及其生产方法,以植物纤维为主要原料,配以适量的无机填料和化学添加剂,低克重表面涂布,生产出伸缩率、抗张强度、吸水性、平滑度、转移率等指标均符合要求的转移印花原纸。以低克重的转印原纸去承载喷墨墨水,并提高了墨水的干燥速率和转移率,转印均匀,保证转印效果的同时,降低了墨水和原纸材料成本。其虽解决了以低克重的转印原纸去承载高喷墨量的问题,但仍然需要进行涂布涂层,存在漏涂、涂布量不均、刮线等问题。因此,制备一种无涂层热转印印花纸成为亟待解决的问题。
4.羧甲基纤维素(cmc)是天然纤维经羧甲基化后得到,其水溶液具有增稠、成膜、黏接、水分保持、胶体保护、乳化及悬浮等作用,被广泛应用于石油、食品、医药、纺织和造纸等行业。在热转印纸制造领域,cmc主要作为施胶剂或水性粘合剂。现有研究表明,cmc还具有良好的热转移性能,被用作热转印印花纸吸墨涂层的重要组分。然而,通常情况下,羧甲基纤维素(cmc),是粉体状的,可完全溶于水,不具备直接用于生产纸张的条件。例如,中国专利文献cn106378102a公布的羧甲基化纸浆纤维重金属吸附材料及其制备方法和用途,利用纸浆、碱、氯乙酸进行醚化反应,得到改性的羧甲基纤维。该羧甲基纤维的羧甲基取代度约为0.03~0.3,其取代度波动大,且醚化度不足,如果用于生产热转印纸的话,将无法转移热转印油墨。
技术实现要素:
5.针对上述提出的现有热转印印花纸存在的涂层漏涂、涂布量不均刮线等问题,本发明提供一种无涂层热转印印花纸及其制备方法。将纸浆纤维经碱化反应、醚化反应形成半流质状的羧甲基纤维浆料后直接抄造成热转印印花纸,无需涂布热转印涂料,直接用于热转印。具体技术方案如下:
6.首先,本发明提供一种无涂层热转印印花纸,该热转印印花纸为纸浆纤维经碱化反应、醚化反应形成半流质状的改性羧甲基纤维浆料后直接抄造而成,无需涂布热转印涂料,直接用于热转印;所述纸浆为针叶浆、阔叶浆或竹浆的一种或几种的混合浆,其打浆游离度为400
±
30;所述改性羧甲基纤维浆料的取代度为0.35~0.45,其打浆游离度为480
±
30。
7.其次,本发明提供一种无涂层热转印印花纸的制备方法,包括如下步骤:通过控制纸浆纤维碱化反应和醚化反应的反应条件,控制羧甲基纤维的取代度,形成适用于纸张抄造的半流质状的改性羧甲基纤维浆料,然后将该改性羧甲基纤维浆料直接进行抄造成热转印印花成纸;具体步骤如下:
8.1)碱化反应:在碎浆机中将纸浆纤维和naoh溶液按一定的质量比充分混合,进行碱化反应,控制碱化反应时间,获得碱性纤维浆料;
9.2)醚化反应:将碱化反应获得的碱性纤维浆料再按一定的质量比与氯乙酸混合,进行醚化反应,控制醚化反应时间,获得羧甲基纤维;该羧甲基纤维其羧甲基纤维的取代度控制在0.35~0.45范围内;
10.3)过滤浸泡:将醚化反应后的羧甲基纤维浆料过滤后,用水浸泡,并调节其ph值,获得半流质状的改性羧甲基纤维浆料;
11.4)抄造:将浸泡后的改性羧甲基纤维浆料经除渣、脱气后直接抄造成成品热转印印花纸。
12.作为优选的技术方案的,步骤1)中,所述纸浆为针叶浆、阔叶浆或竹浆的一种或几种的混合浆,其打浆游离度为400
±
30。
13.作为优选的技术方案的,步骤1)中,所述纸浆和naoh溶液混合的质量比为1∶0.5~1.5;所述naoh溶液的质量分数浓度为25%~35%;所述碱化反应的条件为:温度25~45℃,时间50~120min。
14.作为进一步优选的技术方案的,所述纸浆和naoh溶液混合的质量比为1∶1;所述碱化反应的条件为:温度35℃,时间50min。
15.作为优选的技术方案的,步骤2)中,所述碱性纤维与氯乙酸混合的质量比为1∶0.5~1;所述醚化反应条件为:温度65~80℃,时间50~90min。
16.作为进一步优选的技术方案的,所述碱性纤维浆料与氯乙酸混合的质量比为1∶0.5;所述醚化反应条件为:温度70℃,时间70min。
17.作为优选的技术方案的,步骤2)中,醚化反应后,甲基纤维浆料的取代度控制在0.42。
18.作为优选的技术方案的,步骤3)中,所述半流质状的改性羧甲基纤维浆料,其打浆游离度为480
±
30,ph值为7。
19.作为优选的技术方案的,步骤4)中,所述改性羧甲基纤维浆料,可再补加一定量的纸浆纤维。然后进行抄造,所补加的纸浆纤维为整体纸浆纤维质量的10%。
20.本发明的有益效果:
21.1)本发明热转印印花纸,为纸浆纤维经碱化反应、醚化反应形成半流质状的改性羧甲基纤维浆料后直接抄造而成;无需再进行施胶、涂布热转印涂料等工艺,彻底解决了热转印印花纸涂层漏涂、涂布量不均、刮线等问题。
22.2)本发明制备方法通控制纸浆纤维碱化反应和醚化反应的反应条件,将羧甲基纤维的取代度控制在0.35~0.45,使其改性后保持纤维形态,形成半流质状的羧甲基纤维适应抄纸造纸,从而使改性羧甲基纤维直接抄造成纸张成为可能,且操作具有产量高、能耗低、成本低、品质稳定等优点。
23.3)本发明制备方法通过将羧甲基纤维的取代度控制在0.35~0.45范围内,使其制备的热转印纸可直接用于热转印,且不会产生油墨残留在原纸上,满足市场需求。
24.4)本发明热转印印花纸,因无需涂布热转印涂料,省去涂布和烘干生产工序,造纸成本可节降900元/吨,且制备的纸张a级率可以提升至99%,利于热转印印花纸生产,减少碳排放,具有重要的经济价值和推广前景。
具体实施方式
25.为使本发明的目的、技术方案和优点更加清楚,下面将结合实施例,对本发明的技术方案进行清楚、完整地描述。
26.实施例1
27.本实施例为一种无涂层热转印印花纸的制备方法,该热转印印花纸为纸浆纤维经碱化反应、醚化反应形成半流质状的改性羧甲基纤维浆料后直接抄造而成,无需涂布热转印涂料,直接用于热转印。该无涂层热转印印花纸的制备方法,包括如下步骤:
28.1)碱化反应:在碎浆机中将纸浆纤维和naoh溶液混合,纸浆纤维与naoh的量比为1∶0.5~1.5,优选为1∶1;控制进行碱化反应条件为:25~45℃,优选35℃;反应50~120min,优选50min;获得碱性纤维。所述纸浆为针叶浆、阔叶浆或竹浆的一种或几种的混合浆,其打浆游离度为400
±
30;为保证浆料的游离度,所述naoh溶液的采用质量分数浓度为25%~35%的高浓度碱液,优选为30%。
29.2)醚化反应:将碱化反应获得的碱性纤维浆料再与氯乙酸混合,进行醚化反应,获得羧甲基纤维浆料;氯乙酸的用量为:纸浆纤维与氯乙酸的质量比为1∶0.5~1,优选为1∶0.5;醚化反应条件为:反应温度65~80℃,优选70℃;反应时间50~90min,优选70min;控制改性羧甲基纤维的取代度在0.35~0.45范围内,优选控制在0.42。因为申请人发现,如果羧甲基纤维取代度低于0.35,其制备的热转印纸会有大量的油墨残留在原纸上,无法满足市场需求;而当羧甲基纤维取代度大于0.5时,纸浆纤维开始向羧甲基纤维素(cmc)转化,不能进行抄造生产纸张。
30.3)过滤浸泡:将醚化反应后的羧甲基纤维浆料过滤,然后将其用水浸泡(固含量为4%),获得半流质状的改性羧甲基纤维浆料,并用稀盐酸中和,调节其ph值至7;该改性羧甲基纤维浆料的游离度为480
±
30。
31.4)抄造:向过浸泡后的改性羧甲基纤维浆料补加一定量的未改性的纸浆,经除渣、脱气后直接抄造成成品热转印印花纸。所补加的未改性的纸浆为整体纤维素纸浆质量的10%,纸浆补入后,改性后的羧甲基纤维和纸浆纤维的结合,将减少纸浆的流失;并且可以提升热转印纸的挺度、白度、交织度,有利于纸机的生产。
32.实施例2
33.本实施例为基于实施例1所述的制备方法制备无涂层热转印印花纸。具体如下:
34.采用阔叶浆=90g的桨板,送至碎浆机中与水进行高速分散,制成固含量在4%的
混合浆,打浆游离度400
±
30。碎浆过程中加入质量分数为30%的naoh溶液,纸浆纤维和naoh溶液的质量比1∶1,在35℃的环境下,反应90min,获得碱性纤维浆料。然后将碱性纤维浆料送至浆池中,并向浆池中加入氯乙酸粉末,碱性纤维浆料与氯乙酸的质量比1∶0.5,控制反应温度为70℃,醚化反应70min,获得羧甲基纤维浆料。经检测改性后的羧甲基纤维的取代度为0.42,且保持了纤维形态。将反应结束的羧甲基纤维浆料进行滤水,然后再加水浸泡,调制成固含量为4%的湿浆,并利用稀盐酸调节其ph值至7左右,获得打浆游离度为480
±
30的半流质状的改性羧甲基纤维浆料。然后向该改性羧甲基纤维浆料中加入10g针叶浆,获得混合浆料;将该混合浆料经除渣、脱气,进入头箱、成型网、压榨、干燥,卷取,获得成品热转印印花纸。
35.实施例3
36.本实施例为基于实施例2考察碱用量对羧甲基纤维取代度的影响。根据实施例1中的制备方法进行制备无涂层热转印印花纸,各热转印印花纸的配方与实施例2相同,其具体的制备条件除了碱化反应时碱用量不同,其他均与实施例2相同。本实施例中,重点考察了碱用量为纸浆纤维质量的30%、50%、100%、150%和200%,对取代度的影响,试验结果如表1所示。
37.表1.不同碱用量对羧甲基纤维取代度的影响
38.碱用量比例(%)2050100150200取代度(ds)0.150.340.420.450.53
39.由上表可以看出,随着碱用量的增加,取代度(ds)也增加,在碱用量为纸浆纤维质量的30%时,取代度(ds)仅为0.15;碱用量为纸浆纤维质量的200%时,取代度(ds)为0.53;考虑到取代度低于0.35,制备的热转印纸会有大量的油墨残留在原纸上,无法满足市场需求;而当羧甲基取代度大于0.5时,纸浆纤维开始向羧甲基纤维转化,不能进行抄纸生产纸张,因此本发明选择的碱用量控制为纸浆纤维质量的50%~150%。
40.实施例4
41.本实施例为基于实施例2考察碱化时间对羧甲基纤维取代度的影响。根据实施例1中的制备方法进行制备无涂层热转印印花纸,各热转印印花纸的配方与实施例2相同,其具体的制备条件除了碱化反应时间不同,其他均与实施例2相同。本实施例中,重点考察了碱化反应时间为30min、50min、90min、120min、150min对取代度的影响,试验结果如表2所示。
42.表2.不同碱化时间对羧甲基纤维取代度的影响
43.碱时间(min)305090120150取代度(ds)0.120.320.420.470.78
44.由上表可以看出,随着碱化时间的增加,取代度(ds)也增加,在碱化时间为30min时,取代度(ds)仅为0.12;碱化时间为150min时,取代度(ds)为0.78;鉴于将羧甲基纤维取代度控制在0.35~0.45,因此本发明碱化时间控制为50min~120min。
45.实施例5
46.本实施例为基于实施例2考察氯乙酸用量对羧甲基纤维取代度的影响。根据实施例1中的制备方法进行制备无涂层热转印印花纸,各热转印印花纸的配方与实施例2相同,其具体的制备条件除了醚化反应时氯乙酸用量不同,其他均与实施例2相同。本实施例中,重点考察了氯乙酸用量为纸浆纤维质量的25%、50%、75%、100%和125%对取代度的影
响,试验结果如表3所示。
47.表3.不同氯乙酸用量对羧甲基纤维取代度的影响
48.氯乙酸用量比例(%)255075100125取代度(ds)0.270.390.420.481.02
49.由上表可以看出,随着氯乙酸用量的增加,取代度(ds)也增加,在氯乙酸用量为纸浆纤维质量的25%时,取代度(ds)为0.27;碱用量为纸浆纤维质量的125%时,取代度(ds)为1.02;鉴于取代度低于0.35,其制备的热转印纸会有大量的油墨残留在原纸上,无法满足市场需求;而当取代度大于0.5时,纸浆纤维开始向羧甲基纤维转化,不能进行抄纸生产纸张,因此本发明氯乙酸用量控制为纸浆纤维质量的50%~100%。
50.实施例6
51.本实施例为基于实施例2考察醚化时间对羧甲基纤维取代度的影响。根据实施例1中的制备方法进行制备无涂层热转印印花纸,各热转印印花纸的配方与实施例2相同,其具体的制备条件除了醚化反应时醚化时间不同,其他均与实施例2相同。本实施例中,重点考察了醚化时间为30min、50min、70min、90min、120min对取代度的影响,试验结果如表4所示。
52.表4.不同醚化时间对羧甲基纤维取代度的影响
53.醚化时间(min)20507090120取代度(ds)0.220.350.420.500.65
54.由上表可以看出,随着醚化时间的增加,取代度(ds)也增加,在醚化时间为30min时,取代度(ds)仅为0.12;碱化时间为120min时,取代度(ds)为0.65;鉴于取代度低于0.35,其制备的热转印纸会有大量的油墨残留在原纸上,无法满足市场需求;而当取代度大于0.5时,纸浆纤维开始向羧甲基纤维转化,不能进行抄纸生产纸张,因此本发明醚化反应时间控制为50min~90min。
55.实施例7效果例
56.本实施例为考察所制备的热转印印花纸的热转印效果。本实施例采用实施例2制备的取代度(ds)为0.15、0.22、0.27、0.35、0.39、0.42、0.47、0.50、0.63、0.78及1.02的羧甲基纤维制备的热转印印花纸进行热转印实验(d1~d9),同时从市面购入某低克重热转印印花纸作为对比实验组(d),每组实验平行重复3次;分别测定各热转印印花纸转印率及物理性能。
57.转印率测定:使用装有热转印纸专用墨水的喷墨打印机在纸张上分别打印100%蓝色(c)、100%品红色(m)、100%黄色(y)和100%黑色(k)的四色色块,待油墨完全干燥后,使用反射密度计测定试样cmyk四色块的反射密度(测定时试样下垫8张d65亮度大于80%的白纸),即得热转印纸的打印色密度。
58.将漂白涤纶布正面朝上置于平板烫画机上,然后将打印有cmyk四色块的纸张覆盖于漂白涤纶布上(纸张印有cmyk四色块面与涤纶布相接触),将温度为220℃的平板烫画机在一定压力下置于纸张上,高温热压30s后,取下纸张和漂白涤纶布,此时纸张上的cmyk四色块已转印到漂白涤纶布上。用反射密度计测量漂白涤纶布上cmyk四色块的反射密度,即为cmyk四色块转印色密度;用反射密度计测量热转印后纸张上cmyk四色块的反射密度,即为cmyk四色块残留色密度;转印色密度除以转印色密度与残留色密度的和,即为转印率。不同热转印印花纸的转印率如表5所示。
59.表5.不同热转印印花纸平均转印率
60.试验组平均转移率d1(ds=0.15)25.55%d2(ds=0.27)42.38%d3(ds=0.35)61.19%d4(ds=0.42)68.06%d5(ds=0.45)68.18%d6(ds=0.50)72.51%d7(ds=0.63)/d8(ds=0.78)/d9(ds=1.02)/d(市场购入)69.42%
61.由上表可以看出,改性的羧甲基纤维的取代度小于0.35时,热转印油墨首先与纸浆纤维发生结合,油墨无法转移出,转移率均小于60%,油墨残留较多,不能满足市场需求。当取代度大于0.35小于0.5时,转移率与现有的热转印纸的转印效果相当,且随着取代度的提高,其转移率也提高;当取代度大于0.5时,纸浆纤维开始向羧甲基纤维素(cmc)转化,流失率太大,不能进行抄纸生产纸张。且从该表可以看出在取代度控制在0.42时,其制备的热转印印花纸转印效果最好。
62.物理性能检测:本实施例物理性能检测采用的是行业标准方法进行检测,不同取代度的热转印纸的物理性能进行检测结果如表6所示。
63.表6.不同取代度的热转印成纸物理性能性检测
[0064][0065]
由上表可以看出,随着取代度的增加,对应羧甲基纤维制备的热转印纸的定量和厚度均减小;且当取代度小于0.35时,热转印纸的定量及厚度均大于标准;取代度大于0.45时,热转印纸的定量及厚度均小于标准。而随着取代度的增加,对应羧甲基纤维制备的热转印纸的抗张指数及伸缩率增加,且在取代度大于0.35时,其纸张的抗张指数小于标准规定;在取代度大于0.45时,纸张的伸缩率大于标准规定。这是由于,随着取代度的增加,纸浆纤维开始向羧甲基纤维素(cmc)转化程度高,形成胶质物质,制备的纸张变轻薄,且弹性增加,抗张指数及伸缩率增加。
[0066]
因此,综合上述实验,本发明将改性的羧甲基纤维取代度控制为0.35~0.45的情况下,其热转印效果好于市面购入的热转印印花纸或与其持平,纸张的物理性能满足热转印的性能求,并能实现将制备的热转印印花纸直接用于热转印。
[0067]
总体来说,本发明将纸浆进行醚化,控制其取代度,使其形成半流质状的羧甲基纤维,适应抄纸机抄造,实现利用羧甲基纤维生产无涂层印花纸,且该原纸可直接作为热转印印花,无需再进行涂布工艺,不仅具有产量高、能耗低、成本低、品质稳定等优点,而且彻底解决涂层漏涂、涂布量不均、刮线的问题。且本发明通过控制碱化反应及醚化反应条件,控制羧甲基纤维的取代度在0.35~0.45范围内,使其制备的热转印纸可直接用于热转印,且不会产生油墨残留在原纸上,满足市场需求。另外,本发明通过改性羧甲基纤维制备成无涂层印花原纸,无需涂布热转移涂层,省去涂布和烘干生产工序,造纸成本可节降900元/吨,与此同时制造的纸张a级率可以提升至99%,利于热转印印花纸生产,减少碳排放,具有重要的经济价值和推广前景。
[0068]
对于本领域技术人员而言,显然本发明不限于上述示范性实施例的细节,而且在不背离本发明的精神或基本特征的情况下,能够以其他的具体形式实现本发明。因此,无论从哪一点来看,均应将实施例看作是示范性的,而且是非限制性的。此外,应当理解,虽然本说明书按照实施方式加以描述,但并非只包含一个的技术方案,说明书的这种叙述方式仅仅是为清楚起见,本领域技术人员应当将说明书作为一个整体,实施例中的技术方案也可以经适当组合,形成本领域技术人员可以理解的其他实施方式。
再多了解一些
本文用于企业家、创业者技术爱好者查询,结果仅供参考。