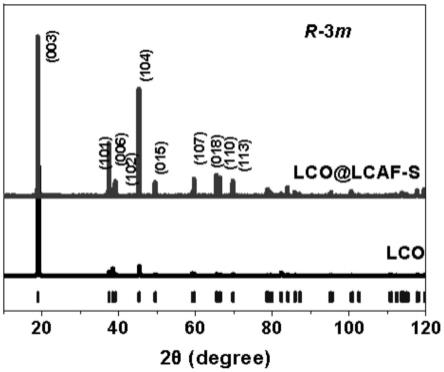
1.本技术涉及电池正极材料领域,特别是涉及一种电池层状正极材料及其制备方法和应用。
背景技术:
2.随着时代发展,人们对于能源需求的增加,导致能源短缺和环境恶化成为全球性的难题。
3.当前,化石燃料作为人类主要能源,在使用过程中产生大量的co2等温室气体,使地球温度升高,生态环境恶化。基于此,中国提出了“碳达峰”和“碳中和”的国家战略,以实现国家能源利用方式从不可再生化石能源到可再生清洁能源的转变,如风能、太阳能等。这种转变给储能器件的开发及应用提出了机遇和挑战。
4.锂离子电池自问世以来,由于开路电压高、循环寿命长、功率密度高、自放电少、无记忆效用等优点,不仅在3c应用领域,包括手机、数码相机、笔记本电脑等方面显示出广阔应用前景,而且在电动汽车、无人机、电动船等应用领域也有较多应用。
5.锂离子电池的性能与电池用电极材料的选择、制备工艺及性能等密切相关。当前,钴酸锂licoo2和三元正极材料li[ni
x
coymn
1-x-y
]o2(0《x《1,0《y《1)以高容量、高倍率和合成工艺简单等特性成为3c数码、无人机及电动车动力电源等锂电池的正极材料。这两类正极材料均为典型的层状结构,即过渡族金属层和锂层交替堆叠排列的晶体结构。这两类正极材料的层状结构在充放电过程中,伴随着循环往复的li
嵌入/脱出过程,过渡族金属层会发生滑移、层错、扭曲、甚至产生微裂纹,这种情况在高电压充放电过程中尤为严重。在循环往复的高电压充放电过程中,过渡族金属层的滑移、层错、扭曲及微裂纹的产生,导致界面结构坍塌、活性材料粉化、及高价态的活性ni/co离子导致界面副反应加剧等,最终导致电池内阻增加,容量快速衰减。
[0006]
为解决以上问题,目前采取的比较有效的策略是在活性材料表面进行包覆处理,该界面包覆层一般具有高的离子电导,且能够有效隔绝电解液与活性材料的直接接触。虽然这些策略能够对抑制副反应、延缓内阻增加有帮助,但对于解决过渡族金属层滑移、坍塌、扭曲和微裂纹形成的问题,并无显著作用。
[0007]
因此,如何有效解决过渡族金属层滑移、坍塌、扭曲和微裂纹形成,是从根本上解决电池层状正极材料容量快速衰减的关键,也是本领域的研究重点和难点。
技术实现要素:
[0008]
本技术的目的是提供一种改进的电池层状正极材料及其制备方法和应用。
[0009]
本技术采用了以下技术方案:
[0010]
本技术的一方面公开了一种电池层状正极材料,该电池层状正极材料的晶体结构中具有以钉扎的方式扎入晶体结构的表面界面层和体相层的异质相结构;该异质相结构均匀分布于晶体结构的表面,将晶体结构包覆其中,形成均匀的晶体表层。
[0011]
需要说明的是,本技术的晶体结构表面具有异质相结构的电池层状正极材料,其界面的异质相以钉扎的方式扎入各层中,能够起到保障各层状相稳定的作用,从根本上解决电池层状正极材料各层滑移、坍塌、扭曲和微裂纹的问题;并且,异质相结构形成的包覆晶体结构的晶体表层能够隔离电解液,抑制界面副反应,解决电池层状正极材料容量快速衰减的问题。因此,本技术的电池层状正极材料极大的提高了层状正极材料的电化学性能,尤其是在高电压(>4.3vvs.li/li
)充放电条件下表现出优异的容量、倍率和循环稳定性。本技术中,所谓“异质相结构”是指,对电池层状正极材料的晶体结构的表面界面进行元素替换或掺杂形成的结构,即元素构成异于电池层状正极材料;本技术的一种实现方式中,这种“异质相结构”是电池层状正极材料的晶体结构的体相层晶格延伸形成的,与电池层状正极材料的晶体结构的体相层共晶格的尖晶石相或岩盐相结构。
[0012]
还需要说明的是,本技术的电池层状正极材料,其异质相结构以钉扎的形式扎入晶体结构的体相各层和表面界面,还能够构筑形成三维的锂离子扩散网络,提高循环稳定性、容量和倍率性能。可以理解,本技术的晶体表层就是异质相结构均匀包覆晶体结构而形成的表面层;本技术的晶体表层是从微观的晶体结构水平形成的包覆在晶体结构表面的层,与现有的宏观的正极材料表面包覆修饰有本质区别。
[0013]
本技术的一种实现方式中,异质相结构为尖晶石相或岩盐相结构。
[0014]
需要说明的是,尖晶石相结构和岩盐相结构只是本技术的一种实现方式中具体形成的钉扎入晶体结构各层的异质相结构,不排除还可以是其他的异质相结构。
[0015]
本技术的一种实现方式中,异质相结构是由电池层状正极材料的晶体结构的体相层按照其相同晶格外延生长到晶体结构的表面界面层而成,即异质相结构与晶体结构的体相层共晶格。
[0016]
需要说明的是,共晶格的异质相结构只是本技术的一种实现方式中,由体相层的晶格外延生长而成,理论上来说,只要能够形成钉扎的异质相结构,不排除还可以是其他的非共晶格的方式。
[0017]
本技术的一种实现方式中,晶体表层的厚度大于或等于10nm。
[0018]
需要说明的是,本技术的晶体表层实际上就是异质相结构包覆晶体结构形成的位于晶体结构表面的微观结构层;因此,晶体表层的厚度,实际上就是钉扎的异质相结构扎入晶体结构各层的深度。为了确保异质相结构对各层状相的稳定作用,以及晶体表层对电解液的隔绝作用,本技术优选晶体表层的厚度不小于10nm。
[0019]
本技术的一种实现方式中,电池层状正极材料为li
1 x
tmo
2 y
,其中0≤x≤1,0≤y≤1,tm为co、mn、ni和al的至少一种。
[0020]
需要说明的是,锂离子电池层状正极材料只是本技术的一种实现方式中具体试验的电池层状正极材料,按照本技术的发明构思,不排除还可以是其他的离子电池层状正极材料。可以理解,过渡金属为co、mn、ni和al中的至少一种,这些只是比较常见的锂离子电池层状正极材料,不排除还可以是其他的过渡金属。
[0021]
本技术的一种实现方式中,电池层状正极材料为钴酸锂、高镍二元材料、高镍多元材料、富锂锰正极材料中的至少一种;其中,高镍是指镍含量大于或等于50%。
[0022]
需要说明的是,本技术的二元材料和多元材料,是指含镍、钴、锰、铝等中的两种或多种的正极材料;即二元材料就是含其中两种的正极材料;多元材料即含其中两种以上的
正极材料,例如含其中三种,即三元材料。
[0023]
本技术的一种实现方式中,电池层状正极材料为lini
0.8
co
0.1
mn
0.1
o2、lini
0.5
co
0.3
mn
0.2
o2和licoo2中的至少一种。
[0024]
可以理解,以上几种具体的电池层状正极材料只是本技术的一种实现方式中具体制备的几种锂离子电池层状正极材料,不排除还可以是其他的电池层状正极材料。
[0025]
本技术的一种实现方式中,晶体表层的组成元素包括阳离子和阴离子,阳离子包括li、co、mn、ni、al、b、mg、ca和zn中的至少一种,阴离子包括o和/或f。
[0026]
本技术的一种实现方式中,al、b、mg、ca、zn和/或氟的含量由内而外逐渐升高,co、mn、ni和/或o的含量由内而外逐渐降低。
[0027]
需要说明的是,在本技术的一种实现方式中,共晶格的异质相结构的层主要是预处理时采用的原材料中的元素,以及电池层状正极材料中的元素,两者在热处理时通过阴阳离子互扩散形成。因此,异质相结构层的组成元素,主要由预处理的原材料和电池层状正极材料组成。可以理解,虽然异质相是由晶体结构的体相层的晶格外延生长而成;但是,根据其组成元素的来源,各元素呈由内而外的升高或降低的梯度分布。例如,组成元素主要由电池层状正极材料提供的co、mn、ni和o等,其含量由内而外逐渐降低;组成元素主要由预处理的原材料提供的al、b、mg、ca、zn和氟,其含量由内而外逐渐升高。本技术中,由内而外是指由晶体结构的体相层向表层。
[0028]
本技术的另一面公开了本技术的电池层状正极材料的制备方法,包括对常规的电池层状正极材料进行以下处理,获得晶体结构中具有钉扎的异质相结构的电池层状正极材料;
[0029]
步骤一,采用以下方法中的至少一种对常规的电池层状正极材料进行预处理,
[0030]
(a)溶液浸泡法,包括将常规的电池层状正极材料浸泡于含li
、硼酸根、al
3
、mg
2
、ca
2
、zn
2
和f-中的至少一种的溶液中,浸泡条件为0-160℃浸泡1-24h,获得预处理的电池层状正极材料;
[0031]
(b)溶胶凝胶法,包括将常规的电池层状正极材料与含li
、硼酸根、al
3
、mg
2
、ca
2
、zn
2
和f-中的至少一种的溶胶凝胶均匀混合,加热烘干,获得预处理的电池层状正极材料;
[0032]
(c)球磨法,包括将常规的电池层状正极材料与含li
、硼酸根、al
3
、mg
2
、ca
2
、zn
2
和f-中的至少一种的固体材料一起进行球磨混料,获得预处理的电池层状正极材料;
[0033]
步骤二,将步骤一获得的预处理的电池层状正极材料,在惰性气氛或还原性气氛下,400-700℃热处理超过阈值时间,然后,控制降温速率小于或等于1℃/min,降温至室温,即可获得晶体结构中具有钉扎的异质相结构,且晶体表层的厚度大于或等于10nm的电池层状正极材料;其中,惰性气氛为氮气或氩气气氛;还原性气氛为氮气 氢气气氛,或氩气 氢气气氛。阈值时间满足公式τ=36-0.04t,其中τ为阈值时间,单位为h;t为热处理温度,单位为℃。也就是说,热处理温度越高,阈值时间越小。
[0034]
需要说明的是,本技术中,通过将步骤一中预处理的层状正极材料在400-700℃高温下进行超过阈值时间的热处理,同时,控制降温速率小于或等于1℃/min,是形成与体相层状结构共晶格的表面异质相结构的必要条件。通过控制高温下的热处理时间,能够实现表面外加替换金属和氟元素向内部体相层状结构的扩散,与体相层状结构共晶格的异质相
结构在该扩散过程中逐步形成;同时较慢的降温速率保证了与体相层状结构共晶格的异质相结构从高温到常温能够完全的保留下来,且消除因两相共晶格带来的材料内应力。本技术中,步骤二中热处理工艺的选择还能够使层状正极材料表面区域的异质相结构厚度大于或等于10nm,以保证表面区域异质相对层状结构具有足够的钉扎作用,从而抑制高电压下层状结构的滑移、坍塌和微裂纹产生。
[0035]
还需要说明的是,本技术中步骤一中通过溶液浸泡法、溶胶凝胶法、和球磨法,在原始层状正极材料粉末表面引入一层薄层且均匀的覆盖物,但该层覆盖物最大的作用是用于步骤二中对材料表层区域进行元素替换/扩散,以形成厚度大于10nm的表界面异质相结构层,这点与传统的包覆层用于导锂和隔绝电解液的作用有很大的区别。还需要说明的是,步骤二中热处理的时间需要足够长,同时,热处理后降温的速率足够慢,才能获得表面足够厚度的均匀的异质相结构区域,这样才能在高电压循环过程中起到对体相层状材料钉扎稳定的作用,这点与传统的包覆层也有很大区别。如果热处理时间过短或降温速率过快,材料表面的异质相区域的厚度小于10nm,则不足以让粒径尺度超过5μm的层状正极材料的层状结构在高电压充放电条件下保持稳定,材料内部由于大的结构应力导致的层状结构滑移、坍塌、微裂纹很难避免,最终影响到层状正极材料的循环稳定性。
[0036]
还需要说明的是,层状正极材料表面异质相结构与热处理温度和时间密切相关。一般来说,在满足“400-700℃高温下进行超过阈值时间的热处理,同时,控制降温速率小于1℃/min”的前提下,温度越高,热处理时间越长,降温速率越慢,越容易形成尖晶石相结构,反之,则容易形成岩盐相结构。岩盐相结构同样能够对晶体结构的各层进行钉扎,起到保障各层稳定的作用。
[0037]
本技术中,常规的电池层状正极材料是指晶体结构表面为正常的主金属层的电池层状正极材料;例如常规的licoo2,即晶体结构表面为正常的锂层,正常的锂氧结构的钴酸锂。本技术直接对常规的电池层状正极材料进行预处理和后续的热处理,即可获得本技术的晶体结构表面具有与体相层状结构共晶格的异质相结构的电池层状正极材料。
[0038]
本技术的再一面公开了本技术的电池层状正极材料在制备动力电池、大规模储能电池,或3c消费电子产品、无人机或电子烟的锂离子电池中的应用。
[0039]
可以理解,本技术的电池层状正极材料具有电压高、可逆充放电容量高、倍率高和循环稳定性好等优点,能够更好的用于动力电池或大规模储能电池,例如电动汽车或其他中大型电动设备的动力电池。同样的,本技术的电池层状正极材料也能够用于3c消费电子产品、无人机或电子烟的锂离子电池。
[0040]
本技术的再一面公开了一种采用本技术的电池层状正极材料的锂离子电池。
[0041]
可以理解,本技术的锂离子电池,由于采用本技术的电池层状正极材料,使得电池能够在更高的充放电电压下工作,并且具有更高的可逆充放电容量和倍率,且循环稳定性更好。
[0042]
本技术的有益效果在于:
[0043]
本技术的电池层状正极材料,其晶体结构中具有钉扎入各层的异质相结构,利用该异质相结构的钉扎作用,一方面,能够保障各层状相的稳定,解决晶体结构中各层滑移、坍塌、扭曲和微裂纹的问题;另一方面,异质相结构形成的晶体表层能够导电、导锂,并且在界面起到隔离电解液的作用。本技术的电池层状正极材料,在大于4.3v的高电压下也具有
较高的容量、倍率和循环稳定性,在高电压充放电条件下表现出优异的电化学性能。此外,本技术的电池层状正极材料制备方法简单,易于大规模工业化生产。
附图说明
[0044]
图1是本技术实施例中licoo2@lcaf-s的xrd表征结果图;
[0045]
图2是本技术实施例中licoo2@lcaf-s的表面形貌、元素分布及电子衍射特征分析结果;
[0046]
图3是本技术实施例中licoo2@lcaf-s与常规licoo2正极在3-4.6v vs.li/li
区间的倍率和循环性能结果图,其中,左图为两者倍率性能对比,右图为两者循环稳定性对比。
具体实施方式
[0047]
近年来,学界和产业界迫切的想通过提高充放电电压的方法实现锂离子电池更大的可逆容量存储,但以钴酸锂licoo2和三元正极材料li[ni
x
coymn
1-x-y
]o2(0《x《1,0《y《1)为代表的层状正极活性材料,在高电压(>4.35v vs.li/li
)循环过程中,不仅面临因界面副反应增加导致的电池内阻增加问题,而且,更重要的是,材料体相会产生因相结构演变导致的过渡族金属层滑移、坍塌、扭曲和微裂纹形成的问题,最终导致活性材料粉化。活性材料粉化进一步的促进了活性材料/电解液界面副反应,进一步导致内阻增加,电池性能加速衰减。也就是说,层状正极材料在高电压下面临的主要问题是大量离子嵌入/脱出导致的材料内应力累积诱发层状结构滑移、坍塌和裂纹滋生的问题。因此,高电压下,若想解决该问题,最重要的就是提出提高层状结构稳定性的策略。
[0048]
基于此,若想提高高电压下锂电池的循环稳定性,仅仅要通过传统的电化学惰性包覆层对层状正极活性材料进行包覆以降低界面副反应,是远远不够的。而且,传统的电化学惰性包覆层,是以牺牲材料可逆容量来获得高循环稳定性,这对产业化应用不利。本技术发明人创造性的提出,从正极材料表面结构/元素调控设计的角度,通过构筑表面异质相结构,增加层状正极材料过渡族金属层在高电压工况条件下、大量脱锂时的结构稳定性,以防止大量不可逆的微裂纹结构缺陷产生,降低层状正极材料在高压下快速衰减的可能性。
[0049]
以往的研究,主要集中在增加界面离子/电子电导和抑制副反应方面,而针对晶体结构优化提高层状结构稳定性的相关研究很少。本技术研究表明,在晶体结构表面形成的异质相结构,例如,本技术的一种实现方式中,具体是体相层状材料同晶格外延生长到表面界面形成的尖晶石相或岩盐相,这种晶体结构的电池层状正极材料,由于尖晶石结构或岩盐相结构在高电压充放电过程中能够保持稳定,且能够提供一个三维的锂离子传输网络,因此能够有效抑制高电压下过渡族金属层的滑移、坍塌、扭曲和微裂纹形成问题的同时,提高层状正极材料的容量和倍率性能。
[0050]
根据以上研究和认识,本技术创造性的提出了一种新的电池层状正极材料,其晶体结构中具有以钉扎的方式扎入晶体结构的表面界面层和体相层的异质相结构;异质相结构均匀分布于晶体结构的表面,将晶体结构包覆其中,形成均匀的晶体表层。
[0051]
在本技术中,与体相层状结构同晶格外延生长异质相结构非常稳定,在高电压充放电过程中,能对体相层状结构起到强烈钉扎作用,有效抑制因相结构演变导致的过渡族金属层滑移、坍塌、扭曲和微裂纹形成问题。因此,本技术的界面优化策略,能有效抑制高电
压循环过程副反应加剧和内阻快速增加问题,因而使层状正极材料在高电压下(>4.3v vs.li/li
)获得高的容量、倍率和循环稳定性。
[0052]
下面通过具体实施例对本技术作进一步详细说明。以下实施例仅对本技术进行进一步说明,不应理解为对本技术的限制。
[0053]
实施例一
[0054]
本例采用市售的商业化钴酸锂为原料,采用溶液浸泡法对其进行预处理,然后对预处理的钴酸锂进行热处理,即获得本例的晶体结构表面具有共晶格的尖晶石相界面的钴酸锂层状正极材料。具体制备方法如下:
[0055]
步骤一:预处理,将0.3mmol的硫酸铝放入40ml的去离子水中,搅拌10min形成澄清溶液a;将1g的商业化钴酸锂(d50为10-13微米,厦钨)和0.5g聚乙二醇放入溶液a中,搅拌10min,形成黑色的悬浊液b;将1.8mmol的氟化锂放入40ml去离子水中,搅拌2min形成溶液c;将溶液c逐滴加入到悬浊溶液b中,滴加过程中持续搅拌,形成悬浊液d;将该悬浊液d转移至60℃的水浴锅中水热反应6h后,抽滤,采用去离子水及无水乙醇进行清洗,在100℃真空烘箱中烘干,获得预处理的钴酸锂粉末。
[0056]
步骤二,后续热处理烧结,将上述预处理处理的licoo2粉末,在空气气氛下,600℃热处理24h后,控制降温速率1℃/min降温至常温,将所获得的粉末100目过筛,获得表面带有li、al、co、o和f成分尖晶石相的licoo2粉末,标记为licoo2@lcaf-spinel-1#。
[0057]
电化学测试:采用nmp作为溶剂,将licoo2@lcaf-spinel、炭黑和pvdf以质量比8:1:1的比例均匀混合,制备成正极极片,活性物质载量约为2.1mg cm-2
。使用2032纽扣电池制备以锂片作为负极的半电池,使用celgard 2035隔膜和高电压电解液(质量比lipf6:emc:fec=15:55:30),将该半电池在3-4.6v(vs.li/li
)之间循环。
[0058]
材料表征及电化学结果:xrd分析结果表明,所得licoo2@lcaf-spinel-1#晶胞参数属于r-3m,为典型的钴酸锂层状结构,如图1所示。tem eds-mapping元素分析结果表明,表明存在一层厚度约20nm的成分包含co、mg、f和o元素的梯度层,如图2所示。进一步对该界面层的电子衍射特征进行分析,表明该厚度约20nm的界面层表现出明显的尖晶石结构特征,说明表面存在一层成分包含li、co、mg、o和f的尖晶石结构层,即晶体结构表面具有共晶格的尖晶石相界面层。分析结果显示,共晶格的尖晶石相界面是由电池层状正极材料的晶体结构的体相层按照其相同晶格外延生长到晶体结构的表面界面而成;尖晶石相界面中共晶格的尖晶石以钉扎的形式扎入晶体结构的表面区域与体相层;并且,尖晶石相界面中共晶格的尖晶石均匀分布于表面界面。综合多方面结果分析,该合成的材料为表面梯度尖晶石钉扎的钴酸锂层状正极材料,即金属元素al和f的含量由内而外逐渐升高,co和氧的含量由内而外逐渐降低。电化学测试结果表明,以正极材料licoo2@lcmf-spinel-1#和锂金属负极搭配的扣式电池,在3-4.6v vs.li/li
区间充放电循环过程中,相比购买的没有经过任何处理的licoo2,本例预处理和热处理的licoo2表现出更高的倍率和循环稳定性,其在0.1c和10c电流下的放电容量分别是~218mah/g和~109mah/g,在2c电流下45℃高温循环200圈后容量保持率为~79.4%。
[0059]
实施例二
[0060]
本例采用市售的商业化钴酸锂为原料,采用球磨法对其进行预处理,然后对预处理的钴酸锂进行热处理,即获得本例的晶体结构表面具有共晶格的尖晶石相界面的钴酸锂
层状正极材料。具体制备方法如下:
[0061]
步骤一:预处理,将0.3mmol的氟化锌(纳米粉末,d
50
约为20nm)、0.3mmol的氟化锂(纳米粉末,d
50
约为15nm)与和10mmol的商业化钴酸锂(d
50
为10-13微米,厦钨)混合均匀,手工研磨60min。将混合均匀的粉料放在120℃的真空烘箱中干燥12h以上,100目过筛,备用,即可获得预处理的表面含li、co、zn、o和f的钴酸锂粉末。
[0062]
步骤二,后续热处理烧结,将上述预处理的licoo2粉末,在ar惰性气氛下,在旋转管式炉中650℃热处理24h后,控制降温速度低于1℃/min,将所获得的粉末100目过筛,标记为licoo2@lzf-spinel-2#。作为对比,未经过步骤二处理的材料标记为licoo2@lf af。
[0063]
电化学测试:采用nmp作为溶剂,将licoo2@lzf-spinel-2#、炭黑和pvdf以质量比8:1:1的比例均匀混合,制备成正极极片,活性物质载量约为2.5mg cm-2
。使用2032纽扣电池制备以锂片作为负极的半电池,使用celgard 2035隔膜和高电压电解液(质量比lipf6:emc:fec=15:55:30),将该半电池在3-4.6v(vs.li/li
)之间循环。
[0064]
材料表征及电化学结果:xrd分析结果表明,所得licoo2@lzf-spinel-2#晶胞参数属于r-3m,为典型的钴酸锂层状结构。tem eds-mapping及衍射分析结果表明,表面存在一层厚度约25nm左右的尖晶石层,尖晶石层的元素成分包括li、co、al、o和f,即材料表面具有尖晶石层。针对未经过步骤二处理的材料分析表明,所得材料表面仅存在若干5-20nm纳米尺度的氟化锂和氟化铝的纳米粒子附着层,而未形成尖晶石相。
[0065]
电化学测试结果表明,以正极材料licoo2@lczf-s和锂金属负极搭配的扣式电池,在3-4.6v vs.li/li
区间充放电循环过程中,相比购买的没有经过任何处理的licoo2和未经过步骤二处理的licoo2@lf af材料,表现出更高的倍率和循环稳定性,其在在0.1c和10c电流下的放电容量分别是~220mah/g和~129mah/g,在2c电流下循环200圈后容量保持率为89.4%。未经过步骤二处理的licoo2@lf af材料,在在0.1c和10c电流下的放电容量分别是~201mah/g和~65mah/g,在2c电流下循环200圈后容量保持率为59.1%。
[0066]
实施例三
[0067]
本例采用市售的商业化钴酸锂为原料,采用溶胶凝胶法对其进行预处理,然后对预处理的钴酸锂进行后续热处理,即获得本例的晶体结构表面具有共晶格的尖晶石相界面的钴酸锂层状正极材料。具体制备方法如下:
[0068]
步骤一:预处理,将10mmol的商业化钴酸锂(d
50
为10-13微米,厦钨)和1g的聚乙二醇(分子量大于2000)倒入40ml去离子水中,搅拌均匀形成悬浊溶液a;在溶液a中加入0.3mmol的硫酸镁和0.3mmol的硫酸锂,持续搅拌溶解形成悬浊溶液b;在40ml的去离子水中加入0.9mmol的氟化钾,形成溶液c;将溶液c逐滴加入到溶液b中,并在90℃下持续搅拌,直至水分蒸发完毕;将所获得的材料进行在120℃的真空烘箱中干燥12h以上,100目过筛,备用。
[0069]
步骤二,后续热处理烧结,将步骤一预处理后的粉末,在ar惰性气氛下,在旋转管式炉中650℃热处理24h后,控制降温速度低于1℃/min,将所获得的粉末100目过筛,标记为licoo2@lmf-spinel-3#。
[0070]
电化学测试:采用nmp作为溶剂,将licoo2@lcmf-spinel-3#、炭黑和pvdf以质量比8:1:1的比例均匀混合,制备成正极极片,活性物质载量约为2.5mg cm-2
。使用2032纽扣电池制备以锂片作为负极的半电池,使用celgard 2035隔膜和高电压电解液(质量比lipf6:
emc:fec=15:55:30),将该半电池在3-4.6v(vs.li/li
)之间循环。
[0071]
材料表征及电化学结果:xrd分析结果表明,所得licoo2@lcmf-spinel-3#晶胞参数属于r-3m,为典型的钴酸锂层状结构。tem eds-mapping及衍射分析结果表明,表面存在一层厚度约28nm左右的尖晶石层,尖晶石层的元素成分包括li、co、al、o和f,即材料表面具有尖晶石层。
[0072]
电化学测试结果表明,以正极材料licoo2@lcmf-s和锂金属负极搭配的扣式电池,在3-4.6v vs.li/li
区间充放电循环过程中,相比购买的没有经过任何处理的licoo2,表现出更高的倍率和循环稳定性,其在在0.1c和10c电流下的放电容量分别是~225mah/g和~134mah/g,在2c电流下循环200圈后容量保持率为92.3%。
[0073]
实施例四
[0074]
采用与实施例二中相同的球磨法和热处理,对lini
0.8
co
0.1
mn
0.1
o2和lini
0.5
co
0.3
mn
0.2
o2进行步骤一和步骤二的预处理和后续热处理,所得材料分别标记为ncm811@lzf-spinel和替换ncm532@lzf-spinel。即分别采用lini
0.8
co
0.1
mn
0.1
o2和lini
0.5
co
0.3
mn
0.2
o2等量替换实施例二的钴酸锂,其余不变。
[0075]
xrd分析结果表明,所得ncm811@lzf-spinel和ncm532@lzf-spinel为典型层状结构。tem eds-mapping及衍射分析结果表明,表明存在一层厚度分别约为35nm和27nm左右的尖晶石相区域,在表界面处均匀分布,其中,尖晶石相层的元素成分包括li、ni、co、mn、zn、o和f。经过步骤一和步骤二处理后的两种材料均表现出了更优异的倍率和循环稳定性。
[0076]
以正极材料ncm811@lzf-spinel和锂金属负极搭配的扣式电池,在3-4.3v vs.li/li
区间充放电循环过程中,其在在0.1c和10c电流下的放电容量分别是~215mah/g和~125mah/g,在2c电流下循环200圈后容量保持率为89.3%。
[0077]
以正极材料ncm532@lzf-spinel和锂金属负极搭配的扣式电池,在3-4.3v vs.li/li
区间充放电循环过程中,其在在0.1c和10c电流下的放电容量分别是~205mah/g和~113mah/g,在2c电流下循环200圈后容量保持率为84.3%。
[0078]
实施例五
[0079]
采用与实施例二中相同的球磨法和热处理,对一些典型的高镍二元材料,例如lini
0.8
co
0.2
o2(nc82)、lini
0.8
mn
0.2
o2(nm82)、lini
0.6
co
0.4
o2(nc64)、lini
0.6
mn
0.4
o2(nm64);高镍三元材料,例如lini
0.6
co
0.2
mn
0.2
o2(ncm622)、lini
0.8
co
0.1
mn
0.1
o2(ncm811)、lini
0.8
co
0.1
al
0.1
o2(nca811);高镍多元材料,例如lini
0.7
co
0.1
mn
0.1
al
0.1
o2(ncma7111)进行步骤一和步骤二的预处理和后续热处理,合成完毕后获得的样品在3-4.3v的电位区间进行电化学测试,所得结果表1所示,
[0080]
表1采用实施例二方法处理的高镍典型正极材料的电化学性能
[0081][0082][0083]
通过对表1中几种典型高镍材料进行球磨和热处理前后的电化学数据结果分析,可知,表面区域异质相钉扎对所有典型高镍材料的倍率、容量和循环稳定性均具有有益效果。
[0084]
实施例六
[0085]
采用与实施例二中相同的球磨法,对商业化licoo2材料(d
50
为10-13微米,厦钨)进行步骤一和步骤二的预处理和后续热处理,通过调控步骤二后续热处理工艺中热处理温度/时间及降温控制时间,获得不同厚度的表面区域尖晶石相层。具体的,热处理工艺条件如表2所示。
[0086]
表2热处理工艺条件及正极材料性能测试结果
[0087][0088][0089]
采用实施例二相同的方法对本例制备的晶体结构表面具有共晶格的尖晶石相界面的正极材料进行0.1c/10c容量测试和2c循环200圈容量保持率测试,结果如表2所示。
[0090]
通过对表2中结果的分析,可得到如下结论:
[0091]
1)对比350-750℃热处理24h,同时降温速率小于1℃/min的6个样品,发现350℃样品表面并未发现明显尖晶石相层。随着热处理温度提高,2c循环200圈容量保持率逐渐提高,但相应的容量和倍率性能降低。
[0092]
2)对比600℃热处理24h,但降温速率不同的5个样品,发现随着降温速率的提高,材料容量和倍率变化不大,但循环稳定性逐步降低。
[0093]
3)对比400℃热处理6h、12h和24h,降温速率均低于1℃/min的3个样品,发现,热处理时间延长,尖晶石相层的厚度逐渐增加,但400℃热处理12h的样品尖晶石相厚度仍小于10nm,导致循环稳定性不佳;对比700℃热处理6h、12h和24h,降温速率均低于1℃/min的3个样品,发现,热处理时间延长,尖晶石相层的厚度逐渐增加,700℃热处理超过6h样品表面尖晶石相厚度即可大于10nm,同时在2c循环200圈后容量保持率均大于80%。
[0094]
4)对于750℃热处理24h,同时降温速率小于1℃/min的样品的电化学数据,发现温度超过700℃,尽管循环稳定性极大提高,但不利于倍率和容量的发挥。
[0095]
本实施例的结果表明,不同热处理温度下获得“尖晶石相结构厚度大于或等于10nm”的时间阈值是不同的,热处理温度越高,时间阈值越低;原则上,只要满足在特定热处
理温度t时,热处理的时间超过阈值时间τ即可,两者满足公式τ=36-0.04t,其中τ为阈值时间,单位为h;t为热处理温度,单位为℃。在700℃高温条件下,热处理超过6h即可获得厚度超过10nm的尖晶石相界面层。实际生产过程中,基于能耗问题考虑,我们选取合适的温度和时间对材料进行热处理。因此,优选采用400-700℃热处理超过阈值时间。同时,本实施例的结果表明,降温速率对材料容量和倍率的影响较小,但对材料循环稳定性的影响很大,只有在降温速率低于或等于1℃/min条件下,所获得的层状正极材料的循环稳定性才能得到保证。
[0096]
以上内容是结合具体的实施方式对本技术所作的进一步详细说明,不能认定本技术的具体实施只局限于这些说明。对于本技术所属技术领域的普通技术人员来说,在不脱离本技术构思的前提下,还可以做出若干简单推演或替换。
再多了解一些
本文用于企业家、创业者技术爱好者查询,结果仅供参考。